ΠΠΈΡΠ»ΠΎΡΠΎΠ΄Π½ΠΎ-ΠΊΠΎΠ½Π²Π΅ΡΡΠ΅ΡΠ½ΡΠΉ ΡΠΏΠΎΡΠΎΠ± ΠΏΡΠΎΠΈΠ·Π²ΠΎΠ΄ΡΡΠ²Π° ΡΡΠ°Π»ΠΈ: Π²ΠΈΠ΄Ρ ΠΈ ΠΏΡΠΎΡΠ΅ΡΡ
ΠΠΊΠΎΠ»ΠΎ 70% ΡΡΠ°Π»ΠΈ ΠΎΡ ΠΎΠ±ΡΠ΅Π³ΠΎ ΠΎΠ±ΡΠ΅ΠΌΠ° ΠΌΠΈΡΠΎΠ²ΠΎΠ³ΠΎ ΠΏΡΠΎΠΈΠ·Π²ΠΎΠ΄ΡΡΠ²Π° ΠΈΠ·Π³ΠΎΡΠ°Π²Π»ΠΈΠ²Π°Π΅ΡΡΡ ΠΊΠΎΠ½Π²Π΅ΡΡΠ΅ΡΠ½ΡΠΌ ΡΠΏΠΎΡΠΎΠ±ΠΎΠΌ. ΠΠΎ ΡΠ΅ΡΠ΅Π΄ΠΈΠ½Ρ ΠΏΡΠΎΡΠ»ΠΎΠ³ΠΎ ΡΡΠΎΠ»Π΅ΡΠΈΡ Π΄Π»Ρ ΠΏΠΎΠ»ΡΡΠ΅Π½ΠΈΡ ΡΡΠ°Π»ΠΈ ΠΏΡΠΈΠΌΠ΅Π½ΡΠ»ΠΈΡΡ Π±Π΅ΡΡΠ΅ΠΌΠ΅ΡΠΎΠ²ΡΠΊΠΈΠΉ ΠΈ ΡΠΎΠΌΠ°ΡΠΎΠ²ΡΠΊΠΈΠΉ ΠΏΡΠΎΡΠ΅ΡΡΡ. ΠΠ΄Π½Π°ΠΊΠΎ Π² Π΄Π°Π»ΡΠ½Π΅ΠΉΡΠ΅ΠΌ ΡΡΠ°Π»Ρ Π½Π°ΡΠ°Π»ΠΈ ΠΏΡΠΎΠΈΠ·Π²ΠΎΠ΄ΠΈΡΡ ΡΡΠΎΠ²Π΅ΡΡΠ΅Π½ΡΡΠ²ΠΎΠ²Π°Π½Π½ΡΠΌ ΠΊΠΈΡΠ»ΠΎΡΠΎΠ΄Π½ΠΎ-ΠΊΠΎΠ½Π²Π΅ΡΡΠ΅ΡΠ½ΡΠΌ ΡΠΏΠΎΡΠΎΠ±ΠΎΠΌ. Π Π½Π°ΡΡΠΎΡΡΠ΅Π΅ Π²ΡΠ΅ΠΌΡ ΠΏΡΠ΅Π΄ΡΠ΅ΡΡΠ²Π΅Π½Π½ΠΈΠΊΠΈ ΡΠΎΠ²ΡΠ΅ΠΌΠ΅Π½Π½ΠΎΠ³ΠΎ ΠΌΠ΅ΡΠΎΠ΄Π° ΠΏΡΠ°ΠΊΡΠΈΡΠ΅ΡΠΊΠΈ Π½Π΅ ΠΏΡΠΈΠΌΠ΅Π½ΡΡΡΡΡ.
Π‘ΡΡΡ ΠΊΠΎΠ½Π²Π΅ΡΡΠ΅ΡΠ½ΠΎΠ³ΠΎ ΠΏΡΠΎΠΈΠ·Π²ΠΎΠ΄ΡΡΠ²Π°
Π ΠΊΠΎΠ½Π²Π΅ΡΡΠ΅ΡΠ½ΠΎΠΌ ΠΏΡΠΎΠΈΠ·Π²ΠΎΠ΄ΡΡΠ²Π΅ ΠΏΡΠΈΠΌΠ΅Π½ΡΡΡΡΡ ΡΠΏΠ΅ΡΠΈΠ°Π»ΡΠ½ΡΠ΅ ΡΡΠ°Π»Π΅ΠΏΠ»Π°Π²ΠΈΠ»ΡΠ½ΡΠ΅ Π°Π³ΡΠ΅Π³Π°ΡΡ, Π½Π°Π·ΡΠ²Π°Π΅ΠΌΡΠ΅ ΠΊΠΎΠ½Π²Π΅ΡΡΠ΅ΡΠ°ΠΌΠΈ. ΠΡΠΎΠΈΠ·Π²ΠΎΠ΄ΡΡΠ²ΠΎ ΡΡΠ°Π»ΠΈ ΠΎΡΡΡΠ΅ΡΡΠ²Π»ΡΠ΅ΡΡΡ ΠΏΡΡΠ΅ΠΌ ΠΏΡΠΎΠ΄ΡΠ²ΠΊΠΈ ΠΆΠΈΠ΄ΠΊΠΎΠ³ΠΎ ΡΡΠ³ΡΠ½Π° Π²ΠΎΠ·Π΄ΡΡ ΠΎΠΌ ΠΈΠ»ΠΈ ΠΊΠΈΡΠ»ΠΎΡΠΎΠ΄ΠΎΠΌ. ΠΠ°Π½Π½ΡΠΉ ΠΌΠ΅ΡΠ°Π»Π» ΡΠΎΠ΄Π΅ΡΠΆΠΈΡ ΡΠ°Π·Π»ΠΈΡΠ½ΡΠ΅ ΠΏΡΠΈΠΌΠ΅ΡΠΈ, Π² ΡΠΎΠΌ ΡΠΈΡΠ»Π΅ ΠΊΡΠ΅ΠΌΠ½ΠΈΠΉ, ΡΠ³Π»Π΅ΡΠΎΠ΄ ΠΈ ΠΌΠ°ΡΠ³Π°Π½Π΅Ρ. ΠΡΠΈΠΌΠ΅ΡΠΈ ΠΎΠΊΠΈΡΠ»ΡΡΡΡΡ ΠΏΠΎΠ΄ Π΄Π΅ΠΉΡΡΠ²ΠΈΠ΅ΠΌ ΠΊΠΈΡΠ»ΠΎΡΠΎΠ΄Π° ΠΈ ΡΠ΄Π°Π»ΡΡΡΡΡ ΠΈΠ· ΡΠ°ΡΠΏΠ»Π°Π²Π°. ΠΡΠ½ΠΎΠ²Π½ΡΠΌ ΠΏΡΠ΅ΠΈΠΌΡΡΠ΅ΡΡΠ²ΠΎΠΌ ΠΊΠΎΠ½Π²Π΅ΡΡΠ΅ΡΠ½ΠΎΠ³ΠΎ ΡΠΏΠΎΡΠΎΠ±Π° ΡΠ²Π»ΡΠ΅ΡΡΡ ΡΠΎ, ΡΡΠΎ Π΄Π»Ρ ΡΠ°Π±ΠΎΡΡ ΡΡΠ°Π»Π΅ΠΏΠ»Π°Π²ΠΈΠ»ΡΠ½ΠΎΠ³ΠΎ ΡΡΡΡΠΎΠΉΡΡΠ²Π° Π½Π΅ ΡΡΠ΅Π±ΡΠ΅ΡΡΡ ΡΠΎΠΏΠ»ΠΈΠ²ΠΎ. Π‘ΡΠ°Π»Ρ ΡΠ°ΡΠΏΠ»Π°Π²Π»ΡΠ΅ΡΡΡ ΠΏΠΎΠ΄ Π΄Π΅ΠΉΡΡΠ²ΠΈΠ΅ΠΌ ΡΠ΅ΠΏΠ»Π°, ΠΊΠΎΡΠΎΡΠΎΠ΅ Π²ΡΠ΄Π΅Π»ΡΡΡ ΠΎΠΊΠΈΡΠ»ΡΡΡΠΈΠ΅ΡΡ ΠΏΡΠΈΠΌΠ΅ΡΠΈ.
ΠΡΠΈΠ½ΡΠΈΠΏ Π±Π΅ΡΡΠ΅ΠΌΠ΅ΡΠΎΠ²ΡΠΊΠΎΠ³ΠΎ ΡΠΏΠΎΡΠΎΠ±Π°
ΠΠΏΠ΅ΡΠ²ΡΠ΅ ΠΌΠ°ΡΡΠΎΠ²ΠΎΠ΅ ΠΏΠΎΠ»ΡΡΠ΅Π½ΠΈΠ΅ ΠΆΠΈΠ΄ΠΊΠΎΠΉ ΡΡΠ°Π»ΠΈ ΡΡΠ°Π»ΠΎ Π²ΠΎΠ·ΠΌΠΎΠΆΠ½ΡΠΌ Π² 1856 Π³ΠΎΠ΄Ρ Π±Π»Π°Π³ΠΎΠ΄Π°ΡΡ Π. ΠΠ΅ΡΡΠ΅ΠΌΠ΅ΡΡ β ΠΈΠ·ΠΎΠ±ΡΠ΅ΡΠ°ΡΠ΅Π»Ρ ΠΈΠ· ΠΠ½Π³Π»ΠΈΠΈ. ΠΠ½ ΠΏΡΠΈΠ΄ΡΠΌΠ°Π», ΠΊΠ°ΠΊ Π½Π°Π³ΡΠ΅ΡΡ ΠΌΠ΅ΡΠ°Π»Π» Π΄ΠΎ ΡΠ΅ΠΌΠΏΠ΅ΡΠ°ΡΡΡΡ, ΠΏΡΠ΅Π²ΡΡΠ°ΡΡΠ΅ΠΉ 1500Β°Π‘. ΠΠΌΠ΅Π½Π½ΠΎ ΡΠ°ΠΊΠ°Ρ ΡΠ΅ΠΌΠΏΠ΅ΡΠ°ΡΡΡΠ° Π½Π΅ΠΎΠ±Ρ ΠΎΠ΄ΠΈΠΌΠ° Π΄Π»Ρ ΡΠΎΠ³ΠΎ, ΡΡΠΎΠ±Ρ ΡΠ°ΡΠΏΠ»Π°Π²ΠΈΡΡ ΠΌΠ΅ΡΠ°Π»Π» Ρ ΠΏΠΎΠ½ΠΈΠΆΠ΅Π½Π½ΡΠΌ ΡΠΎΠ΄Π΅ΡΠΆΠ°Π½ΠΈΠ΅ΠΌ ΡΠ³Π»Π΅ΡΠΎΠ΄Π°.

Π‘Ρ Π΅ΠΌΠ° ΠΊΠΎΠ½Π²Π΅ΡΡΠ΅ΡΠ° ΠΈ ΠΎΡΠ½ΠΎΠ²Π½ΡΠ΅ ΠΏΠ΅ΡΠΈΠΎΠ΄Ρ ΠΏΠ»Π°Π²ΠΊΠΈ
ΠΠ΅ΡΡΠ΅ΠΌΠ΅ΡΠΎΠ²ΡΠΊΠΈΠΉ ΠΏΡΠΎΡΠ΅ΡΡ ΠΏΡΠ΅Π΄ΡΡΠΌΠ°ΡΡΠΈΠ²Π°Π΅Ρ ΠΏΡΠΎΠ΄ΡΠ²ΠΊΡ ΡΠ°ΡΠΏΠ»Π°Π²Π° Π°ΡΠΌΠΎΡΡΠ΅ΡΠ½ΡΠΌ Π²ΠΎΠ·Π΄ΡΡ ΠΎΠΌ. ΠΠ»Ρ ΡΡΠΈΡ ΡΠ΅Π»Π΅ΠΉ ΠΏΡΠΈΠΌΠ΅Π½ΡΡΡΡΡ ΠΊΠΎΠ½Π²Π΅ΡΡΠ΅ΡΡ, Ρ ΠΊΠΎΡΠΎΡΡΡ Π²Π½ΡΡΡΠ΅Π½Π½ΡΡ ΡΠ°ΡΡΡ ΠΊΠ°ΠΌΠ΅ΡΡ ΡΠ³ΠΎΡΠ°Π½ΠΈΡ Π·Π°ΡΠΈΡΠ΅Π½Π° Π΄ΠΈΠ½Π°ΡΠΎΠ²ΡΠΌ ΠΊΠΈΡΠΏΠΈΡΠΎΠΌ. ΠΠ»Π°Π³ΠΎΠ΄Π°ΡΡ ΡΠ°ΠΊΠΎΠΉ Π·Π°ΡΠΈΡΠ΅ Π±Π΅ΡΡΠ΅ΠΌΠ΅ΡΠΎΠ²ΡΠΊΠΈΠΉ ΡΠΏΠΎΡΠΎΠ± Π½Π°Π·ΡΠ²Π°ΡΡ ΠΊΠΈΡΠ»ΠΎΠΉ ΡΡΡΠ΅ΡΠΎΠ²ΠΊΠΎΠΉ ΠΊΠΎΠ½Π²Π΅ΡΡΠ΅ΡΠ°.
ΠΠ»Π°Π²ΠΊΠ° Π² Π±Π΅ΡΡΠ΅ΠΌΠ΅ΡΠΎΠ²ΡΠΊΠΎΠΌ ΡΡΠ°Π»Π΅ΠΏΠ»Π°Π²ΠΈΠ»ΡΠ½ΠΎΠΌ Π°Π³ΡΠ΅Π³Π°ΡΠ΅ ΠΎΡΡΡΠ΅ΡΡΠ²Π»ΡΠ΅ΡΡΡ ΠΏΡΡΠ΅ΠΌ Π·Π°Π»ΠΈΠ²ΠΊΠΈ ΡΡΠ³ΡΠ½Π° ΠΏΡΠΈ ΡΠ΅ΠΌΠΏΠ΅ΡΠ°ΡΡΡΠ΅ 1250β1300Β°Π‘. Π‘Π»Π΅Π΄ΡΠ΅Ρ Π·Π°ΠΌΠ΅ΡΠΈΡΡ, ΡΡΠΎ Π΄Π»Ρ Π²ΡΠΏΠ»Π°Π²ΠΊΠΈ Π±Π΅ΡΡΠ΅ΠΌΠ΅ΡΠΎΠ²ΡΠΊΠΈΡ ΡΡΠ³ΡΠ½ΠΎΠ² ΡΡΠ΅Π±ΡΡΡΡΡ ΠΆΠ΅Π»Π΅Π·Π½ΡΠ΅ ΡΡΠ΄Ρ Ρ Π½ΠΈΠ·ΠΊΠΈΠΌ ΡΠΎΠ΄Π΅ΡΠΆΠ°Π½ΠΈΠ΅ΠΌ ΡΠ΅ΡΡ ΠΈ ΡΠΎΡΡΠΎΡΠ°.
ΠΠ°Π»ΠΈΡΡΠΉ ΡΡΠ³ΡΠ½ ΠΏΡΠΎΠ΄ΡΠ²Π°ΡΡ Π²ΠΎΠ·Π΄ΡΡ ΠΎΠΌ, Π² ΡΠ΅Π·ΡΠ»ΡΡΠ°ΡΠ΅ ΡΠ΅Π³ΠΎ ΠΏΡΠΎΠΈΡΡ ΠΎΠ΄ΠΈΡ ΠΎΠΊΠΈΡΠ»Π΅Π½ΠΈΠ΅ ΡΠ³Π»Π΅ΡΠΎΠ΄Π°, ΠΌΠ°ΡΠ³Π°Π½ΡΠ° ΠΈ ΠΊΡΠ΅ΠΌΠ½ΠΈΡ. ΠΡΠΈ ΠΎΠΊΠΈΡΠ»Π΅Π½ΠΈΠΈ ΠΎΠ±ΡΠ°Π·ΡΡΡΡΡ ΠΎΠΊΡΠΈΠ΄Ρ, ΡΠΎΡΠΌΠΈΡΡΡΡΠΈΠ΅ ΠΊΠΈΡΠ»ΡΠΉ ΡΠ»Π°ΠΊ. ΠΡΠΎΠ΄ΡΠ²ΠΊΡ Π²ΠΎΠ·Π΄ΡΡ ΠΎΠΌ Π·Π°ΠΊΠ°Π½ΡΠΈΠ²Π°ΡΡ ΠΏΠΎΡΠ»Π΅ ΡΠΎΠ³ΠΎ, ΠΊΠ°ΠΊ ΡΠ³Π»Π΅ΡΠΎΠ΄ ΠΎΠΊΠΈΡΠ»ΠΈΡΡΡ Π΄ΠΎ ΡΡΠ΅Π±ΡΠ΅ΠΌΡΡ Π·Π½Π°ΡΠ΅Π½ΠΈΠΉ.
ΠΠ°Π»Π΅Π΅ ΠΌΠ΅ΡΠ°Π»Π» ΡΠ΅ΡΠ΅Π· Π³ΠΎΡΠ»ΠΎΠ²ΠΈΠ½Ρ ΡΠ»ΠΈΠ²Π°ΡΡ Π² ΠΊΠΎΠ²Ρ, ΠΏΠΎΠΏΡΡΠ½ΠΎ Π΅Π³ΠΎ ΠΎΠΊΠΈΡΠ»ΡΡ. Π£ ΡΠ°ΠΊΠΎΠ³ΠΎ ΡΠΏΠΎΡΠΎΠ±Π° ΠΏΡΠΈΡΡΡΡΡΠ²ΡΠ΅Ρ ΠΎΠ΄ΠΈΠ½ ΡΡΡΠ΅ΡΡΠ²Π΅Π½Π½ΡΠΉ Π½Π΅Π΄ΠΎΡΡΠ°ΡΠΎΠΊ, Π·Π°ΠΊΠ»ΡΡΠ°ΡΡΠΈΠΉΡΡ Π² Π½Π΅Π²ΡΡΠΎΠΊΠΎΠΌ ΠΊΠ°ΡΠ΅ΡΡΠ²Π΅ ΠΊΠΎΠ½Π΅ΡΠ½ΠΎΠ³ΠΎ ΠΏΡΠΎΠ΄ΡΠΊΡΠ°, ΠΊΠΎΡΠΎΡΡΠΉ ΠΏΠΎΠ»ΡΡΠ°Π΅ΡΡΡ ΡΠ»ΠΈΡΠΊΠΎΠΌ Ρ ΡΡΠΏΠΊΠΈΠΌ Π·Π° ΡΡΠ΅Ρ Π½Π΅ΠΏΠΎΠ»Π½ΠΎΠ³ΠΎ ΡΠ΄Π°Π»Π΅Π½ΠΈΡ ΡΠ΅ΡΡ ΠΈ ΡΠΎΡΡΠΎΡΠ°.
ΠΡΠΈΠ½ΡΠΈΠΏ ΡΠΎΠΌΠ°ΡΠΎΠ²ΡΠΊΠΎΠ³ΠΎ ΡΠΏΠΎΡΠΎΠ±Π°
Π 1878 Π³ΠΎΠ΄Ρ Π°Π½Π³Π»ΠΈΡΠ°Π½ΠΈΠ½Ρ Π‘.Π. Π’ΠΎΠΌΠ°ΡΡ ΡΠ΄Π°Π»ΠΎΡΡ ΡΡΡΡΠ°Π½ΠΈΡΡ Π³Π»Π°Π²Π½ΡΠΉ Π½Π΅Π΄ΠΎΡΡΠ°ΡΠΎΠΊ Π±Π΅ΡΡΠ΅ΠΌΠ΅ΡΠΎΠ²ΡΠΊΠΎΠ³ΠΎ ΡΠΏΠΎΡΠΎΠ±Π°. ΠΠΈΡΠ»ΡΡ ΡΡΡΠ΅ΡΠΎΠ²ΠΊΡ ΠΊΠΎΠ½Π²Π΅ΡΡΠ΅ΡΠ° ΠΎΠ½ Π·Π°ΠΌΠ΅Π½ΠΈΠ» ΠΎΡΠ½ΠΎΠ²Π½ΠΎΠΉ. ΠΠ½ΡΡΡΠ΅Π½Π½ΠΈΠΉ Π·Π°ΡΠΈΡΠ½ΡΠΉ ΡΠ»ΠΎΠΉ Π² Π²Π°Π½Π½ΠΎΠΉ Π±ΡΠ» Π²ΡΠ»ΠΎΠΆΠ΅Π½ ΡΠΌΠΎΠ»ΠΎΠ΄ΠΎΠ»ΠΎΠΌΠΈΡΠΎΠ²ΡΠΌ ΠΊΠΈΡΠΏΠΈΡΠΎΠΌ. Π ΡΡΠΎΠ±Ρ ΡΠ΄Π°Π»ΠΈΡΡ ΠΈΠ· ΠΌΠ΅ΡΠ°Π»Π»Π° Π±ΠΎΠ»ΡΡΡΡ ΡΠ°ΡΡΡ ΠΏΡΠΈΠΌΠ΅ΡΠ΅ΠΉ, ΠΎΠ½ ΠΏΡΠ΅Π΄Π»ΠΎΠΆΠΈΠ» ΠΈΡΠΏΠΎΠ»ΡΠ·ΠΎΠ²Π°ΡΡ ΠΈΠ·Π²Π΅ΡΡΡ, ΡΡΠ½ΠΊΡΠΈΡ ΠΊΠΎΡΠΎΡΠΎΠΉ Π·Π°ΠΊΠ»ΡΡΠ°Π»Π°ΡΡ Π² ΡΠ²ΡΠ·ΡΠ²Π°Π½ΠΈΠΈ ΡΠΎΡΡΠΎΡΠ°.
Π’ΠΎΠΌΠ°ΡΠΎΠ²ΡΠΊΠΈΠΉ ΠΏΡΠΎΡΠ΅ΡΡ ΠΏΠΎΠ·Π²ΠΎΠ»ΠΈΠ» ΠΏΠ΅ΡΠ΅ΡΠ°Π±Π°ΡΡΠ²Π°ΡΡ ΡΡΠ³ΡΠ½ Ρ Π²ΡΡΠΎΠΊΠΈΠΌ ΡΠΎΠ΄Π΅ΡΠΆΠ°Π½ΠΈΠ΅ΠΌ ΡΠΎΡΡΠΎΡΠ°. ΠΠΎΡΡΠΎΠΌΡ Π½Π°ΠΈΠ±ΠΎΠ»ΡΡΠ΅Π΅ ΡΠ°ΡΠΏΡΠΎΡΡΡΠ°Π½Π΅Π½ΠΈΠ΅ Π΄Π°Π½Π½ΡΠΉ ΡΠΏΠΎΡΠΎΠ± ΠΏΠΎΠ»ΡΡΠΈΠ» Π² ΡΡΡΠ°Π½Π°Ρ
, Π³Π΄Π΅ ΠΆΠ΅Π»Π΅Π·Π½ΡΠ΅ ΡΡΠ΄Ρ ΡΠΎΠ΄Π΅ΡΠΆΠ°Ρ ΠΌΠ½ΠΎΠ³ΠΎ ΡΠΎΡΡΠΎΡΠ°. ΠΠΎ Π²ΡΠ΅ΠΌ ΠΎΡΡΠ°Π»ΡΠ½ΠΎΠΌ ΠΌΠ΅ΡΠΎΠ΄, ΠΈΠ·ΠΎΠ±ΡΠ΅ΡΠ΅Π½Π½ΡΠΉ Π’ΠΎΠΌΠ°ΡΠΎΠΌ, ΠΌΠ°Π»ΠΎ ΡΠ΅ΠΌ ΠΎΡΠ»ΠΈΡΠ°Π΅ΡΡΡ ΠΎΡ ΠΏΡΠ΅Π΄Π»ΠΎΠΆΠ΅Π½Π½ΠΎΠ³ΠΎ ΠΠ΅ΡΡΠ΅ΠΌΠ΅ΡΠΎΠΌ:
- ΠΈ Π² ΡΠΎΠΌ, ΠΈ Π² Π΄ΡΡΠ³ΠΎΠΌ ΡΠ»ΡΡΠ°Π΅ ΠΈΡΠΏΠΎΠ»ΡΠ·ΡΠ΅ΡΡΡ ΡΡΠ°Π»Π΅ΠΏΠ»Π°Π²ΠΈΠ»ΡΠ½ΡΠΉ Π°Π³ΡΠ΅Π³Π°Ρ, Π² ΠΊΠΎΡΠΎΡΡΠΉ ΡΡΠ³ΡΠ½ ΠΏΠΎΠ΄Π°Π΅ΡΡΡ ΡΠ²Π΅ΡΡ Ρ ΡΠ΅ΡΠ΅Π· ΠΎΡΠ²Π΅ΡΡΡΠΈΠ΅ Π² Π³ΠΎΡΠ»ΠΎΠ²ΠΈΠ½Π΅;
- ΡΠ΅ΡΠ΅Π· ΡΡΠΎ ΠΆΠ΅ ΠΎΡΠ²Π΅ΡΡΡΠΈΠ΅ ΠΏΡΠΎΠΈΠ·Π²ΠΎΠ΄ΠΈΡΡΡ Π²ΡΠΏΡΡΠΊ ΡΡΠ°Π»ΠΈ.
- ΡΠ½ΠΈΠ·Ρ ΡΡΠ°Π»Π΅ΠΏΠ»Π°Π²ΠΈΠ»ΡΠ½ΡΠΉ Π°Π³ΡΠ΅Π³Π°Ρ ΡΠ½Π°Π±ΠΆΠ΅Π½ ΡΡΠ΅ΠΌΠ½ΡΠΌ Π΄Π½ΠΈΡΠ΅ΠΌ, ΡΡΠΎ ΠΏΠΎΠ·Π²ΠΎΠ»ΡΠ΅Ρ Π·Π°ΠΌΠ΅Π½ΡΡΡ Π΅Π³ΠΎ ΠΏΠΎ ΠΌΠ΅ΡΠ΅ Π²ΡΡΠ°Π±ΠΎΡΠΊΠΈ ΠΎΠΏΡΠ΅Π΄Π΅Π»Π΅Π½Π½ΠΎΠ³ΠΎ ΡΡΠΎΠΊΠ° ΡΠ»ΡΠΆΠ±Ρ;
- Π΄ΡΡΡΠ΅ Π² ΠΏΠΎΠ»ΠΎΡΡΡ ΡΡΠ°Π»Π΅ΠΏΠ»Π°Π²ΠΈΡΠ΅Π»Ρ ΠΏΠΎΡΡΡΠΏΠ°Π΅Ρ ΡΠ΅ΡΠ΅Π· ΡΠΏΠ΅ΡΠΈΠ°Π»ΡΠ½ΡΠ΅ ΡΠΎΠΏΠ»Π°, ΡΠ°ΡΠΏΠΎΠ»ΠΎΠΆΠ΅Π½Π½ΡΠ΅ Π² ΡΡΡΠ΅ΡΠΎΠ²ΠΊΠ΅ Π΄Π½ΠΈΡΠ°.
ΠΠ°ΠΊ ΡΠΆΠ΅ Π³ΠΎΠ²ΠΎΡΠΈΠ»ΠΎΡΡ Π²ΡΡΠ΅, ΡΠ»ΠΈΠ² ΡΡΠ°Π»ΠΈ ΠΏΡΠΎΠΈΠ·Π²ΠΎΠ΄ΠΈΡΡΡ ΡΠ΅ΡΠ΅Π· ΠΎΡΠ²Π΅ΡΡΡΠΈΠ΅ Π² Π³ΠΎΡΠ»ΠΎΠ²ΠΈΠ½Π΅. ΠΠ΅ΡΠ΅Π²Π΅ΡΠ½ΡΡΡ ΠΌΠ½ΠΎΠ³ΠΎΡΠΎΠ½Π½ΡΠΉ Π°Π³ΡΠ΅Π³Π°Ρ ΠΏΠΎΠ·Π²ΠΎΠ»ΡΡΡ ΡΠ°ΠΏΡΡ Π² ΡΠΈΠ»ΠΈΠ½Π΄ΡΠΈΡΠ΅ΡΠΊΠΎΠΉ ΡΠ°ΡΡΠΈ ΠΊΠΎΠ½Π²Π΅ΡΡΠ΅ΡΠ°. ΠΡΠΈ ΡΠΎΠΌΠ°ΡΠΎΠ²ΡΠΊΠΎΠΌ ΠΏΡΠΎΡΠ΅ΡΡΠ΅ Π² ΡΡΠ°Π»Π΅ΠΏΠ»Π°Π²ΠΈΡΠ΅Π»Ρ Π·Π°Π³ΡΡΠΆΠ°ΡΡ ΠΈΠ·Π²Π΅ΡΡΡ, ΠΏΠΎΠ·Π²ΠΎΠ»ΡΡΡΡΡ ΠΏΠΎΠ»ΡΡΠΈΡΡ ΠΎΡΠ½ΠΎΠ²Π½ΠΎΠΉ ΡΠ»Π°ΠΊ. ΠΠ°Π»Π΅Π΅ ΡΡΠ΄Π° ΠΆΠ΅ Π·Π°Π»ΠΈΠ²Π°ΡΡ Π²ΡΡΠΎΠΊΠΎΡΠΎΡΡΠΎΡΠΈΡΡΡΠΉ ΡΡΠ³ΡΠ½, Π½Π°Π³ΡΠ΅ΡΡΠΉ Π΄ΠΎ 1200β1250Β°Π‘ ΠΈ ΠΏΠΎΠ΄Π°ΡΡ Π΄ΡΡΡΠ΅. ΠΡΠΈ ΠΏΠΎΠ΄Π°ΡΠ΅ Π΄ΡΡΡΡ ΠΏΡΠΎΠΈΡΡ ΠΎΠ΄ΠΈΡ ΠΎΠΊΠΈΡΠ»Π΅Π½ΠΈΠ΅ ΠΊΡΠ΅ΠΌΠ½ΠΈΡ, ΠΌΠ°ΡΠ³Π°Π½ΡΠ° ΠΈ ΡΠ³Π»Π΅ΡΠΎΠ΄Π°. Π ΠΎΡΠ½ΠΎΠ²Π½ΠΎΠΉ ΡΠ»Π°ΠΊ ΡΠ΄Π°Π»ΡΡΡΡΡ ΡΠ΅ΡΠ° ΠΈ ΡΠΎΡΡΠΎΡ. ΠΡΠΎΠ΄ΡΠ²ΠΊΠ° Π·Π°Π²Π΅ΡΡΠ°Π΅ΡΡΡ ΡΠΎΠ³Π΄Π°, ΠΊΠΎΠ³Π΄Π° ΡΠΎΠ΄Π΅ΡΠΆΠ°Π½ΠΈΠ΅ ΡΠΎΡΡΠΎΡΠ° ΡΠ½ΠΈΠ·ΠΈΡΡΡ Π΄ΠΎ ΠΎΠΏΡΠ΅Π΄Π΅Π»Π΅Π½Π½ΡΡ ΠΏΠΎΠΊΠ°Π·Π°ΡΠ΅Π»Π΅ΠΉ. ΠΠΊΠΎΠ½ΡΠ°ΡΠ΅Π»ΡΠ½ΡΠΌ ΡΡΠ°ΠΏΠΎΠΌ, ΠΊΠ°ΠΊ ΠΈ Π² Π±Π΅ΡΡΠ΅ΠΌΠ΅ΡΠΎΠ²ΡΠΊΠΎΠΌ ΠΏΡΠΎΡΠ΅ΡΡΠ΅, ΡΠ²Π»ΡΠ΅ΡΡΡ Π²ΡΠΏΡΡΠΊ ΠΌΠ΅ΡΠ°Π»Π»Π° Ρ ΠΏΠΎΡΠ»Π΅Π΄ΡΡΡΠΈΠΌ ΡΠ°ΡΠΊΠΈΡΠ»Π΅Π½ΠΈΠ΅ΠΌ.
ΠΡΠΈΠ½ΡΠΈΠΏ ΡΠ°Π±ΠΎΡΡ ΠΊΠΈΡΠ»ΠΎΡΠΎΠ΄Π½ΠΎΠ³ΠΎ ΠΊΠΎΠ½Π²Π΅ΡΡΠ΅ΡΠ°
ΠΠΏΠ΅ΡΠ²ΡΠ΅ ΠΊΠΈΡΠ»ΠΎΡΠΎΠ΄Π½ΠΎΠ΅ Π΄ΡΡΡΠ΅ Π±ΡΠ»ΠΎ Π·Π°ΠΏΠ°ΡΠ΅Π½ΡΠΎΠ²Π°Π½ΠΎ Π. ΠΠ΅ΡΡΠ΅ΠΌΠ΅ΡΠΎΠΌ. ΠΠ΄Π½Π°ΠΊΠΎ Π² ΡΠ΅ΡΠ΅Π½ΠΈΠ΅ ΠΏΡΠΎΠ΄ΠΎΠ»ΠΆΠΈΡΠ΅Π»ΡΠ½ΠΎΠ³ΠΎ Π²ΡΠ΅ΠΌΠ΅Π½ΠΈ ΠΊΠΈΡΠ»ΠΎΡΠΎΠ΄Π½ΠΎ-ΠΊΠΎΠ½Π²Π΅ΡΡΠ΅ΡΠ½ΡΠΉ ΠΏΡΠΎΡΠ΅ΡΡ Π½Π΅ ΠΏΡΠΈΠΌΠ΅Π½ΡΠ»ΡΡ, Π² ΡΠ²ΡΠ·ΠΈ Ρ ΠΎΡΡΡΡΡΡΠ²ΠΈΠ΅ΠΌ ΠΌΠ°ΡΡΠΎΠ²ΠΎΠ³ΠΎ ΠΏΡΠΎΠΈΠ·Π²ΠΎΠ΄ΡΡΠ²Π° ΠΊΠΈΡΠ»ΠΎΡΠΎΠ΄Π°. ΠΠ΅ΡΠ²ΡΠ΅ ΠΎΠΏΡΡΡ ΠΏΠΎ ΠΏΡΠΎΠ΄ΡΠ²ΠΊΠ΅ ΠΊΠΈΡΠ»ΠΎΡΠΎΠ΄ΠΎΠΌ ΡΡΠ°Π»ΠΈ Π²ΠΎΠ·ΠΌΠΎΠΆΠ½ΡΠΌΠΈ Π² Π½Π°ΡΠ°Π»Π΅ ΡΠΎΡΠΎΠΊΠΎΠ²ΡΡ Π³ΠΎΠ΄ΠΎΠ² ΠΏΡΠΎΡΠ»ΠΎΠ³ΠΎ ΡΡΠΎΠ»Π΅ΡΠΈΡ.
Π£ΡΡΡΠΎΠΉΡΡΠ²ΠΎ ΠΊΠΈΡΠ»ΠΎΡΠΎΠ΄Π½ΠΎΠ³ΠΎ ΠΊΠΎΠ½Π²Π΅ΡΡΠ΅ΡΠ° ΠΎΡΡΠ°Π»ΠΎΡΡ ΠΏΡΠ΅ΠΆΠ½ΠΈΠΌ:
- ΠΊΠ°ΠΌΠ΅ΡΠ° ΡΠ³ΠΎΡΠ°Π½ΠΈΡ ΠΈΠ·Π½ΡΡΡΠΈ Π·Π°ΡΠΈΡΠ΅Π½Π° ΠΎΡΠ½ΠΎΠ²Π½ΠΎΠΉ ΡΡΡΠ΅ΡΠΎΠ²ΠΊΠΎΠΉ;
- ΠΎΠ΄Π½Π°ΠΊΠΎ Π²ΠΌΠ΅ΡΡΠΎ Π²ΠΎΠ·Π΄ΡΡ Π° Π² Π½Π΅ΠΌ ΠΏΡΠΈΠΌΠ΅Π½ΡΠ΅ΡΡΡ ΠΏΡΠΎΠ΄ΡΠ²ΠΊΠ° ΠΊΠΈΡΠ»ΠΎΡΠΎΠ΄ΠΎΠΌ;
- ΠΏΠΎΠ΄Π°ΡΠ° ΠΊΠΈΡΠ»ΠΎΡΠΎΠ΄Π° ΠΎΡΡΡΠ΅ΡΡΠ²Π»ΡΠ΅ΡΡΡ ΡΠ΅ΡΠ΅Π· Π²ΠΎΠ΄ΠΎΠΎΡ Π»Π°ΠΆΠ΄Π°Π΅ΠΌΡΠ΅ ΡΠΎΠΏΠ»Π°.
ΠΠ° ΡΠ΅ΡΡΠΈΡΠΎΡΠΈΠΈ Π ΠΎΡΡΠΈΠΈ ΠΏΡΠΈΠΌΠ΅Π½ΡΡΡΡΡ ΡΡΠ°Π»Π΅ΠΏΠ»Π°Π²ΠΈΡΠ΅Π»ΠΈ Ρ Π²Π΅ΡΡ Π½Π΅ΠΉ ΠΏΠΎΠ΄Π°ΡΠ΅ΠΉ ΠΊΠΈΡΠ»ΠΎΡΠΎΠ΄Π°.
ΠΡΠΎΠ±Π΅Π½Π½ΠΎΡΡΡΡ ΠΊΠΎΠ½Π²Π΅ΡΡΠ΅ΡΠ½ΠΎΠ³ΠΎ ΡΠΏΠΎΡΠΎΠ±Π° Ρ ΠΊΠΈΡΠ»ΠΎΡΠΎΠ΄Π½ΠΎΠΉ ΠΏΡΠΎΠ΄ΡΠ²ΠΊΠΎΠΉ ΡΠ²Π»ΡΠ΅ΡΡΡ ΡΠΊΠΎΡΠΎΡΠ΅ΡΠ½ΠΎΡΡΡ. ΠΠ΅ΡΡ ΠΏΡΠΎΡΠ΅ΡΡ ΡΠ°ΡΠΏΠ»Π°Π²Π»Π΅Π½ΠΈΡ ΠΌΠ΅ΡΠ°Π»Π»Π° Π·Π°Π½ΠΈΠΌΠ°Π΅Ρ Π΄Π΅ΡΡΡΠΊΠΈ ΠΌΠΈΠ½ΡΡ. ΠΠ΄Π½Π°ΠΊΠΎ Π²ΠΎ Π²ΡΠ΅ΠΌΡ ΡΠ°Π±ΠΎΡΡ ΡΡΠ΅Π±ΡΠ΅ΡΡΡ ΡΡΠ°ΡΠ΅Π»ΡΠ½ΠΎ ΠΎΡΡΠ»Π΅ΠΆΠΈΠ²Π°ΡΡ ΡΠΎΠ΄Π΅ΡΠΆΠ°Π½ΠΈΠ΅ Π² ΡΡΠ³ΡΠ½Π΅ ΡΠ³Π»Π΅ΡΠΎΠ΄Π°, ΡΠ΅ΠΌΠΏΠ΅ΡΠ°ΡΡΡΡ Π΅Π³ΠΎ ΡΠ°ΡΠΏΠ»Π°Π²Π° ΠΈ ΠΏΡΠΎΡΠΈΠ΅ ΠΏΠ°ΡΠ°ΠΌΠ΅ΡΡΡ, ΡΡΠΎΠ±Ρ Π²ΠΎΠ²ΡΠ΅ΠΌΡ ΠΏΡΠ΅ΠΊΡΠ°ΡΠΈΡΡ ΠΏΡΠΎΠ΄ΡΠ²ΠΊΡ.
ΠΡΠΎΡΠ΅ΡΡ ΡΡΠ°Π»Π΅ΠΏΠ»Π°Π²ΠΈΠ»ΡΠ½ΠΎΠ³ΠΎ ΠΏΡΠΎΠΈΠ·Π²ΠΎΠ΄ΡΡΠ²Π° ΡΠΏΡΠΎΡΡΠΈΠ»ΡΡ, ΠΊΠΎΠ³Π΄Π° ΠΊΠΈΡΠ»ΠΎΡΠΎΠ΄Π½ΡΠ΅ ΠΊΠΎΠ½Π²Π΅ΡΡΠ΅ΡΡ ΠΎΡΠ½Π°ΡΡΠΈΠ»ΠΈ Π°Π²ΡΠΎΠΌΠ°ΡΠΈΡΠ΅ΡΠΊΠΈΠΌΠΈ ΡΠΈΡΡΠ΅ΠΌΠ°ΠΌΠΈ, ΡΡΠΎΠ²Π΅ΡΡΠ΅Π½ΡΡΠ²ΠΎΠ²Π°Π»ΠΈ Π»Π°Π±ΠΎΡΠ°ΡΠΎΡΠ½ΡΡ ΡΠ΅Ρ Π½ΠΈΠΊΡ ΠΈ ΠΈΠ·ΠΌΠ΅ΡΠΈΡΠ΅Π»ΡΠ½ΡΠ΅ ΠΏΡΠΈΠ±ΠΎΡΡ. Π£ΡΠΎΠ²Π΅ΡΡΠ΅Π½ΡΡΠ²ΠΎΠ²Π°Π½ΠΈΠ΅ ΠΊΠΈΡΠ»ΠΎΡΠΎΠ΄Π½ΠΎ-ΠΊΠΎΠ½Π²Π΅ΡΡΠ΅ΡΠ½ΠΎΠ³ΠΎ ΠΏΡΠΎΡΠ΅ΡΡΠ° ΠΏΠΎΠ·Π²ΠΎΠ»ΠΈΠ»ΠΎ ΠΏΠΎΠ²ΡΡΠΈΡΡ ΠΏΡΠΎΠΈΠ·Π²ΠΎΠ΄ΠΈΡΠ΅Π»ΡΠ½ΠΎΡΡΡ, ΡΠ½ΠΈΠ·ΠΈΡΡ ΡΠ΅Π±Π΅ΡΡΠΎΠΈΠΌΠΎΡΡΡ ΠΌΠ΅ΡΠ°Π»Π»Π° ΠΈ ΠΏΠΎΠ²ΡΡΠΈΡΡ Π΅Π³ΠΎ ΠΊΠ°ΡΠ΅ΡΡΠ²ΠΎ.
Π‘ΠΎΠ²ΡΠ΅ΠΌΠ΅Π½Π½ΡΠ΅ ΠΊΠΈΡΠ»ΠΎΡΠΎΠ΄Π½ΡΠ΅ ΠΊΠΎΠ½Π²Π΅ΡΡΠ΅ΡΡ ΠΌΠΎΠ³ΡΡ ΡΠ°Π±ΠΎΡΠ°ΡΡ Π² ΡΡΠ΅Ρ ΠΎΡΠ½ΠΎΠ²Π½ΡΡ ΡΠ΅ΠΆΠΈΠΌΠ°Ρ :
- Ρ ΠΏΠΎΠ»Π½ΡΠΌ Π΄ΠΎΠΆΠΈΠ³Π°Π½ΠΈΠ΅ΠΌ ΠΎΠΊΠΈΡΠΈ ΡΠ³Π»Π΅ΡΠΎΠ΄Π°;
- Ρ ΡΠ°ΡΡΠΈΡΠ½ΡΠΌ Π΄ΠΎΠΆΠΈΠ³Π°Π½ΠΈΠ΅ΠΌ ΠΠ‘;
- Π±Π΅Π· Π΄ΠΎΠΆΠΈΠ³Π°Π½ΠΈΡ ΠΠ‘.

Π‘Ρ Π΅ΠΌΠ° ΠΏΠΎΠ»ΡΡΠ΅Π½ΠΈΡ ΡΡΠ°Π»ΠΈ Π² ΠΊΠΈΡΠ»ΠΎΡΠΎΠ΄Π½ΠΎΠΌ ΠΊΠΎΠ½Π²Π΅ΡΡΠ΅ΡΠ΅
ΠΠ½ΠΈ ΠΏΠΎΠ·Π²ΠΎΠ»ΡΡΡ ΠΏΡΠΎΠΈΠ·Π²ΠΎΠ΄ΠΈΡΡ ΡΡΠ°Π»Ρ ΠΈΠ· ΡΡΠ³ΡΠ½Π° ΡΠ°Π·Π»ΠΈΡΠ½ΠΎΠ³ΠΎ ΡΠΎΡΡΠ°Π²Π°.
ΠΠΈΡΠ»ΠΎΡΠΎΠ΄Π½ΡΠΉ ΠΊΠΎΠ½Π²Π΅ΡΡΠ΅Ρ β ΠΎΠΏΠΈΡΠ°Π½ΠΈΠ΅ ΠΏΡΠΎΡΠ΅ΡΡΠ° ΠΏΠ»Π°Π²ΠΊΠΈ
ΠΠΈΡΠ»ΠΎΡΠΎΠ΄Π½ΡΠΉ ΠΊΠΎΠ½Π²Π΅ΡΡΠ΅Ρ β ΡΡΠΎ ΡΡΠ°Π»ΡΠ½ΠΎΠΉ ΡΠΎΡΡΠ΄ Π³ΡΡΡΠ΅Π²ΠΈΠ΄Π½ΠΎΠΉ ΡΠΎΡΠΌΡ. ΠΠ³ΠΎ Π²Π½ΡΡΡΠ΅Π½Π½ΡΡ ΡΠ°ΡΡΡ Π·Π°ΡΠΈΡΠ΅Π½Π° ΡΠΌΠΎΠ»ΠΎΠ΄ΠΎΠ»ΠΎΠΌΠΈΡΠΎΠ²ΡΠΌ (ΠΎΡΠ½ΠΎΠ²Π½ΡΠΌ) ΠΊΠΈΡΠΏΠΈΡΠΎΠΌ. ΠΠΌΠ΅ΡΡΠΈΠΌΠΎΡΡΡ ΡΡΠ°Π»Π΅ΠΏΠ»Π°Π²ΠΈΠ»ΡΠ½ΠΎΠ³ΠΎ Π°Π³ΡΠ΅Π³Π°ΡΠ° Π²Π°ΡΡΠΈΡΡΠ΅ΡΡΡ ΠΎΡ 50 Π΄ΠΎ 350 ΡΠΎΠ½Π½. Π‘ΠΎΡΡΠ΄ ΡΠ°ΡΠΏΠ»ΠΎΠΆΠ΅Π½ Π½Π° ΡΠ°ΠΏΡΠ°Ρ ΠΈ ΡΠΏΠΎΡΠΎΠ±Π΅Π½ ΠΏΠΎΠ²ΠΎΡΠ°ΡΠΈΠ²Π°ΡΡΡΡ Π²ΠΎΠΊΡΡΠ³ Π³ΠΎΡΠΈΠ·ΠΎΠ½ΡΠ°Π»ΡΠ½ΠΎΠΉ ΠΎΡΠΈ, ΡΡΠΎ ΠΏΠΎΠ·Π²ΠΎΠ»ΡΠ΅Ρ Π±Π΅ΡΠΏΡΠ΅ΠΏΡΡΡΡΠ²Π΅Π½Π½ΠΎ Π·Π°Π»ΠΈΠ²Π°ΡΡ Π² Π½Π΅Π³ΠΎ ΡΡΠ³ΡΠ½, Π·Π°ΠΊΠ»Π°Π΄ΡΠ²Π°ΡΡ Π΄ΡΡΠ³ΠΈΠ΅ Π΄ΠΎΠ±Π°Π²ΠΊΠΈ ΠΈ ΡΠ»ΠΈΠ²Π°ΡΡ ΠΌΠ΅ΡΠ°Π»Π» ΡΠΎ ΡΠ»Π°ΠΊΠΎΠΌ.
Π§ΡΠΎΠ±Ρ ΠΏΠΎΠ»ΡΡΠΈΡΡ ΠΊΠΎΠ½Π΅ΡΠ½ΡΠΉ ΠΏΡΠΎΠ΄ΡΠΊΡ, Π² ΠΊΠΎΠ½Π²Π΅ΡΡΠ΅Ρ Π·Π°Π»ΠΈΠ²Π°Π΅ΡΡΡ Π½Π΅ ΡΠΎΠ»ΡΠΊΠΎ ΡΡΠ³ΡΠ½, Π½ΠΎ ΠΈ Π·Π°ΠΊΠ»Π°Π΄ΡΠ²Π°ΡΡ Π΄ΠΎΠ±Π°Π²ΠΊΠΈ. Π Π½ΠΈΠΌ ΠΎΡΠ½ΠΎΡΡΡΡΡ:
- Π»ΠΎΠΌ ΠΌΠ΅ΡΠ°Π»Π»Π°;
- ΡΠ»Π°ΠΊΠΎΠΎΠ±ΡΠ°Π·ΡΡΡΠΈΠ΅ ΠΌΠ°ΡΠ΅ΡΠΈΠ°Π»Ρ (ΠΆΠ΅Π»Π΅Π·Π½Π°Ρ ΡΡΠ΄Π°, ΠΈΠ·Π²Π΅ΡΡΡ, ΠΏΠΎΠ»Π΅Π²ΠΎΠΉ ΡΠΏΠ°Ρ, Π±ΠΎΠΊΡΠΈΡΡ).
ΠΠΎΠ½Π²Π΅ΡΡΠ΅ΡΠ½ΡΠΉ ΡΠΏΠΎΡΠΎΠ± Ρ ΠΊΠΈΡΠ»ΠΎΡΠΎΠ΄Π½ΠΎΠΉ ΠΏΡΠΎΠ΄ΡΠ²ΠΊΠΎΠΉ ΠΏΡΠ΅Π΄ΡΡΠΌΠ°ΡΡΠΈΠ²Π°Π΅Ρ Π·Π°Π»ΠΈΠ²ΠΊΡ Π² ΠΊΠΎΠ½Π²Π΅ΡΡΠ΅Ρ ΡΡΠ³ΡΠ½Π°, Π½Π°Π³ΡΠ΅ΡΠΎΠ³ΠΎ Π΄ΠΎ 1250β1400Β°Π‘. Π£ΡΡΠ°Π½ΠΎΠ²ΠΈΠ² ΠΊΠΎΠ½Π²Π΅ΡΡΠ΅Ρ Π² Π²Π΅ΡΡΠΈΠΊΠ°Π»ΡΠ½ΠΎΠ΅ ΠΏΠΎΠ»ΠΎΠΆΠ΅Π½ΠΈΠ΅, Π² Π½Π΅Π³ΠΎ ΠΏΠΎΠ΄Π°ΡΡ ΠΊΠΈΡΠ»ΠΎΡΠΎΠ΄. ΠΠ°ΠΊ ΡΠΎΠ»ΡΠΊΠΎ Π½Π°ΡΠ°Π»Π°ΡΡ ΠΏΡΠΎΠ΄ΡΠ²ΠΊΠ°, Π² ΡΠ°ΡΠΏΠ»Π°Π²Π»Π΅Π½Π½ΡΠΉ ΡΡΠ³ΡΠ½ Π²Π²ΠΎΠ΄ΡΡ ΠΎΡΡΠ°Π»ΡΠ½ΡΠ΅ ΠΊΠΎΠΌΠΏΠΎΠ½Π΅Π½ΡΡ, Π²Ρ ΠΎΠ΄ΡΡΠΈΠ΅ Π² ΡΠΎΡΡΠ°Π² ΡΠ»Π°ΠΊΠ°. ΠΠ΅ΡΠ΅ΠΌΠ΅ΡΠΈΠ²Π°Π½ΠΈΠ΅ ΡΡΠ³ΡΠ½Π° ΡΠΎ ΡΠ»Π°ΠΊΠΎΠΌ ΠΎΡΡΡΠ΅ΡΡΠ²Π»ΡΠ΅ΡΡΡ ΠΏΠΎΠ΄ Π΄Π΅ΠΉΡΡΠ²ΠΈΠ΅ΠΌ ΠΏΡΠΎΠ΄ΡΠ²ΠΊΠΈ.
Π’Π°ΠΊ ΠΊΠ°ΠΊ ΠΊΠΎΠ½ΡΠ΅Π½ΡΡΠ°ΡΠΈΡ ΡΡΠ³ΡΠ½Π° Π³ΠΎΡΠ°Π·Π΄ΠΎ Π²ΡΡΠ΅, ΡΠ΅ΠΌ ΠΏΡΠΈΠΌΠ΅ΡΠ΅ΠΉ, Π² ΠΏΡΠΎΡΠ΅ΡΡΠ΅ ΠΏΡΠΎΠ΄ΡΠ²ΠΊΠΈ ΠΏΡΠΎΠΈΡΡ ΠΎΠ΄ΠΈΡ ΠΎΠ±ΡΠ°Π·ΠΎΠ²Π°Π½ΠΈΠ΅ ΠΎΠΊΡΠΈΠ΄Π° ΠΆΠ΅Π»Π΅Π·Π°, ΠΊΠΎΡΠΎΡΡΠΉ ΡΠ°ΡΡΠ²ΠΎΡΡΡΡΡ, ΠΎΠ±ΠΎΠ³Π°ΡΠ°Π΅Ρ ΠΌΠ΅ΡΠ°Π»Π» ΠΊΠΈΡΠ»ΠΎΡΠΎΠ΄ΠΎΠΌ. ΠΠΌΠ΅Π½Π½ΠΎ ΡΠ°ΡΡΠ²ΠΎΡΠ΅Π½Π½ΡΠΉ ΠΊΠΈΡΠ»ΠΎΡΠΎΠ΄ ΡΠΏΠΎΡΠΎΠ±ΡΡΠ²ΡΠ΅Ρ ΡΠΌΠ΅Π½ΡΡΠ΅Π½ΠΈΡ Π² ΠΌΠ΅ΡΠ°Π»Π»Π΅ ΠΊΠΎΠ½ΡΠ΅Π½ΡΡΠ°ΡΠΈΠΈ ΠΊΡΠ΅ΠΌΠ½ΠΈΡ, ΡΠ³Π»Π΅ΡΠΎΠ΄Π° ΠΈ ΠΌΠ°ΡΠ³Π°Π½ΡΠ°. Π ΠΊΠΎΠ³Π΄Π° ΠΏΡΠΈΠΌΠ΅ΡΠΈ ΠΎΠΊΠΈΡΠ»ΡΡΡΡΡ, Π²ΡΠ΄Π΅Π»ΡΠ΅ΡΡΡ ΠΏΠΎΠ»Π΅Π·Π½ΠΎΠ΅ ΡΠ΅ΠΏΠ»ΠΎ.
ΠΡΠΎΠ±Π΅Π½Π½ΠΎΡΡΡΡ ΠΎΡΠ½ΠΎΠ²Π½ΠΎΠ³ΠΎ ΡΠ»Π°ΠΊΠ° ΡΠ²Π»ΡΠ΅ΡΡΡ Π±ΠΎΠ»ΡΡΠΎΠ΅ ΡΠΎΠ΄Π΅ΡΠΆΠ°Π½ΠΈΠ΅ ΠΎΠΊΡΠΈΠ΄Π° ΠΊΠ°Π»ΡΡΠΈΡ ΠΈ ΠΎΠΊΡΠΈΠ΄Π° ΠΆΠ΅Π»Π΅Π·Π°, ΠΊΠΎΡΠΎΡΡΠ΅ Π² Π½Π°ΡΠ°Π»Π΅ ΠΏΡΠΎΠ΄ΡΠ²ΠΊΠΈ ΡΠΏΠΎΡΠΎΠ±ΡΡΠ²ΡΡΡ ΡΠ΄Π°Π»Π΅Π½ΠΈΡ ΡΠΎΡΡΠΎΡΠ°. ΠΡΠ»ΠΈ ΠΆΠ΅ ΡΠΎΠ΄Π΅ΡΠΆΠ°Π½ΠΈΠ΅ ΡΠΎΡΡΠΎΡΠ° ΠΏΡΠ΅Π²ΡΡΠ°Π΅Ρ ΡΡΠ΅Π±ΡΠ΅ΠΌΡΠΉ ΠΏΠΎΠΊΠ°Π·Π°ΡΠ΅Π»Ρ, ΡΠ»Π°ΠΊ ΡΠ»ΠΈΠ²Π°ΡΡ ΠΈ Π½Π°Π²ΠΎΠ΄ΡΡ Π½ΠΎΠ²ΡΠΉ. ΠΡΠΎΠ΄ΡΠ²ΠΊΡ ΠΊΠΈΡΠ»ΠΎΡΠΎΠ΄ΠΎΠΌ Π·Π°ΠΊΠ°Π½ΡΠΈΠ²Π°ΡΡ, ΠΊΠΎΠ³Π΄Π° ΡΠΎΠ΄Π΅ΡΠΆΠ°Π½ΠΈΠ΅ ΡΠ³Π»Π΅ΡΠΎΠ΄Π° Π² ΠΊΠΎΠ½Π΅ΡΠ½ΠΎΠΌ ΠΏΡΠΎΠ΄ΡΠΊΡΠ΅ ΡΠΎΠΎΡΠ²Π΅ΡΡΡΠ²ΡΠ΅Ρ ΠΎΠΏΡΠ΅Π΄Π΅Π»Π΅Π½Π½ΠΎΠΌΡ ΠΏΠ°ΡΠ°ΠΌΠ΅ΡΡΡ. ΠΠΎΡΠ»Π΅ ΡΡΠΎΠ³ΠΎ ΠΊΠΎΠ½Π²Π΅ΡΡΠ΅Ρ ΠΏΠ΅ΡΠ΅Π²ΠΎΡΠ°ΡΠΈΠ²Π°ΡΡ ΠΈ ΠΏΡΠΎΠΈΠ·Π²ΠΎΠ΄ΡΡ ΡΠ»ΠΈΠ² ΡΡΠ°Π»ΠΈ Π² ΠΊΠΎΠ²Ρ, ΠΊΡΠ΄Π° Π΄ΠΎΠ±Π°Π²Π»ΡΡΡ ΡΠ°ΡΠΊΠΈΡΠ»ΠΈΡΠ΅Π»ΠΈ ΠΈ Π΄ΡΡΠ³ΠΈΠ΅ Π΄ΠΎΠ±Π°Π²ΠΊΠΈ.
ΠΠΈΠ΄Π΅ΠΎ ΠΏΠΎ ΡΠ΅ΠΌΠ΅: ΠΡΠ½ΠΎΠ²Ρ ΠΊΠΈΡΠ»ΠΎΡΠΎΠ΄Π½ΠΎ ΠΊΠΎΠ½Π²Π΅ΡΡΠ΅ΡΠ½ΠΎΠ³ΠΎ ΠΏΡΠΎΠΈΠ·Π²ΠΎΠ΄ΡΡΠ²Π°
ΡΡΡΡΠΎΠΉΡΡΠ²ΠΎ ΠΈ ΡΠ΅Ρ Π½ΠΎΠ»ΠΎΠ³ΠΈΡ Π²ΡΠΏΠ»Π°Π²ΠΊΠΈ ΡΡΠ°Π»ΠΈ
Π ΠΏΡΠΎΡΠ΅ΡΡΠ°Ρ ΠΏΠΎΠ»ΡΡΠ΅Π½ΠΈΡ Π²ΡΡΠΎΠΊΠΎΠΏΡΠΎΡΠ½ΡΡ ΡΡΠ°Π»Π΅ΠΉ Π²Π°ΠΆΠ½ΡΡ ΡΠΎΠ»Ρ ΠΈΠ³ΡΠ°ΡΡ ΠΎΠΏΠ΅ΡΠ°ΡΠΈΠΈ Π»Π΅Π³ΠΈΡΠΎΠ²Π°Π½ΠΈΡ ΠΈ ΠΌΠΎΠ΄ΠΈΡΠΈΠΊΠ°ΡΠΈΠΈ Π±Π°Π·ΠΎΠ²ΠΎΠ³ΠΎ ΡΠΎΡΡΠ°Π²Π°. ΠΡΠ½ΠΎΠ²Ρ ΠΏΠΎΠ΄ΠΎΠ±Π½ΡΡ ΠΏΡΠΎΡΠ΅Π΄ΡΡ ΡΠΎΡΡΠ°Π²Π»ΡΡΡ ΡΠ΅Ρ Π½ΠΈΠΊΠΈ Π΄ΠΎΠ±Π°Π²Π»Π΅Π½ΠΈΡ ΠΌΠ΅ΡΠ°Π»Π»ΠΈΡΠ΅ΡΠΊΠΈΡ ΠΏΡΠΈΠΌΠ΅ΡΠ΅ΠΉ ΡΠ°Π·Π½ΠΎΠ³ΠΎ ΡΠ²ΠΎΠΉΡΡΠ²Π°, Π½ΠΎ ΠΈ Π³Π°Π·ΠΎ-Π²ΠΎΠ·Π΄ΡΡΠ½Π°Ρ ΡΠ΅Π³ΡΠ»ΡΡΠΈΡ ΠΎΠΊΠ°Π·ΡΠ²Π°Π΅Ρ Π½Π΅ΠΌΠ°Π»ΠΎΠ²Π°ΠΆΠ½ΠΎΠ΅ Π·Π½Π°ΡΠ΅Π½ΠΈΠ΅. ΠΠΌΠ΅Π½Π½ΠΎ Π½Π° ΡΡΡ ΡΠ΅Ρ Π½ΠΎΠ»ΠΎΠ³ΠΈΡΠ΅ΡΠΊΡΡ ΠΎΠΏΠ΅ΡΠ°ΡΠΈΡ ΠΎΡΠΈΠ΅Π½ΡΠΈΡΡΠ΅ΡΡΡ ΡΠ°Π±ΠΎΡΠ° ΠΊΠΈΡΠ»ΠΎΡΠΎΠ΄Π½ΠΎΠ³ΠΎ ΠΊΠΎΠ½Π²Π΅ΡΡΠ΅ΡΠ°, ΠΊΠΎΡΠΎΡΡΠΉ ΡΠΈΡΠΎΠΊΠΎ ΠΈΡΠΏΠΎΠ»ΡΠ·ΡΠ΅ΡΡΡ Π² ΠΌΠ΅ΡΠ°Π»Π»ΡΡΠ³ΠΈΠΈ ΠΏΡΠΈ ΠΏΠΎΠ»ΡΡΠ΅Π½ΠΈΠΈ ΡΠΏΠ»Π°Π²ΠΎΠ² ΡΡΠ°Π»ΠΈ Π² Π±ΠΎΠ»ΡΡΠΈΡ ΠΎΠ±ΡΠ΅ΠΌΠ°Ρ .
ΠΠΎΠ½ΡΡΡΡΠΊΡΠΈΡ ΠΊΠΎΠ½Π²Π΅ΡΡΠ΅ΡΠ°

