Конвертерное производство
Около 70% стали от общего объема мирового производства изготавливается конвертерным способом. До середины прошлого столетия для получения стали применялись бессемеровский и томасовский процессы. Однако в дальнейшем сталь начали производить усовершенствованным кислородно-конвертерным способом. В настоящее время предшественники современного метода практически не применяются.
Блок: 1/6 | Кол-во символов: 376
Источник: https://promzn.ru/obrabotka-metalla/kislorodno-konvertornoe-proizvodstvo-stali.html
Суть конвертерного производства
В конвертерном производстве применяются специальные сталеплавильные агрегаты, называемые конвертерами. Производство стали осуществляется путем продувки жидкого чугуна воздухом или кислородом. Данный металл содержит различные примеси, в том числе кремний, углерод и марганец. Примеси окисляются под действием кислорода и удаляются из расплава. Основным преимуществом конвертерного способа является то, что для работы сталеплавильного устройства не требуется топливо.
Блок: 2/6 | Кол-во символов: 576
Источник: https://promzn.ru/obrabotka-metalla/kislorodno-konvertornoe-proizvodstvo-stali.html
Конструкция конвертера
Оборудование представляет собой грушевидный сосуд, обеспеченный внутренней футеровкой и леткой для выпуска продуктов плавки. В верхней части конструкции предусмотрено отверстие с горловиной для подачи фурмы, лома, расплавленного чугуна, легирующих смесей и отвода газа. Тоннаж варьируется от 50 до 400 т. В качестве материалов для изготовления конструкции применяется листовая или сварная сталь средней толщиной порядка 50-70 мм. Типовое устройство кислородного конвертера предусматривает возможность отсоединения днища – это модификации с донной продувкой газо-воздушными смесями. Среди вспомогательных и функциональных элементов агрегата можно выделить электродвигатель, трубопроводную инфраструктуру для циркуляции потоков кислорода, опорные подшипники, демпферную платформу и опорную станину для монтажа конструкции.
Блок: 2/11 | Кол-во символов: 845
Источник: https://autogear.ru/article/410/705/kislorodnyiy-konverter-ustroystvo-i-tehnologiya-vyiplavki-stali/
Автоматизация конвертерного процесса
С точки зрения автоматического управления в конвертерном производстве выделяют следующие величины:
- Основные выходные (управляемые) величины: масса металла в процессе и в конце продувки, концентрация углерода, фосфора и серы в ванне в процессе и в конце продувки, температура металла в процессе и в конце продувки.
- Дополнительные выходные величины: масса шлака, температура шлака, температура конвертерных газов, количество конвертерных газов, состав шлака, состав конвертерных газов.
- Входные управляющие величины: масса чугуна, масса стального лома, масса руды в каждой порции, масса извести, масса известняка, время ввода в конвертер сыпучих материалов, расход кислорода, расстояние между кислородной фурмой и уровнем спокойной ванны, продолжительность продувки.
- Контролируемые возмущающие воздействия: содержание в чугуне кремния, марганца, серы, фосфора, температура чугуна, содержание кислорода в дутье, интервал времени между плавками.
- Неконтролируемые возмущающие воздействия: содержание углерода в чугуне, состав сыпучих материалов, размеры и температура лома, масса и состав попадающего в конвертер миксерного шлака.
Блок: 3/5 | Кол-во символов: 1162
Источник: https://ru.wikipedia.org/wiki/%D0%9A%D0%BE%D0%BD%D0%B2%D0%B5%D1%80%D1%82%D0%B5%D1%80%D0%BD%D0%BE%D0%B5_%D0%BF%D1%80%D0%BE%D0%B8%D0%B7%D0%B2%D0%BE%D0%B4%D1%81%D1%82%D0%B2%D0%BE
Опорные кольца и цапфа
Конвертер располагается на роликовых подшипниках, которые фиксируются на станине. Конструкция может быть и стационарной, но это встречается редко. Обычно на этапах проектирования определяется возможность транспортировки или перемещения агрегата в тех или иных условиях. Именно за эти функции отвечает оснастка в виде опорных колец и цапфы. Группа подшипников обеспечивает возможность кручения оборудования вокруг оси цапф. Прежние модели конвертеров предполагали совмещение несущей оснастки и корпуса плавильного оборудования, но из-за воздействия высоких температур и деформации вспомогательных материалов это конструкционное решение было заменено более сложной, но надежной и долговечной схемой взаимодействия функционального блока и емкости.
Современный кислородный конвертер, в частности, обеспечивается отдельным опорным кольцом, в структуру которого также вводятся цапфы и закрепленный кожух. Технологический промежуток между кожухом и опорной базой предотвращает негативное температурное воздействие на чувствительные элементы подвесок и передвижных механизмов. Непосредственно система фиксации конвертера реализуется за счет упоров. Само же опорное кольцо представляет собой несущее устройство, сформированное двумя полукольцами и цапфовыми плитами, закрепленными в узлах стыковки.
Блок: 3/11 | Кол-во символов: 1314
Источник: https://autogear. ru/article/410/705/kislorodnyiy-konverter-ustroystvo-i-tehnologiya-vyiplavki-stali/
Принцип работы кислородного конвертера
Впервые кислородное дутье было запатентовано Г. Бессемером. Однако в течение продолжительного времени кислородно-конвертерный процесс не применялся, в связи с отсутствием массового производства кислорода. Первые опыты по продувке кислородом стали возможными в начале сороковых годов прошлого столетия.
Устройство кислородного конвертера осталось прежним:
- камера сгорания изнутри защищена основной футеровкой;
- однако вместо воздуха в нем применяется продувка кислородом;
- подача кислорода осуществляется через водоохлаждаемые сопла.
На территории России применяются сталеплавители с верхней подачей кислорода.
Особенностью конвертерного способа с кислородной продувкой является скоротечность. Весь процесс расплавления металла занимает десятки минут. Однако во время работы требуется тщательно отслеживать содержание в чугуне углерода, температуры его расплава и прочие параметры, чтобы вовремя прекратить продувку.
Процесс сталеплавильного производства упростился, когда кислородные конвертеры оснастили автоматическими системами, усовершенствовали лабораторную технику и измерительные приборы. Усовершенствование кислородно-конвертерного процесса позволило повысить производительность, снизить себестоимость металла и повысить его качество.
Современные кислородные конвертеры могут работать в трех основных режимах:
- с полным дожиганием окиси углерода;
- с частичным дожиганием ОС;
- без дожигания ОС.
Схема получения стали в кислородном конвертере
Они позволяют производить сталь из чугуна различного состава.
Блок: 5/6 | Кол-во символов: 1530
Источник: https://promzn.ru/obrabotka-metalla/kislorodno-konvertornoe-proizvodstvo-stali.html
Поворотный механизм
Электропривод обеспечивает возможность поворота конвертера на 360°. Средняя скорость вращения составляет 0,1-1 м/мин. Сама по себе эта функция требуется не всегда – в зависимости от организации технологических операций в ходе рабочего процесса.
Блок: 4/11 | Кол-во символов: 1259
Источник: https://autogear. ru/article/410/705/kislorodnyiy-konverter-ustroystvo-i-tehnologiya-vyiplavki-stali/
Примечания
Эта страница в последний раз была отредактирована 25 августа 2019 в 19:15.
Блок: 5/5 | Кол-во символов: 181
Источник: https://wiki2.org/ru/%D0%9A%D0%BE%D0%BD%D0%B2%D0%B5%D1%80%D1%82%D0%B5%D1%80%D0%BD%D0%BE%D0%B5_%D0%BF%D1%80%D0%BE%D0%B8%D0%B7%D0%B2%D0%BE%D0%B4%D1%81%D1%82%D0%B2%D0%BE
Размеры конвертера
В ходе проектирования параметры конструкции должны рассчитываться исходя из того, какой примерный объем продувки без учета выброса расплава будет производиться. В последние годы разрабатываются агрегаты, принимающие материалы в объеме от 1 до 0,85 м3/т. Также рассчитывается уклон горловины, угол которого в среднем составляет от 20° до 35°. Однако практика эксплуатации таких сооружений показывает, что превышение наклона в 26° ухудшает качество футеровки. По глубине размеры конвертера составляют 1-2 м, но по мере увеличения емкости загрузки и высота конструкции может увеличиваться.
Блок: 5/11 | Кол-во символов: 783
Источник: https://autogear.ru/article/410/705/kislorodnyiy-konverter-ustroystvo-i-tehnologiya-vyiplavki-stali/
Кислородный конвертер – описание процесса плавки
Кислородный конвертер – это стальной сосуд грушевидной формы. Его внутренняя часть защищена смолодоломитовым (основным) кирпичом. Вместимость сталеплавильного агрегата варьируется от 50 до 350 тонн. Сосуд распложен на цапфах и способен поворачиваться вокруг горизонтальной оси, что позволяет беспрепятственно заливать в него чугун, закладывать другие добавки и сливать металл со шлаком.
Чтобы получить конечный продукт, в конвертер заливается не только чугун, но и закладывают добавки. К ним относятся:
- лом металла;
- шлакообразующие материалы (железная руда, известь, полевой шпат, бокситы).
Конвертерный способ с кислородной продувкой предусматривает заливку в конвертер чугуна, нагретого до 1250–1400°С. Установив конвертер в вертикальное положение, в него подают кислород. Как только началась продувка, в расплавленный чугун вводят остальные компоненты, входящие в состав шлака. Перемешивание чугуна со шлаком осуществляется под действием продувки.
Так как концентрация чугуна гораздо выше, чем примесей, в процессе продувки происходит образование оксида железа, который растворяясь, обогащает металл кислородом. Именно растворенный кислород способствует уменьшению в металле концентрации кремния, углерода и марганца. А когда примеси окисляются, выделяется полезное тепло.
Особенностью основного шлака является большое содержание оксида кальция и оксида железа, которые в начале продувки способствуют удалению фосфора. Если же содержание фосфора превышает требуемый показатель, шлак сливают и наводят новый. Продувку кислородом заканчивают, когда содержание углерода в конечном продукте соответствует определенному параметру. После этого конвертер переворачивают и производят слив стали в ковш, куда добавляют раскислители и другие добавки.
Видео по теме: Основы кислородно конвертерного производства
Блок: 6/6 | Кол-во символов: 1845
Источник: https://promzn.ru/obrabotka-metalla/kislorodno-konvertornoe-proizvodstvo-stali.html
Футеровка кислородного конвертера
Обязательная технологическая процедура, в ходе которой внутренние стены конвертера обеспечиваются защитным слоем. При этом надо учитывать, что в отличие от большинства металлургических печей данная конструкция подвергается гораздо более высоким термическим нагрузкам, что обуславливает и особенности выполнения футеровка. Это процедура, предполагающая укладку двух защитных слоев – функционального и армирующего. Непосредственно к поверхности корпуса примыкает пласт защитной арматуры толщиной 100-250 мм. Его задача заключается в снижении теплопотерь и недопущении прогара верхнего слоя. В качестве материала применяется магнезитовый или магнезитохромитовый кирпич, который может служить годами без обновления.
Верхний рабочий слой имеет толщину порядка 500-700 мм и заменяется довольно часто по мере износа. На этом этапе кислородный конвертер обрабатывается безобжиговыми песко- или смоловязанными огнеупорными составами. Основу материала для этого слоя футеровки составляет доломит с добавками магнезита. Стандартный расчет по нагрузке делается исходя из температурного воздействия порядка 100-500 °С.
Блок: 6/11 | Кол-во символов: 1140
Источник: https://autogear.ru/article/410/705/kislorodnyiy-konverter-ustroystvo-i-tehnologiya-vyiplavki-stali/
Торкретирование футеровки
Под агрессивными температурно-химическими воздействиями внутренние поверхности конструкции конвертера быстро утрачивают свои качества – опять же, это касается внешнего износа рабочего слоя термической защиты. В качестве ремонтной операции применяется торкретирование футеровки. Это технология горячего восстановления, при которой с помощью специального оборудования укладывается огнеупорный состав. Его наносят не сплошным способом, а точечно на сильно изношенные участки базовой футеровки. Процедура выполняется на специальных торкрет-машинах, подающих к поврежденному участку водоохлаждаемую фурму с массой из коксовой пыли и магнезитового порошка.
