3D-принтер: виды, характеристики, технологии и схемы печати
3D-принтер – внешнее устройство компьютера, которое является нечем иным, как станком с числовым программным управлением (ЧПУ) предназначенным для быстрого получения прототипов изделий, спроектированных на ПК, методом послойной печати.
Основные характеристики 3D-принтера
Назначение
3D-принтеры выпускаются под конкретные задачи: архитектура, дизайн, медицина, образование, производство, протезирование, прототипирование.
Технология печати
Производители 3D-принтеров используют различные технологии печати. Чтобы у вас не возникло проблем, при выборе конкретной модели, рассмотрим основные виды 3D-печати. Именно от технологии печати зависят такие важные параметры, как минимальная и максимальная толщина слоя и скорость построения изделия. А также цена, как самого 3D-устройства, так и расходных материалов.
В зависимости от принципа создания заготовок, выделяют следующие виды 3D-печати:
- SLA — лазерная стереолитография,
- SLS (EBM, SLM) — селективное лазерное спекание,
- FDM — метод последовательного наплавления,
- DLP — технология цифрового проецирования,
- MJM — многоструйная укладка полимера.
Лазерная стереолитография
Суть SLA-технологии заключается в использовании жидкого фотополимера и специального реагента, который позволяет исходному материалу застывать под воздействием ультрафиолетового лазера.
Фотополимер заливается в ванну и нагревается до рабочей температуры. Затем в смесь погружается подвижная платформа, которая постепенно перемещается вверх. В этот момент ультрафиолетовый лазер производит засветку платформы снизу по заданным координатам, в следствие чего затвердевший полимер вначале прилипает к платформе, а последующие слои к ранее застывшему полимеру. Платформа многократно поднимается и опускается с предварительным перемешиванием фотополимера. Процесс повторяется слоем за слоем, а изделие печатается снизу-вверх.
Большинство 3D-принтеров данного вида печатают тонкими слоями, у них небольшая погрешность.
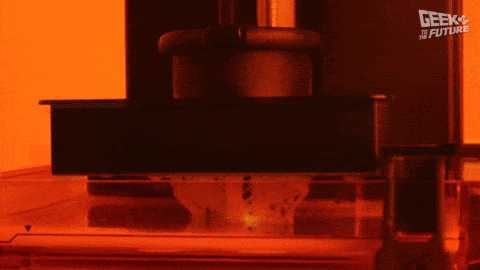
Селективное лазерное спекание
Метод SLS основан на равномерном распределении специального порошка с последующим его плавлением под воздействием лазера, в соответствии с геометрией сечения каждого слоя изделия. По завершении печати, необходимо удалить порошок, снять изделие со вспомогательных подпорок и выполнить минимальные доработки по доведению детали до кондиции.
SLS 3D-принтеры также, как и SLA-модели, обладают высокой точностью печати и приемлемым качеством изделий.
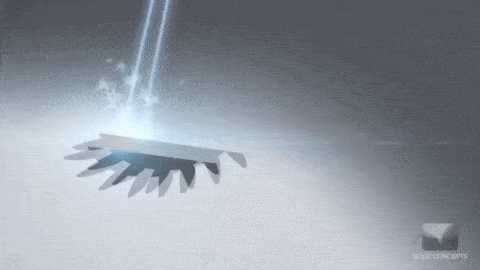
Метод последовательного наплавления
Технология FDM наиболее распространена благодаря своей простоте. В печатающую головку (экструдер) 3D-принтера, подается полимер в виде нити, который подвергается плавлению при воздействии температуры, после чего он наносится на рабочую поверхность в заданную точку координат через специальное сопло. Готовые изделия необходимо подвергать постобработке, чтобы сгладить структуру слоёв.
3D-принтеры, использующие FDM-технологию, позволяют печатать изделия различных цветов.
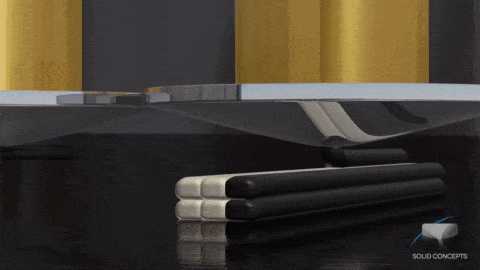
Технология цифрового проецирования
DLP метод аналогичен лазерной стереолитографии. Отличие заключает в том, что засветка платформы осуществляется проекциями слоев 3D-модели, в следствие чего смола застывает в нужных областях.
Несмотря на продвинутый подход DLP-технологии, в сравнении с SLA-технологией, есть существенный минус — изделие должно остыть после печати, что может привести к возникновению деформаций.
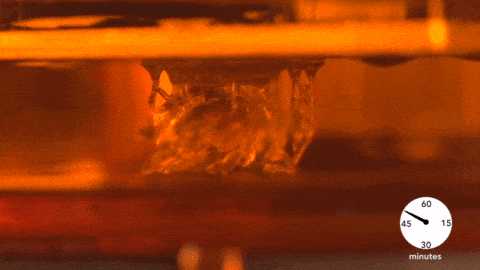
Многоструйная укладка полимера
Принцип MJM-печати заключается в послойном нанесении расплавленного материала через несколько сопел одновременно. При печати модели необходимо использовать поддерживающие элементы (подпорки).
Технология MJM позволяет печатать высокоточные изделия.
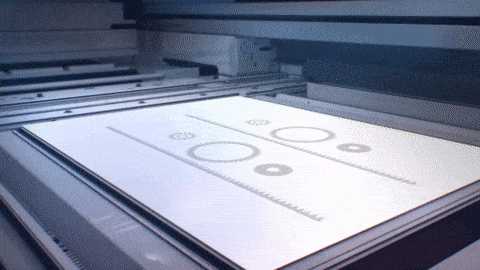
Интерфейс подключения
3D-принтеры оснащаются одним или несколькими интерфейсами подключения:
- LAN – устройство соединяется с компьютером посредствам сетевого протокола и может входить в состав проводной локальной сети,
- USB – 3D-принтер подключается к компьютеру напрямую через usb-кабель,
- Wi-Fi – ЧПУ использует беспроводной протокол передачи данных по локальной сети,
- SD – устройство имеет картридер, что позволяет осуществлять печать изделий c SD-карт.
Программные требования
Обязательно учитывайте такие параметры 3D-принтеров, как:
- совместимость с операционными системами,
- возможность использования сторонних программ,
- поддерживаемые файловые форматы.
Конструктивные особенности 3D-принтеров
Принцип работы 3D-принтера основан на законах кинематики. Выделяют несколько схем 3D-печати, исходя из перемещений платформы и печатающей головки, которые могут двигаться относительно друг друга в различных плоскостях.
Существует четыре основные схемы печати:
- дельта,
- экструдер перемещается по осям Х и Y,
- экструдер меняет положение в пространстве по осям X и Z,
- экструдер движется по осям X, Y и Z.
I схема
Платформа находится в неподвижном состоянии, положение по осям x, y, z меняет только экструдер. Особенность модели — наличие высокого каркаса. Печатающая головка размещена на трёх стержнях, каждый из которых закреплен на подвижном блоке, размещённом на опоре, с возможностью вертикального перемещения.
Плюсы: высокая скорость печати, хорошая точность.

II схема — экструдер движется по осям Х и Y
Печатающая головка находится над платформой и способна двигаться влево-вправо или вперед-назад, а платформа вверх-вниз.
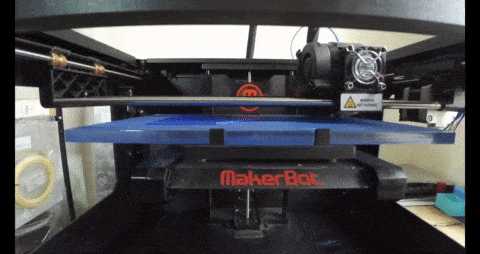
III схема — экструдер перемещается по осям X и Z
Экструдер, как в предыдущем типе, способен передвигаться влево или вправо, а также менять своё положение в пространстве по высоте. Платформа, в свою очередь, способна двигаться вперед или назад не меняя высоты.
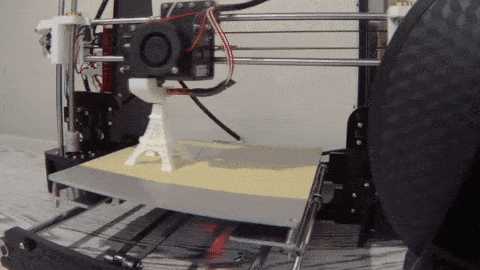
IV схема – экструдер движется по осям X, Y и Z
Последняя схема предполагает использование неподвижной платформы. Как в случае со схемой «Дельта», экструдер способен перемещаться по трём осям [x, y, z], однако в данном случае нет сложного механизма фиксации печатающей головки.
Как выбрать 3D-принтер?
Рынок переполнен дешёвыми моделями 3D-принтеров потребительского уровня с ограниченным функционалом, которые, несомненно, подойдут для печати малогабаритных изделий. Данные 3D-принтеры имеют большую погрешность в точности и низкую скорость печати. Несмотря на это, открывается возможность ознакомиться с технологией 3D-печати и сделать простые детали.
3D-принтеры начального уровня
Установки данного плана годятся для моделирования, способны печатать методом FDM, в редких случаях поддерживают технологии SLA и SLS. В комплектации предоставляется одно сопло, используются недорогие полимерные материалы. У моделей низкая скорость печати, а также отсутствуют дополнительные функции.
Плюсы:
- подходит для знакомства с оборудованием,
- простая установка,
- возможность быстрой настройки.
- открытая камера,
- поддерживает не все виды пластика.
Профессиональные 3D-принтеры
К особенностям профессиональных 3D-принтеров приписывают огромный функционал, плюс высокую скорость печати. Установки способны работать с широким спектром расходных материалов. При печати используются тонкие слои, поэтому изделия получаются гладкими.
Плюсы:
- возможность печати больших объектов,
- в комплекте несколько экструдеров,
- поддержка пластика от различных производителей.
Минусы:
- дорогая стоимость,
- сложность проведения ремонта.
2hpc.ru
Из чего состоит и как работает 3D-принтер для персонального использования
Хотите собрать своими руками 3D-принтер из отдельных комплектующих? Это не так сложно, как кажется на первый взгляд. Практически все персональные 3D-принтеры используют один и тот же подход к 3D-печати, различаясь в деталях. Их конструкция выглядит предельно просто: 4 или 5 шаговых моторов, экструдер с нагревателем и датчиком температуры, платформа с подогревом, три концевых датчика на нулевой отметке осей. Более сложные принтеры могут иметь второй экструдер с нагревателем и датчиком температуры, вентилятор для охлаждения головки, концевые датчики на максимальных отметках осей.
Подключить исполнительные механизмы и датчики напрямую к компьютеру невозможно, поэтому используется промежуточное звено – управляющий контроллер, для которого необходимо из математической 3D-модели подготовить специальный G-код – несложный набор команд, с помощью которых определяется последовательность действий принтера. Определенные типы контроллеров имеют собственный картридер со слотом под SD-карту памяти, непосредственно с которой и могут считываться G-коды. В этом случае компьютер не требуется, а для управления 3D-принтером хватает нескольких кнопок и LCD-дисплея. Управляющие контроллеры чаще всего создаются под среду разработки Arduino IDE.
Перемещение печатающей головки (экструдера) происходит в трех плоскостях – по осям X, Y и Z, для чего используются шаговые двигатели с обычной точностью 1,8° на шаг. Вспомогательными элементами являются ремни ГРМ и ролики по осям Х и Y. Зачастую применяются металлические стержни с резьбой или особые винты для точного позиционирования по оси Z. Управляемый контроллером 3D-принтер перемещает печатающую головку, выдавливающий расплавленный пластик, тем самым наплавляя модель слой за слоем.
Шаговые двигатели NEMA 17
NEMA 17 – это условное обозначение типоразмера стандартного посадочного места для различных шаговых двигателей, которое имеет размеры 1.7×1.7 дюйма (43.2×43.2 мм). Меньший типоразмер обозначается как NEMA 14 (1.4×1.4 дюйма или 35.6×35.6 мм).
Шаговые двигатели могут иметь три режима работы: полношаговый, полушаговый и микрошаговый. Во время полношагового режима шаговый двигатель проворачивает свою ось на 360 градусов, совершая 200 шагов, во время полушагового – 400, а в микрошаговом режиме каждый шаг делится еще на 4, 8 или 16 частей. Управление двигателем в микрошаговом режиме настолько сложное, что для него используются специальные контроллеры шаговых двигателей. Шаговые двигатели бывают рассчитаны на 4, 8 и 12 В.
Экструдер
Функцию равномерного распределения по рабочей поверхности пластика и других материалов выполняет экструдер, который плавит и подает через сопло термопластик (ABS или PLA) на поверхность стола. Являясь самой сложной частью 3D-принтера, экструдер состоит из привода подачи пластика и термоголовки.
Привод экструдера с помощью редукторного механизма выталкивает нить пластика диаметром 1,75 или 3 мм. В большинстве современных приводов используется шаговый двигатель для лучшего контроля подачи нити к термоголовке. Нить подается в алюминиевую термоголовку со встроенным нагревателем, где разогревается до температуры 170-260 °С, в зависимости от типа пластика, и переходя в полужидкое состояние, выдавливается из печатающей головки, диаметр отверстия которой обычно располагается в диапазоне от 0,35 до 0,5 мм.
Поверхность для печати
Рабочая поверхность, на которой формируются 3D-детали, называется столом или платформой. Её размеры варьируются в зависимости от модели принтера и обычно располагаются в диапазоне от 150 до 200 мм2. Большинство производителей 3D-принтеров предлагают подогреваемую платформу уже в комплекте, либо как дополнительную опцию. Всегда есть возможность самому сделать подогреваемую платформу из подручного материала. Задача платформы – не допустить разрывов или трещин модели, а также обеспечить надежное сцепление между первыми слоями печатаемой детали и рабочей поверхностью.
Верхняя часть платформы изготавливается из стекла или алюминия для лучшего распределения тепла по всей площади и обеспечения гладкой и ровной поверхности. Стекло дает более ровную поверхность, в то время как алюминий лучше распределяет тепло в случае подогрева. Чтобы предотвратить отрыв модели во время печати, поверхность платформы часто покрывается какой-либо липкой массой или пленкой. Такие материалы часто состоят из каптона или полиамидной ленты, в зависимости от типа пластика.
Линейный двигатель
Используемый привод (линейный мотор) во многом определяет точность и скорость печати, а также периодичность обслуживания 3D-принтера. Обычно используются гладкие, высокоточные металлические стержни для каждой оси, а также пластиковые или бронзовые шарикоподшипники для перемещения по каждому стержню. Линейные шарикоподшипники обеспечивают более долговечную и качественную работу, однако они более шумные, чем бронзовые, которые, в свою очередь, сложнее откалибровать на момент сборки.
Концевые датчики
Диапазон движения линейных приводов обычно ограничивается механическими или оптическими фиксаторами – простейшими концевыми датчиками (EndStop), которые сигнализируют о приближении головки принтера к краю рабочей поверхности, чтобы предотвратить выход ее за рамки платформы. Фиксаторы также используются для определения начала координат (0,0,0) по всем трем осям.
Строго говоря, наличие фиксаторов не является обязательным в работе 3D-принтеров, но их наличие позволяет калибровать принтер перед началом печати, что делает печать более точной и аккуратной. Концевые датчики бывают двух видов: нажимные и оптические. Оптические являются более точными, но для упрощения (например, по X-Y осям) можно воспользоваться и нажимными.
Рама принтера
То, что соединяет все описанные выше элементы в единое целое, называется рамой. Форма рамы, и особенно материал, из которого она изготовлена, довольно сильно влияют на точность и качество печати. Конструкция рамы, основанная на принципе слотов, когда пластиковые или даже фанерные листы, нарезанные лазером, соединяются гребнями в пазы, а потом скручиваются болтами и гайками, сильно упрощает сборку 3D-принтера и является более точной для калибровки, однако не способствует подавлению шумов, а крепежные элементы со временем приходится подкручивать. Если же рама содержит металлические стержни с резьбой, то аппарат получается более тихим, однако усложняется процесс сборки и калибровки.
Если вы всё же предпочтете приобрести уже готовый 3D-принтер, то обратите внимание на модели, популярные в данный момент на рынке:
Кроме того, посетив наши магазины в Москве и Санкт-Петербурге, вы сможете даже потрогать некоторые из них своими руками.
www.terraelectronica.ru
Как работает 3D принтер: объяснение на простых примерах
3D-печать распространена повсеместно. Она позволяет создать что угодно — от прототипов всевозможных изделий, до функциональных частей реактивных двигателей самолетов и космических аппаратов, от канцелярских принадлежностей и автозапчастей, до шоколадок и сувениров.
Но, как именно работают 3D-принтеры, как они создают трехмерные объекты любой возможной формы — знают еще не все. Если вы хоть раз задавались этими вопросами, то перед вами — самое простое объяснение 3D-печати.
Общие принципы 3D-печати
Принцип 3D-печати по любой существующей технологии — создание объемных объектов из совокупности плоских слоев.
Цифровая модель изделия разделяется на слои специальной программой — слайсером, а принтер печатает эти слои, один на другом, составляя из них трехмерный объект. Так, из множества слоев, получается объемная деталь.
Общий принцип один, но технологии различаются; самая распространенная и доступная среди них — FDM.
FDM
Моделирование методом послойного наплавления (FDM), также известное как производство способом наплавления нитей (FFF) — самый популярный и массовый тип 3D-печати.

Стандартное FDM-устройство работает как термоклеевой пистолет управляемый роботом, что не удивляет, ведь разработка технологии FDM когда-то начиналась с опытов с термоклеем. Пластиковый пруток проталкивается через горячее сопло, где он плавится, а выходя из него укладывается слоями. Процесс повторяется снова и снова, пока не появится готовый 3D-объект.
Единственное отличие в том, что 3D-принтеры используют не стержни термоклея, а пластиковый филамент намотанный на катушки.
Самые распространенные материалы для FDM (FFF) — пластики ABS и PLA.
Пластиковая нить, она же филамент, выпускается в такой форме для того, чтобы она могла легко плавиться при заданной температуре, но очень быстро застывать — после охлаждения всего на пару градусов. Именно это и позволяет печатать 3D изделия со сложной геометрией с высокой точностью.

Проще говоря, 3D-печать отличается от традиционной 2D-печати только тем, что повторяется снова и снова, создавая слой за слоем, один на поверхности другого. В конце концов, тысячи слоев образуют 3D-объект.

FDM-принтер на примере MakerBot Replicator 2
Стереолитография

Стереолитография использует свет для “выращивания” объектов в емкости с фотополимерной смолой. Как и в прочих технологиях 3D-печати, изделие образуется слой за слоем, здесь — при отверждении жидкого фотополимера светом.
От FDM стереолитография отличается более монолитными принтами, даже с одинаковой заданной толщиной слоя.

На фото: принты FDM и SLA, слой обеих моделей — 0,1 мм.

Дело в разнице в технологиях — фотополимерная засветка дает более аккуратные слои, чем расплавленный филамент выдавливаемый из сопла FDM-принтера.
SLA и DLP — две разновидности стереолитографии. SLA — лазерная стереолитография, DLP — цифровая проекция. Различие между ними в том, что в SLA источником света служит лазер, а в DLP — проектор.
Независимо от технических особенностей, принцип работы устройств SLA и DLP схож. Для запуска печати необходимо опустить специальную платформу построения в емкость с жидкой фотополимерной смолой.
Платформа останавливается на высоте одного слоя от дна емкости.
Происходит засветка источником света принтера.
Жидкий полимер, под воздействием света, становится твердым и прилипает к платформе построения. После этого платформа поднимается на высоту еще одного слоя и процесс повторяется.
SLA-принтер на примере Formlabs Form 2
SLA дает более гладкие поверхности, по сравнению не только с FDM, но и с DLP, о которой рассказываем далее.

Так получается потому, что DLP проецирует слои картинкой из пикселей, а луч лазера в SLA движется непрерывно, что дает ровный, не пикселизованный слой.
DLP в тех же целях использует проектор, а LED DLP — ЖК-дисплей с ультрафиолетовой подсветкой. В этих конструкциях свет проецируется на смолу по всей площади слоя одновременно, что дает преимущество в скорости, когда необходима печать крупных объектов с заполнением в 100% — полная засветка слоя происходит быстрее, чем в SLA.
Но при печати мелких или пустотелых объектов SLA быстрее, так как интенсивность засветки лазерным лучом, а значит и скорость полимеризации, выше.
DLP-принтер на примере SprintRay MoonRay S
SLS
Главное преимущество технологии перед FDM и SLA — SLS-печать не требует создания поддерживающих структур, ведь материалом поддержки служит окружающий модель материал — это позволяет печатать изделия любой формы, с любым количеством внутренних полостей, и заполнять ими весь рабочий объем принтера. SLS-принтеры работают с широким спектром материалов, а их принты прочнее, чем большинство напечатанных FDM или стереолитографией.

Благодаря прочностным характеристикам, напечатанные на SLS-принтерах детали могут использоваться в практических целях, а не только как прототипы и декоративные элементы.
Для создания объекта аппарат направляет лазер на слой мелкофракционного порошка, сплавляя частицы друг с другом для формирования слоя изделия. Затем, устройство рассыпает следующую порцию порошка на поверхность готового слоя и разравнивает его, а лазер расплавляет, создавая следующий слой изделия. Процедура повторяется до тех пор, пока печать не будет завершена.
Есть у SLS-принтеров и минус — их стоимость. Они очень дороги, по сравнению с FDM и SLA/DLP. Это связано с ценой необходимых для такой печати высокоэнергетических лазеров. В принципе, стоимость даже самых дешевых SLS-принтеров совсем недавно начиналась от $200 000.
Тем не менее, некоторые компании в настоящее время работают над тем, чтобы сделать данную технологию более доступной, поэтому есть шанс, что приобрести SLS-принтер в ближайшем будущем смогут позволить себе даже любители. Один из примеров — польская компания Sinterit.
SLS-принтер на примере Sinterit Lisa Pro
Извлеченная из SLS-принтера модель не требует удаления поддержек и может использоваться без постобработки, ее надо лишь очистить от лишнего порошка.
Polyjet

Главное преимущество технологии Polyjet в ее мультиматериальности — многие Polyjet-принтеры способны печатать объект большим количеством различных материалов одновременно, что позволяет создавать изделия состоящие из участков с разными механическими и оптическими свойствами, то есть — разной твердости и цвета. Это фирменная технология компании Stratasys.
Пример: принтер Stratasys и напечатанные на нем кроссовки.