ΠΠ±ΠΎΡΡΠ΄ΠΎΠ²Π°Π½ΠΈΠ΅ ΠΏΡΠ΅Π΄ΡΡΠ°Π²Π»ΡΠ΅Ρ ΡΠΎΠ±ΠΎΠΉ Π³ΡΡΡΠ΅Π²ΠΈΠ΄Π½ΡΠΉ ΡΠΎΡΡΠ΄, ΠΎΠ±Π΅ΡΠΏΠ΅ΡΠ΅Π½Π½ΡΠΉ Π²Π½ΡΡΡΠ΅Π½Π½Π΅ΠΉ ΡΡΡΠ΅ΡΠΎΠ²ΠΊΠΎΠΉ ΠΈ Π»Π΅ΡΠΊΠΎΠΉ Π΄Π»Ρ Π²ΡΠΏΡΡΠΊΠ° ΠΏΡΠΎΠ΄ΡΠΊΡΠΎΠ² ΠΏΠ»Π°Π²ΠΊΠΈ. Π Π²Π΅ΡΡ Π½Π΅ΠΉ ΡΠ°ΡΡΠΈ ΠΊΠΎΠ½ΡΡΡΡΠΊΡΠΈΠΈ ΠΏΡΠ΅Π΄ΡΡΠΌΠΎΡΡΠ΅Π½ΠΎ ΠΎΡΠ²Π΅ΡΡΡΠΈΠ΅ Ρ Π³ΠΎΡΠ»ΠΎΠ²ΠΈΠ½ΠΎΠΉ Π΄Π»Ρ ΠΏΠΎΠ΄Π°ΡΠΈ ΡΡΡΠΌΡ, Π»ΠΎΠΌΠ°, ΡΠ°ΡΠΏΠ»Π°Π²Π»Π΅Π½Π½ΠΎΠ³ΠΎ ΡΡΠ³ΡΠ½Π°, Π»Π΅Π³ΠΈΡΡΡΡΠΈΡ ΡΠΌΠ΅ΡΠ΅ΠΉ ΠΈ ΠΎΡΠ²ΠΎΠ΄Π° Π³Π°Π·Π°. Π’ΠΎΠ½Π½Π°ΠΆ Π²Π°ΡΡΠΈΡΡΠ΅ΡΡΡ ΠΎΡ 50 Π΄ΠΎ 400 Ρ. Π ΠΊΠ°ΡΠ΅ΡΡΠ²Π΅ ΠΌΠ°ΡΠ΅ΡΠΈΠ°Π»ΠΎΠ² Π΄Π»Ρ ΠΈΠ·Π³ΠΎΡΠΎΠ²Π»Π΅Π½ΠΈΡ ΠΊΠΎΠ½ΡΡΡΡΠΊΡΠΈΠΈ ΠΏΡΠΈΠΌΠ΅Π½ΡΠ΅ΡΡΡ Π»ΠΈΡΡΠΎΠ²Π°Ρ ΠΈΠ»ΠΈ ΡΠ²Π°ΡΠ½Π°Ρ ΡΡΠ°Π»Ρ ΡΡΠ΅Π΄Π½Π΅ΠΉ ΡΠΎΠ»ΡΠΈΠ½ΠΎΠΉ ΠΏΠΎΡΡΠ΄ΠΊΠ° 50-70 ΠΌΠΌ. Π’ΠΈΠΏΠΎΠ²ΠΎΠ΅ ΡΡΡΡΠΎΠΉΡΡΠ²ΠΎ ΠΊΠΈΡΠ»ΠΎΡΠΎΠ΄Π½ΠΎΠ³ΠΎ ΠΊΠΎΠ½Π²Π΅ΡΡΠ΅ΡΠ° ΠΏΡΠ΅Π΄ΡΡΠΌΠ°ΡΡΠΈΠ²Π°Π΅Ρ Π²ΠΎΠ·ΠΌΠΎΠΆΠ½ΠΎΡΡΡ ΠΎΡΡΠΎΠ΅Π΄ΠΈΠ½Π΅Π½ΠΈΡ Π΄Π½ΠΈΡΠ° β ΡΡΠΎ ΠΌΠΎΠ΄ΠΈΡΠΈΠΊΠ°ΡΠΈΠΈ Ρ Π΄ΠΎΠ½Π½ΠΎΠΉ ΠΏΡΠΎΠ΄ΡΠ²ΠΊΠΎΠΉ Π³Π°Π·ΠΎ-Π²ΠΎΠ·Π΄ΡΡΠ½ΡΠΌΠΈ ΡΠΌΠ΅ΡΡΠΌΠΈ. Π‘ΡΠ΅Π΄ΠΈ Π²ΡΠΏΠΎΠΌΠΎΠ³Π°ΡΠ΅Π»ΡΠ½ΡΡ ΠΈ ΡΡΠ½ΠΊΡΠΈΠΎΠ½Π°Π»ΡΠ½ΡΡ ΡΠ»Π΅ΠΌΠ΅Π½ΡΠΎΠ² Π°Π³ΡΠ΅Π³Π°ΡΠ° ΠΌΠΎΠΆΠ½ΠΎ Π²ΡΠ΄Π΅Π»ΠΈΡΡ ΡΠ»Π΅ΠΊΡΡΠΎΠ΄Π²ΠΈΠ³Π°ΡΠ΅Π»Ρ, ΡΡΡΠ±ΠΎΠΏΡΠΎΠ²ΠΎΠ΄Π½ΡΡ ΠΈΠ½ΡΡΠ°ΡΡΡΡΠΊΡΡΡΡ Π΄Π»Ρ ΡΠΈΡΠΊΡΠ»ΡΡΠΈΠΈ ΠΏΠΎΡΠΎΠΊΠΎΠ² ΠΊΠΈΡΠ»ΠΎΡΠΎΠ΄Π°, ΠΎΠΏΠΎΡΠ½ΡΠ΅ ΠΏΠΎΠ΄ΡΠΈΠΏΠ½ΠΈΠΊΠΈ, Π΄Π΅ΠΌΠΏΡΠ΅ΡΠ½ΡΡ ΠΏΠ»Π°ΡΡΠΎΡΠΌΡ ΠΈ ΠΎΠΏΠΎΡΠ½ΡΡ ΡΡΠ°Π½ΠΈΠ½Ρ Π΄Π»Ρ ΠΌΠΎΠ½ΡΠ°ΠΆΠ° ΠΊΠΎΠ½ΡΡΡΡΠΊΡΠΈΠΈ.
ΠΠΏΠΎΡΠ½ΡΠ΅ ΠΊΠΎΠ»ΡΡΠ° ΠΈ ΡΠ°ΠΏΡΠ°
ΠΠΎΠ½Π²Π΅ΡΡΠ΅Ρ ΡΠ°ΡΠΏΠΎΠ»Π°Π³Π°Π΅ΡΡΡ Π½Π° ΡΠΎΠ»ΠΈΠΊΠΎΠ²ΡΡ ΠΏΠΎΠ΄ΡΠΈΠΏΠ½ΠΈΠΊΠ°Ρ , ΠΊΠΎΡΠΎΡΡΠ΅ ΡΠΈΠΊΡΠΈΡΡΡΡΡΡ Π½Π° ΡΡΠ°Π½ΠΈΠ½Π΅. ΠΠΎΠ½ΡΡΡΡΠΊΡΠΈΡ ΠΌΠΎΠΆΠ΅Ρ Π±ΡΡΡ ΠΈ ΡΡΠ°ΡΠΈΠΎΠ½Π°ΡΠ½ΠΎΠΉ, Π½ΠΎ ΡΡΠΎ Π²ΡΡΡΠ΅ΡΠ°Π΅ΡΡΡ ΡΠ΅Π΄ΠΊΠΎ. ΠΠ±ΡΡΠ½ΠΎ Π½Π° ΡΡΠ°ΠΏΠ°Ρ ΠΏΡΠΎΠ΅ΠΊΡΠΈΡΠΎΠ²Π°Π½ΠΈΡ ΠΎΠΏΡΠ΅Π΄Π΅Π»ΡΠ΅ΡΡΡ Π²ΠΎΠ·ΠΌΠΎΠΆΠ½ΠΎΡΡΡ ΡΡΠ°Π½ΡΠΏΠΎΡΡΠΈΡΠΎΠ²ΠΊΠΈ ΠΈΠ»ΠΈ ΠΏΠ΅ΡΠ΅ΠΌΠ΅ΡΠ΅Π½ΠΈΡ Π°Π³ΡΠ΅Π³Π°ΡΠ° Π² ΡΠ΅Ρ ΠΈΠ»ΠΈ ΠΈΠ½ΡΡ ΡΡΠ»ΠΎΠ²ΠΈΡΡ . ΠΠΌΠ΅Π½Π½ΠΎ Π·Π° ΡΡΠΈ ΡΡΠ½ΠΊΡΠΈΠΈ ΠΎΡΠ²Π΅ΡΠ°Π΅Ρ ΠΎΡΠ½Π°ΡΡΠΊΠ° Π² Π²ΠΈΠ΄Π΅ ΠΎΠΏΠΎΡΠ½ΡΡ ΠΊΠΎΠ»Π΅Ρ ΠΈ ΡΠ°ΠΏΡΡ. ΠΡΡΠΏΠΏΠ° ΠΏΠΎΠ΄ΡΠΈΠΏΠ½ΠΈΠΊΠΎΠ² ΠΎΠ±Π΅ΡΠΏΠ΅ΡΠΈΠ²Π°Π΅Ρ Π²ΠΎΠ·ΠΌΠΎΠΆΠ½ΠΎΡΡΡ ΠΊΡΡΡΠ΅Π½ΠΈΡ ΠΎΠ±ΠΎΡΡΠ΄ΠΎΠ²Π°Π½ΠΈΡ Π²ΠΎΠΊΡΡΠ³ ΠΎΡΠΈ ΡΠ°ΠΏΡ. ΠΡΠ΅ΠΆΠ½ΠΈΠ΅ ΠΌΠΎΠ΄Π΅Π»ΠΈ ΠΊΠΎΠ½Π²Π΅ΡΡΠ΅ΡΠΎΠ² ΠΏΡΠ΅Π΄ΠΏΠΎΠ»Π°Π³Π°Π»ΠΈ ΡΠΎΠ²ΠΌΠ΅ΡΠ΅Π½ΠΈΠ΅ Π½Π΅ΡΡΡΠ΅ΠΉ ΠΎΡΠ½Π°ΡΡΠΊΠΈ ΠΈ ΠΊΠΎΡΠΏΡΡΠ° ΠΏΠ»Π°Π²ΠΈΠ»ΡΠ½ΠΎΠ³ΠΎ ΠΎΠ±ΠΎΡΡΠ΄ΠΎΠ²Π°Π½ΠΈΡ, Π½ΠΎ ΠΈΠ·-Π·Π° Π²ΠΎΠ·Π΄Π΅ΠΉΡΡΠ²ΠΈΡ Π²ΡΡΠΎΠΊΠΈΡ ΡΠ΅ΠΌΠΏΠ΅ΡΠ°ΡΡΡ ΠΈ Π΄Π΅ΡΠΎΡΠΌΠ°ΡΠΈΠΈ Π²ΡΠΏΠΎΠΌΠΎΠ³Π°ΡΠ΅Π»ΡΠ½ΡΡ ΠΌΠ°ΡΠ΅ΡΠΈΠ°Π»ΠΎΠ² ΡΡΠΎ ΠΊΠΎΠ½ΡΡΡΡΠΊΡΠΈΠΎΠ½Π½ΠΎΠ΅ ΡΠ΅ΡΠ΅Π½ΠΈΠ΅ Π±ΡΠ»ΠΎ Π·Π°ΠΌΠ΅Π½Π΅Π½ΠΎ Π±ΠΎΠ»Π΅Π΅ ΡΠ»ΠΎΠΆΠ½ΠΎΠΉ, Π½ΠΎ Π½Π°Π΄Π΅ΠΆΠ½ΠΎΠΉ ΠΈ Π΄ΠΎΠ»Π³ΠΎΠ²Π΅ΡΠ½ΠΎΠΉ ΡΡ Π΅ΠΌΠΎΠΉ Π²Π·Π°ΠΈΠΌΠΎΠ΄Π΅ΠΉΡΡΠ²ΠΈΡ ΡΡΠ½ΠΊΡΠΈΠΎΠ½Π°Π»ΡΠ½ΠΎΠ³ΠΎ Π±Π»ΠΎΠΊΠ° ΠΈ Π΅ΠΌΠΊΠΎΡΡΠΈ.

Π‘ΠΎΠ²ΡΠ΅ΠΌΠ΅Π½Π½ΡΠΉ ΠΊΠΈΡΠ»ΠΎΡΠΎΠ΄Π½ΡΠΉ ΠΊΠΎΠ½Π²Π΅ΡΡΠ΅Ρ, Π² ΡΠ°ΡΡΠ½ΠΎΡΡΠΈ, ΠΎΠ±Π΅ΡΠΏΠ΅ΡΠΈΠ²Π°Π΅ΡΡΡ ΠΎΡΠ΄Π΅Π»ΡΠ½ΡΠΌ ΠΎΠΏΠΎΡΠ½ΡΠΌ ΠΊΠΎΠ»ΡΡΠΎΠΌ, Π² ΡΡΡΡΠΊΡΡΡΡ ΠΊΠΎΡΠΎΡΠΎΠ³ΠΎ ΡΠ°ΠΊΠΆΠ΅ Π²Π²ΠΎΠ΄ΡΡΡΡ ΡΠ°ΠΏΡΡ ΠΈ Π·Π°ΠΊΡΠ΅ΠΏΠ»Π΅Π½Π½ΡΠΉ ΠΊΠΎΠΆΡΡ . Π’Π΅Ρ Π½ΠΎΠ»ΠΎΠ³ΠΈΡΠ΅ΡΠΊΠΈΠΉ ΠΏΡΠΎΠΌΠ΅ΠΆΡΡΠΎΠΊ ΠΌΠ΅ΠΆΠ΄Ρ ΠΊΠΎΠΆΡΡ ΠΎΠΌ ΠΈ ΠΎΠΏΠΎΡΠ½ΠΎΠΉ Π±Π°Π·ΠΎΠΉ ΠΏΡΠ΅Π΄ΠΎΡΠ²ΡΠ°ΡΠ°Π΅Ρ Π½Π΅Π³Π°ΡΠΈΠ²Π½ΠΎΠ΅ ΡΠ΅ΠΌΠΏΠ΅ΡΠ°ΡΡΡΠ½ΠΎΠ΅ Π²ΠΎΠ·Π΄Π΅ΠΉΡΡΠ²ΠΈΠ΅ Π½Π° ΡΡΠ²ΡΡΠ²ΠΈΡΠ΅Π»ΡΠ½ΡΠ΅ ΡΠ»Π΅ΠΌΠ΅Π½ΡΡ ΠΏΠΎΠ΄Π²Π΅ΡΠΎΠΊ ΠΈ ΠΏΠ΅ΡΠ΅Π΄Π²ΠΈΠΆΠ½ΡΡ ΠΌΠ΅Ρ Π°Π½ΠΈΠ·ΠΌΠΎΠ². ΠΠ΅ΠΏΠΎΡΡΠ΅Π΄ΡΡΠ²Π΅Π½Π½ΠΎ ΡΠΈΡΡΠ΅ΠΌΠ° ΡΠΈΠΊΡΠ°ΡΠΈΠΈ ΠΊΠΎΠ½Π²Π΅ΡΡΠ΅ΡΠ° ΡΠ΅Π°Π»ΠΈΠ·ΡΠ΅ΡΡΡ Π·Π° ΡΡΠ΅Ρ ΡΠΏΠΎΡΠΎΠ². Π‘Π°ΠΌΠΎ ΠΆΠ΅ ΠΎΠΏΠΎΡΠ½ΠΎΠ΅ ΠΊΠΎΠ»ΡΡΠΎ ΠΏΡΠ΅Π΄ΡΡΠ°Π²Π»ΡΠ΅Ρ ΡΠΎΠ±ΠΎΠΉ Π½Π΅ΡΡΡΠ΅Π΅ ΡΡΡΡΠΎΠΉΡΡΠ²ΠΎ, ΡΡΠΎΡΠΌΠΈΡΠΎΠ²Π°Π½Π½ΠΎΠ΅ Π΄Π²ΡΠΌΡ ΠΏΠΎΠ»ΡΠΊΠΎΠ»ΡΡΠ°ΠΌΠΈ ΠΈ ΡΠ°ΠΏΡΠΎΠ²ΡΠΌΠΈ ΠΏΠ»ΠΈΡΠ°ΠΌΠΈ, Π·Π°ΠΊΡΠ΅ΠΏΠ»Π΅Π½Π½ΡΠΌΠΈ Π² ΡΠ·Π»Π°Ρ ΡΡΡΠΊΠΎΠ²ΠΊΠΈ.
ΠΠΎΠ²ΠΎΡΠΎΡΠ½ΡΠΉ ΠΌΠ΅Ρ Π°Π½ΠΈΠ·ΠΌ
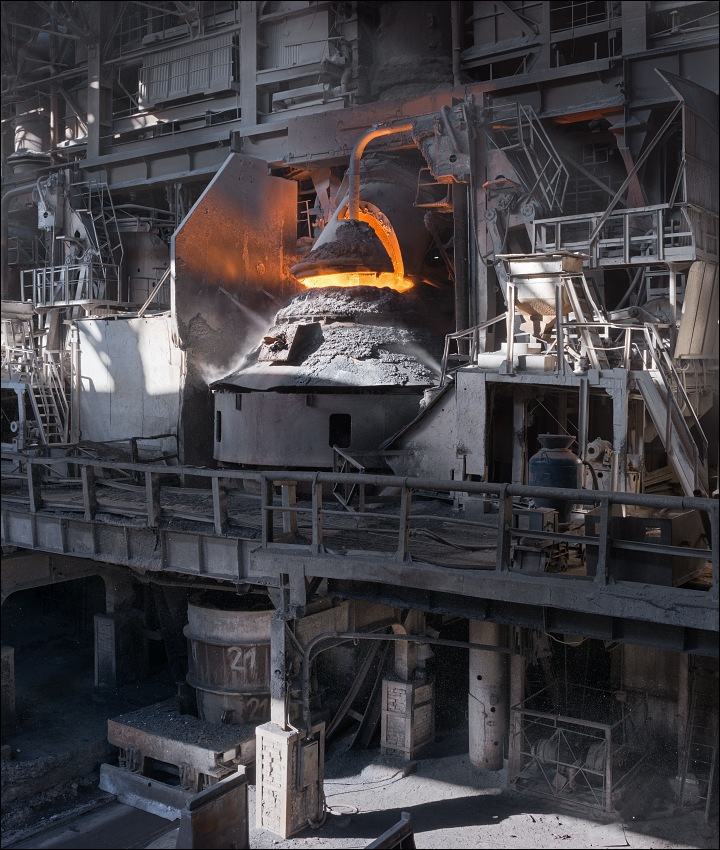
ΠΠ»Π΅ΠΊΡΡΠΎΠΏΡΠΈΠ²ΠΎΠ΄ ΠΎΠ±Π΅ΡΠΏΠ΅ΡΠΈΠ²Π°Π΅Ρ Π²ΠΎΠ·ΠΌΠΎΠΆΠ½ΠΎΡΡΡ ΠΏΠΎΠ²ΠΎΡΠΎΡΠ° ΠΊΠΎΠ½Π²Π΅ΡΡΠ΅ΡΠ° Π½Π° 360Β°. Π‘ΡΠ΅Π΄Π½ΡΡ ΡΠΊΠΎΡΠΎΡΡΡ Π²ΡΠ°ΡΠ΅Π½ΠΈΡ ΡΠΎΡΡΠ°Π²Π»ΡΠ΅Ρ 0,1-1 ΠΌ/ΠΌΠΈΠ½. Π‘Π°ΠΌΠ° ΠΏΠΎ ΡΠ΅Π±Π΅ ΡΡΠ° ΡΡΠ½ΠΊΡΠΈΡ ΡΡΠ΅Π±ΡΠ΅ΡΡΡ Π½Π΅ Π²ΡΠ΅Π³Π΄Π° β Π² Π·Π°Π²ΠΈΡΠΈΠΌΠΎΡΡΠΈ ΠΎΡ ΠΎΡΠ³Π°Π½ΠΈΠ·Π°ΡΠΈΠΈ ΡΠ΅Ρ Π½ΠΎΠ»ΠΎΠ³ΠΈΡΠ΅ΡΠΊΠΈΡ ΠΎΠΏΠ΅ΡΠ°ΡΠΈΠΉ Π² Ρ ΠΎΠ΄Π΅ ΡΠ°Π±ΠΎΡΠ΅Π³ΠΎ ΠΏΡΠΎΡΠ΅ΡΡΠ°. ΠΠ°ΠΏΡΠΈΠΌΠ΅Ρ, ΠΏΠΎΠ²ΠΎΡΠΎΡ ΠΌΠΎΠΆΠ΅Ρ ΠΏΠΎΡΡΠ΅Π±ΠΎΠ²Π°ΡΡΡΡ Π΄Π»Ρ ΠΎΡΠΈΠ΅Π½ΡΠ°ΡΠΈΠΈ Π³ΠΎΡΠ»ΠΎΠ²ΠΈΠ½Ρ ΠΏΡΡΠΌΠΎ ΠΊ ΡΠΎΡΠΊΠ΅ ΠΏΠΎΠ΄Π°ΡΠΈ Π»ΠΎΠΌΠ°, Π·Π°Π»ΠΈΠ²ΠΊΠΈ ΡΡΠ³ΡΠ½Π°, ΡΠ»ΠΈΠ²Π° ΡΡΠ°Π»ΠΈ ΠΈ Ρ. Π΄. Π€ΡΠ½ΠΊΡΠΈΠΎΠ½Π°Π» ΠΏΠΎΠ²ΠΎΡΠΎΡΠ½ΠΎΠ³ΠΎ ΠΌΠ΅Ρ Π°Π½ΠΈΠ·ΠΌΠ° ΠΌΠΎΠΆΠ΅Ρ Π±ΡΡΡ ΡΠ°Π·Π½ΡΠΌ. ΠΡΠ²Π°ΡΡ ΠΈ ΠΎΠ΄Π½ΠΎΡΡΠΎΡΠΎΠ½Π½ΠΈΠ΅, ΠΈ Π΄Π²ΡΡ ΡΡΠΎΡΠΎΠ½Π½ΠΈΠ΅ ΡΠΈΡΡΠ΅ΠΌΡ. ΠΠ°ΠΊ ΠΏΡΠ°Π²ΠΈΠ»ΠΎ, ΠΊΠΈΡΠ»ΠΎΡΠΎΠ΄Π½ΡΠ΅ ΠΊΠΎΠ½Π²Π΅ΡΡΠ΅ΡΡ Π³ΡΡΠ·ΠΎΠΏΠΎΠ΄ΡΠ΅ΠΌΠ½ΠΎΡΡΡΡ Π΄ΠΎ 200 Ρ ΠΏΡΠ΅Π΄ΠΏΠΎΠ»Π°Π³Π°ΡΡ ΠΏΠΎΠ²ΠΎΡΠΎΡ Π»ΠΈΡΡ Π² ΠΎΠ΄Π½Ρ ΡΡΠΎΡΠΎΠ½Ρ. Π‘Π²ΡΠ·Π°Π½ΠΎ ΡΡΠΎ Ρ ΡΠ΅ΠΌ, ΡΡΠΎ Π² ΡΠ°ΠΊΠΈΡ ΠΊΠΎΠ½ΡΡΡΡΠΊΡΠΈΡΡ ΡΡΠ΅Π±ΡΠ΅ΡΡΡ ΠΌΠ΅Π½ΡΡΠ΅ ΠΊΡΡΡΡΡΠ΅Π³ΠΎ ΠΌΠΎΠΌΠ΅Π½ΡΠ° ΠΏΡΠΈ Π½Π°ΠΊΠ»ΠΎΠ½Π΅ Π³ΠΎΡΠ»ΠΎΠ²ΠΈΠ½Ρ. Π§ΡΠΎΠ±Ρ ΠΈΡΠΊΠ»ΡΡΠΈΡΡ ΡΠ°ΡΡ ΠΎΠ΄ Π»ΠΈΡΠ½Π΅ΠΉ ΡΠ½Π΅ΡΠ³ΠΈΠΈ ΠΏΡΠΈ ΡΠΊΡΠΏΠ»ΡΠ°ΡΠ°ΡΠΈΠΈ Π±ΠΎΠ»ΡΡΠ΅Π³ΡΡΠ·Π½ΠΎΠ³ΠΎ ΠΎΠ±ΠΎΡΡΠ΄ΠΎΠ²Π°Π½ΠΈΡ, Π΅Π³ΠΎ ΠΎΠ±Π΅ΡΠΏΠ΅ΡΠΈΠ²Π°ΡΡ ΠΌΠ΅Ρ Π°Π½ΠΈΠ·ΠΌΠΎΠΌ Π΄Π²ΡΡ ΡΡΠΎΡΠΎΠ½Π½Π΅Π³ΠΎ ΠΏΠΎΠ²ΠΎΡΠΎΡΠ°, ΡΡΠΎ ΠΊΠΎΠΌΠΏΠ΅Π½ΡΠΈΡΡΠ΅Ρ Π·Π°ΡΡΠ°ΡΡ Π½Π° ΠΌΠ°Π½ΠΈΠΏΡΠ»ΡΡΠΈΠΈ Ρ Π³ΠΎΡΠ»ΠΎΠ²ΠΈΠ½ΠΎΠΉ. Π ΡΡΡΡΠΊΡΡΡΡ ΡΠΈΡΡΠ΅ΠΌΡ ΠΊΡΡΡΠ΅Π½ΠΈΡ Π²Ρ ΠΎΠ΄ΠΈΡ ΡΠ΅Π΄ΡΠΊΡΠΎΡ, ΡΠ»Π΅ΠΊΡΡΠΎΠ΄Π²ΠΈΠ³Π°ΡΠ΅Π»Ρ ΠΈ ΡΠΏΠΈΠ½Π΄Π΅Π»Ρ. ΠΡΠΎ ΡΡΠ°Π΄ΠΈΡΠΈΠΎΠ½Π½Π°Ρ ΠΊΠΎΠΌΠΏΠΎΠ½ΠΎΠ²ΠΊΠ° ΡΡΠ°ΡΠΈΠΎΠ½Π°ΡΠ½ΠΎΠ³ΠΎ ΠΏΡΠΈΠ²ΠΎΠ΄Π°, Π·Π°ΠΊΡΠ΅ΠΏΠ»Π΅Π½Π½ΠΎΠ³ΠΎ Π½Π° Π±Π΅ΡΠΎΠ½Π½ΠΎΠΉ ΡΡΡΠΆΠΊΠ΅. ΠΠΎΠ»Π΅Π΅ ΡΠ΅Ρ Π½ΠΎΠ»ΠΎΠ³ΠΈΡΠ½ΡΠ΅ Π½Π°Π²Π΅ΡΠ½ΡΠ΅ ΠΌΠ΅Ρ Π°Π½ΠΈΠ·ΠΌΡ ΡΠΈΠΊΡΠΈΡΡΡΡΡΡ Π½Π° ΡΠ°ΠΏΡΠ΅ ΠΈ ΠΏΡΠΈΠ²ΠΎΠ΄ΡΡΡΡ Π² Π΄Π΅ΠΉΡΡΠ²ΠΈΠ΅ Π·Π° ΡΡΠ΅Ρ Π²Π΅Π΄ΠΎΠΌΠΎΠ³ΠΎ Π·ΡΠ±ΡΠ°ΡΠΎΠ³ΠΎ ΠΊΠΎΠ»Π΅ΡΠ° Ρ ΡΠΈΡΡΠ΅ΠΌΠΎΠΉ ΠΏΠΎΠ΄ΡΠΈΠΏΠ½ΠΈΠΊΠΎΠ², ΠΊΠΎΡΠΎΡΡΠ΅ ΡΠ°ΠΊΠΆΠ΅ ΡΠ΅ΡΠ΅Π· ΡΠΈΡΡΠ΅ΠΌΡ Π²Π°Π»ΠΎΠ² Π°ΠΊΡΠΈΠ²ΠΈΠ·ΠΈΡΡΡΡΡΡ ΡΠ»Π΅ΠΊΡΡΠΎΠΌΠΎΡΠΎΡΠ°ΠΌΠΈ.
Π Π°Π·ΠΌΠ΅ΡΡ ΠΊΠΎΠ½Π²Π΅ΡΡΠ΅ΡΠ°
Π Ρ ΠΎΠ΄Π΅ ΠΏΡΠΎΠ΅ΠΊΡΠΈΡΠΎΠ²Π°Π½ΠΈΡ ΠΏΠ°ΡΠ°ΠΌΠ΅ΡΡΡ ΠΊΠΎΠ½ΡΡΡΡΠΊΡΠΈΠΈ Π΄ΠΎΠ»ΠΆΠ½Ρ ΡΠ°ΡΡΡΠΈΡΡΠ²Π°ΡΡΡΡ ΠΈΡΡ ΠΎΠ΄Ρ ΠΈΠ· ΡΠΎΠ³ΠΎ, ΠΊΠ°ΠΊΠΎΠΉ ΠΏΡΠΈΠΌΠ΅ΡΠ½ΡΠΉ ΠΎΠ±ΡΠ΅ΠΌ ΠΏΡΠΎΠ΄ΡΠ²ΠΊΠΈ Π±Π΅Π· ΡΡΠ΅ΡΠ° Π²ΡΠ±ΡΠΎΡΠ° ΡΠ°ΡΠΏΠ»Π°Π²Π° Π±ΡΠ΄Π΅Ρ ΠΏΡΠΎΠΈΠ·Π²ΠΎΠ΄ΠΈΡΡΡΡ. Π ΠΏΠΎΡΠ»Π΅Π΄Π½ΠΈΠ΅ Π³ΠΎΠ΄Ρ ΡΠ°Π·ΡΠ°Π±Π°ΡΡΠ²Π°ΡΡΡΡ Π°Π³ΡΠ΅Π³Π°ΡΡ, ΠΏΡΠΈΠ½ΠΈΠΌΠ°ΡΡΠΈΠ΅ ΠΌΠ°ΡΠ΅ΡΠΈΠ°Π»Ρ Π² ΠΎΠ±ΡΠ΅ΠΌΠ΅ ΠΎΡ 1 Π΄ΠΎ 0,85 ΠΌ3/Ρ. Π’Π°ΠΊΠΆΠ΅ ΡΠ°ΡΡΡΠΈΡΡΠ²Π°Π΅ΡΡΡ ΡΠΊΠ»ΠΎΠ½ Π³ΠΎΡΠ»ΠΎΠ²ΠΈΠ½Ρ, ΡΠ³ΠΎΠ» ΠΊΠΎΡΠΎΡΠΎΠ³ΠΎ Π² ΡΡΠ΅Π΄Π½Π΅ΠΌ ΡΠΎΡΡΠ°Π²Π»ΡΠ΅Ρ ΠΎΡ 20Β° Π΄ΠΎ 35Β°. ΠΠ΄Π½Π°ΠΊΠΎ ΠΏΡΠ°ΠΊΡΠΈΠΊΠ° ΡΠΊΡΠΏΠ»ΡΠ°ΡΠ°ΡΠΈΠΈ ΡΠ°ΠΊΠΈΡ ΡΠΎΠΎΡΡΠΆΠ΅Π½ΠΈΠΉ ΠΏΠΎΠΊΠ°Π·ΡΠ²Π°Π΅Ρ, ΡΡΠΎ ΠΏΡΠ΅Π²ΡΡΠ΅Π½ΠΈΠ΅ Π½Π°ΠΊΠ»ΠΎΠ½Π° Π² 26Β° ΡΡ ΡΠ΄ΡΠ°Π΅Ρ ΠΊΠ°ΡΠ΅ΡΡΠ²ΠΎ ΡΡΡΠ΅ΡΠΎΠ²ΠΊΠΈ. ΠΠΎ Π³Π»ΡΠ±ΠΈΠ½Π΅ ΡΠ°Π·ΠΌΠ΅ΡΡ ΠΊΠΎΠ½Π²Π΅ΡΡΠ΅ΡΠ° ΡΠΎΡΡΠ°Π²Π»ΡΡΡ 1-2 ΠΌ, Π½ΠΎ ΠΏΠΎ ΠΌΠ΅ΡΠ΅ ΡΠ²Π΅Π»ΠΈΡΠ΅Π½ΠΈΡ Π΅ΠΌΠΊΠΎΡΡΠΈ Π·Π°Π³ΡΡΠ·ΠΊΠΈ ΠΈ Π²ΡΡΠΎΡΠ° ΠΊΠΎΠ½ΡΡΡΡΠΊΡΠΈΠΈ ΠΌΠΎΠΆΠ΅Ρ ΡΠ²Π΅Π»ΠΈΡΠΈΠ²Π°ΡΡΡΡ. ΠΠ±ΡΡΠ½ΡΠ΅ ΠΊΠΎΠ½Π²Π΅ΡΡΠ΅ΡΡ Π³Π»ΡΠ±ΠΈΠ½ΠΎΠΉ Π΄ΠΎ 1 ΠΌ ΠΌΠΎΠ³ΡΡ ΠΏΡΠΈΠ½ΠΈΠΌΠ°ΡΡ Π·Π°Π³ΡΡΠ·ΠΊΡ Π½Π΅ Π±ΠΎΠ»Π΅Π΅ 50 Ρ. Π§ΡΠΎ ΠΊΠ°ΡΠ°Π΅ΡΡΡ Π΄ΠΈΠ°ΠΌΠ΅ΡΡΠ°, ΡΠΎ ΠΎΠ½ Π² ΡΡΠ΅Π΄Π½Π΅ΠΌ Π²Π°ΡΡΠΈΡΡΠ΅ΡΡΡ ΠΎΡ 4 Π΄ΠΎ 7 ΠΌ. Π’ΠΎΠ»ΡΠΈΠ½Π° Π³ΠΎΡΠ»ΠΎΠ²ΠΈΠ½Ρ ΡΠΎΡΡΠ°Π²Π»ΡΠ΅Ρ 2-2,5 ΠΌ.
Π€ΡΡΠ΅ΡΠΎΠ²ΠΊΠ° ΠΊΠΈΡΠ»ΠΎΡΠΎΠ΄Π½ΠΎΠ³ΠΎ ΠΊΠΎΠ½Π²Π΅ΡΡΠ΅ΡΠ°

ΠΠ±ΡΠ·Π°ΡΠ΅Π»ΡΠ½Π°Ρ ΡΠ΅Ρ Π½ΠΎΠ»ΠΎΠ³ΠΈΡΠ΅ΡΠΊΠ°Ρ ΠΏΡΠΎΡΠ΅Π΄ΡΡΠ°, Π² Ρ ΠΎΠ΄Π΅ ΠΊΠΎΡΠΎΡΠΎΠΉ Π²Π½ΡΡΡΠ΅Π½Π½ΠΈΠ΅ ΡΡΠ΅Π½Ρ ΠΊΠΎΠ½Π²Π΅ΡΡΠ΅ΡΠ° ΠΎΠ±Π΅ΡΠΏΠ΅ΡΠΈΠ²Π°ΡΡΡΡ Π·Π°ΡΠΈΡΠ½ΡΠΌ ΡΠ»ΠΎΠ΅ΠΌ. ΠΡΠΈ ΡΡΠΎΠΌ Π½Π°Π΄ΠΎ ΡΡΠΈΡΡΠ²Π°ΡΡ, ΡΡΠΎ Π² ΠΎΡΠ»ΠΈΡΠΈΠ΅ ΠΎΡ Π±ΠΎΠ»ΡΡΠΈΠ½ΡΡΠ²Π° ΠΌΠ΅ΡΠ°Π»Π»ΡΡΠ³ΠΈΡΠ΅ΡΠΊΠΈΡ ΠΏΠ΅ΡΠ΅ΠΉ Π΄Π°Π½Π½Π°Ρ ΠΊΠΎΠ½ΡΡΡΡΠΊΡΠΈΡ ΠΏΠΎΠ΄Π²Π΅ΡΠ³Π°Π΅ΡΡΡ Π³ΠΎΡΠ°Π·Π΄ΠΎ Π±ΠΎΠ»Π΅Π΅ Π²ΡΡΠΎΠΊΠΈΠΌ ΡΠ΅ΡΠΌΠΈΡΠ΅ΡΠΊΠΈΠΌ Π½Π°Π³ΡΡΠ·ΠΊΠ°ΠΌ, ΡΡΠΎ ΠΎΠ±ΡΡΠ»Π°Π²Π»ΠΈΠ²Π°Π΅Ρ ΠΈ ΠΎΡΠΎΠ±Π΅Π½Π½ΠΎΡΡΠΈ Π²ΡΠΏΠΎΠ»Π½Π΅Π½ΠΈΡ ΡΡΡΠ΅ΡΠΎΠ²ΠΊΠ°. ΠΡΠΎ ΠΏΡΠΎΡΠ΅Π΄ΡΡΠ°, ΠΏΡΠ΅Π΄ΠΏΠΎΠ»Π°Π³Π°ΡΡΠ°Ρ ΡΠΊΠ»Π°Π΄ΠΊΡ Π΄Π²ΡΡ Π·Π°ΡΠΈΡΠ½ΡΡ ΡΠ»ΠΎΠ΅Π² β ΡΡΠ½ΠΊΡΠΈΠΎΠ½Π°Π»ΡΠ½ΠΎΠ³ΠΎ ΠΈ Π°ΡΠΌΠΈΡΡΡΡΠ΅Π³ΠΎ. ΠΠ΅ΠΏΠΎΡΡΠ΅Π΄ΡΡΠ²Π΅Π½Π½ΠΎ ΠΊ ΠΏΠΎΠ²Π΅ΡΡ Π½ΠΎΡΡΠΈ ΠΊΠΎΡΠΏΡΡΠ° ΠΏΡΠΈΠΌΡΠΊΠ°Π΅Ρ ΠΏΠ»Π°ΡΡ Π·Π°ΡΠΈΡΠ½ΠΎΠΉ Π°ΡΠΌΠ°ΡΡΡΡ ΡΠΎΠ»ΡΠΈΠ½ΠΎΠΉ 100-250 ΠΌΠΌ. ΠΠ³ΠΎ Π·Π°Π΄Π°ΡΠ° Π·Π°ΠΊΠ»ΡΡΠ°Π΅ΡΡΡ Π² ΡΠ½ΠΈΠΆΠ΅Π½ΠΈΠΈ ΡΠ΅ΠΏΠ»ΠΎΠΏΠΎΡΠ΅ΡΡ ΠΈ Π½Π΅Π΄ΠΎΠΏΡΡΠ΅Π½ΠΈΠΈ ΠΏΡΠΎΠ³Π°ΡΠ° Π²Π΅ΡΡ Π½Π΅Π³ΠΎ ΡΠ»ΠΎΡ. Π ΠΊΠ°ΡΠ΅ΡΡΠ²Π΅ ΠΌΠ°ΡΠ΅ΡΠΈΠ°Π»Π° ΠΏΡΠΈΠΌΠ΅Π½ΡΠ΅ΡΡΡ ΠΌΠ°Π³Π½Π΅Π·ΠΈΡΠΎΠ²ΡΠΉ ΠΈΠ»ΠΈ ΠΌΠ°Π³Π½Π΅Π·ΠΈΡΠΎΡ ΡΠΎΠΌΠΈΡΠΎΠ²ΡΠΉ ΠΊΠΈΡΠΏΠΈΡ, ΠΊΠΎΡΠΎΡΡΠΉ ΠΌΠΎΠΆΠ΅Ρ ΡΠ»ΡΠΆΠΈΡΡ Π³ΠΎΠ΄Π°ΠΌΠΈ Π±Π΅Π· ΠΎΠ±Π½ΠΎΠ²Π»Π΅Π½ΠΈΡ.
ΠΠ΅ΡΡ Π½ΠΈΠΉ ΡΠ°Π±ΠΎΡΠΈΠΉ ΡΠ»ΠΎΠΉ ΠΈΠΌΠ΅Π΅Ρ ΡΠΎΠ»ΡΠΈΠ½Ρ ΠΏΠΎΡΡΠ΄ΠΊΠ° 500-700 ΠΌΠΌ ΠΈ Π·Π°ΠΌΠ΅Π½ΡΠ΅ΡΡΡ Π΄ΠΎΠ²ΠΎΠ»ΡΠ½ΠΎ ΡΠ°ΡΡΠΎ ΠΏΠΎ ΠΌΠ΅ΡΠ΅ ΠΈΠ·Π½ΠΎΡΠ°. ΠΠ° ΡΡΠΎΠΌ ΡΡΠ°ΠΏΠ΅ ΠΊΠΈΡΠ»ΠΎΡΠΎΠ΄Π½ΡΠΉ ΠΊΠΎΠ½Π²Π΅ΡΡΠ΅Ρ ΠΎΠ±ΡΠ°Π±Π°ΡΡΠ²Π°Π΅ΡΡΡ Π±Π΅Π·ΠΎΠ±ΠΆΠΈΠ³ΠΎΠ²ΡΠΌΠΈ ΠΏΠ΅ΡΠΊΠΎ- ΠΈΠ»ΠΈ ΡΠΌΠΎΠ»ΠΎΠ²ΡΠ·Π°Π½Π½ΡΠΌΠΈ ΠΎΠ³Π½Π΅ΡΠΏΠΎΡΠ½ΡΠΌΠΈ ΡΠΎΡΡΠ°Π²Π°ΠΌΠΈ. ΠΡΠ½ΠΎΠ²Ρ ΠΌΠ°ΡΠ΅ΡΠΈΠ°Π»Π° Π΄Π»Ρ ΡΡΠΎΠ³ΠΎ ΡΠ»ΠΎΡ ΡΡΡΠ΅ΡΠΎΠ²ΠΊΠΈ ΡΠΎΡΡΠ°Π²Π»ΡΠ΅Ρ Π΄ΠΎΠ»ΠΎΠΌΠΈΡ Ρ Π΄ΠΎΠ±Π°Π²ΠΊΠ°ΠΌΠΈ ΠΌΠ°Π³Π½Π΅Π·ΠΈΡΠ°. Π‘ΡΠ°Π½Π΄Π°ΡΡΠ½ΡΠΉ ΡΠ°ΡΡΠ΅Ρ ΠΏΠΎ Π½Π°Π³ΡΡΠ·ΠΊΠ΅ Π΄Π΅Π»Π°Π΅ΡΡΡ ΠΈΡΡ ΠΎΠ΄Ρ ΠΈΠ· ΡΠ΅ΠΌΠΏΠ΅ΡΠ°ΡΡΡΠ½ΠΎΠ³ΠΎ Π²ΠΎΠ·Π΄Π΅ΠΉΡΡΠ²ΠΈΡ ΠΏΠΎΡΡΠ΄ΠΊΠ° 100-500 Β°Π‘.
Π’ΠΎΡΠΊΡΠ΅ΡΠΈΡΠΎΠ²Π°Π½ΠΈΠ΅ ΡΡΡΠ΅ΡΠΎΠ²ΠΊΠΈ

ΠΠΎΠ΄ Π°Π³ΡΠ΅ΡΡΠΈΠ²Π½ΡΠΌΠΈ ΡΠ΅ΠΌΠΏΠ΅ΡΠ°ΡΡΡΠ½ΠΎ-Ρ ΠΈΠΌΠΈΡΠ΅ΡΠΊΠΈΠΌΠΈ Π²ΠΎΠ·Π΄Π΅ΠΉΡΡΠ²ΠΈΡΠΌΠΈ Π²Π½ΡΡΡΠ΅Π½Π½ΠΈΠ΅ ΠΏΠΎΠ²Π΅ΡΡ Π½ΠΎΡΡΠΈ ΠΊΠΎΠ½ΡΡΡΡΠΊΡΠΈΠΈ ΠΊΠΎΠ½Π²Π΅ΡΡΠ΅ΡΠ° Π±ΡΡΡΡΠΎ ΡΡΡΠ°ΡΠΈΠ²Π°ΡΡ ΡΠ²ΠΎΠΈ ΠΊΠ°ΡΠ΅ΡΡΠ²Π° β ΠΎΠΏΡΡΡ ΠΆΠ΅, ΡΡΠΎ ΠΊΠ°ΡΠ°Π΅ΡΡΡ Π²Π½Π΅ΡΠ½Π΅Π³ΠΎ ΠΈΠ·Π½ΠΎΡΠ° ΡΠ°Π±ΠΎΡΠ΅Π³ΠΎ ΡΠ»ΠΎΡ ΡΠ΅ΡΠΌΠΈΡΠ΅ΡΠΊΠΎΠΉ Π·Π°ΡΠΈΡΡ. Π ΠΊΠ°ΡΠ΅ΡΡΠ²Π΅ ΡΠ΅ΠΌΠΎΠ½ΡΠ½ΠΎΠΉ ΠΎΠΏΠ΅ΡΠ°ΡΠΈΠΈ ΠΏΡΠΈΠΌΠ΅Π½ΡΠ΅ΡΡΡ ΡΠΎΡΠΊΡΠ΅ΡΠΈΡΠΎΠ²Π°Π½ΠΈΠ΅ ΡΡΡΠ΅ΡΠΎΠ²ΠΊΠΈ. ΠΡΠΎ ΡΠ΅Ρ Π½ΠΎΠ»ΠΎΠ³ΠΈΡ Π³ΠΎΡΡΡΠ΅Π³ΠΎ Π²ΠΎΡΡΡΠ°Π½ΠΎΠ²Π»Π΅Π½ΠΈΡ, ΠΏΡΠΈ ΠΊΠΎΡΠΎΡΠΎΠΉ Ρ ΠΏΠΎΠΌΠΎΡΡΡ ΡΠΏΠ΅ΡΠΈΠ°Π»ΡΠ½ΠΎΠ³ΠΎ ΠΎΠ±ΠΎΡΡΠ΄ΠΎΠ²Π°Π½ΠΈΡ ΡΠΊΠ»Π°Π΄ΡΠ²Π°Π΅ΡΡΡ ΠΎΠ³Π½Π΅ΡΠΏΠΎΡΠ½ΡΠΉ ΡΠΎΡΡΠ°Π². ΠΠ³ΠΎ Π½Π°Π½ΠΎΡΡΡ Π½Π΅ ΡΠΏΠ»ΠΎΡΠ½ΡΠΌ ΡΠΏΠΎΡΠΎΠ±ΠΎΠΌ, Π° ΡΠΎΡΠ΅ΡΠ½ΠΎ Π½Π° ΡΠΈΠ»ΡΠ½ΠΎ ΠΈΠ·Π½ΠΎΡΠ΅Π½Π½ΡΠ΅ ΡΡΠ°ΡΡΠΊΠΈ Π±Π°Π·ΠΎΠ²ΠΎΠΉ ΡΡΡΠ΅ΡΠΎΠ²ΠΊΠΈ. ΠΡΠΎΡΠ΅Π΄ΡΡΠ° Π²ΡΠΏΠΎΠ»Π½ΡΠ΅ΡΡΡ Π½Π° ΡΠΏΠ΅ΡΠΈΠ°Π»ΡΠ½ΡΡ ΡΠΎΡΠΊΡΠ΅Ρ-ΠΌΠ°ΡΠΈΠ½Π°Ρ , ΠΏΠΎΠ΄Π°ΡΡΠΈΡ ΠΊ ΠΏΠΎΠ²ΡΠ΅ΠΆΠ΄Π΅Π½Π½ΠΎΠΌΡ ΡΡΠ°ΡΡΠΊΡ Π²ΠΎΠ΄ΠΎΠΎΡ Π»Π°ΠΆΠ΄Π°Π΅ΠΌΡΡ ΡΡΡΠΌΡ Ρ ΠΌΠ°ΡΡΠΎΠΉ ΠΈΠ· ΠΊΠΎΠΊΡΠΎΠ²ΠΎΠΉ ΠΏΡΠ»ΠΈ ΠΈ ΠΌΠ°Π³Π½Π΅Π·ΠΈΡΠΎΠ²ΠΎΠ³ΠΎ ΠΏΠΎΡΠΎΡΠΊΠ°.
Π’Π΅Ρ Π½ΠΎΠ»ΠΎΠ³ΠΈΠΈ Π²ΡΠΏΠ»Π°Π²ΠΊΠΈ
Π’ΡΠ°Π΄ΠΈΡΠΈΠΎΠ½Π½ΠΎ Π²ΡΠ΄Π΅Π»ΡΡΡ Π΄Π²Π° ΠΏΠΎΠ΄Ρ ΠΎΠ΄Π° ΠΊ ΡΠ΅Π°Π»ΠΈΠ·Π°ΡΠΈΠΈ ΠΊΠΈΡΠ»ΠΎΡΠΎΠ΄Π½ΠΎ-ΠΊΠΎΠ½Π²Π΅ΡΡΠ΅ΡΠ½ΠΎΠ³ΠΎ ΠΏΠ»Π°Π²Π»Π΅Π½ΠΈΡ β Π±Π΅ΡΡΠ΅ΠΌΠ΅ΡΠΎΠ²ΡΠΊΠΈΠΉ ΠΈ ΡΠΎΠΌΠ°ΡΠΎΠ²ΡΠΊΠΈΠΉ. ΠΠ΄Π½Π°ΠΊΠΎ ΡΠΎΠ²ΡΠ΅ΠΌΠ΅Π½Π½ΡΠ΅ ΠΌΠ΅ΡΠΎΠ΄ΠΈΠΊΠΈ ΠΎΡΠ»ΠΈΡΠ°ΡΡΡΡ ΠΎΡ Π½ΠΈΡ Π½ΠΈΠ·ΠΊΠΈΠΌ ΡΠΎΠ΄Π΅ΡΠΆΠ°Π½ΠΈΠ΅ΠΌ Π°Π·ΠΎΡΠ° Π² ΠΏΠ΅ΡΠΈ, ΡΡΠΎ ΠΏΠΎΠ²ΡΡΠ°Π΅Ρ ΠΊΠ°ΡΠ΅ΡΡΠ²ΠΎ ΡΠ°Π±ΠΎΡΠ΅Π³ΠΎ ΠΏΡΠΎΡΠ΅ΡΡΠ°. ΠΡΠΏΠΎΠ»Π½ΡΠ΅ΡΡΡ ΡΠ΅Ρ Π½ΠΎΠ»ΠΎΠ³ΠΈΡ ΠΏΠΎ ΡΠ»Π΅Π΄ΡΡΡΠΈΠΌ ΡΡΠ°ΠΏΠ°ΠΌ:
- ΠΠ°Π³ΡΡΠ·ΠΊΠ° Π»ΠΎΠΌΠ°. ΠΠΎΡΡΠ΄ΠΊΠ° 25-27 % ΠΎΡ ΠΎΠ±ΡΠ΅ΠΉ ΠΌΠ°ΡΡΡ ΡΠΈΡ ΡΡ Π·Π°Π³ΡΡΠΆΠ°Π΅ΡΡΡ Π² Π½Π°ΠΊΠ»ΠΎΠ½Π΅Π½Π½ΡΠΉ ΠΊΠΎΠ½Π²Π΅ΡΡΠ΅Ρ ΠΏΠΎΡΡΠ΅Π΄ΡΡΠ²ΠΎΠΌ ΡΠΎΠ²ΠΊΠΎΠ².
- ΠΠ°Π»ΠΈΠ²ΠΊΠ° ΡΡΠ³ΡΠ½Π° ΠΈΠ»ΠΈ ΡΡΠ°Π»ΡΠ½ΠΎΠ³ΠΎ ΡΠΏΠ»Π°Π²Π°. ΠΠΈΠ΄ΠΊΠΈΠΉ ΠΌΠ΅ΡΠ°Π»Π» ΠΏΡΠΈ ΡΠ΅ΠΌΠΏΠ΅ΡΠ°ΡΡΡΠ΅ Π΄ΠΎ 1450 Β°Π‘ ΠΊΠΎΠ²ΡΠ°ΠΌΠΈ Π·Π°Π»ΠΈΠ²Π°Π΅ΡΡΡ Π² Π½Π°ΠΊΠ»ΠΎΠ½Π΅Π½Π½ΡΠΉ ΠΊΠΎΠ½Π²Π΅ΡΡΠ΅Ρ. ΠΠΏΠ΅ΡΠ°ΡΠΈΡ ΠΏΡΠΎΠ΄ΠΎΠ»ΠΆΠ°Π΅ΡΡΡ Π½Π΅ Π±ΠΎΠ»Π΅Π΅ 3 ΠΌΠΈΠ½.
- ΠΡΠΎΠ΄ΡΠ²ΠΊΠ°. Π ΡΡΠΎΠΉ ΡΠ°ΡΡΠΈ ΡΠ΅Ρ Π½ΠΎΠ»ΠΎΠ³ΠΈΡ Π²ΡΠΏΠ»Π°Π²ΠΊΠΈ ΡΡΠ°Π»ΠΈ Π² ΠΊΠΈΡΠ»ΠΎΡΠΎΠ΄Π½ΡΡ ΠΊΠΎΠ½Π²Π΅ΡΡΠ΅ΡΠ°Ρ Π΄ΠΎΠΏΡΡΠΊΠ°Π΅Ρ ΡΠ°Π·Π½ΡΠ΅ ΠΏΠΎΠ΄Ρ ΠΎΠ΄Ρ Π² ΠΏΠ»Π°Π½Π΅ ΠΏΠΎΠ΄Π°ΡΠΈ Π³Π°Π·ΠΎ-Π²ΠΎΠ·Π΄ΡΡΠ½ΠΎΠΉ ΡΠΌΠ΅ΡΠΈ. ΠΠΎΡΠΎΠΊ ΠΌΠΎΠΆΠ΅Ρ Π½Π°ΠΏΡΠ°Π²Π»ΡΡΡΡΡ ΡΠ²Π΅ΡΡ Ρ, ΡΠ½ΠΈΠ·Ρ, Π΄ΠΎΠ½Π½ΡΠΌ ΠΈ ΠΊΠΎΠΌΠ±ΠΈΠ½ΠΈΡΠΎΠ²Π°Π½Π½ΡΠΌ ΡΠΏΠΎΡΠΎΠ±Π°ΠΌΠΈ Π² Π·Π°Π²ΠΈΡΠΈΠΌΠΎΡΡΠΈ ΠΎΡ ΡΠΈΠΏΠ° ΠΊΠΎΠ½ΡΡΡΡΠΊΡΠΈΠΈ ΠΎΠ±ΠΎΡΡΠ΄ΠΎΠ²Π°Π½ΠΈΡ.
- ΠΠΎΠ»ΡΡΠ΅Π½ΠΈΠ΅ ΠΏΡΠΎΠ±. ΠΡΠΏΠΎΠ»Π½ΡΠ΅ΡΡΡ Π·Π°ΠΌΠ΅Ρ ΡΠ΅ΠΌΠΏΠ΅ΡΠ°ΡΡΡΡ, ΡΠ΄Π°Π»ΡΡΡΡΡ Π½Π΅Π½ΡΠΆΠ½ΡΠ΅ ΠΏΡΠΈΠΌΠ΅ΡΠΈ, ΠΎΠΆΠΈΠ΄Π°Π΅ΡΡΡ Π°Π½Π°Π»ΠΈΠ· ΡΠΎΡΡΠ°Π²Π°. ΠΡΠ»ΠΈ Π΅Π³ΠΎ ΡΠ΅Π·ΡΠ»ΡΡΠ°ΡΡ ΡΠΎΠΎΡΠ²Π΅ΡΡΡΠ²ΡΡΡ ΠΏΡΠΎΠ΅ΠΊΡΠ½ΡΠΌ ΡΡΠ΅Π±ΠΎΠ²Π°Π½ΠΈΡΠΌ, ΠΏΠ»Π°Π²ΠΊΠ° Π²ΡΠΏΡΡΠΊΠ°Π΅ΡΡΡ, Π° Π΅ΡΠ»ΠΈ Π½Π΅Ρ β Π²Π½ΠΎΡΡΡΡΡ ΠΊΠΎΡΡΠ΅ΠΊΡΠΈΡΠΎΠ²ΠΊΠΈ.