Блок: 7/11 | Кол-во символов: 678
Источник: https://autogear.ru/article/410/705/kislorodnyiy-konverter-ustroystvo-i-tehnologiya-vyiplavki-stali/
Технологии выплавки
Традиционно выделяют два подхода к реализации кислородно-конвертерного плавления – бессемеровский и томасовский. Однако современные методики отличаются от них низким содержанием азота в печи, что повышает качество рабочего процесса. Выполняется технология по следующим этапам:
- Загрузка лома. Порядка 25-27 % от общей массы шихты загружается в наклоненный конвертер посредством совков.
- Заливка чугуна или стального сплава. Жидкий металл при температуре до 1450 °С ковшами заливается в наклоненный конвертер. Операция продолжается не более 3 мин.
- Продувка. В этой части технология выплавки стали в кислородных конвертерах допускает разные подходы в плане подачи газо-воздушной смеси. Поток может направляться сверху, снизу, донным и комбинированным способами в зависимости от типа конструкции оборудования.
- Получение проб. Выполняется замер температуры, удаляются ненужные примеси, ожидается анализ состава. Если его результаты соответствуют проектным требованиям, плавка выпускается, а если нет – вносятся корректировки.
Блок: 8/11 | Кол-во символов: 1041
Источник: https://autogear.ru/article/410/705/kislorodnyiy-konverter-ustroystvo-i-tehnologiya-vyiplavki-stali/
Плюсы и минусы технологии
Способ ценится за высокую производительность, простые схемы подачи кислорода, конструкционную надежность и относительно низкие расходы в целом на организацию процесса. Что касается недостатков, то к ним, в частности, относятся ограничения в плане добавления шлама и вторсырья. Тот же лом металла с другими включениями может составлять не более 10 %, а это не позволяет в нужной степени модифицировать структуру выплавки. Также при выдувке расходуется большой объем полезного железа.
Блок: 9/11 | Кол-во символов: 509
Источник: https://autogear.ru/article/410/705/kislorodnyiy-konverter-ustroystvo-i-tehnologiya-vyiplavki-stali/
Применение технологии
Сочетание плюсов и минусов в итоге обусловило и характер применения конвертеров. В частности, металлургические комбинаты выпускают низколегированную, углеродистую и легированную сталь высокого качества, достаточного для применения материала в тяжелой промышленности и строительстве. Получение сталей в кислородном конвертере происходит с легированием и улучшением отдельных свойств, что расширяет сферы применения конечной продукции. Из получаемого сырья изготавливают трубы, проволоку, рельсы, метизы, скобяные изделия и т. д. Технология широко применяется и в цветной металлургии, где при достаточной продувке получают черновую медь.
Блок: 10/11 | Кол-во символов: 659
Источник: https://autogear.ru/article/410/705/kislorodnyiy-konverter-ustroystvo-i-tehnologiya-vyiplavki-stali/
Заключение
Плавка в конвертерных сооружениях считается морально устаревшей техникой, но ее продолжают использовать по причинам оптимального сочетания производительности и финансовых затрат на обеспечение процесса. В немалой степени востребованности технологии способствуют и конструкционные достоинства применяемого оборудования. Та же возможность прямой загрузки лома металла, шихты, шлама и других отходов, хоть и в ограниченном объеме, расширяет возможности для модификации сплава. Другое дело, что для полноценной эксплуатации крупногабаритных конвертеров с возможностями поворота требуется организация соответствующего помещения на предприятии. Поэтому осуществляют выплавку с кислородной продувкой в больших объемах преимущественно крупные компании.
Блок: 11/11 | Кол-во символов: 755
Источник: https://autogear.ru/article/410/705/kislorodnyiy-konverter-ustroystvo-i-tehnologiya-vyiplavki-stali/
Количество использованных доноров: 4
Информация по каждому донору:
- https://promzn.ru/obrabotka-metalla/kislorodno-konvertornoe-proizvodstvo-stali.html: использовано 4 блоков из 6, кол-во символов 4327 (30%)
- https://ru.wikipedia.org/wiki/%D0%9A%D0%BE%D0%BD%D0%B2%D0%B5%D1%80%D1%82%D0%B5%D1%80%D0%BD%D0%BE%D0%B5_%D0%BF%D1%80%D0%BE%D0%B8%D0%B7%D0%B2%D0%BE%D0%B4%D1%81%D1%82%D0%B2%D0%BE: использовано 1 блоков из 5, кол-во символов 1162 (8%)
- https://wiki2.org/ru/%D0%9A%D0%BE%D0%BD%D0%B2%D0%B5%D1%80%D1%82%D0%B5%D1%80%D0%BD%D0%BE%D0%B5_%D0%BF%D1%80%D0%BE%D0%B8%D0%B7%D0%B2%D0%BE%D0%B4%D1%81%D1%82%D0%B2%D0%BE: использовано 1 блоков из 5, кол-во символов 181 (1%)
- https://autogear.ru/article/410/705/kislorodnyiy-konverter-ustroystvo-i-tehnologiya-vyiplavki-stali/: использовано 10 блоков из 11, кол-во символов 8983 (61%)
Кислородные конвертеры – Справочник химика 21
РеО) = (8Юг) + 2Ге – ДЯ Образовавшиеся при окислении оксиды марганца и кремния переходят в шлак.

Процессы в расплаве являются вариантом газификации угля в режиме уноса. В них уголь и газифицирующий агент подаются на поверхность расплавов металлов, шлаков или солей, которые играют роль теплоносителей. Наиболее перспективен процесс с расплавом железа, поскольку можно использовать имеющиеся в ряде стран свободные мощности кислородных конвертеров в черной металлургии [97]. В данном процессе газогенератором служит полый, футерованный огнеупорным материалом аппарат-конвертер с ванной расплавленного (температура 1400—1600°С) железа. Угольная пыль в смеси с кислородом и водяным паром подается с верха аппарата перпендикулярно поверхности расплава с высокой скоростью. Этот поток как бы сдувает образовавшийся на поверхности расплава шлам и перемешивает расплав, увеличивая поверхность его контакта с углем. Благодаря высокой температуре газификация проходит очень быстро. Степень конверсии углерода достигает 98%, а термический к. п. д. составляет 75— 80%. Предполагается, что железо играет также роль катализатора газификации. При добавлении в расплав извести последняя взаимодействует с серой угля, образуя сульфид кальция, который непрерывно выводится вместе со шлаком. В результате удается освободить синтез-газ от серы, содержащейся в угле, на 95%. Синтез-газ, полученный в процессе с расплавом, содержит 677о (об.) СО и 28% (об.) Нг. Потери железа, которые должны восполняться, составляют 5—15 г/м газа. [c.97]
Технологический процесс. Процесс выплавки стали в кислородном конвертере состоит из нескольких операций, которым соответствует определенное положение конвертера относительно его оси. [c.85]
При выплавке стали в мартеновских печах протекают процессы окисления углерода и примесей в шихте и образования шлаков аналогичные тем, которые идут в кислородном конвертере. Однако мартеновский процесс имеет ряд существенных особенностей. К ним относятся [c.92]
Технологический процесс переработки железной руды, угля, известняка и углеводородных топлив в конечный продукт может быть разбит на 3—4 основные стадии, которые осуществляются раздельно с получением определенного продукта, на следующей стадии перерабатываемого в продукт нового вида. Различные стадии процесса могут проходить в одной технологической установке. Это будет способствовать не только экономии энергии и расходов на транспортировку, но и упрощению технологического процесса. Основные технологические стадии при производстве чугуна и стали следующие подготовка сырья (коксование угля, обжиг известняка, производство железорудного агломерата и окатышей) производство чугуна (доменная выплавка, производство губчатого чугуна за счет прямого восстановления железа) стали (в мартеновских и электродуговых печах, бессемеровских и основных кислородных конвертерах) проката (непрерывное литье заготовок, прокатка сортовой стали, производство труб, поковки).

Огромные масштабы производства и зна.чительное потребление всех видов топлива даже на относительно малых сталеплавильных заводах дают основание полагать, что СНГ при их современных ресурсах вряд ли могут стать основой энергообеспечения металлургической промышленности. Однако то обстоятельство, что основным видом топлива в этой отрасли является кокс, который становится все более дефицитным, создает благоприятные условия для использования дополнительных видов топлива, способных замещать кокс и коксовый газ. Такие условия возникают прежде всего на металлургических заводах неполного цикла. Здесь дополнительные виды топлива можно использовать для подогрева скрапа в электродуговых печах обогащения колошникового доменного газа охлаждения воздушной коробки бессемеровского конвертера замены (полной или частичной) кокса в вагранках нагрева слитков в колодцах перед ковкой или прокаткой ускорения процесса плавления металла в кислородных конвертерах повышения выхода коксового газа при коксовании угля. Помимо этого СНГ может заменить природный газ в других процессах для дополнительной подачи топлива в дутьевые фурмы доменных печей вдувания конвертированных газов в фурменную зону прямого восстановления железной руды газообразными углеводородами. [c.310]
Определить объем заполнения сталью 350-тонно-г(. кислородного конвертера, у которого форма бл зкa к нгаровидной, а внутренний диаметр 8 м. Рассчтать высоту слоя стали в 600-тонной мартеновской печи, если плавильное пространство ее имеет длину 17 м и ширину 7 м. Плотность жидкой стали 7200 кг/м . [c.223]
Основные размеры конвертера — высота рабочего пространства Н, диаметр О, диаметр горловины д, и глубина ванны жидкого металла в спокойном состоянии I (рис. 5.2) — зависят от емкости (мощности) конвертера, которая рассчитывается по массе жидкой стали. В РФ ГОСТом установлен ряд типовых емкостей кислородных конвертеров от 50 до 400 тонн. [c.83]
В табл.
Известняк, применяемый в сталеплавильной промышленности, как правило, должен быть высокого качества. Доля серы в нем не должна превышать 0,15%, так как она имеет тенденцию переходить в готовую сталь, выплавляемую в дуговых электропечах или основных кислородных конвертерах, что, безусловно, сказывается на качестве стали. По этой причине поставщики известняка для [c.303]
Мартеновские печи пригодны для переработки практически любого вида сырья. Однако современная практика сталеварения развивается преимущественно в направлении использования кислородных конвертеров и электродуговых сталеплавильных печен. [c.308]
Использование дополнительного топлива в сталеплавильных процессах (кроме мартеновского) ограничивается потребностью предварительного подогрева скрапа в электродуговых печах н кислородных конвертерах, что облегчает процесс выплавки стали. Для выплавки стали в электродуговых печах или кислородных конвертерах можно использовать только чистое газовое топливо. Известно, что при подаче в воздушное дутье бессемеровского конвертера СНГ повышается стойкость распределительной решетки за счет охлаждения ее этими газами. Впервые конвертер, в котором использовались СНГ, был разработан в Швеции. В настоящее время их эксплуатируют во многих странах (так называемый Кю-БОП-процесс ). [c.308]
Чугун также содержит множество примесей, которые придают ему высокую хрупкость и низкое сопротивление разрыву поэтому чугун находит мало применений. Большую часть чугуна превращают в сталь, причем свыше половины этого количества-в кислородных конвертерах. В кислородно-конвертерном процессе в расплавлен-иое железо добавляют известняк, который образует шлак, содержащий фосфор и кремний. При продувании через расплавленное железо кислорода под высоким давлением в нем выгорают примеси серы и углерода (схема кислородного конвертера показана на рис. 22.18). После этого в железо можно добавлять небольшие контролируемые количества углерода и других веществ в зависимости от того, какой сорт стали требуется получить. Небольшие примеси углерода повышают твердость и прочность стали. [c.359]
Можно ли использовать для рафинирования меди такой же способ, как и для рафинирования железа в кислородном конвертере Можно ли использовать подобный способ для рафинирования магния Поясните свой ответ. [c.368]
Конвертерный способ. В мощ ном современном кислородном конвертере за 30—35 мин получают 350— 400 т жидкой высококачественной стали. Конвертер представляет собой реактор, изготовленный из прочных [c.