Polyjet 3D-принтеры распыляют крошечные капельки фотополимерной смолы на поверхность и полимеризуют их ультрафиолетовым излучением.
Этот процесс повторяется до тех пор, пока не будет создан объект. В отличие от FDM-принтеров, Polyjet-устройства могут наносить материал из многочисленных сопел одновременно.
Polyjet-принтер на примере Stratasys J750
Заключение
Прочитав эту статью, вы ознакомились с принципами и примерами работы 3D-принтеров функционирующих по самым распространенным технологиям.
Существуют и другие технологии, в основном — связанные с 3D-печатью металлами, но они используются только в промышленности. О них мы поговорим отдельно.
Чтобы выбрать 3D-печатное оборудование и материалы для любых задач обращайтесь в Top 3D Shop — проконсультируем, подберем максимально подходящую технику и расходники, оформим заказ, доставим, установим и научим.
top3dshop.ru
3d-принтер (конструкция, виды, производители) | Wiki 3DP
3D-принтер — это периферийное устройство, осуществляющее 3D-печать методом послойного формирования физического объекта по заданной цифровой 3D-модели.
Благодаря определенной простоте базовой конструкции оборудования, позволяющего осуществлять объемную печать, разработки в данной области ведутся как простыми людьми – энтузиастами 3d-печати (фактически каждый может собрать свой собственный 3d-принтер своими руками), так и крупными отраслевыми компаниями и центрами разработки.
Современные 3d-принтеры могут печатать как различными полимерными материалами (основная доля расходных материалов), так и металлом, специализированными строительными составами, продуктами питания и био-материалами.
3д-принтеры уже сегодня применяются как для бытового так и для профессионального прототипирования объектов. На сегодняшний день помимо условно “стандартных” образцов оборудования, имеются разработки и конструкции, осуществляющие печать еды, принтеры применяемые в медицине и принтеры способные печатать малоэтажные дома и небольшие конструкции.
Также отметим, что 3д-принтеры в частности и 3д-печать в целом активно используются в образовании, робототехнике и ряде других социально-значимых и инновационно-перспективных направлений.
Следует отметить, что 3d-принтеры – это одна из немногих категорий оборудования имеющих реальную возможность к самовоспроизведению (в частности, проект RepRap).[1]
Виды 3d-принтеров
Классификация 3д-принтеров ведется по нескольким ключевым параметрам, основными из которых являются: применяемая технология 3d-печати; материал печати; уровень качества и стабильности размеров получаемых изделий.
В последнем случае различают домашний (настольный) 3d-принтер и 3d-принтер профессионального класса, демонстрирующий более стабильные размеры напечатанных объектов, повышенную производительность (скорость печати) и качество прототипирования. Оборудование профессионального класса активно применяется в различных конструкторских бюро (с целью создания моделей и прототипов разрабатываемой продукции или конструкций), а также для целей мелкосерийного производства широкой гаммы изделий (сувенирная продукция, индивидуализированные корпуса электроники и тому подобное).
Типовая конструкция 3d-принтера
Индустрия 3D-печати переживает в настоящий момент этап бурного роста и развития, что привело к тому, что на сегодняшний день на рынке присутствует крайне широкая и весьма пестрая гамма образцов оборудования: от любительских принтеров, собранных своими руками в единичном экземпляре из подсобных деталей и элементов, до промышленных образцов, способных создавать высокоточные копии объектов с весьма сложной геометрией.
В целом, устройство 3D-принтеров на самом деле не очень сложное. Главные проблемы при изготовлении принтеров – обеспечить точность сборки и дальнейшей точности позиционирования по всем осям для экструдера, чтобы обеспечить качество печати.
Для того чтобы представить типовую конструкцию 3д-принтера рассмотрим самую распространенную (в настоящее время) технологию объемной печати – FDM (метод послойного наплавления).

Типовая конструкция 3D-принтера печатающего по методу послойного наплавления (FDM). (Визуализация: 3D Today)
3d-принтер состоит из:
- Корпус, играющий роль скелета для монтажа конструкционных элементов;
- Направляющие, осуществляющие сравнительно свободное перемещение печатающей головки в заданном пространстве;
- Печатающая головка (экструдер) – группа частей, которая выполняет подачу, нагрев и вытеснение (экструзию) расходного материала через сопло на рабочую поверхность;
- Шаговые двигатели – элементы конструкции 3д-принтера, отвечающие за равномерное перемещение печатающей головки в заданном пространстве;
- Рабочий стол – строительная платформа 3D-принтера, на которой и осуществляется непосредственное создание трёхмерного объекта;
- Электроника – набор элементов, отвечающий за управление и координацию действий принтера в процессе печати.
Подробнее остановимся на некоторых (наиболее важных) элементах базовой конструкции 3д-принтера[2].
Экструдер (печатающая головка) 3d-принтера
Наиболее важный элемент конструкции данного вида оборудования. Экструдер 3д-принтера – это узел, который обеспечивает подачу расплавленного пластика в рабочую зону аппарата. На сегодняшний день уже имеется огромное количество различных конструкторских решений.
В частности, имеются образцы оборудования оснащенные сменными соплами различного диаметра. Также есть варианты принтеров с двумя экструдерами в конструкции. Такие образцы способные печатать двумя цветами или осуществлять печать поддержек растворяемым пластиком PVA или HIPS.
Обслуживание экструдера 3д-принтера состоит в его очистке снаружи от налипших в процессе печати кусочков пластика. Иногда, обычно при работе с некачественными расходными материалами, сопло экструдера может довольно сильно засоряться – в этом случае приходится проводить его чистку.
Рабочий стол 3д-принтера
Стол может быть как нагреваемым, так и без такового. Для калибровки стола применяются либо автоматические приводы (автоматическая калибровка) или подпружиненные болты (ручная регулировка). Покрыт обычно стеклом, хотя есть варианты 3д-принтеров и с перфорированной платформой. Для нагреваемого стола еще добавляется и нагреваемый элемент.
Обслуживание данного элемента конструкции заключается в его калибровке и регулярной чистке поверхности.
Электроника и управление
Плата управления может находиться в корпусе. Большинство 3d-принтеров имеют плату на основе RAMPS. Но есть и варианты со своими решениями. Обычно достаточно проверять работает ли кулер охлаждения (если он необходим в данной конструкции).
Что касается экрана управления 3д-принтером, то он, следует отметить, присутствует отнюдь не на всех моделях данной категории оборудования. Обычно он есть там, где есть возможность печатать с SD карты.
Принцип работы 3д-принтера
Как уже было замечено, на сегодняшний день в индустрии насчитывается уже несколько подвидов методов 3д-печати, а также весьма обширный набор соответствующего оборудования и конструкций.
Для того, чтобы рассмотреть принцип работы 3d-принтера обратимся к его ключевому элементу (головке экструдера) и методу объемной печати, использующей пластиковую нить.
Процесс 3д-печати:
Нить (филамент) поступает в печатающую головку (экструдер), после чего осуществляется разогрев нити до ее жидкого состояния. Далее полученная масса выдавливается через сопло экструдера. При этом шаговые двигатели с помощью зубчатых ремней приводят в движение Экструдер, который перемещается по направляющим в заданном направлении и наносит пластик на платформу слой за слоем согласно заданной модели.[3]
3d-принтер – производители
Технология 3d-печати с одной стороны еще находится на этапе своего зарождения и становления, с другой стороны базируется на весьма проработанных технологических решениях из ряда других областей (в частности, экструзии полимеров). Данные обстоятельства в совокупности с развитием интернета, значительно ускорившего и упростившего обмен информацией в мировых масштабах, привели к тому, что теми или иными успехами в области разработки, конструирования и производства оборудования для 3d-печати могут похвастаться очень многие компании по всему миру.
Подавляющее большинство таких компаний (на сегодняшний день) занимается сборкой оборудования из готовых конструкционных элементов по находящимся в свободном доступе конструкторским схемам с минимальными изменениями и новациями. Однако на рынке уже есть и свое лидеры, – относительно крупные компании, сравнительно (учитывая возраст самого рынка 3д-печати) давно работающие в данной области. Список наиболее заметных из них представлен ниже.
Ведущие производители:
- 3D Systems (США);
- EnvisionTEC (Германия);
- Stratasys (США);
- MX3D (Нидерланды);
- Rapid Shape (Германия);
- DWS s.r.l. (Италия);
- Wuhan Binhu Mechanical & Electrical (Китай);
- MakerBot Industries (США);
- RepRapPro (Великобритания);
- Magnum (Россия);
- Ultimaker (Нидерланды);
- PICASO 3D (Россия).
В общем и целом свое разработчики и (или) производители 3д-принтеров имеются практически в каждой цивилизованной стране мира. По различным оценкам экспертов и аналитиков, на сегодняшний день в мире можно купить 3d-принтер по меньшей мере от 300 компаний.
В Европе (как можно заметить из приведенного выше списка) центральное место занимают немецкие, голландские и итальянские компании, что вполне коррелирует с тем какое место на международном рынке занимают местные компании-производители оборудования для переработки полимеров. Также заметное место на мировом рынке аддитивных технологий занимает и Великобритания, где по разным оценкам насчитывается как минимум 15 компаний, разрабатывающих и изготавливающих оборудование для объемной печати.
В Азии безусловным лидером рынка выступают китайские компании. Однако и кроме них здесь есть заметные игроки и из других стран региона: Индия, Япония, Южная Корея, Тайвань и даже Таиланд и Гонконг.
На постсоветском пространстве безусловным лидером по количеству отраслевых компаний, работающих в области разработки и изготовления 3d-принтеров и вспомогательного оборудования, выступает Российская Федерация, на территории которой (по различным оценкам) уместилось по меньшей мере 36 предприятий, главные из которых представлены выше. Также следует отметить, что свое отраслевые фирмы имеются в Украине, Беларуси, Литве и Латвии.
В Северной Америке, помимо мирового лидера – США, свое функционеры в области разработки, производства и внедрения оборудования для печати 3dp присутствуют и в Канаде.
В заключении отметим, что есть свое компании-производители и в таких странах, как Израиль; Бразилия, Новая Зеландия и Австралия, хотя их можно в прямом смысле слова “пересчитать по пальцам” и заметного влияния на мировой рынок они (на данный момент) не оказывают.
Узнать больше про 3d-принтер:
Также, для получения более полной картины по тематике 3д-печати в целом и 3д-принтеров в частности рекомендуем воспользоваться поиском по сайту (вверху страницы).
mplast.by
Принцип устройства и работы 3D принтера
Сегодня трехмерной печатью удивить можно, пожалуй, только маленького ребенка. Метод 3Д моделирования запросто используется в личных или коммерческих целях, а многие современные предприятия уже не могут обойтись без такого принтера. Сама технология была создана довольно давно, однако, мало кто задумывался каков принцип действия 3Д принтера. В этой статье речь пойдет как об устройстве, так и о распространенных методах этого вида моделирования.

Устройство принтера для 3Д печати
О чём пойдет речь:
Из чего состоит
Тип устройства принтера для 3Д печати похож со своим собратом, изготавливающим любые изображения в формате 2Д. Основным отличием считается способность продвинутого принтера печатать объемные элементы. Так, к привычной длине и ширине, здесь добавляется еще и глубина. Нужно понимать, что абсолютно все 3D принтеры имеют одинаковый набор рабочих элементов.

Принцип работы 3D-принтеров DLP или SLA на смолах
Любое устройство, печатающее в трех плоскостях, состоит из таких рабочих элементов:
- Экструдер. Он нагревает и выдавливает вязкий пластик;
- Платформа. Основа, на которой проходит процесс;
- Мотор. Он двигает необходимые элементы принтера;
- Фиксаторы. Специальные датчики, стопорящие подвижные части принтера во время работы. Они не позволяют выйти за границы платформы;
- Рама;
- Картезианский робот. Устройство, способное двигаться по 3-м осям.
Зная устройство машины, становится понятен принцип работы 3Д принтера. Конечно, это основные рабочие узлы, принимающие непосредственное участие в создании трехмерных конструкций.

Устройство 3D-принтера
Как работает
Всего различают несколько основных технологий 3Д печати:
- Метод постепенного наслоения пластика.
- Стереолитографическое моделирование.
- Лазерное спекание.
Эти методы были названы от более популярного к менее распространенному. И сейчас кратко расскажем о каждом из них.

Схематическое изображение 3D-принтера
Метод послойного наплавления термопласта
Большинство 3Д принтеров работает с термопластиком, в том числе с полилактидом. Он отличается природным происхождением и неспособностью выделять вредные вещества. Работа заключается в подаче тонкой нити вязкого пластика в трубу сопла. Она и формирует необходимый элемент.

Метод послойного наплавления термопласта
Стереолитографическая печать
Эта технология широко применяется в стоматологии. С ее помощью изготавливают зубные протезы. Главным преимуществом таких принтеров считается высокое качество изготовленных конструкций. К тому же эти установки гораздо дешевле. Они не нуждаются в зеркалах, что делает устройство гораздо проще.

Тереолитографический лазерный 3D-принтер
Лазерное спекание
Для этой технологии используют легко плавящийся пластик. Мощный луч прорисовывает объект. Это действие спекает материал. И так слой за слоем проходит моделирование выбранного элемента. После завершения печати остатки материала просто отряхиваются. Минусов этого метода считается пористая поверхность изделия.