ΠΠ»ΡΡΡ ΠΈ ΠΌΠΈΠ½ΡΡΡ ΡΠ΅Ρ Π½ΠΎΠ»ΠΎΠ³ΠΈΠΈ
Π‘ΠΏΠΎΡΠΎΠ± ΡΠ΅Π½ΠΈΡΡΡ Π·Π° Π²ΡΡΠΎΠΊΡΡ ΠΏΡΠΎΠΈΠ·Π²ΠΎΠ΄ΠΈΡΠ΅Π»ΡΠ½ΠΎΡΡΡ, ΠΏΡΠΎΡΡΡΠ΅ ΡΡ Π΅ΠΌΡ ΠΏΠΎΠ΄Π°ΡΠΈ ΠΊΠΈΡΠ»ΠΎΡΠΎΠ΄Π°, ΠΊΠΎΠ½ΡΡΡΡΠΊΡΠΈΠΎΠ½Π½ΡΡ Π½Π°Π΄Π΅ΠΆΠ½ΠΎΡΡΡ ΠΈ ΠΎΡΠ½ΠΎΡΠΈΡΠ΅Π»ΡΠ½ΠΎ Π½ΠΈΠ·ΠΊΠΈΠ΅ ΡΠ°ΡΡ ΠΎΠ΄Ρ Π² ΡΠ΅Π»ΠΎΠΌ Π½Π° ΠΎΡΠ³Π°Π½ΠΈΠ·Π°ΡΠΈΡ ΠΏΡΠΎΡΠ΅ΡΡΠ°. Π§ΡΠΎ ΠΊΠ°ΡΠ°Π΅ΡΡΡ Π½Π΅Π΄ΠΎΡΡΠ°ΡΠΊΠΎΠ², ΡΠΎ ΠΊ Π½ΠΈΠΌ, Π² ΡΠ°ΡΡΠ½ΠΎΡΡΠΈ, ΠΎΡΠ½ΠΎΡΡΡΡΡ ΠΎΠ³ΡΠ°Π½ΠΈΡΠ΅Π½ΠΈΡ Π² ΠΏΠ»Π°Π½Π΅ Π΄ΠΎΠ±Π°Π²Π»Π΅Π½ΠΈΡ ΡΠ»Π°ΠΌΠ° ΠΈ Π²ΡΠΎΡΡΡΡΡΡ. Π’ΠΎΡ ΠΆΠ΅ Π»ΠΎΠΌ ΠΌΠ΅ΡΠ°Π»Π»Π° Ρ Π΄ΡΡΠ³ΠΈΠΌΠΈ Π²ΠΊΠ»ΡΡΠ΅Π½ΠΈΡΠΌΠΈ ΠΌΠΎΠΆΠ΅Ρ ΡΠΎΡΡΠ°Π²Π»ΡΡΡ Π½Π΅ Π±ΠΎΠ»Π΅Π΅ 10 %, Π° ΡΡΠΎ Π½Π΅ ΠΏΠΎΠ·Π²ΠΎΠ»ΡΠ΅Ρ Π² Π½ΡΠΆΠ½ΠΎΠΉ ΡΡΠ΅ΠΏΠ΅Π½ΠΈ ΠΌΠΎΠ΄ΠΈΡΠΈΡΠΈΡΠΎΠ²Π°ΡΡ ΡΡΡΡΠΊΡΡΡΡ Π²ΡΠΏΠ»Π°Π²ΠΊΠΈ. Π’Π°ΠΊΠΆΠ΅ ΠΏΡΠΈ Π²ΡΠ΄ΡΠ²ΠΊΠ΅ ΡΠ°ΡΡ ΠΎΠ΄ΡΠ΅ΡΡΡ Π±ΠΎΠ»ΡΡΠΎΠΉ ΠΎΠ±ΡΠ΅ΠΌ ΠΏΠΎΠ»Π΅Π·Π½ΠΎΠ³ΠΎ ΠΆΠ΅Π»Π΅Π·Π°.
ΠΡΠΈΠΌΠ΅Π½Π΅Π½ΠΈΠ΅ ΡΠ΅Ρ Π½ΠΎΠ»ΠΎΠ³ΠΈΠΈ
Π‘ΠΎΡΠ΅ΡΠ°Π½ΠΈΠ΅ ΠΏΠ»ΡΡΠΎΠ² ΠΈ ΠΌΠΈΠ½ΡΡΠΎΠ² Π² ΠΈΡΠΎΠ³Π΅ ΠΎΠ±ΡΡΠ»ΠΎΠ²ΠΈΠ»ΠΎ ΠΈ Ρ Π°ΡΠ°ΠΊΡΠ΅Ρ ΠΏΡΠΈΠΌΠ΅Π½Π΅Π½ΠΈΡ ΠΊΠΎΠ½Π²Π΅ΡΡΠ΅ΡΠΎΠ². Π ΡΠ°ΡΡΠ½ΠΎΡΡΠΈ, ΠΌΠ΅ΡΠ°Π»Π»ΡΡΠ³ΠΈΡΠ΅ΡΠΊΠΈΠ΅ ΠΊΠΎΠΌΠ±ΠΈΠ½Π°ΡΡ Π²ΡΠΏΡΡΠΊΠ°ΡΡ Π½ΠΈΠ·ΠΊΠΎΠ»Π΅Π³ΠΈΡΠΎΠ²Π°Π½Π½ΡΡ, ΡΠ³Π»Π΅ΡΠΎΠ΄ΠΈΡΡΡΡ ΠΈ Π»Π΅Π³ΠΈΡΠΎΠ²Π°Π½Π½ΡΡ ΡΡΠ°Π»Ρ Π²ΡΡΠΎΠΊΠΎΠ³ΠΎ ΠΊΠ°ΡΠ΅ΡΡΠ²Π°, Π΄ΠΎΡΡΠ°ΡΠΎΡΠ½ΠΎΠ³ΠΎ Π΄Π»Ρ ΠΏΡΠΈΠΌΠ΅Π½Π΅Π½ΠΈΡ ΠΌΠ°ΡΠ΅ΡΠΈΠ°Π»Π° Π² ΡΡΠΆΠ΅Π»ΠΎΠΉ ΠΏΡΠΎΠΌΡΡΠ»Π΅Π½Π½ΠΎΡΡΠΈ ΠΈ ΡΡΡΠΎΠΈΡΠ΅Π»ΡΡΡΠ²Π΅. ΠΠΎΠ»ΡΡΠ΅Π½ΠΈΠ΅ ΡΡΠ°Π»Π΅ΠΉ Π² ΠΊΠΈΡΠ»ΠΎΡΠΎΠ΄Π½ΠΎΠΌ ΠΊΠΎΠ½Π²Π΅ΡΡΠ΅ΡΠ΅ ΠΏΡΠΎΠΈΡΡ ΠΎΠ΄ΠΈΡ Ρ Π»Π΅Π³ΠΈΡΠΎΠ²Π°Π½ΠΈΠ΅ΠΌ ΠΈ ΡΠ»ΡΡΡΠ΅Π½ΠΈΠ΅ΠΌ ΠΎΡΠ΄Π΅Π»ΡΠ½ΡΡ ΡΠ²ΠΎΠΉΡΡΠ², ΡΡΠΎ ΡΠ°ΡΡΠΈΡΡΠ΅Ρ ΡΡΠ΅ΡΡ ΠΏΡΠΈΠΌΠ΅Π½Π΅Π½ΠΈΡ ΠΊΠΎΠ½Π΅ΡΠ½ΠΎΠΉ ΠΏΡΠΎΠ΄ΡΠΊΡΠΈΠΈ. ΠΠ· ΠΏΠΎΠ»ΡΡΠ°Π΅ΠΌΠΎΠ³ΠΎ ΡΡΡΡΡ ΠΈΠ·Π³ΠΎΡΠ°Π²Π»ΠΈΠ²Π°ΡΡ ΡΡΡΠ±Ρ, ΠΏΡΠΎΠ²ΠΎΠ»ΠΎΠΊΡ, ΡΠ΅Π»ΡΡΡ, ΠΌΠ΅ΡΠΈΠ·Ρ, ΡΠΊΠΎΠ±ΡΠ½ΡΠ΅ ΠΈΠ·Π΄Π΅Π»ΠΈΡ ΠΈ Ρ. Π΄. Π’Π΅Ρ Π½ΠΎΠ»ΠΎΠ³ΠΈΡ ΡΠΈΡΠΎΠΊΠΎ ΠΏΡΠΈΠΌΠ΅Π½ΡΠ΅ΡΡΡ ΠΈ Π² ΡΠ²Π΅ΡΠ½ΠΎΠΉ ΠΌΠ΅ΡΠ°Π»Π»ΡΡΠ³ΠΈΠΈ, Π³Π΄Π΅ ΠΏΡΠΈ Π΄ΠΎΡΡΠ°ΡΠΎΡΠ½ΠΎΠΉ ΠΏΡΠΎΠ΄ΡΠ²ΠΊΠ΅ ΠΏΠΎΠ»ΡΡΠ°ΡΡ ΡΠ΅ΡΠ½ΠΎΠ²ΡΡ ΠΌΠ΅Π΄Ρ.

ΠΠ°ΠΊΠ»ΡΡΠ΅Π½ΠΈΠ΅
ΠΠ»Π°Π²ΠΊΠ° Π² ΠΊΠΎΠ½Π²Π΅ΡΡΠ΅ΡΠ½ΡΡ ΡΠΎΠΎΡΡΠΆΠ΅Π½ΠΈΡΡ ΡΡΠΈΡΠ°Π΅ΡΡΡ ΠΌΠΎΡΠ°Π»ΡΠ½ΠΎ ΡΡΡΠ°ΡΠ΅Π²ΡΠ΅ΠΉ ΡΠ΅Ρ Π½ΠΈΠΊΠΎΠΉ, Π½ΠΎ Π΅Π΅ ΠΏΡΠΎΠ΄ΠΎΠ»ΠΆΠ°ΡΡ ΠΈΡΠΏΠΎΠ»ΡΠ·ΠΎΠ²Π°ΡΡ ΠΏΠΎ ΠΏΡΠΈΡΠΈΠ½Π°ΠΌ ΠΎΠΏΡΠΈΠΌΠ°Π»ΡΠ½ΠΎΠ³ΠΎ ΡΠΎΡΠ΅ΡΠ°Π½ΠΈΡ ΠΏΡΠΎΠΈΠ·Π²ΠΎΠ΄ΠΈΡΠ΅Π»ΡΠ½ΠΎΡΡΠΈ ΠΈ ΡΠΈΠ½Π°Π½ΡΠΎΠ²ΡΡ Π·Π°ΡΡΠ°Ρ Π½Π° ΠΎΠ±Π΅ΡΠΏΠ΅ΡΠ΅Π½ΠΈΠ΅ ΠΏΡΠΎΡΠ΅ΡΡΠ°. Π Π½Π΅ΠΌΠ°Π»ΠΎΠΉ ΡΡΠ΅ΠΏΠ΅Π½ΠΈ Π²ΠΎΡΡΡΠ΅Π±ΠΎΠ²Π°Π½Π½ΠΎΡΡΠΈ ΡΠ΅Ρ Π½ΠΎΠ»ΠΎΠ³ΠΈΠΈ ΡΠΏΠΎΡΠΎΠ±ΡΡΠ²ΡΡΡ ΠΈ ΠΊΠΎΠ½ΡΡΡΡΠΊΡΠΈΠΎΠ½Π½ΡΠ΅ Π΄ΠΎΡΡΠΎΠΈΠ½ΡΡΠ²Π° ΠΏΡΠΈΠΌΠ΅Π½ΡΠ΅ΠΌΠΎΠ³ΠΎ ΠΎΠ±ΠΎΡΡΠ΄ΠΎΠ²Π°Π½ΠΈΡ. Π’Π° ΠΆΠ΅ Π²ΠΎΠ·ΠΌΠΎΠΆΠ½ΠΎΡΡΡ ΠΏΡΡΠΌΠΎΠΉ Π·Π°Π³ΡΡΠ·ΠΊΠΈ Π»ΠΎΠΌΠ° ΠΌΠ΅ΡΠ°Π»Π»Π°, ΡΠΈΡ ΡΡ, ΡΠ»Π°ΠΌΠ° ΠΈ Π΄ΡΡΠ³ΠΈΡ ΠΎΡΡ ΠΎΠ΄ΠΎΠ², Ρ ΠΎΡΡ ΠΈ Π² ΠΎΠ³ΡΠ°Π½ΠΈΡΠ΅Π½Π½ΠΎΠΌ ΠΎΠ±ΡΠ΅ΠΌΠ΅, ΡΠ°ΡΡΠΈΡΡΠ΅Ρ Π²ΠΎΠ·ΠΌΠΎΠΆΠ½ΠΎΡΡΠΈ Π΄Π»Ρ ΠΌΠΎΠ΄ΠΈΡΠΈΠΊΠ°ΡΠΈΠΈ ΡΠΏΠ»Π°Π²Π°. ΠΡΡΠ³ΠΎΠ΅ Π΄Π΅Π»ΠΎ, ΡΡΠΎ Π΄Π»Ρ ΠΏΠΎΠ»Π½ΠΎΡΠ΅Π½Π½ΠΎΠΉ ΡΠΊΡΠΏΠ»ΡΠ°ΡΠ°ΡΠΈΠΈ ΠΊΡΡΠΏΠ½ΠΎΠ³Π°Π±Π°ΡΠΈΡΠ½ΡΡ ΠΊΠΎΠ½Π²Π΅ΡΡΠ΅ΡΠΎΠ² Ρ Π²ΠΎΠ·ΠΌΠΎΠΆΠ½ΠΎΡΡΡΠΌΠΈ ΠΏΠΎΠ²ΠΎΡΠΎΡΠ° ΡΡΠ΅Π±ΡΠ΅ΡΡΡ ΠΎΡΠ³Π°Π½ΠΈΠ·Π°ΡΠΈΡ ΡΠΎΠΎΡΠ²Π΅ΡΡΡΠ²ΡΡΡΠ΅Π³ΠΎ ΠΏΠΎΠΌΠ΅ΡΠ΅Π½ΠΈΡ Π½Π° ΠΏΡΠ΅Π΄ΠΏΡΠΈΡΡΠΈΠΈ. ΠΠΎΡΡΠΎΠΌΡ ΠΎΡΡΡΠ΅ΡΡΠ²Π»ΡΡΡ Π²ΡΠΏΠ»Π°Π²ΠΊΡ Ρ ΠΊΠΈΡΠ»ΠΎΡΠΎΠ΄Π½ΠΎΠΉ ΠΏΡΠΎΠ΄ΡΠ²ΠΊΠΎΠΉ Π² Π±ΠΎΠ»ΡΡΠΈΡ ΠΎΠ±ΡΠ΅ΠΌΠ°Ρ ΠΏΡΠ΅ΠΈΠΌΡΡΠ΅ΡΡΠ²Π΅Π½Π½ΠΎ ΠΊΡΡΠΏΠ½ΡΠ΅ ΠΊΠΎΠΌΠΏΠ°Π½ΠΈΠΈ.
ΠΠΈΡΠ»ΠΎΡΠΎΠ΄Π½ΠΎ-ΠΊΠΎΠ½Π²Π΅ΡΡΠ΅ΡΠ½ΡΠΉ ΡΠΏΠΎΡΠΎΠ± ΠΏΡΠΎΠΈΠ·Π²ΠΎΠ΄ΡΡΠ²Π° ΡΡΠ°Π»ΠΈ: Π²ΠΈΠ΄Ρ ΠΈ ΠΏΡΠΎΡΠ΅ΡΡ
ΠΠΊΠΎΠ»ΠΎ 70% ΡΡΠ°Π»ΠΈ ΠΎΡ ΠΎΠ±ΡΠ΅Π³ΠΎ ΠΎΠ±ΡΠ΅ΠΌΠ° ΠΌΠΈΡΠΎΠ²ΠΎΠ³ΠΎ ΠΏΡΠΎΠΈΠ·Π²ΠΎΠ΄ΡΡΠ²Π° ΠΈΠ·Π³ΠΎΡΠ°Π²Π»ΠΈΠ²Π°Π΅ΡΡΡ ΠΊΠΎΠ½Π²Π΅ΡΡΠ΅ΡΠ½ΡΠΌ ΡΠΏΠΎΡΠΎΠ±ΠΎΠΌ. ΠΠΎ ΡΠ΅ΡΠ΅Π΄ΠΈΠ½Ρ ΠΏΡΠΎΡΠ»ΠΎΠ³ΠΎ ΡΡΠΎΠ»Π΅ΡΠΈΡ Π΄Π»Ρ ΠΏΠΎΠ»ΡΡΠ΅Π½ΠΈΡ ΡΡΠ°Π»ΠΈ ΠΏΡΠΈΠΌΠ΅Π½ΡΠ»ΠΈΡΡ Π±Π΅ΡΡΠ΅ΠΌΠ΅ΡΠΎΠ²ΡΠΊΠΈΠΉ ΠΈ ΡΠΎΠΌΠ°ΡΠΎΠ²ΡΠΊΠΈΠΉ ΠΏΡΠΎΡΠ΅ΡΡΡ. ΠΠ΄Π½Π°ΠΊΠΎ Π² Π΄Π°Π»ΡΠ½Π΅ΠΉΡΠ΅ΠΌ ΡΡΠ°Π»Ρ Π½Π°ΡΠ°Π»ΠΈ ΠΏΡΠΎΠΈΠ·Π²ΠΎΠ΄ΠΈΡΡ ΡΡΠΎΠ²Π΅ΡΡΠ΅Π½ΡΡΠ²ΠΎΠ²Π°Π½Π½ΡΠΌ ΠΊΠΈΡΠ»ΠΎΡΠΎΠ΄Π½ΠΎ-ΠΊΠΎΠ½Π²Π΅ΡΡΠ΅ΡΠ½ΡΠΌ ΡΠΏΠΎΡΠΎΠ±ΠΎΠΌ. Π Π½Π°ΡΡΠΎΡΡΠ΅Π΅ Π²ΡΠ΅ΠΌΡ ΠΏΡΠ΅Π΄ΡΠ΅ΡΡΠ²Π΅Π½Π½ΠΈΠΊΠΈ ΡΠΎΠ²ΡΠ΅ΠΌΠ΅Π½Π½ΠΎΠ³ΠΎ ΠΌΠ΅ΡΠΎΠ΄Π° ΠΏΡΠ°ΠΊΡΠΈΡΠ΅ΡΠΊΠΈ Π½Π΅ ΠΏΡΠΈΠΌΠ΅Π½ΡΡΡΡΡ.
Π‘ΡΡΡ ΠΊΠΎΠ½Π²Π΅ΡΡΠ΅ΡΠ½ΠΎΠ³ΠΎ ΠΏΡΠΎΠΈΠ·Π²ΠΎΠ΄ΡΡΠ²Π°
Π ΠΊΠΎΠ½Π²Π΅ΡΡΠ΅ΡΠ½ΠΎΠΌ ΠΏΡΠΎΠΈΠ·Π²ΠΎΠ΄ΡΡΠ²Π΅ ΠΏΡΠΈΠΌΠ΅Π½ΡΡΡΡΡ ΡΠΏΠ΅ΡΠΈΠ°Π»ΡΠ½ΡΠ΅ ΡΡΠ°Π»Π΅ΠΏΠ»Π°Π²ΠΈΠ»ΡΠ½ΡΠ΅ Π°Π³ΡΠ΅Π³Π°ΡΡ, Π½Π°Π·ΡΠ²Π°Π΅ΠΌΡΠ΅ ΠΊΠΎΠ½Π²Π΅ΡΡΠ΅ΡΠ°ΠΌΠΈ. ΠΡΠΎΠΈΠ·Π²ΠΎΠ΄ΡΡΠ²ΠΎ ΡΡΠ°Π»ΠΈ ΠΎΡΡΡΠ΅ΡΡΠ²Π»ΡΠ΅ΡΡΡ ΠΏΡΡΠ΅ΠΌ ΠΏΡΠΎΠ΄ΡΠ²ΠΊΠΈ ΠΆΠΈΠ΄ΠΊΠΎΠ³ΠΎ ΡΡΠ³ΡΠ½Π° Π²ΠΎΠ·Π΄ΡΡ ΠΎΠΌ ΠΈΠ»ΠΈ ΠΊΠΈΡΠ»ΠΎΡΠΎΠ΄ΠΎΠΌ. ΠΠ°Π½Π½ΡΠΉ ΠΌΠ΅ΡΠ°Π»Π» ΡΠΎΠ΄Π΅ΡΠΆΠΈΡ ΡΠ°Π·Π»ΠΈΡΠ½ΡΠ΅ ΠΏΡΠΈΠΌΠ΅ΡΠΈ, Π² ΡΠΎΠΌ ΡΠΈΡΠ»Π΅ ΠΊΡΠ΅ΠΌΠ½ΠΈΠΉ, ΡΠ³Π»Π΅ΡΠΎΠ΄ ΠΈ ΠΌΠ°ΡΠ³Π°Π½Π΅Ρ. ΠΡΠΈΠΌΠ΅ΡΠΈ ΠΎΠΊΠΈΡΠ»ΡΡΡΡΡ ΠΏΠΎΠ΄ Π΄Π΅ΠΉΡΡΠ²ΠΈΠ΅ΠΌ ΠΊΠΈΡΠ»ΠΎΡΠΎΠ΄Π° ΠΈ ΡΠ΄Π°Π»ΡΡΡΡΡ ΠΈΠ· ΡΠ°ΡΠΏΠ»Π°Π²Π°. ΠΡΠ½ΠΎΠ²Π½ΡΠΌ ΠΏΡΠ΅ΠΈΠΌΡΡΠ΅ΡΡΠ²ΠΎΠΌ ΠΊΠΎΠ½Π²Π΅ΡΡΠ΅ΡΠ½ΠΎΠ³ΠΎ ΡΠΏΠΎΡΠΎΠ±Π° ΡΠ²Π»ΡΠ΅ΡΡΡ ΡΠΎ, ΡΡΠΎ Π΄Π»Ρ ΡΠ°Π±ΠΎΡΡ ΡΡΠ°Π»Π΅ΠΏΠ»Π°Π²ΠΈΠ»ΡΠ½ΠΎΠ³ΠΎ ΡΡΡΡΠΎΠΉΡΡΠ²Π° Π½Π΅ ΡΡΠ΅Π±ΡΠ΅ΡΡΡ ΡΠΎΠΏΠ»ΠΈΠ²ΠΎ. Π‘ΡΠ°Π»Ρ ΡΠ°ΡΠΏΠ»Π°Π²Π»ΡΠ΅ΡΡΡ ΠΏΠΎΠ΄ Π΄Π΅ΠΉΡΡΠ²ΠΈΠ΅ΠΌ ΡΠ΅ΠΏΠ»Π°, ΠΊΠΎΡΠΎΡΠΎΠ΅ Π²ΡΠ΄Π΅Π»ΡΡΡ ΠΎΠΊΠΈΡΠ»ΡΡΡΠΈΠ΅ΡΡ ΠΏΡΠΈΠΌΠ΅ΡΠΈ.
ΠΡΠΈΠ½ΡΠΈΠΏ Π±Π΅ΡΡΠ΅ΠΌΠ΅ΡΠΎΠ²ΡΠΊΠΎΠ³ΠΎ ΡΠΏΠΎΡΠΎΠ±Π°
ΠΠΏΠ΅ΡΠ²ΡΠ΅ ΠΌΠ°ΡΡΠΎΠ²ΠΎΠ΅ ΠΏΠΎΠ»ΡΡΠ΅Π½ΠΈΠ΅ ΠΆΠΈΠ΄ΠΊΠΎΠΉ ΡΡΠ°Π»ΠΈ ΡΡΠ°Π»ΠΎ Π²ΠΎΠ·ΠΌΠΎΠΆΠ½ΡΠΌ Π² 1856 Π³ΠΎΠ΄Ρ Π±Π»Π°Π³ΠΎΠ΄Π°ΡΡ Π. ΠΠ΅ΡΡΠ΅ΠΌΠ΅ΡΡ β ΠΈΠ·ΠΎΠ±ΡΠ΅ΡΠ°ΡΠ΅Π»Ρ ΠΈΠ· ΠΠ½Π³Π»ΠΈΠΈ. ΠΠ½ ΠΏΡΠΈΠ΄ΡΠΌΠ°Π», ΠΊΠ°ΠΊ Π½Π°Π³ΡΠ΅ΡΡ ΠΌΠ΅ΡΠ°Π»Π» Π΄ΠΎ ΡΠ΅ΠΌΠΏΠ΅ΡΠ°ΡΡΡΡ, ΠΏΡΠ΅Π²ΡΡΠ°ΡΡΠ΅ΠΉ 1500Β°Π‘. ΠΠΌΠ΅Π½Π½ΠΎ ΡΠ°ΠΊΠ°Ρ ΡΠ΅ΠΌΠΏΠ΅ΡΠ°ΡΡΡΠ° Π½Π΅ΠΎΠ±Ρ ΠΎΠ΄ΠΈΠΌΠ° Π΄Π»Ρ ΡΠΎΠ³ΠΎ, ΡΡΠΎΠ±Ρ ΡΠ°ΡΠΏΠ»Π°Π²ΠΈΡΡ ΠΌΠ΅ΡΠ°Π»Π» Ρ ΠΏΠΎΠ½ΠΈΠΆΠ΅Π½Π½ΡΠΌ ΡΠΎΠ΄Π΅ΡΠΆΠ°Π½ΠΈΠ΅ΠΌ ΡΠ³Π»Π΅ΡΠΎΠ΄Π°.
ΠΠ΅ΡΡΠ΅ΠΌΠ΅ΡΠΎΠ²ΡΠΊΠΈΠΉ ΠΏΡΠΎΡΠ΅ΡΡ ΠΏΡΠ΅Π΄ΡΡΠΌΠ°ΡΡΠΈΠ²Π°Π΅Ρ ΠΏΡΠΎΠ΄ΡΠ²ΠΊΡ ΡΠ°ΡΠΏΠ»Π°Π²Π° Π°ΡΠΌΠΎΡΡΠ΅ΡΠ½ΡΠΌ Π²ΠΎΠ·Π΄ΡΡ ΠΎΠΌ. ΠΠ»Ρ ΡΡΠΈΡ ΡΠ΅Π»Π΅ΠΉ ΠΏΡΠΈΠΌΠ΅Π½ΡΡΡΡΡ ΠΊΠΎΠ½Π²Π΅ΡΡΠ΅ΡΡ, Ρ ΠΊΠΎΡΠΎΡΡΡ Π²Π½ΡΡΡΠ΅Π½Π½ΡΡ ΡΠ°ΡΡΡ ΠΊΠ°ΠΌΠ΅ΡΡ ΡΠ³ΠΎΡΠ°Π½ΠΈΡ Π·Π°ΡΠΈΡΠ΅Π½Π° Π΄ΠΈΠ½Π°ΡΠΎΠ²ΡΠΌ ΠΊΠΈΡΠΏΠΈΡΠΎΠΌ. ΠΠ»Π°Π³ΠΎΠ΄Π°ΡΡ ΡΠ°ΠΊΠΎΠΉ Π·Π°ΡΠΈΡΠ΅ Π±Π΅ΡΡΠ΅ΠΌΠ΅ΡΠΎΠ²ΡΠΊΠΈΠΉ ΡΠΏΠΎΡΠΎΠ± Π½Π°Π·ΡΠ²Π°ΡΡ ΠΊΠΈΡΠ»ΠΎΠΉ ΡΡΡΠ΅ΡΠΎΠ²ΠΊΠΎΠΉ ΠΊΠΎΠ½Π²Π΅ΡΡΠ΅ΡΠ°.
ΠΠ»Π°Π²ΠΊΠ° Π² Π±Π΅ΡΡΠ΅ΠΌΠ΅ΡΠΎΠ²ΡΠΊΠΎΠΌ ΡΡΠ°Π»Π΅ΠΏΠ»Π°Π²ΠΈΠ»ΡΠ½ΠΎΠΌ Π°Π³ΡΠ΅Π³Π°ΡΠ΅ ΠΎΡΡΡΠ΅ΡΡΠ²Π»ΡΠ΅ΡΡΡ ΠΏΡΡΠ΅ΠΌ Π·Π°Π»ΠΈΠ²ΠΊΠΈ ΡΡΠ³ΡΠ½Π° ΠΏΡΠΈ ΡΠ΅ΠΌΠΏΠ΅ΡΠ°ΡΡΡΠ΅ 1250β1300Β°Π‘. Π‘Π»Π΅Π΄ΡΠ΅Ρ Π·Π°ΠΌΠ΅ΡΠΈΡΡ, ΡΡΠΎ Π΄Π»Ρ Π²ΡΠΏΠ»Π°Π²ΠΊΠΈ Π±Π΅ΡΡΠ΅ΠΌΠ΅ΡΠΎΠ²ΡΠΊΠΈΡ ΡΡΠ³ΡΠ½ΠΎΠ² ΡΡΠ΅Π±ΡΡΡΡΡ ΠΆΠ΅Π»Π΅Π·Π½ΡΠ΅ ΡΡΠ΄Ρ Ρ Π½ΠΈΠ·ΠΊΠΈΠΌ ΡΠΎΠ΄Π΅ΡΠΆΠ°Π½ΠΈΠ΅ΠΌ ΡΠ΅ΡΡ ΠΈ ΡΠΎΡΡΠΎΡΠ°.
ΠΠ°Π»ΠΈΡΡΠΉ ΡΡΠ³ΡΠ½ ΠΏΡΠΎΠ΄ΡΠ²Π°ΡΡ Π²ΠΎΠ·Π΄ΡΡ ΠΎΠΌ, Π² ΡΠ΅Π·ΡΠ»ΡΡΠ°ΡΠ΅ ΡΠ΅Π³ΠΎ ΠΏΡΠΎΠΈΡΡ ΠΎΠ΄ΠΈΡ ΠΎΠΊΠΈΡΠ»Π΅Π½ΠΈΠ΅ ΡΠ³Π»Π΅ΡΠΎΠ΄Π°, ΠΌΠ°ΡΠ³Π°Π½ΡΠ° ΠΈ ΠΊΡΠ΅ΠΌΠ½ΠΈΡ. ΠΡΠΈ ΠΎΠΊΠΈΡΠ»Π΅Π½ΠΈΠΈ ΠΎΠ±ΡΠ°Π·ΡΡΡΡΡ ΠΎΠΊΡΠΈΠ΄Ρ, ΡΠΎΡΠΌΠΈΡΡΡΡΠΈΠ΅ ΠΊΠΈΡΠ»ΡΠΉ ΡΠ»Π°ΠΊ. ΠΡΠΎΠ΄ΡΠ²ΠΊΡ Π²ΠΎΠ·Π΄ΡΡ ΠΎΠΌ Π·Π°ΠΊΠ°Π½ΡΠΈΠ²Π°ΡΡ ΠΏΠΎΡΠ»Π΅ ΡΠΎΠ³ΠΎ, ΠΊΠ°ΠΊ ΡΠ³Π»Π΅ΡΠΎΠ΄ ΠΎΠΊΠΈΡΠ»ΠΈΡΡΡ Π΄ΠΎ ΡΡΠ΅Π±ΡΠ΅ΠΌΡΡ Π·Π½Π°ΡΠ΅Π½ΠΈΠΉ.
ΠΠ°Π»Π΅Π΅ ΠΌΠ΅ΡΠ°Π»Π» ΡΠ΅ΡΠ΅Π· Π³ΠΎΡΠ»ΠΎΠ²ΠΈΠ½Ρ ΡΠ»ΠΈΠ²Π°ΡΡ Π² ΠΊΠΎΠ²Ρ, ΠΏΠΎΠΏΡΡΠ½ΠΎ Π΅Π³ΠΎ ΠΎΠΊΠΈΡΠ»ΡΡ. Π£ ΡΠ°ΠΊΠΎΠ³ΠΎ ΡΠΏΠΎΡΠΎΠ±Π° ΠΏΡΠΈΡΡΡΡΡΠ²ΡΠ΅Ρ ΠΎΠ΄ΠΈΠ½ ΡΡΡΠ΅ΡΡΠ²Π΅Π½Π½ΡΠΉ Π½Π΅Π΄ΠΎΡΡΠ°ΡΠΎΠΊ, Π·Π°ΠΊΠ»ΡΡΠ°ΡΡΠΈΠΉΡΡ Π² Π½Π΅Π²ΡΡΠΎΠΊΠΎΠΌ ΠΊΠ°ΡΠ΅ΡΡΠ²Π΅ ΠΊΠΎΠ½Π΅ΡΠ½ΠΎΠ³ΠΎ ΠΏΡΠΎΠ΄ΡΠΊΡΠ°, ΠΊΠΎΡΠΎΡΡΠΉ ΠΏΠΎΠ»ΡΡΠ°Π΅ΡΡΡ ΡΠ»ΠΈΡΠΊΠΎΠΌ Ρ ΡΡΠΏΠΊΠΈΠΌ Π·Π° ΡΡΠ΅Ρ Π½Π΅ΠΏΠΎΠ»Π½ΠΎΠ³ΠΎ ΡΠ΄Π°Π»Π΅Π½ΠΈΡ ΡΠ΅ΡΡ ΠΈ ΡΠΎΡΡΠΎΡΠ°.
ΠΡΠΈΠ½ΡΠΈΠΏ ΡΠΎΠΌΠ°ΡΠΎΠ²ΡΠΊΠΎΠ³ΠΎ ΡΠΏΠΎΡΠΎΠ±Π°
Π 1878 Π³ΠΎΠ΄Ρ Π°Π½Π³Π»ΠΈΡΠ°Π½ΠΈΠ½Ρ Π‘.Π. Π’ΠΎΠΌΠ°ΡΡ ΡΠ΄Π°Π»ΠΎΡΡ ΡΡΡΡΠ°Π½ΠΈΡΡ Π³Π»Π°Π²Π½ΡΠΉ Π½Π΅Π΄ΠΎΡΡΠ°ΡΠΎΠΊ Π±Π΅ΡΡΠ΅ΠΌΠ΅ΡΠΎΠ²ΡΠΊΠΎΠ³ΠΎ ΡΠΏΠΎΡΠΎΠ±Π°. ΠΠΈΡΠ»ΡΡ ΡΡΡΠ΅ΡΠΎΠ²ΠΊΡ ΠΊΠΎΠ½Π²Π΅ΡΡΠ΅ΡΠ° ΠΎΠ½ Π·Π°ΠΌΠ΅Π½ΠΈΠ» ΠΎΡΠ½ΠΎΠ²Π½ΠΎΠΉ. ΠΠ½ΡΡΡΠ΅Π½Π½ΠΈΠΉ Π·Π°ΡΠΈΡΠ½ΡΠΉ ΡΠ»ΠΎΠΉ Π² Π²Π°Π½Π½ΠΎΠΉ Π±ΡΠ» Π²ΡΠ»ΠΎΠΆΠ΅Π½ ΡΠΌΠΎΠ»ΠΎΠ΄ΠΎΠ»ΠΎΠΌΠΈΡΠΎΠ²ΡΠΌ ΠΊΠΈΡΠΏΠΈΡΠΎΠΌ. Π ΡΡΠΎΠ±Ρ ΡΠ΄Π°Π»ΠΈΡΡ ΠΈΠ· ΠΌΠ΅ΡΠ°Π»Π»Π° Π±ΠΎΠ»ΡΡΡΡ ΡΠ°ΡΡΡ ΠΏΡΠΈΠΌΠ΅ΡΠ΅ΠΉ, ΠΎΠ½ ΠΏΡΠ΅Π΄Π»ΠΎΠΆΠΈΠ» ΠΈΡΠΏΠΎΠ»ΡΠ·ΠΎΠ²Π°ΡΡ ΠΈΠ·Π²Π΅ΡΡΡ, ΡΡΠ½ΠΊΡΠΈΡ ΠΊΠΎΡΠΎΡΠΎΠΉ Π·Π°ΠΊΠ»ΡΡΠ°Π»Π°ΡΡ Π² ΡΠ²ΡΠ·ΡΠ²Π°Π½ΠΈΠΈ ΡΠΎΡΡΠΎΡΠ°.
Π’ΠΎΠΌΠ°ΡΠΎΠ²ΡΠΊΠΈΠΉ ΠΏΡΠΎΡΠ΅ΡΡ ΠΏΠΎΠ·Π²ΠΎΠ»ΠΈΠ» ΠΏΠ΅ΡΠ΅ΡΠ°Π±Π°ΡΡΠ²Π°ΡΡ ΡΡΠ³ΡΠ½ Ρ Π²ΡΡΠΎΠΊΠΈΠΌ ΡΠΎΠ΄Π΅ΡΠΆΠ°Π½ΠΈΠ΅ΠΌ ΡΠΎΡΡΠΎΡΠ°. ΠΠΎΡΡΠΎΠΌΡ Π½Π°ΠΈΠ±ΠΎΠ»ΡΡΠ΅Π΅ ΡΠ°ΡΠΏΡΠΎΡΡΡΠ°Π½Π΅Π½ΠΈΠ΅ Π΄Π°Π½Π½ΡΠΉ ΡΠΏΠΎΡΠΎΠ± ΠΏΠΎΠ»ΡΡΠΈΠ» Π² ΡΡΡΠ°Π½Π°Ρ
, Π³Π΄Π΅ ΠΆΠ΅Π»Π΅Π·Π½ΡΠ΅ ΡΡΠ΄Ρ ΡΠΎΠ΄Π΅ΡΠΆΠ°Ρ ΠΌΠ½ΠΎΠ³ΠΎ ΡΠΎΡΡΠΎΡΠ°. ΠΠΎ Π²ΡΠ΅ΠΌ ΠΎΡΡΠ°Π»ΡΠ½ΠΎΠΌ ΠΌΠ΅ΡΠΎΠ΄, ΠΈΠ·ΠΎΠ±ΡΠ΅ΡΠ΅Π½Π½ΡΠΉ Π’ΠΎΠΌΠ°ΡΠΎΠΌ, ΠΌΠ°Π»ΠΎ ΡΠ΅ΠΌ ΠΎΡΠ»ΠΈΡΠ°Π΅ΡΡΡ ΠΎΡ ΠΏΡΠ΅Π΄Π»ΠΎΠΆΠ΅Π½Π½ΠΎΠ³ΠΎ ΠΠ΅ΡΡΠ΅ΠΌΠ΅ΡΠΎΠΌ:
- ΠΈ Π² ΡΠΎΠΌ, ΠΈ Π² Π΄ΡΡΠ³ΠΎΠΌ ΡΠ»ΡΡΠ°Π΅ ΠΈΡΠΏΠΎΠ»ΡΠ·ΡΠ΅ΡΡΡ ΡΡΠ°Π»Π΅ΠΏΠ»Π°Π²ΠΈΠ»ΡΠ½ΡΠΉ Π°Π³ΡΠ΅Π³Π°Ρ, Π² ΠΊΠΎΡΠΎΡΡΠΉ ΡΡΠ³ΡΠ½ ΠΏΠΎΠ΄Π°Π΅ΡΡΡ ΡΠ²Π΅ΡΡ Ρ ΡΠ΅ΡΠ΅Π· ΠΎΡΠ²Π΅ΡΡΡΠΈΠ΅ Π² Π³ΠΎΡΠ»ΠΎΠ²ΠΈΠ½Π΅,
- ΡΠ΅ΡΠ΅Π· ΡΡΠΎ ΠΆΠ΅ ΠΎΡΠ²Π΅ΡΡΡΠΈΠ΅ ΠΏΡΠΎΠΈΠ·Π²ΠΎΠ΄ΠΈΡΡΡ Π²ΡΠΏΡΡΠΊ ΡΡΠ°Π»ΠΈ.
- ΡΠ½ΠΈΠ·Ρ ΡΡΠ°Π»Π΅ΠΏΠ»Π°Π²ΠΈΠ»ΡΠ½ΡΠΉ Π°Π³ΡΠ΅Π³Π°Ρ ΡΠ½Π°Π±ΠΆΠ΅Π½ ΡΡΠ΅ΠΌΠ½ΡΠΌ Π΄Π½ΠΈΡΠ΅ΠΌ, ΡΡΠΎ ΠΏΠΎΠ·Π²ΠΎΠ»ΡΠ΅Ρ Π·Π°ΠΌΠ΅Π½ΡΡΡ Π΅Π³ΠΎ ΠΏΠΎ ΠΌΠ΅ΡΠ΅ Π²ΡΡΠ°Π±ΠΎΡΠΊΠΈ ΠΎΠΏΡΠ΅Π΄Π΅Π»Π΅Π½Π½ΠΎΠ³ΠΎ ΡΡΠΎΠΊΠ° ΡΠ»ΡΠΆΠ±Ρ,
- Π΄ΡΡΡΠ΅ Π² ΠΏΠΎΠ»ΠΎΡΡΡ ΡΡΠ°Π»Π΅ΠΏΠ»Π°Π²ΠΈΡΠ΅Π»Ρ ΠΏΠΎΡΡΡΠΏΠ°Π΅Ρ ΡΠ΅ΡΠ΅Π· ΡΠΏΠ΅ΡΠΈΠ°Π»ΡΠ½ΡΠ΅ ΡΠΎΠΏΠ»Π°, ΡΠ°ΡΠΏΠΎΠ»ΠΎΠΆΠ΅Π½Π½ΡΠ΅ Π² ΡΡΡΠ΅ΡΠΎΠ²ΠΊΠ΅ Π΄Π½ΠΈΡΠ°.
ΠΠ°ΠΊ ΡΠΆΠ΅ Π³ΠΎΠ²ΠΎΡΠΈΠ»ΠΎΡΡ Π²ΡΡΠ΅, ΡΠ»ΠΈΠ² ΡΡΠ°Π»ΠΈ ΠΏΡΠΎΠΈΠ·Π²ΠΎΠ΄ΠΈΡΡΡ ΡΠ΅ΡΠ΅Π· ΠΎΡΠ²Π΅ΡΡΡΠΈΠ΅ Π² Π³ΠΎΡΠ»ΠΎΠ²ΠΈΠ½Π΅. ΠΠ΅ΡΠ΅Π²Π΅ΡΠ½ΡΡΡ ΠΌΠ½ΠΎΠ³ΠΎΡΠΎΠ½Π½ΡΠΉ Π°Π³ΡΠ΅Π³Π°Ρ ΠΏΠΎΠ·Π²ΠΎΠ»ΡΡΡ ΡΠ°ΠΏΡΡ Π² ΡΠΈΠ»ΠΈΠ½Π΄ΡΠΈΡΠ΅ΡΠΊΠΎΠΉ ΡΠ°ΡΡΠΈ ΠΊΠΎΠ½Π²Π΅ΡΡΠ΅ΡΠ°. ΠΡΠΈ ΡΠΎΠΌΠ°ΡΠΎΠ²ΡΠΊΠΎΠΌ ΠΏΡΠΎΡΠ΅ΡΡΠ΅ Π² ΡΡΠ°Π»Π΅ΠΏΠ»Π°Π²ΠΈΡΠ΅Π»Ρ Π·Π°Π³ΡΡΠΆΠ°ΡΡ ΠΈΠ·Π²Π΅ΡΡΡ, ΠΏΠΎΠ·Π²ΠΎΠ»ΡΡΡΡΡ ΠΏΠΎΠ»ΡΡΠΈΡΡ ΠΎΡΠ½ΠΎΠ²Π½ΠΎΠΉ ΡΠ»Π°ΠΊ. ΠΠ°Π»Π΅Π΅ ΡΡΠ΄Π° ΠΆΠ΅ Π·Π°Π»ΠΈΠ²Π°ΡΡ Π²ΡΡΠΎΠΊΠΎΡΠΎΡΡΠΎΡΠΈΡΡΡΠΉ ΡΡΠ³ΡΠ½, Π½Π°Π³ΡΠ΅ΡΡΠΉ Π΄ΠΎ 1200β1250Β°Π‘ ΠΈ ΠΏΠΎΠ΄Π°ΡΡ Π΄ΡΡΡΠ΅. ΠΡΠΈ ΠΏΠΎΠ΄Π°ΡΠ΅ Π΄ΡΡΡΡ ΠΏΡΠΎΠΈΡΡ ΠΎΠ΄ΠΈΡ ΠΎΠΊΠΈΡΠ»Π΅Π½ΠΈΠ΅ ΠΊΡΠ΅ΠΌΠ½ΠΈΡ, ΠΌΠ°ΡΠ³Π°Π½ΡΠ° ΠΈ ΡΠ³Π»Π΅ΡΠΎΠ΄Π°. Π ΠΎΡΠ½ΠΎΠ²Π½ΠΎΠΉ ΡΠ»Π°ΠΊ ΡΠ΄Π°Π»ΡΡΡΡΡ ΡΠ΅ΡΠ° ΠΈ ΡΠΎΡΡΠΎΡ. ΠΡΠΎΠ΄ΡΠ²ΠΊΠ° Π·Π°Π²Π΅ΡΡΠ°Π΅ΡΡΡ ΡΠΎΠ³Π΄Π°, ΠΊΠΎΠ³Π΄Π° ΡΠΎΠ΄Π΅ΡΠΆΠ°Π½ΠΈΠ΅ ΡΠΎΡΡΠΎΡΠ° ΡΠ½ΠΈΠ·ΠΈΡΡΡ Π΄ΠΎ ΠΎΠΏΡΠ΅Π΄Π΅Π»Π΅Π½Π½ΡΡ ΠΏΠΎΠΊΠ°Π·Π°ΡΠ΅Π»Π΅ΠΉ. ΠΠΊΠΎΠ½ΡΠ°ΡΠ΅Π»ΡΠ½ΡΠΌ ΡΡΠ°ΠΏΠΎΠΌ, ΠΊΠ°ΠΊ ΠΈ Π² Π±Π΅ΡΡΠ΅ΠΌΠ΅ΡΠΎΠ²ΡΠΊΠΎΠΌ ΠΏΡΠΎΡΠ΅ΡΡΠ΅, ΡΠ²Π»ΡΠ΅ΡΡΡ Π²ΡΠΏΡΡΠΊ ΠΌΠ΅ΡΠ°Π»Π»Π° Ρ ΠΏΠΎΡΠ»Π΅Π΄ΡΡΡΠΈΠΌ ΡΠ°ΡΠΊΠΈΡΠ»Π΅Π½ΠΈΠ΅ΠΌ.
ΠΡΠΈΠ½ΡΠΈΠΏ ΡΠ°Π±ΠΎΡΡ ΠΊΠΈΡΠ»ΠΎΡΠΎΠ΄Π½ΠΎΠ³ΠΎ ΠΊΠΎΠ½Π²Π΅ΡΡΠ΅ΡΠ°
ΠΠΏΠ΅ΡΠ²ΡΠ΅ ΠΊΠΈΡΠ»ΠΎΡΠΎΠ΄Π½ΠΎΠ΅ Π΄ΡΡΡΠ΅ Π±ΡΠ»ΠΎ Π·Π°ΠΏΠ°ΡΠ΅Π½ΡΠΎΠ²Π°Π½ΠΎ Π. ΠΠ΅ΡΡΠ΅ΠΌΠ΅ΡΠΎΠΌ. ΠΠ΄Π½Π°ΠΊΠΎ Π² ΡΠ΅ΡΠ΅Π½ΠΈΠ΅ ΠΏΡΠΎΠ΄ΠΎΠ»ΠΆΠΈΡΠ΅Π»ΡΠ½ΠΎΠ³ΠΎ Π²ΡΠ΅ΠΌΠ΅Π½ΠΈ ΠΊΠΈΡΠ»ΠΎΡΠΎΠ΄Π½ΠΎ-ΠΊΠΎΠ½Π²Π΅ΡΡΠ΅ΡΠ½ΡΠΉ ΠΏΡΠΎΡΠ΅ΡΡ Π½Π΅ ΠΏΡΠΈΠΌΠ΅Π½ΡΠ»ΡΡ, Π² ΡΠ²ΡΠ·ΠΈ Ρ ΠΎΡΡΡΡΡΡΠ²ΠΈΠ΅ΠΌ ΠΌΠ°ΡΡΠΎΠ²ΠΎΠ³ΠΎ ΠΏΡΠΎΠΈΠ·Π²ΠΎΠ΄ΡΡΠ²Π° ΠΊΠΈΡΠ»ΠΎΡΠΎΠ΄Π°. ΠΠ΅ΡΠ²ΡΠ΅ ΠΎΠΏΡΡΡ ΠΏΠΎ ΠΏΡΠΎΠ΄ΡΠ²ΠΊΠ΅ ΠΊΠΈΡΠ»ΠΎΡΠΎΠ΄ΠΎΠΌ ΡΡΠ°Π»ΠΈ Π²ΠΎΠ·ΠΌΠΎΠΆΠ½ΡΠΌΠΈ Π² Π½Π°ΡΠ°Π»Π΅ ΡΠΎΡΠΎΠΊΠΎΠ²ΡΡ Π³ΠΎΠ΄ΠΎΠ² ΠΏΡΠΎΡΠ»ΠΎΠ³ΠΎ ΡΡΠΎΠ»Π΅ΡΠΈΡ.
Π£ΡΡΡΠΎΠΉΡΡΠ²ΠΎ ΠΊΠΈΡΠ»ΠΎΡΠΎΠ΄Π½ΠΎΠ³ΠΎ ΠΊΠΎΠ½Π²Π΅ΡΡΠ΅ΡΠ° ΠΎΡΡΠ°Π»ΠΎΡΡ ΠΏΡΠ΅ΠΆΠ½ΠΈΠΌ:
- ΠΊΠ°ΠΌΠ΅ΡΠ° ΡΠ³ΠΎΡΠ°Π½ΠΈΡ ΠΈΠ·Π½ΡΡΡΠΈ Π·Π°ΡΠΈΡΠ΅Π½Π° ΠΎΡΠ½ΠΎΠ²Π½ΠΎΠΉ ΡΡΡΠ΅ΡΠΎΠ²ΠΊΠΎΠΉ,
- ΠΎΠ΄Π½Π°ΠΊΠΎ Π²ΠΌΠ΅ΡΡΠΎ Π²ΠΎΠ·Π΄ΡΡ Π° Π² Π½Π΅ΠΌ ΠΏΡΠΈΠΌΠ΅Π½ΡΠ΅ΡΡΡ ΠΏΡΠΎΠ΄ΡΠ²ΠΊΠ° ΠΊΠΈΡΠ»ΠΎΡΠΎΠ΄ΠΎΠΌ,
- ΠΏΠΎΠ΄Π°ΡΠ° ΠΊΠΈΡΠ»ΠΎΡΠΎΠ΄Π° ΠΎΡΡΡΠ΅ΡΡΠ²Π»ΡΠ΅ΡΡΡ ΡΠ΅ΡΠ΅Π· Π²ΠΎΠ΄ΠΎΠΎΡ Π»Π°ΠΆΠ΄Π°Π΅ΠΌΡΠ΅ ΡΠΎΠΏΠ»Π°.
ΠΠ° ΡΠ΅ΡΡΠΈΡΠΎΡΠΈΠΈ Π ΠΎΡΡΠΈΠΈ ΠΏΡΠΈΠΌΠ΅Π½ΡΡΡΡΡ ΡΡΠ°Π»Π΅ΠΏΠ»Π°Π²ΠΈΡΠ΅Π»ΠΈ Ρ Π²Π΅ΡΡ Π½Π΅ΠΉ ΠΏΠΎΠ΄Π°ΡΠ΅ΠΉ ΠΊΠΈΡΠ»ΠΎΡΠΎΠ΄Π°.
ΠΡΠΎΠ±Π΅Π½Π½ΠΎΡΡΡΡ ΠΊΠΎΠ½Π²Π΅ΡΡΠ΅ΡΠ½ΠΎΠ³ΠΎ ΡΠΏΠΎΡΠΎΠ±Π° Ρ ΠΊΠΈΡΠ»ΠΎΡΠΎΠ΄Π½ΠΎΠΉ ΠΏΡΠΎΠ΄ΡΠ²ΠΊΠΎΠΉ ΡΠ²Π»ΡΠ΅ΡΡΡ ΡΠΊΠΎΡΠΎΡΠ΅ΡΠ½ΠΎΡΡΡ. ΠΠ΅ΡΡ ΠΏΡΠΎΡΠ΅ΡΡ ΡΠ°ΡΠΏΠ»Π°Π²Π»Π΅Π½ΠΈΡ ΠΌΠ΅ΡΠ°Π»Π»Π° Π·Π°Π½ΠΈΠΌΠ°Π΅Ρ Π΄Π΅ΡΡΡΠΊΠΈ ΠΌΠΈΠ½ΡΡ. ΠΠ΄Π½Π°ΠΊΠΎ Π²ΠΎ Π²ΡΠ΅ΠΌΡ ΡΠ°Π±ΠΎΡΡ ΡΡΠ΅Π±ΡΠ΅ΡΡΡ ΡΡΠ°ΡΠ΅Π»ΡΠ½ΠΎ ΠΎΡΡΠ»Π΅ΠΆΠΈΠ²Π°ΡΡ ΡΠΎΠ΄Π΅ΡΠΆΠ°Π½ΠΈΠ΅ Π² ΡΡΠ³ΡΠ½Π΅ ΡΠ³Π»Π΅ΡΠΎΠ΄Π°, ΡΠ΅ΠΌΠΏΠ΅ΡΠ°ΡΡΡΡ Π΅Π³ΠΎ ΡΠ°ΡΠΏΠ»Π°Π²Π° ΠΈ ΠΏΡΠΎΡΠΈΠ΅ ΠΏΠ°ΡΠ°ΠΌΠ΅ΡΡΡ, ΡΡΠΎΠ±Ρ Π²ΠΎΠ²ΡΠ΅ΠΌΡ ΠΏΡΠ΅ΠΊΡΠ°ΡΠΈΡΡ ΠΏΡΠΎΠ΄ΡΠ²ΠΊΡ.
ΠΡΠΎΡΠ΅ΡΡ ΡΡΠ°Π»Π΅ΠΏΠ»Π°Π²ΠΈΠ»ΡΠ½ΠΎΠ³ΠΎ ΠΏΡΠΎΠΈΠ·Π²ΠΎΠ΄ΡΡΠ²Π° ΡΠΏΡΠΎΡΡΠΈΠ»ΡΡ, ΠΊΠΎΠ³Π΄Π° ΠΊΠΈΡΠ»ΠΎΡΠΎΠ΄Π½ΡΠ΅ ΠΊΠΎΠ½Π²Π΅ΡΡΠ΅ΡΡ ΠΎΡΠ½Π°ΡΡΠΈΠ»ΠΈ Π°Π²ΡΠΎΠΌΠ°ΡΠΈΡΠ΅ΡΠΊΠΈΠΌΠΈ ΡΠΈΡΡΠ΅ΠΌΠ°ΠΌΠΈ, ΡΡΠΎΠ²Π΅ΡΡΠ΅Π½ΡΡΠ²ΠΎΠ²Π°Π»ΠΈ Π»Π°Π±ΠΎΡΠ°ΡΠΎΡΠ½ΡΡ ΡΠ΅Ρ Π½ΠΈΠΊΡ ΠΈ ΠΈΠ·ΠΌΠ΅ΡΠΈΡΠ΅Π»ΡΠ½ΡΠ΅ ΠΏΡΠΈΠ±ΠΎΡΡ. Π£ΡΠΎΠ²Π΅ΡΡΠ΅Π½ΡΡΠ²ΠΎΠ²Π°Π½ΠΈΠ΅ ΠΊΠΈΡΠ»ΠΎΡΠΎΠ΄Π½ΠΎ-ΠΊΠΎΠ½Π²Π΅ΡΡΠ΅ΡΠ½ΠΎΠ³ΠΎ ΠΏΡΠΎΡΠ΅ΡΡΠ° ΠΏΠΎΠ·Π²ΠΎΠ»ΠΈΠ»ΠΎ ΠΏΠΎΠ²ΡΡΠΈΡΡ ΠΏΡΠΎΠΈΠ·Π²ΠΎΠ΄ΠΈΡΠ΅Π»ΡΠ½ΠΎΡΡΡ, ΡΠ½ΠΈΠ·ΠΈΡΡ ΡΠ΅Π±Π΅ΡΡΠΎΠΈΠΌΠΎΡΡΡ ΠΌΠ΅ΡΠ°Π»Π»Π° ΠΈ ΠΏΠΎΠ²ΡΡΠΈΡΡ Π΅Π³ΠΎ ΠΊΠ°ΡΠ΅ΡΡΠ²ΠΎ.
Π‘ΠΎΠ²ΡΠ΅ΠΌΠ΅Π½Π½ΡΠ΅ ΠΊΠΈΡΠ»ΠΎΡΠΎΠ΄Π½ΡΠ΅ ΠΊΠΎΠ½Π²Π΅ΡΡΠ΅ΡΡ ΠΌΠΎΠ³ΡΡ ΡΠ°Π±ΠΎΡΠ°ΡΡ Π² ΡΡΠ΅Ρ ΠΎΡΠ½ΠΎΠ²Π½ΡΡ ΡΠ΅ΠΆΠΈΠΌΠ°Ρ :
- Ρ ΠΏΠΎΠ»Π½ΡΠΌ Π΄ΠΎΠΆΠΈΠ³Π°Π½ΠΈΠ΅ΠΌ ΠΎΠΊΠΈΡΠΈ ΡΠ³Π»Π΅ΡΠΎΠ΄Π°,
- Ρ ΡΠ°ΡΡΠΈΡΠ½ΡΠΌ Π΄ΠΎΠΆΠΈΠ³Π°Π½ΠΈΠ΅ΠΌ ΠΠ‘,
- Π±Π΅Π· Π΄ΠΎΠΆΠΈΠ³Π°Π½ΠΈΡ ΠΠ‘.
ΠΠ½ΠΈ ΠΏΠΎΠ·Π²ΠΎΠ»ΡΡΡ ΠΏΡΠΎΠΈΠ·Π²ΠΎΠ΄ΠΈΡΡ ΡΡΠ°Π»Ρ ΠΈΠ· ΡΡΠ³ΡΠ½Π° ΡΠ°Π·Π»ΠΈΡΠ½ΠΎΠ³ΠΎ ΡΠΎΡΡΠ°Π²Π°.
ΠΠΈΡΠ»ΠΎΡΠΎΠ΄Π½ΡΠΉ ΠΊΠΎΠ½Π²Π΅ΡΡΠ΅Ρ β ΠΎΠΏΠΈΡΠ°Π½ΠΈΠ΅ ΠΏΡΠΎΡΠ΅ΡΡΠ° ΠΏΠ»Π°Π²ΠΊΠΈ
ΠΠΈΡΠ»ΠΎΡΠΎΠ΄Π½ΡΠΉ ΠΊΠΎΠ½Π²Π΅ΡΡΠ΅Ρ β ΡΡΠΎ ΡΡΠ°Π»ΡΠ½ΠΎΠΉ ΡΠΎΡΡΠ΄ Π³ΡΡΡΠ΅Π²ΠΈΠ΄Π½ΠΎΠΉ ΡΠΎΡΠΌΡ. ΠΠ³ΠΎ Π²Π½ΡΡΡΠ΅Π½Π½ΡΡ ΡΠ°ΡΡΡ Π·Π°ΡΠΈΡΠ΅Π½Π° ΡΠΌΠΎΠ»ΠΎΠ΄ΠΎΠ»ΠΎΠΌΠΈΡΠΎΠ²ΡΠΌ (ΠΎΡΠ½ΠΎΠ²Π½ΡΠΌ) ΠΊΠΈΡΠΏΠΈΡΠΎΠΌ. ΠΠΌΠ΅ΡΡΠΈΠΌΠΎΡΡΡ ΡΡΠ°Π»Π΅ΠΏΠ»Π°Π²ΠΈΠ»ΡΠ½ΠΎΠ³ΠΎ Π°Π³ΡΠ΅Π³Π°ΡΠ° Π²Π°ΡΡΠΈΡΡΠ΅ΡΡΡ ΠΎΡ 50 Π΄ΠΎ 350 ΡΠΎΠ½Π½. Π‘ΠΎΡΡΠ΄ ΡΠ°ΡΠΏΠ»ΠΎΠΆΠ΅Π½ Π½Π° ΡΠ°ΠΏΡΠ°Ρ ΠΈ ΡΠΏΠΎΡΠΎΠ±Π΅Π½ ΠΏΠΎΠ²ΠΎΡΠ°ΡΠΈΠ²Π°ΡΡΡΡ Π²ΠΎΠΊΡΡΠ³ Π³ΠΎΡΠΈΠ·ΠΎΠ½ΡΠ°Π»ΡΠ½ΠΎΠΉ ΠΎΡΠΈ, ΡΡΠΎ ΠΏΠΎΠ·Π²ΠΎΠ»ΡΠ΅Ρ Π±Π΅ΡΠΏΡΠ΅ΠΏΡΡΡΡΠ²Π΅Π½Π½ΠΎ Π·Π°Π»ΠΈΠ²Π°ΡΡ Π² Π½Π΅Π³ΠΎ ΡΡΠ³ΡΠ½, Π·Π°ΠΊΠ»Π°Π΄ΡΠ²Π°ΡΡ Π΄ΡΡΠ³ΠΈΠ΅ Π΄ΠΎΠ±Π°Π²ΠΊΠΈ ΠΈ ΡΠ»ΠΈΠ²Π°ΡΡ ΠΌΠ΅ΡΠ°Π»Π» ΡΠΎ ΡΠ»Π°ΠΊΠΎΠΌ.
Π§ΡΠΎΠ±Ρ ΠΏΠΎΠ»ΡΡΠΈΡΡ ΠΊΠΎΠ½Π΅ΡΠ½ΡΠΉ ΠΏΡΠΎΠ΄ΡΠΊΡ, Π² ΠΊΠΎΠ½Π²Π΅ΡΡΠ΅Ρ Π·Π°Π»ΠΈΠ²Π°Π΅ΡΡΡ Π½Π΅ ΡΠΎΠ»ΡΠΊΠΎ ΡΡΠ³ΡΠ½, Π½ΠΎ ΠΈ Π·Π°ΠΊΠ»Π°Π΄ΡΠ²Π°ΡΡ Π΄ΠΎΠ±Π°Π²ΠΊΠΈ. Π Π½ΠΈΠΌ ΠΎΡΠ½ΠΎΡΡΡΡΡ:
- Π»ΠΎΠΌ ΠΌΠ΅ΡΠ°Π»Π»Π°,
- ΡΠ»Π°ΠΊΠΎΠΎΠ±ΡΠ°Π·ΡΡΡΠΈΠ΅ ΠΌΠ°ΡΠ΅ΡΠΈΠ°Π»Ρ (ΠΆΠ΅Π»Π΅Π·Π½Π°Ρ ΡΡΠ΄Π°, ΠΈΠ·Π²Π΅ΡΡΡ, ΠΏΠΎΠ»Π΅Π²ΠΎΠΉ ΡΠΏΠ°Ρ, Π±ΠΎΠΊΡΠΈΡΡ).
ΠΠΎΠ½Π²Π΅ΡΡΠ΅ΡΠ½ΡΠΉ ΡΠΏΠΎΡΠΎΠ± Ρ ΠΊΠΈΡΠ»ΠΎΡΠΎΠ΄Π½ΠΎΠΉ ΠΏΡΠΎΠ΄ΡΠ²ΠΊΠΎΠΉ ΠΏΡΠ΅Π΄ΡΡΠΌΠ°ΡΡΠΈΠ²Π°Π΅Ρ Π·Π°Π»ΠΈΠ²ΠΊΡ Π² ΠΊΠΎΠ½Π²Π΅ΡΡΠ΅Ρ ΡΡΠ³ΡΠ½Π°, Π½Π°Π³ΡΠ΅ΡΠΎΠ³ΠΎ Π΄ΠΎ 1250β1400Β°Π‘. Π£ΡΡΠ°Π½ΠΎΠ²ΠΈΠ² ΠΊΠΎΠ½Π²Π΅ΡΡΠ΅Ρ Π² Π²Π΅ΡΡΠΈΠΊΠ°Π»ΡΠ½ΠΎΠ΅ ΠΏΠΎΠ»ΠΎΠΆΠ΅Π½ΠΈΠ΅, Π² Π½Π΅Π³ΠΎ ΠΏΠΎΠ΄Π°ΡΡ ΠΊΠΈΡΠ»ΠΎΡΠΎΠ΄. ΠΠ°ΠΊ ΡΠΎΠ»ΡΠΊΠΎ Π½Π°ΡΠ°Π»Π°ΡΡ ΠΏΡΠΎΠ΄ΡΠ²ΠΊΠ°, Π² ΡΠ°ΡΠΏΠ»Π°Π²Π»Π΅Π½Π½ΡΠΉ ΡΡΠ³ΡΠ½ Π²Π²ΠΎΠ΄ΡΡ ΠΎΡΡΠ°Π»ΡΠ½ΡΠ΅ ΠΊΠΎΠΌΠΏΠΎΠ½Π΅Π½ΡΡ, Π²Ρ ΠΎΠ΄ΡΡΠΈΠ΅ Π² ΡΠΎΡΡΠ°Π² ΡΠ»Π°ΠΊΠ°. ΠΠ΅ΡΠ΅ΠΌΠ΅ΡΠΈΠ²Π°Π½ΠΈΠ΅ ΡΡΠ³ΡΠ½Π° ΡΠΎ ΡΠ»Π°ΠΊΠΎΠΌ ΠΎΡΡΡΠ΅ΡΡΠ²Π»ΡΠ΅ΡΡΡ ΠΏΠΎΠ΄ Π΄Π΅ΠΉΡΡΠ²ΠΈΠ΅ΠΌ ΠΏΡΠΎΠ΄ΡΠ²ΠΊΠΈ.
Π’Π°ΠΊ ΠΊΠ°ΠΊ ΠΊΠΎΠ½ΡΠ΅Π½ΡΡΠ°ΡΠΈΡ ΡΡΠ³ΡΠ½Π° Π³ΠΎΡΠ°Π·Π΄ΠΎ Π²ΡΡΠ΅, ΡΠ΅ΠΌ ΠΏΡΠΈΠΌΠ΅ΡΠ΅ΠΉ, Π² ΠΏΡΠΎΡΠ΅ΡΡΠ΅ ΠΏΡΠΎΠ΄ΡΠ²ΠΊΠΈ ΠΏΡΠΎΠΈΡΡ ΠΎΠ΄ΠΈΡ ΠΎΠ±ΡΠ°Π·ΠΎΠ²Π°Π½ΠΈΠ΅ ΠΎΠΊΡΠΈΠ΄Π° ΠΆΠ΅Π»Π΅Π·Π°, ΠΊΠΎΡΠΎΡΡΠΉ ΡΠ°ΡΡΠ²ΠΎΡΡΡΡΡ, ΠΎΠ±ΠΎΠ³Π°ΡΠ°Π΅Ρ ΠΌΠ΅ΡΠ°Π»Π» ΠΊΠΈΡΠ»ΠΎΡΠΎΠ΄ΠΎΠΌ. ΠΠΌΠ΅Π½Π½ΠΎ ΡΠ°ΡΡΠ²ΠΎΡΠ΅Π½Π½ΡΠΉ ΠΊΠΈΡΠ»ΠΎΡΠΎΠ΄ ΡΠΏΠΎΡΠΎΠ±ΡΡΠ²ΡΠ΅Ρ ΡΠΌΠ΅Π½ΡΡΠ΅Π½ΠΈΡ Π² ΠΌΠ΅ΡΠ°Π»Π»Π΅ ΠΊΠΎΠ½ΡΠ΅Π½ΡΡΠ°ΡΠΈΠΈ ΠΊΡΠ΅ΠΌΠ½ΠΈΡ, ΡΠ³Π»Π΅ΡΠΎΠ΄Π° ΠΈ ΠΌΠ°ΡΠ³Π°Π½ΡΠ°. Π ΠΊΠΎΠ³Π΄Π° ΠΏΡΠΈΠΌΠ΅ΡΠΈ ΠΎΠΊΠΈΡΠ»ΡΡΡΡΡ, Π²ΡΠ΄Π΅Π»ΡΠ΅ΡΡΡ ΠΏΠΎΠ»Π΅Π·Π½ΠΎΠ΅ ΡΠ΅ΠΏΠ»ΠΎ.
ΠΡΠΎΠ±Π΅Π½Π½ΠΎΡΡΡΡ ΠΎΡΠ½ΠΎΠ²Π½ΠΎΠ³ΠΎ ΡΠ»Π°ΠΊΠ° ΡΠ²Π»ΡΠ΅ΡΡΡ Π±ΠΎΠ»ΡΡΠΎΠ΅ ΡΠΎΠ΄Π΅ΡΠΆΠ°Π½ΠΈΠ΅ ΠΎΠΊΡΠΈΠ΄Π° ΠΊΠ°Π»ΡΡΠΈΡ ΠΈ ΠΎΠΊΡΠΈΠ΄Π° ΠΆΠ΅Π»Π΅Π·Π°, ΠΊΠΎΡΠΎΡΡΠ΅ Π² Π½Π°ΡΠ°Π»Π΅ ΠΏΡΠΎΠ΄ΡΠ²ΠΊΠΈ ΡΠΏΠΎΡΠΎΠ±ΡΡΠ²ΡΡΡ ΡΠ΄Π°Π»Π΅Π½ΠΈΡ ΡΠΎΡΡΠΎΡΠ°. ΠΡΠ»ΠΈ ΠΆΠ΅ ΡΠΎΠ΄Π΅ΡΠΆΠ°Π½ΠΈΠ΅ ΡΠΎΡΡΠΎΡΠ° ΠΏΡΠ΅Π²ΡΡΠ°Π΅Ρ ΡΡΠ΅Π±ΡΠ΅ΠΌΡΠΉ ΠΏΠΎΠΊΠ°Π·Π°ΡΠ΅Π»Ρ, ΡΠ»Π°ΠΊ ΡΠ»ΠΈΠ²Π°ΡΡ ΠΈ Π½Π°Π²ΠΎΠ΄ΡΡ Π½ΠΎΠ²ΡΠΉ. ΠΡΠΎΠ΄ΡΠ²ΠΊΡ ΠΊΠΈΡΠ»ΠΎΡΠΎΠ΄ΠΎΠΌ Π·Π°ΠΊΠ°Π½ΡΠΈΠ²Π°ΡΡ, ΠΊΠΎΠ³Π΄Π° ΡΠΎΠ΄Π΅ΡΠΆΠ°Π½ΠΈΠ΅ ΡΠ³Π»Π΅ΡΠΎΠ΄Π° Π² ΠΊΠΎΠ½Π΅ΡΠ½ΠΎΠΌ ΠΏΡΠΎΠ΄ΡΠΊΡΠ΅ ΡΠΎΠΎΡΠ²Π΅ΡΡΡΠ²ΡΠ΅Ρ ΠΎΠΏΡΠ΅Π΄Π΅Π»Π΅Π½Π½ΠΎΠΌΡ ΠΏΠ°ΡΠ°ΠΌΠ΅ΡΡΡ. ΠΠΎΡΠ»Π΅ ΡΡΠΎΠ³ΠΎ ΠΊΠΎΠ½Π²Π΅ΡΡΠ΅Ρ ΠΏΠ΅ΡΠ΅Π²ΠΎΡΠ°ΡΠΈΠ²Π°ΡΡ ΠΈ ΠΏΡΠΎΠΈΠ·Π²ΠΎΠ΄ΡΡ ΡΠ»ΠΈΠ² ΡΡΠ°Π»ΠΈ Π² ΠΊΠΎΠ²Ρ, ΠΊΡΠ΄Π° Π΄ΠΎΠ±Π°Π²Π»ΡΡΡ ΡΠ°ΡΠΊΠΈΡΠ»ΠΈΡΠ΅Π»ΠΈ ΠΈ Π΄ΡΡΠ³ΠΈΠ΅ Π΄ΠΎΠ±Π°Π²ΠΊΠΈ.
ΠΠΈΠ΄Π΅ΠΎ ΠΏΠΎ ΡΠ΅ΠΌΠ΅: ΠΡΠ½ΠΎΠ²Ρ ΠΊΠΈΡΠ»ΠΎΡΠΎΠ΄Π½ΠΎ ΠΊΠΎΠ½Π²Π΅ΡΡΠ΅ΡΠ½ΠΎΠ³ΠΎ ΠΏΡΠΎΠΈΠ·Π²ΠΎΠ΄ΡΡΠ²Π°