Процесс передела чугуна в сталь осуществляется в окислительной среде, например, в кислородном конвертере. Поэтому расплавленный металл неизбежно содержит некоторое количество растворенного кислорода (порядка [c.155]
Кислородные гальванические элементы с твердым электролитом применяются для экспрессных определений концентраций этого элемента в жидкой стали. Они особенно важны для управления выплавкой стали в кислородных конвертерах, в которых все металлургические реакции протекают с большими скоростями. Схема такого элемента имеет вид [c.242]
Вентури должен быть создан перепад давлений, превышающий 12-10 даПа, не снижающийся во всем диапазоне изменения производительности. Известно, что некоторые фирмы для кислородных конвертеров ограничивают снижение перепада давлений на трубе Вентури до 1,5-10 даПа. [c.24]
При замкнутой фазовой траектории или траектории очень близкой к ней в системе могут происходить устойчивые периодические колебания, т. е. в ней возможен помпаж и система газоотводящий тракт — дымосос не всегда будет устойчивой. Это наглядно представлено на рис. 19. Исследование устойчивости системы газоотводящий тракт — дымосос кислородных конвертеров проводилось для обращенных характеристик, но для наглядности рассчитанные фазовые траектории перенесены на обычные характеристики. [c.32]
Сколько 350-ТОННЫХ кислородных конвертеров должно быть установлено на заводе, который оборудован 2 доменными печами с 1Голсзиыми объемами 3200 и 3000 м , если КИПО для первой из них составляет в среднем 0,53, а для второй 0,55, а средняя длительность плавки в конвертере равна соответственно 43 и 60 мин Выход стали составляет 0,93 массовой доли чугуна. [c.223]
В 30-е и 40-е годы в стране были построены Магнитогорский и Кузнецкий металлургические комбинаты. Запорожский и Криворожский заводы, реконструированы Днепропетровский, Макеевский, Нижнеднепровский и Таганрогский заводы, строятся заводы высококачественных сталей Электросталь и Днепроспецсталь . В послевоенные годы в стране продолжается рост производства черных металлов, строятся Новолипецкий, Западно-Сибирский, Череповецкий и другие заводы. В металлургическом производстве начинают применяться кислородные конвертеры емкостью 350 т, 900-тонные мартеновские печи, двухванные сталеплавильные агрегаты, доменные печи с полезным объемом до 5000 м . Одновременно развивается металлургия специальных сталей и сплавов, в производство внедряются методы электрошлакового (ЭШП), вакуумного индукционного (ВИП), вакуумно-ду-гового (ВДП), электронно-лучевого (ЭЛП) и плазменно-дзггового (ПДП) переплава стали. [c.50]
Из трех основных методов производства стали доля мартеновского непрерывно падает, что объясняется его неконкурен-тноспособностью с кислородно-конвертерным и электросталеплавильным методами, обеспечивающими, наряду с получением высококачественных сортов стали, высокую экономичность производства. Так, по данным Кузбасского металлургического комбината за 1990 год переход с мартеновских печей на кислородные конвертеры дал годовую экономию металла 7-10 т, энергии (топлива) 6-10 т и рабочей силы 200 человек. В 1987 году во всех индустриально-развитых странах Европы сталь выплавлялась исключительно в кислородных конвертерах и электрических печах. В США доля мартеновской стали составляла всего около 4%. [c.74]
Устройство конвертетера. Кислородный конвертер является реактором периодического действия РИС-П. Это поворачивающийся на цапфах в вертикальной плоскости стальной сосуд грушевидной формы, имеющий концентрически расположенную горловину для заливки чугуна, завалки твердых компонентов шихты и отвода , – газа. Через горловину вводится в [c.82]
Недостатки мартеновского способа выплавки стали (большие капитальные затраты, низкая по сравнению с кислородноконвертерным способом производительность, затраты на топливо, сложность обслуживания регенераторов вследствие разрушения их насадки) не могут быть полностью компенсированы такими методами интенсификации процесса как повышение давления и обогащение кислородом воздушного дутья и предварительная карбюрация топлива. Это вызвало необходимость изменения уже не технологии, а конструкции мартеновских печей — создания двухванных сталеплавильных агрегатов (рис. 5.5), В основу их действия положен принцип работы кислородного конвертера — окисление углерода и примесей продувкой шихты кислородом. При этом в двухванных печах для нагрева шихты используют часть выделяющегося тепла в виде теплосодержания отходящих газов и теплового эффекта дожигания оксида углерода (П), [c.93]
Конвертер работает периодически. В него загружают металлический лом, заливяют жидкий чугун, после чего опускают фурму, через которую вдувают кислород под давлением в 1 МПа, Кислородные конвертеры бывают с донным и комбинированным продуванием. [c.152]
Получение. Схема металлургич. передела железных руд включает дробление, измельчение, обогащение маги, сепарацией (до содержания Ре 64-68%), получение концентрата (74-83% Ре), плавку осн. массу Ж. выплавляют в виде чугуна и стали (см. Железа сплавы). Технически чистое Ж., или армко-Ж. (0,02% С, 0,035% Мп, 0,14% Сг, 0,02% 8, 0,015% Р), выплавляют из чугуна в сталеплавильных печах или кислородных конвертерах. Чистое Ж. получают восстановлением оксидов Ж. твердым (коксик, кам.-уг. пыль), газообразным (Н2, СО, их смесь, прнр. конвертированный газ) илн комбинир. восстановителем электролизом водных р-ров илн расплавов солей Ж. разложением пентакарбонила Ре(СО)5 (карбонильное Ж.). Сварочное, илн кричное, Ж. производят окислением примесей малоуглеродистой стали железистым шлаком прн 1350°С илн восстановлением из руд твердым углеродом. Восстановлением оксидов Ж. прн 750-1200°С получают губчатое Ж. (97-99% Ре)-пористый агломерат частиц Ж. пирофорно в горячем состоянии поддается обработке давлением. Карбонильное Ж. (до 0,00016% С) получают разложением Ре(СО)5 при 300 °С в среде КНз с послед, восстановит, отжигом в среде Н2 прн 500-600 С, порошок с размером частиц 1-15 мкм перерабатывается методами порошковой металлургии. Особо чистое Ж. получают зонной плавкой и др.
методами. [c.141]
В кислородных конвертерах выплавляют сталь из сырого чугуна, продувая расплав сырья воздухом, обогащенным кислородом или кислородными смесями. При разуглероживании чугуна выделя- [c.92]
Разрабатываются также способы обогащения цветными металлами пылей и шламов с целью их последующей утилизации. В этом плане весьма перспективно обогащение в пирометаллургических агрегатах, традиционно применяемых в черной металлургии (дуговые печи, кислородные конвертеры и т.п.). [c.63]
Компания Кавасаки испьггала способ извлечения цинка, в соответствии с которым пыль в смеси с углем и воздухом инжектируют в кислородный конвертер. Цинк возгоняется и улавливается системой пылеочистки, а железо и силикатная составляющая усваиваются соответственно сталью и шлаком. В 1998 г. предполагалось приступить к сооружению установки, способной переработать всю пыль ДСП Японии ( 500 тыс. т). [c.92]
Интерес к газификации в расплаве железа проявляется также в Великобритании. Так, фирма “Дэви Макки” предлагает использовать в качестве, газогенераторов существующие кислородные конвертеры сталелитейных производств одновремевно это является- переходным этапом к промышленному внедрению процесса. [c.47]
Условия работы дымососов газоотводящих трактов мартеновских печей схожи с уловиями работы дымососов, рассмотренных кислородных конвертеров. В процессе плавки стали выгорают те же компоненты, вводятся те же флюсы, а для интенсификации процесса также подается кислород. Очистка газов осуществляется в аналогичных сооружениях мокрой газоочистки. Электрофильтры применяются редко. Различия этих процессов заключаются в следующем. [c.84]
Конструкция конвертера с кислородным дутьем отличается от обычного конвертера отсутствием воздушного дутья через днище и наличием летки для выпуска стали и шлака (рис. 84). Футеровка кислородных конвертеров выполняется из специального периклазошпинельного или смолодоломитного кирпича. [c. 189]
Для наглядности на рис. 17 показаны обычные и обращенные хараю-еристики дымососа, созданного для газоотводящего тракта кислородного конвертера и сети. На рис. 18 приведены обра-, щенные характеристики дымососа (кривая 1) и сети (кривая 2) 1, равновесным режимом в точке О и показана схема построения. /траектории. [c.31]
Опыт эксплуатации газоочистных сооружений позволяет в настоящее время оценить условия работы дымососов, устанавливаемых в газоотводящих трактах, и в первом прибшше-нии систематизировать предъявляемые к ним требования. Газоочистные соорзгжения применяют в основном после технологических агрегатов, длительно работающих без остановов и отличающихся большой интенсивностью выброса газов, например, за кислородными конвертерами для производства стали, которые не могут эксплуатироваться с отключенными газоочистными сооружениями. В связи с этим надежность работы дымососов приобретает решающее значение. [c.74]
В начале освоения кислородных конвертеров считалось, что производительность дымососа в межпродувочный период должна быть сокращена до 0,2 максимальной, а характеристика дымососа Ру (9) должна быть монотонно падающей. Опыт наладки газоотводящих трактов крупных отечественных конвертеров показал, что для об печения отвода газов без дожигания СО соотношение минимального расхода газа через тракт к максимальному может быть равно примерно 0,6. Сокращение объемов отсасываемого воздуха в межпродувочный период обусловлено экономией электроэнергии. [c.76]
Производство стали в кислородных конвертерах
Производство стали в кислородных конвертерах. Сталь отличается от чугуна меньшим содержанием углерода (до 2,1 %), кремния (до 0,4 %), марганца (до 0,8 %), примесей серы (до 0,04 %) и фосфора (до 0,04 %). Исходными материалами для получения стали являются передельный чугун и стальной лом (скрап). Сутью передела чугуна в сталь является уменьшение содержания углерода и других входящих в чугун элементов. В настоящее время сталь получают преимущественно в кислородных конвертерах, мартеновских и электрических печах. Кислородно-конвертерным и мартеновским способами выплавляют около 80 % всей стали.
Кислородно-конвертерный процесс заключается в продувке жидкого чугуна кислородом. Сталь, полученная этим способом, наиболее дешевая и не уступает по качеству мартеновской. Кислородный конвертер представляет собой стальной сосуд грушевидной формы, внутренняя поверхность которого облицована алюмосиликатным кирпичом (рис. 2.3). Конвертеры изготовляют емкостью на 100—350 т жидкого чугуна. Общий расход технического кислорода на получение 1 т стали составляет 50—60 м3. Перед началом работы конвертер поворачивают на цапфах вокруг горизонтальной оси и с помощью завалочной машины загружают до 30 % объема металлоломом, затем заливают жидкий чугун, нагретый до температуры 1250—1400 °С, возвращают конвертер в исходное вертикальное положение, подают кислород и добавляют шлакообразующие материалы: известь, плавиковый шпат и железную руду, которая ускоряет процесс окисления. При продувке конвертера техническим кислородом углерод и другие примеси окисляются в процессе дутья и благодаря присутствию в руде оксида железа FeO. При этом образуется химически активный шлак с необходимым содержанием окиси кальция СаО, благодаря чему происходит удаление серы. В момент, когда содержание углерода достигает количества, заданного для выплавляемой стали определенной марки, подачу кислорода прекращают, конвертер поворачивают и выливают вначале сталь, а затем шлак.
Рис. 2.3. Кислородный конвертер 1 — горловина для загрузки; 2 — водоохлаждаемая фурма; 3 — выпускное отверстие
Для уменьшения содержания кислорода в стали при выпуске из конвертера ее раскисляют, т. е. вводят в нее элементы с большим, чем у железа, сродством к кислороду — Mn, Si, Al. Взаимодействуя с кислородом и оксидом железа FeO, забирая у него кислород, они образуют нерастворимые оксиды MnО, SiO2, Al2O3, переходящие в шлак:
0,5O2 + Mn = MnO; O2 + Si = SiO2;
1,5O2 + 2Al = Al2O3; FeO + Mn = MnO + Fe;
2FeO + Si = SiO2 + 2Fe; 3FeO + 2Al = Al2O3 + 3Fe.