Селективное лазерное спекание
Управление работой принтера и ПО
Основные процессы регулируются с помощью ПК:
- температура сопла;
- скорость подачи пластиковой нити;
- работа мотора.
Базовой системой 3Д принтеров сегодня считается Arduino с открытой архитектурой. А программа должна выбираться в зависимости от конкретной модели машины. Чаще всего, изготовители рекомендуют использовать только фирменное программное обеспечение.
Сегодня 3Д принтер можно рассматривать как специализированное оснащение для специалистов, которые смогут решить массу задач с помощью этого устройства.
printergid.ru
Конструкция FDM-принтеров
Терминология, составные части, возможные проблемы и способы их решенияМы уже довольно подробно рассмотрели FDM-технологию 3D-печати (Fused Deposition Modeling — послойное наплавление или моделирование методом осаждения расплавленной нити) и используемые расходные материалы, а также выяснили причины, по которым FDM-принтеры стали в настоящее время столь распространенными и популярными. Теперь пришло время познакомиться с принятой терминологией и рассмотреть составные части и особенности конструкции таких 3D-принтеров.
Печатающая головка: экструдер и hot-end
Наиболее важная часть любого принтера, будь то струйный 2D или Fused Deposition Modeling 3D, это печатающая головка. В данном случае она состоит из нагревателя, в котором пластиковая нить (иногда используется не нить, а пруток) расплавляется и затем выдавливается через сопло с отверстием малого диаметра — обычно в пределах 0,15–0,5 мм, а также механизма, обеспечивающего дозированную подачу нити в нагреватель. Подающий механизм принято называть экструдером (от англ. extrude — выталкивать, т.е. extruder — толкатель), а нагреватель с соплом называют хот-энд (hot-end; по аналогии экструдер иногда называют cold-end). Порой всю печатающую головку, включая hot-end и cold-end, для краткости называют экструдером, что не совсем правильно: экструдер лишь самая крупная часть головки.
Напомним, что нить или прутки поставляются двух диаметров: 1,75 и 3,0 мм. Экструдер может работать только с каким-то одним диаметром, который надо уточнять в спецификации принтера и учитывать при покупке расходных материалов. Для подачи нити используются шаговый двигатель и система шестеренок и валов. Управляющий двигателем контроллер обеспечивает не только нужную скорость подачи нити, но и обратное действие — ее извлечение, например, при смене материала.
Естественно, температура hot-end контролируется термистором, поэтому к этой части головки всегда подходят четыре провода: два потолще к нагревателю и два потоньше к термистору.
Поскольку рабочая температура большинства материалов достаточно высока — 200–250 °C, а порой и выше, то приходится принимать меры, чтобы обеспечить расплавление нити именно в сопле и избежать нагрева экструдера, в котором могут быть пластиковые детали.
Для этого устанавливают радиаторы между hot-end и cold-end, экструдер дополнительно охлаждают небольшим вентилятором, а также используют «тепловые барьеры» (thermal break, thermal barrier): прокладки из вещества с малой теплопроводностью, в качестве которого может использоваться политетрафторэтилен (PTFE, также известный как тефлон и фторопласт) или полиэфирэфиркетон (ПЭЭК, латиницей PEEK). Поскольку при работе с некоторыми материалами температура hot-end может приближаться к 300 °C, то прокладки должны выдерживать такую температуру не только без значительных деформаций, но и без выделения токсичных веществ. В отношении тефлона в этом плане бытуют подозрения, обоснованность которых мы обсуждать не будем и лишь скажем, что в любом случае работать с FDM-принтером лучше в хорошо проветриваемом помещении.
Трубки из PTFE или PEEK используют еще и для снижения трения между нитью и стенками отверстия нагревателя, на входе в которое пластик нити еще твердый, затем, по мере продвижения к более нагретой зоне, он проходит температуру стеклования, и лишь в области с наиболее высокой температурой переходит в расплавленное состояние. В зоне стеклования, где материал нити уже не твердый, но еще не жидкий, наблюдается высокое сопротивление проталкиванию нити, поэтому крайне желательно, чтобы трубка доходила до точки, в которой нить уже расплавлена.
Сопло считается расходным материалом: его отверстие со временем засоряется, покрываясь нагаром, и приходится либо чистить (что непросто, особенно если отверстие диаметром 0,15 мм), либо заменять сопло. Поэтому крайне желательно, чтобы сопло было не просто сменным, а еще и заменялось без особых хлопот, для чего используют резьбовое соединение. Сопла разных принтеров далеко не всегда взаимозаменяемы: шаг и диаметр резьбы могут быть разными, к тому же сама резьба на сопле может быть не только внешней, как на фото, но и внутренней.
Печатающая головка не обязательно бывает одна: есть немало принтеров с двумя головками. Они позволяют использовать при печати сразу два материала — например, один для собственно модели, а второй, легко удаляемый, для поддерживающих структур, о чем мы писали в обзоре технологий.
Рабочий стол
Следующая важная деталь — рабочий стол или платформа (print bed), на поверхности которой и формируется создаваемая модель. Для рабочего стола нужно обеспечить возможность достаточно точной юстировки, чтобы расстояние между его верхней плоскостью и выходным отверстием сопла по всей рабочей площади было одинаковым. С другой стороны, стол должен двигаться, поэтому к нему нужно жестко крепить конструктивные элементы, обеспечивающие перемещение. Поэтому часто платформа представляет собой двухслойный «бутерброд», к нижней части которого не предъявляется особых требований — она лишь служит для крепления таких элементов и является основой, на которой располагается юстируемая рабочая поверхность, на которой как раз и будет создаваться 3D-модель. Именно об этой части платформы мы и будем говорить далее. Добавим лишь, что в некоторых прототипах, созданных в рамках проекта RepRap, нижняя часть рабочего стола может изготавливаться из самых доступных материалов — МДФ или фанеры.
Очень желательно, чтобы крепление верхней части стола было не жестким, а подпружиненным: при этом, в частности, не так критичны небольшие ошибки в юстировке, когда в какой-то позиции зазор между выходным отверстием сопла и поверхностью платформы становится слишком малым, а то и вовсе переходит в область отрицательных величин.
В качестве материала для платформы используют разные материалы: стекло, акрил, алюминий. И почти всегда приходится решать одну из самых частых проблем FDM-печати — надежную фиксацию первого слоя модели на платформе, поскольку используемые для печати пластики плохо прилипают к алюминию или стеклу. Это решается разными способами: перфорацией платформы, нанесением покрытия, подогревом стола, а также комбинацией этих методов.
Для покрытия нужны материалы, не только обеспечивающие хорошую адгезию, но и выдерживающие температуру расплавленной нити при нанесении первых слоев. Часто используют каптон (Kapton) — тонкую пленку желтого цвета из полиимида, выдерживающую температуру до 400 °C. Для принтеров используется каптон в виде самоклеящейся ленты шириной от 5 до 200 мм, отрезками которой, наклеенными встык, покрывается рабочая поверхность платформы. Конечно, использовать для этого 5-миллиметровую ленту затруднительно — слишком много отрезков придется наклеивать, а 200-миллиметровую сложнее наклеить ровно, поэтому чаще используют промежуточные значения.
Другой распространенный вариант — синий скотч или Scotch Blue Tape на основе полипропилена, выпускаемый фирмой 3M. Вообще-то он предназначен для малярных и упаковочных работ (им, например, часто защищают глянцевые детали различных изделий), но высокая термостойкость сделала его пригодным для FDM-печати.
Для справки: артикул синего скотча 2090, а последующие цифры определяют примерную ширину рулона в дюймах: 2090-.75A — 18 мм, 2090-1А — 24 мм, 2090-1.5А — 36 мм, 2090-2А — 48 мм; есть еще 2090-CM, предназначенный для углов. Длина рулона 55 м.
Достоинство покрытия, состоящего из отдельных полос, в том, что его по мере износа или при повреждениях можно заменять частями, а не целиком.
Есть и другие варианты, включая «доморощенные» — нанесение лака для волос. Еще один материал, самоклеящаяся пленка для лазерных принтеров, использован в принтере PrintBox3D One, о чем мы расскажем в свое время.
Но даже наличие покрытия не обеспечивает должную адгезию для большинства расходных материалов, поэтому платформу приходится подогревать, для чего в ряде моделей на нижней части рабочего стола размещается электрический нагреватель — из нихромовой проволоки, или выполненный в виде печатных проводников, или даже просто в виде нескольких мощных низкоомных резисторов.
Этот нагреватель также контролируется термистором. Прогрев платформы должен быть равномерным, что может обеспечиваться достаточной толщиной самой платформы, но при этом желательно, чтобы рабочий стол нагревался достаточно быстро — не за секунды, конечно, но хотя бы в пределах минуты-двух. А такой популярный пластик, как ABS, требует подогрева до температуры свыше ста градусов, поэтому нагреватель должен быть достаточно мощным.
Подогрев стола нужен еще и для уменьшения температурного градиента между первыми из напечатанных слоев и теми, которые созданы только что. Нижние слои начинают остывать, и особенно быстро, если они соприкасаются с гораздо более массивной платформой, имеющей комнатную температуру. При этом возникают деформации, из-за которых модель может начать выгибаться, а порой и просто отрывается от стола. Поэтому подогрев желателен даже при работе с материалами, адгезия которых к поверхности стола мало зависит от температуры этой поверхности.
Отметим, что и нагреватель, и термистор располагаются с нижней стороны платформы, поэтому контролируется температура именно этой стороны, а деталь будет располагаться на верхней. Поэтому лучше не торопиться и подождать немного, чтобы платформа прогрелась целиком, особенно если она сделана из достаточно толстого материала.
Механизмы перемещения
Во время печати и головка, и платформа должны двигаться. Для этого нужны как механизмы, реализующие собственно перемещение (двигатели), так и направляющие, обеспечивающие точность перемещения.
Обычно головка перемещается по одной из горизонтальных осей, а движение по вертикали и по второй горизонтальной оси обеспечивается движением рабочего стола. Таким образом, нужны три двигателя. Как и в экструдере, используются шаговые двигатели, обычно имеющие шаг в 1,8 градуса, т.е. 200 шагов на полный оборот. Это полношаговый режим, есть еще полушаговый и микрошаговый, который и используют для повышения точности перемещения — управляющая двигателем электроника добавляет некоторое количество промежуточных шагов, причем зачастую значительное: наиболее популярные контроллеры обеспечивают деление шага двигателя на 4, 8 и даже 16 частей, и тогда полный оборот ротора двигателя будет соответствовать уже 3200 микрошагам.
Вращение роторов двигателей нужно преобразовать в поступательные движения головки и рабочего стола. Для этого используются либо системы шкивов и зубчатых ремней, либо валы с резьбой. Передача с помощью вала обходится дешевле, но она не может обеспечить точность позиционирования при высоких скоростях, поэтому чаще всего ее используют для вертикального перемещения платформы, которое происходит достаточно медленно, и лишь в дешевых моделях применяют еще и для движений в горизонтальной плоскости.
Направляющие используют цилиндрические в дешевых моделях и линейные в более дорогих. Материал, естественно, сталь, а к точности изготовления и чистоте обработки предъявляются высокие требования, потому что от этого напрямую будет зависеть точность печати.
Сложная по конструкции и прочная платформа будет иметь немалую массу, что создаст серьезную нагрузку на двигатель, обеспечивающий ее перемещение в горизонтальной плоскости (в вертикальном направлении перемещение и более медленное, и не постоянное). Двигатель будет нагреваться, из-за чего в какой-то момент могут начаться пропуски шагов и другие неприятности. Поэтому рабочий стол стараются максимально облегчить — конечно, не в ущерб прочности, скорость печати порой приходится ограничивать и принимать меры к нормализации теплового режима двигателя (например, обеспечив тепловой контакт с массивной металлической рамой).
Крайние позиции перемещения как головки, так и платформы контролируются установленными в соответствующих местах датчиками. В простейшем случае датчиком может быть механический замыкатель или размыкатель, но и точность, и надежность такого датчика не всегда достаточны, поэтому порой используют оптические (светодиод и фотодиод, в нужный момент зазор между ними перекрывается шторкой) или магнитные, на датчиках Холла.
Температурный режим модели
Есть и еще один момент, который учитывается во многих принтерах. Он связан с тем, что пластик, вышедший из сопла, застывает не сразу, а потому подвержен деформациям. Особенно это критично при наличии так называемых «мостов» — протяженных горизонтальных перемычек, имеющих опоры только по краям: нити еще не застывшего пластика неизбежно провисают, что потребует создания дополнительных поддерживающих структур, которые потом придется удалять. Но даже если «мостов» в модели нет, то может возникать заворачивание углов с малым радиусом кривизны (curling corners), а на элементах небольшого размера — оплывание предыдущего слоя, который не успел отвердеть до момента нанесения следующего.
До известной степени избежать подобных проблем можно, если принять меры к скорейшему отверждению пластика, а это можно сделать одним способом: охлаждением с помощью дополнительного вентилятора, одного или нескольких. Выбрать вентилятор несложно, есть множество моделей разного размера, предназначенных для компьютеров; управлять скоростью их вращения тоже не составляет труда, зато выбор места размещения самого вентилятора и правильного направления потока воздуха от него — это целое искусство. В этом отношении FDM-печать имеет неприятную двойственность: с одной стороны, нужно быстро охладить выдавленный из сопла пластик, а с другой — делать это нужно равномерно, чтобы одна сторона модели не охлаждалась быстрее другой, иначе неизбежны термические деформации. К тому же охлаждающий поток воздуха не должен заметно влиять на те элементы принтера, которые должны иметь постоянную высокую температуру: хот-энд и подогреваемый стол.
Поэтому FDM-принтер «боится» сквозняков, и некоторые модели даже снабжают защитным кожухом, который при домашнем использовании заодно помогает ограничить доступ детей к опасным частям аппарата. Но под кожухом образуется замкнутое пространство, подогреваемое и хот-эндом, и нагретой платформой, и работающими двигателями, и остывающим пластиком уже созданной части модели, что замедляет отверждение выдавленной нити и приводит к еще большим деформациям.
Рама
Конечно, все перечисленные компоненты должны располагаться на достаточно прочной и жесткой раме, обеспечивающей в долговременном плане сохранение геометрии и отсутствие люфтов независимо от различных неблагоприятных условий — температуры и влажности окружающей среды, а также вибраций, возникающих во время печати.
Зачастую для рамы используют недорогой алюминиевый профиль, например, используемый в качестве мебельной фурнитуры, а порой и обычные стержни с резьбой, которые можно купить в магазинах стройматериалов. Они соединяются в единое целое с помощью изготовленных из пластика муфт, хомутов и других элементов, скрепляемых гайками и болтами. Подобное допустимо лишь в самодельных принтерах, где во главу угла ставится минимальная себестоимость конструктивных элементов и их максимальная доступность в продаже.
В некоторых моделях, в том числе «заводских», рама сделана из оргстекла или фанеры, причем особо подчеркивается, что фанерные элементы сделаны лазерной резкой; конечно, никакой лазер не сделает фанеру металлом, поэтому весьма сомнительны и долговечность подобных конструкций, и отсутствие проблем при работе с такими принтерами.
Электронные блоки
Теперь переходим к управляющей электронике.
Управляет работой всех компонентов принтера контроллер, в который поступает программа на языке G-code. Она генерируется на основе подготовленного в каком-либо 3D-редакторе STL-файла, описывающего будущую модель. G-code достаточно прост для восприятия: в строчках программы содержатся команды на перемещение головки и платформы, включение-выключение нагревателей и вентиляторов, поэтому для более-менее опытного специалиста не составляет проблемы внести правку в готовый код.
Подавляющее большинство контроллеров 3D-принтеров работает на платформе Arduino, имеющей открытые архитектуру и программный код. Язык программирования основан на C/C++ и прост в освоении, а среда программирования Arduino подразумевает работу через USB-порт без всяких дополнительных программаторов.
В качестве аппаратной части Arduino с самых ранних версий использовались и до сих пор используются распространенные и относительно недорогие микроконтроллеры Atmel: ATmega32u4, ATmega328, ATmega2560, ATmega1280 и т.п., а в последних разработках применен 32bit-микропроцессор Cortex-M3 ARM SAM3U4E. В FDM-принтерах чаще встречается ATmega2560.
Для управления различными устройствами (в 3D-принтерах это двигатели, нагреватели, вентиляторы) и получения данных (с термисторов и датчиков крайних положений) используются дополнительные модули, прежде всего драйверы шаговых двигателей, способные обеспечить соответствующие выходные токи и работу в микрошаговом режиме.
Для удобства сопряжения таких модулей с платой микроконтроллера используются промежуточные платы RAMPS (RepRap Arduino Mega Pololu Shield, где Pololu — название фирмы, специализирующейся на выпуске комплектующих для робототехники). Эти платы бывают разных версий, в настоящее время самой распространенной является RAMPS 1.4 с smd-компонентами. Такая плата с одной стороны имеет группы штыревых разъемов для соединения с платой микроконтроллера, а с другой — разъемы для подключения модулей и внешнего оборудования (двигателей, нагревателей, термисторов). В результате получается единый компактный блок, который после загрузки в микроконтроллер управляющей прошивки готов работать в составе FDM-принтера.
Некоторые принтеры управляются только через компьютер (обычно через USB-порт, но встречаются модели с подключением по сети Wi-Fi), а другие имеют собственную панель управления, с помощью которой в простейшем случае можно осуществлять контроль температур по ЖК-индикатору, запускать и останавливать печать, а в более продвинутых вариантах еще и производить калибровку, загружать и выгружать пластиковую нить. Встречаются принтеры со встроенным картоводом для SD-карт или портом для накопителей USB-флэш, через которые можно загружать файл с последующей печатью модели без участия компьютера. Всё это обеспечивается «навешиванием» на микроконтроллер соответствующих модулей и, конечно, реализацией на микропрограммном уровне в прошивке.
От контроллера к печатающей головке, даже если она одна, подходит толстый пучок проводов: к шаговому двигателю, к нагревателю и термистору хот-энда, возможно — к вентилятору экструдера (при наличии). Еще один подобный пучок соединяет контроллер с рабочим столом. Конечно, можно просто стянуть провода стяжками, что и делается в самых бюджетных самодельных конструкциях, но главное: оба эти элемента постоянно перемещаются, и даже при достаточной длине пучков есть реальная опасность, что какой-то провод либо попадет в движущиеся части, либо через какое-то время просто перетрется или обломится. Поэтому эти провода укладывают в специальные гибкие оболочки, обеспечивающие свободное перемещение головки и рабочего стола, но в то же время страхующие от обрывов и замыканий.
Понятно, что принтер не будет работать без питания. Причем если для питания электронных схем зачастую вполне достаточно возможностей USB-порта, к которому обычно подключается принтер, то для двигателей и особенно нагревателей (хотя бы hot-end, если подогрев стола не предусмотрен) без блока питания соответствующей мощности не обойтись.
Поскольку процесс печати бывает очень длительным — время изготовления сложных моделей может занять 10–15 часов и более, то желательно позаботиться и о бесперебойном питании как самого принтера, так и компьютера, к которому он подключен (если, конечно, рабочие коды не загружаются с встроенного в принтер картовода). Понятно, что суммарное потребление энергии будет немалым, и подобрать ИБП, способный обеспечить работу в течение многих часов, и непросто, и дорого, но нужно хотя бы принять меры против сильных импульсных помех на линии электропитания, к которой подключен принтер, и отключить в управляющем компьютере переход в режим энергосбережения — кроме, конечно, гашения экрана.
Иллюстрации получены из различных источников в интернете
www.ixbt.com
3D печать для самых новеньких. От А до Я. Кинематика.
В данной статье мы разберемся, что такое 3D печать и какая бывает кинематика 3D принтеров.1. 3D печать. Какая она на вкус?
Технологий печати существует большое множество, от FDM (FFF), по которой печатает больше 90% принтеров на данном портале, до SLA/DLP/LCD (с фотополимерами) и SLS/SLM (спекание порошка с помощью мощных лазеров)Нас на начальном этапе интересует FDM – послойное наплавление расплавленного прутка. На картинке ниже изображен хотенд (Hot end) – та часть экструдера 3D принтера, где происходит расплавление прутка.
Пластиковый пруток подается через тефлоновую трубку и радиатор в термобарьер, и через него в нагревательный блок. Там плавится и выходит через сопло. Сопло имеет определенный диаметр, который маркируется на нем.
Часто его делают из латуни, так как материал недорогой,легко обрабатывается. От сопла зависит точность печати. Чем меньше сопло, тем больше ниточек укладывается в один мм.
Нагреватель и терморезистор образуют обратную связь для контроля и регулировки температуры. То есть подача напряжения на нагреватель зависит от того какую температуру показывает терморезистор, а процессор сравнивает ее с заданной.
Далее видим нагревательный блок. В него с одной стороны вкручивается сопло, а с другой – термобарьер.Термобарьер служит для того,что бы минимизировать нагрев пластика выше термоблока.
[IMG]http://3d-makers.nethouse.ru/static/img/0000/0002/6151/26151635.2ofdbr37y8.W665.jpg[/IMG]Наиболее часто выполняется из нержавеющей стали. У нее теплопроводность ниже, чем у обычной,нелегированной стали. Для предотвращения плавления прутка выше термоблока сверху на термобарьер накручивается радиатор и обдувается кулером. Все достаточно просто.
Очень часто возникает протечка расплавленного пластика через резьбу.
Это означает, что сопло не поджало термобарьер в нагревательном блоке. Поэтому при разборке и сборке хотэнда вкручиваем сначала термобарьер в нагревательный блок, а потом поджимаем соплом. Если у вас при закручивании сопла остается зазор между торцем сопла и нагревательным блоком, то это нормально, зазор для того, что бы поджать соплом термобарьер.