ΠΠΈΡΠ»ΠΎΡΠΎΠ΄Π½ΠΎ-ΠΊΠΎΠ½Π²Π΅ΡΡΠ΅ΡΠ½ΡΠΉ ΠΏΡΠΎΡΠ΅ΡΡ β ΡΡΠΎβ¦ Π§ΡΠΎ ΡΠ°ΠΊΠΎΠ΅ ΠΠΈΡΠ»ΠΎΡΠΎΠ΄Π½ΠΎ-ΠΊΠΎΠ½Π²Π΅ΡΡΠ΅ΡΠ½ΡΠΉ ΠΏΡΠΎΡΠ΅ΡΡ?
ΠΎΠ΄ΠΈΠ½ ΠΈΠ· Π²ΠΈΠ΄ΠΎΠ² ΠΏΠ΅ΡΠ΅Π΄Π΅Π»Π° ΠΆΠΈΠ΄ΠΊΠΎΠ³ΠΎ ΡΡΠ³ΡΠ½Π° Π² ΡΡΠ°Π»Ρ Π±Π΅Π· Π·Π°ΡΡΠ°ΡΡ ΡΠΎΠΏΠ»ΠΈΠ²Π° ΠΏΡΡΡΠΌ ΠΏΡΠΎΠ΄ΡΠ²ΠΊΠΈ ΡΡΠ³ΡΠ½Π° Π² ΠΠΎΠ½Π²Π΅ΡΡΠ΅ΡΠ΅ ΡΠ΅Ρ Π½ΠΈΡΠ΅ΡΠΊΠΈ ΡΠΈΡΡΡΠΌ ΠΊΠΈΡΠ»ΠΎΡΠΎΠ΄ΠΎΠΌ ΡΠ²Π΅ΡΡ Ρ. Π ΡΠ΅Π»Π΅ΡΠΎΠΎΠ±ΡΠ°Π·Π½ΠΎΡΡΠΈ ΠΈΡΠΏΠΎΠ»ΡΠ·ΠΎΠ²Π°Π½ΠΈΡ ΠΊΠΈΡΠ»ΠΎΡΠΎΠ΄Π° ΠΏΡΠΈ ΠΏΡΠΎΠΈΠ·Π²ΠΎΠ΄ΡΡΠ²Π΅ ΡΡΠ°Π»ΠΈ Π² ΠΊΠΎΠ½Π²Π΅ΡΡΠ΅ΡΠ°Ρ ΡΠΊΠ°Π·ΡΠ²Π°Π» Π΅ΡΡ Π² 1876 ΡΡΡΡΠΊΠΈΠΉ ΠΌΠ΅ΡΠ°Π»Π»ΡΡΠ³ Π. Π. Π§Π΅ΡΠ½ΠΎΠ². ΠΠΏΠ΅ΡΠ²ΡΠ΅ ΠΏΡΠΈΠΌΠ΅Π½ΠΈΠ» ΡΠΈΡΡΡΠΉ ΠΊΠΈΡΠ»ΠΎΡΠΎΠ΄ Π΄Π»Ρ ΠΏΡΠΎΠ΄ΡΠ²ΠΊΠΈ ΠΆΠΈΠ΄ΠΊΠΎΠ³ΠΎ ΡΡΠ³ΡΠ½Π° ΡΠ½ΠΈΠ·Ρ ΡΠΎΠ²Π΅ΡΡΠΊΠΈΠΉ ΠΈΠ½ΠΆΠ΅Π½Π΅Ρ Π. Π. ΠΠΎΠ·Π³ΠΎΠ²ΠΎΠΉ Π² 1936. Π 1939β41 Π½Π° ΠΠΎΡΠΊΠΎΠ²ΡΠΊΠΎΠΌ Π·Π°Π²ΠΎΠ΄Π΅ ΡΡΠ°Π½ΠΊΠΎΠΊΠΎΠ½ΡΡΡΡΠΊΡΠΈΠΉ ΠΏΡΠΎΠ²ΠΎΠ΄ΠΈΠ»ΠΈΡΡ ΠΎΠΏΡΡΡ ΠΏΠΎ ΠΏΡΠΎΠ΄ΡΠ²ΠΊΠ΅ ΡΡΠ³ΡΠ½Π° ΡΠ²Π΅ΡΡ Ρ ΠΊΠΈΡΠ»ΠΎΡΠΎΠ΄ΠΎΠΌ Π² 1,5-Π‘. Π. ΠΡΠ°Π½Π°ΡΡΠ΅Π².

Π‘Ρ Π΅ΠΌΠ° ΠΏΠΎΠ»ΡΡΠ΅Π½ΠΈΡ ΡΡΠ°Π»ΠΈ Π² ΠΊΠΈΡΠ»ΠΎΡΠΎΠ΄Π½ΠΎΠΌ ΠΊΠΎΠ½Π²Π΅ΡΡΠ΅ΡΠ΅: Π° β Π·Π°Π³ΡΡΠ·ΠΊΠ° ΠΌΠ΅ΡΠ°Π»Π»ΠΎΠ»ΠΎΠΌΠ°; Π± β Π·Π°Π»ΠΈΠ²ΠΊΠ° ΡΡΠ³ΡΠ½Π°; Π² β ΠΏΡΠΎΠ΄ΡΠ²ΠΊΠ°; Π³ β Π²ΡΠΏΡΡΠΊ ΡΡΠ°Π»ΠΈ; Π΄ β ΡΠ»ΠΈΠ² ΡΠ»Π°ΠΊΠ°.
ΡΡΡΡΠΎΠΉΡΡΠ²ΠΎ ΠΈ ΡΠ΅Ρ Π½ΠΎΠ»ΠΎΠ³ΠΈΡ Π²ΡΠΏΠ»Π°Π²ΠΊΠΈ ΡΡΠ°Π»ΠΈ
Π ΠΏΡΠΎΡΠ΅ΡΡΠ°Ρ ΠΏΠΎΠ»ΡΡΠ΅Π½ΠΈΡ Π²ΡΡΠΎΠΊΠΎΠΏΡΠΎΡΠ½ΡΡ ΡΡΠ°Π»Π΅ΠΉ Π²Π°ΠΆΠ½ΡΡ ΡΠΎΠ»Ρ ΠΈΠ³ΡΠ°ΡΡ ΠΎΠΏΠ΅ΡΠ°ΡΠΈΠΈ Π»Π΅Π³ΠΈΡΠΎΠ²Π°Π½ΠΈΡ ΠΈ ΠΌΠΎΠ΄ΠΈΡΠΈΠΊΠ°ΡΠΈΠΈ Π±Π°Π·ΠΎΠ²ΠΎΠ³ΠΎ ΡΠΎΡΡΠ°Π²Π°. ΠΡΠ½ΠΎΠ²Ρ ΠΏΠΎΠ΄ΠΎΠ±Π½ΡΡ ΠΏΡΠΎΡΠ΅Π΄ΡΡ ΡΠΎΡΡΠ°Π²Π»ΡΡΡ ΡΠ΅Ρ Π½ΠΈΠΊΠΈ Π΄ΠΎΠ±Π°Π²Π»Π΅Π½ΠΈΡ ΠΌΠ΅ΡΠ°Π»Π»ΠΈΡΠ΅ΡΠΊΠΈΡ ΠΏΡΠΈΠΌΠ΅ΡΠ΅ΠΉ ΡΠ°Π·Π½ΠΎΠ³ΠΎ ΡΠ²ΠΎΠΉΡΡΠ²Π°, Π½ΠΎ ΠΈ Π³Π°Π·ΠΎ-Π²ΠΎΠ·Π΄ΡΡΠ½Π°Ρ ΡΠ΅Π³ΡΠ»ΡΡΠΈΡ ΠΎΠΊΠ°Π·ΡΠ²Π°Π΅Ρ Π½Π΅ΠΌΠ°Π»ΠΎΠ²Π°ΠΆΠ½ΠΎΠ΅ Π·Π½Π°ΡΠ΅Π½ΠΈΠ΅. ΠΠΌΠ΅Π½Π½ΠΎ Π½Π° ΡΡΡ ΡΠ΅Ρ Π½ΠΎΠ»ΠΎΠ³ΠΈΡΠ΅ΡΠΊΡΡ ΠΎΠΏΠ΅ΡΠ°ΡΠΈΡ ΠΎΡΠΈΠ΅Π½ΡΠΈΡΡΠ΅ΡΡΡ ΡΠ°Π±ΠΎΡΠ° ΠΊΠΈΡΠ»ΠΎΡΠΎΠ΄Π½ΠΎΠ³ΠΎ ΠΊΠΎΠ½Π²Π΅ΡΡΠ΅ΡΠ°, ΠΊΠΎΡΠΎΡΡΠΉ ΡΠΈΡΠΎΠΊΠΎ ΠΈΡΠΏΠΎΠ»ΡΠ·ΡΠ΅ΡΡΡ Π² ΠΌΠ΅ΡΠ°Π»Π»ΡΡΠ³ΠΈΠΈ ΠΏΡΠΈ ΠΏΠΎΠ»ΡΡΠ΅Π½ΠΈΠΈ ΡΠΏΠ»Π°Π²ΠΎΠ² ΡΡΠ°Π»ΠΈ Π² Π±ΠΎΠ»ΡΡΠΈΡ ΠΎΠ±ΡΠ΅ΠΌΠ°Ρ .
ΠΠΎΠ½ΡΡΡΡΠΊΡΠΈΡ ΠΊΠΎΠ½Π²Π΅ΡΡΠ΅ΡΠ°

ΠΠ±ΠΎΡΡΠ΄ΠΎΠ²Π°Π½ΠΈΠ΅ ΠΏΡΠ΅Π΄ΡΡΠ°Π²Π»ΡΠ΅Ρ ΡΠΎΠ±ΠΎΠΉ Π³ΡΡΡΠ΅Π²ΠΈΠ΄Π½ΡΠΉ ΡΠΎΡΡΠ΄, ΠΎΠ±Π΅ΡΠΏΠ΅ΡΠ΅Π½Π½ΡΠΉ Π²Π½ΡΡΡΠ΅Π½Π½Π΅ΠΉ ΡΡΡΠ΅ΡΠΎΠ²ΠΊΠΎΠΉ ΠΈ Π»Π΅ΡΠΊΠΎΠΉ Π΄Π»Ρ Π²ΡΠΏΡΡΠΊΠ° ΠΏΡΠΎΠ΄ΡΠΊΡΠΎΠ² ΠΏΠ»Π°Π²ΠΊΠΈ. Π Π²Π΅ΡΡ Π½Π΅ΠΉ ΡΠ°ΡΡΠΈ ΠΊΠΎΠ½ΡΡΡΡΠΊΡΠΈΠΈ ΠΏΡΠ΅Π΄ΡΡΠΌΠΎΡΡΠ΅Π½ΠΎ ΠΎΡΠ²Π΅ΡΡΡΠΈΠ΅ Ρ Π³ΠΎΡΠ»ΠΎΠ²ΠΈΠ½ΠΎΠΉ Π΄Π»Ρ ΠΏΠΎΠ΄Π°ΡΠΈ ΡΡΡΠΌΡ, Π»ΠΎΠΌΠ°, ΡΠ°ΡΠΏΠ»Π°Π²Π»Π΅Π½Π½ΠΎΠ³ΠΎ ΡΡΠ³ΡΠ½Π°, Π»Π΅Π³ΠΈΡΡΡΡΠΈΡ ΡΠΌΠ΅ΡΠ΅ΠΉ ΠΈ ΠΎΡΠ²ΠΎΠ΄Π° Π³Π°Π·Π°. Π’ΠΎΠ½Π½Π°ΠΆ Π²Π°ΡΡΠΈΡΡΠ΅ΡΡΡ ΠΎΡ 50 Π΄ΠΎ 400 Ρ. Π ΠΊΠ°ΡΠ΅ΡΡΠ²Π΅ ΠΌΠ°ΡΠ΅ΡΠΈΠ°Π»ΠΎΠ² Π΄Π»Ρ ΠΈΠ·Π³ΠΎΡΠΎΠ²Π»Π΅Π½ΠΈΡ ΠΊΠΎΠ½ΡΡΡΡΠΊΡΠΈΠΈ ΠΏΡΠΈΠΌΠ΅Π½ΡΠ΅ΡΡΡ Π»ΠΈΡΡΠΎΠ²Π°Ρ ΠΈΠ»ΠΈ ΡΠ²Π°ΡΠ½Π°Ρ ΡΡΠ°Π»Ρ ΡΡΠ΅Π΄Π½Π΅ΠΉ ΡΠΎΠ»ΡΠΈΠ½ΠΎΠΉ ΠΏΠΎΡΡΠ΄ΠΊΠ° 50-70 ΠΌΠΌ. Π’ΠΈΠΏΠΎΠ²ΠΎΠ΅ ΡΡΡΡΠΎΠΉΡΡΠ²ΠΎ ΠΊΠΈΡΠ»ΠΎΡΠΎΠ΄Π½ΠΎΠ³ΠΎ ΠΊΠΎΠ½Π²Π΅ΡΡΠ΅ΡΠ° ΠΏΡΠ΅Π΄ΡΡΠΌΠ°ΡΡΠΈΠ²Π°Π΅Ρ Π²ΠΎΠ·ΠΌΠΎΠΆΠ½ΠΎΡΡΡ ΠΎΡΡΠΎΠ΅Π΄ΠΈΠ½Π΅Π½ΠΈΡ Π΄Π½ΠΈΡΠ° β ΡΡΠΎ ΠΌΠΎΠ΄ΠΈΡΠΈΠΊΠ°ΡΠΈΠΈ Ρ Π΄ΠΎΠ½Π½ΠΎΠΉ ΠΏΡΠΎΠ΄ΡΠ²ΠΊΠΎΠΉ Π³Π°Π·ΠΎ-Π²ΠΎΠ·Π΄ΡΡΠ½ΡΠΌΠΈ ΡΠΌΠ΅ΡΡΠΌΠΈ. Π‘ΡΠ΅Π΄ΠΈ Π²ΡΠΏΠΎΠΌΠΎΠ³Π°ΡΠ΅Π»ΡΠ½ΡΡ ΠΈ ΡΡΠ½ΠΊΡΠΈΠΎΠ½Π°Π»ΡΠ½ΡΡ ΡΠ»Π΅ΠΌΠ΅Π½ΡΠΎΠ² Π°Π³ΡΠ΅Π³Π°ΡΠ° ΠΌΠΎΠΆΠ½ΠΎ Π²ΡΠ΄Π΅Π»ΠΈΡΡ ΡΠ»Π΅ΠΊΡΡΠΎΠ΄Π²ΠΈΠ³Π°ΡΠ΅Π»Ρ, ΡΡΡΠ±ΠΎΠΏΡΠΎΠ²ΠΎΠ΄Π½ΡΡ ΠΈΠ½ΡΡΠ°ΡΡΡΡΠΊΡΡΡΡ Π΄Π»Ρ ΡΠΈΡΠΊΡΠ»ΡΡΠΈΠΈ ΠΏΠΎΡΠΎΠΊΠΎΠ² ΠΊΠΈΡΠ»ΠΎΡΠΎΠ΄Π°, ΠΎΠΏΠΎΡΠ½ΡΠ΅ ΠΏΠΎΠ΄ΡΠΈΠΏΠ½ΠΈΠΊΠΈ, Π΄Π΅ΠΌΠΏΡΠ΅ΡΠ½ΡΡ ΠΏΠ»Π°ΡΡΠΎΡΠΌΡ ΠΈ ΠΎΠΏΠΎΡΠ½ΡΡ ΡΡΠ°Π½ΠΈΠ½Ρ Π΄Π»Ρ ΠΌΠΎΠ½ΡΠ°ΠΆΠ° ΠΊΠΎΠ½ΡΡΡΡΠΊΡΠΈΠΈ.
ΠΠΏΠΎΡΠ½ΡΠ΅ ΠΊΠΎΠ»ΡΡΠ° ΠΈ ΡΠ°ΠΏΡΠ°
ΠΠΎΠ½Π²Π΅ΡΡΠ΅Ρ ΡΠ°ΡΠΏΠΎΠ»Π°Π³Π°Π΅ΡΡΡ Π½Π° ΡΠΎΠ»ΠΈΠΊΠΎΠ²ΡΡ ΠΏΠΎΠ΄ΡΠΈΠΏΠ½ΠΈΠΊΠ°Ρ , ΠΊΠΎΡΠΎΡΡΠ΅ ΡΠΈΠΊΡΠΈΡΡΡΡΡΡ Π½Π° ΡΡΠ°Π½ΠΈΠ½Π΅. ΠΠΎΠ½ΡΡΡΡΠΊΡΠΈΡ ΠΌΠΎΠΆΠ΅Ρ Π±ΡΡΡ ΠΈ ΡΡΠ°ΡΠΈΠΎΠ½Π°ΡΠ½ΠΎΠΉ, Π½ΠΎ ΡΡΠΎ Π²ΡΡΡΠ΅ΡΠ°Π΅ΡΡΡ ΡΠ΅Π΄ΠΊΠΎ. ΠΠ±ΡΡΠ½ΠΎ Π½Π° ΡΡΠ°ΠΏΠ°Ρ ΠΏΡΠΎΠ΅ΠΊΡΠΈΡΠΎΠ²Π°Π½ΠΈΡ ΠΎΠΏΡΠ΅Π΄Π΅Π»ΡΠ΅ΡΡΡ Π²ΠΎΠ·ΠΌΠΎΠΆΠ½ΠΎΡΡΡ ΡΡΠ°Π½ΡΠΏΠΎΡΡΠΈΡΠΎΠ²ΠΊΠΈ ΠΈΠ»ΠΈ ΠΏΠ΅ΡΠ΅ΠΌΠ΅ΡΠ΅Π½ΠΈΡ Π°Π³ΡΠ΅Π³Π°ΡΠ° Π² ΡΠ΅Ρ ΠΈΠ»ΠΈ ΠΈΠ½ΡΡ ΡΡΠ»ΠΎΠ²ΠΈΡΡ . ΠΠΌΠ΅Π½Π½ΠΎ Π·Π° ΡΡΠΈ ΡΡΠ½ΠΊΡΠΈΠΈ ΠΎΡΠ²Π΅ΡΠ°Π΅Ρ ΠΎΡΠ½Π°ΡΡΠΊΠ° Π² Π²ΠΈΠ΄Π΅ ΠΎΠΏΠΎΡΠ½ΡΡ ΠΊΠΎΠ»Π΅Ρ ΠΈ ΡΠ°ΠΏΡΡ. ΠΡΡΠΏΠΏΠ° ΠΏΠΎΠ΄ΡΠΈΠΏΠ½ΠΈΠΊΠΎΠ² ΠΎΠ±Π΅ΡΠΏΠ΅ΡΠΈΠ²Π°Π΅Ρ Π²ΠΎΠ·ΠΌΠΎΠΆΠ½ΠΎΡΡΡ ΠΊΡΡΡΠ΅Π½ΠΈΡ ΠΎΠ±ΠΎΡΡΠ΄ΠΎΠ²Π°Π½ΠΈΡ Π²ΠΎΠΊΡΡΠ³ ΠΎΡΠΈ ΡΠ°ΠΏΡ. ΠΡΠ΅ΠΆΠ½ΠΈΠ΅ ΠΌΠΎΠ΄Π΅Π»ΠΈ ΠΊΠΎΠ½Π²Π΅ΡΡΠ΅ΡΠΎΠ² ΠΏΡΠ΅Π΄ΠΏΠΎΠ»Π°Π³Π°Π»ΠΈ ΡΠΎΠ²ΠΌΠ΅ΡΠ΅Π½ΠΈΠ΅ Π½Π΅ΡΡΡΠ΅ΠΉ ΠΎΡΠ½Π°ΡΡΠΊΠΈ ΠΈ ΠΊΠΎΡΠΏΡΡΠ° ΠΏΠ»Π°Π²ΠΈΠ»ΡΠ½ΠΎΠ³ΠΎ ΠΎΠ±ΠΎΡΡΠ΄ΠΎΠ²Π°Π½ΠΈΡ, Π½ΠΎ ΠΈΠ·-Π·Π° Π²ΠΎΠ·Π΄Π΅ΠΉΡΡΠ²ΠΈΡ Π²ΡΡΠΎΠΊΠΈΡ ΡΠ΅ΠΌΠΏΠ΅ΡΠ°ΡΡΡ ΠΈ Π΄Π΅ΡΠΎΡΠΌΠ°ΡΠΈΠΈ Π²ΡΠΏΠΎΠΌΠΎΠ³Π°ΡΠ΅Π»ΡΠ½ΡΡ ΠΌΠ°ΡΠ΅ΡΠΈΠ°Π»ΠΎΠ² ΡΡΠΎ ΠΊΠΎΠ½ΡΡΡΡΠΊΡΠΈΠΎΠ½Π½ΠΎΠ΅ ΡΠ΅ΡΠ΅Π½ΠΈΠ΅ Π±ΡΠ»ΠΎ Π·Π°ΠΌΠ΅Π½Π΅Π½ΠΎ Π±ΠΎΠ»Π΅Π΅ ΡΠ»ΠΎΠΆΠ½ΠΎΠΉ, Π½ΠΎ Π½Π°Π΄Π΅ΠΆΠ½ΠΎΠΉ ΠΈ Π΄ΠΎΠ»Π³ΠΎΠ²Π΅ΡΠ½ΠΎΠΉ ΡΡ Π΅ΠΌΠΎΠΉ Π²Π·Π°ΠΈΠΌΠΎΠ΄Π΅ΠΉΡΡΠ²ΠΈΡ ΡΡΠ½ΠΊΡΠΈΠΎΠ½Π°Π»ΡΠ½ΠΎΠ³ΠΎ Π±Π»ΠΎΠΊΠ° ΠΈ Π΅ΠΌΠΊΠΎΡΡΠΈ.

Π‘ΠΎΠ²ΡΠ΅ΠΌΠ΅Π½Π½ΡΠΉ ΠΊΠΈΡΠ»ΠΎΡΠΎΠ΄Π½ΡΠΉ ΠΊΠΎΠ½Π²Π΅ΡΡΠ΅Ρ, Π² ΡΠ°ΡΡΠ½ΠΎΡΡΠΈ, ΠΎΠ±Π΅ΡΠΏΠ΅ΡΠΈΠ²Π°Π΅ΡΡΡ ΠΎΡΠ΄Π΅Π»ΡΠ½ΡΠΌ ΠΎΠΏΠΎΡΠ½ΡΠΌ ΠΊΠΎΠ»ΡΡΠΎΠΌ, Π² ΡΡΡΡΠΊΡΡΡΡ ΠΊΠΎΡΠΎΡΠΎΠ³ΠΎ ΡΠ°ΠΊΠΆΠ΅ Π²Π²ΠΎΠ΄ΡΡΡΡ ΡΠ°ΠΏΡΡ ΠΈ Π·Π°ΠΊΡΠ΅ΠΏΠ»Π΅Π½Π½ΡΠΉ ΠΊΠΎΠΆΡΡ . Π’Π΅Ρ Π½ΠΎΠ»ΠΎΠ³ΠΈΡΠ΅ΡΠΊΠΈΠΉ ΠΏΡΠΎΠΌΠ΅ΠΆΡΡΠΎΠΊ ΠΌΠ΅ΠΆΠ΄Ρ ΠΊΠΎΠΆΡΡ ΠΎΠΌ ΠΈ ΠΎΠΏΠΎΡΠ½ΠΎΠΉ Π±Π°Π·ΠΎΠΉ ΠΏΡΠ΅Π΄ΠΎΡΠ²ΡΠ°ΡΠ°Π΅Ρ Π½Π΅Π³Π°ΡΠΈΠ²Π½ΠΎΠ΅ ΡΠ΅ΠΌΠΏΠ΅ΡΠ°ΡΡΡΠ½ΠΎΠ΅ Π²ΠΎΠ·Π΄Π΅ΠΉΡΡΠ²ΠΈΠ΅ Π½Π° ΡΡΠ²ΡΡΠ²ΠΈΡΠ΅Π»ΡΠ½ΡΠ΅ ΡΠ»Π΅ΠΌΠ΅Π½ΡΡ ΠΏΠΎΠ΄Π²Π΅ΡΠΎΠΊ ΠΈ ΠΏΠ΅ΡΠ΅Π΄Π²ΠΈΠΆΠ½ΡΡ ΠΌΠ΅Ρ Π°Π½ΠΈΠ·ΠΌΠΎΠ². ΠΠ΅ΠΏΠΎΡΡΠ΅Π΄ΡΡΠ²Π΅Π½Π½ΠΎ ΡΠΈΡΡΠ΅ΠΌΠ° ΡΠΈΠΊΡΠ°ΡΠΈΠΈ ΠΊΠΎΠ½Π²Π΅ΡΡΠ΅ΡΠ° ΡΠ΅Π°Π»ΠΈΠ·ΡΠ΅ΡΡΡ Π·Π° ΡΡΠ΅Ρ ΡΠΏΠΎΡΠΎΠ². Π‘Π°ΠΌΠΎ ΠΆΠ΅ ΠΎΠΏΠΎΡΠ½ΠΎΠ΅ ΠΊΠΎΠ»ΡΡΠΎ ΠΏΡΠ΅Π΄ΡΡΠ°Π²Π»ΡΠ΅Ρ ΡΠΎΠ±ΠΎΠΉ Π½Π΅ΡΡΡΠ΅Π΅ ΡΡΡΡΠΎΠΉΡΡΠ²ΠΎ, ΡΡΠΎΡΠΌΠΈΡΠΎΠ²Π°Π½Π½ΠΎΠ΅ Π΄Π²ΡΠΌΡ ΠΏΠΎΠ»ΡΠΊΠΎΠ»ΡΡΠ°ΠΌΠΈ ΠΈ ΡΠ°ΠΏΡΠΎΠ²ΡΠΌΠΈ ΠΏΠ»ΠΈΡΠ°ΠΌΠΈ, Π·Π°ΠΊΡΠ΅ΠΏΠ»Π΅Π½Π½ΡΠΌΠΈ Π² ΡΠ·Π»Π°Ρ ΡΡΡΠΊΠΎΠ²ΠΊΠΈ.
ΠΠΎΠ²ΠΎΡΠΎΡΠ½ΡΠΉ ΠΌΠ΅Ρ Π°Π½ΠΈΠ·ΠΌ

ΠΠ»Π΅ΠΊΡΡΠΎΠΏΡΠΈΠ²ΠΎΠ΄ ΠΎΠ±Π΅ΡΠΏΠ΅ΡΠΈΠ²Π°Π΅Ρ Π²ΠΎΠ·ΠΌΠΎΠΆΠ½ΠΎΡΡΡ ΠΏΠΎΠ²ΠΎΡΠΎΡΠ° ΠΊΠΎΠ½Π²Π΅ΡΡΠ΅ΡΠ° Π½Π° 360Β°. Π‘ΡΠ΅Π΄Π½ΡΡ ΡΠΊΠΎΡΠΎΡΡΡ Π²ΡΠ°ΡΠ΅Π½ΠΈΡ ΡΠΎΡΡΠ°Π²Π»ΡΠ΅Ρ 0,1-1 ΠΌ/ΠΌΠΈΠ½. Π‘Π°ΠΌΠ° ΠΏΠΎ ΡΠ΅Π±Π΅ ΡΡΠ° ΡΡΠ½ΠΊΡΠΈΡ ΡΡΠ΅Π±ΡΠ΅ΡΡΡ Π½Π΅ Π²ΡΠ΅Π³Π΄Π° β Π² Π·Π°Π²ΠΈΡΠΈΠΌΠΎΡΡΠΈ ΠΎΡ ΠΎΡΠ³Π°Π½ΠΈΠ·Π°ΡΠΈΠΈ ΡΠ΅Ρ Π½ΠΎΠ»ΠΎΠ³ΠΈΡΠ΅ΡΠΊΠΈΡ ΠΎΠΏΠ΅ΡΠ°ΡΠΈΠΉ Π² Ρ ΠΎΠ΄Π΅ ΡΠ°Π±ΠΎΡΠ΅Π³ΠΎ ΠΏΡΠΎΡΠ΅ΡΡΠ°. ΠΠ°ΠΏΡΠΈΠΌΠ΅Ρ, ΠΏΠΎΠ²ΠΎΡΠΎΡ ΠΌΠΎΠΆΠ΅Ρ ΠΏΠΎΡΡΠ΅Π±ΠΎΠ²Π°ΡΡΡΡ Π΄Π»Ρ ΠΎΡΠΈΠ΅Π½ΡΠ°ΡΠΈΠΈ Π³ΠΎΡΠ»ΠΎΠ²ΠΈΠ½Ρ ΠΏΡΡΠΌΠΎ ΠΊ ΡΠΎΡΠΊΠ΅ ΠΏΠΎΠ΄Π°ΡΠΈ Π»ΠΎΠΌΠ°, Π·Π°Π»ΠΈΠ²ΠΊΠΈ ΡΡΠ³ΡΠ½Π°, ΡΠ»ΠΈΠ²Π° ΡΡΠ°Π»ΠΈ ΠΈ Ρ. Π΄. Π€ΡΠ½ΠΊΡΠΈΠΎΠ½Π°Π» ΠΏΠΎΠ²ΠΎΡΠΎΡΠ½ΠΎΠ³ΠΎ ΠΌΠ΅Ρ Π°Π½ΠΈΠ·ΠΌΠ° ΠΌΠΎΠΆΠ΅Ρ Π±ΡΡΡ ΡΠ°Π·Π½ΡΠΌ. ΠΡΠ²Π°ΡΡ ΠΈ ΠΎΠ΄Π½ΠΎΡΡΠΎΡΠΎΠ½Π½ΠΈΠ΅, ΠΈ Π΄Π²ΡΡ ΡΡΠΎΡΠΎΠ½Π½ΠΈΠ΅ ΡΠΈΡΡΠ΅ΠΌΡ. ΠΠ°ΠΊ ΠΏΡΠ°Π²ΠΈΠ»ΠΎ, ΠΊΠΈΡΠ»ΠΎΡΠΎΠ΄Π½ΡΠ΅ ΠΊΠΎΠ½Π²Π΅ΡΡΠ΅ΡΡ Π³ΡΡΠ·ΠΎΠΏΠΎΠ΄ΡΠ΅ΠΌΠ½ΠΎΡΡΡΡ Π΄ΠΎ 200 Ρ ΠΏΡΠ΅Π΄ΠΏΠΎΠ»Π°Π³Π°ΡΡ ΠΏΠΎΠ²ΠΎΡΠΎΡ Π»ΠΈΡΡ Π² ΠΎΠ΄Π½Ρ ΡΡΠΎΡΠΎΠ½Ρ. Π‘Π²ΡΠ·Π°Π½ΠΎ ΡΡΠΎ Ρ ΡΠ΅ΠΌ, ΡΡΠΎ Π² ΡΠ°ΠΊΠΈΡ ΠΊΠΎΠ½ΡΡΡΡΠΊΡΠΈΡΡ ΡΡΠ΅Π±ΡΠ΅ΡΡΡ ΠΌΠ΅Π½ΡΡΠ΅ ΠΊΡΡΡΡΡΠ΅Π³ΠΎ ΠΌΠΎΠΌΠ΅Π½ΡΠ° ΠΏΡΠΈ Π½Π°ΠΊΠ»ΠΎΠ½Π΅ Π³ΠΎΡΠ»ΠΎΠ²ΠΈΠ½Ρ. Π§ΡΠΎΠ±Ρ ΠΈΡΠΊΠ»ΡΡΠΈΡΡ ΡΠ°ΡΡ ΠΎΠ΄ Π»ΠΈΡΠ½Π΅ΠΉ ΡΠ½Π΅ΡΠ³ΠΈΠΈ ΠΏΡΠΈ ΡΠΊΡΠΏΠ»ΡΠ°ΡΠ°ΡΠΈΠΈ Π±ΠΎΠ»ΡΡΠ΅Π³ΡΡΠ·Π½ΠΎΠ³ΠΎ ΠΎΠ±ΠΎΡΡΠ΄ΠΎΠ²Π°Π½ΠΈΡ, Π΅Π³ΠΎ ΠΎΠ±Π΅ΡΠΏΠ΅ΡΠΈΠ²Π°ΡΡ ΠΌΠ΅Ρ Π°Π½ΠΈΠ·ΠΌΠΎΠΌ Π΄Π²ΡΡ ΡΡΠΎΡΠΎΠ½Π½Π΅Π³ΠΎ ΠΏΠΎΠ²ΠΎΡΠΎΡΠ°, ΡΡΠΎ ΠΊΠΎΠΌΠΏΠ΅Π½ΡΠΈΡΡΠ΅Ρ Π·Π°ΡΡΠ°ΡΡ Π½Π° ΠΌΠ°Π½ΠΈΠΏΡΠ»ΡΡΠΈΠΈ Ρ Π³ΠΎΡΠ»ΠΎΠ²ΠΈΠ½ΠΎΠΉ. Π ΡΡΡΡΠΊΡΡΡΡ ΡΠΈΡΡΠ΅ΠΌΡ ΠΊΡΡΡΠ΅Π½ΠΈΡ Π²Ρ ΠΎΠ΄ΠΈΡ ΡΠ΅Π΄ΡΠΊΡΠΎΡ, ΡΠ»Π΅ΠΊΡΡΠΎΠ΄Π²ΠΈΠ³Π°ΡΠ΅Π»Ρ ΠΈ ΡΠΏΠΈΠ½Π΄Π΅Π»Ρ. ΠΡΠΎ ΡΡΠ°Π΄ΠΈΡΠΈΠΎΠ½Π½Π°Ρ ΠΊΠΎΠΌΠΏΠΎΠ½ΠΎΠ²ΠΊΠ° ΡΡΠ°ΡΠΈΠΎΠ½Π°ΡΠ½ΠΎΠ³ΠΎ ΠΏΡΠΈΠ²ΠΎΠ΄Π°, Π·Π°ΠΊΡΠ΅ΠΏΠ»Π΅Π½Π½ΠΎΠ³ΠΎ Π½Π° Π±Π΅ΡΠΎΠ½Π½ΠΎΠΉ ΡΡΡΠΆΠΊΠ΅. ΠΠΎΠ»Π΅Π΅ ΡΠ΅Ρ Π½ΠΎΠ»ΠΎΠ³ΠΈΡΠ½ΡΠ΅ Π½Π°Π²Π΅ΡΠ½ΡΠ΅ ΠΌΠ΅Ρ Π°Π½ΠΈΠ·ΠΌΡ ΡΠΈΠΊΡΠΈΡΡΡΡΡΡ Π½Π° ΡΠ°ΠΏΡΠ΅ ΠΈ ΠΏΡΠΈΠ²ΠΎΠ΄ΡΡΡΡ Π² Π΄Π΅ΠΉΡΡΠ²ΠΈΠ΅ Π·Π° ΡΡΠ΅Ρ Π²Π΅Π΄ΠΎΠΌΠΎΠ³ΠΎ Π·ΡΠ±ΡΠ°ΡΠΎΠ³ΠΎ ΠΊΠΎΠ»Π΅ΡΠ° Ρ ΡΠΈΡΡΠ΅ΠΌΠΎΠΉ ΠΏΠΎΠ΄ΡΠΈΠΏΠ½ΠΈΠΊΠΎΠ², ΠΊΠΎΡΠΎΡΡΠ΅ ΡΠ°ΠΊΠΆΠ΅ ΡΠ΅ΡΠ΅Π· ΡΠΈΡΡΠ΅ΠΌΡ Π²Π°Π»ΠΎΠ² Π°ΠΊΡΠΈΠ²ΠΈΠ·ΠΈΡΡΡΡΡΡ ΡΠ»Π΅ΠΊΡΡΠΎΠΌΠΎΡΠΎΡΠ°ΠΌΠΈ.
Π Π°Π·ΠΌΠ΅ΡΡ ΠΊΠΎΠ½Π²Π΅ΡΡΠ΅ΡΠ°
Π Ρ ΠΎΠ΄Π΅ ΠΏΡΠΎΠ΅ΠΊΡΠΈΡΠΎΠ²Π°Π½ΠΈΡ ΠΏΠ°ΡΠ°ΠΌΠ΅ΡΡΡ ΠΊΠΎΠ½ΡΡΡΡΠΊΡΠΈΠΈ Π΄ΠΎΠ»ΠΆΠ½Ρ ΡΠ°ΡΡΡΠΈΡΡΠ²Π°ΡΡΡΡ ΠΈΡΡ ΠΎΠ΄Ρ ΠΈΠ· ΡΠΎΠ³ΠΎ, ΠΊΠ°ΠΊΠΎΠΉ ΠΏΡΠΈΠΌΠ΅ΡΠ½ΡΠΉ ΠΎΠ±ΡΠ΅ΠΌ ΠΏΡΠΎΠ΄ΡΠ²ΠΊΠΈ Π±Π΅Π· ΡΡΠ΅ΡΠ° Π²ΡΠ±ΡΠΎΡΠ° ΡΠ°ΡΠΏΠ»Π°Π²Π° Π±ΡΠ΄Π΅Ρ ΠΏΡΠΎΠΈΠ·Π²ΠΎΠ΄ΠΈΡΡΡΡ. Π ΠΏΠΎΡΠ»Π΅Π΄Π½ΠΈΠ΅ Π³ΠΎΠ΄Ρ ΡΠ°Π·ΡΠ°Π±Π°ΡΡΠ²Π°ΡΡΡΡ Π°Π³ΡΠ΅Π³Π°ΡΡ, ΠΏΡΠΈΠ½ΠΈΠΌΠ°ΡΡΠΈΠ΅ ΠΌΠ°ΡΠ΅ΡΠΈΠ°Π»Ρ Π² ΠΎΠ±ΡΠ΅ΠΌΠ΅ ΠΎΡ 1 Π΄ΠΎ 0,85 ΠΌ3/Ρ. Π’Π°ΠΊΠΆΠ΅ ΡΠ°ΡΡΡΠΈΡΡΠ²Π°Π΅ΡΡΡ ΡΠΊΠ»ΠΎΠ½ Π³ΠΎΡΠ»ΠΎΠ²ΠΈΠ½Ρ, ΡΠ³ΠΎΠ» ΠΊΠΎΡΠΎΡΠΎΠ³ΠΎ Π² ΡΡΠ΅Π΄Π½Π΅ΠΌ ΡΠΎΡΡΠ°Π²Π»ΡΠ΅Ρ ΠΎΡ 20Β° Π΄ΠΎ 35Β°. ΠΠ΄Π½Π°ΠΊΠΎ ΠΏΡΠ°ΠΊΡΠΈΠΊΠ° ΡΠΊΡΠΏΠ»ΡΠ°ΡΠ°ΡΠΈΠΈ ΡΠ°ΠΊΠΈΡ ΡΠΎΠΎΡΡΠΆΠ΅Π½ΠΈΠΉ ΠΏΠΎΠΊΠ°Π·ΡΠ²Π°Π΅Ρ, ΡΡΠΎ ΠΏΡΠ΅Π²ΡΡΠ΅Π½ΠΈΠ΅ Π½Π°ΠΊΠ»ΠΎΠ½Π° Π² 26Β° ΡΡ ΡΠ΄ΡΠ°Π΅Ρ ΠΊΠ°ΡΠ΅ΡΡΠ²ΠΎ ΡΡΡΠ΅ΡΠΎΠ²ΠΊΠΈ. ΠΠΎ Π³Π»ΡΠ±ΠΈΠ½Π΅ ΡΠ°Π·ΠΌΠ΅ΡΡ ΠΊΠΎΠ½Π²Π΅ΡΡΠ΅ΡΠ° ΡΠΎΡΡΠ°Π²Π»ΡΡΡ 1-2 ΠΌ, Π½ΠΎ ΠΏΠΎ ΠΌΠ΅ΡΠ΅ ΡΠ²Π΅Π»ΠΈΡΠ΅Π½ΠΈΡ Π΅ΠΌΠΊΠΎΡΡΠΈ Π·Π°Π³ΡΡΠ·ΠΊΠΈ ΠΈ Π²ΡΡΠΎΡΠ° ΠΊΠΎΠ½ΡΡΡΡΠΊΡΠΈΠΈ ΠΌΠΎΠΆΠ΅Ρ ΡΠ²Π΅Π»ΠΈΡΠΈΠ²Π°ΡΡΡΡ. ΠΠ±ΡΡΠ½ΡΠ΅ ΠΊΠΎΠ½Π²Π΅ΡΡΠ΅ΡΡ Π³Π»ΡΠ±ΠΈΠ½ΠΎΠΉ Π΄ΠΎ 1 ΠΌ ΠΌΠΎΠ³ΡΡ ΠΏΡΠΈΠ½ΠΈΠΌΠ°ΡΡ Π·Π°Π³ΡΡΠ·ΠΊΡ Π½Π΅ Π±ΠΎΠ»Π΅Π΅ 50 Ρ. Π§ΡΠΎ ΠΊΠ°ΡΠ°Π΅ΡΡΡ Π΄ΠΈΠ°ΠΌΠ΅ΡΡΠ°, ΡΠΎ ΠΎΠ½ Π² ΡΡΠ΅Π΄Π½Π΅ΠΌ Π²Π°ΡΡΠΈΡΡΠ΅ΡΡΡ ΠΎΡ 4 Π΄ΠΎ 7 ΠΌ. Π’ΠΎΠ»ΡΠΈΠ½Π° Π³ΠΎΡΠ»ΠΎΠ²ΠΈΠ½Ρ ΡΠΎΡΡΠ°Π²Π»ΡΠ΅Ρ 2-2,5 ΠΌ.
Π€ΡΡΠ΅ΡΠΎΠ²ΠΊΠ° ΠΊΠΈΡΠ»ΠΎΡΠΎΠ΄Π½ΠΎΠ³ΠΎ ΠΊΠΎΠ½Π²Π΅ΡΡΠ΅ΡΠ°

ΠΠ±ΡΠ·Π°ΡΠ΅Π»ΡΠ½Π°Ρ ΡΠ΅Ρ Π½ΠΎΠ»ΠΎΠ³ΠΈΡΠ΅ΡΠΊΠ°Ρ ΠΏΡΠΎΡΠ΅Π΄ΡΡΠ°, Π² Ρ ΠΎΠ΄Π΅ ΠΊΠΎΡΠΎΡΠΎΠΉ Π²Π½ΡΡΡΠ΅Π½Π½ΠΈΠ΅ ΡΡΠ΅Π½Ρ ΠΊΠΎΠ½Π²Π΅ΡΡΠ΅ΡΠ° ΠΎΠ±Π΅ΡΠΏΠ΅ΡΠΈΠ²Π°ΡΡΡΡ Π·Π°ΡΠΈΡΠ½ΡΠΌ ΡΠ»ΠΎΠ΅ΠΌ. ΠΡΠΈ ΡΡΠΎΠΌ Π½Π°Π΄ΠΎ ΡΡΠΈΡΡΠ²Π°ΡΡ, ΡΡΠΎ Π² ΠΎΡΠ»ΠΈΡΠΈΠ΅ ΠΎΡ Π±ΠΎΠ»ΡΡΠΈΠ½ΡΡΠ²Π° ΠΌΠ΅ΡΠ°Π»Π»ΡΡΠ³ΠΈΡΠ΅ΡΠΊΠΈΡ ΠΏΠ΅ΡΠ΅ΠΉ Π΄Π°Π½Π½Π°Ρ ΠΊΠΎΠ½ΡΡΡΡΠΊΡΠΈΡ ΠΏΠΎΠ΄Π²Π΅ΡΠ³Π°Π΅ΡΡΡ Π³ΠΎΡΠ°Π·Π΄ΠΎ Π±ΠΎΠ»Π΅Π΅ Π²ΡΡΠΎΠΊΠΈΠΌ ΡΠ΅ΡΠΌΠΈΡΠ΅ΡΠΊΠΈΠΌ Π½Π°Π³ΡΡΠ·ΠΊΠ°ΠΌ, ΡΡΠΎ ΠΎΠ±ΡΡΠ»Π°Π²Π»ΠΈΠ²Π°Π΅Ρ ΠΈ ΠΎΡΠΎΠ±Π΅Π½Π½ΠΎΡΡΠΈ Π²ΡΠΏΠΎΠ»Π½Π΅Π½ΠΈΡ ΡΡΡΠ΅ΡΠΎΠ²ΠΊΠ°. ΠΡΠΎ ΠΏΡΠΎΡΠ΅Π΄ΡΡΠ°, ΠΏΡΠ΅Π΄ΠΏΠΎΠ»Π°Π³Π°ΡΡΠ°Ρ ΡΠΊΠ»Π°Π΄ΠΊΡ Π΄Π²ΡΡ Π·Π°ΡΠΈΡΠ½ΡΡ ΡΠ»ΠΎΠ΅Π² β ΡΡΠ½ΠΊΡΠΈΠΎΠ½Π°Π»ΡΠ½ΠΎΠ³ΠΎ ΠΈ Π°ΡΠΌΠΈΡΡΡΡΠ΅Π³ΠΎ. ΠΠ΅ΠΏΠΎΡΡΠ΅Π΄ΡΡΠ²Π΅Π½Π½ΠΎ ΠΊ ΠΏΠΎΠ²Π΅ΡΡ Π½ΠΎΡΡΠΈ ΠΊΠΎΡΠΏΡΡΠ° ΠΏΡΠΈΠΌΡΠΊΠ°Π΅Ρ ΠΏΠ»Π°ΡΡ Π·Π°ΡΠΈΡΠ½ΠΎΠΉ Π°ΡΠΌΠ°ΡΡΡΡ ΡΠΎΠ»ΡΠΈΠ½ΠΎΠΉ 100-250 ΠΌΠΌ. ΠΠ³ΠΎ Π·Π°Π΄Π°ΡΠ° Π·Π°ΠΊΠ»ΡΡΠ°Π΅ΡΡΡ Π² ΡΠ½ΠΈΠΆΠ΅Π½ΠΈΠΈ ΡΠ΅ΠΏΠ»ΠΎΠΏΠΎΡΠ΅ΡΡ ΠΈ Π½Π΅Π΄ΠΎΠΏΡΡΠ΅Π½ΠΈΠΈ ΠΏΡΠΎΠ³Π°ΡΠ° Π²Π΅ΡΡ Π½Π΅Π³ΠΎ ΡΠ»ΠΎΡ. Π ΠΊΠ°ΡΠ΅ΡΡΠ²Π΅ ΠΌΠ°ΡΠ΅ΡΠΈΠ°Π»Π° ΠΏΡΠΈΠΌΠ΅Π½ΡΠ΅ΡΡΡ ΠΌΠ°Π³Π½Π΅Π·ΠΈΡΠΎΠ²ΡΠΉ ΠΈΠ»ΠΈ ΠΌΠ°Π³Π½Π΅Π·ΠΈΡΠΎΡ ΡΠΎΠΌΠΈΡΠΎΠ²ΡΠΉ ΠΊΠΈΡΠΏΠΈΡ, ΠΊΠΎΡΠΎΡΡΠΉ ΠΌΠΎΠΆΠ΅Ρ ΡΠ»ΡΠΆΠΈΡΡ Π³ΠΎΠ΄Π°ΠΌΠΈ Π±Π΅Π· ΠΎΠ±Π½ΠΎΠ²Π»Π΅Π½ΠΈΡ.
ΠΠ΅ΡΡ Π½ΠΈΠΉ ΡΠ°Π±ΠΎΡΠΈΠΉ ΡΠ»ΠΎΠΉ ΠΈΠΌΠ΅Π΅Ρ ΡΠΎΠ»ΡΠΈΠ½Ρ ΠΏΠΎΡΡΠ΄ΠΊΠ° 500-700 ΠΌΠΌ ΠΈ Π·Π°ΠΌΠ΅Π½ΡΠ΅ΡΡΡ Π΄ΠΎΠ²ΠΎΠ»ΡΠ½ΠΎ ΡΠ°ΡΡΠΎ ΠΏΠΎ ΠΌΠ΅ΡΠ΅ ΠΈΠ·Π½ΠΎΡΠ°. ΠΠ° ΡΡΠΎΠΌ ΡΡΠ°ΠΏΠ΅ ΠΊΠΈΡΠ»ΠΎΡΠΎΠ΄Π½ΡΠΉ ΠΊΠΎΠ½Π²Π΅ΡΡΠ΅Ρ ΠΎΠ±ΡΠ°Π±Π°ΡΡΠ²Π°Π΅ΡΡΡ Π±Π΅Π·ΠΎΠ±ΠΆΠΈΠ³ΠΎΠ²ΡΠΌΠΈ ΠΏΠ΅ΡΠΊΠΎ- ΠΈΠ»ΠΈ ΡΠΌΠΎΠ»ΠΎΠ²ΡΠ·Π°Π½Π½ΡΠΌΠΈ ΠΎΠ³Π½Π΅ΡΠΏΠΎΡΠ½ΡΠΌΠΈ ΡΠΎΡΡΠ°Π²Π°ΠΌΠΈ. ΠΡΠ½ΠΎΠ²Ρ ΠΌΠ°ΡΠ΅ΡΠΈΠ°Π»Π° Π΄Π»Ρ ΡΡΠΎΠ³ΠΎ ΡΠ»ΠΎΡ ΡΡΡΠ΅ΡΠΎΠ²ΠΊΠΈ ΡΠΎΡΡΠ°Π²Π»ΡΠ΅Ρ Π΄ΠΎΠ»ΠΎΠΌΠΈΡ Ρ Π΄ΠΎΠ±Π°Π²ΠΊΠ°ΠΌΠΈ ΠΌΠ°Π³Π½Π΅Π·ΠΈΡΠ°. Π‘ΡΠ°Π½Π΄Π°ΡΡΠ½ΡΠΉ ΡΠ°ΡΡΠ΅Ρ ΠΏΠΎ Π½Π°Π³ΡΡΠ·ΠΊΠ΅ Π΄Π΅Π»Π°Π΅ΡΡΡ ΠΈΡΡ ΠΎΠ΄Ρ ΠΈΠ· ΡΠ΅ΠΌΠΏΠ΅ΡΠ°ΡΡΡΠ½ΠΎΠ³ΠΎ Π²ΠΎΠ·Π΄Π΅ΠΉΡΡΠ²ΠΈΡ ΠΏΠΎΡΡΠ΄ΠΊΠ° 100-500 Β°Π‘.
Π’ΠΎΡΠΊΡΠ΅ΡΠΈΡΠΎΠ²Π°Π½ΠΈΠ΅ ΡΡΡΠ΅ΡΠΎΠ²ΠΊΠΈ