По степени раскисления различают сталь кипящую (кп), спокойную (сп) и полуспокойную (пс). Кипящая сталь — наименее (слабо) раскисленная. В такой стали реакция образования окиси углерода C + O = СО не прекращается до ее полного отверждения: во время разливки металл продолжает «кипеть» из-за выделения пузырей СО. В слитке образуются газовые раковины, которые завариваются впоследствии при обработке стали давлением. Выход годного металла при производстве кипящей стали выше, чем при производстве других сталей, так как в этом случае не образуется усадочной раковины, а сама сталь обходится дешевле. Спокойная сталь получается при полном раскислении, когда выделение СО прекращается. Эта сталь наиболее качественная, но и наиболее дорогая. В верхней части слитка образуются большая усадочная раковина и рыхлота, что уменьшает выход годного металла. Полуспокойная сталь получается при неполном раскислении.
Производительность кислородного конвертера емкостью 300 т достигает 400—500 т/ч, в то время как производительность мартеновских и электрических печей не превышает 80 т/ч. Благодаря высокой производительности, простоте устройства, отсутствию необходимости в топливе и малой металлоемкости кислородно-конвертерный способ становится основным способом производства стали.
исходные материалы, технология, технико-экономические показатели. Схема кислородного конвертера.
Кислородно-конвертерный процесс – это выплавка стали из жидкого чугуна в конвертере с основной футеровкой и продувкой кислородом через водоохлаждаемую фурму.
Кислородный конвертер – это сосуд грушевидной формы из стального листа, футерованный основным кирпичом. Вместимость конвертера 130—350 т жидкого чугуна. В процессе работы конвертер может поворачиваться на цапфах вокруг горизонтальной оси на 360°С для завалки скрапа, заливки чугуна, слива стали и шлака.
Шихтовыми
материалами кислородно-конвертерного
процесса являются жидкий передельный
чугун, стальной лом (не более 30 %), известь
для наведения шлака, железная руда, а
также боксит (А12О3), плавиковый шпат
(CaF2), которые применяют для разжижения
шлака.
Технология плавки. Перед плавкой конвертер наклоняют, через горловину с помощью завалочных машин загружают скрап, заливают чугун при температуре 1250—1400°С. После этого конвертер поворачивают в вертикальное рабочее положение (рис. 2.4, в), внутрь его вводят водоохлаждаемую фурму и через нее подают кислород под давлением 0,9-1,4 МПа. Одновременно с началом продувки в конвертер загружают известь, боксит, железную руду. Струи кислорода проникают в металл, вызывают его циркуляцию в конвертере и перемешивание со шлаком. Благодаря интенсивному окислению примесей чугуна при взаимодействии с кислородом в зоне под фурмой развивается температура до 2400°С.
В
зоне контакта кислородной струи с
чугуном в первую очередь окисляется
железо, так как его концентрация во
много раз выше, чем примесей. Образующийся
оксид железа растворяется в шлаке и
металле, обогащая металл кислородом.
Кислород, растворенный в металле,
окисляет кремний, марганец, углерод в
металле, и содержание их понижается. При этом происходит разогрев ванны
металла теплотой, выделяющейся при
окислении примесей, поддержание его в
жидком состоянии.
В кислородном конвертере благодаря присутствию шлаков с большим содержанием СаО и FeO, перемешиванию металла и шлака создаются условия для удаления из металла фосфора по реакции в начале продувки ванны кислородом, когда ее температура еще невысока. В чугунax перерабатываемых в конвертерах, не должно быть более 0,15 % Р. При повышенном (до 0,3 %) содержании фосфора для его удаления необходимо сливать шлак и наводить новый, что снижает производительность конвертера.
Удаление серы из металла в шлак протекает в течение всей плавки по реакциям (7) и (8). Однако высокое содержание в шлаке FeO (до 7-20 %) затрудняет удаление серы из металла. Поэтому для передела в сталь в кислородных конвертерах применяют чугун с содержанием до 0,07 % S.
Подачу
кислорода заканчивают, когда содержание
углерода в металле соответствует
заданному. После этого конвертер
поворачивают и выпускают сталь в ковш
(рис. 2.4, г).
При выпуске стали из конвертера ее раскисляют в ковше осаждающим методом ферромарганцем, ферросилицием и алюминием; затем из конвертера сливают шлак (рис. 2.4, д).
В кислородных конвертерах выплавляют конструкционные стали с различным содержанием углерода, кипящие и спокойные.
В кислородных конвертерах трудно выплавлять стали, содержащие легкоокисляющиеся легирующие элементы, поэтому в них выплавляют низколегированные (до 2-3 % легирующих элементов) стали. Легирующие элементы вводят в ковш, расплавив их в электропечи, или твердые ферросплавы вводят в ковш перед выпуском в пего стали. Плавка в конвертерах вместимостью 130-300 т заканчивается через 25-50 мин. Кислородно-конвертерный процесс более производительный, чем плавка стали в мартеновских печах.
Кислородный конвертер верхнего дутья
В научно-технической литературе процесс получения стали в конвертере с использованием продувки кислородом (кислородный конвертер), который подают сверху при помощи водоохлаждаемой фурмы имеет несколько названий: кислородно-конвертерный процесс – в русскоязычной литературе стран СНГ; LD процесс – от немецкого Linz Dusenverfahren – фурменный процесс в Линце; BOP – от английского Basic Oxygen Process.
Устройство кислородного конвертера верхнего дутья (LD конвертер, BOF – от английского Basic Oxygen Furnace) показано на рисунке 9.1.
Рисунок 9.1 – Устройство кислородного конвертера верхнего дутья: 1 – корпус; 2 – футеровка; 3 – рабочее пространство конвертера; 4 – опорное кольцо с цапфами и системой крепления в нем корпуса; 5 – опорные узлы и станины; 6 – механизм поворота; 7 – кислородная фурма с системой крепления и перемещения
Типовые конструкции кислородных конвертеров имеют тоннаж 50 т, 100 т, 130 т, 160 т, 200 т, 250 т, 350 т и 400 т.
Корпус кислородного конвертера выполняется сварным из листовой стали толщиной 20 – 110 мм. Он может быть цельным или с отъемным днищем.
В верхней части цилиндрической части корпуса имеется отверстие, предназначенное для слива металла.
Горловина конвертера в большей мере, чем другие его элементы, подвержена воздействию высоких температур. Она может быть повреждена при удалении застывших выплесков металла и в процессе слива шлака. Поэтому верх горловины защищают массивным сварным или литым шлемом.
Расположенная внутри стального корпуса футеровка конвертера образует его рабочее пространство, удельный объем которого равен 0,8 – 1,1 м3/т.
Футеровка кислородного конвертера обычно выполняется из нескольких слоев различных огнеупорных материалов. Для защиты боковой поверхности корпуса конвертера применяют трех- и двухслойные футеровки.
Трехслойная футеровка состоит из арматурного, промежуточного и рабочего слоев.
Арматурный слой предназначен для защиты металлического корпуса конвертера от перегрева и прогара в результате непосредственного воздействия расплава. Его изготавливают из магнезитового, периклазошпинелидного или хромомагнезитового кирпича. Арматурный слой футеровки конвертера обычно эксплуатируется несколько кампаний без замены.
Промежуточный слой изготавливается набивным из огнеупорной массы, аналогичной по составу кирпичу, из которого изготовлен рабочий слой футеровки, толщиной 50 – 100 мм.
Рабочий слой футеровки боковой поверхности корпуса конвертера на отечественных заводах длительное время изготавливали из безобжиговых огнеупоров на смоляной связке (смолодоломитовый кирпич). Однако в настоящее время с целью повышения стойкости футеровки конвертера применяют периклазоуглеродистые огнеупоры. При этом кампания конвертера может достигать 10 и более тыс. плавок.
В настоящее время футеровку боковой поверхности большинства конвертеров выполняют в два слоя – арматурный и рабочий. Отказ от промежуточного слоя был вызван трудоемкостью его изготовления, увеличением длительности ремонта, а также возможностью увеличения толщины рабочего слоя футеровки. В этом случае кладку по толщине рабочего ее слоя ведут из двух кирпичей различной длины.
Футеровку днища конвертера изготавливают в несколько слоев. На металлическую поверхность днища наносят смолодоломитовую массу толщиной 25 – 30 мм. Затем укладывают один ряд шамотного кирпича. На шамотный кирпич кладут несколько рядов магнезитового кирпича. Для кладки рабочего слоя днища обычно используют периклазошпинелидные огнеупоры.
Стойкость футеровки из безобжиговых огнеупоров составляет 400 – 700 плавок, при использовании термообработанных безобжиговых огнеупоров – 800 – 900 плавок. При стойкости футеровки 400 – 900 плавок расход огнеупоров составляет 2 – 5 кг/т стали.
В последние годы показана перспективность использования для изготовления футеровки боковой поверхности корпуса конвертеров периклазоуглеродистых огнеупоров, которые изготавливают из электроплавленных чистых (MgO > 96%) магнезитовых порошков. К ним добавляют чешуйчатый графит высокой чистоты, а в ряде случаев и антиокислительные металлические порошки (Al, Mg или Si). Из полученной массы на связке из фенолформальдегидной смолы прессуют кирпичи под давлением более 1000 т. По окончанию кладки периклазоуглеродистую футеровку сушат в течение 24 часов и вводят конвертер в работу.
Фурма кислородного конвертера верхнего дутья (кислородная фурма конвертера) выполнена из концентрических стальных труб (рисунок 9. 2). По центральной трубе осуществляется подача кислорода, а в зазоре между трубами циркулирует охлаждающая вода. Нижний участок фурмы (головка), который испытывает максимальные тепловые нагрузки, обычно изготавливают из меди, обладающей высокой теплопроводностью. В настоящее время кислородные конвертеры, как правило, оборудованы многосопловыми фурмами, выходные отверстия которых имеют форму сопла Лаваля.
Рисунок 9.2 – Головка четырехсопловой кислородной фурмы: 1 – 3 – стальные трубы; 4 – сопловой коллектор; 5 – сопло; 6 – распределитель воды; 7 – торец головки фурмы
Принципиальная схема кислородного конвертера » Все о металлургии
15.01.2015
В практике металлургии стран Содружества используется следующий типовой ряд номинальных вместимостей (емкостей) конвертеров (по массе жидкой стали): 50, 100, 130, 160, 200, 250, 300, 350, 400, 500 т. Широко употребляемой характеристикой конвертера является его садка, т.

Кислородно-конвертерный процесс можно схематически представить как продувку ванны из жидкого чугуна сверху кислородными струями, выходящими со сверхзвуковой скоростью из вертикальной фурмы, расположенной выше уровня спокойной ванны (рис. 3.2).
Конвертер для продувки сверху отличается наличием, как правило, глуходонного днища и имеет симметричную форму. Он представляет собой сосуд грушевидной формы, изготовленный из стального листа и футерованный изнутри основными огнеупорами.
Сварной корпус 1 имеет среднюю цилиндрическую часть, глухое дно и симметричную горловину 2, которая служит для ввода в полость конвертера кислородной фурмы, отвода газов, заливки чугуна и завалки лома, взятия проб металла и шлака, замера температуры. Сталевыпускное отверстие (летка) 3, выполненное из магнезитовых блоков, служит для слива металла.
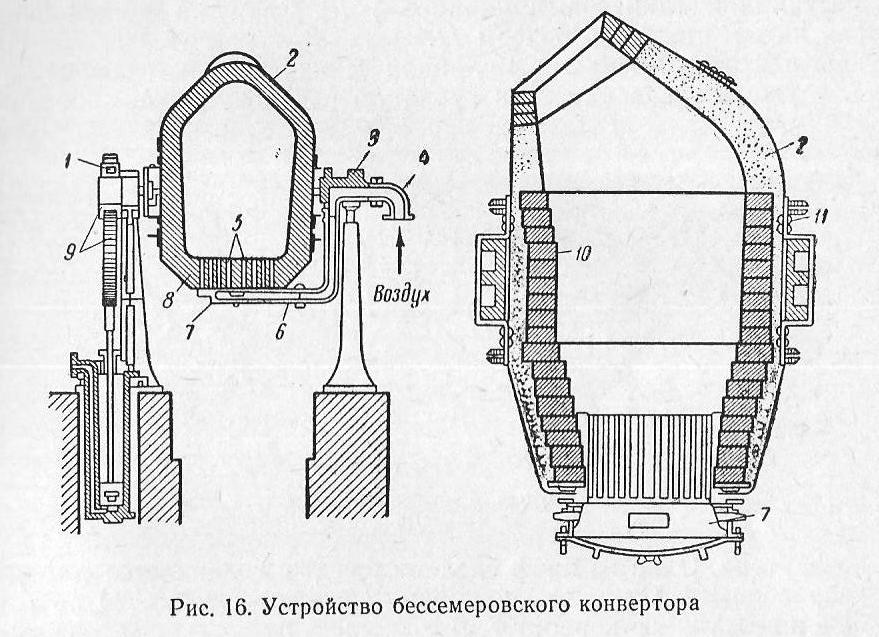
Конвертер имеет опорный пояс (кольцо) с цапфами 4, расположенными в подшипниках опор. При помощи привода конвертер может вращаться в обе стороны на 360°.