Для того, чтобы подать пруток в нужное время и в нужном месте необходим фидер (feeder), то есть устройство подачи прутка.Иногда его выполняют совмещенным с хотэндом, и тогда такой тип экструдера (это все вместе хотэнд+фидер) называют директом (direct), то есть подача прямая, без трубок.
Та же фидер делают отдельно, а подачу прутка осуществляют через фторопластовую трубку. Называют такую систему – боуден (bowden).
Это делается для того, чтобы облегчить движущуюся часть. По части положительных моментов и недостатков – у каждой конструкции они,несомненно, есть.Директ экструдер:
1. Достоинства:
а) Более надежный за счет меньшего числа соединений для подачи пластика;
б) Менее придирчив к материалам, которыми печатает, в частности резиной на основе каучуков проблематично печатать на боуден экструдерах;
2. Недостатки:
а) Большой вес, за счет этого при ускорениях/замедлениях можно наблюдать небольшую рябь на поверхности детали;
б) Габариты. Они очень сильно влияют на область построения. Скажем, как на картинке выше, директ с 4 цветами был бы очень громадным. А для боудена это в самый раз.
Боуден экструдер:
1. Достоинства:
а) Вынесенный мотор снижает вес движущихся частей принтера, а их меньшая инерционность не влияет на поверхность модели;
б) Катушка не дергается вслед за моделью, а то при запутывании витков катушки с директом получим пропуск шагов, так как каретка будет тянуть за собой катушку.
2. Недостатки:
а) Настройки ретракта (вытягивание прутка обратно при холостых перемещениях, что бы расплавленный пластик, расширяясь не сочился из сопла) сложнее, так как пруток меньше внутреннего диаметра трубки, он имеет свойство тянуться;
б) Сложнее, чем на директе, выбрать все зазоры, чтобы печатать различными гибкими пластиками. Все, кто говорит,что на боудене печать невозможна гибкими пластиками – нагло врут. Я печатаю. И вполне успешно.
Теперь переходим непосредственно к механике и ее калибровке.
Часть 2. Механика. Что, как и чем дергает?
Существует весьма ограниченное число кинематических схем, под которые написана прошивка, и которые вполне сносно отрабатывают перемещения.Рассмотрим все, от самых распространенных:
1. Конструкция и кинематика от Джозефа Прюши ( не надо читать Прусся,Праша и прочее, это имя человека, в конце концов).
Перемещение вдоль каждой из осей обеспечивается своим независимым мотором. Перемещение по оси Z (вверх-вниз) обеспечивается с помощью 2 моторов и с помощью кинематической пары винт-гайка. Часто используются шпильки М5, в последнее время все чаще ставят винты с трапециеидальной резьбой.Вот винт с трапециеидальной резьбой. Как шпильки с метрической резьбой выглядят прикладывать не буду.
Единственное, что объясню относительно перемещения по шпилькам и трапециям – для производства трапеций берут калиброванный пруток и прокатывают между роликов, находящихся под углом. Получаются винтовые канавки. Такой метод, априори, дает лучшее качество и точность шага, нежели у строительных шпилек по далеко не самому высокому квалитету.Для подключения одновременно 2 двигателей на одну ось (и на 1 разъем) применяется следующая схема.
Соединение последовательное, 2 провода запаиваются, а оставшиеся обжимаются. На цвета можно не обращать внимания, главное, что бы обмотки звонились. А и В это обмотки, а 1 и 2 – выводы.Плюсы данной кинематики:
1) Независимое перемещение каждой из осей. Легко поймать понять какая ось пропускает шаги. Кинематика перекочевала в принтеры от фрезерных ЧПУ, поэтому многие производители делают на ней настольные фрезерные станки, вместо экструдера предлагают установить лазер для гравировок или резки, шпиндель для фрезеровки плат, экструдер для шоколада или даже теста, что б печь блины.
На фото выше – принтер ZMorph. Он может использоваться и как принтер (с одним или двумя экструдерами), как гравировщик (установка Dremel), лазером для гравировок и так далее. Небольшое презентацонное видео.
Фрезерный станок на этой кинематике. Замечу, что для фрезеровки необходимо использовать для перемещения пару винт-гайка,а не ремни, они не предназначены для таких нагрузок.
Принтеры для печати шоколадом и для выпечки блинов по вашему эскизу. Стоит заметить, что шоколадки типа Аленка или Бабаевские использовать не рекомендуется, так как они уже имеют в своем составе какао-масло и при переработке (расплавка и затвердевание) результат непредсказуем. Необходимо использовать шоколад в галлетах, например бельгийский Callebaut, так как в нем нет какао-масла, и для окончательной заливки его нужно добавить. Для такого типа шоколада на каждой пачке есть график его кристализации. Масло желательно брать в порошке. Для более подробной информации рекомендую погуглить про темперирование шоколада.
2) Кинематика проста как два пальца. Ее очень просто собрать. Многие даже собирают на старых DVD дисководах.
3) Легко изменяется под свои нужды, размер экструдера тоже имеет небольшое значение, так как он выступает вперед и не мешает движению остальных частей. Многие ставят второй экструдер, или делают сопла качающимися, что бы сопли одного экструдера не оставались на детали, при печати вторым соплом.
Поэтому для данной кинематики существует огромное число вариаций экструдера, на любой вкус, на очень известном сайте.Недостатки данной кинематики:
1) Сложная калибровка. Да, поскольку стол ‘дрыгается’ печатать сложновато качественно, ибо деталь+стол при резкой смене направления перемещения по инерции стремяться ехать дальше. Получаются некрасивые артефакты печати. И для качественной печати нужна небольшая скорость. А вообще, все зависит от рамы. У меня первым принтером была китайская прюша. С акриловой рамой.
А акрил не очень-то жесткий. А как известно, жесткость принтера как и ЧПУ – самое важное. И печатать можно было более или менее качественно на скоростях 40-50 мм/с. Далее я его пересадил на стальную раму от МЗТО.
И после этого без потери качества печати смог печатать на скоростях до 100 мм/с.2) Деламинация. Из-за открытого корпуса и постоянно перемещающейся платформы горячий воздух, можно сказать, постоянно сдувается, а охлаждая излишне деталь сквозняками мы увеличиваем и без того большую усадку нейлонов,абс и прочих капризных пластиков. Кто-то шьет шубу для принтера из ткани, а кто-то довольствуется и коробками.
Но цель, как всегда, одна и та же – уменьшить влияние сквозняков на усадку детали.Основные моменты правильной калибровки принтеров с данной кинематикой:
1) Установить принтер на ровную поверхность. Желательно горизонтальную. Для этого необходим пузырьковый уровень. Далее устанавливаем по уровню положение оси X.
2) Переводим в домашнее положение. Делается либо в меню принтера командой Home/Домой, если печатаете с компьютера, то или командой G28 в строку команд, или специальными кнопками с иконкой домика.
Далее подкручиваем винт стола так, что бы сопло касалось стекла. Не давило на стекло, а касалось. Смотрим на просвет и крутим. После этого перемещаем экструдер к другому углу стрелками в +Х, +Y с ПК, или через меню
Точно так же крутим винтик до соприкосновения с соплом. И повторяем операцию для остальных точек.Постараюсь избавить вас от ошибок. На фото принтера выше стекло на столе крепится аж 8 зажимами. И вполне возможно, что по центру будет горб. Чтобы избежать подобных проблем стекло стоит закреплять 3 зажимами. Плоскость строится, как известно из начертательной геометрии, по 3 точкам. И калибровка будет проще в этом случае. Просто подкручиваем винт над концевиком по Z.
Чтобы сопло касалось стекла посередине той стороны, на которой стоит 1 зажим. Дальше перегоняем хотенд в угол где еще один зажим, подкручиваем винт стола, и повторяем операцию с другим углом.Касательно вобблинга.
Всякие антивобблинговые системы вроде установки продшипника в верхнюю опору не работают.
Просто потому, что поставить идеально параллельно и в одной плоскости 4 далеко не идеально ровных циллиндра – задача нереальная. Особенно на хлипкой акриловой раме с печатными деталями. Поэтому, если принять за константу прямизну валов, и выставить их параллельно на раме (чисто гипотетически), а винты освободить (снизу муфта для крепления к мотору) и гайки для крепления оси Х. Винты за счет своей кривизны будут вертеться как миксер, но на печать это не будет влиять.
Иначе конструкция будет работать на то, кто же окажется сильнее на сопротивление изгибу. И будет получаться далеко не ровная стенка. Оно вам надо?2. Конструкция по типу кинематики принтеров компании Felix printers.
Таких принтеров много, такие делает МЗТО (mz3d.ru), уже упомянутые Felix. По сути кинематика та же, что и у Prusa. Независимые друг от друга оси. Только теперь стол ездит не вдоль одной оси, а сразу вдоль целых двух. Вдоль оси Z, и по оси Y.
Конструкция стола примерно такая.
На валах по Z ездит платформа. Сзади висит двигатель. По рельсам при помощи ремня передвигается стол. Хотенд передвигается только вдоль одной оси. Конструкция весьма забавна, так как стол весит куда больше хотенда, а его пытаются перемещать по 2 осям сразу.Плюсы данной кинематики:
1) Отсутствует второй мотор по оси Z. Пресловутого вобблинга нет просто потому, что есть 2 вала и 1 винт. Винт, так же не стоит закреплять сверху. Если это не ШВП.
ШВП это отдельная тема. Если брать качественную ШВП, скажем, от тех же Hiwin, то она изготавливается как минимум по 7 классу точности (если катанная, а если шлифованная, то класс еще выше) и устанавливаться должны в подшипниковых опорах. Со стороны привода – 2 радиально-упорных подшипника back-to-back,а с другого конца – радиальный со свободной посадкой для компенсаци теплового расширения.
Цель установки ШВП – обеспечение точности перемещения. Если же ее устанавливать неправильно – деньги на ветер, и точность будет не выше пары винт-гайка с трапециеидальной резьбой. Для FDM c лихвой хватит точности трапеций.2) Много места для установки директ-экструдера. Как и в предыдущей кинематике есть простор для творчества, подбирать тот самый, единственный и неповторимый экструдер, который вам по душе.
3) Жесткая рама. Есть возможность сделать нормальную раму. Жесткую,прочную. Да хоть чугуниевую. Ребята из Феликса решили не забивать голову и лепят из алюминиевого профиля. МЗТО пошли дальше, погнули стальной лист. А полку под установку стола отфрезеровали из листа алюминия.
4) Если брать конструкцию Феликса на профиле, то с помощью замены пары кусков профиля и винта по Z можно увеличить область печати.
Только обязательно добавить жесткости. А то получится как это чудо конструкторской мысли. Большое, бессмысленное и беспощадное.Недостатки кинематики:
1) Несомненно, большие дергающиеся массы. Стол вперед-назад,а если включить движение по Z при холостых перемещениях (Z-hope), то будет дискотека.
2) Нет возможности сделать ему нормальную термокамеру. Стол двигается вперед-назад и градиент температуры просто сдувается. Отсюда проблемы при печати нейлонами или ABS. Небольшие сквознячки в комнате с легкостью покажут вам где раки зимуют как усаживается материал.
Калибровка стола данного принтера аналогична калибровке стола у Prusa, только несколько проще. Проще за счет того, что ось X вам выставлять по уровню не надо, она автоматически выставлена при сборке рамы. Подводим сопло к столу и крутим барашки.
3. Кинематика Ultimaker.
Одна из наиболее распространенных вариаций Cartesian кинематики.
Таких принтеров не очень много, но они есть. Вариация от Zortrax заслуживает внимания. Вариант того же Raise более приближен к классике.
У Zortrax установлены двойные валы, причина проста – на них стоит директ экструдер с полноразмерным двигателем Nema 17. У Raise Dual стоит двойной директ экструдер, поэтому классические 6 мм валы заменены на 8 мм. А общий вес ‘головы’ составляет почти 900 грамм.
Кинематика построена полностью на валах. Они выступают одновременно и как направляющие, и как шкивы. Кинематика так же относится к Cartesian кинематикам с независимым перемещением вдоль каждой оси своим мотором. Очень привередлива к прямоте валов. Если использовать кривые валы можно получить весьма забавные артефакты на стенках моделей. И они будут по всем 3 координатам. Чаще всего это выглядит как разная толщина первого слоя и небольшие волны по стенкам. Поэтому вся соль и высокая цена оригинальных Ultimaker только в качественных комплектующих. А именно в прямых валах. Ремни используются часто кольцевые, что упрощает систему их натяжки, так как важно, чтобы все 4 ремня были одинаково натянуты.Плюсы данной кинематики:
1) Стол движется только вдоль одной оси. Вертикальной. И градиент температур никоим образом от этого не страдает. Стол консольный, поэтому желательно предусмотреть ребра жесткости или учесть это толщиной стола.
Отгиб металла на столе работает как ребро жесткости.
Многие китайские клоны комплектуются такими вот ребрами жесткости для стола.
2) При всей кажущейся сложности кинематической схемы она проста и каждая ось перемещается с помощью своего же мотора.3) Корпус закрытый, что защищает от сквозняков, и следовательно деламинации. Некоторые для пущего эффекта ставят акриловую дверцу.
Минусы кинематики:
1) Для хорошей печати мало купить пачку ровных валов. Собрать все эти валы правильно воедино та еще задачка. Заодно и купить хорошие подшипники. Не то, китайское барахло, что чаще втюхивают на али, а нормальные подшипники. Если подшипники, что ставят в корпус будут плохо вращаться – печать будет рывками и со сдвигом слоев. Последствия можно спросить у Вани (Plastmaska). Так же, покупая леопардовые втулки латунные подшипники с графитовыми вставками будьте готовы к тому, что они будут люфтить. А если будет люфт – вся конструкция будет стучать.
А так же, китаезы любят вместо бронзы впихивать латунь. А при равномерном износе латуни и графита на валах будет будет маслянистая липкая черная пленка, из-за чего перемещения будут происходить тяжелее. Хорошие втулки предлагает Илья ( tiger). Он же и писал про эти сложности.
2) Необходимо выставить правильно все параллели валов. Предлагаю воспользоваться таким девайсом.
4 вала, что идут вдоль стенок корпуса автоматически встают правильно, а вот крестовину важно выставить правильно, что бы получить углы 90 градусов в плоскости XY.3) Конструкция не предусматривает увеличение области печати с помощью пары кусоков профиля, поэтому размеры хотенда имеют значение. Директ сложновато поставить, но можно при желании.
Калибровка стола проще некуда. Стол часто на 3 точках крепления. Перемещаем хотенд по 3 точкам и крутим барашки.
4. Кинематика, используемая фирмой Makerbot.
Так же, весьма широко распространена. В частности принтеры компании Makerbot, BQ, BCN3D ,Magnum, клон магнума – Zenit и вполне сносные реплики makerbot – Flashforge и Hori работают на данной кинематической схеме.
В данном случае мы имеем независимое движение каждой из осей, с Z столом и всеми вытекающими из этого сторонами.Основной недостаток заключается в том, что на катающейся балке с одной стороны висит двигатель, создавая эдакий дисбаланс. Этот недостаток компенсировали в двухэкструдерном варианте – BCN3D Sigma. Там у каждой bowden-головы для перемещения вдоль балки есть свой двигатель. И они установлены по краям балки и уравновешивают друг друга. Для равномерного перемещения каждого из краев балки применяется 2 вала, шкивы и ремни. Ремни необходимо натягивать одинаково.
Достоинства кинематики:
1) Независимое перемещение каждой из осей.
2) Движущийся по Z стол. Градиент температур не страдает ‘сдуванием’.
3) Закрытый корпус. Если не закрытый, то есть вполне нормальный с точки зрения эстетики шанс закрыть его.
4) Масштабируемость кинематики возможна. Различные BigREP и иже с ними с метровыми областями печати используют именно эту кинематику, так как различные H-bot/CoreXY будут адово звенеть по причине наличия 4-5 метровых ремней и их растяжения во время ускорений.
Недостатки кинематики:
1) Неуравновешенные массы на движущейся балке, отсюда максимальная скорость печати, с приемлемым качеством не больше 60-80 мм/с. Некоторые умудряются их уравновесить и это не столь заметно.
2) Громоздкие конструкции на валах, дабы избежать дисбалланса при перемещениях.
3) Необходимо следить, чтобы натяжения ремней справа и слева были одинаковы.
4. Кинематика H-bot/CoreXY.
Следующая по распространению. Так же, Cartesian. Два мотора неподвижны, но перемещают каретку по направляющим с помощью одного длинного куска ремня, или с помощью двух, но покороче. Математика сложнее, чем у предыдущих, так как необходимо синхронизировать поворот обоих роторов двигателя. То есть, для перемещения вдоль каждой оси нужно вращать оба мотора, а для перемещения по диагонали – всего 1.
[IMG]http://www.doublejumpelectric.com/projects/core_xy/pics/hbot.svg[/IMG]По сути математика для вращения моторов одна и та же, а реализация в механике разная. Один из самых больших недостатков H-bot перед CoreXY состоит в том, что при перемещениях ремень стремится повернуть балку.
На картинке слева это заметно, силы справа и силы слева создают крутящий момент. Поэтому для реализации этой кинематики необходима жесткость кинематической схемы. Чаще всего ее реализуют в рельсах.
С жесткой балкой. Некоторые делают, конечно, на валах, но по итогу – это не фонтан.
А потом понимают это и переезжают на рельсы.
Ибо они и проще в сборке и настройке, и выдумывать каретки, что б хорошо валы закрепить не нужно.CoreXY, в отличии от H-bot, приводится в движение при помощи двух ремней.
И так, для простоты понимания, опишу положительные и отрицательные стороны каждой вариации этой кинематики.H-bot.
Достоинства:
1) Ремень необходим всего один, а схема предусматривает его работу без скручиваний.
2) Натягивать один ремень удобнее, чем 2, поэтому в этой схеме нужен всего один нормальный натяжитель.
Можно даже так.Недостатки:
1) Ремень имеет свойство растягиваться со временем, а так как величина растяжения напрямую зависит от длины, то необходимо следить за его натяжением. Иначе получатся некрасивые волны на поверхности перед остановками.
При слабой натяжке ремня каретка будет иметь такой люфт.2) Необходимо выставлять ролики строго перпендикулярно плоскости XY, так как при небольшом перекосе ролика ремень будет съедаться об буртики ролика. И мы получим такую вот бяку.
Проверено на своей шкуре и принтере ZAV. Поэтому всегда рекомендую нормально закреплять ролики, а не консольно, дабы избежать изгиба оси ролика от натяжки ремня.3) Сложная математика, из-за чего на скоростях выше 100 мм/с могут быть проблемы с нехваткой ресурсов 8 битных плат.
CoreXY.
Достоинства:
1) Два коротких куска ремня. Их проще найти, чем один длинный.
2) Силы уравновешивают балку, а не стремятся ее повернуть, поэтому эту кинематику можно собирать и на валах.
Недостатки:
1) Есть схемы с перекручиванием ремней и перехода ремня с одного уровня на другой – для ремня это не очень приятно. Особенно, когда один ремень трется об другой. На видео этот момент есть.
:{}
2) Сложность нятяжки ремней. Их необходимо натягивать одинаково, иначе силы нятяжки будут стремиться повернуть каретку.
3) Сложность сборки и разработки. Необходимо выдержать вертикальность роликов, относительно горизонтальности площадки для установки моторов и рельс. Небольшой перекос роликов приведет к тому, что ремень будет стремиться съехать по ролику, а если будет упираться в буртик ролика, то будет скрипеть, если буртик большой, а если маленький – то будет пытаться на него заехать, как на фото из описания h-bot.
Общий недостаток кинематики – плохая масштабируемость. То есть ставить такую кинематику для области печати больше 300*300 весьма проблемно просто из-за удлинений ремня при печати. Для небольших принтеров с большой скоростью печати – одна из лучших кинематик.
5. Delta кинематика.
Кинематика основана на движениях дельта-робота.
Только вместо захватов устанавливается хотенд. Имеет свои проблемы с настройкой, но на печать можно залипать очень долго. Редко когда устанавливают директ-экструдеры, так как эффектор (площадка для установки хотенда) часто крепится на магнитах и необходимо максимально разгрузить его. Но для уменьшения длины трубки (а конкретнее, влияния длины трубки на качество печати за счет правильной настройки ретрактов ( вытягивания пластикового прутка назад с целью уменьшения его вытекания от расширения)) на качество печати, экструдер вешают на те же каретки, но на отдельных подвесах. За счет этого уменьшается длина bowden трубки и увеличивается качество печати.
Достоинства:1) Легко кастомизируется. Для увеличения высоты достаточно прикупить 3 куска профиля подлиннее, и увеличить максимальную высоту в настройках.
2) Занимает мало места. Она чаще высокая, чем громоздкая по длине и ширине, за счет этого компактность.
3) Если сделать легкий эффектор ( каретка, на которой установлен хотенд), то можно добиться больших скоростей без потери качества печати.
4) Перемещение по высоте не отличается от перемещения по XY. Таким образом, нет залипания линейных подшипников на переездах стола, как у Cartesian принтеров, лишних двигателей, катающихся на балке…
5) Отсутствие выступающих частей дает возможность закрыть корпус и придать раме жесткости.
6) Эстетическая часть – на работу дельты интереснее залипать.
Недостатки:
1) Сложная математика перемещений, рекомендуется ставить сразу 32-битные платы.
2) Сложная настройка. Частая проблема в настройке – убрать так называемую ‘линзу’, ведь каждый стержень вращается с радиусом, и при некорректной настройке у вас печатаемая плоскость будет либо выпуклой,либо вогнутой линзой.
3) Сложно и дорого сделать жесткую раму, что бы ее не болтало от постоянных дрыганий кареток.4) Сложность установки директ-экструдера. Он получается тяжелым, а так как многие дельты делаются на магнитах, то не будет возможности разогнаться. Хотя, есть одно аккуратное и легкое решение – установка готового директ-экструдера с редуктором. Как, например E3D Titan Aero или Bondtech BMG.
5) Проблемы точности изготовления деталей – любые неровности и несоосности будут видны, даже если они на одной оси. И они складываются по осям.
Резюмируя, хотите небольшой принтер (не больше 300*300 мм) с шустрой кинематикой? Тогда вам к Ultimaker или H-bot/CoreXY. Нужен принтер с большой областью печати или с 2 независимыми экструдерами? Тогда к Makerbot. Если печатать вазочки, кальяны и достаточно высокие детали – дельта. Для всего остального есть классика – Prusa. Эксперименты с двойными каретками, шоколадом, гравировками? Да все что угодно. И самое главное – дешево.
Можно даже 4 цвета прикрутить.3dtoday.ru
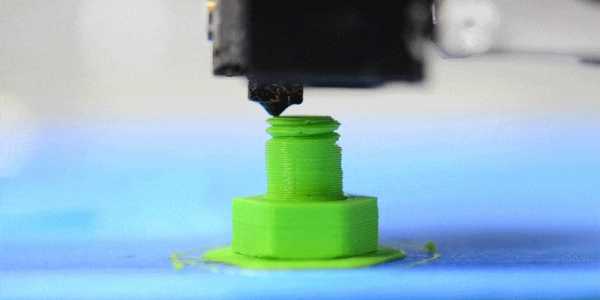
Стандартное FDM-устройство работает как термоклеевой пистолет управляемый роботом, что не удивляет, ведь разработка технологии FDM когда-то начиналась с опытов с термоклеем. Пластиковый пруток проталкивается через горячее сопло, где он плавится, а выходя из него укладывается слоями. Процесс повторяется снова и снова, пока не появится готовый 3D-объект.

