Устройство и принцип работы плазменного резака
Плазмотрон – базовый элемент аппарата плазменной резки
Плазменная резка давно зарекомендовала себя как высокопроизводительный, безопасный и скоростной метод обработки металлов, позволяющий получить чистую и ровную поверхность без дополнительной обработки. Главным «участником» этого процесса является резак – базовый рабочий орган плазмореза. Несмотря на растущий интерес к технологии, путаница в терминологии остается до сих пор: иногда под «плазмотроном» ошибочно подразумевают всю установку для резки. Что же представляет собой этот аппарат и как именно он устроен?
Составляющие плазмотрона
- Сопло, формирующее плазменную струю. Размер реза, характеристики дуги и скорость охлаждения оборудования во многом зависят от диаметра комплектующей и ее длины: чем она длиннее, тем аккуратнее получается разрез, но вместе с тем и сокращается срок эксплуатации.
Самыми лучшими считаются сопла из чистой меди, поскольку этот материал удачно сочетает высокую теплопроводность и малую стоимость.
- Электрододержатель с катодом (электродом), изготовленным чаще всего из гафния, реже – из циркония, бериллия или тория (оксиды последних могут быть токсичными или радиоактивными и наносят вред здоровью оператора, поэтому их применяют не так часто).
- Дуговая камера для подачи воздушного потока.
- Изоляционная втулка, разделяющая электродный и сопловый узлы.
- Кожух с внешней стороны.
- Кабель-шланговый пакет, соединяющий устройство с источником питания. Кабель служит для передачи тока от инвертора или трансформатора, а шланг – для транспортировки сжатого воздуха.
- Роликовые упоры, головка резака, защитный колпачок также входят в конструкцию прибора, хоть и не принимают непосредственного участия в процессе.
В комплектации может быть также завихритель, например выполненный в виде керамических колец или шайб. Размещенные перед входом в сопловый узел подобные приспособления обеспечивают вихревую подачу газа в дуговую камеру и способствуют более эффективному сжатию дуги и ее стабилизации.
При обработке металла толщиной до 10 мм одного комплекта «сопло + электрод» хватает примерно на 8 рабочих часов
Принцип работы
Сигналом к началу работы становится нажатие кнопки «розжиг» или «старт», в ответ на которое от источника питания в плазмотрон поступают токи высокой частоты. Под их воздействием внутри аппарата между наконечником сопла и электродом образуется дежурная электрическая дуга температурой 6000 – 8000 °С, столб которой заполняет собой весь канал.
Следующий этап – в камеру по шлангу поступает сжатый воздух. Проходя через электродугу, он нагревается и ионизируется, приобретая токопроводящие свойства, а объем увеличивается в 50-100 раз. Сопло, суженное книзу, формирует воздушный поток, готовый вырваться наружу на большой скорости. Именно этот нагретый до 25000-30000 °С ионизированный воздух и называют плазмой, выполняющей разрез.
Плазмообразующими газами выступают кислород, смесь водорода с аргоном, азот.В промышленности, кроме них, используют ряд защитных газов (гелий, аргон) и их смеси.
В момент, когда плазма соприкасается с поверхностью металла, дежурная дуга гаснет, а вместо нее зажигается рабочая, или режущая. Под ее действием металл плавится, образуя рез, а расплавленные частицы удаляются струей под высоким давлением.
Охлаждение плазмотронов осуществляется воздушным или водяным способом. Первый вариант с применением потоков газа актуален для маломощных установок. Второй – с циркулирующей водой – практикуют в аппаратах высокой мощности на крупном производстве. «Жидкая» технология более эффективна, однако утяжеляет конструкцию устройства и повышает стоимость его эксплуатации.
Использование этого незамысловатого с виду аппарата позволяет не только выполнять прямые, но и делать фигурные резы, проемы и отверстия, выравнивать кромки и т.д. – как в небольших мастерских, так и в промышленных масштабах.