Кислород поступает в конвертер под давлением 14-20 ат. через водоохлаждаемую фурму, которую вводят через горловину. Высота фурмы над уровнем ванны может меняться по ходу продувки с помощью механизма перемещения, обеспечивая рациональный режим ведения процесса.
Кислородная фурма обычно выполняется из трех стальных труб и снабжена снизу медной головкой с соплами (рис. 3.3). По центральной трубе подается кислород, две внешние служат для охлаждения фурмы. Расход воды должен выбираться из расчета получения перепада ее температуры (до и после фурмы) не более 20-25°С. Головка фурмы – сменная, приваривается к внешней и внутренней трубам. В первые годы освоения конвертеров они были односопловыми. В настоящее время используют многосопловые головки, которые вследствие рассредоточения кислородного потока на несколько струй обеспечили более «мягкую» продувку и позволили значительно увеличить интенсивность подачи кислорода.

Над конвертером, кроме фурмы, находятся газоотводящий тракт и система загрузки сыпучих. Под конвертером по рельсам перемещаются сталевоз и шлаковоз.
Конвертер кислородный – Энциклопедия по машиностроению XXL
ПРОИЗВОДСТВО СТАЛИ в КИСЛОРОДНЫХ КОНВЕРТЕРАХ [c.35]Кислородно-конвертерный процесс — это выплавка стали из жидкого чугуна в конвертере с основной футеровкой и продувкой кислородом через водоохлаждаемую фурму. [c.35]
Кислородный конвертер —это сосуд грушевидной формы из стального листа, футерованный основным кирпичом. Вместимость конвертера 130—350 т жидкого чугуна. В процессе работы конвертер может поворачиваться на цапфах вокруг горизонтальной оси на 360 °С для завалки скрапа, заливки чугуна, слива стали и шлака. [c.35]
Рис. 2.4. Последовательность в кислородных конвертерах |

Удаление серы из металла в шлак протекает в течение всей плавки по реакциям (7) и (8). Однако высокое содержание в шлаке FeO (до 7—20 %) затрудняет удаление серы из металла. Поэтому для передела в сталь в кислородных конвертерах применяют чугун с содержанием до 0,07 % S. [c.37]
В кислородных конвертерах выплавляют конструкционные стали с различным содержанием углерода, кипящие и спокойные. [c.37]
В кислородных конвертерах трудно выплавлять стали, содержащие легкоокисляющиеся легирующие элементы, поэтому в них выплавляют низколегированные (до 2—3 % легирующих элементов) стали. Легирующие элементы вводят в ковш, расплавив их в электропечи, или твердые ферросплавы вводят в ковш перед выпуском в него стали. Плавка в конвертерах вместимостью 130—300 т заканчивается через 25—50 мин. Кислородно-конвертерный процесс более производительный, чем плавка стали в мартеновских печах. [c.37]
Вследствие низкого качества выплавляемого металла и особых требований к составу чугуна конвертеры с воздушным дутьем практически вытеснены кислородными.
[c.172]
Приведены результаты исследований рафинирования металла при обычном пульсирующем кислородном дутье в условиях висящей в магнитном поле капли, хорошо моделирующих реакции между кислородом и каплями металла при конвертерной плавке, холодного и горячего моделировании и изучения характера и строения реакционной зоны конвертера. Рассмотрена аэродинамика сверхзвуковых кислородных струй при их истечении из многосопловых насадок и фурм. [c.43]
Плавка в кислородном конвертере [c.143]
Одним из главных потребителей компрессорных машин являются предприятия черной металлургии. Компрессоры находят применение в металлургических процессах для следующих целей подачи газовых сред в доменные печи подачи воздуха в воздухоразделительные установки для получения кислорода отсасывания продуктов сгорания от агломерационных машин в процессе обогащения руд отсасывания продуктов сгорания от кислородных сталеплавильных конвертеров и от мартеновских печей, работающих при подаче кислорода отсасывания от коксовых батарей продуктов коксования на коксохимических заводах.
[c.5]
В черной металлургии при традиционной схеме производства металла чугун — сталь — прокат (с учетом производств, обслуживающих металлургические заводы) к агрегатам-источникам ВЭР могут быть отнесены доменные печи, кауперы, агломерационные машины, ферросплавные печи, мартеновские печи, кислородные конвертеры, нагревательные устройства (методи- [c.39]
При схеме охлаждения без дожигания окиси углерода конвертерный газ после очистки можно использовать в качестве топлива. В связи с периодичностью работы конвертеров выход тазов и их теплота сгорания по циклам плавки значительно изменяются. Поэтому при существующих схемах утилизации в топливную сеть можно собрать 65—-75% газов, выходящих из конвертера. Однако из-за периодичности работы конвертера, подсоса воздуха и возможности образования взрывоопасной смеси в настоящее время проблема аккумуляции конвертерного газа не решена, на действующих крупных конвертерах газ сжигается на свечах. Выход физического тепла стали определяется количеством выплавленной стали и ее энтальпией при выпуске из мартеновской печи или из кислородного конвертера.
[c.46]
Паровая обдувка не обеспечивает стабильность аэродинамического сопротивления, к тому же требует в несколько раз больших эксплуатационных затрат. Новые способы очистки на 30—60% повышают степень использования тепла уходящих газов мартеновских печей [33]. В результате стабилизации аэродинамического сопротивления котлов-утилизаторов значительно улучшился тяговый режим печей и газоочисток. При этом в ряде случаев была увеличена производительность мартеновских печей и кислородных конвертеров [43]. Виброочистка обеспечивает наименьшую загрязненность поверхностей нагрева, однако для ее внедрения необходимо осуществить реконструкцию креплений поверхностей нагрева кот- [c.169]
Для кислородного сталеплавильного конвертера емкостью 350—400 т выход конвертерного газа в зависимости от интенсивности продувки при отводе без дожигания составит 200—400 тыс. м /ч, выход пара от котла-утилизатора достигнет 150—400 т/ч.
[c.172]
ОКГ-100-ЗА 100—130-тонные сталеплавильные кислородные конвертеры, охлаждение газов с дожитом окиси углерода До 200 4,7 [c.309]
Хорошим комплексом свойств обладают низкоуглеродистые стали, выплавленные в мартеновских печах. Сталь, полученная в конвертерах с кислородным дутьем и основной футеровкой, приближается по своим свойствам к стали, выплавленной в мартеновских печах. [c.90]
При одинаковом содержании углерода бессемеровская сталь имеет более высокую прочность и твердость, чем мартеновская. Эта разница в свойствах объясняется тем, что в бессемеровской стали содержится повышенное количество растворенных азота и фосфора — элементов, упрочняющих сталь, но делающих ее одновременно и более хрупкой. Применение кислородного дутья в конвертерах значительно ослабляет этот недостаток конверторной стали. [c.43]
Сталь, выплавленная в конвертерах с кислородным дутьем, приближается по своим свойствам к мартеновской и во многих случаях вполне заменяет ее.
[c.43]
Газ коксовых печей Газ от кислородных конвертеров 25,5 3,0 2,4 0.5 59,8 2,3 16 900 [c.77]
Нижний предел содержания СО в газе кислородных конвертеров, поступающих в газгольдер, после газоочистки составляет 50 % свободного Ог в газе должно быть не более 3 %. [c.78]
Сталеплавильные кислородные конвертеры [c.82]
Цикличность работы технологической установки — источника тепловых отходов – создает значительные трудности при использовании газов, как это имеет место в кислородных сталеплавильных конвертерах. В ряде случаев при цикличности выхода газового потока использование его практически невозможно. [c.27]
Конвертеры вместимостью, т 80-125 16,0-17,0 3,5 0,1-0,2 0,5 1,5-3,0 0,5 80,0-82,0 16,0 675-1125 775-875 До 20 0-2 Без кислородного дутья С кислородным дутьем [c.30]
Передел чугуна в сталеплавильных конвертерах с верхним кислородным дутьем получил широкое развитие в производстве стали.
[c.69]
Механические свойства сталей обыкновен юго качества ниже механических свойств сталей других групп. Основны.м элементом, определяющим механические свойства этих сталей, является углерод. Их выплавляют в кислородных конвертерах и мартеновских печах. Стали обыкновенного качества подразделяют на спокойные (полностью раскисленные), кипящие (не полностью раскисленные) и полу-спокойные (занимающие промежуточное положение между спокойными и кипящими). Спокойные, полуспокойные и кипящие стали обозначают в конце марки буквами соответственно сп пс и кп . [c.15]
Чугун переделывают п, лаль в различных по принципу деУктвия металлургических агрегатах- мартеновских печах, кислородных конвертерах, дуговых электропечах. [c.32]
Кислородный конвертер (рис. 3.28) состоит из корпуса I диаметром до 8 м и днища 4, футерованных огнеупорным кирпичем, опорных подшипников 2, станин 5 и механизма поворота 3, позволяющего поворачивать конвертер на любой угол вокруг горизонтальной оси. Продувка кислородом производится через специальную водоохлаждаемую фурму, вводимую в горловину конвертера. Наконечник фурмы имеет несколько (3 — 4) сопл Лаваля диаметром 30 — 50 мм, обеспечивающих скорость струи с числом Ма 2 при давлении кислорода 1 — 1,4 МПа. Наконечник устанавливается на высоте 1 — 2 м от уровня ванны. Продолжительность продувки составляет 20 — 25 мин. Газ, отходящий из конвертера с температурой около 2000 К, состоит из 90% СО и 10% СО2 и имеет теплоту сгорания 10 — 12 МДж/м . Преимуществом конвертеров является высокая производительность без расхода топлива, недостатком — невозможность использования большого количества скрапа в шихте.
[c.172]
Тепловые ВЭР цветной металлургии образуются за счет физической теплоты уходящих газов обжиговых, шахтных, отражательных, рудно-термических, анодных и других печей, конвертеров, агрегатов для кислородно-взвешенной плавки, шлаковозгоночных установок, охлаждения и пр. Годовой выход тепловых ВЭР, пригодных к утилизации, в цветной металлургии составляет 74,1 млн. ГДж.
[c.410]
Приведены характеристики шихтовых и огнеупорных материа лов, применяемых в конвертерном производстве. Расемотрены уст ройство и конструкции конвертеров, подготовка конвертеров к ра боте и обслуживание их в процессе эксплуатации. Основное внима ние уделено кислородно-конвертерному способу производства стали Рассмотрены технико-экономические показатели работы конвертер ных цехов, нормы выработки и оплаты труда, вопросы техники без опасности и производственной санитарии. [c.15]
Рассмотрены физико-химические особенности и технология выплавки ванадиевых шлаков в конвертерах с кислородным и воздушным дутьем. Описаны плавки с накоплением шлака в конвертере, а также с использованием углеродсодержащих материалов и ванадийсодержащего агломерат.а. Изложена промышленная технология выплавки низко- и высоколегированных сталей в электродуговых и кислых мартеновских печах с использованием ванадиевого шлака и металлоотсева для легирования стали.
[c.45]
Использование электропечей в производстве стали расширилось после введения кислородной продувки металла в конвертерах. Удельные капитальные затраты на строительство конвертеров примерно на 40% ниже стоимости мартенов, при этом и себестоимость плавки стали в конвертерах с кислородной продувкой стали сокращается на 30%. Поскольку кислородная продувка стали в конвертере позволила получать металл, по качеству ра1иный с мартеновским, то оказа- [c.31]
Важным резервом является экономия электрической и тепловой энергии и топлива промышленностью, сельскохозяйственными, коммунально-бытовыми потребителями и на транспорте, т. е. развитие уже известных и внедрение новых энергоэкономичных прогрессивных технологий, в том числе таких, кж использование непрерывной разливки стали, кислородных конвертеров, комбинированного дутья доменных печей в черной металлургии, автогенных процессо1в в цветной металлургии, мощных энерготехнологических агрегатов, в химической промышленности, сухого способа производства цемента, более эффективных горелочных устройств в котельных и печных агрегатах. и т. п. За счет мер такого характера, а также путем модернизации энергоиспользующего оборудования и за счет организационных мероприятий должна быть обеспечена в 1985 г. экономия топливно-энергетических ресурсов на 160—170 млн. т условного топлива, в том числе 70—80 млн. т условного топлива за счет снижения норм энергопотребления.