ΠΠΎΠ΄ Π°Π³ΡΠ΅ΡΡΠΈΠ²Π½ΡΠΌΠΈ ΡΠ΅ΠΌΠΏΠ΅ΡΠ°ΡΡΡΠ½ΠΎ-Ρ ΠΈΠΌΠΈΡΠ΅ΡΠΊΠΈΠΌΠΈ Π²ΠΎΠ·Π΄Π΅ΠΉΡΡΠ²ΠΈΡΠΌΠΈ Π²Π½ΡΡΡΠ΅Π½Π½ΠΈΠ΅ ΠΏΠΎΠ²Π΅ΡΡ Π½ΠΎΡΡΠΈ ΠΊΠΎΠ½ΡΡΡΡΠΊΡΠΈΠΈ ΠΊΠΎΠ½Π²Π΅ΡΡΠ΅ΡΠ° Π±ΡΡΡΡΠΎ ΡΡΡΠ°ΡΠΈΠ²Π°ΡΡ ΡΠ²ΠΎΠΈ ΠΊΠ°ΡΠ΅ΡΡΠ²Π° β ΠΎΠΏΡΡΡ ΠΆΠ΅, ΡΡΠΎ ΠΊΠ°ΡΠ°Π΅ΡΡΡ Π²Π½Π΅ΡΠ½Π΅Π³ΠΎ ΠΈΠ·Π½ΠΎΡΠ° ΡΠ°Π±ΠΎΡΠ΅Π³ΠΎ ΡΠ»ΠΎΡ ΡΠ΅ΡΠΌΠΈΡΠ΅ΡΠΊΠΎΠΉ Π·Π°ΡΠΈΡΡ. Π ΠΊΠ°ΡΠ΅ΡΡΠ²Π΅ ΡΠ΅ΠΌΠΎΠ½ΡΠ½ΠΎΠΉ ΠΎΠΏΠ΅ΡΠ°ΡΠΈΠΈ ΠΏΡΠΈΠΌΠ΅Π½ΡΠ΅ΡΡΡ ΡΠΎΡΠΊΡΠ΅ΡΠΈΡΠΎΠ²Π°Π½ΠΈΠ΅ ΡΡΡΠ΅ΡΠΎΠ²ΠΊΠΈ. ΠΡΠΎ ΡΠ΅Ρ Π½ΠΎΠ»ΠΎΠ³ΠΈΡ Π³ΠΎΡΡΡΠ΅Π³ΠΎ Π²ΠΎΡΡΡΠ°Π½ΠΎΠ²Π»Π΅Π½ΠΈΡ, ΠΏΡΠΈ ΠΊΠΎΡΠΎΡΠΎΠΉ Ρ ΠΏΠΎΠΌΠΎΡΡΡ ΡΠΏΠ΅ΡΠΈΠ°Π»ΡΠ½ΠΎΠ³ΠΎ ΠΎΠ±ΠΎΡΡΠ΄ΠΎΠ²Π°Π½ΠΈΡ ΡΠΊΠ»Π°Π΄ΡΠ²Π°Π΅ΡΡΡ ΠΎΠ³Π½Π΅ΡΠΏΠΎΡΠ½ΡΠΉ ΡΠΎΡΡΠ°Π². ΠΠ³ΠΎ Π½Π°Π½ΠΎΡΡΡ Π½Π΅ ΡΠΏΠ»ΠΎΡΠ½ΡΠΌ ΡΠΏΠΎΡΠΎΠ±ΠΎΠΌ, Π° ΡΠΎΡΠ΅ΡΠ½ΠΎ Π½Π° ΡΠΈΠ»ΡΠ½ΠΎ ΠΈΠ·Π½ΠΎΡΠ΅Π½Π½ΡΠ΅ ΡΡΠ°ΡΡΠΊΠΈ Π±Π°Π·ΠΎΠ²ΠΎΠΉ ΡΡΡΠ΅ΡΠΎΠ²ΠΊΠΈ. ΠΡΠΎΡΠ΅Π΄ΡΡΠ° Π²ΡΠΏΠΎΠ»Π½ΡΠ΅ΡΡΡ Π½Π° ΡΠΏΠ΅ΡΠΈΠ°Π»ΡΠ½ΡΡ ΡΠΎΡΠΊΡΠ΅Ρ-ΠΌΠ°ΡΠΈΠ½Π°Ρ , ΠΏΠΎΠ΄Π°ΡΡΠΈΡ ΠΊ ΠΏΠΎΠ²ΡΠ΅ΠΆΠ΄Π΅Π½Π½ΠΎΠΌΡ ΡΡΠ°ΡΡΠΊΡ Π²ΠΎΠ΄ΠΎΠΎΡ Π»Π°ΠΆΠ΄Π°Π΅ΠΌΡΡ ΡΡΡΠΌΡ Ρ ΠΌΠ°ΡΡΠΎΠΉ ΠΈΠ· ΠΊΠΎΠΊΡΠΎΠ²ΠΎΠΉ ΠΏΡΠ»ΠΈ ΠΈ ΠΌΠ°Π³Π½Π΅Π·ΠΈΡΠΎΠ²ΠΎΠ³ΠΎ ΠΏΠΎΡΠΎΡΠΊΠ°.
Π’Π΅Ρ Π½ΠΎΠ»ΠΎΠ³ΠΈΠΈ Π²ΡΠΏΠ»Π°Π²ΠΊΠΈ
Π’ΡΠ°Π΄ΠΈΡΠΈΠΎΠ½Π½ΠΎ Π²ΡΠ΄Π΅Π»ΡΡΡ Π΄Π²Π° ΠΏΠΎΠ΄Ρ ΠΎΠ΄Π° ΠΊ ΡΠ΅Π°Π»ΠΈΠ·Π°ΡΠΈΠΈ ΠΊΠΈΡΠ»ΠΎΡΠΎΠ΄Π½ΠΎ-ΠΊΠΎΠ½Π²Π΅ΡΡΠ΅ΡΠ½ΠΎΠ³ΠΎ ΠΏΠ»Π°Π²Π»Π΅Π½ΠΈΡ β Π±Π΅ΡΡΠ΅ΠΌΠ΅ΡΠΎΠ²ΡΠΊΠΈΠΉ ΠΈ ΡΠΎΠΌΠ°ΡΠΎΠ²ΡΠΊΠΈΠΉ. ΠΠ΄Π½Π°ΠΊΠΎ ΡΠΎΠ²ΡΠ΅ΠΌΠ΅Π½Π½ΡΠ΅ ΠΌΠ΅ΡΠΎΠ΄ΠΈΠΊΠΈ ΠΎΡΠ»ΠΈΡΠ°ΡΡΡΡ ΠΎΡ Π½ΠΈΡ Π½ΠΈΠ·ΠΊΠΈΠΌ ΡΠΎΠ΄Π΅ΡΠΆΠ°Π½ΠΈΠ΅ΠΌ Π°Π·ΠΎΡΠ° Π² ΠΏΠ΅ΡΠΈ, ΡΡΠΎ ΠΏΠΎΠ²ΡΡΠ°Π΅Ρ ΠΊΠ°ΡΠ΅ΡΡΠ²ΠΎ ΡΠ°Π±ΠΎΡΠ΅Π³ΠΎ ΠΏΡΠΎΡΠ΅ΡΡΠ°. ΠΡΠΏΠΎΠ»Π½ΡΠ΅ΡΡΡ ΡΠ΅Ρ Π½ΠΎΠ»ΠΎΠ³ΠΈΡ ΠΏΠΎ ΡΠ»Π΅Π΄ΡΡΡΠΈΠΌ ΡΡΠ°ΠΏΠ°ΠΌ:
- ΠΠ°Π³ΡΡΠ·ΠΊΠ° Π»ΠΎΠΌΠ°. ΠΠΎΡΡΠ΄ΠΊΠ° 25-27 % ΠΎΡ ΠΎΠ±ΡΠ΅ΠΉ ΠΌΠ°ΡΡΡ ΡΠΈΡ ΡΡ Π·Π°Π³ΡΡΠΆΠ°Π΅ΡΡΡ Π² Π½Π°ΠΊΠ»ΠΎΠ½Π΅Π½Π½ΡΠΉ ΠΊΠΎΠ½Π²Π΅ΡΡΠ΅Ρ ΠΏΠΎΡΡΠ΅Π΄ΡΡΠ²ΠΎΠΌ ΡΠΎΠ²ΠΊΠΎΠ².
- ΠΠ°Π»ΠΈΠ²ΠΊΠ° ΡΡΠ³ΡΠ½Π° ΠΈΠ»ΠΈ ΡΡΠ°Π»ΡΠ½ΠΎΠ³ΠΎ ΡΠΏΠ»Π°Π²Π°. ΠΠΈΠ΄ΠΊΠΈΠΉ ΠΌΠ΅ΡΠ°Π»Π» ΠΏΡΠΈ ΡΠ΅ΠΌΠΏΠ΅ΡΠ°ΡΡΡΠ΅ Π΄ΠΎ 1450 Β°Π‘ ΠΊΠΎΠ²ΡΠ°ΠΌΠΈ Π·Π°Π»ΠΈΠ²Π°Π΅ΡΡΡ Π² Π½Π°ΠΊΠ»ΠΎΠ½Π΅Π½Π½ΡΠΉ ΠΊΠΎΠ½Π²Π΅ΡΡΠ΅Ρ. ΠΠΏΠ΅ΡΠ°ΡΠΈΡ ΠΏΡΠΎΠ΄ΠΎΠ»ΠΆΠ°Π΅ΡΡΡ Π½Π΅ Π±ΠΎΠ»Π΅Π΅ 3 ΠΌΠΈΠ½.
- ΠΡΠΎΠ΄ΡΠ²ΠΊΠ°. Π ΡΡΠΎΠΉ ΡΠ°ΡΡΠΈ ΡΠ΅Ρ Π½ΠΎΠ»ΠΎΠ³ΠΈΡ Π²ΡΠΏΠ»Π°Π²ΠΊΠΈ ΡΡΠ°Π»ΠΈ Π² ΠΊΠΈΡΠ»ΠΎΡΠΎΠ΄Π½ΡΡ ΠΊΠΎΠ½Π²Π΅ΡΡΠ΅ΡΠ°Ρ Π΄ΠΎΠΏΡΡΠΊΠ°Π΅Ρ ΡΠ°Π·Π½ΡΠ΅ ΠΏΠΎΠ΄Ρ ΠΎΠ΄Ρ Π² ΠΏΠ»Π°Π½Π΅ ΠΏΠΎΠ΄Π°ΡΠΈ Π³Π°Π·ΠΎ-Π²ΠΎΠ·Π΄ΡΡΠ½ΠΎΠΉ ΡΠΌΠ΅ΡΠΈ. ΠΠΎΡΠΎΠΊ ΠΌΠΎΠΆΠ΅Ρ Π½Π°ΠΏΡΠ°Π²Π»ΡΡΡΡΡ ΡΠ²Π΅ΡΡ Ρ, ΡΠ½ΠΈΠ·Ρ, Π΄ΠΎΠ½Π½ΡΠΌ ΠΈ ΠΊΠΎΠΌΠ±ΠΈΠ½ΠΈΡΠΎΠ²Π°Π½Π½ΡΠΌ ΡΠΏΠΎΡΠΎΠ±Π°ΠΌΠΈ Π² Π·Π°Π²ΠΈΡΠΈΠΌΠΎΡΡΠΈ ΠΎΡ ΡΠΈΠΏΠ° ΠΊΠΎΠ½ΡΡΡΡΠΊΡΠΈΠΈ ΠΎΠ±ΠΎΡΡΠ΄ΠΎΠ²Π°Π½ΠΈΡ.
- ΠΠΎΠ»ΡΡΠ΅Π½ΠΈΠ΅ ΠΏΡΠΎΠ±. ΠΡΠΏΠΎΠ»Π½ΡΠ΅ΡΡΡ Π·Π°ΠΌΠ΅Ρ ΡΠ΅ΠΌΠΏΠ΅ΡΠ°ΡΡΡΡ, ΡΠ΄Π°Π»ΡΡΡΡΡ Π½Π΅Π½ΡΠΆΠ½ΡΠ΅ ΠΏΡΠΈΠΌΠ΅ΡΠΈ, ΠΎΠΆΠΈΠ΄Π°Π΅ΡΡΡ Π°Π½Π°Π»ΠΈΠ· ΡΠΎΡΡΠ°Π²Π°. ΠΡΠ»ΠΈ Π΅Π³ΠΎ ΡΠ΅Π·ΡΠ»ΡΡΠ°ΡΡ ΡΠΎΠΎΡΠ²Π΅ΡΡΡΠ²ΡΡΡ ΠΏΡΠΎΠ΅ΠΊΡΠ½ΡΠΌ ΡΡΠ΅Π±ΠΎΠ²Π°Π½ΠΈΡΠΌ, ΠΏΠ»Π°Π²ΠΊΠ° Π²ΡΠΏΡΡΠΊΠ°Π΅ΡΡΡ, Π° Π΅ΡΠ»ΠΈ Π½Π΅Ρ β Π²Π½ΠΎΡΡΡΡΡ ΠΊΠΎΡΡΠ΅ΠΊΡΠΈΡΠΎΠ²ΠΊΠΈ.

ΠΠ»ΡΡΡ ΠΈ ΠΌΠΈΠ½ΡΡΡ ΡΠ΅Ρ Π½ΠΎΠ»ΠΎΠ³ΠΈΠΈ
Π‘ΠΏΠΎΡΠΎΠ± ΡΠ΅Π½ΠΈΡΡΡ Π·Π° Π²ΡΡΠΎΠΊΡΡ ΠΏΡΠΎΠΈΠ·Π²ΠΎΠ΄ΠΈΡΠ΅Π»ΡΠ½ΠΎΡΡΡ, ΠΏΡΠΎΡΡΡΠ΅ ΡΡ Π΅ΠΌΡ ΠΏΠΎΠ΄Π°ΡΠΈ ΠΊΠΈΡΠ»ΠΎΡΠΎΠ΄Π°, ΠΊΠΎΠ½ΡΡΡΡΠΊΡΠΈΠΎΠ½Π½ΡΡ Π½Π°Π΄Π΅ΠΆΠ½ΠΎΡΡΡ ΠΈ ΠΎΡΠ½ΠΎΡΠΈΡΠ΅Π»ΡΠ½ΠΎ Π½ΠΈΠ·ΠΊΠΈΠ΅ ΡΠ°ΡΡ ΠΎΠ΄Ρ Π² ΡΠ΅Π»ΠΎΠΌ Π½Π° ΠΎΡΠ³Π°Π½ΠΈΠ·Π°ΡΠΈΡ ΠΏΡΠΎΡΠ΅ΡΡΠ°. Π§ΡΠΎ ΠΊΠ°ΡΠ°Π΅ΡΡΡ Π½Π΅Π΄ΠΎΡΡΠ°ΡΠΊΠΎΠ², ΡΠΎ ΠΊ Π½ΠΈΠΌ, Π² ΡΠ°ΡΡΠ½ΠΎΡΡΠΈ, ΠΎΡΠ½ΠΎΡΡΡΡΡ ΠΎΠ³ΡΠ°Π½ΠΈΡΠ΅Π½ΠΈΡ Π² ΠΏΠ»Π°Π½Π΅ Π΄ΠΎΠ±Π°Π²Π»Π΅Π½ΠΈΡ ΡΠ»Π°ΠΌΠ° ΠΈ Π²ΡΠΎΡΡΡΡΡΡ. Π’ΠΎΡ ΠΆΠ΅ Π»ΠΎΠΌ ΠΌΠ΅ΡΠ°Π»Π»Π° Ρ Π΄ΡΡΠ³ΠΈΠΌΠΈ Π²ΠΊΠ»ΡΡΠ΅Π½ΠΈΡΠΌΠΈ ΠΌΠΎΠΆΠ΅Ρ ΡΠΎΡΡΠ°Π²Π»ΡΡΡ Π½Π΅ Π±ΠΎΠ»Π΅Π΅ 10 %, Π° ΡΡΠΎ Π½Π΅ ΠΏΠΎΠ·Π²ΠΎΠ»ΡΠ΅Ρ Π² Π½ΡΠΆΠ½ΠΎΠΉ ΡΡΠ΅ΠΏΠ΅Π½ΠΈ ΠΌΠΎΠ΄ΠΈΡΠΈΡΠΈΡΠΎΠ²Π°ΡΡ ΡΡΡΡΠΊΡΡΡΡ Π²ΡΠΏΠ»Π°Π²ΠΊΠΈ. Π’Π°ΠΊΠΆΠ΅ ΠΏΡΠΈ Π²ΡΠ΄ΡΠ²ΠΊΠ΅ ΡΠ°ΡΡ ΠΎΠ΄ΡΠ΅ΡΡΡ Π±ΠΎΠ»ΡΡΠΎΠΉ ΠΎΠ±ΡΠ΅ΠΌ ΠΏΠΎΠ»Π΅Π·Π½ΠΎΠ³ΠΎ ΠΆΠ΅Π»Π΅Π·Π°.
ΠΡΠΈΠΌΠ΅Π½Π΅Π½ΠΈΠ΅ ΡΠ΅Ρ Π½ΠΎΠ»ΠΎΠ³ΠΈΠΈ
Π‘ΠΎΡΠ΅ΡΠ°Π½ΠΈΠ΅ ΠΏΠ»ΡΡΠΎΠ² ΠΈ ΠΌΠΈΠ½ΡΡΠΎΠ² Π² ΠΈΡΠΎΠ³Π΅ ΠΎΠ±ΡΡΠ»ΠΎΠ²ΠΈΠ»ΠΎ ΠΈ Ρ Π°ΡΠ°ΠΊΡΠ΅Ρ ΠΏΡΠΈΠΌΠ΅Π½Π΅Π½ΠΈΡ ΠΊΠΎΠ½Π²Π΅ΡΡΠ΅ΡΠΎΠ². Π ΡΠ°ΡΡΠ½ΠΎΡΡΠΈ, ΠΌΠ΅ΡΠ°Π»Π»ΡΡΠ³ΠΈΡΠ΅ΡΠΊΠΈΠ΅ ΠΊΠΎΠΌΠ±ΠΈΠ½Π°ΡΡ Π²ΡΠΏΡΡΠΊΠ°ΡΡ Π½ΠΈΠ·ΠΊΠΎΠ»Π΅Π³ΠΈΡΠΎΠ²Π°Π½Π½ΡΡ, ΡΠ³Π»Π΅ΡΠΎΠ΄ΠΈΡΡΡΡ ΠΈ Π»Π΅Π³ΠΈΡΠΎΠ²Π°Π½Π½ΡΡ ΡΡΠ°Π»Ρ Π²ΡΡΠΎΠΊΠΎΠ³ΠΎ ΠΊΠ°ΡΠ΅ΡΡΠ²Π°, Π΄ΠΎΡΡΠ°ΡΠΎΡΠ½ΠΎΠ³ΠΎ Π΄Π»Ρ ΠΏΡΠΈΠΌΠ΅Π½Π΅Π½ΠΈΡ ΠΌΠ°ΡΠ΅ΡΠΈΠ°Π»Π° Π² ΡΡΠΆΠ΅Π»ΠΎΠΉ ΠΏΡΠΎΠΌΡΡΠ»Π΅Π½Π½ΠΎΡΡΠΈ ΠΈ ΡΡΡΠΎΠΈΡΠ΅Π»ΡΡΡΠ²Π΅. ΠΠΎΠ»ΡΡΠ΅Π½ΠΈΠ΅ ΡΡΠ°Π»Π΅ΠΉ Π² ΠΊΠΈΡΠ»ΠΎΡΠΎΠ΄Π½ΠΎΠΌ ΠΊΠΎΠ½Π²Π΅ΡΡΠ΅ΡΠ΅ ΠΏΡΠΎΠΈΡΡ ΠΎΠ΄ΠΈΡ Ρ Π»Π΅Π³ΠΈΡΠΎΠ²Π°Π½ΠΈΠ΅ΠΌ ΠΈ ΡΠ»ΡΡΡΠ΅Π½ΠΈΠ΅ΠΌ ΠΎΡΠ΄Π΅Π»ΡΠ½ΡΡ ΡΠ²ΠΎΠΉΡΡΠ², ΡΡΠΎ ΡΠ°ΡΡΠΈΡΡΠ΅Ρ ΡΡΠ΅ΡΡ ΠΏΡΠΈΠΌΠ΅Π½Π΅Π½ΠΈΡ ΠΊΠΎΠ½Π΅ΡΠ½ΠΎΠΉ ΠΏΡΠΎΠ΄ΡΠΊΡΠΈΠΈ. ΠΠ· ΠΏΠΎΠ»ΡΡΠ°Π΅ΠΌΠΎΠ³ΠΎ ΡΡΡΡΡ ΠΈΠ·Π³ΠΎΡΠ°Π²Π»ΠΈΠ²Π°ΡΡ ΡΡΡΠ±Ρ, ΠΏΡΠΎΠ²ΠΎΠ»ΠΎΠΊΡ, ΡΠ΅Π»ΡΡΡ, ΠΌΠ΅ΡΠΈΠ·Ρ, ΡΠΊΠΎΠ±ΡΠ½ΡΠ΅ ΠΈΠ·Π΄Π΅Π»ΠΈΡ ΠΈ Ρ. Π΄. Π’Π΅Ρ Π½ΠΎΠ»ΠΎΠ³ΠΈΡ ΡΠΈΡΠΎΠΊΠΎ ΠΏΡΠΈΠΌΠ΅Π½ΡΠ΅ΡΡΡ ΠΈ Π² ΡΠ²Π΅ΡΠ½ΠΎΠΉ ΠΌΠ΅ΡΠ°Π»Π»ΡΡΠ³ΠΈΠΈ, Π³Π΄Π΅ ΠΏΡΠΈ Π΄ΠΎΡΡΠ°ΡΠΎΡΠ½ΠΎΠΉ ΠΏΡΠΎΠ΄ΡΠ²ΠΊΠ΅ ΠΏΠΎΠ»ΡΡΠ°ΡΡ ΡΠ΅ΡΠ½ΠΎΠ²ΡΡ ΠΌΠ΅Π΄Ρ.