Принцип работы плазмореза | Строительный портал
Плазменная резка широко используется в различных отраслях промышленности: машиностроении, судостроении, изготовлении рекламы, коммунальной сфере, изготовлении металлоконструкций и в других отраслях. К тому же, в частной мастерской плазморез тоже может пригодиться. Ведь с помощью него можно быстро и качественно разрезать любой токопроводящий материал, а также некоторые нетокопроводящие материалы – пластик, камень и дерево. Разрезать трубы, листовой металл, выполнить фигурный рез или изготовить деталь можно просто, быстро и удобно с помощью технологии плазменной резки. Рез выполняется высокотемпературной плазменной дугой, для создания которой нужен лишь источник тока, резак и воздух. Чтобы работа с плазморезом давалась легко, а рез получался красивым и ровным, не мешает узнать принцип работы плазмореза, который даст базовое понятие, как можно управлять процессом резки.
- Устройство плазмореза
- Принцип работы плазмореза
- Параметры плазмореза
- Плазморез своими руками
- ЧПУ плазморез своими руками
Устройство плазмореза
Аппарат под названием «плазморез» состоит из нескольких элементов: источника питания, плазменного резака/плазмотрона, воздушного компрессора и кабель-шлангового пакета.
Источник питания для плазмореза подает на плазмотрон определенную силу тока. Может представлять собой трансформатор или инвертор.
Трансформаторы более увесисты, потребляют больше энергии, но зато менее чувствительны к перепадам напряжения, и с помощью них можно разрезать заготовки большей толщины.
Инверторы легче, дешевле, экономнее в плане энергопотребления, но при этом позволяют разрезать заготовки меньшей толщины. Поэтому их используют на маленьких производствах и в частных мастерских. Также КПД инверторных плазморезов на 30 % больше, чем у трансформаторных, у них стабильнее горит дуга. Пригождаются они и для работы в труднодоступных местах.
Плазмотрон или как его еще называют «плазменный резак» является главным элементом плазмореза. В некоторых источниках можно встретить упоминание плазмотрона в таком контексте, что можно подумать будто «плазмотрон» и «плазморез» идентичные понятия.
Основными элементами плазменного резака/плазмотрона являются сопло, электрод, охладитель/изолятор между ними и канал для подачи сжатого воздуха.
Схема плазмореза наглядно демонстрирует расположение всех элементов плазмореза.
Внутри корпуса плазмотрона находится электрод, который служит для возбуждения электрической дуги. Он может быть изготовлен из гафния, циркония, бериллия или тория. Эти металлы приемлемы для воздушно-плазменной резки потому, что в процессе работы на их поверхности образуются тугоплавкие оксиды, препятствующие разрушению электрода. Тем не менее, используют не все эти металлы, потому что оксиды некоторых из них могут нанести вред здоровью оператора. Например, оксид тория – токсичен, а оксид бериллия – радиоактивен. Поэтому самым распространенным металлом для изготовления электродов плазмотрона является гафний.
Сопло плазмотрона обжимает и формирует плазменную струю, которая вырывается из выходного канала и разрезает заготовку. От размера сопла зависят возможности и характеристики плазмореза, а также технология работы с ним. Зависимость такая: от диаметра сопла зависит, какой объем воздуха может через него пройти за единицу времени, а от объема воздуха зависят ширина реза, скорость охлаждения и скорость работы плазмотрона. Чаще всего сопло плазмотрона имеет диаметр 3 мм. Длина сопла тоже важный параметр: чем длиннее сопло, тем аккуратнее и качественнее рез. Но с этим надо быть поаккуратнее. Слишком длинное сопло быстрее разрушается.
Компрессор

Кабель-шланговый пакет соединяет источник питания, компрессор и плазмотрон. По электрическому кабелю подается ток от трансформатора или инвертора для возбуждения электрической дуги, а по шлангу идет сжатый воздух, который необходим для образования плазмы внутри плазмотрона. Более детально, что именно происходит в плазмотроне, расскажем ниже.
Принцип работы плазмореза
Как только нажимается кнопка розжига, источник питания (трансформатор или инвертор) начинает подавать на плазмотрон токи высокой частоты. В результате внутри плазмотрона возникает дежурная электрическая дуга, температура которой 6000 – 8000 °С.