[c.42]
ОКГ д-250М 250—300-тонные сталеплавильные кислородные конвертеры, охлаждение газоа без до-жига окиси углерода До 160 1,8 [c.309]
III группа. Механизмы, включающие литые корпусные и некорпусные детали с прямолинейной и криволинейной поверхностью, содержащие более двух кинематических naps требующие расчетов кинематических передач с несколькими степенями свободы и имеющие соединения в пределах 3-го класса точности. К ним относятся редукторы двух- и трехступенчатые цилиндрические коробки скоростей стопорные устройства сталеразливочных ковшей транспортирующие, загрузочные, фиксирующие и закрепляющие устройства и механизмы установка для подъема и транспортировки конвертеров тормоза колодочные и специального типа, установка кислородной фурмы муфты специального типа установка для подачи кислорода в конвертер вакуумметры прокатное оборудование главные муфты обжимных толстолисТовых, листовых станов горячей и холодной прокатки приводы вращения, подъема, наклона, передвижения механизмы открывания [Рольганги с групповым и индивидуальным приводом рабочие клети обжимных тонколистовых, листовых станов горячей и холодной прокатки клети для про-
[c. 241]
Значения указанных коэффициентов определяются видом производства и характеристиками технологического процесса. Применительно к процессу производства стали в кислородных конвертерах Твых/Тцикла З сред/ макс 0,8 Qh [c.77]
Банию газоп от кислородных конвертеров показаны па рис. 1.49. [c.80]
Тепловая мощность отходящего от теплотехнической установки газового потока Qbh, зависящая от расхода отходящих газов и их температуры, оказывает существенное влияние на экономику теплоиспользо-вания. Выход отходящих газов зависит от количества сжигаемого топлива в технологической установке и от выхода шихтовых газов, образуемых при термической обработке исходных технологических материалов. Большое количество шихтовых газов образуется, например, при плавке сульфидных руд цветных металлов, кислородной продувке сталеплавильных конвертеров для передела чугуна в сталь. [c.26]
При кислородно-конвертерном процессе продувка чугуна производится сверху через водоохлаждаемую фурму техническим кислородом (чистотой 98—99,5 %). После заливки в конвертер чугуна и загрузки извести на зеркало металла подается по фурме кислород для окисления углерода и примесей, содержащихся в чугуне. Продукты окисления кремния, марганца, фосфора и серы в основном переходят в шлаки, продукты окисления углерода удаляются с уходящими конвертерными газами. Эти газы на выходе из конвертера состоят в основном из оксида углерода (СО = 90 95 %), имеют высокую температуру (более 2000 К) и содержат много конвертерного уноса (до 150 г/м ). Выход конвертерных газов цикличный, отличается большой неравномерностью, зависит от конструкции кислородной фурмы и ее расположения в конвертере во время продувки, интенсивности продувки и состава, характеристики и режима подачи шихтовых материалов. Газовы-деление начинается через 2—4 мин после начала продувки, быстро достигает максимального выхода, затем снижается до нуля за 2—3 мин до завершения процесса продувки. Для конвертера вместимостью 300 т среднечасовой выход газа составляет 18 000 м /ч, а максимальный -пиковый 150 000 м /ч.
Выброс таких газов в атмосферу запрещен, их очистка и охлаждение являются технологической необходимостью,
[c.69]
Действующие охладители конвертерных газов с дожиганием СО рассчитаны на пропуск максимального выхода конвертерных газов и поэтому ограничивают возможности повышения интенсивности продувки, т.е. удельного расхода кислорода на тонну выплавляемой стали в минуту, м /(т-мин), а следовательно, и производительности конвертеров. Исследованиями Всесоюзного научно-исследовательского института металлургической теплотехники (ВНИИМТ) установлена зависимость интенсивности газовыделения V , м /(т-мин), и длительности цикла плавки т, мин, от интенсивности кислородной продувки г, м /(т-мин) (рис. 3.26, а) и длительности продувки 7д, мин, от интенсивности кислородного дутья (рис. 3.26, б). Опыт работы ОКГ на Новолипецком металлругическом заводе и исследования ВНИИМТ обусловили создание ОКГ без дожигания оксида углерода. [c.75]
Как работает мой концентратор кислорода?
Кислородные концентраторы работают по принципу «быстрой адсорбции при переменном давлении», при которой азот удаляется из воздуха с использованием цеолитных минералов, которые адсорбируют азот, оставляя другие газы для прохождения сквозь них и оставляя кислород в качестве основного газа.
Как только кислород собирается, давление падает, что позволяет азоту десорбироваться и выталкиваться обратно в воздух.
Кислородный концентратор имеет воздушный компрессор, два цилиндра, заполненных гранулами цеолита, резервуар для выравнивания давления, клапаны и трубки.В течение первого полупериода первый цилиндр получает воздух от компрессора, который длится около 3 секунд. В течение этого времени давление в первом цилиндре повышается с атмосферного до нескольких раз нормального атмосферного давления (около 20 фунтов на квадратный дюйм), и цеолит насыщается азотом. Когда первый баллон достигает почти чистого кислорода (есть небольшое количество аргона, CO2, водяного пара, радона и других второстепенных компонентов атмосферы), открывается клапан, и обогащенный кислородом газ течет в резервуар выравнивания давления, который подключается к кислородному шлангу пациента .В конце первой половины цикла воздух из компрессора направляется во 2-й цилиндр. Давление в первом цилиндре падает, когда обогащенный кислород перемещается в резервуар, позволяя азоту десорбироваться обратно в газ. В середине второй половины цикла происходит еще одно изменение положения клапана, чтобы выпустить газ из первого цилиндра обратно в окружающую атмосферу, удерживая концентрацию кислорода в резервуаре для выравнивания давления ниже примерно 90%.Давление в шланге, подающем кислород из уравнительного резервуара, поддерживается редукционным клапаном.
Портативные концентраторы кислорода
Они существуют уже несколько десятилетий, но старые модели были громоздкими, ненадежными и не допускались к использованию в самолетах. С 2000 года производители повысили надежность и размер, и теперь они производят 1-6 л / мин кислорода. Портативные концентраторы подключаются непосредственно к обычной домашней розетке для зарядки дома или в отеле, но они поставлялись с адаптером питания, который обычно можно подключить к автомобильному адаптеру постоянного тока.Они могут работать от батареи, а также для использования в амбулаторных условиях, вдали от источника питания или в самолете.
Переносные кислородные концентраторы работают по тому же принципу, что и домашние бытовые концентраторы, работая через серию циклов. Воздух проходит от миниатюрного воздушного компрессора через молекулярное сито из гранул цеолита, которое адсорбирует азот. Часть произведенного кислорода доставляется пациенту, а часть подается обратно в сита, чтобы очистить их от накопившегося азота и подготовить их к следующему циклу.Благодаря этому процессу система способна стабильно производить до 90% кислорода. Последние модели могут питаться от электросети, постоянного тока 12 В (автомобиль / лодка и т. Д.), А также от аккумуляторных батарей, что избавляет пациента от необходимости полагаться на баллоны и другие современные решения, которые со временем ограничивают его деятельность и мобильность. вес и размер.
Большинство современных портативных систем концентраторов кислорода обеспечивают подачу кислорода в импульсном режиме (по требованию), чтобы максимально повысить чистоту кислорода. Система обеспечивает высокую концентрацию кислорода и используется с назальной канюлей для направления кислорода от концентратора к пациенту.
Ссылки: http://en.wikipedia.org и http://www.inogen.com и http://hme-business.com
Что такое концентратор кислорода и как он работает? (Использование и причины)
Благодаря большим достижениям медицины, концентраторы кислорода сегодня компактны, малы, бесшумны и легки, но при этом обеспечивают максимальную совместимость и высокую производительность.Прежние кислородные концентраторы громоздкие и тяжелые, что затрудняет кислородную терапию для пациентов во время путешествий или вне дома.
Сегодня вы можете выбирать из стационарных концентраторов для дома и переносных концентраторов кислорода (POC), которые можно легко взять с собой куда угодно.
Что такое концентратор кислорода? Определение концентратора кислорода: Концентратор кислорода – это тип медицинского устройства, используемого для доставки кислорода людям с нарушениями дыхания. Людям, у которых концентрация кислорода в крови ниже нормы, часто требуется кислородный концентратор для замены этого кислорода.
Как правило, кислородный концентратор нельзя купить без рецепта. Врач должен прописать его после завершения тщательного медицинского осмотра. Врачи также обычно показывают пациентам, как эффективно использовать эти концентраторы во время путешествий и дома.
Кислородные концентраторы фильтруют окружающий воздух, сжимая его до необходимой плотности, а затем доставляя очищенный кислород медицинского класса в систему доставки импульсной дозы или систему непрерывного потока к пациенту.
Он также оснащен специальными фильтрами и ситами, которые помогают удалять азот из воздуха, обеспечивая доставку полностью очищенного кислорода пациенту. Эти устройства также поставляются с электронным пользовательским интерфейсом, позволяющим регулировать уровни концентрации кислорода и параметры подачи. Затем вы вдыхаете кислород через носовую канюлю или специальную маску.
Обычно производительность концентратора кислорода измеряется в л / мин (литрах в минуту). Ваш врач определит, какой уровень кислорода вам нужен, который может варьироваться в состоянии покоя, во время сна и во время физических упражнений.
Каковы возможности и причины использования концентратора кислорода?Есть много причин для использования концентратора кислорода, и врачи могут рекомендовать кислородную терапию своим пациентам при различных заболеваниях. Обычно легкие поглощают кислород из воздуха, попадая в кровоток.
Если вам недавно делали анализ крови или пульсоксиметрию для оценки уровня насыщения кислородом, и у вас был обнаружен низкий уровень кислорода в крови, ваш врач может порекомендовать краткосрочную или долгосрочную кислородную терапию.
Вам, наверное, интересно, для чего нужен кислородный концентратор? Острые состояния обычно требуют кратковременной кислородной терапии. Эти условия обычно сохраняются в течение короткого периода времени. У них могут быть внезапные симптомы по сравнению с хроническими состояниями, при которых все происходит постепенно. Однако некоторые респираторные или хронические заболевания требуют длительного приема кислорода.
Несколько примеров острых состояний, при которых вам может потребоваться использование концентратора кислорода для краткосрочной кислородной терапии:
Астма: Это состояние, при котором ваши дыхательные пути воспаляются и начинает вырабатывать много слизи, что затрудняет дыхание.Несмотря на то, что существует ряд фармацевтических препаратов, которые могут лечить и контролировать астму, концентратор кислорода может перекачивать высокий уровень кислорода в кровоток пациента, когда он страдает или уже перенес приступ астмы.
Пневмония: Пневмония – это инфекция, при которой у вас развивается воспаление в одном или обоих воздушных мешочках легких, и во многих случаях они заполняются жидкостью. Многим пациентам с пневмонией была назначена кислородная терапия, и у них были хорошие клинические результаты.
Респираторный дистресс-синдром (RDS): RDS – это нарушение дыхания, в основном поражающее новорожденных, особенно тех, кто родился за шесть или более недель до даты родов. Новорожденные, страдающие RDS, не вырабатывают достаточно сурфактанта (жидкости, покрывающей легкие), что вызывает коллапс легких и затрудняет дыхание. Кислородная терапия с использованием концентраторов кислорода помогает перекачивать кислород в кровоток и легкие ребенка, чтобы уменьшить дальнейшие осложнения.
Бронхолегочная дисплазия (БЛД): Новорожденные, страдающие РДС, также имеют более высокий риск развития БЛД.Это тяжелое заболевание легких, требующее длительной поддержки дыхания.
В некоторых случаях после операции вам может потребоваться кислород на короткий период времени.