ΠΠ°ΠΊΠ»ΡΡΠ΅Π½ΠΈΠ΅
ΠΠ»Π°Π²ΠΊΠ° Π² ΠΊΠΎΠ½Π²Π΅ΡΡΠ΅ΡΠ½ΡΡ ΡΠΎΠΎΡΡΠΆΠ΅Π½ΠΈΡΡ ΡΡΠΈΡΠ°Π΅ΡΡΡ ΠΌΠΎΡΠ°Π»ΡΠ½ΠΎ ΡΡΡΠ°ΡΠ΅Π²ΡΠ΅ΠΉ ΡΠ΅Ρ Π½ΠΈΠΊΠΎΠΉ, Π½ΠΎ Π΅Π΅ ΠΏΡΠΎΠ΄ΠΎΠ»ΠΆΠ°ΡΡ ΠΈΡΠΏΠΎΠ»ΡΠ·ΠΎΠ²Π°ΡΡ ΠΏΠΎ ΠΏΡΠΈΡΠΈΠ½Π°ΠΌ ΠΎΠΏΡΠΈΠΌΠ°Π»ΡΠ½ΠΎΠ³ΠΎ ΡΠΎΡΠ΅ΡΠ°Π½ΠΈΡ ΠΏΡΠΎΠΈΠ·Π²ΠΎΠ΄ΠΈΡΠ΅Π»ΡΠ½ΠΎΡΡΠΈ ΠΈ ΡΠΈΠ½Π°Π½ΡΠΎΠ²ΡΡ Π·Π°ΡΡΠ°Ρ Π½Π° ΠΎΠ±Π΅ΡΠΏΠ΅ΡΠ΅Π½ΠΈΠ΅ ΠΏΡΠΎΡΠ΅ΡΡΠ°. Π Π½Π΅ΠΌΠ°Π»ΠΎΠΉ ΡΡΠ΅ΠΏΠ΅Π½ΠΈ Π²ΠΎΡΡΡΠ΅Π±ΠΎΠ²Π°Π½Π½ΠΎΡΡΠΈ ΡΠ΅Ρ Π½ΠΎΠ»ΠΎΠ³ΠΈΠΈ ΡΠΏΠΎΡΠΎΠ±ΡΡΠ²ΡΡΡ ΠΈ ΠΊΠΎΠ½ΡΡΡΡΠΊΡΠΈΠΎΠ½Π½ΡΠ΅ Π΄ΠΎΡΡΠΎΠΈΠ½ΡΡΠ²Π° ΠΏΡΠΈΠΌΠ΅Π½ΡΠ΅ΠΌΠΎΠ³ΠΎ ΠΎΠ±ΠΎΡΡΠ΄ΠΎΠ²Π°Π½ΠΈΡ. Π’Π° ΠΆΠ΅ Π²ΠΎΠ·ΠΌΠΎΠΆΠ½ΠΎΡΡΡ ΠΏΡΡΠΌΠΎΠΉ Π·Π°Π³ΡΡΠ·ΠΊΠΈ Π»ΠΎΠΌΠ° ΠΌΠ΅ΡΠ°Π»Π»Π°, ΡΠΈΡ ΡΡ, ΡΠ»Π°ΠΌΠ° ΠΈ Π΄ΡΡΠ³ΠΈΡ ΠΎΡΡ ΠΎΠ΄ΠΎΠ², Ρ ΠΎΡΡ ΠΈ Π² ΠΎΠ³ΡΠ°Π½ΠΈΡΠ΅Π½Π½ΠΎΠΌ ΠΎΠ±ΡΠ΅ΠΌΠ΅, ΡΠ°ΡΡΠΈΡΡΠ΅Ρ Π²ΠΎΠ·ΠΌΠΎΠΆΠ½ΠΎΡΡΠΈ Π΄Π»Ρ ΠΌΠΎΠ΄ΠΈΡΠΈΠΊΠ°ΡΠΈΠΈ ΡΠΏΠ»Π°Π²Π°. ΠΡΡΠ³ΠΎΠ΅ Π΄Π΅Π»ΠΎ, ΡΡΠΎ Π΄Π»Ρ ΠΏΠΎΠ»Π½ΠΎΡΠ΅Π½Π½ΠΎΠΉ ΡΠΊΡΠΏΠ»ΡΠ°ΡΠ°ΡΠΈΠΈ ΠΊΡΡΠΏΠ½ΠΎΠ³Π°Π±Π°ΡΠΈΡΠ½ΡΡ ΠΊΠΎΠ½Π²Π΅ΡΡΠ΅ΡΠΎΠ² Ρ Π²ΠΎΠ·ΠΌΠΎΠΆΠ½ΠΎΡΡΡΠΌΠΈ ΠΏΠΎΠ²ΠΎΡΠΎΡΠ° ΡΡΠ΅Π±ΡΠ΅ΡΡΡ ΠΎΡΠ³Π°Π½ΠΈΠ·Π°ΡΠΈΡ ΡΠΎΠΎΡΠ²Π΅ΡΡΡΠ²ΡΡΡΠ΅Π³ΠΎ ΠΏΠΎΠΌΠ΅ΡΠ΅Π½ΠΈΡ Π½Π° ΠΏΡΠ΅Π΄ΠΏΡΠΈΡΡΠΈΠΈ. ΠΠΎΡΡΠΎΠΌΡ ΠΎΡΡΡΠ΅ΡΡΠ²Π»ΡΡΡ Π²ΡΠΏΠ»Π°Π²ΠΊΡ Ρ ΠΊΠΈΡΠ»ΠΎΡΠΎΠ΄Π½ΠΎΠΉ ΠΏΡΠΎΠ΄ΡΠ²ΠΊΠΎΠΉ Π² Π±ΠΎΠ»ΡΡΠΈΡ ΠΎΠ±ΡΠ΅ΠΌΠ°Ρ ΠΏΡΠ΅ΠΈΠΌΡΡΠ΅ΡΡΠ²Π΅Π½Π½ΠΎ ΠΊΡΡΠΏΠ½ΡΠ΅ ΠΊΠΎΠΌΠΏΠ°Π½ΠΈΠΈ.
ΠΠΈΡΠ»ΠΎΡΠΎΠ΄Π½ΡΠΉ ΠΊΠΎΠ½Π²Π΅ΡΡΠ΅Ρ β Π‘ΡΡΠ΄ΠΎΠΏΠ΅Π΄ΠΈΡ
1 β ΡΡΠ°Π»ΡΠ½ΠΎΠΉ ΡΠ²Π°ΡΠ½ΠΎΠΉ ΠΊΠΎΡΠΏΡΡ, Π²ΡΠ»ΠΎΠΆΠ΅Π½Π½ΡΠΉ ΠΈΠ·Π½ΡΡΡΠΈ ΠΎΠ³Π½Π΅ΡΠΏΠΎΡΠ½ΡΠΌ ΡΠ°ΠΌΠΎΡΠ½ΡΠΌ ΠΊΠΈΡΠΏΠΈΡΠΎΠΌ;
2 β ΠΆΠΈΠ΄ΠΊΠΈΠΉ ΡΠ»Π°ΠΊ;
3 β Π²Π°Π½Π½Π° ΡΠ°ΡΠΏΠ»Π°Π²Π»Π΅Π½Π½ΠΎΠ³ΠΎ ΠΌΠ΅ΡΠ°Π»Π»Π°;
4 β Π²ΠΎΠ΄ΠΎΠΎΡ Π»Π°ΠΆΠ΄Π°Π΅ΠΌΠ°Ρ ΡΡΡΠΌΠ°;
5 β ΠΎΠΏΠΎΡΡ.
Π ΠΈΡΡΠ½ΠΎΠΊ 2.3 β Π£ΡΡΡΠΎΠΉΡΡΠ²ΠΎ ΠΊΠΈΡΠ»ΠΎΡΠΎΠ΄Π½ΠΎΠ³ΠΎ ΠΊΠΎΠ½Π²Π΅ΡΡΠ΅ΡΠ°
ΠΡΠΎΡΠ΅ΡΡ ΠΈΠ΄Π΅Ρ Π² ΡΡΠ°Π»ΡΠ½ΠΎΠΌ ΡΠ²Π°ΡΠ½ΠΎΠΌ ΠΊΠΎΡΠΏΡΡΠ΅ 1 (ΡΠΈΡΡΠ½ΠΎΠΊ 2.3), Π²ΡΠ»ΠΎΠΆΠ΅Π½Π½ΡΠΌ ΠΈΠ·Π½ΡΡΡΠΈ ΠΎΠ³Π½Π΅ΡΠΏΠΎΡΠ½ΡΠΌ ΡΠ°ΠΌΠΎΡΠ½ΡΠΌ ΠΊΠΈΡΠΏΠΈΡΠΎΠΌ. Π ΠΊΠΎΠ½Π²Π΅ΡΡΠ΅Ρ ΡΠ΅ΡΠ΅Π· Π³ΠΎΡΠ»ΠΎΠ²ΠΈΠ½Ρ Π·Π°Π³ΡΡΠΆΠ°ΡΡ ΠΌΠ΅ΡΠ°Π»Π»ΠΈΡΠ΅ΡΠΊΠΈΠΉ Π»ΠΎΠΌ (ΡΠΊΡΠ°ΠΏ) ΠΈ ΠΌΠ΅ΡΠ°Π»Π»ΠΈΡΠ΅ΡΠΊΠΈΠ΅ ΠΎΡΡ ΠΎΠ΄Ρ. ΠΠ°ΡΠ΅ΠΌ Π·Π°Π»ΠΈΠ²Π°ΡΡ ΠΆΠΈΠ΄ΠΊΠΈΠΉ ΡΡΠ³ΡΠ½ ΠΈ Π·Π°Π³ΡΡΠΆΠ°ΡΡ Π‘Π°Π‘Π3 . ΠΠΎΡΠ»Π΅ ΡΡΠΎΠ³ΠΎ ΠΎΠΏΡΡΠΊΠ°ΡΡ Π²ΠΎΠ΄ΠΎΠΎΡ Π»Π°ΠΆΠ΄Π°Π΅ΠΌΡΡ ΡΡΡΠΌΡ 4 ΠΈ Π² ΡΠ΅ΡΠ΅Π½ΠΈΠΈ 18-30 ΠΌΠΈΠ½ΡΡ ΠΏΡΠΎΠ΄ΡΠ²Π°ΡΡ ΡΠ΅Ρ Π½ΠΈΡΠ΅ΡΠΊΠΈΠΌ ΠΊΠΈΡΠ»ΠΎΡΠΎΠ΄ΠΎΠΌ. Π ΡΠ΅Π·ΡΠ»ΡΡΠ°ΡΠ΅ ΠΈΠ½ΡΠ΅Π½ΡΠΈΠ²Π½ΠΎΠ³ΠΎ ΠΎΠΊΠΈΡΠ»Π΅Π½ΠΈΡ ΠΌΠ΅ΡΠ°Π»Π»Π°, ΠΊΠΎΡΠΎΡΠΎΠ΅ ΠΏΡΠΎΠΈΡΡ ΠΎΠ΄ΠΈΡ Ρ Π²ΡΠ΄Π΅Π»Π΅Π½ΠΈΠ΅ΠΌ ΡΠ΅ΠΏΠ»ΠΎΡΡ, ΡΠ΅ΠΌΠΏΠ΅ΡΠ°ΡΡΡΠ° Π² ΠΊΠΎΠ½Π²Π΅ΡΡΠ΅ΡΠ΅ Π΄ΠΎΡΡΠΈΠ³Π°Π΅Ρ 2400 ΠΎΠ‘. ΠΠ±ΡΠ°Π·ΡΠ΅ΡΡΡ Π²Π°Π½Π½Π° ΡΠ°ΡΠΏΠ»Π°Π²Π»Π΅Π½Π½ΠΎΠ³ΠΎ ΠΌΠ΅ΡΠ°Π»Π»Π° 3 ΠΈ ΠΆΠΈΠ΄ΠΊΠΈΠΉ ΡΠ»Π°ΠΊ 2. ΠΠΎΠ΄Π°ΡΠ° ΠΊΠΈΡΠ»ΠΎΡΠΎΠ΄Π° ΠΏΡΠ΅ΠΊΡΠ°ΡΠ°Π΅ΡΡΡ ΠΈ ΡΡΡΠΌΠ° ΡΠ±ΠΈΡΠ°Π΅ΡΡΡ. Π‘Π»ΠΈΠ² ΡΠ»Π°ΠΊΠ° ΠΈ ΡΠ°ΡΠΏΠ»Π°Π²Π»Π΅Π½Π½ΠΎΠ³ΠΎ ΠΌΠ΅ΡΠ°Π»Π»Π° ΠΎΡΡΡΠ΅ΡΡΠ²Π»ΡΠ΅ΡΡΡ ΠΏΡΠΈ ΠΏΠΎΠ²ΠΎΡΠΎΡΠ΅ ΠΊΠΎΠ½Π²Π΅ΡΡΠΎΡΠ° ΠΎΡΠ½ΠΎΡΠΈΡΠ΅Π»ΡΠ½ΠΎ ΠΎΠΏΠΎΡ 5.
ΠΡΠ°ΠΏΡ Π²ΡΠΏΠ»Π°Π²ΠΊΠΈ:
1. ΠΠ°Π³ΡΡΠ·ΠΊΠ° ΠΊΠΎΠ½Π²Π΅ΡΡΠ΅ΡΠ°, ΠΏΠΎΠ΄Π°ΡΠ° Π2 , ΠΎΠ±ΡΠ°Π·ΠΎΠ²Π°Π½ΠΈΠ΅ ΠΆΠΈΠ΄ΠΊΠΎΠ³ΠΎ ΡΠ»Π°ΠΊΠ° ΠΈ ΡΠ°ΡΠΏΠ»Π°Π²Π»Π΅Π½Π½ΠΎΠ³ΠΎ ΠΌΠ΅ΡΠ°Π»Π»Π°, ΡΠ»ΠΈΠ² ΡΠ»Π°ΠΊΠ°.
ΠΠ° ΡΡΠΎΠΌ ΡΡΠ°ΠΏΠ΅ ΠΏΡΠΎΠΈΡΡ ΠΎΠ΄ΠΈΡ ΠΎΠΊΠΈΡΠ»Π΅Π½ΠΈΠ΅ ΠΏΡΠΈΠΌΠ΅ΡΠ΅ΠΉ ΡΡΠ³ΡΠ½Π° , ΡΠ½ΠΈΠΆΠ΅Π½ΠΈΠ΅ Π² ΡΠ°ΡΠΏΠ»Π°Π²Π΅ ΡΠΎΠ΄Π΅ΡΠΆΠ°Π½ΠΈΡ S ΠΈ P.
2. Π Π°ΡΠΊΠΈΡΠ»Π΅Π½ΠΈΠ΅ ΡΡΠ°Π»ΠΈ.
Π Π°ΡΠΊΠΈΡΠ»ΠΈΡΠ΅Π»ΠΈ ΠΏΠΎΠ΄Π°ΡΡΡΡ Π½Π΅ Π² ΠΊΠΎΠ½Π²Π΅ΡΡΠ΅Ρ, Π° Π½Π° ΡΡΡΡΡ ΡΠ°ΡΠΏΠ»Π°Π²Π»Π΅Π½Π½ΠΎΠ³ΠΎ ΠΌΠ΅ΡΠ°Π»Π»Π° ΠΏΡΠΈ ΡΠ°Π·Π»ΠΈΠ²ΠΊΠ΅ ΡΠ°ΡΠΏΠ»Π°Π²Π° Π² ΡΠ°Π·Π»ΠΈΠ²ΠΎΡΠ½ΡΠΉ ΠΊΠΎΠ²Ρ, Ρ.ΠΊ ΠΏΡΠΈ ΠΏΠΎΠ΄Π°ΡΠ΅ Π² ΠΊΠΎΠ½Π²Π΅ΡΡΠ΅Ρ ΠΎΠ½ΠΈ Π²ΡΠ³ΠΎΡΡΡ Π² Π°ΡΠΌΠΎΡΡΠ΅ΡΠ΅ ΠΊΠΈΡΠ»ΠΎΡΠΎΠ΄Π°.
3. ΠΠ΅Π³ΠΈΡΠΎΠ²Π°Π½ΠΈΠ΅ ΡΡΠ°Π»ΠΈ
ΠΠ΅Π³ΠΈΡΡΡΡΠΈΠ΅ ΡΠ»Π΅ΠΌΠ΅Π½ΡΡ ΡΠ°ΠΊΠΆΠ΅ Π²Π²ΠΎΠ΄ΡΡΡΡ Π½Π΅ Π² ΠΊΠΎΠ½Π²Π΅ΡΡΠ΅Ρ, Π° Π² ΠΊΠΎΠ²Ρ ΠΏΠ΅ΡΠ΅Π΄ ΡΠ°Π·Π»ΠΈΠ²ΠΊΠΎΠΉ Π² Π½Π΅Π³ΠΎ ΡΡΠ°Π»ΠΈ.
ΠΡΠΎΠΈΠ·Π²ΠΎΠ΄ΠΈΡΠ΅Π»ΡΠ½ΠΎΡΡΡ ΠΊΠΎΠ½Π²Π΅ΡΡΠ΅ΡΠ° 600 ΡΠΎΠ½Π½ Π·Π° 24 ΡΠ°ΡΠ°
Π ΠΊΠΎΠ½Π²Π΅ΡΡΠ΅ΡΠ΅ Π²ΡΠΏΠ»Π°Π²Π»ΡΡΡΡΡ Π½ΠΈΠ·ΠΊΠΎΡΠ³Π»Π΅ΡΠΎΠ΄ΠΈΡΡΡΠ΅ ΠΈ Π½ΠΈΠ·ΠΊΠΎΠ»Π΅Π³ΠΈΡΠΎΠ²Π°Π½Π½ΡΠ΅ ΡΡΠ°Π»ΠΈ ΠΎΠ±ΡΡΠ½ΠΎΠ³ΠΎ ΠΊΠ°ΡΠ΅ΡΡΠ²Π°.
ΠΠ°ΡΡΠ΅Π½ΠΎΠ²ΡΠΊΠ°Ρ ΠΏΠ΅ΡΡ
ΠΡΠΎΡΠ΅ΡΡ ΠΈΠ΄Π΅Ρ Π² ΡΡΠ°Π»ΡΠ½ΠΎΠΌ ΡΠ²Π°ΡΠ½ΠΎΠΌ ΠΊΠΎΡΠΏΡΡΠ΅ 1 (ΡΠΈΡΡΠ½ΠΎΠΊ 2.4), Π²ΡΠ»ΠΎΠΆΠ΅Π½Π½ΡΠΌ ΠΈΠ·Π½ΡΡΡΠΈ ΠΎΠ³Π½Π΅ΡΠΏΠΎΡΠ½ΡΠΌ ΡΠ°ΠΌΠΎΡΠ½ΡΠΌ ΠΊΠΈΡΠΏΠΈΡΠΎΠΌ. Π ΠΏΠ΅ΡΡ ΡΠ΅ΡΠ΅Π· Π·Π°Π³ΡΡΠ·ΠΎΡΠ½ΠΎΠ΅ ΠΎΠΊΠ½ΠΎ 8 Π·Π°Π³ΡΡΠΆΠ°ΡΡ ΠΆΠ΅Π»Π΅Π·Π½ΡΡ ΡΡΠ΄Ρ, ΡΡΠ°Π»ΡΠ½ΠΎΠΉ Π»ΠΎΠΌ (ΡΠΊΡΠ°ΠΏ), ΠΈΠ·Π²Π΅ΡΡΠ½ΡΠΊ CaCO3. ΠΠ°ΡΠ΅ΠΌ ΡΡΠΈ ΠΊΠΎΠΌΠΏΠΎΠ½Π΅Π½ΡΡ ΠΏΠΎΠ΄ΠΎΠ³ΡΠ΅Π²Π°ΡΡ Π²ΠΎΠ·Π΄ΡΡ ΠΎΠΌ, Π½Π°Π³ΡΠ΅ΡΡΠΌ Ρ ΠΏΠΎΠΌΠΎΡΡΡ ΡΠ΅Π³Π΅Π½Π΅ΡΠ°ΡΠΎΡΠ° 10 Π΄ΠΎ Π’ 1200 ο°Π‘. ΠΠΎΡΠ»Π΅ ΡΡΠΎΠ³ΠΎ Π² ΠΏΠ΅ΡΡ Π·Π°Π»ΠΈΠ²Π°ΡΡ ΠΆΠΈΠ΄ΠΊΠΈΠΉ ΡΡΠ³ΡΠ½ ΠΈ ΡΠ΅ΡΠ΅Π· ΡΡΡΠΌΡ 4 ΠΏΠΎΠ΄Π°ΡΡ ΡΠΎΠΏΠ»ΠΈΠ²ΠΎ (ΠΌΠ°Π·ΡΡ, ΠΏΡΠΈΡΠΎΠ΄Π½ΡΠΉ Π³Π°Π·). Π’ΠΎΠΏΠ»ΠΈΠ²ΠΎ, ΡΠ³ΠΎΡΠ°Ρ, ΠΎΠ±ΡΠ°Π·ΡΠ΅Ρ ΡΠ°ΠΊΠ΅Π» ΠΏΠ»Π°ΠΌΠ΅Π½ΠΈ 5, ΡΠ΅ΠΌΠΏΠ΅ΡΠ°ΡΡΡΠ° ΠΊΠΎΡΠΎΡΠΎΠ³ΠΎ ΠΎΠΊΠΎΠ»ΠΎ 2000 ο°Π‘. ΠΠ±ΡΠ°Π·ΡΠ΅ΡΡΡ ΡΠ°ΡΠΏΠ»Π°Π²Π»Π΅Π½Π½ΡΠΉ ΠΌΠ΅ΡΠ°Π»Π» 3 ΠΈ ΠΆΠΈΠ΄ΠΊΠΈΠΉ ΡΠ»Π°ΠΊ 2. Π‘Π»ΠΈΠ² ΠΆΠΈΠ΄ΠΊΠΎΠ³ΠΎ ΡΠ»Π°ΠΊΠ° ΠΈ ΡΠ°ΡΠΏΠ»Π°Π²Π»Π΅Π½Π½ΠΎΠ³ΠΎ ΠΌΠ΅ΡΠ°Π»Π»Π° Π²ΡΠΏΠΎΠ»Π½ΡΠ΅ΡΡΡ ΡΠ΅ΡΠ΅Π· Π»Π΅ΡΠΊΠΈ 6 ΠΈ 7 ΡΠΎΠΎΡΠ²Π΅ΡΡΡΠ²Π΅Π½Π½ΠΎ. ΠΡΡΠ°Π±ΠΎΡΠ°Π½Π½ΡΠ΅ Π³Π°Π·Ρ ΠΎΡΠΈΡΠ°ΡΡΡΡ Π² ΠΎΡΠΈΡΡΠ½ΠΎΠΌ ΡΡΡΡΠΎΠΉΡΡΠ²Π΅ 9 ΠΈ Π²ΡΠ²ΠΎΠ΄ΡΡΡΡ Π² Π°ΡΠΌΠΎΡΡΠ΅ΡΡ.
ΠΡΠ°ΠΏΡ Π²ΡΠΏΠ»Π°Π²ΠΊΠΈ ΡΠ°ΠΊΠΈΠ΅ ΠΆΠ΅, ΠΊΠ°ΠΊ ΠΈ ΠΏΡΠΈ ΡΠ»Π΅ΠΊΡΡΠΎΠ΄ΡΠ³ΠΎΠ²ΠΎΠΉ ΠΏΠ»Π°Π²ΠΊΠ΅.
ΠΡΠΎΠΈΠ·Π²ΠΎΠ΄ΠΈΡΠ΅Π»ΡΠ½ΠΎΡΡΡ 600 ΡΠΎΠ½Π½ ΡΡΠ°Π»ΠΈ Π·Π° 24 ΡΠ°ΡΠ°
Π ΠΌΠ°ΡΡΠ΅Π½ΠΎΠ²ΡΠΊΠΈΡ ΠΏΠ΅ΡΠ°Ρ Π²ΡΠΏΠ»Π°Π²Π»ΡΡΡ Π»Π΅Π³ΠΈΡΠΎΠ²Π°Π½Π½ΡΠ΅ ΡΡΠ°Π»ΠΈ ΠΎΠ±ΡΡΠ½ΠΎΠ³ΠΎ ΠΊΠ°ΡΠ΅ΡΡΠ²Π°.
1 β ΡΡΠ°Π»ΡΠ½ΠΎΠΉ ΡΠ²Π°ΡΠ½ΠΎΠΉ ΠΊΠΎΡΠΏΡΡ, Π²ΡΠ»ΠΎΠΆΠ΅Π½Π½ΡΠΉ ΠΈΠ·Π½ΡΡΡΠΈ ΠΎΠ³Π½Π΅ΡΠΏΠΎΡΠ½ΡΠΌ ΡΠ°ΠΌΠΎΡΠ½ΡΠΌ ΠΊΠΈΡΠΏΠΈΡΠΎΠΌ; 2 β ΠΆΠΈΠ΄ΠΊΠΈΠΉ ΡΠ»Π°ΠΊ; 3 β Π²Π°Π½Π½Π° ΡΠ°ΡΠΏΠ»Π°Π²Π»Π΅Π½Π½ΠΎΠ³ΠΎ ΠΌΠ΅ΡΠ°Π»Π»Π°; 4 β ΡΡΡΠΌΠ°; | 5 β ΡΠ°ΠΊΠ΅Π» ΠΏΠ»Π°ΠΌΠ΅Π½ΠΈ; 6 β Π»Π΅ΡΠΊΠ° Π΄Π»Ρ ΡΠ»ΠΈΠ²Π° ΡΠ°ΡΠΏΠ»Π°Π²Π»Π΅Π½Π½ΠΎΠΉ ΡΡΠ°Π»ΠΈ; 7 β Π»Π΅ΡΠΊΠ° Π΄Π»Ρ ΡΠ»ΠΈΠ²Π° ΠΆΠΈΠ΄ΠΊΠΎΠ³ΠΎ ΡΠ»Π°ΠΊΠ°; 8 β Π·Π°Π³ΡΡΠ·ΠΎΡΠ½ΠΎΠ΅ ΠΎΠΊΠ½ΠΎ; 9 β ΠΎΡΠΈΡΡΠ½ΠΎΠ΅ ΡΡΡΡΠΎΠΉΡΡΠ²ΠΎ; 10 β ΡΠ΅Π³Π΅Π½Π΅ΡΠ°ΡΠΎΡ. |
Π ΠΈΡΡΠ½ΠΎΠΊ 2.4 β Π£ΡΡΡΠΎΠΉΡΡΠ²ΠΎ ΠΌΠ°ΡΡΠ΅Π½ΠΎΠ²ΡΠΊΠΎΠΉ ΠΏΠ΅ΡΠΈ |
Π ΠΠΠΠΠΠΠ Π‘Π’ΠΠΠ
ΠΠ· ΡΡΠ°Π»Π΅ΠΏΠ»Π°Π²ΠΈΠ»ΡΠ½ΠΎΠ³ΠΎ Π°Π³ΡΠ΅Π³Π°ΡΠ° ΡΡΠ°Π»Ρ Π²ΡΠΏΡΡΠΊΠ°Π΅ΡΡΡ Π² ΡΡΠ°Π»Π΅ΡΠ°Π·Π»ΠΈΠ²ΠΎΡΠ½ΡΠΉ ΠΊΠΎΠ²Ρ (ΡΠΈΡΡΠ½ΠΎΠΊ 2.6), ΠΊΠΎΡΠΎΡΡΠΉ ΠΌΠΎΡΡΠΎΠ²ΡΠΌ ΠΊΡΠ°Π½ΠΎΠΌ ΠΏΠ΅ΡΠ΅Π½ΠΎΡΡΡ ΠΊ ΠΌΠ΅ΡΡΡ ΡΠ°Π·Π»ΠΈΠ²ΠΊΠΈ ΡΡΠ°Π»ΠΈ.
1 β Π‘ΡΠ°Π»ΡΠ½ΠΎΠΉ ΡΠ²Π°ΡΠ½ΠΎΠΉ ΠΊΠΎΡΠΏΡΡ 2 β ΠΠ³Π½Π΅ΡΠΏΠΎΡΠ½ΡΠΉ ΡΠ°ΠΌΠΎΡΠ½ΡΠΉ ΠΊΠΈΡΠΏΠΈΡ 3 β ΠΠ΅ΡΠ°ΠΌΠΈΡΠ΅ΡΠΊΠΈΠΉ ΡΡΠ°ΠΊΠ°Π½ 4 β ΠΡΠ²Π΅ΡΡΡΠΈΠ΅ Π΄Π»Ρ Π²ΡΠΏΡΡΠΊΠ° ΡΡΠ°Π»ΠΈ 5 β ΠΡΠΎΠ±ΠΊΠ° ΠΈΠ· ΠΎΠ³Π½Π΅ΡΠΏΠΎΡΠ½ΠΎΠ³ΠΎ ΠΌΠ΅ΡΠ°Π»Π»Π° 6 β Π‘ΡΠ°Π»ΡΠ½Π°Ρ ΡΡΠ°Π½Π³Π° 7 β Π’ΡΡΠ±ΠΊΠ° ΠΈΠ· ΠΎΠ³Π½Π΅ΡΠΏΠΎΡΠ½ΠΎΠ³ΠΎ ΠΌΠ΅ΡΠ°Π»Π»Π° | (ΠΊΠΎΠ½ΡΡΡΡΠΊΡΠΈΡ, ΡΠΎΡΡΠΎΡΡΠ°Ρ ΠΈΠ· ΠΏΠΎΠ·. 5; 6; 7 Π½Π°Π·. ΡΡΠΎΠΏΠΎΡΠΎΠΌ) 8 β Π¦Π°ΠΏΡΡ Π΄Π»Ρ ΡΡΠ°Π½ΡΠΏΠΎΡΡΠΈΡΠΎΠ²ΠΊΠΈ ΠΊΠΎΠ²ΡΠ° 9 β Π‘Π»ΠΎΠΉ ΠΆΠΈΠ΄ΠΊΠΎΠ³ΠΎ ΡΠ»Π°ΠΊΠ° 10 β Π Π°ΡΠΏΠ»Π°Π²Π»Π΅Π½Π½ΡΠΉ ΠΌΠ΅ΡΠ°Π»Π» 11 β Π ΡΡΠ°ΠΆΠ½ΡΠΉ ΠΌΠ΅Ρ Π°Π½ΠΈΠ·ΠΌ Π΄Π»Ρ ΠΏΠΎΠ΄ΡΠ΅ΠΌΠ° ΠΈ ΠΎΠΏΡΡΠΊΠ°Π½ΠΈΡ ΡΡΠΎΠΏΠΎΡΠ° ΠΏΡΠΈ ΡΠ°Π·Π»ΠΈΠ²ΠΊΠ΅ ΡΡΠ°Π»ΠΈ |
Π ΠΈΡΡΠ½ΠΎΠΊ 2.6 β Π£ΡΡΡΠΎΠΉΡΡΠ²ΠΎ ΡΡΠ°Π»Π΅ΡΠ°Π·Π»ΠΈΠ²ΠΎΡΠ½ΠΎΠ³ΠΎ ΠΊΠΎΠ²ΡΠ° |
ΠΠ· ΡΡΠ°Π»Π΅ΡΠ°Π·Π»ΠΈΠ²ΠΎΡΠ½ΠΎΠ³ΠΎ ΠΊΠΎΠ²ΡΠ° ΡΡΠ°Π»Ρ ΡΠ°Π·Π»ΠΈΠ²Π°ΡΡ Π² ΠΈΠ·Π»ΠΎΠΆΠ½ΠΈΡΡ (ΡΠΈΡΡΠ½ΠΎΠΊ 2.7) β ΡΡΠ³ΡΠ½Π½ΡΠ΅ ΡΠΎΡΠΌΡ Π΄Π»Ρ ΠΈΠ·Π³ΠΎΡΠΎΠ²Π»Π΅Π½ΠΈΡ ΡΠ»ΠΈΡΠΊΠΎΠ² (ΡΠ»ΠΈΡΠΎΠΊ β Π·Π°Π³ΠΎΡΠΎΠ²ΠΊΠ° Π΄Π»Ρ ΠΏΠΎΠ»ΡΡΠ΅Π½ΠΈΡ ΠΏΡΠΎΠΊΠ°ΡΠ°).
Π ΠΈΡΡΠ½ΠΎΠΊ 2.7 β Π‘Π΅ΡΠ΅Π½ΠΈΠ΅ ΠΈΠ·Π»ΠΎΠΆΠ½ΠΈΡ
ΠΡΠ΅Π΄Π²Π°ΡΠΈΡΠ΅Π»ΡΠ½ΠΎ Π½Π° ΡΠ°Π±ΠΎΡΡΡ ΠΏΠΎΠ²Π΅ΡΡ Π½ΠΎΡΡΡ ΠΈΠ·Π»ΠΎΠΆΠ½ΠΈΡ Π½Π°Π½ΠΎΡΡΡΡΡ ΡΠΏΠ΅ΡΠΈΠ°Π»ΡΠ½ΡΠ΅ ΠΏΠΎΠΊΡΡΡΠΈΡ, ΠΎΠ±Π΅ΡΠΏΠ΅ΡΠΈΠ²Π°ΡΡΠΈΠ΅ Π°Π½ΡΠΈΠΏΡΠΈΠ³Π°ΡΠ½ΡΠ΅ ΡΠ²ΠΎΠΉΡΡΠ²Π° (ΠΎΠΊΠΈΡΡ ΡΠΈΠ½ΠΊΠ°, ΠΌΠ΅Π», ΡΠ°Π»ΡΠΊ, Π³ΡΠ°ΡΠΈΡ) ΠΈ ΠΈΠ·Π»ΠΎΠΆΠ½ΠΈΡΡ ΠΏΠΎΠ΄ΠΎΠ³ΡΠ΅Π²Π°ΡΡΡΡ Π΄ΠΎ ΡΠ΅ΠΌΠΏΠ΅ΡΠ°ΡΡΡΡ 50-60 ΒΊΠ‘.
ΠΠ·Π»ΠΎΠΆΠ½ΠΈΡΡ ΠΈΠΌΠ΅ΡΡ ΠΊΠ²Π°Π΄ΡΠ°ΡΠ½ΠΎΠ΅ (Π°), ΠΏΡΡΠΌΠΎΡΠ³ΠΎΠ»ΡΠ½ΠΎΠ΅ (Π±), ΠΊΡΡΠ³Π»ΠΎΠ΅ (Π²) ΠΈ ΠΌΠ½ΠΎΠ³ΠΎΠ³ΡΠ°Π½Π½ΠΎΠ΅ ΡΠ΅ΡΠ΅Π½ΠΈΠ΅ (Π³). ΠΠ· ΡΠ»ΠΈΡΠΊΠΎΠ² ΠΊΠ²Π°Π΄ΡΠ°ΡΠ½ΠΎΠ³ΠΎ ΡΠ΅ΡΠ΅Π½ΠΈΡ ΠΏΠΎΠ»ΡΡΠ°ΡΡ ΡΠΎΡΡΠΎΠ²ΠΎΠΉ ΠΏΡΠΎΠΊΠ°Ρ, ΠΏΡΡΠΌΠΎΡΠ³ΠΎΠ»ΡΠ½ΠΎΠ³ΠΎ β Π»ΠΈΡΡ.
ΠΠ· ΡΠ»ΠΈΡΠΊΠΎΠ² ΠΊΡΡΠ³Π»ΠΎΠ³ΠΎ ΡΠ΅ΡΠ΅Π½ΠΈΡ ΠΈΠ·Π³ΠΎΡΠ°Π²Π»ΠΈΠ²Π°ΡΡ ΡΡΡΠ±Ρ ΠΈ Π΄ΡΡΠ³ΠΈΠ΅ ΡΠ΅Π»Π° Π²ΡΠ°ΡΠ΅Π½ΠΈΡ. ΠΠ½ΠΎΠ³ΠΎΠ³ΡΠ°Π½Π½ΡΠ΅ ΡΠ»ΠΈΡΠΊΠΈ ΠΈΡΠΏΠΎΠ»ΡΠ·ΡΡΡ Π΄Π»Ρ ΠΏΠΎΠ»ΡΡΠ΅Π½ΠΈΡ ΠΏΠΎΠΊΠΎΠ²ΠΎΠΊ.
ΠΡΠΏΠ»Π°Π²ΠΊΠ° ΡΡΠ°Π»ΠΈ Π² ΠΊΠΈΡΠ»ΠΎΡΠΎΠ΄Π½ΡΡ ΠΊΠΎΠ½Π²Π΅ΡΡΠ΅ΡΠ°Ρ β Π‘ΡΡΠ΄ΠΎΠΏΠ΅Π΄ΠΈΡ
Π ΠΈΡ. 10.1. ΠΠ°ΡΡΠ΅Π½ΠΎΠ²ΡΠΊΠ°Ρ ΠΏΠ΅ΡΡ Π΄Π»Ρ Π²ΡΠΏΠ»Π°Π²ΠΊΠΈ ΡΡΠ°Π»ΠΈ
Π ΠΏΠ΅ΡΠ΅Π΄Π½Π΅ΠΉ Π΅Π΅ ΡΡΠ΅Π½ΠΊΠ΅ Π½Π°Ρ ΠΎΠ΄ΡΡΡΡ Π·Π°Π²Π°Π»ΠΎΡΠ½ΡΠ΅ ΠΎΠΊΠ½Π°, ΡΠ΅ΡΠ΅Π· ΠΊΠΎΡΠΎΡΡΠ΅ Π² ΠΏΠ΅ΡΡ Π·Π°Π³ΡΡΠΆΠ°ΡΡ ΡΠ²Π΅ΡΠ΄ΡΠΉ ΡΡΠ³ΡΠ½, ΠΌΠ΅ΡΠ°Π»Π»ΠΈΡΠ΅ΡΠΊΠΈΠΉ Π»ΠΎΠΌ, Π·Π°Π»ΠΈΠ²Π°ΡΡ ΠΆΠΈΠ΄ΠΊΠΈΠΉ ΡΡΠ³ΡΠ½, ΠΏΠΎΠ΄Π°ΡΡ ΡΠ»Π°ΠΊΠΎΠΎΠ±ΡΠ°Π·ΡΡΡΠΈΠ΅ ΠΌΠ°ΡΠ΅ΡΠΈΠ°Π»Ρ (ΡΠ»ΡΡΡ) ΠΈ ΡΠ°Π·Π»ΠΈΡΠ½ΡΠ΅ Π΄ΠΎΠ±Π°Π²ΠΊΠΈ.
Π ΠΏΡΠΎΡΠΈΠ²ΠΎΠΏΠΎΠ»ΠΎΠΆΠ½ΠΎΠΉ Π·Π°Π΄Π½Π΅ΠΉ ΡΡΠ΅Π½Π΅ ΠΏΠ΅ΡΠΈ ΡΠ°ΡΠΏΠΎΠ»ΠΎΠΆΠ΅Π½Ρ Π²ΡΠΏΡΡΠΊΠ½ΡΠ΅ ΠΎΡΠ²Π΅ΡΡΡΠΈΡ, Π΄Π»Ρ ΡΠ΄Π°Π»Π΅Π½ΠΈΡ Π³ΠΎΡΠΎΠ²ΠΎΠΉ ΡΡΠ°Π»ΠΈ ΠΈ ΡΠ»Π°ΠΊΠ°.
Π ΠΊΠ°ΠΆΠ΄ΠΎΠΉ ΠΈΠ· ΡΠΎΡΡΠΎΠ²ΡΡ ΡΡΠ΅Π½ΠΎΠΊ ΠΏΠ΅ΡΠΈ Π΅ΡΡΡ Π΄Π²Π° ΠΊΠ°Π½Π°Π»Π°: ΠΎΠ΄ΠΈΠ½ Π΄Π»Ρ ΠΏΠΎΠ΄Π°ΡΠΈ ΡΠΎΠΏΠ»ΠΈΠ²Π°, Π²ΡΠΎΡΠΎΠΉ β Π²ΠΎΠ·Π΄ΡΡ Π°, Π½Π΅ΠΎΠ±Ρ ΠΎΠ΄ΠΈΠΌΠΎΠ³ΠΎ Π΄Π»Ρ ΡΠΆΠΈΠ³Π°Π½ΠΈΡ ΡΡΠΎΠ³ΠΎ ΡΠΎΠΏΠ»ΠΈΠ²Π°.
ΠΡΠ°ΠΏΠ»ΠΈΠ²Π°ΡΡ ΠΏΠ΅ΡΠΈ ΠΌΠ°Π·ΡΡΠΎΠΌ ΠΈΠ»ΠΈ Π³Π°Π·ΠΎΠΌ.
Π Π³Π°Π·, ΠΈ Π²ΠΎΠ·Π΄ΡΡ ΠΏΠ΅ΡΠ΅Π΄ ΠΏΠΎΠ΄Π°ΡΠ΅ΠΉ Π² ΠΌΠ°ΡΡΠ΅Π½ΠΎΠ²ΡΠΊΡΡ ΠΏΠ΅ΡΡ Π½Π°Π³ΡΠ΅Π²Π°ΡΡ Π² ΡΠΏΠ΅ΡΠΈΠ°Π»ΡΠ½ΡΡ ΠΊΠ°ΠΌΠ΅ΡΠ°Ρ β ΡΠ΅Π³Π΅Π½Π΅ΡΠ°ΡΠΎΡΠ°Ρ (Π ΠΈΡ. 10.2.):
Π ΠΈΡ. 10.2. Π‘Ρ Π΅ΠΌΠ° ΡΠ°Π±ΠΎΡΡ ΡΠ΅Π³Π΅Π½Π΅ΡΠ°ΡΠΎΡΠΎΠ² ΠΌΠ°ΡΡΠ΅Π½ΠΎΠ²ΡΠΊΠΎΠΉ ΠΏΠ΅ΡΠΈ: Π° β ΠΎΠ±ΡΠ°Ρ ΡΡ Π΅ΠΌΠ°; Π± ΠΈ Π² β ΠΏΡΠΈ ΠΏΠ΅ΡΠ΅ΠΊΠΈΠ΄ΠΊΠ΅ ΠΊΠ»Π°ΠΏΠ°Π½ΠΎΠ²
Π Π΅Π³Π΅Π½Π΅ΡΠ°ΡΠΎΡ β ΡΡΠΎ Π±ΠΎΠ»ΡΡΠ°Ρ ΠΊΠ°ΠΌΠ΅ΡΠ°, Π²ΡΠΏΠΎΠ»Π½Π΅Π½Π½Π°Ρ ΠΈΠ· ΠΎΠ³Π½Π΅ΡΠΏΠΎΡΠ½ΠΎΠ³ΠΎ ΠΌΠ°ΡΠ΅ΡΠΈΠ°Π»Π° ΠΈ Π·Π°ΠΏΠΎΠ»Π½Π΅Π½Π½Π°ΡΡΡΠ΅ΠΉΠΊΠ°ΠΌΠΈ ΠΈΠ· ΠΎΠ³Π½Π΅ΡΠΏΠΎΡΠ½ΠΎΠ³ΠΎ ΠΊΠΈΡΠΏΠΈΡΠ°, ΠΎΠ±ΡΠ°Π·ΡΡΡΠΈΠΌΠΈ Π½Π°ΡΠ°Π΄ΠΊΡ.
ΠΠ°ΡΠ°Π΄ΠΊΠ° ΡΠ΅Π³Π΅Π½Π΅ΡΠ°ΡΠΎΡΠ° Π½Π°Π³ΡΠ΅Π²Π°Π΅ΡΡΡ ΡΠ΅ΠΏΠ»ΠΎΠΌ, Π²ΡΠ½ΠΎΡΠΈΠΌΡΠΌ ΠΈΠ· ΠΏΠ΅ΡΠΈ ΡΠ°ΡΠΊΠ°Π»Π΅Π½Π½ΡΠΌΠΈ ΠΏΡΠΎΠ΄ΡΠΊΡΠ°ΠΌΠΈ ΡΠ³ΠΎΡΠ°Π½ΠΈΡ ΡΠΎΠΏΠ»ΠΈΠ²Π°, Ρ.Π΅. Π² Π½ΠΈΡ ΠΏΡΠΎΠΈΡΡ ΠΎΠ΄ΠΈΡ Π²ΠΎΡΡΡΠ°Π½ΠΎΠ²Π»Π΅Π½ΠΈΠ΅ ΡΡΡΠ°ΡΠ΅Π½Π½ΠΎΠ³ΠΎ ΡΠ΅ΠΏΠ»Π° β Π΅Π³ΠΎ ΡΠ΅Π³Π΅Π½Π΅ΡΠ°ΡΠΈΡ (ΠΎΡΡΡΠ΄Π° ΠΈ Π½Π°Π·Π²Π°Π½ΠΈΠ΅ ΡΡΠΈΡ ΠΊΠ°ΠΌΠ΅Ρ).
Π Π΅ΠΆΠΈΠΌ ΡΠ°Π±ΠΎΡΡ ΡΠ΅Π³Π΅Π½Π΅ΡΠ°ΡΠΎΡΠΎΠ²:
Π°) ΠΏΠΎΡΡΠ΅ΠΏΠ΅Π½Π½ΠΎ Π½Π°ΡΠ°Π΄ΠΊΠ° ΠΎΠ΄Π½ΠΎΠΉ ΠΏΠ°ΡΡ ΡΠ΅Π³Π΅Π½Π΅ΡΠ°ΡΠΎΡΠΎΠ², ΡΠ΅ΡΠ΅Π· ΠΊΠΎΡΠΎΡΡΠ΅ ΠΏΡΠΎΠΏΡΡΠΊΠ°ΡΡ Ρ ΠΎΠ»ΠΎΠ΄Π½ΡΠ΅ Π³Π°Π· ΠΈ Π²ΠΎΠ·Π΄ΡΡ , ΠΎΡΡΡΠ²Π°Π΅Ρ, Π° Π½Π°ΡΠ°Π΄ΠΊΠ° Π²ΡΠΎΡΠΎΠΉ ΠΏΠ°ΡΡ ΡΠ΅Π³Π΅Π½Π΅ΡΠ°ΡΠΎΡΠΎΠ², ΡΠ΅ΡΠ΅Π· ΠΊΠΎΡΠΎΡΡΠ΅ ΠΈΠ· ΠΏΠ΅ΡΠΈ ΡΡ ΠΎΠ΄ΡΡ ΠΏΡΠΎΠ΄ΡΠΊΡΡΡΠ³ΠΎΡΠ°Π½ΠΈΡ, Π½Π°Π³ΡΠ΅Π²Π°Π΅ΡΡΡ;
Π±) ΠΊΠΎΠ³Π΄Π° ΠΎΠ½Π° Π½Π°Π³ΡΠ΅Π΅ΡΡΡ Π΄ΠΎ ΠΎΠΏΡΠ΅Π΄Π΅Π»Π΅Π½Π½ΠΎΠΉ ΡΠ΅ΠΌΠΏΠ΅ΡΠ°ΡΡΡΡ, Π°Π²ΡΠΎΠΌΠ°ΡΠΈΡΠ΅ΡΠΊΠΈ ΠΌΠ΅Π½ΡΠ΅ΡΡΡ Π½Π°ΠΏΡΠ°Π²Π»Π΅Π½ΠΈΠ΅ Π΄Π²ΠΈΠΆΠ΅Π½ΠΈΡ Π³Π°Π·Π° ΠΈ Π²ΠΎΠ·Π΄ΡΡ Π° ΠΏΡΠΈ ΠΏΠΎΠΌΠΎΡΠΈ ΠΏΠ΅ΡΠ΅ΠΊΠΈΠ΄Π½ΡΡ ΠΊΠ»Π°ΠΏΠ°Π½ΠΎΠ², ΡΡΡΠ°Π½ΠΎΠ²Π»Π΅Π½Π½ΡΡ Π² ΠΊΠ°Π½Π°Π»Π°Ρ , ΠΏΠΎΠ΄Π²ΠΎΠ΄ΡΡΠΈΡ Π³Π°Π· ΠΈ Π²ΠΎΠ·Π΄ΡΡ Π² ΠΏΠ΅ΡΡ ΠΈ ΠΎΡΠ²ΠΎΠ΄ΡΡΠΈΡ ΠΏΡΠΎΠ΄ΡΠΊΡΡ ΡΠ³ΠΎΡΠ°Π½ΠΈΡ.
Π²) Π½Π°Π³ΡΠ΅ΡΡΠ΅ ΡΠ΅Π³Π΅Π½Π΅ΡΠ°ΡΠΎΡΡ Π½Π°ΡΠΈΠ½Π°ΡΡ ΡΠ°Π±ΠΎΡΠ°ΡΡ, Π° ΠΎΡΡΡΠ²ΡΠΈΠ΅ ΠΎΡΡΠ°Π½Π°Π²Π»ΠΈΠ²Π°ΡΡΡΡ Π½Π° Π½Π°Π³ΡΠ΅Π².
ΠΡΡ ΠΎΠΏΠ΅ΡΠ°ΡΠΈΡ Π½Π°Π·ΡΠ²Π°ΡΡ ΠΏΠ΅ΡΠ΅ΠΊΠΈΠ΄ΠΊΠΎΠΉ ΠΊΠ»Π°ΠΏΠ°Π½ΠΎΠ² ΠΈ ΠΎΡΡΡΠ΅ΡΡΠ²Π»ΡΡΡ ΠΏΡΠΈΠΌΠ΅ΡΠ½ΠΎ ΡΠ΅ΡΠ΅Π· ΠΊΠ°ΠΆΠ΄ΡΠ΅ 15-20 ΠΌΠΈΠ½ΡΡ.
ΠΠ°Π· ΠΈ Π²ΠΎΠ·Π΄ΡΡ ΠΏΠ΅ΡΠ΅Π΄ ΠΏΠΎΠ΄Π°ΡΠ΅ΠΉ Π² ΠΏΠ»Π°Π²ΠΈΠ»ΡΠ½ΠΎΠ΅ ΠΏΡΠΎΡΡΡΠ°Π½ΡΡΠ²ΠΎ ΠΏΠ΅ΡΠΈ ΠΏΡΠΎΡ ΠΎΠ΄ΡΡ ΡΠ΅ΡΠ΅Π· ΠΏΡΠ΅Π΄Π²Π°ΡΠΈΡΠ΅Π»ΡΠ½ΠΎ ΡΠ°Π·ΠΎΠ³ΡΠ΅ΡΡΠ΅ Π΄ΠΎ ΡΠ΅ΠΌΠΏΠ΅ΡΠ°ΡΡΡΡ ΠΎΠΊΠΎΠ»ΠΎ 1200 ΒΊΠ‘ ΠΊΠ°ΠΌΠ΅ΡΡ-ΡΠ΅Π³Π΅Π½Π΅ΡΠ°ΡΠΎΡΡ, Π³Π΄Π΅ Π½Π°Π³ΡΠ΅Π²Π°ΡΡΡΡ Π΄ΠΎ ΡΠ΅ΠΌΠΏΠ΅ΡΠ°ΡΡΡΡ 800-900 ΒΊΠ‘.
ΠΠ»Π°Π²ΠΊΠ° Π² ΠΌΠ°ΡΡΠ΅Π½ΠΎΠ²ΡΠΊΠΎΠΉ ΠΏΠ΅ΡΠΈ Π΄Π΅Π»ΠΈΡΡΡ Π½Π° Π½Π΅ΡΠΊΠΎΠ»ΡΠΊΠΎ ΡΡΠ°Π΄ΠΈΠΉ:
ΠΠ΅ΡΠ²Π°Ρ ΡΡΠ°Π΄ΠΈΡ β Π·Π°Π²Π°Π»ΠΊΠ° ΡΠΈΡ ΡΡ.
ΠΡΠΎΡΠ°Ρ ΡΡΠ°Π΄ΠΈΡ β ΠΏΡΠΎΠ³ΡΠ΅Π² ΡΠΈΡ ΡΡ ΠΈ Π·Π°Π»ΠΈΠ²ΠΊΠ° ΠΆΠΈΠ΄ΠΊΠΎΠ³ΠΎ ΡΡΠ³ΡΠ½Π°.
ΠΡΠΈ ΡΠΆΠΈΠ³Π°Π½ΠΈΠΈ ΡΠ°Π·ΠΎΠ³ΡΠ΅ΡΠΎΠ³ΠΎ Π³Π°Π·Π° Π² Π°ΡΠΌΠΎΡΡΠ΅ΡΠ΅ ΡΠ°Π·ΠΎΠ³ΡΠ΅ΡΠΎΠ³ΠΎ Π²ΠΎΠ·Π΄ΡΡ Π° Π² Π³ΠΎΡΠ΅Π»ΠΊΠ΅ ΠΎΠ±ΡΠ°Π·ΡΠ΅ΡΡΡ ΡΠ°ΠΊΠ΅Π» ΠΏΠ»Π°ΠΌΠ΅Π½ΠΈ, ΠΏΠΎΠ΄Π½ΠΈΠΌΠ°ΡΡΠΈΠΉ ΡΠ΅ΠΌΠΏΠ΅ΡΠ°ΡΡΡΡ Π² ΡΠ°Π±ΠΎΡΠ΅ΠΌ ΠΏΡΠΎΡΡΡΠ°Π½ΡΡΠ²Π΅ ΠΏΠ΅ΡΠΈ Π΄ΠΎ 1700 ΒΊΠ‘.
Π’Π²Π΅ΡΠ΄ΡΠ΅ ΡΠΈΡ ΡΠΎΠ²ΡΠ΅ ΠΌΠ°ΡΠ΅ΡΠΈΠ°Π»Ρ ΠΏΠ»Π°Π²ΡΡΡΡ Π½Π° ΠΏΠΎΠ΄ΠΈΠ½Π΅.
Π’ΡΠ΅ΡΡΡ ΡΡΠ°Π΄ΠΈΡ β ΠΏΠ»Π°Π²Π»Π΅Π½ΠΈΠ΅:
Π°) Π·Π°Π³ΡΡΠΆΠ΅Π½Π½ΡΠ΅ Π² ΠΏΠ΅ΡΡ ΠΌΠ°ΡΠ΅ΡΠΈΠ°Π»Ρ ΠΏΠΎΡΡΠ΅ΠΏΠ΅Π½Π½ΠΎ ΡΠ°ΡΠΏΠ»Π°Π²Π»ΡΡΡΡΡ, ΠΆΠ΅Π»Π΅Π·ΠΎ ΠΈ Π΄ΡΡΠ³ΠΈΠ΅ ΠΏΡΠΈΠΌΠ΅ΡΠΈ ΠΎΠΊΠΈΡΠ»ΡΡΡΡΡ, ΠΎΠ±ΡΠ°Π·ΡΡΡΡΡ ΡΠ°ΠΊΠΈΠ΅ ΠΎΠΊΠΈΡΠ»Ρ, ΠΊΠ°ΠΊ FeO, SiO2, MnO, P2O5, CO2;
Π±) ΠΈΠ· ΡΡΠΈΡ ΠΎΠΊΠΈΡΠ»ΠΎΠ² (Π½Π΅Π³Π°Π·ΠΎΠΎΠ±ΡΠ°Π·Π½ΡΡ ) ΠΈ Π·Π°Π³ΡΡΠΆΠ°Π΅ΠΌΡΡ Π² ΠΏΠ΅ΡΡ ΡΠ»Π°ΠΊΠΎΠΎΠ±ΡΠ°Π·ΡΡΡΠΈΡ ΠΌΠ°ΡΠ΅ΡΠΈΠ°Π»ΠΎΠ² (ΡΠ»ΡΡΠ°) β ΠΈΠ·Π²Π΅ΡΡΠ½ΡΠΊΠ°, ΠΊΠ²Π°ΡΡΠΈΡΠ°, ΠΏΠ»Π°Π²ΠΈΠΊΠΎΠ²ΠΎΠ³ΠΎ ΡΠΏΠ°ΡΠ° β ΡΠΎΡΠΌΠΈΡΡΠ΅ΡΡΡ ΡΠ»Π°ΠΊ;
Π²) ΠΏΠΎ ΠΎΠΊΠΎΠ½ΡΠ°Π½ΠΈΠΈ ΠΏΠ»Π°Π²Π»Π΅Π½ΠΈΡ Π½Π° ΠΏΠΎΠ΄ΠΈΠ½Π΅ ΠΏΠ΅ΡΠΈ ΡΠ°ΡΠΏΠΎΠ»Π°Π³Π°Π΅ΡΡΡ ΠΆΠΈΠ΄ΠΊΠΈΠΉ ΠΌΠ΅ΡΠ°Π»Π», ΠΏΠΎΠΊΡΡΡΡΠΉ ΡΠ»ΠΎΠ΅ΠΌ ΡΠ»Π°ΠΊΠ°.
Π§Π΅ΡΠ²Π΅ΡΡΠ°Ρ ΡΡΠ°Π΄ΠΈΡ β Β«ΠΊΠΈΠΏΠ΅Π½ΠΈΠ΅Β» ΡΡΠ°Π»ΠΈ.
ΠΠ° ΡΡΠΎΠΉ ΡΡΠ°Π΄ΠΈΠΈ ΠΏΡΠΎΠΈΡΡ ΠΎΠ΄ΠΈΡ ΠΎΠΊΠΈΡΠ»Π΅Π½ΠΈΠ΅ ΡΠ³Π»Π΅ΡΠΎΠ΄Π°:
Π‘ + Β½Π2 = Π‘Π
Π ΠΎΠ»Ρ ΡΡΠΎΠΉ ΡΠ΅Π°ΠΊΡΠΈΠΈ ΠΈΡΠΊΠ»ΡΡΠΈΡΠ΅Π»ΡΠ½ΠΎ Π²Π°ΠΆΠ½Π°.
ΠΠ±ΡΠ°Π·ΡΡΡΠΈΠ΅ΡΡ Π² ΡΠ°ΡΠΏΠ»Π°Π²Π΅ ΠΏΡΠ·ΡΡΡΠΊΠΈ ΠΎΠΊΠΈΡΠΈ ΡΠ³Π»Π΅ΡΠΎΠ΄Π° ΡΠ΅ΡΠ΅Π· ΠΆΠΈΠ΄ΠΊΠΈΠΉ ΠΌΠ΅ΡΠ°Π»Π» ΡΡΡΡΠ΅ΠΌΠ»ΡΡΡΡΡ ΠΊ Π΅Π³ΠΎ ΠΏΠΎΠ²Π΅ΡΡ Π½ΠΎΡΡΠΈ ΠΈ ΡΠ²Π»Π΅ΠΊΠ°ΡΡ Π·Π° ΡΠΎΠ±ΠΎΠΉ Π΄ΡΡΠ³ΠΈΠ΅ ΠΏΡΠΈΠΌΠ΅ΡΠΈ, Π² ΡΠ°ΡΡΠ½ΠΎΡΡΠΈ Π³Π°Π·Ρ, ΡΠ°ΡΡΠ²ΠΎΡΠ΅Π½Π½ΡΠ΅ Π² ΠΌΠ΅ΡΠ°Π»Π»Π΅.
ΠΠΎΠ²Π΅ΡΡ Π½ΠΎΡΡΡ ΠΌΠ΅ΡΠ°Π»Π»ΠΈΡΠ΅ΡΠΊΠΎΠΉ Π²Π°Π½Π½Ρ Π² ΡΡΠΎΡ ΠΏΠ΅ΡΠΈΠΎΠ΄ Π½Π°ΠΏΠΎΠΌΠΈΠ½Π°Π΅Ρ ΠΊΠΈΠΏΡΡΡΡ ΠΆΠΈΠ΄ΠΊΠΎΡΡΡ.
ΠΡΡΠ°Ρ ΡΡΠ°Π΄ΠΈΡ β Π΄ΠΎΠ²ΠΎΠ΄ΠΊΠ° ΡΡΠ°Π»ΠΈ β ΡΠ°ΡΠΊΠΈΡΠ»Π΅Π½ΠΈΠ΅ ΠΈ Π»Π΅Π³ΠΈΡΠΎΠ²Π°Π½ΠΈΠ΅.
Π ΠΌΠ°ΡΡΠ΅Π½ΠΎΠ²ΡΠΊΠΈΡ ΠΏΠ΅ΡΠ°Ρ ΠΏΠ»Π°Π²ΠΊΠ° Π΄Π»ΠΈΡΡΡ 7 β 8 ΡΠ°ΡΠΎΠ², ΠΈ Π·Π° ΠΎΠ΄Π½Ρ ΠΏΠ»Π°Π²ΠΊΡ ΠΏΠ΅ΡΡ ΠΌΠΎΠΆΠ΅Ρ Π²ΡΠ΄Π°ΡΡ Π΄ΠΎ 900 ΡΠΎΠ½Π½ ΡΡΠ°Π»ΠΈ.
ΠΠ°ΡΡΠ΄Ρ Ρ ΡΠ³Π»Π΅ΡΠΎΠ΄ΠΈΡΡΠΎΠΉ ΡΡΠ°Π»ΡΡ Π² Π½ΠΈΡ Π²ΡΠΏΠ»Π°Π²Π»ΡΡΡ ΠΌΠ½ΠΎΠ³ΠΈΠ΅ ΡΠΎΡΡΠ° ΡΠΏΠ΅ΡΠΈΠ°Π»ΡΠ½ΡΡ Π»Π΅Π³ΠΈΡΠΎΠ²Π°Π½Π½ΡΡ ΡΡΠ°Π»Π΅ΠΉ.
Π ΡΠ²ΡΠ·ΠΈ Ρ Π²ΡΡΠΎΠΊΠΎΠΉ ΡΠΊΠΎΠ½ΠΎΠΌΠΈΡΠ½ΠΎΡΡΡΡ ΠΈ Π³ΠΈΠ±ΠΊΠΎΡΡΡΡ ΡΠ΅Ρ Π½ΠΎΠ»ΠΎΠ³ΠΈΠΈ ΠΊΠΈΡΠ»ΠΎΡΠΎΠ΄Π½ΠΎ-ΠΊΠΎΠ½Π²Π΅ΠΊΡΠΎΡΠ½ΠΎΠ³ΠΎ ΡΠΏΠΎΡΠΎΠ±Π° Π²ΡΠΏΠ»Π°Π²ΠΊΠΈ ΡΡΠ°Π»ΠΈ, ΡΡΡΠΎΠΈΡΠ΅Π»ΡΡΡΠ²ΠΎ Π½ΠΎΠ²ΡΡ ΠΌΠ°ΡΡΠ΅Π½ΠΎΠ²ΡΠΊΠΈΡ ΠΏΠ΅ΡΠ΅ΠΉ ΠΏΡΠ΅ΠΊΡΠ°ΡΠ΅Π½ΠΎ.
ΠΠ΄Π½Π°ΠΊΠΎ, ΠΊΠ°ΠΊ ΠΎΡΠΌΠ΅ΡΠ°Π»ΠΎΡΡ ΡΠ°Π½Π΅Π΅, Π΅ΡΡ Π΄ΠΎ Π½Π°ΡΡΠΎΡΡΠ΅Π³ΠΎ Π²ΡΠ΅ΠΌΠ΅Π½ΠΈ 20% ΡΡΠ°Π»ΠΈ Π²ΡΠΏΠ»Π°Π²Π»ΡΠ΅ΡΡΡ Ρ ΠΈΡΠΏΠΎΠ»ΡΠ·ΠΎΠ²Π°Π½ΠΈΠ΅ΠΌ ΠΌΠ°ΡΡΠ΅Π½ΠΎΠ², ΠΏΠΎΡΡΠΎΠΌΡ ΠΎΡΡΡΠ΅ΡΡΠ²Π»ΡΠ΅ΡΡΡ ΡΡΠ΄ ΠΌΠ΅ΡΠΎΠΏΡΠΈΡΡΠΈΠΉ ΠΏΠΎ ΠΈΠ½ΡΠ΅Π½ΡΠΈΡΠΈΠΊΠ°ΡΠΈΠΈ ΠΈΡ ΡΠ°Π±ΠΎΡΡ.
Π£Π²Π΅Π»ΠΈΡΠ΅Π½ΠΈΠ΅ ΡΠΊΠΎΠ½ΠΎΠΌΠΈΡΠ½ΠΎΡΡΠΈ ΠΌΠ°ΡΡΠ΅Π½ΠΎΠ² Π΄ΠΎΡΡΠΈΠ³Π°ΡΡ:
1) ΠΈΡΠΏΠΎΠ»ΡΠ·ΠΎΠ²Π°Π½ΠΈΠ΅ΠΌ Π²ΠΎΠ·Π΄ΡΡ Π°, ΠΎΠ±ΠΎΠ³Π°ΡΡΠ½Π½ΠΎΠ³ΠΎ ΠΊΠΈΡΠ»ΠΎΡΠΎΠ΄ΠΎΠΌ Π΄ΠΎ 30%;
2) ΠΏΡΠΈΠΌΠ΅Π½Π΅Π½ΠΈΠ΅ΠΌ Π²ΡΡΠΎΠΊΠΎΠΊΠ°Π»ΠΎΡΠΈΠΉΠ½ΠΎΠ³ΠΎ ΠΏΡΠΈΡΠΎΠ΄Π½ΠΎΠ³ΠΎ Π³Π°Π·Π°;
3) ΠΏΠ΅ΡΠ΅ΡΡΡΠΎΠΉΠΊΠΎΠΉ ΠΎΠ±ΡΡΠ½ΡΡ ΠΌΠ°ΡΡΠ΅Π½ΠΎΠ²ΡΠΊΠΈΡ ΠΏΠ΅ΡΠ΅ΠΉ Π½Π° Π΄Π²ΡΡ Π²Π°Π½Π½ΡΠ΅: Π² ΠΎΡΠ½ΠΎΠ²Ρ ΠΈΡ Π΄Π΅ΠΉΡΡΠ²ΠΈΡ ΠΏΠΎΠ»ΠΎΠΆΠ΅Π½ ΠΏΡΠΈΠ½ΡΠΈΠΏ ΡΠ°Π±ΠΎΡΡ ΠΊΠΈΡΠ»ΠΎΡΠΎΠ΄Π½ΠΎΠ³ΠΎ ΠΊΠΎΠ½Π²Π΅ΡΡΠ΅ΡΠ° β ΠΎΠΊΠΈΡΠ»Π΅Π½ΠΈΠ΅ ΡΠ³Π»Π΅ΡΠΎΠ΄Π° ΠΈ ΠΏΡΠΈΠΌΠ΅ΡΠ΅ΠΉ ΠΏΡΠΎΠ΄ΡΠ²ΠΊΠΎΠΉ ΠΊΠΈΡΠ»ΠΎΡΠΎΠ΄Π°.
ΠΠΈΡΠ»ΠΎΡΠΎΠ΄Π½ΠΎ-ΠΊΠΎΠ½Π²Π΅ΡΡΠ΅ΡΠ½ΡΠΉ ΠΌΠ΅ΡΠΎΠ΄ Π²ΡΠΏΠ»Π°Π²ΠΊΠΈ ΡΡΠ°Π»ΠΈ ΡΡΠΎ ΠΎΠ΄ΠΈΠ½ ΠΈΠ· ΡΠΏΠΎΡΠΎΠ±ΠΎΠ² ΠΏΠ΅ΡΠ΅Π΄Π΅Π»Π° ΡΡΠ³ΡΠ½Π° Π² ΡΡΠ°Π»Ρ Π±Π΅Π· ΠΈΡΠΏΠΎΠ»ΡΠ·ΠΎΠ²Π°Π½ΠΈΡ ΡΠΎΠΏΠ»ΠΈΠ²Π° ΠΏΡΡΡΠΌ ΠΏΡΠΎΠ΄ΡΠ²ΠΊΠΈ ΡΡΠ³ΡΠ½Π° ΡΠΎΠΊΠΎΠΌ ΠΊΠΈΡΠ»ΠΎΡΠΎΠ΄Π°.
ΠΡΠΈ ΡΡΠΎΠΌ ΠΎΠΊΠΈΡΠ»ΠΈΡΠ΅Π»ΡΠ½ΡΠΉ ΠΈ Π²ΠΎΡΡΡΠ°Π½ΠΎΠ²ΠΈΡΠ΅Π»ΡΠ½ΡΠΉ ΠΏΠ΅ΡΠΈΠΎΠ΄Ρ ΠΏΠ»Π°Π²ΠΊΠΈ ΡΠ°Π·Π½Π΅ΡΠ΅Π½Ρ Π½Π΅ ΡΠΎΠ»ΡΠΊΠΎ Π²ΠΎ Π²ΡΠ΅ΠΌΠ΅Π½ΠΈ, Π½ΠΎ ΠΈ Π² ΠΏΡΠΎΡΡΡΠ°Π½ΡΡΠ²Π΅: ΠΏΠ΅ΡΠ²ΡΠΉ β ΠΏΡΠΎΡΠ΅ΠΊΠ°Π΅Ρ Π² ΠΊΠΎΠ½Π²Π΅ΡΡΠ΅ΡΠ΅, Π²ΡΠΎΡΠΎΠΉ β ΠΏΠΎΡΠ»Π΅ Π²ΡΠΏΡΡΠΊΠ° ΡΡΠ°Π»ΠΈ Π² ΠΊΠΎΠ²ΡΠ΅.
Π‘ΡΠ°Π»Π΅ΠΏΠ»Π°Π²ΠΈΠ»ΡΠ½ΡΠΉ Π°Π³ΡΠ΅Π³Π°Ρ Π² ΠΊΠΈΡΠ»ΠΎΡΠΎΠ΄Π½ΠΎ-ΠΊΠΎΠ½Π²Π΅ΡΡΠΎΡΠ½ΠΎΠΌ ΠΌΠ΅ΡΠΎΠ΄Π΅ Π²ΠΊΠ»ΡΡΠ°Π΅Ρ: ΡΠΎΠ±ΡΡΠ²Π΅Π½Π½ΠΎ ΠΊΠΎΠ½Π²Π΅ΡΡΠ΅Ρ, ΡΠΈΡΡΠ΅ΠΌΡ ΠΏΠΎΠ΄Π°ΡΠΈ ΠΊΠΈΡΠ»ΠΎΡΠΎΠ΄Π° (ΡΡΡΠΌΡ) ΠΈ ΡΠΈΡΡΠ΅ΠΌΡ ΠΎΡΠΈΡΡΠΊΠΈ ΠΊΠΎΠ½Π²Π΅ΡΡΠΎΡΠ½ΡΡ Π³Π°Π·ΠΎΠ² (Π ΠΈΡ. 10.3).
Π ΠΈΡ. 10.3 ΠΠΈΡΠ»ΠΎΡΠΎΠ΄Π½ΡΠΉ ΠΊΠΎΠ½Π²Π΅ΡΡΠ΅Ρ Ρ Π²Π΅ΡΡ Π½Π΅ΠΉ ΠΏΡΠΎΠ΄ΡΠ²ΠΊΠΎΠΉ. 1 β ΡΡΠ°Π»ΡΠ½ΠΎΠΉ ΠΊΠΎΠΆΡΡ ; 2 β ΠΎΠ³Π½Π΅ΡΠΏΠΎΡΠ½Π°Ρ ΡΡΡΠ΅ΡΠΎΠ²ΠΊΠ°; 3 β ΠΊΠΈΡΠ»ΠΎΡΠΎΠ΄Π½Π°Ρ ΡΡΡΠΌΠ°; 4 β Π·Π°Π²Π°Π»ΠΊΠ° ΡΠ»ΡΡΠ°; 5 β Π»Π΅Π³ΠΈΡΡΡΡΠΈΠ΅ Π΄ΠΎΠ±Π°Π²ΠΊΠΈ; 6 β Π»Π΅ΡΠΊΠ°; 7 β ΠΊΠΎΠ²Ρ; 8 β Π·Π°Π³ΠΎΡΠΎΠ²ΠΊΠ°.
ΠΠΎΠ½Π²Π΅ΡΡΠΎΡ, ΠΏΡΠ΅Π΄ΡΡΠ°Π²Π»ΡΠ΅Ρ ΡΠΎΠ±ΠΎΠΉ ΡΡΠ°Π»ΡΠ½ΠΎΠΉ ΠΊΠΎΠ½ΡΠ΅ΠΉΠ½Π΅Ρ Π³ΡΡΡΠ΅Π²ΠΈΠ΄Π½ΠΎΠΉ ΡΠΎΡΠΌΡ (1) Π²ΠΌΠ΅ΡΡΠΈΠΌΠΎΡΡΡΡ 100-350 Ρ. ΠΠ·Π½ΡΡΡΠΈ ΠΊΠΎΠ½Π²Π΅ΡΡΠ΅Ρ Π²ΡΠ»ΠΎΠΆΠ΅Π½ ΠΎΠ³Π½Π΅ΡΠΏΠΎΡΠ½ΡΠΌ ΠΊΠΈΡΠΏΠΈΡΠΎΠΌ (2).
Π Π²Π΅ΡΡ Π½Π΅ΠΉ ΡΠ°ΡΡΠΈ ΡΠΎΡΡΠ΄Π° Π½Π°Ρ ΠΎΠ΄ΠΈΡΡΡ Π³ΠΎΡΠ»ΠΎΠ²ΠΈΠ½Π°, ΠΊΠΎΡΠΎΡΠ°Ρ ΡΠ»ΡΠΆΠΈΡ Π΄Π»Ρ Π·Π°Π»ΠΈΠ²ΠΊΠΈ ΡΡΠ³ΡΠ½Π°, Π·Π°Π²Π°Π»ΠΊΠΈ ΡΠ²ΡΡΠ΄ΡΡ ΠΊΠΎΠΌΠΏΠΎΠ½Π΅Π½ΡΠΎΠ² ΡΠΈΡ ΡΡ ΠΈ ΠΎΡΠ²ΠΎΠ΄Π° Π³Π°Π·Π°; ΡΠ±ΠΎΠΊΡΡΠ°ΡΠΏΠΎΠ»ΠΎΠΆΠ΅Π½Π° Π»Π΅ΡΠΊΠ° (4) β ΠΎΠΊΠΎΡΠΊΠΎ Π΄Π»Ρ ΡΠ»ΠΈΠ²Π° ΡΡΠ°Π»ΠΈ.
Π§Π΅ΡΠ΅Π· Π³ΠΎΡΠ»ΠΎΠ²ΠΈΠ½Ρ Π² ΠΊΠΎΠ½Π²Π΅ΡΡΠ΅Ρ ΡΠ°ΠΊΠΆΠ΅ Π²Π²ΠΎΠ΄ΠΈΡΡΡ ΡΡΡΠΌΠ° (3) Π΄Π»Ρ ΠΏΠΎΠ΄Π°ΡΠΈ ΠΊΠΈΡΠ»ΠΎΡΠΎΠ΄Π°, ΠΈ ΠΏΡΠΎΠΈΡΡ ΠΎΠ΄ΠΈΡ ΠΆΠΈΠ΄ΠΊΠΈΠΉ ΡΠ»ΠΈΠ² ΡΠ»Π°ΠΊΠ°.
Π‘Π½Π°ΡΡΠΆΠΈ ΠΊΠΎΠ½Π²Π΅ΡΡΠ΅Ρ ΠΎΠΏΠΎΡΡΠ°Π½ ΡΡΠ°Π»ΡΠ½ΡΠΌ ΠΊΠΎΠ»ΡΡΠΎΠΌ Ρ Π΄Π²ΡΠΌΡ ΡΠ°ΠΏΡΠ°ΠΌΠΈ, ΠΊΠΎΡΠΎΡΡΠ΅ ΡΠ΄Π΅ΡΠΆΠΈΠ²Π°ΡΡ ΠΊΠΎΠ½ΡΠ΅ΠΉΠ½Π΅Ρ ΠΈ ΠΏΠΎΠ·Π²ΠΎΠ»ΡΡΡ ΠΏΠΎΠ²ΠΎΡΠ°ΡΠΈΠ²Π°ΡΡ Π΅Π³ΠΎ Π²ΠΎΠΊΡΡΠ³ Π³ΠΎΡΠΈΠ·ΠΎΠ½ΡΠ°Π»ΡΠ½ΠΎΠΉ ΠΎΡΠΈ.
1. ΠΠ΅ΡΠ΅Π΄ Π½Π°ΡΠ°Π»ΠΎΠΌ ΠΏΡΠΎΡΠ΅ΡΡΠ° ΠΏΠ»Π°Π²ΠΊΠΈ ΠΊΠΎΠ½Π²Π΅ΡΡΠ΅Ρ ΠΏΠΎΠ²ΠΎΡΠ°ΡΠΈΠ²Π°ΡΡ Π² Π½Π°ΠΊΠ»ΠΎΠ½Π½ΠΎΠ΅ ΠΏΠΎΠ»ΠΎΠΆΠ΅Π½ΠΈΠ΅, Π·Π°ΡΠ΅ΠΌ Π·Π°Π³ΡΡΠΆΠ°ΡΡ ΠΌΠ΅ΡΠ°Π»Π»ΠΈΡΠ΅ΡΠΊΠΈΠΉ Π»ΠΎΠΌ ΠΈ ΠΆΠΈΠ΄ΠΊΠΈΠΉ ΡΡΠ³ΡΠ½.
2. ΠΠΎΡΠ»Π΅ ΡΡΠΎΠ³ΠΎ ΠΊΠΎΠ½Π²Π΅ΡΡΠ΅Ρ Π²ΠΎΠ·Π²ΡΠ°ΡΠ°ΡΡ Π² Π²Π΅ΡΡΠΈΠΊΠ°Π»ΡΠ½ΠΎΠ΅ ΠΏΠΎΠ»ΠΎΠΆΠ΅Π½ΠΈΠ΅, Π·Π°Π³ΡΡΠΆΠ°ΡΡ ΡΠ»ΡΡΡ (ΠΈΠ·Π²Π΅ΡΡΠ½ΡΠΊ) ΠΈ Π²Π²ΠΎΠ΄ΡΡ ΡΡΡΠΌΡ Π΄Π»Ρ ΠΏΠΎΠ΄Π°ΡΠΈ ΠΊΠΈΡΠ»ΠΎΡΠΎΠ΄Π° ΠΏΠΎΠ΄ Π΄Π°Π²Π»Π΅Π½ΠΈΠ΅ΠΌ 1,0β1,4 ΠΠΠ°.
!!! ΠΠΈΡΠ»ΠΎΡΠΎΠ΄Π½ΡΠ΅ ΡΡΡΡΠΈ ΠΏΠΎΠ» Π΄Π°Π²Π»Π΅Π½ΠΈΠ΅ΠΌ ΠΏΡΠΎΠ½ΠΈΠ·ΡΠ²Π°ΡΡ ΠΌΠ΅ΡΠ°Π»Π», Π²ΡΠ·ΡΠ²Π°Ρ Π΅Π³ΠΎ ΡΠΈΡΠΊΡΠ»ΡΡΠΈΡ ΠΈ ΠΏΠ΅ΡΠ΅ΠΌΠ΅ΡΠΈΠ²Π°Π½ΠΈΠ΅ ΡΠΎ ΡΠ»Π°ΠΊΠΎΠΌ.
3. ΠΡΠΈ ΠΊΠΈΡΠ»ΠΎΡΠΎΠ΄Π½ΠΎ-ΠΊΠΎΠ½Π²Π΅ΡΡΠ΅ΡΠ½ΠΎΠΌ ΡΠΏΠΎΡΠΎΠ±Π΅ ΠΏΠ΅ΡΠ΅Π΄Π΅Π»Π° ΡΡΠ³ΡΠ½Π° Π² ΡΡΠ°Π»Ρ ΠΏΡΠΎΡΠ΅ΠΊΠ°ΡΡ ΡΠ΅ ΠΆΠ΅ ΡΠ΅Π°ΠΊΡΠΈΠΈ, ΡΡΠΎ ΠΈ ΠΏΡΠΈ ΠΌΠ°ΡΡΠ΅Π½ΠΎΠ²ΡΠΊΠΎΠΌ ΡΠΏΠΎΡΠΎΠ±Π΅, Π½ΠΎ Π±ΠΎΠ»Π΅Π΅ ΠΈΠ½ΡΠ΅Π½ΡΠΈΠ²Π½ΠΎ.
ΠΡΠ»Π΅Π΄ΡΡΠ²ΠΈΠ΅ ΡΠΊΠ·ΠΎΡΠ΅ΡΠΌΠΈΡΠ½ΠΎΡΡΠΈ ΡΠ΅Π°ΠΊΡΠΈΠΉ ΠΎΠΊΠΈΡΠ»Π΅Π½ΠΈΡ ΠΈ ΠΈΡ Π²ΡΡΠΎΠΊΠΎΠΉ ΡΠΊΠΎΡΠΎΡΡΠΈ ΠΏΠ΅ΡΠΈΠΎΠ΄ ΠΏΠ»Π°Π²ΠΊΠΈ Π² ΠΊΠΈΡΠ»ΠΎΡΠΎΠ΄Π½ΠΎΠΌ ΠΊΠΎΠ½Π²Π΅ΡΡΠ΅ΡΠ΅ ΠΏΡΠΎΡΠ΅ΠΊΠ°Π΅Ρ Π² Π°Π²ΡΠΎΡΠ΅ΡΠΌΠΈΡΠ½ΠΎΠΌ ΡΠ΅ΠΆΠΈΠΌΠ΅ ΠΈ Π½Π΅ ΡΡΠ΅Π±ΡΠ΅Ρ ΠΏΠΎΠ΄Π²ΠΎΠ΄Π° ΡΠ΅ΠΏΠ»Π° ΠΈΠ·Π²Π½Π΅.
ΠΡΠΈ ΡΡΠΎΠΌ ΠΎΠ±Π΅ΡΠΏΠ΅ΡΠΈΠ²Π°Π΅ΡΡΡ Π½Π°Π³ΡΠ΅Π² ΡΡΠ°Π»ΠΈ, Π²ΡΠΏΡΡΠΊΠ°Π΅ΠΌΠΎΠΉ ΠΈΠ· ΠΊΠΎΠ½Π²Π΅ΡΡΠ΅ΡΠ°, Π΄ΠΎ 1600-1650ΒΊΠ‘, ΡΡΠΎ Π·Π½Π°ΡΠΈΡΠ΅Π»ΡΠ½ΠΎ Π²ΡΡΠ΅ ΡΠ΅ΠΌΠΏΠ΅ΡΠ°ΡΡΡΡ Π·Π°Π»ΠΈΠ²Π°Π΅ΠΌΠΎΠ³ΠΎ ΡΡΠ³ΡΠ½Π°, ΠΊΠΎΡΠΎΡΠ°Ρ ΠΏΡΠΈ Π·Π°Π»ΠΈΠ²ΠΊΠ΅ Π΄ΠΎΡΡΠΈΠ³Π°Π΅Ρ 1250-1400 ΒΊΠ‘.
4. ΠΠΎ Ρ ΠΎΠ΄Ρ ΠΏΠ»Π°Π²ΠΊΠΈ Π±Π΅ΡΡΡ ΠΏΡΠΎΠ±Ρ ΠΌΠ΅ΡΠ°Π»Π»Π° Π½Π° ΡΠΊΡΠΏΡΠ΅ΡΡ-Π°Π½Π°Π»ΠΈΠ·. ΠΡΠ»ΠΈ ΡΠΎΠ΄Π΅ΡΠΆΠ°Π½ΠΈΠ΅ ΡΠ³Π»Π΅ΡΠΎΠ΄Π° ΡΠΎΠΎΡΠ²Π΅ΡΡΡΠ²ΡΠ΅Ρ Π·Π°Π΄Π°Π½Π½ΠΎΠΌΡ ΠΊΠΎΠ»ΠΈΡΠ΅ΡΡΠ²Ρ, ΠΏΡΠΎΠ΄ΡΠ²ΠΊΡ ΠΏΡΠ΅ΠΊΡΠ°ΡΠ°ΡΡ.
5. ΠΠΎΠ΄Π½ΠΈΠΌΠ°ΡΡ ΡΡΡΠΌΡ ΠΈ, ΠΏΠΎΠ²Π΅ΡΠ½ΡΠ² ΠΊΠΎΠ½Π²Π΅ΡΡΠ΅Ρ Π² Π³ΠΎΡΠΈΠ·ΠΎΠ½ΡΠ°Π»ΡΠ½ΠΎΠ΅ ΠΏΠΎΠ»ΠΎΠΆΠ΅Π½ΠΈΠ΅, Π²ΡΠΏΡΡΠΊΠ°ΡΡ ΡΡΠ°Π»Ρ ΡΠ΅ΡΠ΅Π· Π»Π΅ΡΠΊΡ, Π° Π·Π°ΡΠ΅ΠΌ ΡΠ΅ΡΠ΅Π· Π³ΠΎΡΠ»ΠΎΠ²ΠΈΠ½Ρ ΡΠ»ΠΈΠ²Π°ΡΡ ΡΠ»Π°ΠΊ.
6. Π Π³ΠΎΡΠΎΠ²ΠΎΠΉ ΡΡΠ°Π»ΠΈ ΠΎΡΡΠ°Π΅ΡΡΡ ΠΊΠΈΡΠ»ΠΎΡΠΎΠ΄ Π² Π²ΠΈΠ΄Π΅ ΠΎΠΊΡΠΈΠ΄Π° ΠΆΠ΅Π»Π΅Π·Π°.
ΠΠ»Ρ Π΅Π³ΠΎ Π²ΠΎΡΡΡΠ°Π½ΠΎΠ²Π»Π΅Π½ΠΈΡ Π² ΠΊΠΎΠ²Ρ Π²Π²ΠΎΠ΄ΡΡ ΡΠ°ΡΠΊΠΈΡΠ»ΠΈΡΠ΅Π»ΠΈ. Π§Π°ΡΡΡ ΡΠ°ΡΠΊΠΈΡΠ»ΠΈΡΠ΅Π»Π΅ΠΉ ΠΌΠΎΠΆΠ΅Ρ Π²Π²ΠΎΠ΄ΠΈΡΡΡ Π² ΠΊΠΎΠ½Π²Π΅ΡΡΠΎΡ Π² ΠΊΠΎΠ½ΡΠ΅ ΠΏΠ»Π°Π²ΠΊΠΈ.
ΠΠ°ΠΊΠΎΠ½ΡΠΈΠ² ΡΠ°ΡΠΊΠΈΡΠ»Π΅Π½ΠΈΠ΅, ΠΏΡΠΈΡΡΡΠΏΠ°ΡΡ ΠΊ ΡΠ°Π·Π»ΠΈΠ²ΠΊΠ΅ ΡΡΠ°Π»ΠΈ ΠΏΠΎ ΠΈΠ·Π»ΠΎΠΆΠ½ΠΈΡΠ°ΠΌ. Π’Π΅ΠΌΠΏΠ΅ΡΠ°ΡΡΡΠ° ΡΡΠ°Π»ΠΈ ΠΏΡΠΈ ΡΠ°Π·Π»ΠΈΠ²ΠΊΠ΅ β 1600-1650 ΒΊΠ‘.
ΠΠ»Π°Π²ΠΊΠ° Π² ΠΊΠΎΠ½Π²Π΅ΡΡΠΎΡΠ΅ Π΄Π»ΠΈΡΡΡ 35-40 ΠΌΠΈΠ½ΡΡ, Π° ΡΠΊΠΎΡΠΎΡΡΠ½Π°Ρ ΠΌΠ°ΡΡΠ΅Π½ΠΎΠ²ΡΠΊΠ°Ρ ΠΏΠ»Π°Π²ΠΊΠ° 6-8 ΡΠ°ΡΠΎΠ².
ΠΡΠΈ ΡΠ°Π²Π½ΠΎΠΉ ΠΏΡΠΎΠΈΠ·Π²ΠΎΠ΄ΠΈΡΠ΅Π»ΡΠ½ΠΎΡΡΠΈ ΠΊΠ°ΠΏΠΈΡΠ°Π»ΡΠ½ΡΠ΅ Π·Π°ΡΡΠ°ΡΡ Π½Π° ΡΡΡΠΎΠΈΡΠ΅Π»ΡΡΡΠ²ΠΎ ΠΊΠΈΡΠ»ΠΎΡΠΎΠ΄Π½ΠΎ-ΠΊΠΎΠ½Π²Π΅ΡΡΠΎΡΠ½ΠΎΠ³ΠΎ ΡΠ΅Ρ Π° Π½Π° 25-30% Π½ΠΈΠΆΠ΅, Π° ΡΠ΅Π±Π΅ΡΡΠΎΠΈΠΌΠΎΡΡΡ ΡΡΠ°Π»ΠΈ Π½Π° 5-7% ΠΌΠ΅Π½ΡΡΠ΅, ΡΠ΅ΠΌ ΠΏΡΠΈ ΠΌΠ°ΡΡΠ΅Π½ΠΎΠ²ΡΠΊΠΎΠΌ ΡΠΏΠΎΡΠΎΠ±Π΅.
ΠΡΠΈΠ½ΡΠΈΠΏ ΡΠ°Π±ΠΎΡΡ, ΡΠΈΠΏΡ ΠΈ ΠΏΡΠΈΠΌΠ΅Π½Π΅Π½ΠΈΠ΅
Π Π½Π°ΡΡΠΎΡΡΠ΅Π΅ Π²ΡΠ΅ΠΌΡ Π°Π²ΡΠΎΠΌΠΎΠ±ΠΈΠ»ΡΠ½ΡΠΌΠΈ Π΄Π²ΠΈΠ³Π°ΡΠ΅Π»ΡΠΌΠΈ ΠΌΠΎΠΆΠ½ΠΎ ΡΠΏΡΠ°Π²Π»ΡΡΡ Ρ ΠΏΠΎΠΌΠΎΡΡΡ ΡΠ°Π·Π»ΠΈΡΠ½ΡΡ ΡΠΈΠΏΠΎΠ² Π΄Π°ΡΡΠΈΠΊΠΎΠ². ΠΡΠΈ Π΄Π°ΡΡΠΈΠΊΠΈ ΠΊΠΎΠ½ΡΡΠΎΠ»ΠΈΡΡΡΡ ΠΏΡΠΎΠΈΠ·Π²ΠΎΠ΄ΠΈΡΠ΅Π»ΡΠ½ΠΎΡΡΡ ΠΈ Π²ΡΠ±ΡΠΎΡΡ Π΄Π²ΠΈΠ³Π°ΡΠ΅Π»Ρ. ΠΠΎΠ³Π΄Π° Π΄Π°ΡΡΠΈΠΊ Π½Π΅ ΠΏΡΠ΅Π΄ΠΎΡΡΠ°Π²Π»ΡΠ΅Ρ ΡΠΎΡΠ½ΡΡ Π΄Π°Π½Π½ΡΡ , Π²ΠΎΠ·Π½ΠΈΠΊΠ°Π΅Ρ ΠΌΠ½ΠΎΠΆΠ΅ΡΡΠ²ΠΎ ΠΏΡΠΎΠ±Π»Π΅ΠΌ, ΡΠ°ΠΊΠΈΡ ΠΊΠ°ΠΊ ΡΠΏΡΠ°Π²Π»ΡΠ΅ΠΌΠΎΡΡΡ, ΡΠ²Π΅Π»ΠΈΡΠ΅Π½ΠΈΠ΅ ΡΠ°ΡΡ ΠΎΠ΄Π° ΡΠΎΠΏΠ»ΠΈΠ²Π° ΠΈ ΠΎΡΠΊΠ°Π· ΠΎΡ Π²ΡΠ±ΡΠΎΡΠΎΠ². ΠΠ΄Π½ΠΈΠΌ ΠΈΠ· ΠΎΡΠ½ΠΎΠ²Π½ΡΡ Π΄Π°ΡΡΠΈΠΊΠΎΠ², ΠΈΡΠΏΠΎΠ»ΡΠ·ΡΠ΅ΠΌΡΡ Π² Π°Π²ΡΠΎΠΌΠΎΠ±ΠΈΠ»ΡΡ , ΡΠ²Π»ΡΠ΅ΡΡΡ Π΄Π°ΡΡΠΈΠΊ ΠΊΠΈΡΠ»ΠΎΡΠΎΠ΄Π°, Ρ ΠΈΠΌΠΈΡΠ΅ΡΠΊΠ°Ρ ΡΠΎΡΠΌΡΠ»Π° ΠΊΠΎΡΠΎΡΠΎΠ³ΠΎ β o2. ΠΠ΅ΡΠ²ΡΠΉ ΠΊΠΈΡΠ»ΠΎΡΠΎΠ΄Π½ΡΠΉ Π΄Π°ΡΡΠΈΠΊ Π±ΡΠ» ΠΈΠ·ΠΎΠ±ΡΠ΅ΡΠ΅Π½ Π² 1976 Π³ΠΎΠ΄Ρ Π² Π°Π²ΡΠΎΠΌΠΎΠ±ΠΈΠ»Π΅ Volvo 240.Π 1980 Π³ΠΎΠ΄Ρ Π°Π²ΡΠΎΠΌΠΎΠ±ΠΈΠ»ΠΈ Π² ΠΠ°Π»ΠΈΡΠΎΡΠ½ΠΈΠΈ ΠΈΡΠΏΠΎΠ»ΡΠ·ΠΎΠ²Π°Π»ΠΈ ΡΡΠΈ Π΄Π°ΡΡΠΈΠΊΠΈ Π΄Π»Ρ ΡΠ½ΠΈΠΆΠ΅Π½ΠΈΡ Π²ΡΠ±ΡΠΎΡΠΎΠ².
Π§ΡΠΎ ΡΠ°ΠΊΠΎΠ΅ Π΄Π°ΡΡΠΈΠΊ ΠΊΠΈΡΠ»ΠΎΡΠΎΠ΄Π°?
ΠΠ°ΡΡΠΈΠΊ ΠΊΠΈΡΠ»ΠΎΡΠΎΠ΄Π° β ΡΡΠΎ ΠΎΠ΄ΠΈΠ½ ΠΈΠ· ΡΠΈΠΏΠΎΠ² Π΄Π°ΡΡΠΈΠΊΠΎΠ², ΠΊΠΎΡΠΎΡΡΠΉ ΠΈΡΠΏΠΎΠ»ΡΠ·ΡΠ΅ΡΡΡ Π² Π²ΡΡ Π»ΠΎΠΏΠ½ΠΎΠΉ ΡΠΈΡΡΠ΅ΠΌΠ΅ Π°Π²ΡΠΎΠΌΠΎΠ±ΠΈΠ»Ρ. Π Π°Π·ΠΌΠ΅Ρ ΠΈ ΡΠΎΡΠΌΠ° ΡΡΠΎΠ³ΠΎ Π΄Π°ΡΡΠΈΠΊΠ° ΠΏΠΎΡ ΠΎΠΆΠΈ Π½Π° ΡΠ²Π΅ΡΡ Π·Π°ΠΆΠΈΠ³Π°Π½ΠΈΡ. Π Π·Π°Π²ΠΈΡΠΈΠΌΠΎΡΡΠΈ ΠΎΡ ΡΠ°ΡΠΏΠΎΠ»ΠΎΠΆΠ΅Π½ΠΈΡ ΠΏΠΎ ΠΎΡΠ½ΠΎΡΠ΅Π½ΠΈΡ ΠΊ ΠΊΠ°ΡΠ°Π»ΠΈΡΠΈΡΠ΅ΡΠΊΠΎΠΌΡ Π½Π΅ΠΉΡΡΠ°Π»ΠΈΠ·Π°ΡΠΎΡΡ ΡΡΠΎΡ Π΄Π°ΡΡΠΈΠΊ ΠΌΠΎΠΆΠ΅Ρ Π±ΡΡΡ ΡΠ°ΡΠΏΠΎΠ»ΠΎΠΆΠ΅Π½ Π΄ΠΎ (ΠΏΠ΅ΡΠ΅Π΄) ΠΈΠ»ΠΈ ΠΏΠΎΡΠ»Π΅ (ΠΏΠΎΡΠ»Π΅) ΠΏΡΠ΅ΠΎΠ±ΡΠ°Π·ΠΎΠ²Π°ΡΠ΅Π»Ρ. ΠΠΎΠ»ΡΡΠΈΠ½ΡΡΠ²ΠΎ Π°Π²ΡΠΎΠΌΠΎΠ±ΠΈΠ»Π΅ΠΉ, ΡΠΏΡΠΎΠ΅ΠΊΡΠΈΡΠΎΠ²Π°Π½Π½ΡΡ ΠΏΠΎΡΠ»Π΅ 1990 Π³ΠΎΠ΄Π°, Π²ΠΊΠ»ΡΡΠ°ΡΡ Π΄Π°ΡΡΠΈΠΊΠΈ o2 Π½Π° Π²Ρ ΠΎΠ΄Π΅ ΠΈ Π²ΡΡ ΠΎΠ΄Π΅.
ΠΠ°ΡΡΠΈΠΊΠΈ ΠΊΠΈΡΠ»ΠΎΡΠΎΠ΄Π°, ΠΈΡΠΏΠΎΠ»ΡΠ·ΡΠ΅ΠΌΡΠ΅ Π² Π°Π²ΡΠΎΠΌΠΎΠ±ΠΈΠ»ΡΡ , ΡΠΎΡΡΠΎΡΡ ΠΈΠ· ΠΎΠ΄Π½ΠΎΠ³ΠΎ Π΄Π°ΡΡΠΈΠΊΠ°, ΡΠ°ΡΠΏΠΎΠ»ΠΎΠΆΠ΅Π½Π½ΠΎΠ³ΠΎ ΠΏΠ΅ΡΠ΅Π΄ ΠΊΠ°ΡΠ°Π»ΠΈΡΠΈΡΠ΅ΡΠΊΠΈΠΌ Π½Π΅ΠΉΡΡΠ°Π»ΠΈΠ·Π°ΡΠΎΡΠΎΠΌ, ΠΈ ΠΎΠ΄Π½ΠΎΠ³ΠΎ Π΄Π°ΡΡΠΈΠΊΠ° Π² ΠΊΠ°ΠΆΠ΄ΠΎΠΌ Π²ΡΠΏΡΡΠΊΠ½ΠΎΠΌ ΠΊΠΎΠ»Π»Π΅ΠΊΡΠΎΡΠ΅ Π°Π²ΡΠΎΠΌΠΎΠ±ΠΈΠ»Ρ. ΠΠΎ ΠΌΠ°ΠΊΡΠΈΠΌΠ°Π»ΡΠ½ΠΎΠ΅ ΠΊΠΎΠ»ΠΈΡΠ΅ΡΡΠ²ΠΎ ΡΡΠΈΡ Π΄Π°ΡΡΠΈΠΊΠΎΠ² Π² Π°Π²ΡΠΎΠΌΠΎΠ±ΠΈΠ»Π΅ Π²ΠΎ ΠΌΠ½ΠΎΠ³ΠΎΠΌ Π·Π°Π²ΠΈΡΠΈΡ ΠΎΡ Π΄Π²ΠΈΠ³Π°ΡΠ΅Π»Ρ, ΠΌΠΎΠ΄Π΅Π»ΠΈ, Π³ΠΎΠ΄Π° Π²ΡΠΏΡΡΠΊΠ°. ΠΠΎ Π±ΠΎΠ»ΡΡΠΈΠ½ΡΡΠ²ΠΎ Π°Π²ΡΠΎΠΌΠΎΠ±ΠΈΠ»Π΅ΠΉ ΠΈΠΌΠ΅ΡΡ 4 Π΄Π°ΡΡΠΈΠΊΠ°