Дежурная дуга зажигается между электродом и наконечником сопла по той причине, что образование дуги между электродом и обрабатываемой заготовкой сразу – затруднительно. Столб дежурной дуги заполняет весь канал.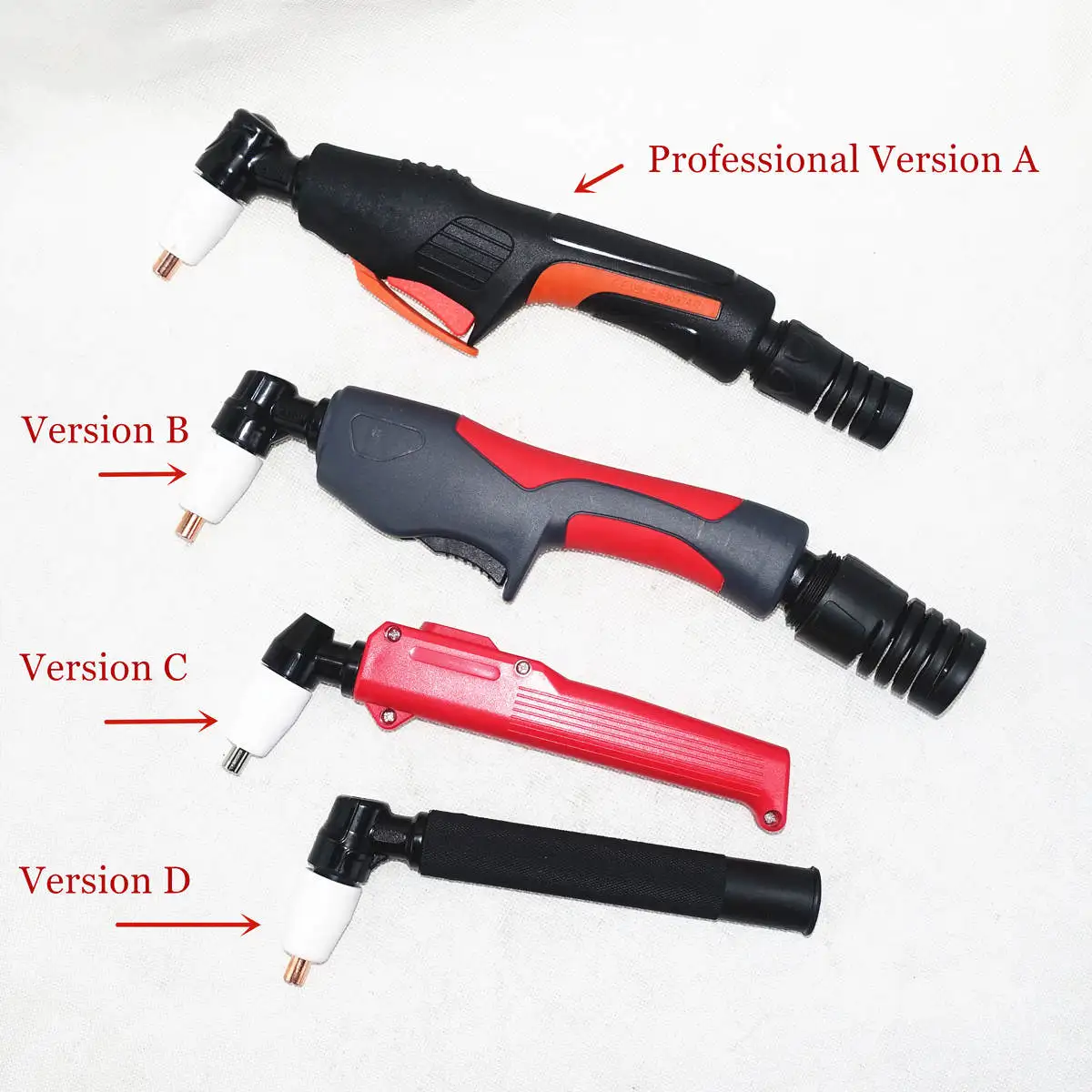
После возникновения дежурной дуги в камеру начинает поступать сжатый воздух. Он вырывается из патрубка, проходит через электрическую дугу, вследствие чего нагревается и увеличивается в объеме в 50 – 100 раз. Помимо этого воздух ионизируется и перестает быть диэлектриком, приобретая токопроводящие свойства.