Хронические заболевания, требующие кислородной терапииНекоторые хронические состояния, требующие длительного использования концентраторов кислорода:
Хроническая обструктивная болезнь легких (ХОБЛ): ХОБЛ поражает около 16 миллионов человек, но кислородный концентратор может быть эффективное лечение. Когда у вас ХОБЛ, у вас хроническое повреждение легких, что затрудняет поглощение легкими достаточного количества кислорода.В результате у вас может возникнуть затрудненное дыхание, и может помочь кислородная терапия через концентратор.
Муковисцидоз: Вы унаследовали это опасное для жизни состояние. Это вызывает повреждение пищеварительной системы и легких. Это редкое заболевание, которое поражает клетки организма, ответственные за выработку слизи, пота и пищеварительных соков. Жидкости меняются, в результате чего получается более липкий и густой раствор, который закупоривает протоки, трубки и проходы инфицированного человека.
Апноэ во сне: Апноэ во сне – это нарушение сна, которое может быть серьезным и вызывать у человека спорадическую остановку и начало дыхания во время сна.Обычно лечением этого состояния является постоянное положительное давление в дыхательных путях (CPAP), потеря веса и физические упражнения, хотя некоторым людям с апноэ во сне может потребоваться кислородная терапия.
Думайте о концентраторе кислорода как о оконном кондиционере – он забирает воздух, меняет его и подает в другой форме. Кислородный концентратор забирает воздух и очищает его для использования людьми, которым необходим медицинский кислород из-за низкого уровня кислорода в крови.
Он работает:
- Сжатие воздуха в качестве охлаждающего механизма предохраняет концентратор от перегрева
- Забор воздуха из окружающей среды
- Использование электронного интерфейса для регулировки параметров подачи
- Удаление азота из воздуха через ситовые слои и фильтр
- Подача очищенного кислорода через маску или назальную канюлю
Пациенты, которым в прошлом требовалась кислородная терапия, в основном полагались на баллоны с кислородом под давлением.Несмотря на то, что эти резервуары чрезвычайно эффективны, они также довольно неэффективны, поскольку поставщики должны регулярно посещать пациентов, чтобы пополнить запас кислорода в их резервуаре.
Узнайте больше о различных концентраторах кислорода, доступных вам на сайте CPAP.com:
1. Портативный мини-концентратор кислорода Philips Respironics SimplyGo с импульсным потоком дозы – удобный для путешествий концентратор кислорода с аксессуарами и функциями специально для активного образа жизни.Он обеспечивает подачу импульсной дозы, помогая продлить срок службы батареи.
2. Портативный кислородный концентратор Philips Respironics SimplyGo с импульсной дозой и непрерывным потоком – это портативный концентратор для людей, которые хотят брать с собой кислородную терапию при выполнении повседневных дел. Он обеспечивает режимы импульсной дозы и непрерывного потока для дополнительной универсальности.
3. Портативный концентратор кислорода Inogen One G4 с импульсным потоком дозы – Inogen One G4 самостоятельно подает кислород, используя окружающий его воздух.Это самый портативный кислородный концентратор на сегодняшний день, он легкий и достаточно маленький, чтобы носить его как большую сумку или кошелек. У него даже есть наплечный ремень, подключенный к устройству напрямую.
4. Портативный кислородный концентратор Inogen One G3 с импульсным потоком дозы – компактный кислородный концентратор, предназначенный для подачи кислорода в импульсной дозе в дороге или дома. Он весит 4,8 фунта, что делает его идеальным для путешествий.
5. Стационарный концентратор кислорода Inogen для дома с непрерывным потоком – концентратор кислорода, обеспечивающий постоянный высокий уровень кислорода для домашнего использования.Это один из наиболее компактных и легких стационарных концентраторов, обеспечивающий непрерывный поток от одного до пяти литров в минуту.
6. Портативный концентратор кислорода ResMed Activox ™ с импульсным потоком дозы – портативный концентратор кислорода, который универсален и идеально подходит для активного пользователя. Он имеет внутреннюю батарею, поэтому вы можете отключить концентратор и взять его с собой куда угодно.
Сначала вы захотите, чтобы ваш врач или специалист по сну провел полное обследование, чтобы определить, подходит ли портативный или стационарный кислородный концентратор для ваших нужд.
Дэвид Репаски использует лечение CPAP с 2017 года и на собственном опыте знает, каково жить с апноэ во сне. Он делится мнением пациента в блоге CPAP.com и прошел формальное обучение работе с аппаратами, масками и оборудованием CPAP.
Принцип работы концентратора кислорода? | Фернанда Юлианто
Концентратор кислородаРабота концентраторов кислорода забирает воздух и очищает его для использования людьми, которым необходим медицинский кислород из-за низкого уровня кислорода в крови.
- Возьмите воздух из свободного воздуха
- Затем сожмите воздух, пока охлаждающий механизм предохраняет концентратор от перегрева
- Процесс удаления азота из воздуха через фильтр
- Регулировка и согласование с электроникой
- И обеспечение очищенного кислорода через нос с маской
Кислородные концентраторы обычно используют технологию адсорбции при переменном давлении (PSA) и очень широко используются для подачи кислорода в медицинских учреждениях, особенно там, где жидкий или сжатый кислород слишком опасен или неудобен, например дома или в мобильной клинике. Для других целей также существуют концентраторы на основе мембранной технологии.
Функция концентратора кислорода?
Медицинские концентраторы кислорода используются в больницах или дома для производства кислорода для пациентов. Генераторы PSA представляют собой экономичный источник кислорода. Они являются более безопасными, дешевыми и удобными альтернативами криогенным кислородным баллонам или баллонам под давлением.
Кислородные концентраторы считаются достаточно безопасными, чтобы их можно было давать каждому пациенту по рецепту для использования дома.Обычно они используются в качестве дополнения к лечению CPAP от тяжелого апноэ во сне. Существуют также другие медицинские применения концентраторов кислорода, включая ХОБЛ и другие респираторные заболевания.
Распределитель концентратора кислорода
Для правильного выбора / покупки концентратора кислорода иногда эта путаница вызывает сомнения у медицинского персонала в выборе. Теперь больше не о чем беспокоиться, потому что мы поставляем медицинское оборудование соответствующего стандарта.Не нужно бояться, если вы не смогли определить хороший бренд и тип, потому что мы будем хорошо обслужены, если вы захотите проконсультироваться или задать вопросы. Может быть полезно.
Медоборудование можно купить здесь жуал алат кесехатан
% PDF-1.5
%
1 0 obj
>
endobj
2 0 obj
> поток
2012-09-27T10: 55: 26 + 02: 002012-09-27T10: 55: 26 + 02: 002012-09-27T10: 55: 26 + 02: 00Приложение Adobe InDesign CS5 (7.0.3) / pdfuuid: dc5aea6b- d35b-ed40-a7df-df840db0d109uuid: fedbd37e-8c27-d847-a18e-043c7bda6097 Adobe PDF Library 9.9 конечный поток
endobj
3 0 obj
>
endobj
5 0 obj
> / ExtGState> / Font> / ProcSet [/ PDF / Text / ImageC] / XObject >>> / Rotate 0 / TrimBox [0. )] fY ~ “jbk̇MRdR-% c_ 곺 + @ 2e) x &” & = I> Uk! Br $ 2L] ‘Концентратор кислорода HEEl
мобильный и для дома; История и современное состояние
На что обращать внимание на ультрасовременный концентратор кислорода с точки зрения мобильности и эффективности;
Как работают концентраторы кислорода сегодня?
Домашние медицинские концентраторы кислорода были изобретены в начале 1970-х годов. В то время эти агрегаты были довольно большими и очень дорогими, а главное – не переносными.Производство этих устройств увеличилось в конце 1970-х годов. Union Carbide Corporation (UCC) и Bendix Corporation были первыми производителями.
До этого времени домашняя медицинская кислородная терапия требовала использования тяжелых кислородных баллонов высокого давления или небольших криогенных систем с жидким кислородом. Обе эти системы доставки требовали частых визитов поставщиков на дом для пополнения запасов кислорода. Эти запасы были не только большими и громоздкими, но и при определенных обстоятельствах могли представлять опасность пожара.
Затем в середине 1980-х годов в США программа Medicare перешла с платы за услуги на фиксированную ежемесячную ставку за кислородную терапию в домашних условиях, в результате чего производители медицинского оборудования длительного пользования (DME) быстро использовали концентраторы как способ контроля затрат. . Эти изменения в компенсации резко сократили количество первичных систем подачи высокого давления и жидкого кислорода, используемых в то время в домах США.
Кислородные концентраторы стали предпочтительным и наиболее распространенным средством доставки домашнего кислорода.В результате этого изменения количество производителей, выходящих на рынок концентраторов кислорода, увеличилось в геометрической прогрессии. Union Carbide Corporation (UCC) изобрела молекулярные сита в 1950-х годах, которые сделали эти устройства возможными. UCC также изобрела первые криогенные домашние медицинские кислородные системы в 60-х годах
Теперь, в 2018 году, выбор компактных, 100% безопасных и эффективных легких портативных концентраторов кислорода и домашних концентраторов кислорода широк и разнообразен. Все они работают в основном так же, как и те большие ранние устройства 1970-х годов, однако современные технологии позволили сделать их намного меньше и легче.
Проще говоря, концентратор кислорода работает на электричестве; забирает воздух в помещении, удаляет из него азот и обеспечивает до 95% чистого кислорода.
Принцип работы концентратора кислорода
Состав воздуха (78% азота, 21% кислорода и 1% других газов, например двуокиси углерода, аргона и т. Д.) ясно показывает, что воздух в основном состоит из двух газов: азота и кислорода [вместе 99%]. Если из воздуха удалить азот, оставшимся первичным газом будет кислород с чистотой около 90-95%. Концентратор кислорода использует эту идею с основным принципом адсорбции при переменном давлении (PSA) для доставки кислорода с чистотой 90-95%.
- Серия фильтров: Для фильтрации загрязнений, присутствующих в воздухе.
- Воздушный компрессор: Для нагнетания комнатного воздуха в машину и его направления к слоям молекулярных сит.
- 2 слоя молекулярных сит – цеолит (микропористый алюмосиликатный минерал): Имеют способность улавливать азот.
- Переключающий клапан: Переключает мощность компрессора между двумя слоями молекулярных сит.
- Выход кислорода: Отверстие, через которое пациенту поступает кислород.
- Расходомер: Для установки расхода в литрах в минуту (л / мин).
1. Окружающий воздух (воздух помещения), проходящий через серию фильтров, втягивается в машину компрессором.
2. Этот воздух сжимается в первом слое молекулярного сита, и весь азот адсорбируется. Слои молекулярных сит пористые и, следовательно, имеют большую площадь поверхности, благодаря которой они адсорбируют большое количество азота.
3. Теперь, потому что воздух содержит только азот и кислород в качестве основных компонентов; основным остающимся газом является кислород. Этот кислород имеет концентрацию до 95% и готов к подаче пациенту через систему доставки кислорода, такую как назальная канюля, кислородная маска и т. Д.
4. Компрессор продолжает сжимать воздух в слой 1-го молекулярного сита до тех пор, пока он не будет насыщен (заполнен) азотом. Слой сита обычно насыщается при давлении 20 фунтов на квадратный дюйм.
5.Незадолго до того, как слой 1-го молекулярного сита станет насыщенным; Клапан переключения вступает в действие, и мощность воздушного компрессора немедленно переключается на 2-й слой сита, то есть компрессор начинает сжимать воздух во 2-е молекулярное сито.
6. Пока этот слой сита насыщается азотом, азот, который был захвачен в первом слое сита, удаляется. Небольшое количество азота, которое остается в слое сита после выгрузки, удаляется обратной промывкой кислорода из другого слоя сита.
7. Переключающий клапан снова переключает мощность воздушного компрессора обратно на 1-й слой сита, как только 2-й слой сита приближается к насыщению.
8. Этот процесс повторяется, чтобы обеспечить непрерывный поток кислорода.
9. Этот процесс переключения слоев сита известен как адсорбция при переменном давлении (PSA).
10. Затем выход кислорода контролируется с помощью расходомера, где расход может быть установлен вручную в литрах в минуту (л / мин).