Проще говоря, 3D-печать отличается от традиционной 2D-печати только тем, что повторяется снова и снова, создавая слой за слоем, один на поверхности другого. В конце концов, тысячи слоев образуют 3D-объект.
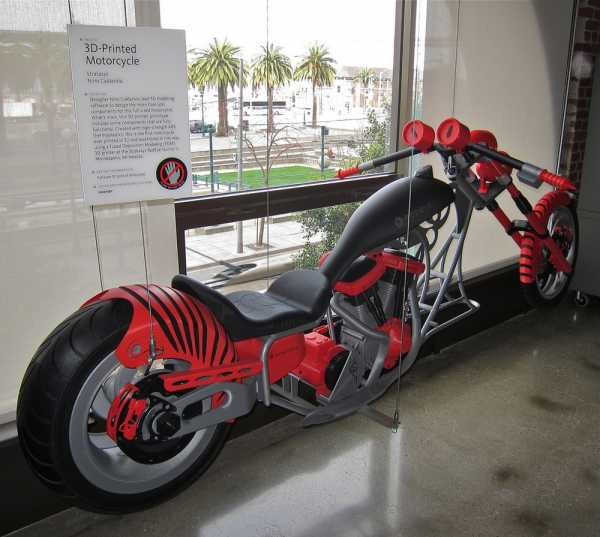
FDM-принтер на примере MakerBot Replicator 2
Стереолитография
Стереолитография использует свет для “выращивания” объектов в емкости с фотополимерной смолой. Как и в прочих технологиях 3D-печати, изделие образуется слой за слоем, здесь — при отверждении жидкого фотополимера светом.
От FDM стереолитография отличается более монолитными принтами, даже с одинаковой заданной толщиной слоя.
На фото: принты FDM и SLA, слой обеих моделей — 0,1 мм.
Дело в разнице в технологиях — фотополимерная засветка дает более аккуратные слои, чем расплавленный филамент выдавливаемый из сопла FDM-принтера.
SLA и DLP — две разновидности стереолитографии. SLA — лазерная стереолитография, DLP — цифровая проекция. Различие между ними в том, что в SLA источником света служит лазер, а в DLP — проектор.
Независимо от технических особенностей, принцип работы устройств SLA и DLP схож. Для запуска печати необходимо опустить специальную платформу построения в емкость с жидкой фотополимерной смолой.
Платформа останавливается на высоте одного слоя от дна емкости.
Происходит засветка источником света принтера.
Жидкий полимер, под воздействием света, становится твердым и прилипает к платформе построения. После этого платформа поднимается на высоту еще одного слоя и процесс повторяется.
SLA-принтер на примере Formlabs Form 2
SLA дает более гладкие поверхности, по сравнению не только с FDM, но и с DLP, о которой рассказываем далее.
Так получается потому, что DLP проецирует слои картинкой из пикселей, а луч лазера в SLA движется непрерывно, что дает ровный, не пикселизованный слой.
DLP в тех же целях использует проектор, а LED DLP — ЖК-дисплей с ультрафиолетовой подсветкой. В этих конструкциях свет проецируется на смолу по всей площади слоя одновременно, что дает преимущество в скорости, когда необходима печать крупных объектов с заполнением в 100% — полная засветка слоя происходит быстрее, чем в SLA.
Но при печати мелких или пустотелых объектов SLA быстрее, так как интенсивность засветки лазерным лучом, а значит и скорость полимеризации, выше.
DLP-принтер на примере SprintRay MoonRay S
SLS
Главное преимущество технологии перед FDM и SLA — SLS-печать не требует создания поддерживающих структур, ведь материалом поддержки служит окружающий модель материал — это позволяет печатать изделия любой формы, с любым количеством внутренних полостей, и заполнять ими весь рабочий объем принтера. SLS-принтеры работают с широким спектром материалов, а их принты прочнее, чем большинство напечатанных FDM или стереолитографией.
Благодаря прочностным характеристикам, напечатанные на SLS-принтерах детали могут использоваться в практических целях, а не только как прототипы и декоративные элементы.
Для создания объекта аппарат направляет лазер на слой мелкофракционного порошка, сплавляя частицы друг с другом для формирования слоя изделия. Затем, устройство рассыпает следующую порцию порошка на поверхность готового слоя и разравнивает его, а лазер расплавляет, создавая следующий слой изделия. Процедура повторяется до тех пор, пока печать не будет завершена.
Есть у SLS-принтеров и минус — их стоимость. Они очень дороги, по сравнению с FDM и SLA/DLP. Это связано с ценой необходимых для такой печати высокоэнергетических лазеров. В принципе, стоимость даже самых дешевых SLS-принтеров совсем недавно начиналась от $200 000.
Тем не менее, некоторые компании в настоящее время работают над тем, чтобы сделать данную технологию более доступной, поэтому есть шанс, что приобрести SLS-принтер в ближайшем будущем смогут позволить себе даже любители. Один из примеров — польская компания Sinterit.
SLS-принтер на примере Sinterit Lisa Pro
Извлеченная из SLS-принтера модель не требует удаления поддержек и может использоваться без постобработки, ее надо лишь очистить от лишнего порошка.
Polyjet
Главное преимущество технологии Polyjet в ее мультиматериальности — многие Polyjet-принтеры способны печатать объект большим количеством различных материалов одновременно, что позволяет создавать изделия состоящие из участков с разными механическими и оптическими свойствами, то есть — разной твердости и цвета. Это фирменная технология компании Stratasys.
Пример: принтер Stratasys и напечатанные на нем кроссовки.
Polyjet 3D-принтеры распыляют крошечные капельки фотополимерной смолы на поверхность и полимеризуют их ультрафиолетовым излучением.
Этот процесс повторяется до тех пор, пока не будет создан объект. В отличие от FDM-принтеров, Polyjet-устройства могут наносить материал из многочисленных сопел одновременно.
Polyjet-принтер на примере Stratasys J750
Заключение
Прочитав эту статью, вы ознакомились с принципами и примерами работы 3D-принтеров функционирующих по самым распространенным технологиям.
Существуют и другие технологии, в основном — связанные с 3D-печатью металлами, но они используются только в промышленности. О них мы поговорим отдельно.
Чтобы выбрать 3D-печатное оборудование и материалы для любых задач обращайтесь в Top 3D Shop — проконсультируем, подберем максимально подходящую технику и расходники, оформим заказ, доставим, установим и научим.
top3dshop.ru
3d-принтер (конструкция, виды, производители) | Wiki 3DP
3D-принтер — это периферийное устройство, осуществляющее 3D-печать методом послойного формирования физического объекта по заданной цифровой 3D-модели.
Благодаря определенной простоте базовой конструкции оборудования, позволяющего осуществлять объемную печать, разработки в данной области ведутся как простыми людьми – энтузиастами 3d-печати (фактически каждый может собрать свой собственный 3d-принтер своими руками), так и крупными отраслевыми компаниями и центрами разработки.
Современные 3d-принтеры могут печатать как различными полимерными материалами (основная доля расходных материалов), так и металлом, специализированными строительными составами, продуктами питания и био-материалами.
3д-принтеры уже сегодня применяются как для бытового так и для профессионального прототипирования объектов. На сегодняшний день помимо условно “стандартных” образцов оборудования, имеются разработки и конструкции, осуществляющие печать еды, принтеры применяемые в медицине и принтеры способные печатать малоэтажные дома и небольшие конструкции.
Также отметим, что 3д-принтеры в частности и 3д-печать в целом активно используются в образовании, робототехнике и ряде других социально-значимых и инновационно-перспективных направлений.
Следует отметить, что 3d-принтеры – это одна из немногих категорий оборудования имеющих реальную возможность к самовоспроизведению (в частности, проект RepRap).[1]
Виды 3d-принтеров
Классификация 3д-принтеров ведется по нескольким ключевым параметрам, основными из которых являются: применяемая технология 3d-печати; материал печати; уровень качества и стабильности размеров получаемых изделий.
В последнем случае различают домашний (настольный) 3d-принтер и 3d-принтер профессионального класса, демонстрирующий более стабильные размеры напечатанных объектов, повышенную производительность (скорость печати) и качество прототипирования. Оборудование профессионального класса активно применяется в различных конструкторских бюро (с целью создания моделей и прототипов разрабатываемой продукции или конструкций), а также для целей мелкосерийного производства широкой гаммы изделий (сувенирная продукция, индивидуализированные корпуса электроники и тому подобное).
Типовая конструкция 3d-принтера
Индустрия 3D-печати переживает в настоящий момент этап бурного роста и развития, что привело к тому, что на сегодняшний день на рынке присутствует крайне широкая и весьма пестрая гамма образцов оборудования: от любительских принтеров, собранных своими руками в единичном экземпляре из подсобных деталей и элементов, до промышленных образцов, способных создавать высокоточные копии объектов с весьма сложной геометрией.
В целом, устройство 3D-принтеров на самом деле не очень сложное. Главные проблемы при изготовлении принтеров – обеспечить точность сборки и дальнейшей точности позиционирования по всем осям для экструдера, чтобы обеспечить качество печати.
Для того чтобы представить типовую конструкцию 3д-принтера рассмотрим самую распространенную (в настоящее время) технологию объемной печати – FDM (метод послойного наплавления).
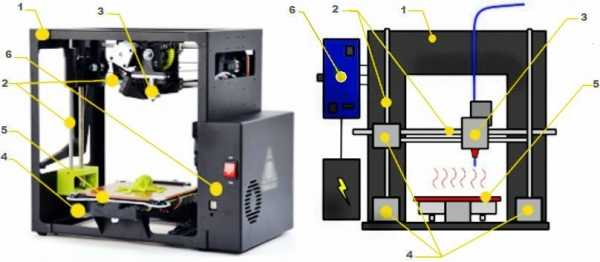
Типовая конструкция 3D-принтера печатающего по методу послойного наплавления (FDM). (Визуализация: 3D Today)
3d-принтер состоит из:
- Корпус, играющий роль скелета для монтажа конструкционных элементов;
- Направляющие, осуществляющие сравнительно свободное перемещение печатающей головки в заданном пространстве;
- Печатающая головка (экструдер) – группа частей, которая выполняет подачу, нагрев и вытеснение (экструзию) расходного материала через сопло на рабочую поверхность;
- Шаговые двигатели – элементы конструкции 3д-принтера, отвечающие за равномерное перемещение печатающей головки в заданном пространстве;
- Рабочий стол – строительная платформа 3D-принтера, на которой и осуществляется непосредственное создание трёхмерного объекта;
- Электроника – набор элементов, отвечающий за управление и координацию действий принтера в процессе печати.
Подробнее остановимся на некоторых (наиболее важных) элементах базовой конструкции 3д-принтера[2].
Экструдер (печатающая головка) 3d-принтера
Наиболее важный элемент конструкции данного вида оборудования. Экструдер 3д-принтера – это узел, который обеспечивает подачу расплавленного пластика в рабочую зону аппарата. На сегодняшний день уже имеется огромное количество различных конструкторских решений.
В частности, имеются образцы оборудования оснащенные сменными соплами различного диаметра. Также есть варианты принтеров с двумя экструдерами в конструкции. Такие образцы способные печатать двумя цветами или осуществлять печать поддержек растворяемым пластиком PVA или HIPS.
Обслуживание экструдера 3д-принтера состоит в его очистке снаружи от налипших в процессе печати кусочков пластика. Иногда, обычно при работе с некачественными расходными материалами, сопло экструдера может довольно сильно засоряться – в этом случае приходится проводить его чистку.
Рабочий стол 3д-принтера
Стол может быть как нагреваемым, так и без такового. Для калибровки стола применяются либо автоматические приводы (автоматическая калибровка) или подпружиненные болты (ручная регулировка). Покрыт обычно стеклом, хотя есть варианты 3д-принтеров и с перфорированной платформой. Для нагреваемого стола еще добавляется и нагреваемый элемент.
Обслуживание данного элемента конструкции заключается в его калибровке и регулярной чистке поверхности.
Электроника и управление
Плата управления может находиться в корпусе. Большинство 3d-принтеров имеют плату на основе RAMPS. Но есть и варианты со своими решениями. Обычно достаточно проверять работает ли кулер охлаждения (если он необходим в данной конструкции).
Что касается экрана управления 3д-принтером, то он, следует отметить, присутствует отнюдь не на всех моделях данной категории оборудования. Обычно он есть там, где есть возможность печатать с SD карты.
Принцип работы 3д-принтера
Как уже было замечено, на сегодняшний день в индустрии насчитывается уже несколько подвидов методов 3д-печати, а также весьма обширный набор соответствующего оборудования и конструкций.
Для того, чтобы рассмотреть принцип работы 3d-принтера обратимся к его ключевому элементу (головке экструдера) и методу объемной печати, использующей пластиковую нить.
Процесс 3д-печати:
Нить (филамент) поступает в печатающую головку (экструдер), после чего осуществляется разогрев нити до ее жидкого состояния. Далее полученная масса выдавливается через сопло экструдера. При этом шаговые двигатели с помощью зубчатых ремней приводят в движение Экструдер, который перемещается по направляющим в заданном направлении и наносит пластик на платформу слой за слоем согласно заданной модели.[3]
3d-принтер – производители
Технология 3d-печати с одной стороны еще находится на этапе своего зарождения и становления, с другой стороны базируется на весьма проработанных технологических решениях из ряда других областей (в частности, экструзии полимеров). Данные обстоятельства в совокупности с развитием интернета, значительно ускорившего и упростившего обмен информацией в мировых масштабах, привели к тому, что теми или иными успехами в области разработки, конструирования и производства оборудования для 3d-печати могут похвастаться очень многие компании по всему миру.
Подавляющее большинство таких компаний (на сегодняшний день) занимается сборкой оборудования из готовых конструкционных элементов по находящимся в свободном доступе конструкторским схемам с минимальными изменениями и новациями. Однако на рынке уже есть и свое лидеры, – относительно крупные компании, сравнительно (учитывая возраст самого рынка 3д-печати) давно работающие в данной области. Список наиболее заметных из них представлен ниже.
Ведущие производители:
- 3D Systems (США);
- EnvisionTEC (Германия);
- Stratasys (США);
- MX3D (Нидерланды);
- Rapid Shape (Германия);
- DWS s.r.l. (Италия);
- Wuhan Binhu Mechanical & Electrical (Китай);
- MakerBot Industries (США);
- RepRapPro (Великобритания);
- Magnum (Россия);
- Ultimaker (Нидерланды);
- PICASO 3D (Россия).
В общем и целом свое разработчики и (или) производители 3д-принтеров имеются практически в каждой цивилизованной стране мира. По различным оценкам экспертов и аналитиков, на сегодняшний день в мире можно купить 3d-принтер по меньшей мере от 300 компаний.
В Европе (как можно заметить из приведенного выше списка) центральное место занимают немецкие, голландские и итальянские компании, что вполне коррелирует с тем какое место на международном рынке занимают местные компании-производители оборудования для переработки полимеров. Также заметное место на мировом рынке аддитивных технологий занимает и Великобритания, где по разным оценкам насчитывается как минимум 15 компаний, разрабатывающих и изготавливающих оборудование для объемной печати.
В Азии безусловным лидером рынка выступают китайские компании. Однако и кроме них здесь есть заметные игроки и из других стран региона: Индия, Япония, Южная Корея, Тайвань и даже Таиланд и Гонконг.
На постсоветском пространстве безусловным лидером по количеству отраслевых компаний, работающих в области разработки и изготовления 3d-принтеров и вспомогательного оборудования, выступает Российская Федерация, на территории которой (по различным оценкам) уместилось по меньшей мере 36 предприятий, главные из которых представлены выше. Также следует отметить, что свое отраслевые фирмы имеются в Украине, Беларуси, Литве и Латвии.
В Северной Америке, помимо мирового лидера – США, свое функционеры в области разработки, производства и внедрения оборудования для печати 3dp присутствуют и в Канаде.
В заключении отметим, что есть свое компании-производители и в таких странах, как Израиль; Бразилия, Новая Зеландия и Австралия, хотя их можно в прямом смысле слова “пересчитать по пальцам” и заметного влияния на мировой рынок они (на данный момент) не оказывают.
Узнать больше про 3d-принтер:
Также, для получения более полной картины по тематике 3д-печати в целом и 3д-принтеров в частности рекомендуем воспользоваться поиском по сайту (вверху страницы).
mplast.by
Принцип устройства и работы 3D принтера
Сегодня трехмерной печатью удивить можно, пожалуй, только маленького ребенка. Метод 3Д моделирования запросто используется в личных или коммерческих целях, а многие современные предприятия уже не могут обойтись без такого принтера. Сама технология была создана довольно давно, однако, мало кто задумывался каков принцип действия 3Д принтера. В этой статье речь пойдет как об устройстве, так и о распространенных методах этого вида моделирования.
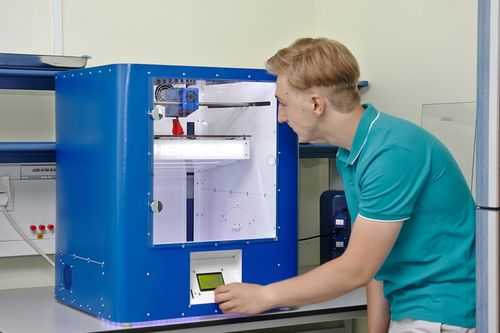
Устройство принтера для 3Д печати
О чём пойдет речь:
Из чего состоит
Тип устройства принтера для 3Д печати похож со своим собратом, изготавливающим любые изображения в формате 2Д. Основным отличием считается способность продвинутого принтера печатать объемные элементы. Так, к привычной длине и ширине, здесь добавляется еще и глубина. Нужно понимать, что абсолютно все 3D принтеры имеют одинаковый набор рабочих элементов.
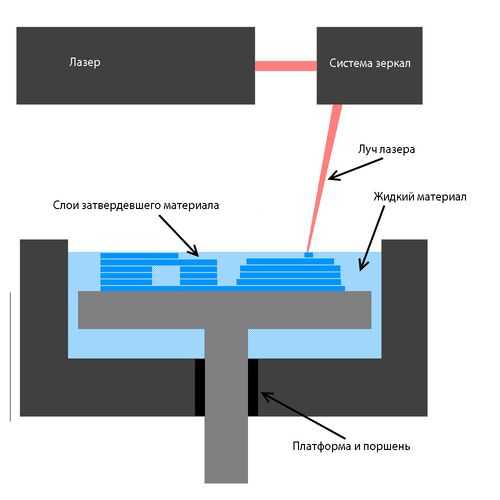
Принцип работы 3D-принтеров DLP или SLA на смолах
Любое устройство, печатающее в трех плоскостях, состоит из таких рабочих элементов:
- Экструдер. Он нагревает и выдавливает вязкий пластик;
- Платформа. Основа, на которой проходит процесс;
- Мотор. Он двигает необходимые элементы принтера;
- Фиксаторы. Специальные датчики, стопорящие подвижные части принтера во время работы. Они не позволяют выйти за границы платформы;
- Рама;
- Картезианский робот. Устройство, способное двигаться по 3-м осям.
Зная устройство машины, становится понятен принцип работы 3Д принтера. Конечно, это основные рабочие узлы, принимающие непосредственное участие в создании трехмерных конструкций.
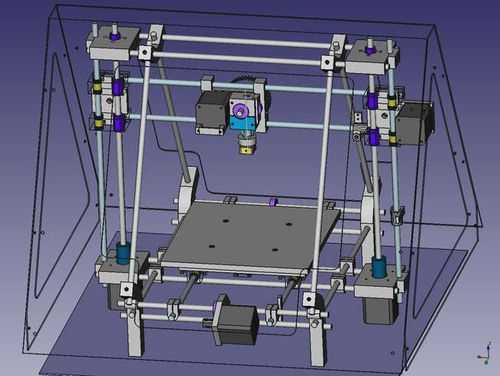
Устройство 3D-принтера
Как работает
Всего различают несколько основных технологий 3Д печати:
- Метод постепенного наслоения пластика.
- Стереолитографическое моделирование.
- Лазерное спекание.
Эти методы были названы от более популярного к менее распространенному. И сейчас кратко расскажем о каждом из них.
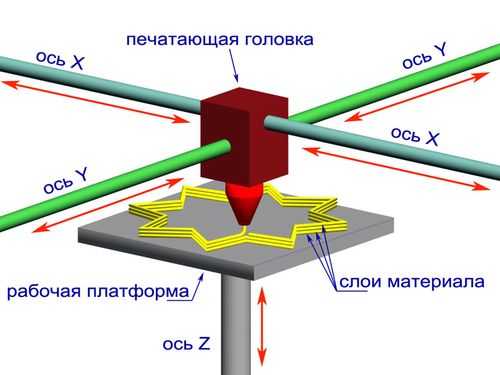
Схематическое изображение 3D-принтера
Метод послойного наплавления термопласта
Большинство 3Д принтеров работает с термопластиком, в том числе с полилактидом. Он отличается природным происхождением и неспособностью выделять вредные вещества. Работа заключается в подаче тонкой нити вязкого пластика в трубу сопла. Она и формирует необходимый элемент.
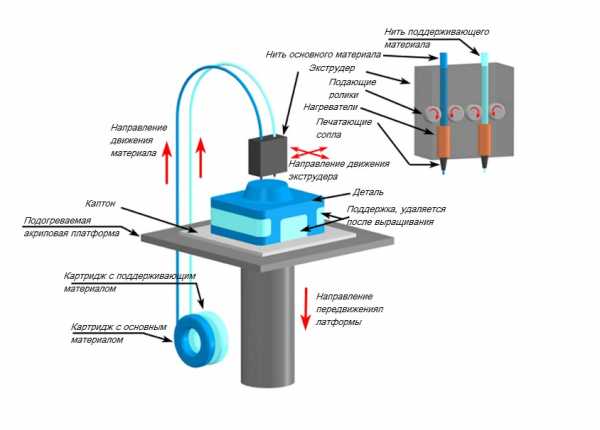
Метод послойного наплавления термопласта
Стереолитографическая печать
Эта технология широко применяется в стоматологии. С ее помощью изготавливают зубные протезы. Главным преимуществом таких принтеров считается высокое качество изготовленных конструкций. К тому же эти установки гораздо дешевле. Они не нуждаются в зеркалах, что делает устройство гораздо проще.
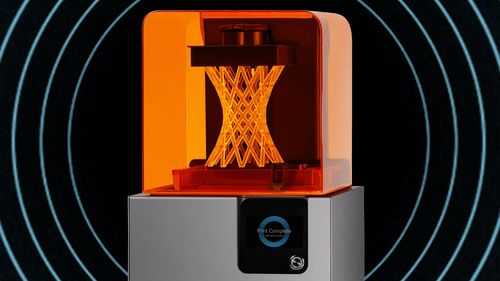
Тереолитографический лазерный 3D-принтер
Лазерное спекание
Для этой технологии используют легко плавящийся пластик. Мощный луч прорисовывает объект. Это действие спекает материал. И так слой за слоем проходит моделирование выбранного элемента. После завершения печати остатки материала просто отряхиваются. Минусов этого метода считается пористая поверхность изделия.
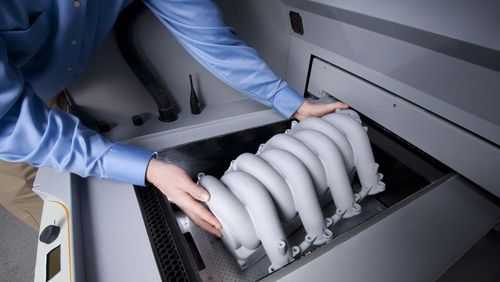
Селективное лазерное спекание
Управление работой принтера и ПО
Основные процессы регулируются с помощью ПК:
- температура сопла;
- скорость подачи пластиковой нити;
- работа мотора.
Базовой системой 3Д принтеров сегодня считается Arduino с открытой архитектурой. А программа должна выбираться в зависимости от конкретной модели машины. Чаще всего, изготовители рекомендуют использовать только фирменное программное обеспечение.
Сегодня 3Д принтер можно рассматривать как специализированное оснащение для специалистов, которые смогут решить массу задач с помощью этого устройства.
printergid.ru
Конструкция FDM-принтеров
Терминология, составные части, возможные проблемы и способы их решенияМы уже довольно подробно рассмотрели FDM-технологию 3D-печати (Fused Deposition Modeling — послойное наплавление или моделирование методом осаждения расплавленной нити) и используемые расходные материалы, а также выяснили причины, по которым FDM-принтеры стали в настоящее время столь распространенными и популярными. Теперь пришло время познакомиться с принятой терминологией и рассмотреть составные части и особенности конструкции таких 3D-принтеров.
Печатающая головка: экструдер и hot-end
Наиболее важная часть любого принтера, будь то струйный 2D или Fused Deposition Modeling 3D, это печатающая головка. В данном случае она состоит из нагревателя, в котором пластиковая нить (иногда используется не нить, а пруток) расплавляется и затем выдавливается через сопло с отверстием малого диаметра — обычно в пределах 0,15–0,5 мм, а также механизма, обеспечивающего дозированную подачу нити в нагреватель. Подающий механизм принято называть экструдером (от англ. extrude — выталкивать, т.е. extruder — толкатель), а нагреватель с соплом называют хот-энд (hot-end; по аналогии экструдер иногда называют cold-end). Порой всю печатающую головку, включая hot-end и cold-end, для краткости называют экструдером, что не совсем правильно: экструдер лишь самая крупная часть головки.