Суженное к низу сопло плазмотрона обжимает воздух, формирует из него поток, который со скоростью 2 – 3 м/с вырывается из сопла. Температура воздуха в этот момент может достигать 25000 – 30000 °С. Именно этот высокотемпературный ионизированный воздух и является в данном случае
В тот момент, когда плазма вырывается из сопла и соприкасается с поверхностью обрабатываемого металла, зажигается режущая дуга, а дежурная дуга гаснет. Режущая/рабочая дуга разогревает обрабатываемую заготовку в месте реза – локально. Металл плавится, появляется рез. На поверхности разрезаемого металла появляются частички расплавленного только что металла, которые сдуваются с нее потоком воздуха, вырывающегося из сопла. Это самая простая технология плазменной резки металла.
Катодное пятно плазменной дуги должно располагаться строго по центру электрода/катода. Чтобы это обеспечить, используется так называемая вихревая или тангенциальная подача сжатого воздуха. Если вихревая подача нарушена, то катодное пятно смещается относительно центра электрода вместе с плазменной дугой. Это может привести к неприятным последствиям: плазменная дуга будет гореть нестабильно, может образовываться две дуги одновременно, а в худшем случае – плазмотрон может выйти из строя.
Если увеличить расход воздуха, то скорость плазменного потока увеличится, также увеличится и скорость резки. Если же увеличить диаметр сопла, то скорость уменьшится и увеличится ширина реза. Скорость плазменного потока примерно равна 800 м/с при токе 250 А.
Скорость реза – тоже важный параметр. Чем она больше, тем тоньше рез. Если скорость маленькая, то ширина реза увеличивается. Если увеличивается сила тока, происходит то же самое – ширина реза увеличивается. Все эти тонкости относятся уже непосредственно к технологии работы с плазморезом.
Параметры плазмореза
Все аппараты плазменной резки можно разделить на две категории: ручные плазморезы и аппараты машинной резки.
Ручные плазморезы используются в быту, на маленьких производствах и в частных мастерских для изготовления и обработки деталей. Основная их особенность в том, что плазмотрон держит в руках оператор, он ведет резак по линии будущего реза, держа его на весу. В итоге рез получается хоть и ровным, но не идеальным. Да и производительность такой технологии маленькая. Чтобы рез получился более ровным, без наплывов и окалины, для ведения плазмотрона используется специальный упор, который одевается на сопло. Упор прижимается к поверхности обрабатываемой заготовки и остается только вести резак, не переживая за то, соблюдается ли необходимое расстояние между заготовкой и соплом.
На ручной плазморез цена зависит от его характеристик: максимальной силы тока, толщины обрабатываемой заготовки и универсальности. Например, существуют модели, которые можно использовать не только для резки металлов, но и для сварки. Их можно отличить по маркировке:
- CUT – разрезание;
- TIG – аргонодуговая сварка;
- MMA – дуговая сварка штучным электродом.
Например, плазморез FoxWeld Plasma 43 Multi совмещает все перечисленные функции. Его стоимость 530 – 550 у.е. Характеристики, касающиеся плазменной резки: сила тока – 60 А, толщина заготовки – до 11 мм.
Кстати, сила тока и толщина заготовки – основные параметры, по которым подбирается плазморез. И они взаимосвязаны.
Чем больше сила тока, тем сильнее плазменная дуга, которая быстрее расплавляет металл. Выбирая плазморез для конкретных нужд, необходимо точно знать, какой металл придется обрабатывать и какой толщины. В приведенной ниже таблице указано, какая сила тока нужна для разрезания 1 мм металла. Обратите внимание, что для обработки цветных металлов требуется большая сила тока. Учтите это, когда будете смотреть на характеристики плазмореза в магазине, на аппарате указана толщина заготовки из черного металла. Если вы планируете резать медь или другой цветной металл, лучше рассчитайте необходимую силу тока самостоятельно.
Например, если требуется разрезать медь толщиной 2 мм, то необходимо 6 А умножить на 2 мм, получим плазморез с силой тока 12 А. Если требуется разрезать сталь толщиной 2 мм, то умножаем 4 А на 2 мм, получаем силу тока 8 А. Только берите аппарат плазменной резки с запасом, так как указанные характеристики являются максимальными, а не номинальными. На них можно работать только непродолжительное время.