ΠΡΠΈΠ½ΡΠΈΠΏ ΡΠ°Π±ΠΎΡΡ
ΠΡΠΈΠ½ΡΠΈΠΏ ΡΠ°Π±ΠΎΡΡ Π΄Π°ΡΡΠΈΠΊΠ° o2 Π·Π°ΠΊΠ»ΡΡΠ°Π΅ΡΡΡ Π² ΠΏΡΠΎΠ²Π΅ΡΠΊΠ΅ ΠΊΠΎΠ»ΠΈΡΠ΅ΡΡΠ²Π° ΠΊΠΈΡΠ»ΠΎΡΠΎΠ΄Π° Π² Π²ΡΡ Π»ΠΎΠΏΠ½ΡΡ Π³Π°Π·Π°Ρ . ΠΠΎ-ΠΏΠ΅ΡΠ²ΡΡ , ΡΡΠΎΡ ΠΊΠΈΡΠ»ΠΎΡΠΎΠ΄ Π±ΡΠ» Π΄ΠΎΠ±Π°Π²Π»Π΅Π½ Π² ΡΠΎΠΏΠ»ΠΈΠ²ΠΎ Π΄Π»Ρ Ρ ΠΎΡΠΎΡΠ΅Π³ΠΎ Π·Π°ΠΆΠΈΠ³Π°Π½ΠΈΡ.Π‘Π²ΡΠ·Ρ Ρ ΡΡΠΈΠΌ Π΄Π°ΡΡΠΈΠΊΠΎΠΌ ΠΌΠΎΠΆΠ΅Ρ ΠΎΡΡΡΠ΅ΡΡΠ²Π»ΡΡΡΡΡ Ρ ΠΏΠΎΠΌΠΎΡΡΡ ΡΠΈΠ³Π½Π°Π»Π° Π½Π°ΠΏΡΡΠΆΠ΅Π½ΠΈΡ. Π’Π°ΠΊΠΈΠΌ ΠΎΠ±ΡΠ°Π·ΠΎΠΌ, ΠΊΠΈΡΠ»ΠΎΡΠΎΠ΄Π½ΡΠΉ ΡΡΠ°ΡΡΡ Π² Π²ΡΡ Π»ΠΎΠΏΠ΅ Π±ΡΠ΄Π΅Ρ ΠΎΠΏΡΠ΅Π΄Π΅Π»ΡΡΡΡΡ ΠΊΠΎΠΌΠΏΡΡΡΠ΅ΡΠΎΠΌ Π°Π²ΡΠΎΠΌΠΎΠ±ΠΈΠ»Ρ.
ΠΠΎΠΌΠΏΡΡΡΠ΅Ρ ΡΠ΅Π³ΡΠ»ΠΈΡΡΠ΅Ρ ΡΠΌΠ΅ΡΡ ΡΠΎΠΏΠ»ΠΈΠ²Π° ΠΈΠ»ΠΈ ΠΊΠΈΡΠ»ΠΎΡΠΎΠ΄Π°, ΠΏΠΎΠ΄Π°Π²Π°Π΅ΠΌΡΡ Π² Π΄Π²ΠΈΠ³Π°ΡΠ΅Π»Ρ Π°Π²ΡΠΎΠΌΠΎΠ±ΠΈΠ»Ρ. Π Π°ΡΠΏΠΎΠ»ΠΎΠΆΠ΅Π½ΠΈΠ΅ Π΄Π°ΡΡΠΈΠΊΠ° Π΄ΠΎ ΠΈ ΠΏΠΎΡΠ»Π΅ ΠΊΠ°ΡΠ°Π»ΠΈΡΠΈΡΠ΅ΡΠΊΠΎΠ³ΠΎ Π½Π΅ΠΉΡΡΠ°Π»ΠΈΠ·Π°ΡΠΎΡΠ° ΠΏΠΎΠ·Π²ΠΎΠ»ΡΠ΅Ρ ΠΏΠΎΠ΄Π΄Π΅ΡΠΆΠΈΠ²Π°ΡΡ Π³ΠΈΠ³ΠΈΠ΅Π½Ρ Π²ΡΡ Π»ΠΎΠΏΠ½ΡΡ Π³Π°Π·ΠΎΠ² ΠΈ ΠΏΡΠΎΠ²Π΅ΡΡΡΡ ΡΡΡΠ΅ΠΊΡΠΈΠ²Π½ΠΎΡΡΡ ΠΏΡΠ΅ΠΎΠ±ΡΠ°Π·ΠΎΠ²Π°ΡΠ΅Π»Ρ.
Π’ΠΈΠΏΡ ΠΊΠΈΡΠ»ΠΎΡΠΎΠ΄Π½ΡΡ Π΄Π°ΡΡΠΈΠΊΠΎΠ²
ΠΠΈΡΠ»ΠΎΡΠΎΠ΄Π½ΡΠ΅ Π΄Π°ΡΡΠΈΠΊΠΈ ΠΏΠΎΠ΄ΡΠ°Π·Π΄Π΅Π»ΡΡΡΡΡ Π½Π° Π΄Π²Π°: Π±ΠΈΠ½Π°ΡΠ½ΡΠ΅ Π²ΡΡ Π»ΠΎΠΏΠ½ΡΠ΅ Π³Π°Π·Ρ ΠΈ ΡΠ½ΠΈΠ²Π΅ΡΡΠ°Π»ΡΠ½ΡΠ΅ Π²ΡΡ Π»ΠΎΠΏΠ½ΡΠ΅ Π³Π°Π·Ρ.
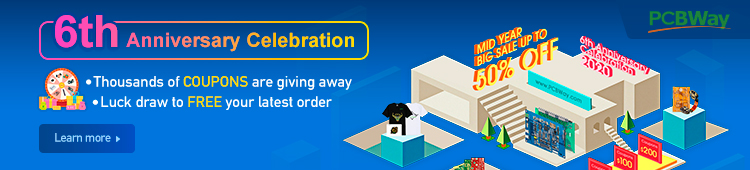
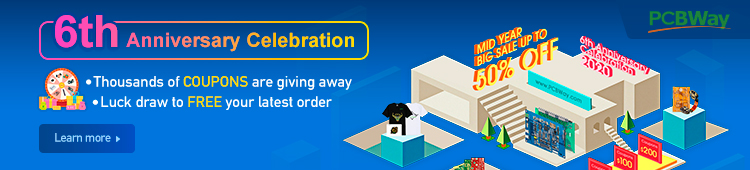
1). ΠΠ²ΠΎΠΈΡΠ½ΡΠΉ Π΄Π°ΡΡΠΈΠΊ ΠΊΠΈΡΠ»ΠΎΡΠΎΠ΄Π° Π² Π²ΡΡ Π»ΠΎΠΏΠ½ΡΡ Π³Π°Π·Π°Ρ
ΠΠ²ΠΎΠΈΡΠ½ΡΠΉ Π΄Π°ΡΡΠΈΠΊ Π²ΡΠ΄Π°Π΅Ρ ΠΈΠ·ΠΌΠ΅Π½Π΅Π½ΠΈΠ΅ ΡΠ»Π΅ΠΊΡΡΠΈΡΠ΅ΡΠΊΠΎΠ³ΠΎ Π½Π°ΠΏΡΡΠΆΠ΅Π½ΠΈΡ ΠΏΡΠΈ ΡΠ΅ΠΌΠΏΠ΅ΡΠ°ΡΡΡΠ΅ 350 Β° C Π² Π·Π°Π²ΠΈΡΠΈΠΌΠΎΡΡΠΈ ΠΎΡ ΡΡΠΎΠ²Π½Ρ ΠΊΠΈΡΠ»ΠΎΡΠΎΠ΄Π° Π² Π²ΡΡ Π»ΠΎΠΏΠ½ΡΡ Π³Π°Π·Π°Ρ . ΠΠ½ ΡΡΠ°Π²Π½ΠΈΠ²Π°Π΅Ρ ΠΎΡΡΠ°ΡΠΎΡΠ½ΠΎΠ΅ ΡΠΎΠ΄Π΅ΡΠΆΠ°Π½ΠΈΠ΅ ΠΊΠΈΡΠ»ΠΎΡΠΎΠ΄Π° Π² Π²ΡΡ Π»ΠΎΠΏΠ½ΡΡ Π³Π°Π·Π°Ρ Ρ ΡΡΠΎΠ²Π½Π΅ΠΌ ΠΊΠΈΡΠ»ΠΎΡΠΎΠ΄Π° Π² ΠΎΠΊΡΡΠΆΠ°ΡΡΠ΅ΠΌ Π²ΠΎΠ·Π΄ΡΡ Π΅ ΠΈ ΡΠ°ΡΠΏΠΎΠ·Π½Π°Π΅Ρ ΠΏΠ΅ΡΠ΅Ρ ΠΎΠ΄ ΠΎΡ Π½Π΅Π΄ΠΎΡΡΠ°ΡΠΊΠ° Π²ΠΎΠ·Π΄ΡΡ Π° ΠΊ ΠΈΠ·Π±ΡΡΠΊΡ Π²ΠΎΠ·Π΄ΡΡ Π° ΠΈ Π½Π°ΠΎΠ±ΠΎΡΠΎΡ.
2). Universal Exhaust Gas
ΠΡΠΎΡ Π΄Π°ΡΡΠΈΠΊ ΠΎΡΠ΅Π½Ρ ΡΠΎΡΠ΅Π½ ΠΏΡΠΈ ΡΠ°ΡΡΠ΅ΡΠ΅ ΡΠΎΠΎΡΠ½ΠΎΡΠ΅Π½ΠΈΠΉ Π½Π΅Π΄ΠΎΡΡΠ°ΡΠΊΠ° ΠΈ ΠΈΠ·Π±ΡΡΠΊΠ° Π²ΠΎΠ·Π΄ΡΡ Π° ΠΈΠ»ΠΈ ΡΠΎΠΏΠ»ΠΈΠ²Π°.ΠΠ½ ΠΈΠΌΠ΅Π΅Ρ Π»ΡΡΡΠΈΠΉ Π΄ΠΈΠ°ΠΏΠ°Π·ΠΎΠ½ ΡΠ°ΡΡΠ΅ΡΠ° ΠΈ ΡΠ°ΠΊΠΆΠ΅ ΠΏΠΎΠ΄Ρ ΠΎΠ΄ΠΈΡ Π΄Π»Ρ ΠΈΡΠΏΠΎΠ»ΡΠ·ΠΎΠ²Π°Π½ΠΈΡ Π² Π±Π΅Π½Π·ΠΈΠ½ΠΎΠ²ΡΡ ΠΈ Π΄ΠΈΠ·Π΅Π»ΡΠ½ΡΡ Π΄Π²ΠΈΠ³Π°ΡΠ΅Π»ΡΡ .
ΠΡΠΈΠ·Π½Π°ΠΊΠΈ Π½Π΅ΠΈΡΠΏΡΠ°Π²Π½ΠΎΡΡΠΈ Π΄Π°ΡΡΠΈΠΊΠ°
ΠΠ΅ΠΈΡΠΏΡΠ°Π²Π½ΡΠΉ Π΄Π°ΡΡΠΈΠΊ ΠΌΠΎΠΆΠ½ΠΎ ΠΎΠΏΡΠ΅Π΄Π΅Π»ΠΈΡΡ ΠΏΠΎ ΡΠ»Π΅Π΄ΡΡΡΠΈΠΌ ΠΏΡΠΈΠ·Π½Π°ΠΊΠ°ΠΌ.
- ΠΠΎΠ»ΠΎΠΌΠΊΠ° Π΄Π»Ρ ΠΏΡΠ΅Π²ΡΡΠ΅Π½ΠΈΡ Π°Π½Π°Π»ΠΈΠ·Π° Π²ΡΠ±ΡΠΎΡΠΎΠ²
- Π Π°ΡΡ ΠΎΠ΄ ΡΠΎΠΏΠ»ΠΈΠ²Π° ΠΌΠΎΠΆΠ΅Ρ Π±ΡΡΡ ΡΠΌΠ΅Π½ΡΡΠ΅Π½.
- ΠΠ°ΠΌΠΏΠ° Π΄Π²ΠΈΠ³Π°ΡΠ΅Π»Ρ Π½Π΅ Π³ΠΎΡΠΈΡ.
- ΠΠ»ΠΎΡ Π°Ρ ΡΠ°Π±ΠΎΡΠ°, Π³Π»ΠΎΡ Π½Π΅Ρ ΠΈ Π³ΡΡΠ±ΡΠΉ Ρ ΠΎΠ»ΠΎΡΡΠΎΠΉ Ρ ΠΎΠ΄.
- Π‘ΡΠ΅Π΄ΡΡΠ²ΠΎ ΠΏΡΠΎΠ²Π΅ΡΠΊΠΈ ΠΊΠΎΠ΄Π°, ΡΠ°ΡΠΏΠΎΠ·Π½Π°ΡΡΠ΅Π΅ ΡΠ±ΠΎΠΉ Π΄Π°ΡΡΠΈΠΊΠ°
ΠΡΠΈΠ»ΠΎΠΆΠ΅Π½ΠΈΡ
Π‘ΡΠ΅ΡΡ ΠΏΡΠΈΠΌΠ΅Π½Π΅Π½ΠΈΡ ΠΊΠΈΡΠ»ΠΎΡΠΎΠ΄Π½ΡΡ Π΄Π°ΡΡΠΈΠΊΠΎΠ² Π²ΠΊΠ»ΡΡΠ°ΡΡ ΡΡΠ΄ΠΎΠ²ΠΎΠ΅ Π΄ΡΡ Π°Π½ΠΈΠ΅, ΠΌΠΎΠ½ΠΈΡΠΎΡΠΈΠ½Π³ Π±ΡΡΡΡΠΎΠΉ ΡΠ΅Π°ΠΊΡΠΈΠΈ, Π»Π°Π±ΠΎΡΠ°ΡΠΎΡΠ½ΡΠ΅ ΠΈΡΡΠ»Π΅Π΄ΠΎΠ²Π°Π½ΠΈΡ ΠΈ ΡΠ°Π·ΡΠ°Π±ΠΎΡΠΊΠΈ, ΠΌΠΎΠ½ΠΈΡΠΎΡΠΈΠ½Π³ ΡΠΎΠΏΠ»ΠΈΠ²Π½ΠΎΠ³ΠΎ Π±Π°ΠΊΠ°, ΠΎΡΠΎΠ±ΡΠ΅ ΡΠ³Π»Π΅Π²ΠΎΠ΄ΠΎΡΠΎΠ΄Π½ΡΠ΅ ΡΡΠ΅Π΄Ρ, Π΄ΠΎΠ»Π³ΠΎΡΡΠΎΡΠ½ΡΠΉ ΠΌΠΎΠ½ΠΈΡΠΎΡΠΈΠ½Π³ ΠΏΡΠΎΡΠ΅Π΄ΡΡ, ΡΠ΅ΡΠΌΠ΅Π½ΡΠ°ΡΠΈΡ, ΡΠΏΠ°ΠΊΠΎΠ²ΠΊΡ ΠΏΠΈΡΠ΅Π²ΡΡ ΠΏΡΠΎΠ΄ΡΠΊΡΠΎΠ² ΠΈ Π£ΠΏΠ°ΠΊΠΎΠ²ΠΊΠ° Π΄Π»Ρ Π½Π°ΠΏΠΈΡΠΊΠΎΠ², ΡΠ°ΡΠΌΠ°ΡΠ΅Π²ΡΠΈΠΊΠ° ΠΈ ΠΌΠ΅Π΄ΠΈΡΠΈΠ½Π° ΠΈ Ρ. Π.
ΠΡΠ°ΠΊ, ΡΡΠΎ Π²ΡΠ΅ ΠΎΠ± ΠΎΠ±Π·ΠΎΡΠ΅ ΠΊΠΈΡΠ»ΠΎΡΠΎΠ΄Π½ΠΎΠ³ΠΎ Π΄Π°ΡΡΠΈΠΊΠ°. ΠΡΠΈ Π΄Π°ΡΡΠΈΠΊΠΈ Π΄ΠΎΡΡΡΠΏΠ½Ρ Π² Π΄Π²ΡΡ Π²Π°ΡΠΈΠ°Π½ΡΠ°Ρ : Π΄Π°ΡΡΠΈΠΊ ΠΈΠΌΠ±ΠΈΡΠ½ΠΎΠ³ΠΎ ΡΠΈΠΏΠ° ΠΈ ΠΏΠ»Π°Π½Π°ΡΠ½ΡΠΉ Π΄Π°ΡΡΠΈΠΊ. ΠΠΎΡ Π²Π°ΠΌ Π²ΠΎΠΏΡΠΎΡ, Π² ΡΠ΅ΠΌ ΠΏΡΠ΅ΠΈΠΌΡΡΠ΅ΡΡΠ²Π° ΠΊΠΈΡΠ»ΠΎΡΠΎΠ΄Π½ΠΎΠ³ΠΎ Π΄Π°ΡΡΠΈΠΊΠ°?
.ΠΠ°ΠΊ ΡΠ°Π±ΠΎΡΠ°Π΅Ρ ΠΊΠΈΡΠ»ΠΎΡΠΎΠ΄Π½ΡΠΉ ΠΊΠΎΠ½ΡΠ΅Π½ΡΡΠ°ΡΠΎΡ?
ΠΡΠΎΡΠ΅ Π³ΠΎΠ²ΠΎΡΡ, ΠΊΠΎΠ½ΡΠ΅Π½ΡΡΠ°ΡΠΎΡ ΠΊΠΈΡΠ»ΠΎΡΠΎΠ΄Π° ΡΠ°Π±ΠΎΡΠ°Π΅Ρ Π½Π° ΡΠ»Π΅ΠΊΡΡΠΈΡΠ΅ΡΡΠ²Π΅; Π·Π°Π±ΠΈΡΠ°Π΅Ρ Π²ΠΎΠ·Π΄ΡΡ ΠΏΠΎΠΌΠ΅ΡΠ΅Π½ΠΈΡ, ΡΠ΄Π°Π»ΡΠ΅Ρ ΠΈΠ· Π½Π΅Π³ΠΎ Π°Π·ΠΎΡ ΠΈ ΠΎΠ±Π΅ΡΠΏΠ΅ΡΠΈΠ²Π°Π΅Ρ Π΄ΠΎ 95% ΡΠΈΡΡΠΎΠ³ΠΎ ΠΊΠΈΡΠ»ΠΎΡΠΎΠ΄Π°.

ΠΡΠΈΠ½ΡΠΈΠΏ
Π‘ΠΎΡΡΠ°Π² Π²ΠΎΠ·Π΄ΡΡ Π° (78% Π°Π·ΠΎΡΠ°, 21% ΠΊΠΈΡΠ»ΠΎΡΠΎΠ΄Π° ΠΈ 1% Π΄ΡΡΠ³ΠΈΡ Π³Π°Π·ΠΎΠ², ΡΠ°ΠΊΠΈΡ ΠΊΠ°ΠΊ Π΄Π²ΡΠΎΠΊΠΈΡΡ ΡΠ³Π»Π΅ΡΠΎΠ΄Π°, Π°ΡΠ³ΠΎΠ½ ΠΈ Ρ. Π.) Π―ΡΠ½ΠΎ ΠΏΠΎΠΊΠ°Π·ΡΠ²Π°Π΅Ρ, ΡΡΠΎ Π²ΠΎΠ·Π΄ΡΡ Π² ΠΎΡΠ½ΠΎΠ²Π½ΠΎΠΌ ΡΠΎΡΡΠΎΠΈΡ ΠΈΠ· Π΄Π²ΡΡ Π³Π°Π·ΠΎΠ²: Π°Π·ΠΎΡΠ° ΠΈ ΠΊΠΈΡΠ»ΠΎΡΠΎΠ΄Π° [Π²ΠΌΠ΅ΡΡΠ΅ 99%]. ΠΡΠ»ΠΈ ΠΈΠ· Π²ΠΎΠ·Π΄ΡΡ Π° ΡΠ΄Π°Π»ΠΈΡΡ Π°Π·ΠΎΡ, ΠΎΡΡΠ°Π²ΡΠΈΠΌΡΡ ΠΏΠ΅ΡΠ²ΠΈΡΠ½ΡΠΌ Π³Π°Π·ΠΎΠΌ Π±ΡΠ΄Π΅Ρ ΠΊΠΈΡΠ»ΠΎΡΠΎΠ΄ Ρ ΡΠΈΡΡΠΎΡΠΎΠΉ ΠΎΠΊΠΎΠ»ΠΎ 90-95%.ΠΠΎΠ½ΡΠ΅Π½ΡΡΠ°ΡΠΎΡ ΠΊΠΈΡΠ»ΠΎΡΠΎΠ΄Π° ΠΈΡΠΏΠΎΠ»ΡΠ·ΡΠ΅Ρ ΡΡΡ ΠΈΠ΄Π΅Ρ Ρ ΠΎΡΠ½ΠΎΠ²Π½ΡΠΌ ΠΏΡΠΈΠ½ΡΠΈΠΏΠΎΠΌ Π°Π΄ΡΠΎΡΠ±ΡΠΈΠΈ ΠΏΡΠΈ ΠΏΠ΅ΡΠ΅ΠΌΠ΅Π½Π½ΠΎΠΌ Π΄Π°Π²Π»Π΅Π½ΠΈΠΈ (PSA) Π΄Π»Ρ Π΄ΠΎΡΡΠ°Π²ΠΊΠΈ ΠΊΠΈΡΠ»ΠΎΡΠΎΠ΄Π° Ρ ΡΠΈΡΡΠΎΡΠΎΠΉ 90-95%.

ΠΡΠ½ΠΎΠ²Π½ΡΠ΅ ΠΊΠΎΠΌΠΏΠΎΠ½Π΅Π½ΡΡ
- Π‘Π΅ΡΠΈΡ ΡΠΈΠ»ΡΡΡΠΎΠ²: ΠΠ»Ρ ΡΠΈΠ»ΡΡΡΠ°ΡΠΈΠΈ Π·Π°Π³ΡΡΠ·Π½Π΅Π½ΠΈΠΉ, ΠΏΡΠΈΡΡΡΡΡΠ²ΡΡΡΠΈΡ Π² Π²ΠΎΠ·Π΄ΡΡ Π΅
- ΠΠΎΠ·Π΄ΡΡΠ½ΡΠΉ ΠΊΠΎΠΌΠΏΡΠ΅ΡΡΠΎΡ: ΠΠ»Ρ Π½Π°Π³Π½Π΅ΡΠ°Π½ΠΈΡ Π²ΠΎΠ·Π΄ΡΡ Π° ΠΈΠ· ΠΏΠΎΠΌΠ΅ΡΠ΅Π½ΠΈΡ Π² ΠΌΠ°ΡΠΈΠ½Ρ ΠΈ ΠΏΠΎΠ΄Π°ΡΠΈ Π΅Π³ΠΎ ΠΊ ΡΠ»ΠΎΡΠΌ ΠΌΠΎΠ»Π΅ΠΊΡΠ»ΡΡΠ½ΡΡ ΡΠΈΡ.
- 2 ΡΠ»ΠΎΡ ΠΌΠΎΠ»Π΅ΠΊΡΠ»ΡΡΠ½ΡΡ ΡΠΈΡ β Π¦Π΅ΠΎΠ»ΠΈΡ (ΠΌΠΈΠΊΡΠΎΠΏΠΎΡΠΈΡΡΡΠΉ Π°Π»ΡΠΌΠΎΡΠΈΠ»ΠΈΠΊΠ°ΡΠ½ΡΠΉ ΠΌΠΈΠ½Π΅ΡΠ°Π»): ΠΎΠ±Π»Π°Π΄Π°Π΅Ρ ΡΠΏΠΎΡΠΎΠ±Π½ΠΎΡΡΡΡ ΡΠ»Π°Π²Π»ΠΈΠ²Π°ΡΡ Π°Π·ΠΎΡ.
- ΠΠ΅ΡΠ΅ΠΊΠ»ΡΡΠ°ΡΡΠΈΠΉ ΠΊΠ»Π°ΠΏΠ°Π½: ΠΠ΅ΡΠ΅ΠΊΠ»ΡΡΠ°Π΅Ρ ΠΌΠΎΡΠ½ΠΎΡΡΡ ΠΊΠΎΠΌΠΏΡΠ΅ΡΡΠΎΡΠ° ΠΌΠ΅ΠΆΠ΄Ρ Π΄Π²ΡΠΌΡ ΡΠ»ΠΎΡΠΌΠΈ ΠΌΠΎΠ»Π΅ΠΊΡΠ»ΡΡΠ½ΡΡ ΡΠΈΡ
- ΠΡΡ ΠΎΠ΄ ΠΊΠΈΡΠ»ΠΎΡΠΎΠ΄Π°: ΠΡΠ²Π΅ΡΡΡΠΈΠ΅, ΡΠ΅ΡΠ΅Π· ΠΊΠΎΡΠΎΡΠΎΠ΅ ΠΏΠ°ΡΠΈΠ΅Π½ΡΡ ΠΏΠΎΡΡΡΠΏΠ°Π΅Ρ ΠΊΠΈΡΠ»ΠΎΡΠΎΠ΄
- Π Π°ΡΡ ΠΎΠ΄ΠΎΠΌΠ΅Ρ: ΠΠ»Ρ ΡΡΡΠ°Π½ΠΎΠ²ΠΊΠΈ ΡΠ°ΡΡ ΠΎΠ΄Π° Π² Π»ΠΈΡΡΠ°Ρ Π² ΠΌΠΈΠ½ΡΡΡ (Π» / ΠΌΠΈΠ½)