Напомним, что нить или прутки поставляются двух диаметров: 1,75 и 3,0 мм. Экструдер может работать только с каким-то одним диаметром, который надо уточнять в спецификации принтера и учитывать при покупке расходных материалов. Для подачи нити используются шаговый двигатель и система шестеренок и валов. Управляющий двигателем контроллер обеспечивает не только нужную скорость подачи нити, но и обратное действие — ее извлечение, например, при смене материала.
Естественно, температура hot-end контролируется термистором, поэтому к этой части головки всегда подходят четыре провода: два потолще к нагревателю и два потоньше к термистору.
Поскольку рабочая температура большинства материалов достаточно высока — 200–250 °C, а порой и выше, то приходится принимать меры, чтобы обеспечить расплавление нити именно в сопле и избежать нагрева экструдера, в котором могут быть пластиковые детали.
Для этого устанавливают радиаторы между hot-end и cold-end, экструдер дополнительно охлаждают небольшим вентилятором, а также используют «тепловые барьеры» (thermal break, thermal barrier): прокладки из вещества с малой теплопроводностью, в качестве которого может использоваться политетрафторэтилен (PTFE, также известный как тефлон и фторопласт) или полиэфирэфиркетон (ПЭЭК, латиницей PEEK). Поскольку при работе с некоторыми материалами температура hot-end может приближаться к 300 °C, то прокладки должны выдерживать такую температуру не только без значительных деформаций, но и без выделения токсичных веществ. В отношении тефлона в этом плане бытуют подозрения, обоснованность которых мы обсуждать не будем и лишь скажем, что в любом случае работать с FDM-принтером лучше в хорошо проветриваемом помещении.
Трубки из PTFE или PEEK используют еще и для снижения трения между нитью и стенками отверстия нагревателя, на входе в которое пластик нити еще твердый, затем, по мере продвижения к более нагретой зоне, он проходит температуру стеклования, и лишь в области с наиболее высокой температурой переходит в расплавленное состояние. В зоне стеклования, где материал нити уже не твердый, но еще не жидкий, наблюдается высокое сопротивление проталкиванию нити, поэтому крайне желательно, чтобы трубка доходила до точки, в которой нить уже расплавлена.
Сопло считается расходным материалом: его отверстие со временем засоряется, покрываясь нагаром, и приходится либо чистить (что непросто, особенно если отверстие диаметром 0,15 мм), либо заменять сопло. Поэтому крайне желательно, чтобы сопло было не просто сменным, а еще и заменялось без особых хлопот, для чего используют резьбовое соединение. Сопла разных принтеров далеко не всегда взаимозаменяемы: шаг и диаметр резьбы могут быть разными, к тому же сама резьба на сопле может быть не только внешней, как на фото, но и внутренней.
Печатающая головка не обязательно бывает одна: есть немало принтеров с двумя головками. Они позволяют использовать при печати сразу два материала — например, один для собственно модели, а второй, легко удаляемый, для поддерживающих структур, о чем мы писали в обзоре технологий.
Рабочий стол
Следующая важная деталь — рабочий стол или платформа (print bed), на поверхности которой и формируется создаваемая модель. Для рабочего стола нужно обеспечить возможность достаточно точной юстировки, чтобы расстояние между его верхней плоскостью и выходным отверстием сопла по всей рабочей площади было одинаковым. С другой стороны, стол должен двигаться, поэтому к нему нужно жестко крепить конструктивные элементы, обеспечивающие перемещение. Поэтому часто платформа представляет собой двухслойный «бутерброд», к нижней части которого не предъявляется особых требований — она лишь служит для крепления таких элементов и является основой, на которой располагается юстируемая рабочая поверхность, на которой как раз и будет создаваться 3D-модель. Именно об этой части платформы мы и будем говорить далее. Добавим лишь, что в некоторых прототипах, созданных в рамках проекта RepRap, нижняя часть рабочего стола может изготавливаться из самых доступных материалов — МДФ или фанеры.
Очень желательно, чтобы крепление верхней части стола было не жестким, а подпружиненным: при этом, в частности, не так критичны небольшие ошибки в юстировке, когда в какой-то позиции зазор между выходным отверстием сопла и поверхностью платформы становится слишком малым, а то и вовсе переходит в область отрицательных величин.
В качестве материала для платформы используют разные материалы: стекло, акрил, алюминий. И почти всегда приходится решать одну из самых частых проблем FDM-печати — надежную фиксацию первого слоя модели на платформе, поскольку используемые для печати пластики плохо прилипают к алюминию или стеклу. Это решается разными способами: перфорацией платформы, нанесением покрытия, подогревом стола, а также комбинацией этих методов.
Для покрытия нужны материалы, не только обеспечивающие хорошую адгезию, но и выдерживающие температуру расплавленной нити при нанесении первых слоев. Часто используют каптон (Kapton) — тонкую пленку желтого цвета из полиимида, выдерживающую температуру до 400 °C. Для принтеров используется каптон в виде самоклеящейся ленты шириной от 5 до 200 мм, отрезками которой, наклеенными встык, покрывается рабочая поверхность платформы. Конечно, использовать для этого 5-миллиметровую ленту затруднительно — слишком много отрезков придется наклеивать, а 200-миллиметровую сложнее наклеить ровно, поэтому чаще используют промежуточные значения.
Другой распространенный вариант — синий скотч или Scotch Blue Tape на основе полипропилена, выпускаемый фирмой 3M. Вообще-то он предназначен для малярных и упаковочных работ (им, например, часто защищают глянцевые детали различных изделий), но высокая термостойкость сделала его пригодным для FDM-печати.
Для справки: артикул синего скотча 2090, а последующие цифры определяют примерную ширину рулона в дюймах: 2090-.75A — 18 мм, 2090-1А — 24 мм, 2090-1.5А — 36 мм, 2090-2А — 48 мм; есть еще 2090-CM, предназначенный для углов. Длина рулона 55 м.
Достоинство покрытия, состоящего из отдельных полос, в том, что его по мере износа или при повреждениях можно заменять частями, а не целиком.
Есть и другие варианты, включая «доморощенные» — нанесение лака для волос. Еще один материал, самоклеящаяся пленка для лазерных принтеров, использован в принтере PrintBox3D One, о чем мы расскажем в свое время.
Но даже наличие покрытия не обеспечивает должную адгезию для большинства расходных материалов, поэтому платформу приходится подогревать, для чего в ряде моделей на нижней части рабочего стола размещается электрический нагреватель — из нихромовой проволоки, или выполненный в виде печатных проводников, или даже просто в виде нескольких мощных низкоомных резисторов.
Этот нагреватель также контролируется термистором. Прогрев платформы должен быть равномерным, что может обеспечиваться достаточной толщиной самой платформы, но при этом желательно, чтобы рабочий стол нагревался достаточно быстро — не за секунды, конечно, но хотя бы в пределах минуты-двух. А такой популярный пластик, как ABS, требует подогрева до температуры свыше ста градусов, поэтому нагреватель должен быть достаточно мощным.
Подогрев стола нужен еще и для уменьшения температурного градиента между первыми из напечатанных слоев и теми, которые созданы только что. Нижние слои начинают остывать, и особенно быстро, если они соприкасаются с гораздо более массивной платформой, имеющей комнатную температуру. При этом возникают деформации, из-за которых модель может начать выгибаться, а порой и просто отрывается от стола. Поэтому подогрев желателен даже при работе с материалами, адгезия которых к поверхности стола мало зависит от температуры этой поверхности.
Отметим, что и нагреватель, и термистор располагаются с нижней стороны платформы, поэтому контролируется температура именно этой стороны, а деталь будет располагаться на верхней. Поэтому лучше не торопиться и подождать немного, чтобы платформа прогрелась целиком, особенно если она сделана из достаточно толстого материала.
Механизмы перемещения
Во время печати и головка, и платформа должны двигаться. Для этого нужны как механизмы, реализующие собственно перемещение (двигатели), так и направляющие, обеспечивающие точность перемещения.
Обычно головка перемещается по одной из горизонтальных осей, а движение по вертикали и по второй горизонтальной оси обеспечивается движением рабочего стола. Таким образом, нужны три двигателя. Как и в экструдере, используются шаговые двигатели, обычно имеющие шаг в 1,8 градуса, т.е. 200 шагов на полный оборот. Это полношаговый режим, есть еще полушаговый и микрошаговый, который и используют для повышения точности перемещения — управляющая двигателем электроника добавляет некоторое количество промежуточных шагов, причем зачастую значительное: наиболее популярные контроллеры обеспечивают деление шага двигателя на 4, 8 и даже 16 частей, и тогда полный оборот ротора двигателя будет соответствовать уже 3200 микрошагам.
Вращение роторов двигателей нужно преобразовать в поступательные движения головки и рабочего стола. Для этого используются либо системы шкивов и зубчатых ремней, либо валы с резьбой. Передача с помощью вала обходится дешевле, но она не может обеспечить точность позиционирования при высоких скоростях, поэтому чаще всего ее используют для вертикального перемещения платформы, которое происходит достаточно медленно, и лишь в дешевых моделях применяют еще и для движений в горизонтальной плоскости.
Направляющие используют цилиндрические в дешевых моделях и линейные в более дорогих. Материал, естественно, сталь, а к точности изготовления и чистоте обработки предъявляются высокие требования, потому что от этого напрямую будет зависеть точность печати.
Сложная по конструкции и прочная платформа будет иметь немалую массу, что создаст серьезную нагрузку на двигатель, обеспечивающий ее перемещение в горизонтальной плоскости (в вертикальном направлении перемещение и более медленное, и не постоянное). Двигатель будет нагреваться, из-за чего в какой-то момент могут начаться пропуски шагов и другие неприятности. Поэтому рабочий стол стараются максимально облегчить — конечно, не в ущерб прочности, скорость печати порой приходится ограничивать и принимать меры к нормализации теплового режима двигателя (например, обеспечив тепловой контакт с массивной металлической рамой).
Крайние позиции перемещения как головки, так и платформы контролируются установленными в соответствующих местах датчиками. В простейшем случае датчиком может быть механический замыкатель или размыкатель, но и точность, и надежность такого датчика не всегда достаточны, поэтому порой используют оптические (светодиод и фотодиод, в нужный момент зазор между ними перекрывается шторкой) или магнитные, на датчиках Холла.
Температурный режим модели
Есть и еще один момент, который учитывается во многих принтерах. Он связан с тем, что пластик, вышедший из сопла, застывает не сразу, а потому подвержен деформациям. Особенно это критично при наличии так называемых «мостов» — протяженных горизонтальных перемычек, имеющих опоры только по краям: нити еще не застывшего пластика неизбежно провисают, что потребует создания дополнительных поддерживающих структур, которые потом придется удалять. Но даже если «мостов» в модели нет, то может возникать заворачивание углов с малым радиусом кривизны (curling corners), а на элементах небольшого размера — оплывание предыдущего слоя, который не успел отвердеть до момента нанесения следующего.
До известной степени избежать подобных проблем можно, если принять меры к скорейшему отверждению пластика, а это можно сделать одним способом: охлаждением с помощью дополнительного вентилятора, одного или нескольких. Выбрать вентилятор несложно, есть множество моделей разного размера, предназначенных для компьютеров; управлять скоростью их вращения тоже не составляет труда, зато выбор места размещения самого вентилятора и правильного направления потока воздуха от него — это целое искусство. В этом отношении FDM-печать имеет неприятную двойственность: с одной стороны, нужно быстро охладить выдавленный из сопла пластик, а с другой — делать это нужно равномерно, чтобы одна сторона модели не охлаждалась быстрее другой, иначе неизбежны термические деформации. К тому же охлаждающий поток воздуха не должен заметно влиять на те элементы принтера, которые должны иметь постоянную высокую температуру: хот-энд и подогреваемый стол.
Поэтому FDM-принтер «боится» сквозняков, и некоторые модели даже снабжают защитным кожухом, который при домашнем использовании заодно помогает ограничить доступ детей к опасным частям аппарата. Но под кожухом образуется замкнутое пространство, подогреваемое и хот-эндом, и нагретой платформой, и работающими двигателями, и остывающим пластиком уже созданной части модели, что замедляет отверждение выдавленной нити и приводит к еще большим деформациям.
Рама
Конечно, все перечисленные компоненты должны располагаться на достаточно прочной и жесткой раме, обеспечивающей в долговременном плане сохранение геометрии и отсутствие люфтов независимо от различных неблагоприятных условий — температуры и влажности окружающей среды, а также вибраций, возникающих во время печати.
Зачастую для рамы используют недорогой алюминиевый профиль, например, используемый в качестве мебельной фурнитуры, а порой и обычные стержни с резьбой, которые можно купить в магазинах стройматериалов. Они соединяются в единое целое с помощью изготовленных из пластика муфт, хомутов и других элементов, скрепляемых гайками и болтами. Подобное допустимо лишь в самодельных принтерах, где во главу угла ставится минимальная себестоимость конструктивных элементов и их максимальная доступность в продаже.
В некоторых моделях, в том числе «заводских», рама сделана из оргстекла или фанеры, причем особо подчеркивается, что фанерные элементы сделаны лазерной резкой; конечно, никакой лазер не сделает фанеру металлом, поэтому весьма сомнительны и долговечность подобных конструкций, и отсутствие проблем при работе с такими принтерами.
Электронные блоки
Теперь переходим к управляющей электронике.
Управляет работой всех компонентов принтера контроллер, в который поступает программа на языке G-code. Она генерируется на основе подготовленного в каком-либо 3D-редакторе STL-файла, описывающего будущую модель. G-code достаточно прост для восприятия: в строчках программы содержатся команды на перемещение головки и платформы, включение-выключение нагревателей и вентиляторов, поэтому для более-менее опытного специалиста не составляет проблемы внести правку в готовый код.
Подавляющее большинство контроллеров 3D-принтеров работает на платформе Arduino, имеющей открытые архитектуру и программный код. Язык программирования основан на C/C++ и прост в освоении, а среда программирования Arduino подразумевает работу через USB-порт без всяких дополнительных программаторов.
В качестве аппаратной части Arduino с самых ранних версий использовались и до сих пор используются распространенные и относительно недорогие микроконтроллеры Atmel: ATmega32u4, ATmega328, ATmega2560, ATmega1280 и т.п., а в последних разработках применен 32bit-микропроцессор Cortex-M3 ARM SAM3U4E. В FDM-принтерах чаще встречается ATmega2560.
Для управления различными устройствами (в 3D-принтерах это двигатели, нагреватели, вентиляторы) и получения данных (с термисторов и датчиков крайних положений) используются дополнительные модули, прежде всего драйверы шаговых двигателей, способные обеспечить соответствующие выходные токи и работу в микрошаговом режиме.
Для удобства сопряжения таких модулей с платой микроконтроллера используются промежуточные платы RAMPS (RepRap Arduino Mega Pololu Shield, где Pololu — название фирмы, специализирующейся на выпуске комплектующих для робототехники). Эти платы бывают разных версий, в настоящее время самой распространенной является RAMPS 1.4 с smd-компонентами. Такая плата с одной стороны имеет группы штыревых разъемов для соединения с платой микроконтроллера, а с другой — разъемы для подключения модулей и внешнего оборудования (двигателей, нагревателей, термисторов). В результате получается единый компактный блок, который после загрузки в микроконтроллер управляющей прошивки готов работать в составе FDM-принтера.
Некоторые принтеры управляются только через компьютер (обычно через USB-порт, но встречаются модели с подключением по сети Wi-Fi), а другие имеют собственную панель управления, с помощью которой в простейшем случае можно осуществлять контроль температур по ЖК-индикатору, запускать и останавливать печать, а в более продвинутых вариантах еще и производить калибровку, загружать и выгружать пластиковую нить. Встречаются принтеры со встроенным картоводом для SD-карт или портом для накопителей USB-флэш, через которые можно загружать файл с последующей печатью модели без участия компьютера. Всё это обеспечивается «навешиванием» на микроконтроллер соответствующих модулей и, конечно, реализацией на микропрограммном уровне в прошивке.
От контроллера к печатающей головке, даже если она одна, подходит толстый пучок проводов: к шаговому двигателю, к нагревателю и термистору хот-энда, возможно — к вентилятору экструдера (при наличии). Еще один подобный пучок соединяет контроллер с рабочим столом. Конечно, можно просто стянуть провода стяжками, что и делается в самых бюджетных самодельных конструкциях, но главное: оба эти элемента постоянно перемещаются, и даже при достаточной длине пучков есть реальная опасность, что какой-то провод либо попадет в движущиеся части, либо через какое-то время просто перетрется или обломится. Поэтому эти провода укладывают в специальные гибкие оболочки, обеспечивающие свободное перемещение головки и рабочего стола, но в то же время страхующие от обрывов и замыканий.
Понятно, что принтер не будет работать без питания. Причем если для питания электронных схем зачастую вполне достаточно возможностей USB-порта, к которому обычно подключается принтер, то для двигателей и особенно нагревателей (хотя бы hot-end, если подогрев стола не предусмотрен) без блока питания соответствующей мощности не обойтись.
Поскольку процесс печати бывает очень длительным — время изготовления сложных моделей может занять 10–15 часов и более, то желательно позаботиться и о бесперебойном питании как самого принтера, так и компьютера, к которому он подключен (если, конечно, рабочие коды не загружаются с встроенного в принтер картовода). Понятно, что суммарное потребление энергии будет немалым, и подобрать ИБП, способный обеспечить работу в течение многих часов, и непросто, и дорого, но нужно хотя бы принять меры против сильных импульсных помех на линии электропитания, к которой подключен принтер, и отключить в управляющем компьютере переход в режим энергосбережения — кроме, конечно, гашения экрана.
Иллюстрации получены из различных источников в интернете
www.ixbt.com
3D печать для самых новеньких. От А до Я. Кинематика.
В данной статье мы разберемся, что такое 3D печать и какая бывает кинематика 3D принтеров.1. 3D печать. Какая она на вкус?
Технологий печати существует большое множество, от FDM (FFF), по которой печатает больше 90% принтеров на данном портале, до SLA/DLP/LCD (с фотополимерами) и SLS/SLM (спекание порошка с помощью мощных лазеров)Нас на начальном этапе интересует FDM – послойное наплавление расплавленного прутка. На картинке ниже изображен хотенд (Hot end) – та часть экструдера 3D принтера, где происходит расплавление прутка.
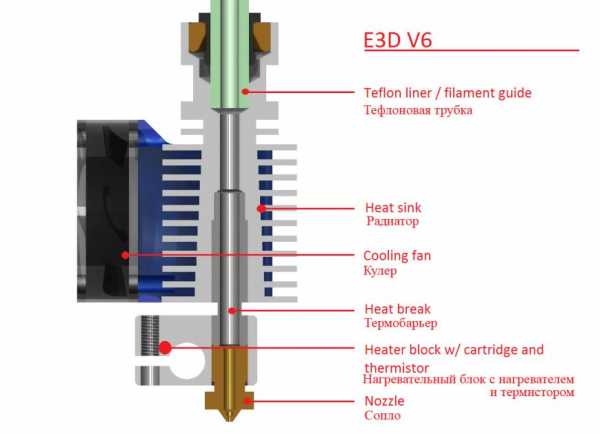
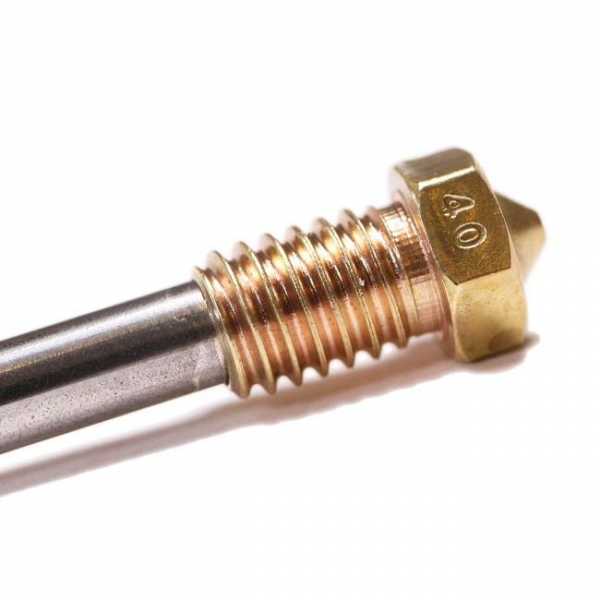
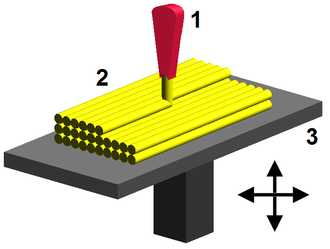
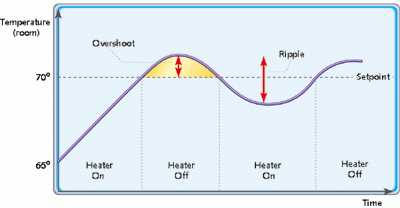
Термобарьер служит для того,что бы минимизировать нагрев пластика выше термоблока.
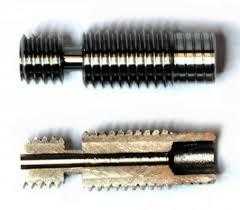
Наиболее часто выполняется из нержавеющей стали. У нее теплопроводность ниже, чем у обычной,нелегированной стали. Для предотвращения плавления прутка выше термоблока сверху на термобарьер накручивается радиатор и обдувается кулером. Все достаточно просто.
Очень часто возникает протечка расплавленного пластика через резьбу.
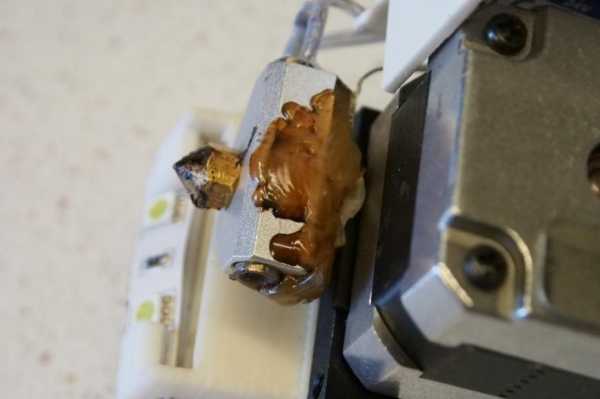