11. Кислород выходит через выпускное отверстие, к которому обычно подключается система доставки кислорода, такая как назальная канюля или маска, через увлажнитель.
СводкаПринцип: адсорбция при колебаниях давления.
Воздух содержит 78% азота и 21% кислорода.
Если удалить азот, в воздухе останется кислород до 95% чистоты.
Комнатный воздух всасывается в машину через компрессор.
В машине 2 молекулярных сита, которые работают попеременно.
- Слой молекулярного сита
улавливает и удаляет азот из воздуха, который втягивается в машину.
Переключающий клапан продолжает переключать вход воздуха с одного слоя сита на другой для непрерывного потока кислорода.
Азот выпускается из каждого слоя сита, как только он становится насыщенным.
Выход кислорода контролируется расходомером и доставляется пациенту через систему доставки кислорода, такую как назальная канюля или маска.
По всем вопросам, связанным с концентратором кислорода, звоните в Sweetwater Medical Central – 386-822-9223
Новый высокопроизводительный клапан для портативных систем концентраторов кислорода
Мощные портативные концентраторы кислорода с питанием от батарей – это растущая тенденция в мобильности пациентов, позволяющая все большему количеству пациентов, зависимых от кислорода, оставлять после себя громоздкие домашние системы концентраторов кислорода; более крупные старые «портативные» концентраторы; или кислородные баллоны на несколько часов. Но создание и изготовление устройств с высокой кислородной емкостью, размером и весом, легко управляемыми кислородзависимым человеком, остается серьезной инженерной проблемой.
Если говорить о производительности концентратора кислорода, размер и вес по-прежнему сильно коррелируют с производительностью. Пациенты с умеренным или серьезным заболеванием легких, которым требуется высокий и непрерывный поток кислорода, по-прежнему полагаются на громоздкие домашние устройства, большие портативные устройства или кислородные баллоны, когда они выходят на улицу.Таким образом, хотя сверхпортативные устройства предлагают большое удобство, их текущая и относительно ограниченная мощность – импульсная мощность 0,75–1,5 стандартных литров в минуту (сл / мин) – слишком мала для обслуживания многих пациентов, зависимых от кислорода.
Но это ограничение постепенно меняется. Внесение этого изменения требует, чтобы производители концентраторов и поставщики компонентов резко миниатюризировали, облегчили, сделали более прочными и снизили энергопотребление для создания устройств все меньшего размера с все большей выходной мощностью. В то время как подключаемые домашние блоки размером с шкаф могут весить 40 фунтов или более, портативные и сверхпортативные концентраторы должны упаковывать все те же основные компоненты в блоки с батарейным питанием, которые весят 15, 10 или всего 4 или 5 фунтов. . Несмотря на то, что последние ультрапортативные устройства были уменьшены до размера большого кошелька – уже чудо миниатюризации – тенденция в дизайне этих портативных устройств-концентраторов заключается в том, чтобы становиться все меньше.
Рынок есть – и он растет. Несколько месяцев назад, еще до пандемии коронавируса, отраслевые наблюдатели прогнозировали, что спрос на небольшие портативные концентраторы кислорода почти удвоится с 180000 единиц сегодня до примерно 300000 примерно к 2025 году.Это число обязательно будет расти, и в него войдут выжившие после коронавируса с респираторным поражением, что повышает вероятность кислородного лечения в более позднем возрасте.
Внутри концентратора кислорода
Концентраторы кислорода были разработаны на простой предпосылке: если атмосферный воздух состоит на 78 процентов из азота и примерно на 21 процент кислорода, почему бы не создать устройство для удаления содержания азота, «концентрирования» кислорода и упрощения процедуры акт дыхания?
С этой целью многие портативные концентраторы используют общие принципы конструкции (см. Рисунок 1).Всасываемый воздух всасывается через фильтр и сжимается с помощью воздушного компрессора перед тем, как проталкиваться через клапан переключения процесса в один из нескольких контуров, каждый из которых содержит слой сита, адсорбирующий азот. Во время цикла всасывания сжатый воздух проталкивается через слой сита, где адсорбируется азот. Оставшийся концентрированный кислород затем направляется в резервуар с «продуктом» для хранения и потребления пациентом. Затем схема сбрасывается на другой входной цикл через нагнетание насыщенного кислородом воздуха через клапан выравнивания давления для удаления накопленного азота путем выпуска этого азота из слоя сита.Два контура чередуют этот процесс, чтобы постоянно пополнять запас кислорода в резервуаре для продукта.
Теперь, когда концентрированный кислород хранится в резервуаре для продукта, «нагнетательный» клапан будет управлять потоком этого кислорода к пациенту либо непрерывным потоком, либо импульсным потоком по требованию. Нагнетательный клапан обязательно ограничен по размеру, поскольку он обычно встроен в коллектор с ограниченным пространством и весом, где он может делить пространство с другими миниатюрными соленоидными и обратными клапанами, а также с отверстиями для двунаправленного потока.
С точки зрения конструкции, поток кислорода через нагнетательный клапан в настоящее время представляет собой проблему для производителей концентраторов в дополнение к этим проблемам, связанным с размером и весом.В этих клапанах каждая особенность – отверстие, путь прохождения жидкости, кривизна, уплотнительная поверхность – представляет собой ограничение, снижающее поток для подачи кислорода. Таким образом, по мере того, как каждый компонент портативных концентраторов продолжает уменьшаться в размерах и улучшаться в возможностях, технология нагнетательного клапана создала узкое место, поскольку концентраторы производят больше кислорода, чем может быть доставлено пациенту.
Новый клапан подачи «свободного потока»
Спрос на небольшие портативные концентраторы кислорода почти удвоится в ближайшие пять лет с 180 000 единиц сегодня до примерно 300 000.(Фото: Emerson) Недавно при рассмотрении требований к новому поколению еще более легких сверхпортативных концентраторов большей емкости производитель попросил команду ASCO Emerson создать новый миниатюрный клапан подачи кислорода с высокой пропускной способностью как часть еще меньше, легче и высокоэффективный вентильный блок. Основой для нового нагнетательного клапана станет проверенный продукт – миниатюрный соленоидный клапан ASCO серии RB. Однако загвоздка заключалась в том, что новый нагнетательный клапан должен был занимать еще меньшую площадь – основание всего 10. 8 мм до 15,2 мм RB – при этом обеспечивает 130 процентов потока кислорода RB, что эквивалентно 30 л / мин при давлении всего 10 фунтов на квадратный дюйм (см. Таблицу 1).
С помощью усовершенствованного программного обеспечения для проектирования команда приступила к моделированию концепций клапана, в которых подчеркивается свободный поток. Внутри корпуса клапана меньшего размера отверстия были расширены, пути потока были расширены и упрощены, а сопротивление потоку было уменьшено. В то же время концепции были оценены с точки зрения технологичности, в частности, возможности точного и повторяемого формования их под давлением.При этом измерялись и сравнивались коэффициенты расхода, связанные с каждой концепцией корпуса клапана.
Таблица 1. Сравнение требований к нагнетательному клапану. В течение нескольких месяцев команда выбрала оптимальную конструкцию, и родился миниатюрный электромагнитный клапан ASCO Series 090. Этот клапан нового поколения представляет собой микроклапан 10,8 мм с выдающимся коэффициентом расхода (Cv) 0,077, что дает ему возможность подачи кислорода, равную 30 л / мин при давлении 10 фунтов на кв. Ширина 11 мм.Это делает его действительно первым миниатюрным соленоидным клапаном, специально оптимизированным для использования в легких портативных концентраторах кислорода. В отличие от предыдущих нагнетательных клапанов, которые жертвовали пропускной способностью в обмен на легкий вес и компактный размер, клапан серии 090 сочетает все три в новой конструкции с долговечной надежностью.
Несмотря на необходимость увеличения соотношения расхода к размеру, потребляемая мощность клапана серии 090 выгодно отличается от его предшественника. Чтобы компенсировать меньший привод клапана, в нормально закрытой серии 090 для срабатывания используется двухступенчатое напряжение «скачок и удержание» – короткий скачок для обеспечения потока, за которым следует маломощное удержание до тех пор, пока сигнал не будет удален и клапан закрывается.Общая потребляемая мощность для этого меньшего клапана немного увеличена по сравнению с серией RB в обмен на 30-процентное увеличение пропускной способности кислорода.
Заключение
В настоящее время портативные концентраторы кислорода имеют потолок непрерывного потока около 3 литров в минуту, отчасти из-за ограничений клапанов подачи кислорода низкого давления. Разработка чрезвычайно компактного, надежного миниатюрного электромагнитного клапана с высоким расходом, который увеличивает максимальный уровень подачи кислорода – с коэффициентом расхода до 0.077 Cv – устраняет этот барьер, помогая открыть путь к новому поколению чрезвычайно легких, высокопроизводительных портативных концентраторов кислорода, способных обслуживать более широкий круг пациентов, зависимых от кислорода.
Эту статью написал Джош Ньютон, менеджер по глобальному маркетингу продуктов, аналитический и медицинский сегмент, Emerson, Florham Park, NJ. Для получения дополнительной информации посетите здесь .
Medical Design Briefs Magazine
Эта статья впервые появилась в июльском выпуске журнала Medical Design Briefs за июль 2020 года.
Читать статьи в этом выпуске здесь.
Другие статьи из архивов читайте здесь.
ПОДПИСАТЬСЯ
Каталитические нейтрализаторы различных типов
Двухкомпонентные каталитические преобразователи
В этой конструкции выхлопные газы проходят через подложку, содержащую драгоценные металлы, платину и палладий, которые позволяют протекать химической реакции. Температура выхлопных газов повышается по мере того, как происходит процесс преобразования.
Из-за сильного нагрева, создаваемого этим процессом, выхлопные газы, выходящие из конвертера, должны быть горячее, чем газы, входящие в конвертер. Это также объясняет, почему на большинстве устройств требуются тепловые экраны.
Двухходовые преобразователи относительно эффективно работают на обедненной топливной смеси. Неэффективность контроля NOx (оксидов азота) привела к внедрению трехходовых преобразователей.
Трехходовые воздушные каталитические нейтрализаторы
Позволяет восстанавливать NOx (оксиды азота) до N2 (азот) и O2 (кислород)
Позволяет окислять CO (оксид углерода) до менее вредного CO2 (диоксида углерода)
Позволяет окислять HC (несгоревшие углеводороды) до CO2 (диоксид углерода) и h3O (вода)
Трехходовые воздушные преобразователи с плюсом использовались в системах выхлопа транспортных средств в Северной Америке в конце 70-х – начале 80-х годов.
Внутри этого преобразователя есть две подложки. Лицевая панель, покрытая драгоценным металлом родием, используется для уменьшения выбросов NOx в простые N2 и O2. Этот процесс наиболее эффективен, когда присутствует мало O2 (богатая смесь). Поэтому он расположен перед воздушной трубкой.
Так как богатая смесь имеет высокое содержание углеводородов и СО, воздушный насос и трубка подают дополнительный О2 в эту смесь, прежде чем она попадет во вторую подложку.
Вторая подложка, покрытая драгоценными металлами, палладием и платиной, позволяет окислять HC и CO до менее вредных выбросов CO2 и h3O.
Эта система была не очень эффективна, и ее сняли с производства в начале 80-х, когда был представлен современный трехходовой преобразователь.
Трехкомпонентные каталитические преобразователи
Трехходовые преобразователи используются в системах контроля выбросов транспортных средств в Северной Америке – и во многих других странах – с 1981 года.
Трехходовой преобразователь без использования воздуха использует передовой химический состав катализатора для хранения и выделения O2 в сочетании с мониторингом O2. и система управления.
В этой системе используется один или несколько датчиков O2 для переключения топливной смеси между бедной и богатой условиями.Это колебание в сочетании с накоплением и высвобождением O2 на поверхности катализатора позволяет оптимально снизить все три выброса.
Трехходовые преобразователи используются вместе с диагностическими системами OBDII на современных автомобилях. Эта система предупреждает водителя, когда преобразователь не работает с максимальной эффективностью.
Узнайте больше о качественных деталях выхлопной системы, найдите нужную деталь для автомобиля или найдите местную ремонтную мастерскую сегодня.
Содержание этой статьи предназначено только для информационных целей и не должно использоваться вместо обращения за профессиональной консультацией к сертифицированному технику или механику.