ΡΠ°Π±ΠΎΡΠ°Ρ
- ΠΠΊΡΡΠΆΠ°ΡΡΠΈΠΉ Π²ΠΎΠ·Π΄ΡΡ (Π²ΠΎΠ·Π΄ΡΡ ΠΏΠΎΠΌΠ΅ΡΠ΅Π½ΠΈΡ), ΠΏΡΠΎΡ ΠΎΠ΄ΡΡΠΈΠΉ ΡΠ΅ΡΠ΅Π· ΡΠ΅ΡΠΈΡ ΡΠΈΠ»ΡΡΡΠΎΠ², Π²ΡΠ°ΡΡΠ²Π°Π΅ΡΡΡ Π² ΠΌΠ°ΡΠΈΠ½Ρ ΠΊΠΎΠΌΠΏΡΠ΅ΡΡΠΎΡΠΎΠΌ.
- ΠΡΠΎΡ Π²ΠΎΠ·Π΄ΡΡ
ΡΠΆΠΈΠΌΠ°Π΅ΡΡΡ Π² ΠΏΠ΅ΡΠ²ΠΎΠΌ ΡΠ»ΠΎΠ΅ ΠΌΠΎΠ»Π΅ΠΊΡΠ»ΡΡΠ½ΠΎΠ³ΠΎ ΡΠΈΡΠ°, ΠΈ Π²Π΅ΡΡ Π°Π·ΠΎΡ Π°Π΄ΡΠΎΡΠ±ΠΈΡΡΠ΅ΡΡΡ . Π‘Π»ΠΎΠΈ ΠΌΠΎΠ»Π΅ΠΊΡΠ»ΡΡΠ½ΡΡ
ΡΠΈΡ ΠΏΠΎΡΠΈΡΡΡΠ΅ ΠΈ, ΡΠ»Π΅Π΄ΠΎΠ²Π°ΡΠ΅Π»ΡΠ½ΠΎ, ΠΈΠΌΠ΅ΡΡ Π±ΠΎΠ»ΡΡΡΡ ΠΏΠ»ΠΎΡΠ°Π΄Ρ ΠΏΠΎΠ²Π΅ΡΡ
Π½ΠΎΡΡΠΈ, Π±Π»Π°Π³ΠΎΠ΄Π°ΡΡ ΠΊΠΎΡΠΎΡΠΎΠΉ ΠΎΠ½ΠΈ Π°Π΄ΡΠΎΡΠ±ΠΈΡΡΡΡ Π±ΠΎΠ»ΡΡΠΎΠ΅ ΠΊΠΎΠ»ΠΈΡΠ΅ΡΡΠ²ΠΎ Π°Π·ΠΎΡΠ°.
- Π’Π΅ΠΏΠ΅ΡΡ, ΠΏΠΎΡΠΎΠΌΡ ΡΡΠΎ Π²ΠΎΠ·Π΄ΡΡ ΡΠΎΠ΄Π΅ΡΠΆΠΈΡ ΡΠΎΠ»ΡΠΊΠΎ Π°Π·ΠΎΡ ΠΈ ΠΊΠΈΡΠ»ΠΎΡΠΎΠ΄ Π² ΠΊΠ°ΡΠ΅ΡΡΠ²Π΅ ΠΎΡΠ½ΠΎΠ²Π½ΡΡ ΠΊΠΎΠΌΠΏΠΎΠ½Π΅Π½ΡΠΎΠ²; ΠΎΡΠ½ΠΎΠ²Π½ΠΎΠΉ ΠΎΡΡΠ°ΡΡΠΈΠΉΡΡ Π³Π°Π· β ΡΡΠΎ ΠΊΠΈΡΠ»ΠΎΡΠΎΠ΄ . ΠΡΠΎΡ ΠΊΠΈΡΠ»ΠΎΡΠΎΠ΄ ΠΈΠΌΠ΅Π΅Ρ ΠΊΠΎΠ½ΡΠ΅Π½ΡΡΠ°ΡΠΈΡ Π΄ΠΎ 95% ΠΈ Π³ΠΎΡΠΎΠ² ΠΊ ΠΏΠΎΠ΄Π°ΡΠ΅ ΠΏΠ°ΡΠΈΠ΅Π½ΡΡ ΡΠ΅ΡΠ΅Π· ΡΠΈΡΡΠ΅ΠΌΡ Π΄ΠΎΡΡΠ°Π²ΠΊΠΈ ΠΊΠΈΡΠ»ΠΎΡΠΎΠ΄Π°, ΡΠ°ΠΊΡΡ ββΠΊΠ°ΠΊ Π½Π°Π·Π°Π»ΡΠ½Π°Ρ ΠΊΠ°Π½ΡΠ»Ρ, ΠΊΠΈΡΠ»ΠΎΡΠΎΠ΄Π½Π°Ρ ΠΌΠ°ΡΠΊΠ° ΠΈ Ρ. Π.
- ΠΠΎΠΌΠΏΡΠ΅ΡΡΠΎΡ ΠΏΡΠΎΠ΄ΠΎΠ»ΠΆΠ°Π΅Ρ ΡΠΆΠΈΠΌΠ°ΡΡ Π²ΠΎΠ·Π΄ΡΡ
Π² ΡΠ»ΠΎΠΉ 1-Π³ΠΎ ΠΌΠΎΠ»Π΅ΠΊΡΠ»ΡΡΠ½ΠΎΠ³ΠΎ ΡΠΈΡΠ°, ΠΏΠΎΠΊΠ° ΠΎΠ½ Π½Π΅ Π±ΡΠ΄Π΅Ρ Π½Π°ΡΡΡΠ΅Π½ (Π·Π°ΠΏΠΎΠ»Π½Π΅Π½) Π°Π·ΠΎΡΠΎΠΌ . Π‘Π»ΠΎΠΉ ΡΠΈΡΠ° ΠΎΠ±ΡΡΠ½ΠΎ Π½Π°ΡΡΡΠ°Π΅ΡΡΡ ΠΏΡΠΈ Π΄Π°Π²Π»Π΅Π½ΠΈΠΈ 20 ΡΡΠ½ΡΠΎΠ² Π½Π° ΠΊΠ²Π°Π΄ΡΠ°ΡΠ½ΡΠΉ Π΄ΡΠΉΠΌ.
- ΠΠ΅ΠΏΠΎΡΡΠ΅Π΄ΡΡΠ²Π΅Π½Π½ΠΎ ΠΏΠ΅ΡΠ΅Π΄ ΡΠ΅ΠΌ, ΠΊΠ°ΠΊ 1-ΠΉ ΡΠ»ΠΎΠΉ ΠΌΠΎΠ»Π΅ΠΊΡΠ»ΡΡΠ½ΠΎΠ³ΠΎ ΡΠΈΡΠ° ΡΡΠ°Π½Π΅Ρ Π½Π°ΡΡΡΠ΅Π½Π½ΡΠΌ , Π²ΠΊΠ»ΡΡΠ°Π΅ΡΡΡ ΠΏΠ΅ΡΠ΅ΠΊΠ»ΡΡΠ°ΡΡΠΈΠΉ ΠΊΠ»Π°ΠΏΠ°Π½ , ΠΈ ΠΌΠΎΡΠ½ΠΎΡΡΡ Π²ΠΎΠ·Π΄ΡΡΠ½ΠΎΠ³ΠΎ ΠΊΠΎΠΌΠΏΡΠ΅ΡΡΠΎΡΠ° Π½Π΅ΠΌΠ΅Π΄Π»Π΅Π½Π½ΠΎ ΠΏΠ΅ΡΠ΅ΠΊΠ»ΡΡΠ°Π΅ΡΡΡ Π½Π° 2-ΠΉ ΡΠ»ΠΎΠΉ ΡΠΈΡΠ° i.Π΅. ΠΊΠΎΠΌΠΏΡΠ΅ΡΡΠΎΡ Π½Π°ΡΠΈΠ½Π°Π΅Ρ ΡΠΆΠ°ΡΠΈΠ΅ Π²ΠΎΠ·Π΄ΡΡ
Π° Π΄ΠΎ 2-Π³ΠΎ ΠΌΠΎΠ»Π΅ΠΊΡΠ»ΡΡΠ½ΠΎΠ³ΠΎ ΡΠΈΡΠ° .
- ΠΠΎΠΊΠ° ΡΡΠΎΡ ΡΠ»ΠΎΠΉ ΡΠΈΡΠ° Π½Π°ΡΡΡΠ°Π΅ΡΡΡ Π°Π·ΠΎΡΠΎΠΌ, ΠΠ·ΠΎΡ, ΠΊΠΎΡΠΎΡΡΠΉ Π±ΡΠ» Π·Π°Ρ Π²Π°ΡΠ΅Π½ Π² ΠΏΠ΅ΡΠ²ΠΎΠΌ ΡΠ»ΠΎΠ΅ ΡΠΈΡΠ°, Π²ΡΠΏΡΡΠΊΠ°Π΅ΡΡΡ Π½Π°ΡΡΠΆΡ . ΠΠ΅Π±ΠΎΠ»ΡΡΠΎΠ΅ ΠΊΠΎΠ»ΠΈΡΠ΅ΡΡΠ²ΠΎ Π°Π·ΠΎΡΠ°, ΠΊΠΎΡΠΎΡΠΎΠ΅ ΠΎΡΡΠ°Π΅ΡΡΡ Π² ΡΠ»ΠΎΠ΅ ΡΠΈΡΠ° ΠΏΠΎΡΠ»Π΅ ΡΠ°Π·Π³ΡΡΠ·ΠΊΠΈ, ΡΠ΄Π°Π»ΡΠ΅ΡΡΡ ΠΎΠ±ΡΠ°ΡΠ½ΠΎΠΉ ΠΏΡΠΎΠΌΡΠ²ΠΊΠΎΠΉ ΠΊΠΈΡΠ»ΠΎΡΠΎΠ΄Π° ΠΈΠ· Π΄ΡΡΠ³ΠΎΠ³ΠΎ ΡΠ»ΠΎΡ ΡΠΈΡΠ°.
- ΠΠ΅ΡΠ΅ΠΊΠ»ΡΡΠ°ΡΡΠΈΠΉ ΠΊΠ»Π°ΠΏΠ°Π½ ΡΠ½ΠΎΠ²Π° ΠΏΠ΅ΡΠ΅ΠΊΠ»ΡΡΠ°Π΅Ρ Π²ΡΡ
ΠΎΠ΄ Π²ΠΎΠ·Π΄ΡΡΠ½ΠΎΠ³ΠΎ ΠΊΠΎΠΌΠΏΡΠ΅ΡΡΠΎΡΠ° ΠΎΠ±ΡΠ°ΡΠ½ΠΎ Π½Π° 1-ΠΉ ΡΠ»ΠΎΠΉ ΡΠΈΡΠ°, ΠΊΠ°ΠΊ ΡΠΎΠ»ΡΠΊΠΎ 2-ΠΉ ΡΠ»ΠΎΠΉ ΡΠΈΡΠ° ΠΏΡΠΈΠ±Π»ΠΈΠΆΠ°Π΅ΡΡΡ ΠΊ Π½Π°ΡΡΡΠ΅Π½ΠΈΡ .
- ΠΡΠΎΡ ΠΏΡΠΎΡΠ΅ΡΡ ΠΏΠΎΠ²ΡΠΎΡΡΠ΅ΡΡΡ, ΡΡΠΎΠ±Ρ ΠΎΠ±Π΅ΡΠΏΠ΅ΡΠΈΡΡ Π½Π΅ΠΏΡΠ΅ΡΡΠ²Π½ΡΠΉ ΠΏΠΎΡΠΎΠΊ ΠΊΠΈΡΠ»ΠΎΡΠΎΠ΄Π° .
- ΠΡΠΎΡ ΠΏΡΠΎΡΠ΅ΡΡ ΠΏΠ΅ΡΠ΅ΠΊΠ»ΡΡΠ΅Π½ΠΈΡ ΡΠ»ΠΎΠ΅Π² ΡΠΈΡΠ° ΠΈΠ·Π²Π΅ΡΡΠ΅Π½ ΠΊΠ°ΠΊ ΠΠ΄ΡΠΎΡΠ±ΡΠΈΡ ΠΏΡΠΈ ΠΏΠ΅ΡΠ΅ΠΌΠ΅Π½Π½ΠΎΠΌ Π΄Π°Π²Π»Π΅Π½ΠΈΠΈ (PSA) .
- ΠΡΡ ΠΎΠ΄ ΠΊΠΈΡΠ»ΠΎΡΠΎΠ΄Π° Π·Π°ΡΠ΅ΠΌ ΠΊΠΎΠ½ΡΡΠΎΠ»ΠΈΡΡΠ΅ΡΡΡ Ρ ΠΏΠΎΠΌΠΎΡΡΡ ΡΠ°ΡΡ ΠΎΠ΄ΠΎΠΌΠ΅ΡΠ° , Π³Π΄Π΅ ΡΠ°ΡΡ ΠΎΠ΄ ΠΌΠΎΠΆΠ΅Ρ Π±ΡΡΡ ΡΡΡΠ°Π½ΠΎΠ²Π»Π΅Π½ Π²ΡΡΡΠ½ΡΡ Π² Π»ΠΈΡΡΠ°Ρ Π² ΠΌΠΈΠ½ΡΡΡ (Π» / ΠΌΠΈΠ½).
- ΠΠΈΡΠ»ΠΎΡΠΎΠ΄ Π²ΡΡ ΠΎΠ΄ΠΈΡ ΡΠ΅ΡΠ΅Π· Π²ΡΠΏΡΡΠΊΠ½ΠΎΠ΅ ΠΎΡΠ²Π΅ΡΡΡΠΈΠ΅, ΠΊ ΠΊΠΎΡΠΎΡΠΎΠΌΡ ΠΎΠ±ΡΡΠ½ΠΎ ΠΏΠΎΠ΄ΠΊΠ»ΡΡΠ°Π΅ΡΡΡ ΡΠΈΡΡΠ΅ΠΌΠ° Π΄ΠΎΡΡΠ°Π²ΠΊΠΈ ΠΊΠΈΡΠ»ΠΎΡΠΎΠ΄Π°, ΡΠ°ΠΊΠ°Ρ ΠΊΠ°ΠΊ Π½Π°Π·Π°Π»ΡΠ½Π°Ρ ΠΊΠ°Π½ΡΠ»Ρ ΠΈΠ»ΠΈ ΠΌΠ°ΡΠΊΠ° , ΡΠ΅ΡΠ΅Π· ΡΠ²Π»Π°ΠΆΠ½ΠΈΡΠ΅Π»Ρ.
,Π‘Π²ΠΎΠ΄ΠΊΠ°
- ΠΡΠΈΠ½ΡΠΈΠΏ: ΠΠ΄ΡΠΎΡΠ±ΡΠΈΡ ΠΏΡΠΈ ΠΏΠ΅ΡΠ΅ΠΌΠ΅Π½Π½ΠΎΠΌ Π΄Π°Π²Π»Π΅Π½ΠΈΠΈ
- Air ΡΠΎΠ΄Π΅ΡΠΆΠΈΡ 78% Π°Π·ΠΎΡΠ° ΠΈ 21% ΠΊΠΈΡΠ»ΠΎΡΠΎΠ΄Π°.
- ΠΡΠ»ΠΈ ΡΠ΄Π°Π»ΠΈΡΡ Π°Π·ΠΎΡ, Π² Π²ΠΎΠ·Π΄ΡΡ Π΅ ΠΎΡΡΠ°Π½Π΅ΡΡΡ ΠΊΠΈΡΠ»ΠΎΡΠΎΠ΄ Π΄ΠΎ 95% ΡΠΈΡΡΠΎΡΡ.
- ΠΠΎΠ·Π΄ΡΡ Π² ΠΏΠΎΠΌΠ΅ΡΠ΅Π½ΠΈΠΈ Π²ΡΠ°ΡΡΠ²Π°Π΅ΡΡΡ Π² ΠΌΠ°ΡΠΈΠ½Ρ ΡΠ΅ΡΠ΅Π· ΠΊΠΎΠΌΠΏΡΠ΅ΡΡΠΎΡ
- Π ΠΌΠ°ΡΠΈΠ½Π΅ 2 ΠΌΠΎΠ»Π΅ΠΊΡΠ»ΡΡΠ½ΡΡ ΡΠΈΡΠ°, ΠΊΠΎΡΠΎΡΡΠ΅ ΡΠ°Π±ΠΎΡΠ°ΡΡ ΠΏΠΎΠΏΠ΅ΡΠ΅ΠΌΠ΅Π½Π½ΠΎ.
- Π‘Π»ΠΎΠΈ ΠΌΠΎΠ»Π΅ΠΊΡΠ»ΡΡΠ½ΡΡ ΡΠΈΡ ΡΠ»Π°Π²Π»ΠΈΠ²Π°ΡΡ ΠΈ ΡΠ΄Π°Π»ΡΡΡ Π°Π·ΠΎΡ ΠΈΠ· Π²ΠΎΠ·Π΄ΡΡ Π°, ΠΊΠΎΡΠΎΡΡΠΉ Π²ΡΡΠ³ΠΈΠ²Π°Π΅ΡΡΡ Π² ΠΌΠ°ΡΠΈΠ½Ρ.
- ΠΠ΅ΡΠ΅ΠΊΠ»ΡΡΠ°ΡΡΠΈΠΉ ΠΊΠ»Π°ΠΏΠ°Π½ ΠΏΡΠΎΠ΄ΠΎΠ»ΠΆΠ°Π΅Ρ ΠΏΠ΅ΡΠ΅ΠΊΠ»ΡΡΠ°ΡΡ ΠΏΠΎΠ΄Π°ΡΡ Π²ΠΎΠ·Π΄ΡΡ Π° Ρ ΠΎΠ΄Π½ΠΎΠ³ΠΎ ΡΠ»ΠΎΡ ΡΠΈΡΠ° Π½Π° Π΄ΡΡΠ³ΠΎΠΉ, ΠΎΠ±Π΅ΡΠΏΠ΅ΡΠΈΠ²Π°Ρ Π½Π΅ΠΏΡΠ΅ΡΡΠ²Π½ΡΠΉ ΠΏΠΎΡΠΎΠΊ ΠΊΠΈΡΠ»ΠΎΡΠΎΠ΄Π°.
- ΠΠ·ΠΎΡ Π²ΡΠΏΡΡΠΊΠ°Π΅ΡΡΡ ΠΈΠ· ΠΊΠ°ΠΆΠ΄ΠΎΠ³ΠΎ ΡΠ»ΠΎΡ ΡΠΈΡΠ°, ΠΊΠΎΠ³Π΄Π° ΡΠ»ΠΎΠΉ Π½Π°ΡΡΡΠ°Π΅ΡΡΡ.
- ΠΡΡ ΠΎΠ΄ ΠΊΠΈΡΠ»ΠΎΡΠΎΠ΄Π° ΠΊΠΎΠ½ΡΡΠΎΠ»ΠΈΡΡΠ΅ΡΡΡ ΡΠ°ΡΡ ΠΎΠ΄ΠΎΠΌΠ΅ΡΠΎΠΌ ΠΈ Π΄ΠΎΡΡΠ°Π²Π»ΡΠ΅ΡΡΡ ΠΏΠ°ΡΠΈΠ΅Π½ΡΡ ΡΠ΅ΡΠ΅Π· ΡΠΈΡΡΠ΅ΠΌΡ Π΄ΠΎΡΡΠ°Π²ΠΊΠΈ ΠΊΠΈΡΠ»ΠΎΡΠΎΠ΄Π°, ΡΠ°ΠΊΡΡ ββΠΊΠ°ΠΊ Π½Π°Π·Π°Π»ΡΠ½Π°Ρ ΠΊΠ°Π½ΡΠ»Ρ ΠΈΠ»ΠΈ ΠΌΠ°ΡΠΊΠ°.
ΠΠ°ΠΊ ΠΈΡΠΏΠΎΠ»ΡΠ·ΠΎΠ²Π°ΡΡ ΠΈ ΠΎΠ±ΡΠ»ΡΠΆΠΈΠ²Π°ΡΡ ΠΊΠΎΠ½ΡΠ΅Π½ΡΡΠ°ΡΠΎΡ ΠΊΠΈΡΠ»ΠΎΡΠΎΠ΄Π°?
ΠΠ°ΠΆΠ΄ΠΎΠΉ ΠΌΠ°ΡΠΈΠ½Π΅ Π½Π΅ΠΎΠ±Ρ ΠΎΠ΄ΠΈΠΌΠΎ ΡΠ΅Ρ Π½ΠΈΡΠ΅ΡΠΊΠΎΠ΅ ΠΎΠ±ΡΠ»ΡΠΆΠΈΠ²Π°Π½ΠΈΠ΅, ΠΈ ΠΊΠΎΠ½ΡΠ΅Π½ΡΡΠ°ΡΠΎΡ ΠΊΠΈΡΠ»ΠΎΡΠΎΠ΄Π° Π½Π΅ ΠΈΡΠΊΠ»ΡΡΠ΅Π½ΠΈΠ΅, Ρ ΠΎΡΡ ΡΠ΅Ρ Π½ΠΈΡΠ΅ΡΠΊΠΎΠ΅ ΠΎΠ±ΡΠ»ΡΠΆΠΈΠ²Π°Π½ΠΈΠ΅ ΡΡΠ΅Π±ΡΠ΅ΡΡΡ ΠΌΠΈΠ½ΠΈΠΌΠ°Π»ΡΠ½ΠΎ.
ΠΡΠ΅ΠΆΠ΄Π΅ ΡΠ΅ΠΌ Π½Π°ΡΡΠΈΡΡΡΡ ΠΏΡΠ°Π²ΠΈΠ»ΡΠ½ΠΎ ΠΎΠ±ΡΠ»ΡΠΆΠΈΠ²Π°ΡΡ ΠΊΠΈΡΠ»ΠΎΡΠΎΠ΄Π½ΡΠΉ Π°ΠΏΠΏΠ°ΡΠ°Ρ, Π½Π΅ΠΎΠ±Ρ ΠΎΠ΄ΠΈΠΌΠΎ Π·Π½Π°ΡΡ, ΠΊΠ°ΠΊ Π΅Π³ΠΎ ΠΈΠ½ΠΈΡΠΈΠ°Π»ΠΈΠ·ΠΈΡΠΎΠ²Π°ΡΡ / ΠΈΡΠΏΠΎΠ»ΡΠ·ΠΎΠ²Π°ΡΡ.
ΠΡΠΏΠΎΠ»ΡΠ·ΠΎΠ²Π°ΡΡ ΠΊΠΈΡΠ»ΠΎΡΠΎΠ΄Π½ΡΠΉ ΠΊΠΎΠ½ΡΠ΅Π½ΡΡΠ°ΡΠΎΡ ΡΠ°ΠΊ ΠΆΠ΅ ΠΏΡΠΎΡΡΠΎ, ΠΊΠ°ΠΊ Π²ΠΊΠ»ΡΡΠΈΡΡ ΡΠ΅Π»Π΅Π²ΠΈΠ·ΠΎΡ. ΠΠ΅ΠΎΠ±Ρ ΠΎΠ΄ΠΈΠΌΠΎ Π²ΡΠΏΠΎΠ»Π½ΠΈΡΡ ΡΠ»Π΅Π΄ΡΡΡΠΈΠ΅ ΡΠ°Π³ΠΈ:
ΠΠ°ΡΠΈΠ΅Π½ΡΡ ΠΈΠ»ΠΈ Π΅Π³ΠΎ ΠΎΠΏΠ΅ΠΊΡΠ½Ρ ΡΠ»Π΅Π΄ΡΠ΅Ρ ΠΏΠΎΠΌΠ½ΠΈΡΡ ΠΎ Π½Π΅ΡΠΊΠΎΠ»ΡΠΊΠΈΡ Π²Π΅ΡΠ°Ρ , ΠΊΠΎΡΠΎΡΡΠ΅ Π½Π΅ΠΎΠ±Ρ ΠΎΠ΄ΠΈΠΌΠΎ ΡΡΠΈΡΡΠ²Π°ΡΡ ΠΏΡΠΈ ΠΈΡΠΏΠΎΠ»ΡΠ·ΠΎΠ²Π°Π½ΠΈΠΈ ΠΊΠΈΡΠ»ΠΎΡΠΎΠ΄Π½ΡΡ Π°ΠΏΠΏΠ°ΡΠ°ΡΠΎΠ².ΠΠ΅ΠΊΠΎΡΠΎΡΡΠ΅ ΠΈΠ· ΡΡΠΈΡ Π²Π΅ΡΠ΅ΠΉ ΡΡΠ΅Π±ΡΡΡ ΠΎΡΠΎΠ±ΠΎΠ³ΠΎ Π²Π½ΠΈΠΌΠ°Π½ΠΈΡ, Π° Π½Π΅ΠΊΠΎΡΠΎΡΡΠ΅ β Π²ΡΠ΅Π³ΠΎ Π»ΠΈΡΡ Π±Π°Π·ΠΎΠ²ΡΠ΅ ΠΌΠ΅ΡΠΎΠ΄Ρ ΠΎΠ±ΡΠ»ΡΠΆΠΈΠ²Π°Π½ΠΈΡ.
ΠΡΠΏΠΎΠ»ΡΠ·ΠΎΠ²Π°Π½ΠΈΠ΅ ΡΡΠ°Π±ΠΈΠ»ΠΈΠ·Π°ΡΠΎΡΠ° Π½Π°ΠΏΡΡΠΆΠ΅Π½ΠΈΡ
ΠΠΎ ΠΌΠ½ΠΎΠ³ΠΈΡ ΡΡΡΠ°Π½Π°Ρ Π»ΡΠ΄ΠΈ ΡΡΠ°Π»ΠΊΠΈΠ²Π°ΡΡΡΡ Ρ ΠΏΡΠΎΠ±Π»Π΅ΠΌΠΎΠΉ ΠΊΠΎΠ»Π΅Π±Π°Π½ΠΈΠΉ Π½Π°ΠΏΡΡΠΆΠ΅Π½ΠΈΡ. ΠΡΠ° ΠΏΡΠΎΠ±Π»Π΅ΠΌΠ° ΠΌΠΎΠΆΠ΅Ρ ΡΡΠ°ΡΡ ΡΠ±ΠΈΠΉΡΠ΅ΠΉ Π½Π΅ ΡΠΎΠ»ΡΠΊΠΎ ΠΊΠΈΡΠ»ΠΎΡΠΎΠ΄Π½ΠΎΠ³ΠΎ ΠΊΠΎΠ½ΡΠ΅Π½ΡΡΠ°ΡΠΎΡΠ°, Π½ΠΎ ΠΈ Π»ΡΠ±ΠΎΠ³ΠΎ Π±ΡΡΠΎΠ²ΠΎΠ³ΠΎ ΡΠ»Π΅ΠΊΡΡΠΎΠΎΠ±ΠΎΡΡΠ΄ΠΎΠ²Π°Π½ΠΈΡ.
ΠΠΎΡΠ»Π΅ ΠΎΡΠΊΠ»ΡΡΠ΅Π½ΠΈΡ ΡΠ»Π΅ΠΊΡΡΠΎΡΠ½Π΅ΡΠ³ΠΈΠΈ ΠΏΠΈΡΠ°Π½ΠΈΠ΅ Π²ΠΎΠ·Π²ΡΠ°ΡΠ°Π΅ΡΡΡ Ρ ΡΠ°ΠΊΠΈΠΌ Π²ΡΡΠΎΠΊΠΈΠΌ Π½Π°ΠΏΡΡΠΆΠ΅Π½ΠΈΠ΅ΠΌ, ΡΡΠΎ ΠΎΠ½ΠΎ ΠΌΠΎΠΆΠ΅Ρ ΠΏΠΎΠ²Π»ΠΈΡΡΡ Π½Π° ΠΊΠΎΠΌΠΏΡΠ΅ΡΡΠΎΡ. Π Π΅ΡΠΈΡΡ ΡΡΡ ΠΏΡΠΎΠ±Π»Π΅ΠΌΡ ΠΌΠΎΠΆΠ½ΠΎ, ΠΏΡΠΈΠΌΠ΅Π½ΠΈΠ² ΡΡΠ°Π±ΠΈΠ»ΠΈΠ·Π°ΡΠΎΡ Π½Π°ΠΏΡΡΠΆΠ΅Π½ΠΈΡ Ρ ΠΎΡΠΎΡΠ΅Π³ΠΎ ΠΊΠ°ΡΠ΅ΡΡΠ²Π°.Π‘ΡΠ°Π±ΠΈΠ»ΠΈΠ·Π°ΡΠΎΡ Π½Π°ΠΏΡΡΠΆΠ΅Π½ΠΈΡ ΡΡΠ°Π±ΠΈΠ»ΠΈΠ·ΠΈΡΡΠ΅Ρ ΠΊΠΎΠ»Π΅Π±Π°Π½ΠΈΡ Π½Π°ΠΏΡΡΠΆΠ΅Π½ΠΈΡ ΠΈ, ΡΠ»Π΅Π΄ΠΎΠ²Π°ΡΠ΅Π»ΡΠ½ΠΎ, ΡΠ²Π΅Π»ΠΈΡΠΈΠ²Π°Π΅Ρ ΡΡΠΎΠΊ ΡΠ»ΡΠΆΠ±Ρ ΡΡΠ°ΡΠΈΠΎΠ½Π°ΡΠ½ΠΎΠ³ΠΎ ΠΊΠΎΠ½ΡΠ΅Π½ΡΡΠ°ΡΠΎΡΠ° ΠΊΠΈΡΠ»ΠΎΡΠΎΠ΄Π°.
ΠΠ΅ΠΎΠ±ΡΠ·Π°ΡΠ΅Π»ΡΠ½ΠΎ ΠΈΡΠΏΠΎΠ»ΡΠ·ΠΎΠ²Π°ΡΡ ΡΡΠ°Π±ΠΈΠ»ΠΈΠ·Π°ΡΠΎΡ Π½Π°ΠΏΡΡΠΆΠ΅Π½ΠΈΡ, Π½ΠΎ ΡΠ΅ΠΊΠΎΠΌΠ΅Π½Π΄ΡΠ΅ΡΡΡ ; Π² ΠΊΠΎΠ½ΡΠ΅ ΠΊΠΎΠ½ΡΠΎΠ², Π²Ρ ΠΏΠΎΡΡΠ°ΡΠΈΡΠ΅ ΠΌΠ½ΠΎΠ³ΠΎ Π΄Π΅Π½Π΅Π³ Π½Π° ΠΏΠΎΠΊΡΠΏΠΊΡ ΠΊΠΎΠ½ΡΠ΅Π½ΡΡΠ°ΡΠΎΡΠ° ΠΊΠΈΡΠ»ΠΎΡΠΎΠ΄Π°, ΠΈ Π½Π΅Ρ Π½ΠΈΡΠ΅Π³ΠΎ ΠΏΠ»ΠΎΡ ΠΎΠ³ΠΎ Π² ΡΠΎΠΌ, ΡΡΠΎΠ±Ρ ΠΏΠΎΡΡΠ°ΡΠΈΡΡ Π΅ΡΠ΅ Π½Π΅ΡΠΊΠΎΠ»ΡΠΊΠΎ Π΄ΠΎΠ»Π»Π°ΡΠΎΠ² Π½Π° ΠΏΠΎΠΊΡΠΏΠΊΡ ΡΡΠ°Π±ΠΈΠ»ΠΈΠ·Π°ΡΠΎΡΠ° Π½Π°ΠΏΡΡΠΆΠ΅Π½ΠΈΡ.
Π Π°Π·ΠΌΠ΅ΡΠ΅Π½ΠΈΠ΅ ΠΊΠΎΠ½ΡΠ΅Π½ΡΡΠ°ΡΠΎΡΠ° ΠΊΠΈΡΠ»ΠΎΡΠΎΠ΄Π°
ΠΠΈΡΠ»ΠΎΡΠΎΠ΄Π½ΡΠΉ ΠΊΠΎΠ½ΡΠ΅Π½ΡΡΠ°ΡΠΎΡ ΠΌΠΎΠΆΠ½ΠΎ ΡΠ°Π·ΠΌΠ΅ΡΡΠΈΡΡ Π² Π»ΡΠ±ΠΎΠΌ ΠΌΠ΅ΡΡΠ΅ Π΄ΠΎΠΌΠ°; Π½ΠΎ Π²ΠΎ Π²ΡΠ΅ΠΌΡ ΡΠ°Π±ΠΎΡΡ Π΅Π³ΠΎ ΡΠ»Π΅Π΄ΡΠ΅Ρ Π΄Π΅ΡΠΆΠ°ΡΡ Π½Π° ΡΠ°ΡΡΡΠΎΡΠ½ΠΈΠΈ ΠΎΠ΄Π½ΠΎΠ³ΠΎ ΡΡΡΠ° ΠΎΡ ΡΡΠ΅Π½, ΠΊΡΠΎΠ²Π°ΡΠΈ, Π΄ΠΈΠ²Π°Π½Π° ΠΈ Ρ. Π΄.
ΠΠΎΠΊΡΡΠ³ Π²ΠΎΠ·Π΄ΡΡ ΠΎΠ·Π°Π±ΠΎΡΠ½ΠΈΠΊΠ° Π²Π°ΡΠ΅Π³ΠΎ ΠΊΠΎΠ½ΡΠ΅Π½ΡΡΠ°ΡΠΎΡΠ° ΠΊΠΈΡΠ»ΠΎΡΠΎΠ΄Π° Π΄ΠΎΠ»ΠΆΠ½ΠΎ Π±ΡΡΡ 1-2 ΡΡΡΠ° ΡΠ²ΠΎΠ±ΠΎΠ΄Π½ΠΎΠ³ΠΎ ΠΏΡΠΎΡΡΡΠ°Π½ΡΡΠ²Π°, ΡΠ°ΠΊ ΠΊΠ°ΠΊ ΠΊΠΎΠΌΠΏΡΠ΅ΡΡΠΎΡΡ Π²Π½ΡΡΡΠΈ ΠΌΠ°ΡΠΈΠ½Ρ Π½Π΅ΠΎΠ±Ρ ΠΎΠ΄ΠΈΠΌΠΎ ΠΏΡΠΎΡΡΡΠ°Π½ΡΡΠ²ΠΎ Π΄Π»Ρ ΠΏΡΠΈΠ΅ΠΌΠ° Π΄ΠΎΡΡΠ°ΡΠΎΡΠ½ΠΎΠ³ΠΎ ΠΊΠΎΠ»ΠΈΡΠ΅ΡΡΠ²Π° ΠΊΠΎΠΌΠ½Π°ΡΠ½ΠΎΠ³ΠΎ Π²ΠΎΠ·Π΄ΡΡ Π°, ΠΊΠΎΡΠΎΡΡΠΉ Π±ΡΠ΄Π΅Ρ ΠΊΠΎΠ½ΡΠ΅Π½ΡΡΠΈΡΠΎΠ²Π°ΡΡΡΡ Π΄ΠΎ ΡΠΈΡΡΠΎΠ³ΠΎ ΠΊΠΈΡΠ»ΠΎΡΠΎΠ΄Π° Π²Π½ΡΡΡΠΈ ΠΌΠ°ΡΠΈΠ½Π°. (ΠΠΎΠ·Π΄ΡΡ ΠΎΠ·Π°Π±ΠΎΡΠ½ΠΈΠΊ ΠΌΠΎΠΆΠ΅Ρ Π±ΡΡΡ ΡΠ·Π°Π΄ΠΈ, ΡΠΏΠ΅ΡΠ΅Π΄ΠΈ ΠΈΠ»ΠΈ ΠΏΠΎ Π±ΠΎΠΊΠ°ΠΌ ΠΌΠ°ΡΠΈΠ½Ρ β Π² Π·Π°Π²ΠΈΡΠΈΠΌΠΎΡΡΠΈ ΠΎΡ ΠΌΠΎΠ΄Π΅Π»ΠΈ).
ΠΡΠ»ΠΈ Π΄Π»Ρ Π·Π°Π±ΠΎΡΠ° Π²ΠΎΠ·Π΄ΡΡ Π° Π½Π΅ ΠΏΡΠ΅Π΄ΡΡΠΌΠΎΡΡΠ΅Π½ΠΎ Π΄ΠΎΡΡΠ°ΡΠΎΡΠ½ΠΎΠ³ΠΎ Π·Π°Π·ΠΎΡΠ°, ΡΠΎ Π΅ΡΡΡ Π²Π΅ΡΠΎΡΡΠ½ΠΎΡΡΡ ΡΠΎΠ³ΠΎ, ΡΡΠΎ ΠΊΠΎΠΌΠΏΡΠ΅ΡΡΠΎΡ ΠΌΠ°ΡΠΈΠ½Ρ ΠΌΠΎΠΆΠ΅Ρ Π½Π°Π³ΡΠ΅ΡΡΡΡ, ΠΏΠΎΡΠΊΠΎΠ»ΡΠΊΡ ΠΎΠ½ Π½Π΅ ΡΠΌΠΎΠΆΠ΅Ρ Π²ΡΠ°ΡΡΠ²Π°ΡΡ Π΄ΠΎΡΡΠ°ΡΠΎΡΠ½ΠΎΠ΅ ΠΊΠΎΠ»ΠΈΡΠ΅ΡΡΠ²ΠΎ ΠΎΠΊΡΡΠΆΠ°ΡΡΠ΅Π³ΠΎ Π²ΠΎΠ·Π΄ΡΡ Π°, ΠΈ ΠΌΠ°ΡΠΈΠ½Π° ΠΏΠΎΠ΄Π°ΡΡ ΡΠΈΠ³Π½Π°Π» ΡΡΠ΅Π²ΠΎΠ³ΠΈ.
Π€Π°ΠΊΡΠΎΡ Π·Π°ΠΏΡΠ»Π΅Π½Π½ΠΎΡΡΠΈ
ΠΡΠ»Ρ Π² ΠΎΠΊΡΡΠΆΠ°ΡΡΠ΅ΠΉ ΡΡΠ΅Π΄Π΅ ΠΈΠ³ΡΠ°Π΅Ρ ΠΎΡΠ΅Π½Ρ Π²Π°ΠΆΠ½ΡΡ ΡΠΎΠ»Ρ Π² ΡΠ°Π½Π½Π΅ΠΌ ΠΎΠ±ΡΠ»ΡΠΆΠΈΠ²Π°Π½ΠΈΠΈ ΠΌΠ°ΡΠΈΠ½Ρ.
ΠΠ°Π³ΡΡΠ·Π½Π΅Π½ΠΈΡ Π²ΠΎΠ·Π΄ΡΡ Π°, ΡΠ°ΠΊΠΈΠ΅ ΠΊΠ°ΠΊ ΡΠ°ΡΡΠΈΡΡ ΠΏΡΠ»ΠΈ, ΠΊΠΎΡΠΎΡΡΠ΅ ΠΎΡΡΠΈΠ»ΡΡΡΠΎΠ²ΡΠ²Π°ΡΡΡΡ ΡΠΈΠ»ΡΡΡΠ°ΠΌΠΈ ΠΌΠ°ΡΠΈΠ½Ρ. ΠΡΠΈ ΡΠΈΠ»ΡΡΡΡ Π·Π°Π±ΠΈΠ²Π°ΡΡΡΡ ΡΠ΅ΡΠ΅Π· Π½Π΅ΡΠΊΠΎΠ»ΡΠΊΠΎ ΠΌΠ΅ΡΡΡΠ΅Π² ΠΏΠΎΠ»Π½ΠΎΡΡΡΡ Π² Π·Π°Π²ΠΈΡΠΈΠΌΠΎΡΡΠΈ ΠΎΡ ΡΡΠΎΠ²Π½Ρ ΠΏΡΠ»ΠΈ Π² Π°ΡΠΌΠΎΡΡΠ΅ΡΠ΅ Π² ΠΏΠΎΠΌΠ΅ΡΠ΅Π½ΠΈΠΈ.
ΠΠΎΠ³Π΄Π° ΡΠΈΠ»ΡΡΡ Π·Π°Π±ΠΈΠ²Π°Π΅ΡΡΡ, ΡΠΈΡΡΠΎΡΠ° ΠΊΠΈΡΠ»ΠΎΡΠΎΠ΄Π° ΠΏΠ°Π΄Π°Π΅Ρ. ΠΠΎΠ³Π΄Π° ΡΡΠΎ ΠΏΡΠΎΠΈΡΡ ΠΎΠ΄ΠΈΡ, Π±ΠΎΠ»ΡΡΠΈΠ½ΡΡΠ²ΠΎ ΠΌΠ°ΡΠΈΠ½ Π½Π°ΡΠΈΠ½Π°ΡΡ ΠΏΠΎΠ΄Π°Π²Π°ΡΡ ΡΠΈΠ³Π½Π°Π» ΡΡΠ΅Π²ΠΎΠ³ΠΈ.Π ΡΠ°ΠΊΠΈΡ ΡΠ»ΡΡΠ°ΡΡ ΡΠΈΠ»ΡΡΡΡ Π½Π΅ΠΎΠ±Ρ ΠΎΠ΄ΠΈΠΌΠΎ ΠΏΠ΅ΡΠΈΠΎΠ΄ΠΈΡΠ΅ΡΠΊΠΈ Π·Π°ΠΌΠ΅Π½ΡΡΡ.
Π₯ΠΎΡΡ Π½Π΅Π²ΠΎΠ·ΠΌΠΎΠΆΠ½ΠΎ ΡΠ΄Π°Π»ΠΈΡΡ ΠΏΡΠ»Ρ ΠΈΠ· Π²ΠΎΠ·Π΄ΡΡ Π°, ΡΠ»Π΅Π΄ΡΠ΅Ρ ΠΈΠ·Π±Π΅Π³Π°ΡΡ ΠΈΡΠΏΠΎΠ»ΡΠ·ΠΎΠ²Π°Π½ΠΈΡ ΠΊΠΈΡΠ»ΠΎΡΠΎΠ΄Π½ΠΎΠ³ΠΎ Π°ΠΏΠΏΠ°ΡΠ°ΡΠ° Π² ΠΏΡΠ»ΡΠ½ΠΎΠΉ ΡΡΠ΅Π΄Π΅ ; ΡΠ°ΠΊΠΆΠ΅ ΠΌΠΎΠ³ΡΡ Π±ΡΡΡ ΠΏΡΠΈΠ½ΡΡΡ ΠΎΡΠ½ΠΎΠ²Π½ΡΠ΅ ΠΌΠ΅ΡΡ ΠΏΡΠ΅Π΄ΠΎΡΡΠΎΡΠΎΠΆΠ½ΠΎΡΡΠΈ, ΡΡΠΎΠ±Ρ ΡΠΌΠ΅Π½ΡΡΠΈΡΡ Π΅Π³ΠΎ, Π½Π°ΠΏΡΠΈΠΌΠ΅Ρ, ΠΊΠΎΠ³Π΄Π° Π΄ΠΎΠΌ ΡΠ±ΠΈΡΠ°ΡΡ, ΠΌΠ°ΡΠΈΠ½Ρ ΠΌΠΎΠΆΠ½ΠΎ Π²ΡΠΊΠ»ΡΡΠΈΡΡ ΠΈ Π½Π°ΠΊΡΡΡΡ, ΠΏΠΎΡΠΎΠΌΡ ΡΡΠΎ ΠΊΠΎΠ»ΠΈΡΠ΅ΡΡΠ²ΠΎ ΠΏΡΠ»ΠΈ Π²ΠΎ Π²ΡΠ΅ΠΌΡ ΡΠ±ΠΎΡΠΊΠΈ ΡΠ΅Π·ΠΊΠΎ Π²ΠΎΠ·ΡΠ°ΡΡΠ°Π΅Ρ.
ΠΠ°ΡΠΈΠ½Π°, Π΅ΡΠ»ΠΈ Π΅Π΅ ΠΈΡΠΏΠΎΠ»ΡΠ·ΠΎΠ²Π°ΡΡ Π² ΡΡΠΎ Π²ΡΠ΅ΠΌΡ, ΠΌΠΎΠΆΠ΅Ρ Π²ΡΠ°ΡΡΠ²Π°ΡΡ Π²ΡΡ ΠΏΡΠ»Ρ, Π² ΡΠ΅Π·ΡΠ»ΡΡΠ°ΡΠ΅ ΡΠ΅Π³ΠΎ ΡΠΈΠ»ΡΡΡ Π±ΡΡΡΡΠΎ Π·Π°Π±ΠΈΠ²Π°Π΅ΡΡΡ.
ΠΡΠ΄ΡΡ Π΄Π»Ρ ΠΌΠ°ΡΠΈΠ½Ρ
ΠΠΈΡΠ»ΠΎΡΠΎΠ΄Π½ΡΠ΅ ΠΊΠΎΠ½ΡΠ΅Π½ΡΡΠ°ΡΠΎΡΡ ΡΠ΄Π΅Π»Π°Π½Ρ ΡΠ°ΠΊΠΈΠΌ ΠΎΠ±ΡΠ°Π·ΠΎΠΌ, ΡΡΠΎ ΠΌΠΎΠ³ΡΡ ΡΠ°Π±ΠΎΡΠ°ΡΡ Π² ΡΠ΅ΡΠ΅Π½ΠΈΠ΅ 24 ΡΠ°ΡΠΎΠ². ΠΠΎ ΠΈΠ½ΠΎΠ³Π΄Π° ΠΎΠ½ΠΈ ΡΡΠ°Π»ΠΊΠΈΠ²Π°ΡΡΡΡ Ρ ΠΏΡΠΎΠ±Π»Π΅ΠΌΠΎΠΉ Π²Π½Π΅Π·Π°ΠΏΠ½ΠΎΠ³ΠΎ Π½Π°Π³ΡΠ΅Π²Π° ΠΈ ΠΎΡΡΠ°Π½ΠΎΠ²ΠΊΠΈ.
Π‘Π»Π΅Π΄ΠΎΠ²Π°ΡΠ΅Π»ΡΠ½ΠΎ, ΠΏΠΎΡΠ»Π΅ Π½Π΅ΠΏΡΠ΅ΡΡΠ²Π½ΠΎΠ³ΠΎ ΠΈΡΠΏΠΎΠ»ΡΠ·ΠΎΠ²Π°Π½ΠΈΡ Π² ΡΠ΅ΡΠ΅Π½ΠΈΠ΅ 7-8 ΡΠ°ΡΠΎΠ² ΠΊΠΎΠ½ΡΠ΅Π½ΡΡΠ°ΡΠΎΡ Π΄ΠΎΠ»ΠΆΠ΅Π½ ΠΎΡΠ΄ΠΎΡ Π½ΡΡΡ Π² ΡΠ΅ΡΠ΅Π½ΠΈΠ΅ 20-30 ΠΌΠΈΠ½ΡΡ.
Π§Π΅ΡΠ΅Π· 20-30 ΠΌΠΈΠ½ΡΡ ΠΏΠ°ΡΠΈΠ΅Π½Ρ ΠΌΠΎΠΆΠ΅Ρ Π²ΠΊΠ»ΡΡΠΈΡΡ ΠΊΠΎΠ½ΡΠ΅Π½ΡΡΠ°ΡΠΎΡ ΠΈ ΠΈΡΠΏΠΎΠ»ΡΠ·ΠΎΠ²Π°ΡΡ Π΅Π³ΠΎ Π΅ΡΠ΅ 7-8 ΡΠ°ΡΠΎΠ², ΠΏΡΠ΅ΠΆΠ΄Π΅ ΡΠ΅ΠΌ ΡΠ½ΠΎΠ²Π° Π΄Π°ΡΡ Π΅ΠΌΡ ΠΎΡΠ΄ΠΎΡ Π½ΡΡΡ Π² ΡΠ΅ΡΠ΅Π½ΠΈΠ΅ 20-30 ΠΌΠΈΠ½ΡΡ.
ΠΠΎΠ³Π΄Π° Π°ΠΏΠΏΠ°ΡΠ°Ρ Π²ΡΠΊΠ»ΡΡΠ΅Π½, ΠΏΠ°ΡΠΈΠ΅Π½Ρ ΠΌΠΎΠΆΠ΅Ρ ΠΈΡΠΏΠΎΠ»ΡΠ·ΠΎΠ²Π°ΡΡ ΡΠ΅Π·Π΅ΡΠ²Π½ΡΠΉ Π±Π°Π»Π»ΠΎΠ½. ΠΡΠΎ ΠΏΡΠΎΠ΄Π»ΠΈΡ ΡΡΠΎΠΊ ΡΠ»ΡΠΆΠ±Ρ ΠΊΠΎΠΌΠΏΡΠ΅ΡΡΠΎΡΠ° ΠΊΠΎΠ½ΡΠ΅Π½ΡΡΠ°ΡΠΎΡΠ°.
ΠΡΡΡ Π² Π΄ΠΎΠΌΠ΅
Π‘ΡΠ°ΡΠΈΠΎΠ½Π°ΡΠ½ΡΠ΅ ΠΊΠΎΠ½ΡΠ΅Π½ΡΡΠ°ΡΠΎΡΡ ΠΊΠΈΡΠ»ΠΎΡΠΎΠ΄Π° ΡΡΠ°Π»ΠΊΠΈΠ²Π°ΡΡΡΡ Ρ ΠΎΠ³ΡΠΎΠΌΠ½ΠΎΠΉ ΠΏΡΠΎΠ±Π»Π΅ΠΌΠΎΠΉ ΠΈΠ·-Π·Π° Π±Π΅Π³Π°ΡΡΠ΅ΠΉ ΠΏΠΎ Π΄ΠΎΠΌΡ ΠΌΡΡΠΈ.
Π Π±ΠΎΠ»ΡΡΠΈΠ½ΡΡΠ²Π΅ ΡΡΠ°ΡΠΈΠΎΠ½Π°ΡΠ½ΡΡ ΠΊΠΎΠ½ΡΠ΅Π½ΡΡΠ°ΡΠΎΡΠΎΠ² ΠΊΠΈΡΠ»ΠΎΡΠΎΠ΄Π° Π΅ΡΡΡ Π²Π΅Π½ΡΠΈΠ»ΡΡΠΈΠΎΠ½Π½ΡΠ΅ ΠΎΡΠ²Π΅ΡΡΡΠΈΡ ΠΏΠΎΠ΄ ΠΈΠ»ΠΈ Π·Π° ΠΌΠ°ΡΠΈΠ½ΠΎΠΉ.
ΠΠΎ Π²ΡΠ΅ΠΌΡ ΡΠ°Π±ΠΎΡΡ Π½Π° ΠΌΠ°ΡΠΈΠ½Π΅ ΠΌΡΡΡ Π½Π΅ ΠΌΠΎΠΆΠ΅Ρ ΠΏΠΎΠΏΠ°ΡΡΡ Π²Π½ΡΡΡΡ ΠΌΠ°ΡΠΈΠ½Ρ.
ΠΠΎ ΠΊΠΎΠ³Π΄Π° ΠΌΠ°ΡΠΈΠ½Π° ΠΎΡΡΠ°Π½ΠΎΠ²Π»Π΅Π½Π°, ΠΌΡΡΡ ΠΌΠΎΠΆΠ΅Ρ ΠΏΠΎΠΏΠ°ΡΡΡ Π²Π½ΡΡΡΡ ΠΈ ΡΠΎΠ·Π΄Π°ΡΡ Π½Π΅ΡΠ΄ΠΎΠ±ΡΡΠ²Π° , Π½Π°ΠΏΡΠΈΠΌΠ΅Ρ, ΠΏΠ΅ΡΠ΅ΠΆΠ΅Π²ΡΠ²Π°ΡΡ ΠΏΡΠΎΠ²ΠΎΠ΄Π° ΠΈ ΠΌΠΎΡΠΈΡΡΡΡ Π½Π° ΠΏΠ΅ΡΠ°ΡΠ½ΡΡ ΠΏΠ»Π°ΡΡ (PCB) ΠΌΠ°ΡΠΈΠ½Ρ. ΠΠ°ΠΊ ΡΠΎΠ»ΡΠΊΠΎ Π²ΠΎΠ΄Π° ΠΏΠΎΠΏΠ°Π΄Π°Π΅Ρ Π½Π° ΠΏΠ΅ΡΠ°ΡΠ½ΡΡ ΠΏΠ»Π°ΡΡ, ΠΌΠ°ΡΠΈΠ½Π° Π²ΡΡ ΠΎΠ΄ΠΈΡ ΠΈΠ· ΡΡΡΠΎΡ. ΠΠ΅ΡΠ°ΡΠ½ΡΠ΅ ΠΏΠ»Π°ΡΡ Π² ΠΎΡΠ»ΠΈΡΠΈΠ΅ ΠΎΡ ΡΠΈΠ»ΡΡΡΠΎΠ² Π΄ΠΎΠ²ΠΎΠ»ΡΠ½ΠΎ Π΄ΠΎΡΠΎΠ³ΠΈΠ΅.
Π€ΠΈΠ»ΡΡΡΡ
Π Π½Π΅ΠΊΠΎΡΠΎΡΡΡ ΠΌΠ°ΡΠΈΠ½Π°Ρ Π΅ΡΡΡ ΡΠΊΠ°Ρ / Π²Π½Π΅ΡΠ½ΠΈΠΉ ΡΠΈΠ»ΡΡΡ ΡΠ½Π°ΡΡΠΆΠΈ, ΠΊΠΎΡΠΎΡΡΠΉ ΠΌΠΎΠΆΠ½ΠΎ Π»Π΅Π³ΠΊΠΎ Π²ΡΠ½ΡΡΡ.ΠΡΠΎΡ ΡΠΈΠ»ΡΡΡ ΡΠ»Π΅Π΄ΡΠ΅Ρ ΠΎΡΠΈΡΠ°ΡΡ ΠΎΠ΄ΠΈΠ½ ΡΠ°Π· Π² Π½Π΅Π΄Π΅Π»Ρ (ΠΈΠ»ΠΈ ΡΠ°ΡΠ΅, Π² Π·Π°Π²ΠΈΡΠΈΠΌΠΎΡΡΠΈ ΠΎΡ ΡΡΠ»ΠΎΠ²ΠΈΠΉ ΡΠΊΡΠΏΠ»ΡΠ°ΡΠ°ΡΠΈΠΈ) ΠΌΡΠ»ΡΠ½ΠΎΠΉ Π²ΠΎΠ΄ΠΎΠΉ. ΠΠ±ΡΠ°ΡΠΈΡΠ΅ Π²Π½ΠΈΠΌΠ°Π½ΠΈΠ΅, ΡΡΠΎ ΠΏΠ΅ΡΠ΅Π΄ ΡΠ΅ΠΌ, ΠΊΠ°ΠΊ ΡΠ½ΠΎΠ²Π° ΠΏΠΎΠ»ΠΎΠΆΠΈΡΡ Π² ΠΌΠ°ΡΠΈΠ½Ρ, Π΅Π³ΠΎ ΡΠ»Π΅Π΄ΡΠ΅Ρ ΠΏΠΎΠ»Π½ΠΎΡΡΡΡ Π²ΡΡΡΡΠΈΡΡ.
ΠΠ°ΠΌΠ΅Π½Ρ Π²Π½ΡΡΡΠ΅Π½Π½ΠΈΡ ΡΠΈΠ»ΡΡΡΠΎΠ² Π΄ΠΎΠ»ΠΆΠ΅Π½ Π²ΡΠΏΠΎΠ»Π½ΡΡΡ ΡΠΎΠ»ΡΠΊΠΎ ΡΠΏΠΎΠ»Π½ΠΎΠΌΠΎΡΠ΅Π½Π½ΡΠΉ ΡΠ΅ΡΠ²ΠΈΡΠ½ΡΠΉ ΠΈΠ½ΠΆΠ΅Π½Π΅Ρ Π²Π°ΡΠ΅Π³ΠΎ ΠΏΠΎΡΡΠ°Π²ΡΠΈΠΊΠ° ΠΎΠ±ΠΎΡΡΠ΄ΠΎΠ²Π°Π½ΠΈΡ. ΠΡΠΈ ΡΠΈΠ»ΡΡΡΡ ΡΠ΅ΠΆΠ΅ ΡΡΠ΅Π±ΡΡΡ Π·Π°ΠΌΠ΅Π½Ρ.
Π£Π²Π»Π°ΠΆΠ½ΠΈΡΠ΅Π»Ρ ΠΡΠΈΡΡΠΊΠ°
- Π‘Π»Π΅Π΄ΡΠ΅Ρ ΠΈΡΠΏΠΎΠ»ΡΠ·ΠΎΠ²Π°ΡΡ ΡΠΈΡΡΡΡ ΠΏΠΈΡΡΠ΅Π²ΡΡ Π²ΠΎΠ΄Ρ Π΄Π»Ρ ΡΠ²Π»Π°ΠΆΠ½Π΅Π½ΠΈΡ, ΡΡΠΎΠ±Ρ ΠΈΠ·Π±Π΅ΠΆΠ°ΡΡ / ΠΎΡΡΡΠΎΡΠΈΡΡ Π·Π°ΡΠΎΡΠ΅Π½ΠΈΠ΅ ΠΎΡΠ²Π΅ΡΡΡΠΈΠΉ Π±ΡΡΡΠ»ΠΊΠΈ Π² Π΄ΠΎΠ»Π³ΠΎΡΡΠΎΡΠ½ΠΎΠΉ ΠΏΠ΅ΡΡΠΏΠ΅ΠΊΡΠΈΠ²Π΅
- ΠΠΎΠ΄Π° Π½Π΅ Π΄ΠΎΠ»ΠΆΠ½Π° Π±ΡΡΡ Π½ΠΈΠΆΠ΅ / Π²ΡΡΠ΅ ΡΠΎΠΎΡΠ²Π΅ΡΡΡΠ²ΡΡΡΠΈΡ ΠΎΡΠΌΠ΅ΡΠΎΠΊ ΠΌΠΈΠ½ΠΈΠΌΠ°Π»ΡΠ½ΠΎΠ³ΠΎ / ΠΌΠ°ΠΊΡΠΈΠΌΠ°Π»ΡΠ½ΠΎΠ³ΠΎ ΡΡΠΎΠ²Π½Ρ Π²ΠΎΠ΄Ρ Π½Π° Π±ΡΡΡΠ»ΠΊΠ΅
- ΠΠΎΠ΄Π° Π² Π±ΡΡΡΠ»ΠΊΠ΅ Π·Π°ΠΌΠ΅Π½ΡΡΡ ΡΠ°Π· Π² 2 Π΄Π½Ρ
- Π€Π»Π°ΠΊΠΎΠ½ Π½Π΅ΠΎΠ±Ρ ΠΎΠ΄ΠΈΠΌΠΎ ΠΎΡΠΈΡΠ°ΡΡ ΠΈΠ·Π½ΡΡΡΠΈ ΡΠ°Π· Π² 2 Π΄Π½Ρ
ΠΡΠ½ΠΎΠ²Π½ΡΠ΅ ΠΌΠ΅ΡΡ ΠΏΡΠ΅Π΄ΠΎΡΡΠΎΡΠΎΠΆΠ½ΠΎΡΡΠΈ ΠΈ ΠΌΠ΅ΡΠΎΠ΄Ρ ΠΎΡΠΈΡΡΠΊΠΈ
- ΠΠ°ΡΠΈΠ½Ρ Π½Π΅Π»ΡΠ·Ρ ΠΏΠ΅ΡΠ΅ΠΌΠ΅ΡΠ°ΡΡ ΠΏΠΎ ΠΏΠ΅ΡΠ΅ΡΠ΅ΡΠ΅Π½Π½ΠΎΠΉ ΠΌΠ΅ΡΡΠ½ΠΎΡΡΠΈ , Π³Π΄Π΅ ΠΊΠΎΠ»Π΅ΡΠ° ΠΌΠ°ΡΠΈΠ½Ρ ΠΌΠΎΠ³ΡΡ ΡΠ»ΠΎΠΌΠ°ΡΡΡΡ.Π ΡΠ°ΠΊΠΈΡ ΡΠ»ΡΡΠ°ΡΡ Π½Π°ΡΡΠΎΡΡΠ΅Π»ΡΠ½ΠΎ ΡΠ΅ΠΊΠΎΠΌΠ΅Π½Π΄ΡΠ΅ΡΡΡ ΠΏΠΎΠ΄Π½ΡΡΡ ΠΌΠ°ΡΠΈΠ½Ρ, Π° Π·Π°ΡΠ΅ΠΌ ΠΏΠ΅ΡΠ΅ΠΌΠ΅ΡΡΠΈΡΡ.
- ΠΠΈΡΠ»ΠΎΡΠΎΠ΄Π½Π°Ρ ΡΡΡΠ±ΠΊΠ° Π½Π΅ Π΄ΠΎΠ»ΠΆΠ½Π° ΠΈΠΌΠ΅ΡΡ ΠΏΠ΅ΡΠ΅Π³ΠΈΠ±ΠΎΠ² ΠΈΠ»ΠΈ ΡΡΠ΅ΡΠΊΠΈ ΠΈΠ· Π²ΡΠΏΡΡΠΊΠ½ΠΎΠ³ΠΎ ΠΎΡΠ²Π΅ΡΡΡΠΈΡ Π΄Π»Ρ ΠΊΠΈΡΠ»ΠΎΡΠΎΠ΄Π°, Π³Π΄Π΅ ΠΎΠ½Π° ΠΏΡΠΈΠΊΡΠ΅ΠΏΠ»Π΅Π½Π° ΠΊ Π½ΠΎΡΠΎΠ²ΡΠΌ ΠΊΠ°Π½ΡΠ»ΡΠΌ.
- ΠΠ΅Π»ΡΠ·Ρ ΠΏΡΠΎΠ»ΠΈΠ²Π°ΡΡ Π²ΠΎΠ΄Ρ Π½Π° ΠΌΠ°ΡΠΈΠ½Ρ
- ΠΠΏΠΏΠ°ΡΠ°Ρ Π½Π΅ ΡΠ»Π΅Π΄ΡΠ΅Ρ Π΄Π΅ΡΠΆΠ°ΡΡ Π²Π±Π»ΠΈΠ·ΠΈ ΠΎΠ³Π½Ρ ΠΈΠ»ΠΈ Π΄ΡΠΌΠ°
- ΠΠ½Π΅ΡΠ½ΠΈΠΉ ΠΊΠΎΡΠΏΡΡ ΠΌΠ°ΡΠΈΠ½Ρ ΡΠ»Π΅Π΄ΡΠ΅Ρ ΠΎΡΠΈΡΡΠΈΡΡ ΠΌΡΠ³ΠΊΠΈΠΌ Π±ΡΡΠΎΠ²ΡΠΌ ΡΠΈΡΡΡΡΠΈΠΌ ΡΡΠ΅Π΄ΡΡΠ²ΠΎΠΌ , Π½Π°Π½Π΅ΡΠ΅Π½Π½ΡΠΌ Ρ ΠΏΠΎΠΌΠΎΡΡΡ Π³ΡΠ±ΠΊΠΈ / Π²Π»Π°ΠΆΠ½ΠΎΠΉ ΡΠΊΠ°Π½ΠΈ, Π° Π·Π°ΡΠ΅ΠΌ Π½Π°ΡΡΡ ΠΎ ΠΏΡΠΎΡΠ΅ΡΠ΅ΡΡ Π²ΡΠ΅ ΠΏΠΎΠ²Π΅ΡΡ Π½ΠΎΡΡΠΈ.ΠΠ΅ Π΄ΠΎΠΏΡΡΠΊΠ°ΠΉΡΠ΅ ΠΏΠΎΠΏΠ°Π΄Π°Π½ΠΈΡ ΠΆΠΈΠ΄ΠΊΠΎΡΡΠΈ Π²Π½ΡΡΡΡ ΡΡΡΡΠΎΠΉΡΡΠ²Π°
Π Π΅Π·ΡΠΌΠ΅
- ΠΡΠΏΠΎΠ»ΡΠ·ΡΠΉΡΠ΅ ΡΡΠ°Π±ΠΈΠ»ΠΈΠ·Π°ΡΠΎΡ Π½Π°ΠΏΡΡΠΆΠ΅Π½ΠΈΡ Ρ ΠΎΡΠΎΡΠ΅Π³ΠΎ ΠΊΠ°ΡΠ΅ΡΡΠ²Π°
- ΠΠ΅ΡΠΆΠΈΡΠ΅ ΠΊΠΎΠ½ΡΠ΅Π½ΡΡΠ°ΡΠΎΡ Π½Π° ΡΠ°ΡΡΡΠΎΡΠ½ΠΈΠΈ 1-2 ΡΡΡΠ° ΠΎΡ Π²ΡΠ΅Ρ ΡΡΠ΅Π½
- ΠΠ·Π±Π΅Π³Π°ΠΉΡΠ΅ ΠΈΡΠΏΠΎΠ»ΡΠ·ΠΎΠ²Π°Π½ΠΈΡ ΠΌΠ°ΡΠΈΠ½Ρ Π² ΠΏΡΠ»ΡΠ½ΠΎΠΉ ΡΡΠ΅Π΄Π΅
- Π Π΅Π³ΡΠ»ΡΡΠ½ΠΎ Π²ΡΠΏΠΎΠ»Π½ΡΠΉΡΠ΅ ΡΠ°Π±ΠΎΡΡ ΠΏΡΠΎΠ²Π΅ΡΠΎΠΊ Π²ΡΠΏΠΎΠ»Π½Π΅Π½ΠΎ
- ΠΠ΅ Π·Π°ΠΏΡΡΠΊΠ°ΠΉΡΠ΅ ΠΌΠ°ΡΠΈΠ½Ρ Π½Π΅ΠΏΡΠ΅ΡΡΠ²Π½ΠΎ Π² ΡΠ΅ΡΠ΅Π½ΠΈΠ΅ Π΄Π»ΠΈΡΠ΅Π»ΡΠ½ΠΎΠ³ΠΎ Π²ΡΠ΅ΠΌΠ΅Π½ΠΈ.ΠΠ°ΠΉΡΠ΅ Π΅ΠΌΡ Π½Π΅ΠΌΠ½ΠΎΠ³ΠΎ ΠΎΡΠ΄ΡΡ Π° .
- ΠΡΠΏΠΎΠ»ΡΠ·ΡΠΉΡΠ΅ ΡΠΈΡΡΡΡ Π²ΠΎΠ΄Ρ Π² ΡΠ²Π»Π°ΠΆΠ½ΠΈΡΠ΅Π»Π΅ ΠΈ Π·Π°ΠΌΠ΅Π½ΡΠΉΡΠ΅ Π΅Π³ΠΎ ΠΊΠ°ΠΆΠ΄ΡΠ΅ 2 Π΄Π½Ρ.
ΠΡΠ΅ Π²ΡΡΠ΅ΠΏΠ΅ΡΠ΅ΡΠΈΡΠ»Π΅Π½Π½ΡΠ΅ ΠΌΠ΅ΡΡ ΠΏΠΎΠ·Π²ΠΎΠ»ΡΡ ΠΏΡΠΎΠ΄Π»ΠΈΡΡ ΡΡΠΎΠΊ ΡΠ»ΡΠΆΠ±Ρ ΠΊΠΈΡΠ»ΠΎΡΠΎΠ΄Π½ΠΎΠ³ΠΎ ΠΊΠΎΠ½ΡΠ΅Π½ΡΡΠ°ΡΠΎΡΠ° ΠΈ ΡΠ½ΠΈΠ·ΠΈΡΡ Π·Π°ΡΡΠ°ΡΡ Π½Π° ΡΠ΅ΠΌΠΎΠ½Ρ / ΠΎΠ±ΡΠ»ΡΠΆΠΈΠ²Π°Π½ΠΈΠ΅ Π°ΠΏΠΏΠ°ΡΠ°ΡΠ°.
ΠΠ΄Π½Π°ΠΊΠΎ ΠΊΠΎΠ½ΡΠ΅Π½ΡΡΠ°ΡΠΎΡ Π²ΡΠ΅ ΡΠ°Π²Π½ΠΎ ΠΌΠΎΠΆΠ΅Ρ Π²ΡΠΉΡΠΈ ΠΈΠ· ΡΡΡΠΎΡ Π² Π»ΡΠ±ΠΎΠΉ ΠΌΠΎΠΌΠ΅Π½Ρ, ΠΏΠΎΡΠΊΠΎΠ»ΡΠΊΡ Π² ΠΊΠΎΠ½ΡΠ΅ ΠΊΠΎΠ½ΡΠΎΠ² ΡΡΠΎ ΠΌΠ°ΡΠΈΠ½Π°. ΠΠΎΡΡΠΎΠΌΡ Π½Π°ΡΡΠΎΡΡΠ΅Π»ΡΠ½ΠΎ ΡΠ΅ΠΊΠΎΠΌΠ΅Π½Π΄ΡΠ΅ΡΡΡ Π²ΡΠ΅Π³Π΄Π° ΠΈΠΌΠ΅ΡΡ ΠΏΡΠΈ ΡΠ΅Π±Π΅ ΡΠ΅Π·Π΅ΡΠ²Π½ΡΠΉ Π±Π°Π»Π»ΠΎΠ½, ΠΏΠΎΡΠΎΠΌΡ ΡΡΠΎ ΡΠ΅ΡΠ²ΠΈΡΠ½ΠΎΠΌΡ ΠΈΠ½ΠΆΠ΅Π½Π΅ΡΡ ΡΠ°ΠΊΠΆΠ΅ ΠΏΠΎΡΡΠ΅Π±ΡΠ΅ΡΡΡ Π½Π΅ΠΊΠΎΡΠΎΡΠΎΠ΅ Π²ΡΠ΅ΠΌΡ, ΡΡΠΎΠ±Ρ Π΄ΠΎΠ±ΡΠ°ΡΡΡΡ Π΄ΠΎ Π²Π°ΡΠ΅Π³ΠΎ Π΄ΠΎΠΌΠ° Π΄Π»Ρ ΡΠ΅ΠΌΠΎΠ½ΡΠ° ΠΊΠΎΠ½ΡΠ΅Π½ΡΡΠ°ΡΠΎΡΠ°.Π ΠΈΠ΄Π΅Π°Π»Π΅ ΡΠ»Π΅Π΄ΡΠ΅Ρ ΠΈΠΌΠ΅ΡΡ Π·Π°ΠΏΠ°ΡΠ½ΠΎΠΉ Π±Π°Π»Π»ΠΎΠ½, ΡΠ°ΡΡΡΠΈΡΠ°Π½Π½ΡΠΉ Π½Π° 24 ΡΠ°ΡΠ°.
.ΠΠ°Π»ΠΈΠ±ΡΠΎΠ²ΠΊΠ° ΠΏΠΎΠ»ΡΡΠΈΠ·Π°ΡΠΈΠΈ ΠΏΡΠΈΠ½ΡΠΈΠΏΠ° ΡΠ°Π±ΠΎΡΡ Π·ΠΎΠ½Π΄Π°Do
ΠΠ·ΠΌΠ΅ΡΠΈΡΠ΅Π»Ρ ΡΠ°ΡΡΠ²ΠΎΡΠ΅Π½Π½ΠΎΠ³ΠΎ ΠΊΠΈΡΠ»ΠΎΡΠΎΠ΄Π°β ΠΎΠ΄ΠΈΠ½ ΠΈΠ· ΠΈΠ½ΡΠ΅ΡΠ°ΠΊΡΠΈΠ²Π½ΡΡ ΡΠ»Π΅ΠΊΡΡΠΎΡ ΠΈΠΌΠΈΡΠ΅ΡΠΊΠΈΡ Π°Π½Π°Π»ΠΈΠ·Π°ΡΠΎΡΠΎΠ², ΡΠ°Π·ΡΠ°Π±ΠΎΡΠ°Π½Π½ΡΡ ΡΡΠΎΠΉ ΠΊΠΎΠΌΠΏΠ°Π½ΠΈΠ΅ΠΉ. ΠΡΠΎ Π²ΡΡΠΎΠΊΠΎΠΈΠ½ΡΠ΅Π»Π»Π΅ΠΊΡΡΠ°Π»ΡΠ½ΠΎΠ΅ ΡΡΡΡΠΎΠΉΡΡΠ²ΠΎ Π½Π΅ΠΏΡΠ΅ΡΡΠ²Π½ΠΎΠ³ΠΎ ΠΎΠΏΠ΅ΡΠ°ΡΠΈΠ²Π½ΠΎΠ³ΠΎ ΠΌΠΎΠ½ΠΈΡΠΎΡΠΈΠ½Π³Π°. ΠΠ³ΠΎ ΠΌΠΎΠΆΠ½ΠΎ ΠΈΡΠΏΠΎΠ»ΡΠ·ΠΎΠ²Π°ΡΡ Π²ΠΌΠ΅ΡΡΠ΅ Ρ ΠΏΠΎΠ»ΡΡΠΎΠ³ΡΠ°ΡΠΈΡΠ΅ΡΠΊΠΈΠΌ ΡΠ»Π΅ΠΊΡΡΠΎΠ΄ΠΎΠΌ Π΄Π»Ρ Π²ΡΠΏΠΎΠ»Π½Π΅Π½ΠΈΡ ΠΈΠ·ΠΌΠ΅ΡΠ΅Π½ΠΈΠΉ Π² ΡΠΈΡΠΎΠΊΠΎΠΌ Π΄ΠΈΠ°ΠΏΠ°Π·ΠΎΠ½Π΅ ΠΎΡ ΡΡΠΎΠ²Π½Ρ ppb Π΄ΠΎ ΡΡΠΎΠ²Π½Ρ ppm. ΠΡΠΎ ΡΠΏΠ΅ΡΠΈΠ°Π»ΡΠ½ΡΠΉ ΠΏΡΠΈΠ±ΠΎΡ Π΄Π»Ρ ΡΠ΅ΡΡΠΈΡΠΎΠ²Π°Π½ΠΈΡ ΠΈ ΠΈΠ·ΠΌΠ΅ΡΠ΅Π½ΠΈΡ ΡΠΎΠ΄Π΅ΡΠΆΠ°Π½ΠΈΡ ΠΊΠΈΡΠ»ΠΎΡΠΎΠ΄Π° Π² ΡΠ°ΠΊΠΎΠΉ Π²ΠΎΠ΄Π΅, ΠΊΠ°ΠΊ ΠΊΠΎΡΠ»ΠΎΠ²Π°Ρ Π²ΠΎΠ΄Π°, ΠΊΠΎΠ½Π΄Π΅Π½ΡΠ°Ρ ΠΈ ΡΡΠΎΡΠ½ΡΠ΅ Π²ΠΎΠ΄Ρ.ΠΠ½ Ρ Π°ΡΠ°ΠΊΡΠ΅ΡΠΈΠ·ΡΠ΅ΡΡΡ Π±ΡΡΡΡΡΠΌ ΠΎΡΠΊΠ»ΠΈΠΊΠΎΠΌ, ΡΡΠ°Π±ΠΈΠ»ΡΠ½ΠΎΡΡΡΡ, Π²ΡΡΠΎΠΊΠΎΠΉ Π½Π°Π΄Π΅ΠΆΠ½ΠΎΡΡΡΡ ΠΈ Π½ΠΈΠ·ΠΊΠΈΠΌΠΈ Π·Π°ΡΡΠ°ΡΠ°ΠΌΠΈ Π½Π° ΡΠ΅Ρ Π½ΠΈΡΠ΅ΡΠΊΠΎΠ΅ ΠΎΠ±ΡΠ»ΡΠΆΠΈΠ²Π°Π½ΠΈΠ΅, ΠΏΠΎΠ΄Ρ ΠΎΠ΄ΠΈΡ Π΄Π»Ρ ΡΠΈΡΠΎΠΊΠΎΠ³ΠΎ ΠΈΡΠΏΠΎΠ»ΡΠ·ΠΎΠ²Π°Π½ΠΈΡ Π½Π° ΡΠ»Π΅ΠΊΡΡΠΎΡΡΠ°Π½ΡΠΈΡΡ .
ΠΠΏΠΈΡΠ°Π½ΠΈΠ΅ ΠΏΡΠΎΠ΄ΡΠΊΡΠ°
ΠΡΠ½ΠΎΠ²Π½ΡΠ΅ ΠΏΠ°ΡΠ°ΠΌΠ΅ΡΡΡ ΠΊΠΎΠ½ΡΡΠΎΠ»Π»Π΅ΡΠ° DOG-3082/2082/2092
900 15 ΠΏΠ°Π½Π΅Π»ΡΠΠΎΠ΄Π΅Π»Ρ | DOG-3082 | DOG-2082 | DOG-2092 |
ΠΠΈΠ°ΠΏΠ°Π·ΠΎΠ½ | 0 ~ 100 ΠΌΠΊΠ³ / Π», 0 ~ 20 ΠΌΠ³ / Π» | 0 ~ 20 ΠΌΠ³ / Π» | |
Π’Π΅ΠΌΠΏΠ΅ΡΠ°ΡΡΡΠ½Π°Ρ ΠΊΠΎΠΌΠΏΠ΅Π½ΡΠ°ΡΠΈΡ | 0 ~ 99.9C / 0 ~ 150C (ΠΈΠ½Π΄ΠΈΠ²ΠΈΠ΄ΡΠ°Π»ΡΠ½ΠΎ) | 0 ~ 99C | |
Π Π°Π·ΡΠ΅ΡΠ΅Π½ΠΈΠ΅ | 0,1 ΠΌΠΊΠ³ / Π»; 0,01 ΠΌΠ³ / Π»; 0,1C | 0,01 ΠΌΠ³ / Π»; 0,01% | |
Π’ΠΎΡΠ½ΠΎΡΡΡ | ΠΌΠΊΠ³ /L:+/-1.0%FS,mg/L:0.5%FS,temp:+/-0.5C | +/- 1,5% | |
Π‘Π²ΡΠ·Ρ | RS485 (Π΄ΠΎΠΏΠΎΠ»Π½ΠΈΡΠ΅Π»ΡΠ½ΠΎ) | ||
ΠΡΡ ΠΎΠ΄ | 0 ~ 10 ΠΌΠ, 4-20 ΠΌΠ | 4-20 ΠΌΠ | |
Π Π΅Π»Π΅ | 2 ΡΠ΅Π»Π΅ | ||
ΠΠΈΡΠ°Π½ΠΈΠ΅ | 220VAC ΠΈΠ»ΠΈ 24VDC | 220VAC | |
ΠΠ°ΡΠΈΡΠ° | IP65 | ||
ΠΡΠ΅ΠΌΡ ΡΠΎΡ ΡΠ°Π½Π΅Π½ΠΈΡ Π΄Π°Π½Π½ΡΡ | 10 Π»Π΅Ρ | ||
ΠΠ±ΡΠΈΠΉ ΡΠ°Π·ΠΌΠ΅Ρ | 146 * 146 * 150 ΠΌΠΌ | 146 * 146 * 108 ΠΌΠΌ | 96 * 96 * 110 ΠΌΠΌ |
Π Π°Π·ΠΌΠ΅Ρ ΠΎΡΠ²Π΅ΡΡΡΠΈΡ | 138 * 138 ΠΌΠΌ | 138 * 138 ΠΌΠΌ | 92 * 62 ΠΌΠΌ |
ΠΠ°Π²Π΅ΡΠ½ΠΎΠΉ | ΠΠ°ΡΡΠ΅Π½Π½ΡΠΉ / ΠΏΠ°Π½Π΅Π»ΡΠ½ΡΠΉ | ΠΠ°ΡΡΠ΅Π½Π½ΡΠΉ / ΠΏΠ°Π½Π΅Π»ΡΠ½ΡΠΉ | |
ΠΡΠΈΠΌΠ΅Π½Π΅Π½ΠΈΠ΅ | ΡΠ½Π΅ΡΠ³Π΅ΡΠΈΠΊΠ°, Ρ ΠΈΠΌΠΈΡ, ΠΌΠ΅ΡΠ°Π»Π», ΡΠ°ΡΠΌΠ°ΡΠΈΡ, ΠΏΠΈΡΠ΅Π²Π°Ρ, ΠΏΠΈΡΡΠ΅Π²Π°Ρ, Π±ΠΈΠΎΡ ΠΈΠΌΠΈΡ | Ρ ΠΈΠΌΠΈΡΠ΅ΡΠΊΠ°Ρ, ΠΏΠΈΡΡΠ΅Π²Π°Ρ |
ΠΡΠ½ΠΎΠ²Π½ΡΠ΅ ΠΏΠ°ΡΠ°ΠΌΠ΅ΡΡΡ ΡΠ»Π΅ΠΊΡΡΠΎΠ΄Π° DOG-208F / FA
ΠΠΎΠ΄Π΅Π»Ρ | DOG-208F | DOG-208FA |
ΠΠΈΠ°ΠΏΠ°Π·ΠΎΠ½ | 0 ~ 100 ΠΌΠΊΠ³ / Π»; 0 ~ 20 ΠΌΠ³ / Π» | |
Π’Π΅ΠΌΠΏΠ΅ΡΠ°ΡΡΡΠ° | 0 ~ 60 Β° C | 0 ~ 130 Β° C |
ΠΡΠ΅ΠΌΡ ΠΏΠΎΠ»ΡΡΠΈΠ·Π°ΡΠΈΠΈ | 8 ΡΠ°ΡΠΎΠ² | |
ΠΠ°ΠΏΡΡΠΆΠ΅Π½ΠΈΠ΅ ΠΏΠΎΠ»ΡΡΠΈΠ·Π°ΡΠΈΠΈ | 0.7V | |
Π’ΠΎΡΠ½ΠΎΡΡΡ | β / + 1ppb | + 0,1ppb |
ΠΡΠ΅ΠΉΡ | <3% / ΠΌΠ΅ΡΡΡ | |
ΠΡΠ»Π΅Π²ΠΎΠΉ ΠΊΠΈΡΠ»ΠΎΡΠΎΠ΄ | <5ppb (60 ΠΌΠΈΠ½) | |
ΠΠ°ΡΠΎΠ΄ / Π°Π½ΠΎΠ΄ | ΠΠ»Π°ΡΠΈΠ½Π° / Ag / AgCL | |
ΠΠ΅ΠΌΠ±ΡΠ°Π½Π° | ΠΡΠΎΠ½ΠΈΡΠ°Π΅ΠΌΠΎΡΡΡ ΡΠΈΠ»ΠΈΠΊΠΎΠ½ΠΎΠ²ΠΎΠΉ ΡΠ΅Π·ΠΈΠ½Ρ | |
ΠΠ°ΡΠ΅ΡΠΈΠ°Π» ΠΊΠΎΡΠΏΡΡΠ° | ΠΠ΅ΡΠΆΠ°Π²Π΅ΡΡΠ°Ρ ΡΡΠ°Π»Ρ SS316L | |
ΠΠΎΠ·Π΄ΡΡΠ½ΡΠΉ ΠΏΠΎΡΠΎΠΊ | 50 ~ 80 Π½Π (ΠΌΠ°ΠΊΡ .: 20 ~ 25 ΠΌΠΊΠ) | 60 Π½Π |
Π’Π΅ΠΌΠΏΠ΅ΡΠ°ΡΡΡΠ½Π°Ρ ΠΊΠΎΠΌΠΏΠ΅Π½ΡΠ°ΡΠΈΡ | PT100 / PT1000 / 22K / 2.252Π | PT1000 / 22K ΠΈ Π΄Ρ. |
ΠΠ»Π΅ΠΊΡΡΠΎΠ»ΠΈΡ | KCL | |
ΠΠ°Π»ΠΈΠ±ΡΠΎΠ²ΠΊΠ° | 60 Π΄Π½Π΅ΠΉ | |
ΠΠ°Π±Π΅Π»Ρ | 5 ΠΌ / 10 ΠΌ / 20 ΠΌ |
ΠΡΠ½ΠΎΠ²Π½ΡΠ΅ ΠΏΠ°ΡΠ°ΠΌΠ΅ΡΡΡ ΡΠ»Π΅ΠΊΡΡΠΎΠ΄Π° DOG-209F / FA
ΠΠΎΠ΄Π΅Π»Ρ | DOG-209F | DOG-209FA |
ΠΠΈΠ°ΠΏΠ°Π·ΠΎΠ½ | 0 ~ 20 ΠΌΠ³ / Π» | |
Π’Π΅ΠΌΠΏΠ΅ΡΠ°ΡΡΡΠ° | 0 ~ 60C | |
ΠΡΠ΅ΠΌΡ ΠΏΠΎΠ»ΡΡΠΈΠ·Π°ΡΠΈΠΈ | 6 ΡΠ°ΡΠΎΠ² | |
ΠΠΎΠ»ΡΡΠΈΠ·Π°ΡΠΈΡ Π½Π°ΠΏΡΡΠΆΠ΅Π½ΠΈΠ΅ | 0.7V | |
Π’ΠΎΡΠ½ΠΎΡΡΡ | <- / + 0,01 ΠΌΠ³ / Π» | |
ΠΡΠ΅ΠΉΡ | <2% / ΠΌΠ΅ΡΡΡ | |
ΠΠΈΠ½. ΠΠ½Π°ΡΠ΅Π½ΠΈΠ΅ ΠΈΠ·ΠΌΠ΅ΡΠ΅Π½ΠΈΡ | <0,1 ΠΌΠ³ / Π» | |
Π’ΠΎΠ½ΠΊΠ°Ρ ΠΌΠ΅ΠΌΠ±ΡΠ°Π½Π° | 50 ΠΌΠΊΠΌ | 100 ΠΌΠΊΠΌ |
ΠΠ°ΡΠ΅ΡΠΈΠ°Π» ΠΊΠΎΡΠΏΡΡΠ° | SS316L / PVC | |
Π’ΠΎΠΊ Π² Π²ΠΎΠ·Π΄ΡΡ Π΅ | 50 ~ 80 Π½Π / 0,1ppm (ΠΌΠ°ΠΊΡ. 3,5 ΠΌΠΊΠ) | |
Π’Π΅ΠΌΠΏΠ΅ΡΠ°ΡΡΡΠ½Π°Ρ ΠΊΠΎΠΌΠΏΠ΅Π½ΡΠ°ΡΠΈΡ | Pt100 / Pt1000 / 22K / 2 ,252K | |
ΠΡΠ΅ΠΌΡ ΠΊΠ°Π»ΠΈΠ±ΡΠΎΠ²ΠΊΠΈ | 90 Π΄Π½Π΅ΠΉ | |
ΠΠ°Π±Π΅Π»Ρ | ΡΡΠ°Π½Π΄Π°ΡΡΠ½ΡΠΉ 5 ΠΌΠ΅ΡΡΠΎΠ² (ΠΈΠ½Π΄ΠΈΠ²ΠΈΠ΄ΡΠ°Π»ΡΠ½ΠΎ) |
ΠΡΠ½ΠΎΠ²Π½ΡΠ΅ ΠΏΠ°ΡΠ°ΠΌΠ΅ΡΡΡ ΡΠ»Π΅ΠΊΡΡΠΎΠ΄Π° DOG-209FYAF / DH-485-DO
ΠΠΎΠ΄Π΅Π»Ρ | DOG-209FYA | BH-485-DO |
ΠΠΈΠ°ΠΏΠ°Π·ΠΎΠ½ | 0 ~ 20 ΠΌΠ³ / Π» | |
Π’ΠΎΡΠ½ΠΎΡΡΡ | DO: 0,1 ΠΌΠ³ / Π», ΡΠ΅ΠΌΠΏΠ΅ΡΠ°ΡΡΡΠ°: 0,2 Β° C, Π½Π°ΡΡΡ.%: 1 % | DO0,3 ΠΌΠ³ / Π», ΡΠ΅ΠΌΠΏ: 0.5C |
ΠΡΠΊΠ»ΠΈΠΊ | ΠΡ 30 Π΄ΠΎ 90%, ΠΎΡ 60 Π΄ΠΎ 100% | ΠΠ΅Π½Π΅Π΅ 60 S |
ΠΡΡ ΠΎΠ΄ | 4-20 ΠΌΠ | RS485 Modbus RTU |
ΠΠΈΡΠ°Π½ΠΈΠ΅ | 24 Π ΠΏΠΎΡΡΠΎΡΠ½Π½ΠΎΠ³ΠΎ ΡΠΎΠΊΠ° | |
ΠΠ°Π±Π΅Π»Ρ | ΡΡΠ°Π½Π΄Π°ΡΡΠ½ΡΠΉ 5 ΠΌΠ΅ΡΡΠΎΠ² (ΡΠ΄Π»ΠΈΠ½Π΅Π½ΠΈΠ΅ ΠΏΠΎ ΠΈΠ½Π΄ΠΈΠ²ΠΈΠ΄ΡΠ°Π»ΡΠ½ΠΎΠΌΡ Π·Π°ΠΊΠ°Π·Ρ) | |
Π₯Π°ΡΠ°ΠΊΡΠ΅ΡΠΈΡΡΠΈΠΊΠΈ | CPVC (ΠΠΠ₯) ΠΈΠ»ΠΈ SS316 ΡΠΎ ΡΠΌΠ΅Π½Π½ΠΎΠΉ ΠΌΠ΅ΠΌΠ±ΡΠ°Π½ΠΎΠΉ, IP68,4-20 ΠΌΠ, ΡΡΠ΅ΠΊΠ΅ΡΠ½ΡΠΉ ΡΠ°Π·ΡΠ΅ΠΌ M9 | ΠΠ°ΡΠ΅ΡΠΈΠ°Π» ABS, Π‘ΡΠ°Π½Π΄Π°ΡΡΠ½ΡΠΉ RS485 modbus RTU |
Π£ΡΡΠ°Π½ΠΎΠ²ΠΊΠ°
ΠΡΠΈΠΌΠ΅Π½Π΅Π½ΠΈΠ΅: ΠΌΠΎΡΡΠΊΠΎΠ΅ Ρ ΠΎΠ·ΡΠΉΡΡΠ²ΠΎ, ΠΌΠΎΠ½ΠΈΡΠΎΡΠΈΠ½Π³ ΡΠ°ΡΡΠ²ΠΎΡΠ΅Π½Π½ΠΎΠ³ΠΎ ΠΊΠΈΡΠ»ΠΎΡΠΎΠ΄Π° Π½Π° ΡΠ»Π΅ΠΊΡΡΠΎΡΡΠ°Π½ΡΠΈΡΡ , ΠΎΡΠΈΡΡΠΊΠ° ΡΡΠΎΡΠ½ΡΡ Π²ΠΎΠ΄, ΠΏΠΎΠ»ΡΠΏΡΠΎΠ²ΠΎΠ΄Π½ΠΈΠΊΠΈ ΠΈ ΠΌΠΈΠΊΡΠΎΡΠ»Π΅ΠΊΡΡΠΎΠ½ΠΈΠΊΠ°, Π±ΠΈΠΎΡ ΠΈΠΌΠΈΡ ΠΈ ΡΠ°ΡΠΌΠ°ΡΠ΅Π²ΡΠΈΠΊΠ°, ΡΠ»Π΅ΠΊΡΡΠΈΡΠ΅ΡΡΠ²ΠΎ ΠΈ ΠΏΠ°Ρ, ΠΏΡΠΎΠ΄ΡΠΊΡΡ ΠΏΠΈΡΠ°Π½ΠΈΡ ΠΈ Π½Π°ΠΏΠΈΡΠΊΠΈ, ΡΠΈΡΡΠ°Ρ Π²ΠΎΠ΄Π° ΠΈ Ρ. Π.
Π‘Π΅ΡΡΠΈΡΠΈΠΊΠ°ΡΡ
ΠΠΎΠΌΠΏΠ°Π½ΠΈΡ BOQU ΠΎΡΠ½ΠΎΠ²Π°Π½Π° Ρ 2007 Π³ΠΎΠ΄Π°, Π² Π½Π°ΡΡΠΎΡΡΠ΅Π΅ Π²ΡΠ΅ΠΌΡ Π² Π½Π΅ΠΉ ΡΠ°Π±ΠΎΡΠ°Π΅Ρ Π±ΠΎΠ»Π΅Π΅ 70 ΡΠΎΡΡΡΠ΄Π½ΠΈΠΊΠΎΠ² ΠΈ ΠΈΠ½ΠΆΠ΅Π½Π΅ΡΠΎΠ² , ΠΈΠ½ΡΡΡΡΠΌΠ΅Π½ΡΡ ΠΈΠ΄ΡΡ Π½Π° ΡΠΊΡΠΏΠΎΡΡ Π·Π°ΡΠ΅Π³ΠΈΡΡΡΠΈΡΠΎΠ²Π°Π½ΠΎ Π±ΠΎΠ»Π΅Π΅ ΡΠ΅ΠΌ Π² 75 ΡΡΡΠ°Π½Π°Ρ ., ΡΠ΅ΠΏΠ΅ΡΡ BOQU Π½Π°Π·Π²Π°Π½ High-Tech Enterprise ΠΏΡΠ°Π²ΠΈΡΠ΅Π»ΡΡΡΠ²ΠΎΠΌ , ISO, CE, SGS β ΡΡΠΎ Π½Π°ΡΠΈ ΠΎΠ±ΡΠΈΠ΅ ΡΠ΅ΡΡΠΈΡΠΈΠΊΠ°ΡΡ. ΠΎΡΠ½ΠΎΠ²Π½Π°Ρ ΡΠ΅Ρ Π½ΠΎΠ»ΠΎΠ³ΠΈΡ ΡΠ»Π΅ΠΊΡΡΠΎΠ΄Π°, ΠΊΠΎΠ½ΡΡΠΎΠ»Π»Π΅ΡΠ° ΠΈ 5 0+ ΠΏΡΠΎΠ³ΡΠ°ΠΌΠΌΠ½ΠΎΠ³ΠΎ ΠΎΠ±Π΅ΡΠΏΠ΅ΡΠ΅Π½ΠΈΡ ΡΠΎΠ±ΡΡΠ²Π΅Π½Π½ΠΎΡΡΠΈ ΡΠ²Π»ΡΠ΅ΡΡΡ Π½Π°ΡΠ΅ΠΉ Π±Π°Π·ΠΎΠΉ. Π²ΡΠ΅ ΠΏΡΠΈΠ±ΠΎΡΡ Π±ΡΠ»ΠΈ ΠΏΡΠΈΠ·Π½Π°Π½Ρ ΠΠ°ΡΠΈΠΎΠ½Π°Π»ΡΠ½ΡΠΌ ΠΌΠ΅ΡΡΠΎΠ»ΠΎΠ³ΠΈΡΠ΅ΡΠΊΠΈΠΌ Π±ΡΡΠΎ . Π ΠΠΈΡΠ°Π΅ ΠΌΠ½ΠΎΠ³ΠΎ Π½Π΅Π±ΠΎΠ»ΡΡΠΈΡ Π·Π°Π²ΠΎΠ΄ΠΎΠ², Π²Π°ΠΌ ΡΠ»Π΅Π΄ΡΠ΅Ρ Π±ΡΡΡ ΠΎΡΡΠΎΡΠΎΠΆΠ½ΡΠΌΠΈ, Π΅ΡΠ»ΠΈ ΠΎΠ½ΠΈ ΠΏΡΠ΅Π΄Π»Π°Π³Π°ΡΡ Π²Π°ΠΌ ΠΎΡΠ΅Π½Ρ Π½ΠΈΠ·ΠΊΡΡ ΡΠ΅Π½Ρ. ΡΡΠΎ ΡΠΎΠ²Π΅ΡΡ Π΄Π»Ρ Π²Π°Ρ Π±Π΅ΡΠΏΠ»Π°ΡΠ½ΠΎ.
ΠΠ°Π²ΠΎΠ΄ΡΠΊΠ°Ρ Π²ΡΡΡΠ°Π²ΠΊΠ°
BOQU Instrument Π±ΡΠ»Π° ΠΎΡΠ½ΠΎΠ²Π°Π½Π° Ρ 2007 Π³ΠΎΠ΄Π°, ΡΠ΅ΠΉΡΠ°Ρ BOQU Π½Π°ΡΡΠΈΡΡΠ²Π°Π΅Ρ Π±ΠΎΠ»Π΅Π΅ 70 ΡΠΎΡΡΡΠ΄Π½ΠΈΠΊΠΎΠ² ΠΈ ΠΈΠ½ΠΆΠ΅Π½Π΅ΡΠΎΠ² ΠΈ ΠΈΠΌΠ΅Π΅Ρ ΠΎΡΠ½ΠΎΠ²Π½ΡΡ ΡΠ΅Ρ Π½ΠΎΠ»ΠΎΠ³ΠΈΠΉ ΡΠ»Π΅ΠΊΡΡΠΎΠ΄ΠΎΠ² ΠΈ ΡΠ°ΠΌΠΎΡΡΠΎΡΡΠ΅Π»ΡΠ½ΠΎ ΡΠ°Π·ΡΠ°Π±Π°ΡΡΠ²Π°Π΅Ρ Π±ΠΎΠ»Π΅Π΅ 50+ ΠΏΡΠΎΠ³ΡΠ°ΠΌΠΌΠ½ΠΎΠ³ΠΎ ΠΎΠ±Π΅ΡΠΏΠ΅ΡΠ΅Π½ΠΈΡ Π΄Π»Ρ ΡΠ°Π·Π»ΠΈΡΠ½ΡΡ ΠΊΠΎΠ½ΡΡΠΎΠ»Π»Π΅ΡΠΎΠ².
ΠΡΡΡΠ°Π²ΠΊΠΈ
BOQU ΠΈΠΌΠ΅Π΅Ρ ΡΠΈΠ»ΡΠ½ΡΠΉ ΠΎΡΠ΄Π΅Π» ΡΠ°Π·ΡΠ°Π±ΠΎΡΠΎΠΊ ΠΈ ΠΌΠΎΠΆΠ΅Ρ ΡΠ°Π·ΡΠ°Π±Π°ΡΡΠ²Π°ΡΡ ΠΌΠ½ΠΎΠΆΠ΅ΡΡΠ²ΠΎ Π½ΠΎΠ²ΡΡ ΠΈΠ½ΡΡΡΡΠΌΠ΅Π½ΡΠΎΠ² ΠΈΠ»ΠΈ ΡΠ΅Ρ Π½ΠΎΠ»ΠΎΠ³ΠΈΠΉ, ΠΏΠΎΡΡΠΎΠΌΡ ΠΌΡ ΠΏΡΠΎΠ²Π΅Π΄Π΅ΠΌ 5-8 Π²ΡΡΡΠ°Π²ΠΎΠΊ Π² ΠΠΈΡΠ°Π΅ ΠΈΠ»ΠΈ Π·Π° ΡΡΠ±Π΅ΠΆΠΎΠΌ, ΡΡΠΎΠ±Ρ ΠΏΡΠΎΠ΄Π΅ΠΌΠΎΠ½ΡΡΡΠΈΡΠΎΠ²Π°ΡΡ Π½Π°ΡΠΈ ΡΠ΅Π·ΡΠ»ΡΡΠ°ΡΡ.
,