Иногда его выполняют совмещенным с хотэндом, и тогда такой тип экструдера (это все вместе хотэнд+фидер) называют директом (direct), то есть подача прямая, без трубок.
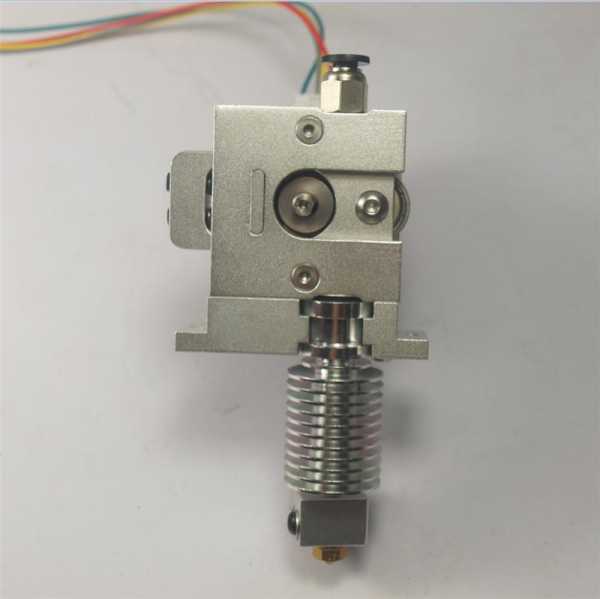
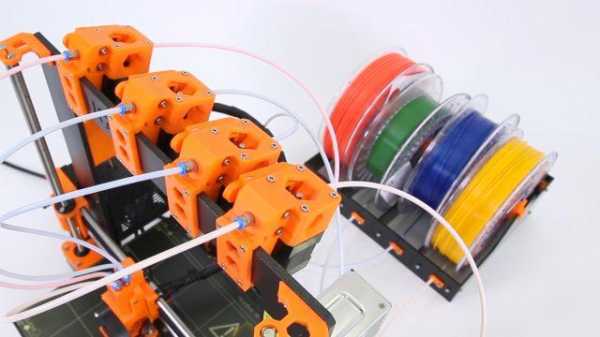
Директ экструдер:
1. Достоинства:
а) Более надежный за счет меньшего числа соединений для подачи пластика;
б) Менее придирчив к материалам, которыми печатает, в частности резиной на основе каучуков проблематично печатать на боуден экструдерах;
2. Недостатки:
а) Большой вес, за счет этого при ускорениях/замедлениях можно наблюдать небольшую рябь на поверхности детали;
б) Габариты. Они очень сильно влияют на область построения. Скажем, как на картинке выше, директ с 4 цветами был бы очень громадным. А для боудена это в самый раз.
Боуден экструдер:
1. Достоинства:
а) Вынесенный мотор снижает вес движущихся частей принтера, а их меньшая инерционность не влияет на поверхность модели;
б) Катушка не дергается вслед за моделью, а то при запутывании витков катушки с директом получим пропуск шагов, так как каретка будет тянуть за собой катушку.
2. Недостатки:
а) Настройки ретракта (вытягивание прутка обратно при холостых перемещениях, что бы расплавленный пластик, расширяясь не сочился из сопла) сложнее, так как пруток меньше внутреннего диаметра трубки, он имеет свойство тянуться;
б) Сложнее, чем на директе, выбрать все зазоры, чтобы печатать различными гибкими пластиками. Все, кто говорит,что на боудене печать невозможна гибкими пластиками – нагло врут. Я печатаю. И вполне успешно.
Теперь переходим непосредственно к механике и ее калибровке.
Часть 2. Механика. Что, как и чем дергает?
Существует весьма ограниченное число кинематических схем, под которые написана прошивка, и которые вполне сносно отрабатывают перемещения.Рассмотрим все, от самых распространенных:
1. Конструкция и кинематика от Джозефа Прюши ( не надо читать Прусся,Праша и прочее, это имя человека, в конце концов).
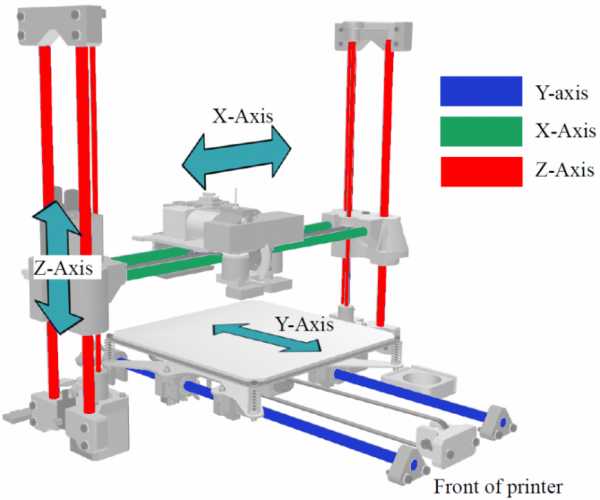
Вот винт с трапециеидальной резьбой. Как шпильки с метрической резьбой выглядят прикладывать не буду.
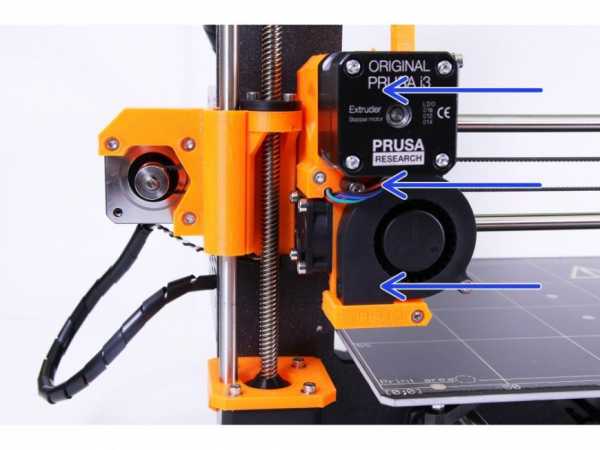
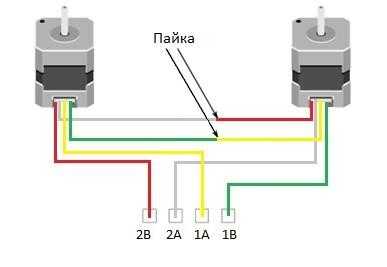
Плюсы данной кинематики:
1) Независимое перемещение каждой из осей. Легко поймать понять какая ось пропускает шаги. Кинематика перекочевала в принтеры от фрезерных ЧПУ, поэтому многие производители делают на ней настольные фрезерные станки, вместо экструдера предлагают установить лазер для гравировок или резки, шпиндель для фрезеровки плат, экструдер для шоколада или даже теста, что б печь блины.
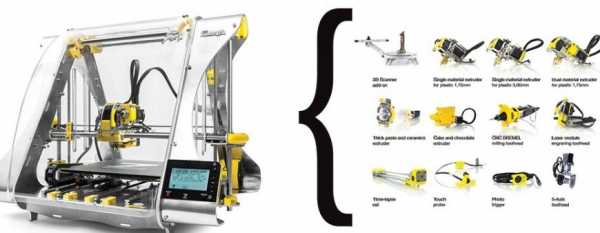
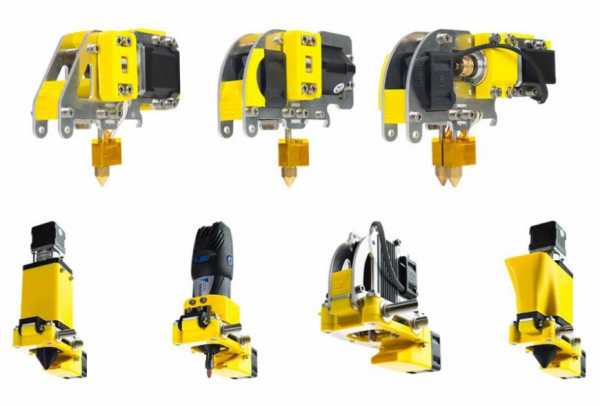
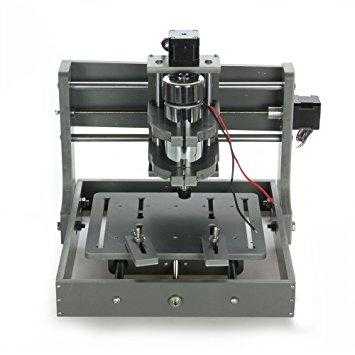
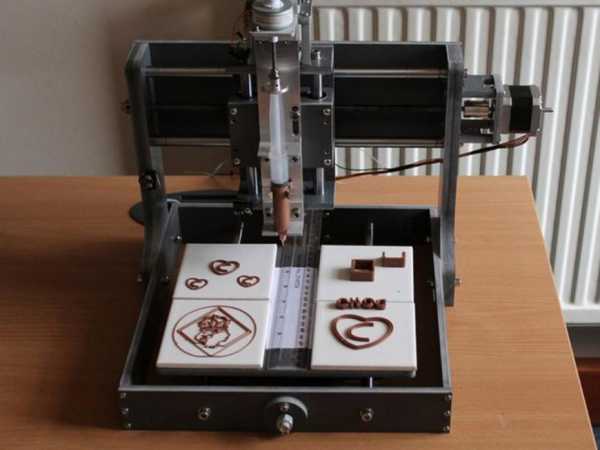
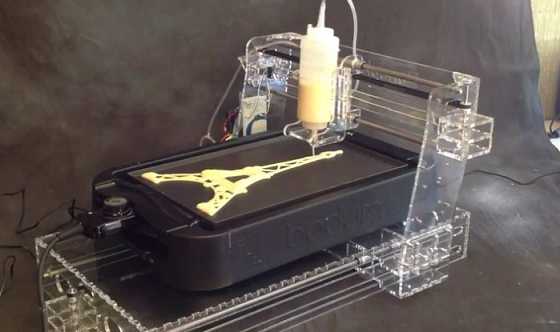
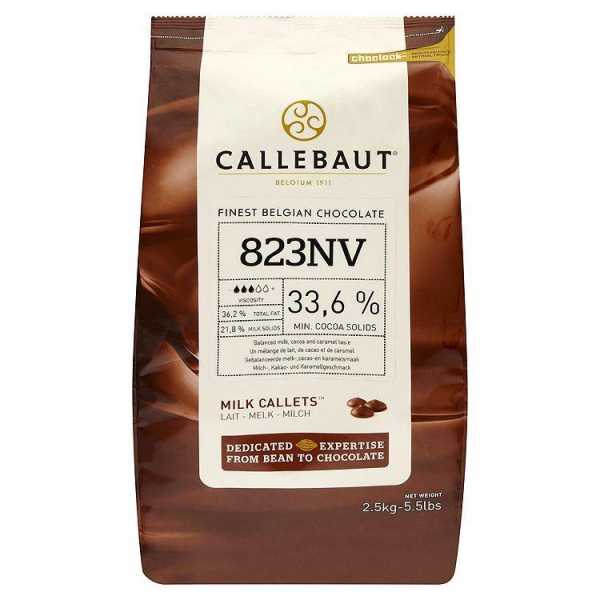
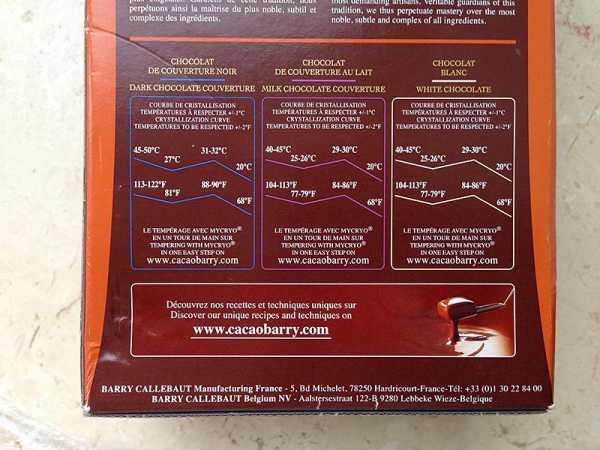
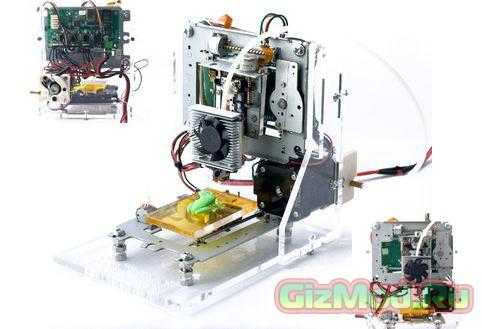
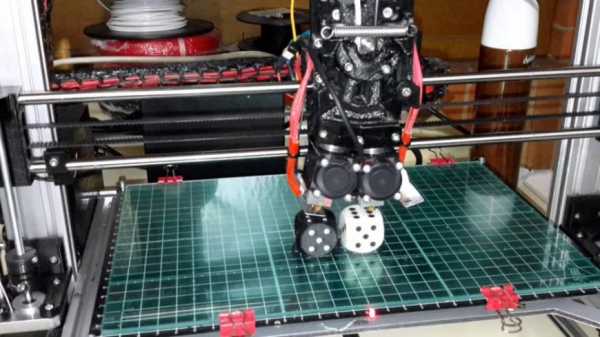
Недостатки данной кинематики:
1) Сложная калибровка. Да, поскольку стол ‘дрыгается’ печатать сложновато качественно, ибо деталь+стол при резкой смене направления перемещения по инерции стремяться ехать дальше. Получаются некрасивые артефакты печати. И для качественной печати нужна небольшая скорость. А вообще, все зависит от рамы. У меня первым принтером была китайская прюша. С акриловой рамой.
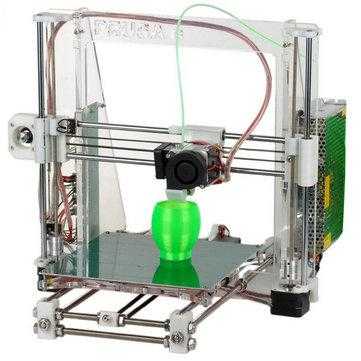
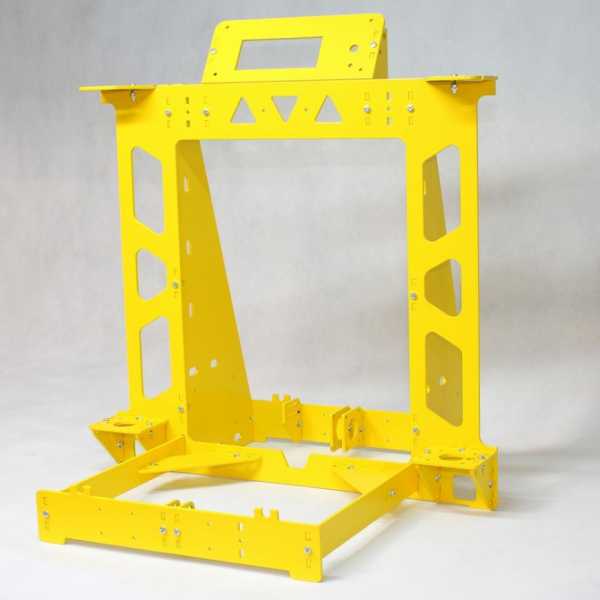
2) Деламинация. Из-за открытого корпуса и постоянно перемещающейся платформы горячий воздух, можно сказать, постоянно сдувается, а охлаждая излишне деталь сквозняками мы увеличиваем и без того большую усадку нейлонов,абс и прочих капризных пластиков. Кто-то шьет шубу для принтера из ткани, а кто-то довольствуется и коробками.
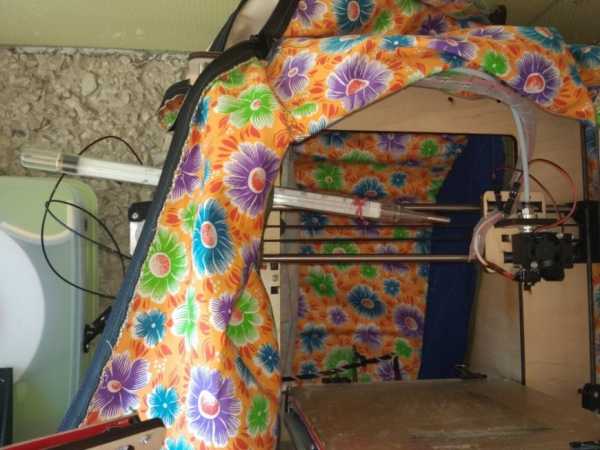
Основные моменты правильной калибровки принтеров с данной кинематикой:
1) Установить принтер на ровную поверхность. Желательно горизонтальную. Для этого необходим пузырьковый уровень. Далее устанавливаем по уровню положение оси X.
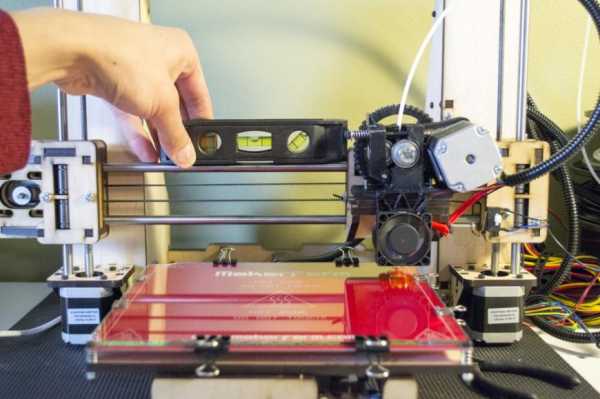
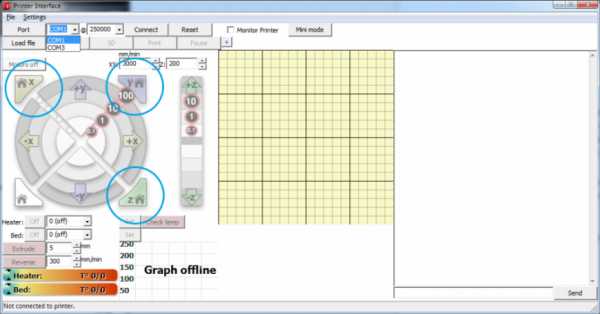
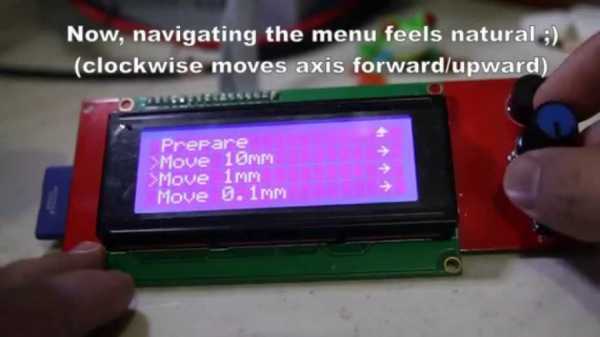
Постараюсь избавить вас от ошибок. На фото принтера выше стекло на столе крепится аж 8 зажимами. И вполне возможно, что по центру будет горб. Чтобы избежать подобных проблем стекло стоит закреплять 3 зажимами. Плоскость строится, как известно из начертательной геометрии, по 3 точкам. И калибровка будет проще в этом случае. Просто подкручиваем винт над концевиком по Z.
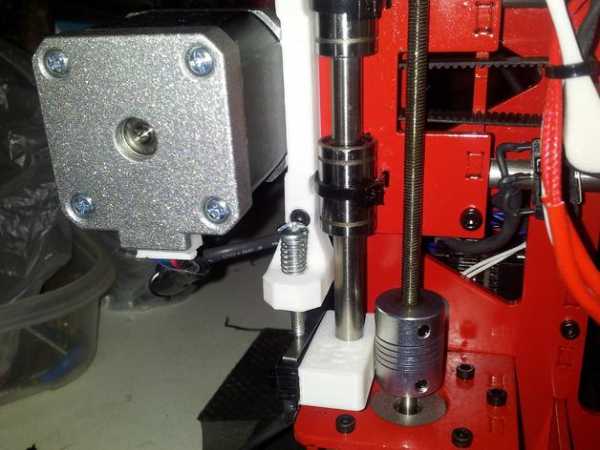
Касательно вобблинга.
Всякие антивобблинговые системы вроде установки продшипника в верхнюю опору не работают.
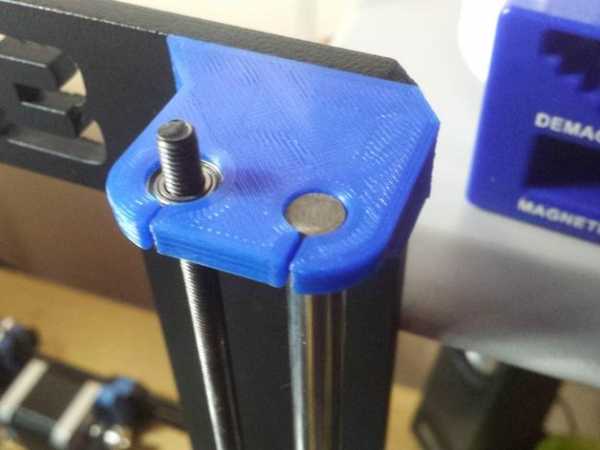
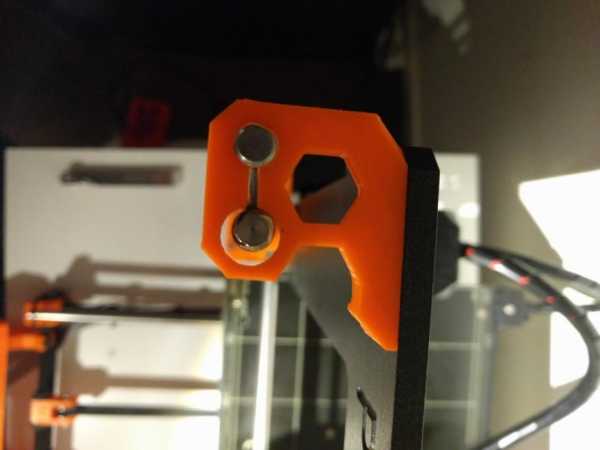
2. Конструкция по типу кинематики принтеров компании Felix printers.
Таких принтеров много, такие делает МЗТО (mz3d.ru), уже упомянутые Felix. По сути кинематика та же, что и у Prusa. Независимые друг от друга оси. Только теперь стол ездит не вдоль одной оси, а сразу вдоль целых двух. Вдоль оси Z, и по оси Y.
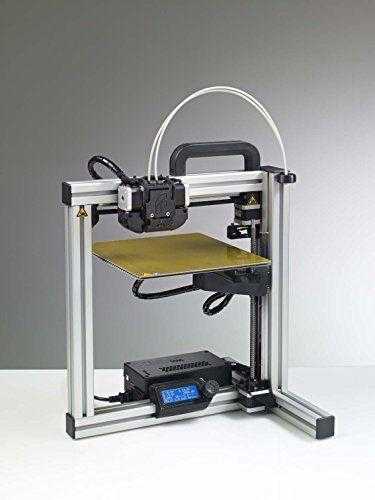
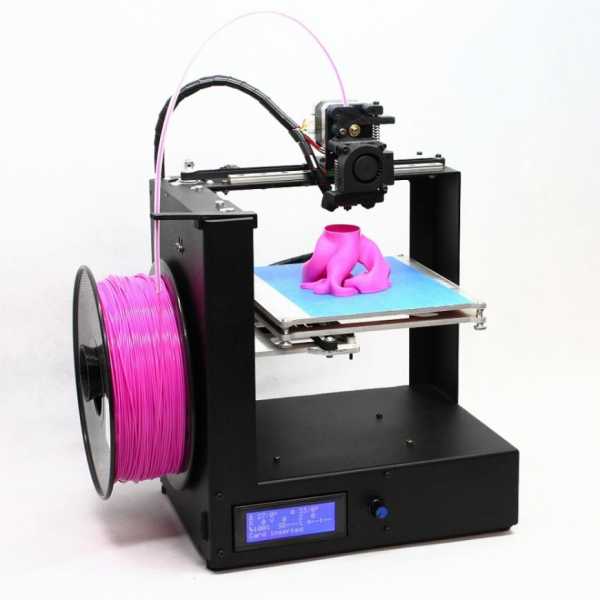
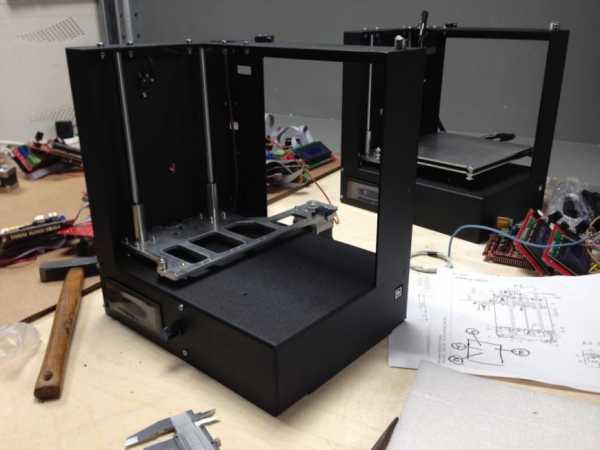
Плюсы данной кинематики:
1) Отсутствует второй мотор по оси Z. Пресловутого вобблинга нет просто потому, что есть 2 вала и 1 винт. Винт, так же не стоит закреплять сверху. Если это не ШВП.
ШВП это отдельная тема. Если брать качественную ШВП, скажем, от тех же Hiwin, то она изготавливается как минимум по 7 классу точности (если катанная, а если шлифованная, то класс еще выше) и устанавливаться должны в подшипниковых опорах. Со стороны привода – 2 радиально-упорных подшипника back-to-back,а с другого конца – радиальный со свободной посадкой для компенсаци теплового расширения.
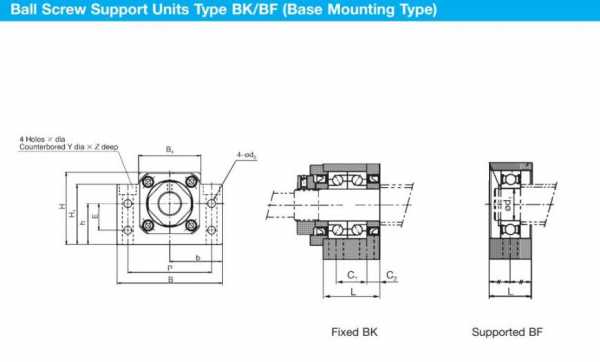
2) Много места для установки директ-экструдера. Как и в предыдущей кинематике есть простор для творчества, подбирать тот самый, единственный и неповторимый экструдер, который вам по душе.
3) Жесткая рама. Есть возможность сделать нормальную раму. Жесткую,прочную. Да хоть чугуниевую. Ребята из Феликса решили не забивать голову и лепят из алюминиевого профиля. МЗТО пошли дальше, погнули стальной лист. А полку под установку стола отфрезеровали из листа алюминия.
4) Если брать конструкцию Феликса на профиле, то с помощью замены пары кусков профиля и винта по Z можно увеличить область печати.
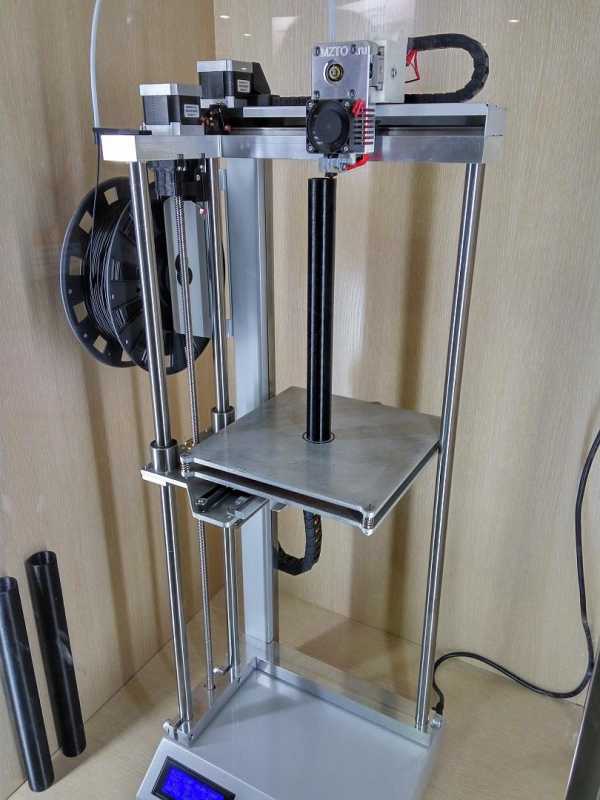
Недостатки кинематики:
1) Несомненно, большие дергающиеся массы. Стол вперед-назад,а если включить движение по Z при холостых перемещениях (Z-hope), то будет дискотека.
2) Нет возможности сделать ему нормальную термокамеру. Стол двигается вперед-назад и градиент температуры просто сдувается. Отсюда проблемы при печати нейлонами или ABS. Небольшие сквознячки в комнате с легкостью покажут вам где раки зимуют как усаживается материал.
Калибровка стола данного принтера аналогична калибровке стола у Prusa, только несколько проще. Проще за счет того, что ось X вам выставлять по уровню не надо, она автоматически выставлена при сборке рамы. Подводим сопло к столу и крутим барашки.
3. Кинематика Ultimaker.
Одна из наиболее распространенных вариаций Cartesian кинематики.
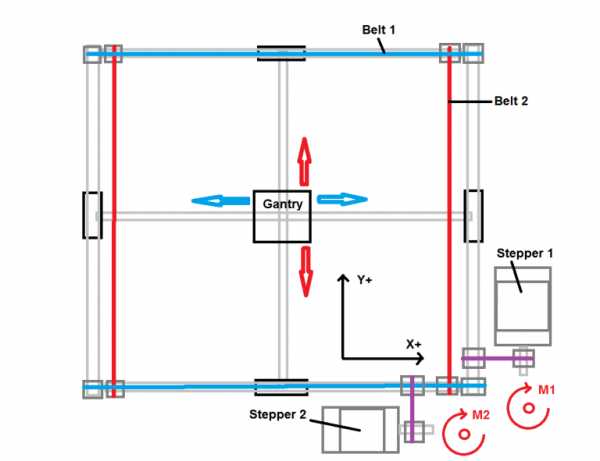
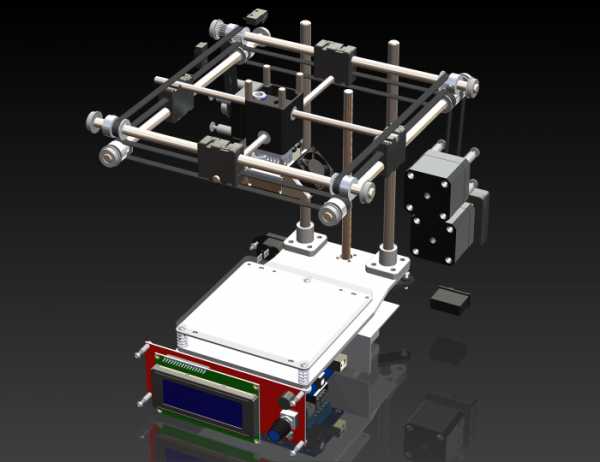
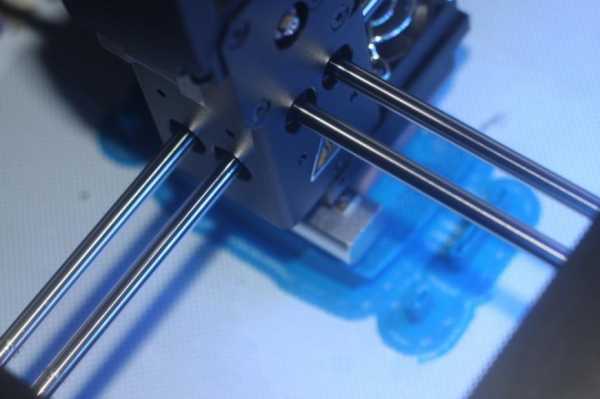
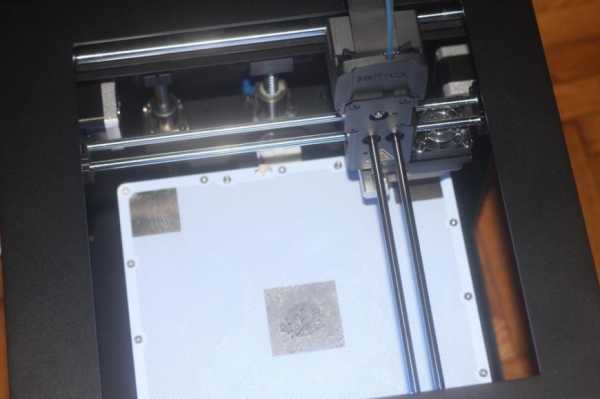
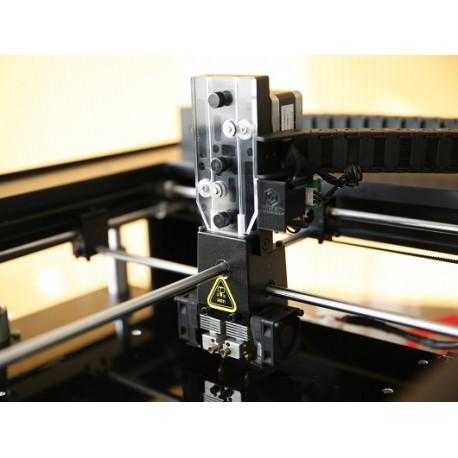
Плюсы данной кинематики:
1) Стол движется только вдоль одной оси. Вертикальной. И градиент температур никоим образом от этого не страдает. Стол консольный, поэтому желательно предусмотреть ребра жесткости или учесть это толщиной стола.
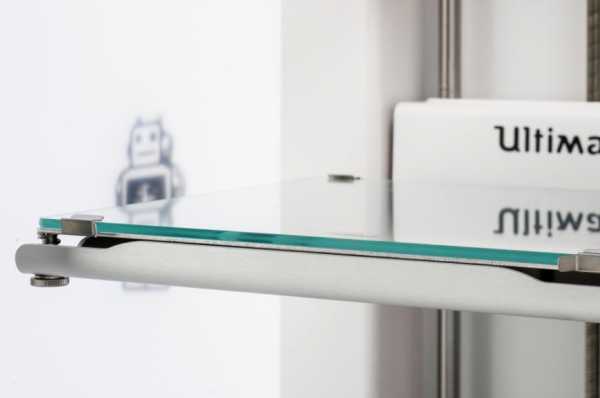
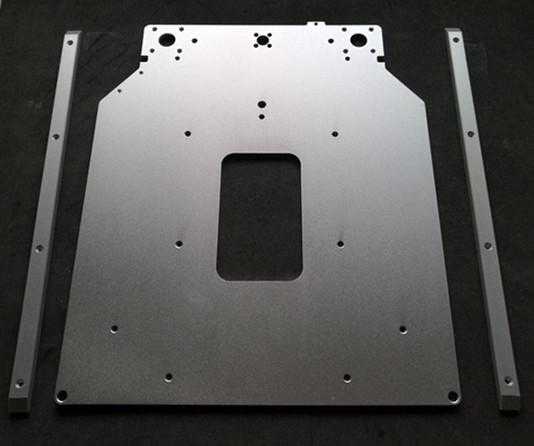
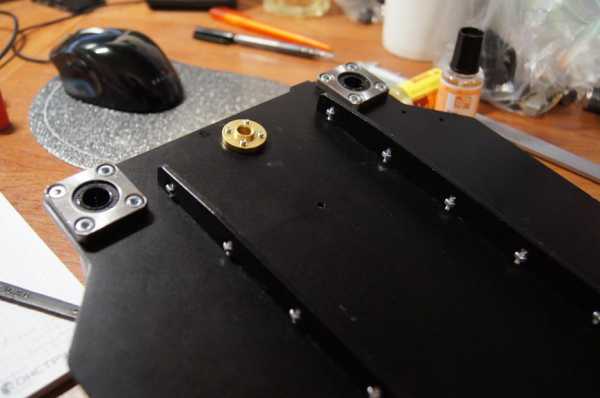
3) Корпус закрытый, что защищает от сквозняков, и следовательно деламинации. Некоторые для пущего эффекта ставят акриловую дверцу.
Минусы кинематики:
1) Для хорошей печати мало купить пачку ровных валов. Собрать все эти валы правильно воедино та еще задачка. Заодно и купить хорошие подшипники. Не то, китайское барахло, что чаще втюхивают на али, а нормальные подшипники. Если подшипники, что ставят в корпус будут плохо вращаться – печать будет рывками и со сдвигом слоев. Последствия можно спросить у Вани (Plastmaska). Так же, покупая леопардовые втулки латунные подшипники с графитовыми вставками будьте готовы к тому, что они будут люфтить. А если будет люфт – вся конструкция будет стучать.
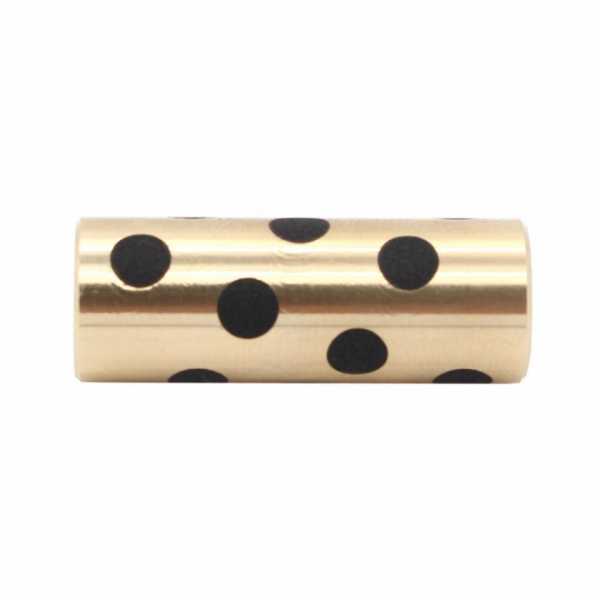
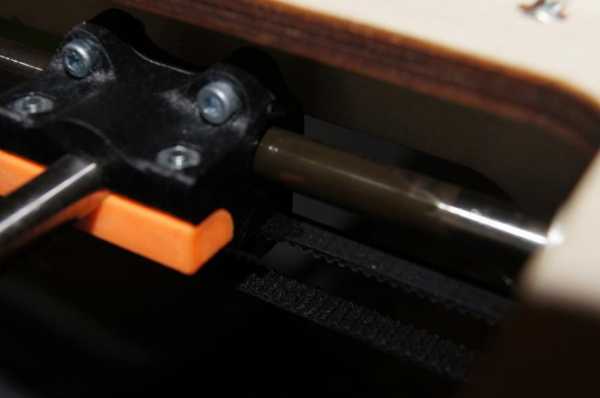
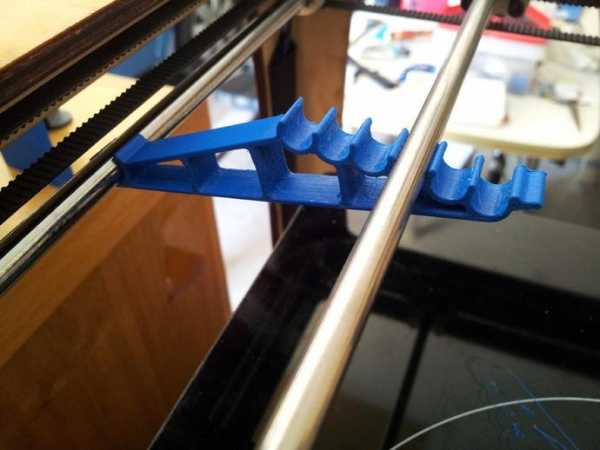
3) Конструкция не предусматривает увеличение области печати с помощью пары кусоков профиля, поэтому размеры хотенда имеют значение. Директ сложновато поставить, но можно при желании.
Калибровка стола проще некуда. Стол часто на 3 точках крепления. Перемещаем хотенд по 3 точкам и крутим барашки.
4. Кинематика, используемая фирмой Makerbot.
Так же, весьма широко распространена. В частности принтеры компании Makerbot, BQ, BCN3D ,Magnum, клон магнума – Zenit и вполне сносные реплики makerbot – Flashforge и Hori работают на данной кинематической схеме.
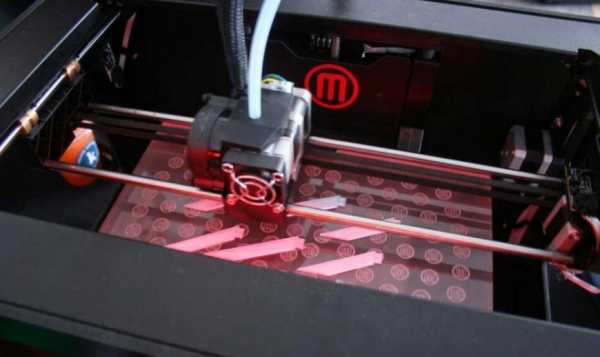
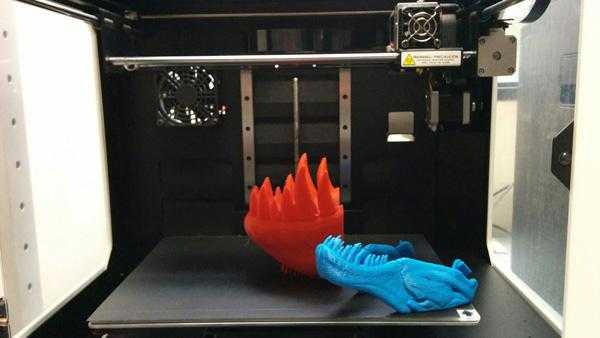
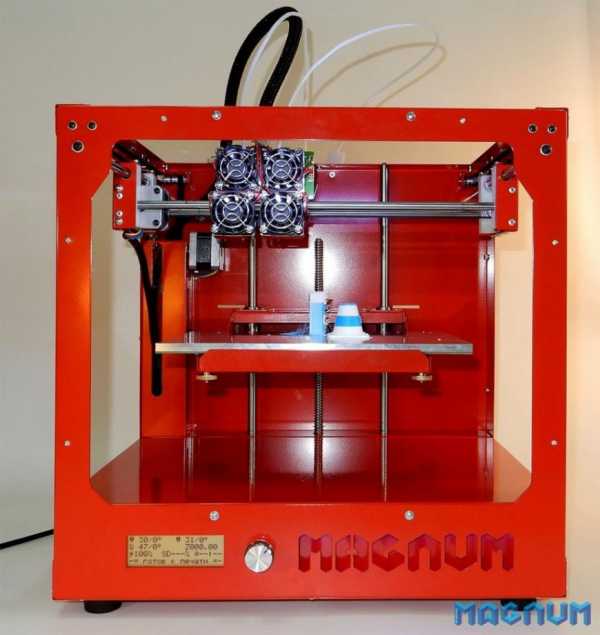
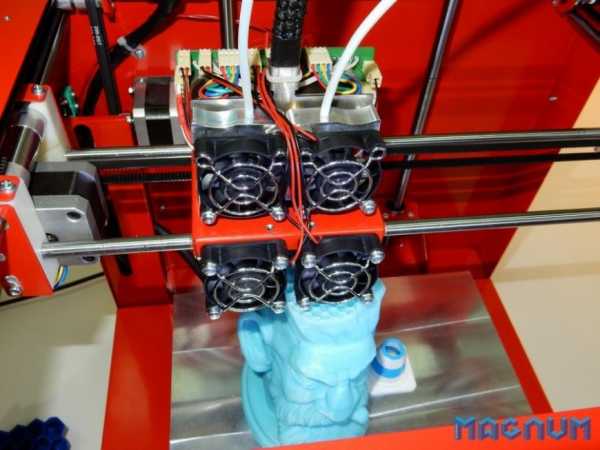
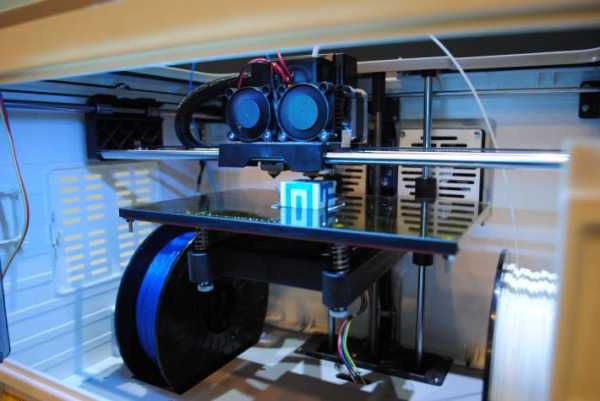
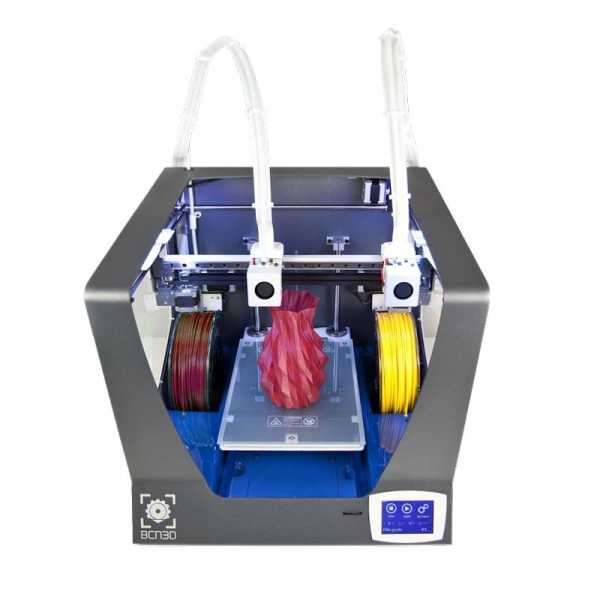
Основной недостаток заключается в том, что на катающейся балке с одной стороны висит двигатель, создавая эдакий дисбаланс. Этот недостаток компенсировали в двухэкструдерном варианте – BCN3D Sigma. Там у каждой bowden-головы для перемещения вдоль балки есть свой двигатель. И они установлены по краям балки и уравновешивают друг друга. Для равномерного перемещения каждого из краев балки применяется 2 вала, шкивы и ремни. Ремни необходимо натягивать одинаково.
Достоинства кинематики:
1) Независимое перемещение каждой из осей.
2) Движущийся по Z стол. Градиент температур не страдает ‘сдуванием’.
3) Закрытый корпус. Если не закрытый, то есть вполне нормальный с точки зрения эстетики шанс закрыть его.
4) Масштабируемость кинематики возможна. Различные BigREP и иже с ними с метровыми областями печати используют именно эту кинематику, так как различные H-bot/CoreXY будут адово звенеть по причине наличия 4-5 метровых ремней и их растяжения во время ускорений.
Недостатки кинематики:
1) Неуравновешенные массы на движущейся балке, отсюда максимальная скорость печати, с приемлемым качеством не больше 60-80 мм/с. Некоторые умудряются их уравновесить и это не столь заметно.
2) Громоздкие конструкции на валах, дабы избежать дисбалланса при перемещениях.
3) Необходимо следить, чтобы натяжения ремней справа и слева были одинаковы.
4. Кинематика H-bot/CoreXY.
Следующая по распространению. Так же, Cartesian. Два мотора неподвижны, но перемещают каретку по направляющим с помощью одного длинного куска ремня, или с помощью двух, но покороче. Математика сложнее, чем у предыдущих, так как необходимо синхронизировать поворот обоих роторов двигателя. То есть, для перемещения вдоль каждой оси нужно вращать оба мотора, а для перемещения по диагонали – всего 1.
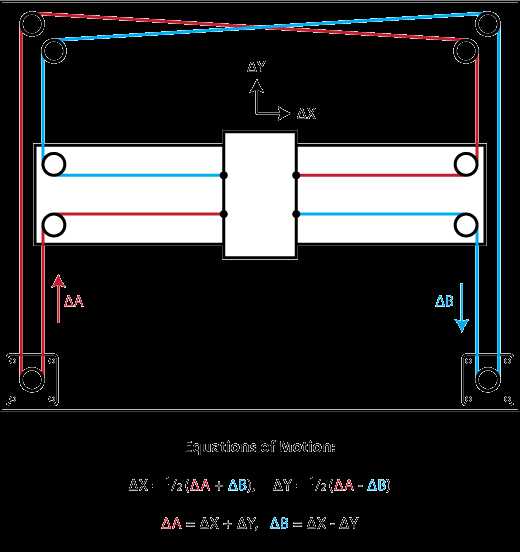
По сути математика для вращения моторов одна и та же, а реализация в механике разная. Один из самых больших недостатков H-bot перед CoreXY состоит в том, что при перемещениях ремень стремится повернуть балку.
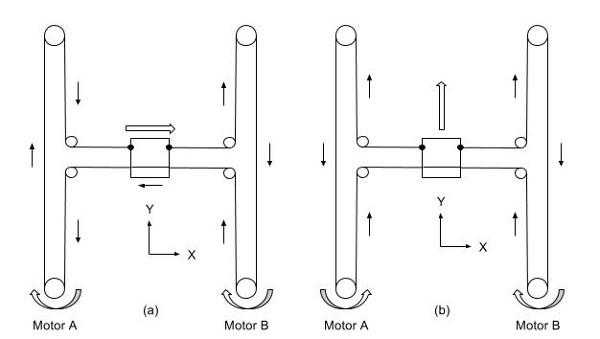
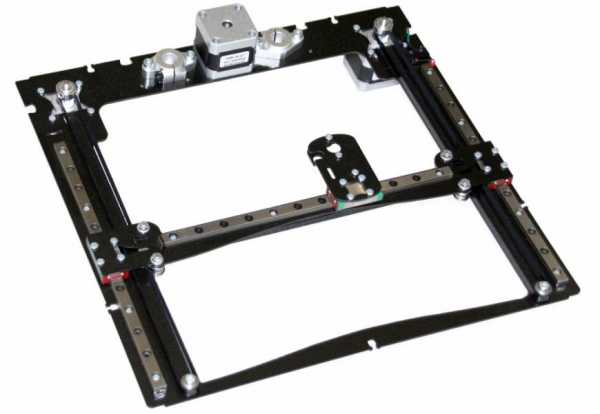
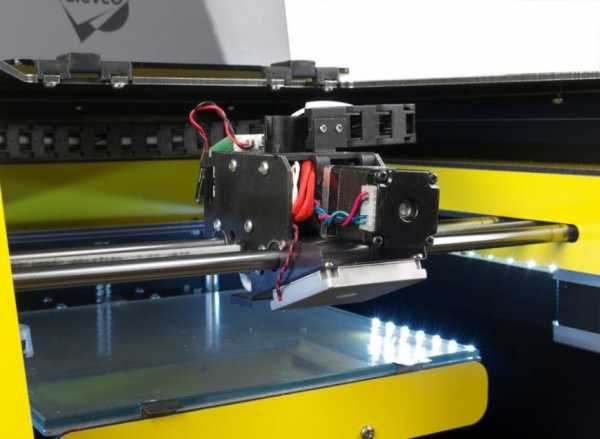
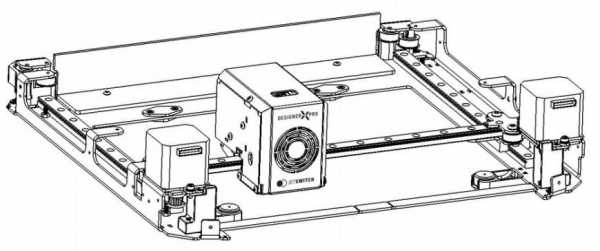
CoreXY, в отличии от H-bot, приводится в движение при помощи двух ремней.
И так, для простоты понимания, опишу положительные и отрицательные стороны каждой вариации этой кинематики.H-bot.
Достоинства:
1) Ремень необходим всего один, а схема предусматривает его работу без скручиваний.
2) Натягивать один ремень удобнее, чем 2, поэтому в этой схеме нужен всего один нормальный натяжитель.
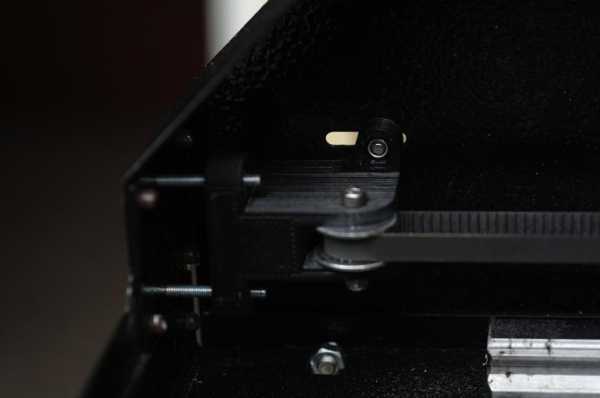
Недостатки:
1) Ремень имеет свойство растягиваться со временем, а так как величина растяжения напрямую зависит от длины, то необходимо следить за его натяжением. Иначе получатся некрасивые волны на поверхности перед остановками.
При слабой натяжке ремня каретка будет иметь такой люфт.2) Необходимо выставлять ролики строго перпендикулярно плоскости XY, так как при небольшом перекосе ролика ремень будет съедаться об буртики ролика. И мы получим такую вот бяку.
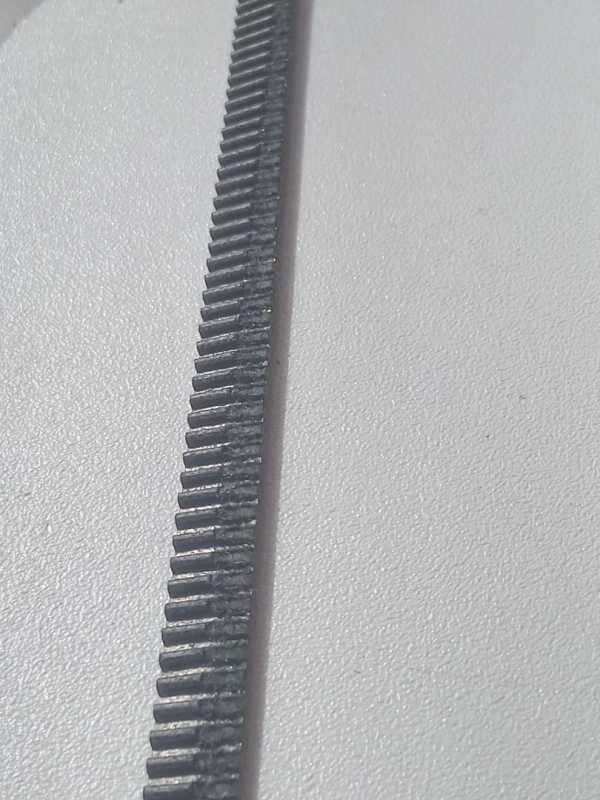
3) Сложная математика, из-за чего на скоростях выше 100 мм/с могут быть проблемы с нехваткой ресурсов 8 битных плат.
CoreXY.
Достоинства:
1) Два коротких куска ремня. Их проще найти, чем один длинный.
2) Силы уравновешивают балку, а не стремятся ее повернуть, поэтому эту кинематику можно собирать и на валах.
Недостатки:
1) Есть схемы с перекручиванием ремней и перехода ремня с одного уровня на другой – для ремня это не очень приятно. Особенно, когда один ремень трется об другой. На видео этот момент есть.
:{}
2) Сложность нятяжки ремней. Их необходимо натягивать одинаково, иначе силы нятяжки будут стремиться повернуть каретку.
3) Сложность сборки и разработки. Необходимо выдержать вертикальность роликов, относительно горизонтальности площадки для установки моторов и рельс. Небольшой перекос роликов приведет к тому, что ремень будет стремиться съехать по ролику, а если будет упираться в буртик ролика, то будет скрипеть, если буртик большой, а если маленький – то будет пытаться на него заехать, как на фото из описания h-bot.
Общий недостаток кинематики – плохая масштабируемость. То есть ставить такую кинематику для области печати больше 300*300 весьма проблемно просто из-за удлинений ремня при печати. Для небольших принтеров с большой скоростью печати – одна из лучших кинематик.
5. Delta кинематика.
Кинематика основана на движениях дельта-робота.
Только вместо захватов устанавливается хотенд. Имеет свои проблемы с настройкой, но на печать можно залипать очень долго. Редко когда устанавливают директ-экструдеры, так как эффектор (площадка для установки хотенда) часто крепится на магнитах и необходимо максимально разгрузить его. Но для уменьшения длины трубки (а конкретнее, влияния длины трубки на качество печати за счет правильной настройки ретрактов ( вытягивания пластикового прутка назад с целью уменьшения его вытекания от расширения)) на качество печати, экструдер вешают на те же каретки, но на отдельных подвесах. За счет этого уменьшается длина bowden трубки и увеличивается качество печати.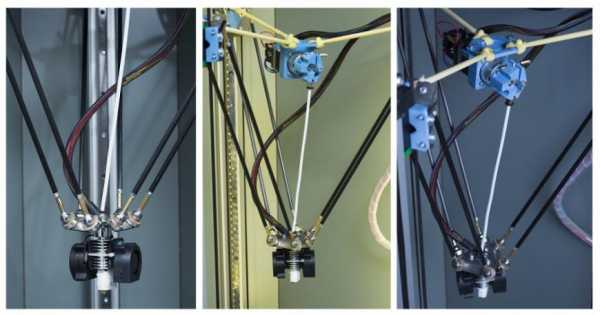
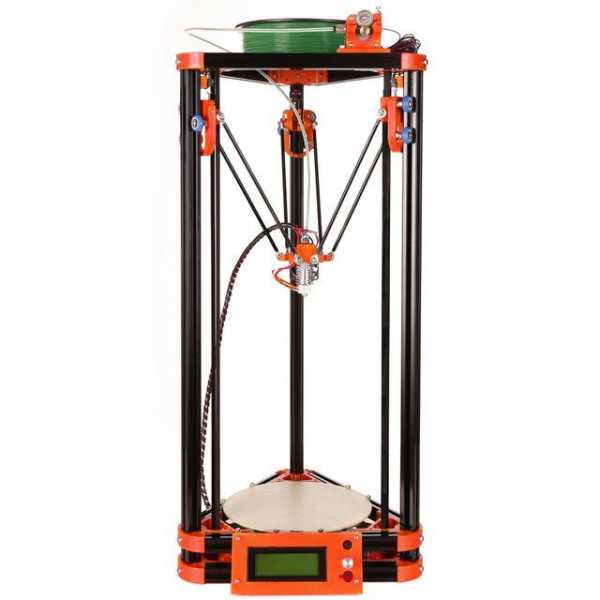
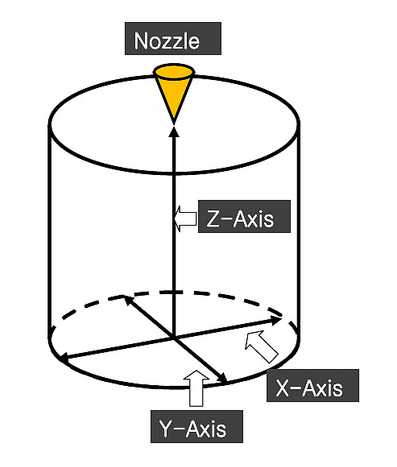
1) Легко кастомизируется. Для увеличения высоты достаточно прикупить 3 куска профиля подлиннее, и увеличить максимальную высоту в настройках.
2) Занимает мало места. Она чаще высокая, чем громоздкая по длине и ширине, за счет этого компактность.
3) Если сделать легкий эффектор ( каретка, на которой установлен хотенд), то можно добиться больших скоростей без потери качества печати.
4) Перемещение по высоте не отличается от перемещения по XY. Таким образом, нет залипания линейных подшипников на переездах стола, как у Cartesian принтеров, лишних двигателей, катающихся на балке…
5) Отсутствие выступающих частей дает возможность закрыть корпус и придать раме жесткости.
6) Эстетическая часть – на работу дельты интереснее залипать.
Недостатки:
1) Сложная математика перемещений, рекомендуется ставить сразу 32-битные платы.
2) Сложная настройка. Частая проблема в настройке – убрать так называемую ‘линзу’, ведь каждый стержень вращается с радиусом, и при некорректной настройке у вас печатаемая плоскость будет либо выпуклой,либо вогнутой линзой.
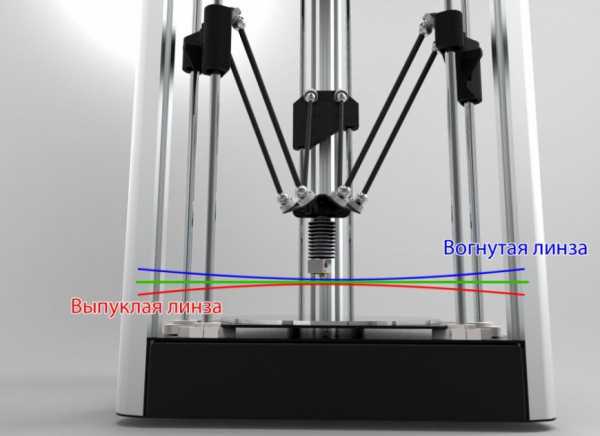
4) Сложность установки директ-экструдера. Он получается тяжелым, а так как многие дельты делаются на магнитах, то не будет возможности разогнаться. Хотя, есть одно аккуратное и легкое решение – установка готового директ-экструдера с редуктором. Как, например E3D Titan Aero или Bondtech BMG.
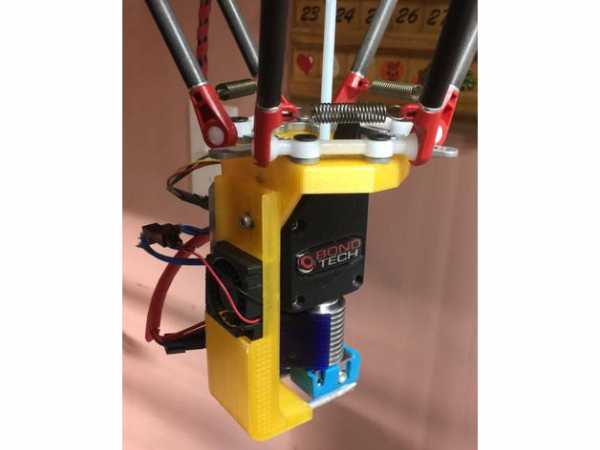
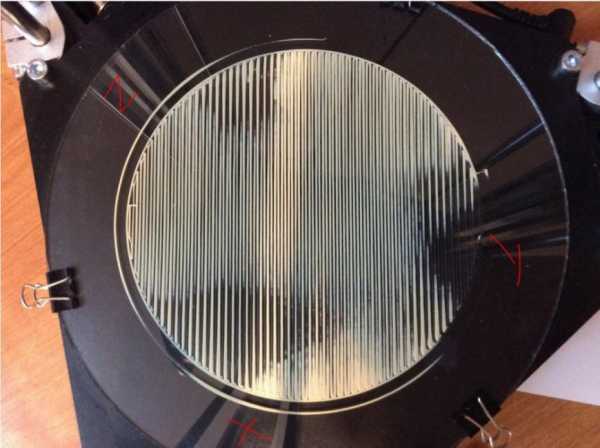

3dtoday.ru