Станок с ЧПУ плазменной резки используется на производственных предприятиях для изготовления деталей или обработки заготовок. ЧПУ означает числовое программное управление. Станок работает по заданной программе с минимальным участием оператора, что максимально исключает человеческий фактор на производстве и увеличивает производительность в разы. Качество реза машинным аппаратом идеально, не требуется дополнительная обработка кромок. А самое главное – фигурные резы и исключительная точность. Достаточно ввести в программу схему реза и аппарат может выполнить любую замысловатую фигуру с идеальной точностью. На станок плазменной резки цена значительно выше, чем на ручной плазморез. Во-первых, используется большой трансформатор. Во-вторых, специальный стол, портал и направляющие. В зависимости от сложности и размеров аппарата цена может быть от 3000 у.е. до 20000 у.е.
Аппараты машинной плазменной резки используют для охлаждения воду, поэтому могут работать всю смену без перерыва. Так называемый ПВ (продолжительность включения) равен 100 %. Хотя у ручных аппаратов он может быть и 40 %, что означает следующее: 4 минуты плазморез работает, а 6 минут ему необходимо для того, чтобы остыть.
Плазморез своими руками
Наиболее разумно будет приобрести плазморез готовый, заводского исполнения. В таких аппаратах все учтено, отрегулировано и работает максимально идеально. Но некоторые умельцы «Кулибины» умудряются смастерить плазморез своими руками. Результаты получаются не очень удовлетворительными, так как качество реза хромает. В качестве примера приведем урезанный вариант, как можно сделать плазморез самостоятельно. Сразу оговоримся, что схема далека от идеала и лишь дает общее понятие процесса.
Итак, трансформатор для плазмореза должен быть с падающей ВАХ.
Пример на фото: первичная обмотка – снизу, вторичная – сверху. Напряжение – 260 В. Сечение обмотки – 45 мм2, каждая шина 6 мм2. Если установить силу тока на 40 А напряжение падает до 100 В. У дросселя также сечение 40 мм2, наматывался той же шиной, всего около 250 витков.
Для работы нужен воздушный компрессор, естественно, заводского исполнения. В данном случае использовался агрегат производительностью 350 л/мин.
Самодельный плазморез – схема работы.
Плазмотрон лучше приобрести заводской, он обойдется примерно в 150 – 200 у.е. В данном примере плазмотрон изготавливался самостоятельно: медное сопло (5 у.е.) и гафниевый электрод (3 у.е.), остальное «кустарщина». За счет чего расходники быстро вышли из строя.
Схема работает так: на резаке находится кнопка пуск, при ее нажатии реле (р1) подает на блок управления напряжение, реле (р2) подает напряжение на трансформатор, затем пускает воздух для продувки плазмотрона. Воздух осушает камеру плазмотрона от возможного конденсата и выдувает все лишнее, на это у него есть 2 – 3 секунды. Именно с такой задержкой срабатывает реле (р3), которое подает питание на электрод для поджига дуги. Затем включается осциллятор, который ионизирует пространство между электродом и соплом, как результат загорается дежурная дуга. Далее плазмотрон подносится к изделию и загорается режущая/рабочая дуга между электродом и заготовкой. Реле геркона отключает сопло и поджиг. Согласно данной схеме, если режущая дуга внезапно погаснет, например, если сопло попало в отверстие в металле, то реле геркона снова подключит поджиг и спустя несколько секунд (2 – 3) загорится дежурная дуга, а затем режущая. Все это при условии, что кнопка «пуск» не отпускается. Реле (р4) пускает воздух в сопло с задержкой, после того, как отпустили кнопку «пуск» и режущая дуга погасла. Все эти предосторожности необходимы для того, чтобы продлить ресурс сопла и электрода.
Самостоятельное изготовление плазмореза в «домашних» условиях дает возможность изрядно сэкономить, но о качестве реза говорить не приходится. Хотя если за работу возьмется инженер, то результат может быть даже лучше заводского исполнения.
ЧПУ плазморез своими руками
Станок плазменной резки с ЧПУ может позволить себе не каждое предприятие, ведь его стоимость может достигать 15000 – 20000 у.е. Довольно часто такие организации заказывают выполнение работ плазменной резки на специальных предприятиях, но это тоже обходится недешево, особенно если объемы работ большие. Но ведь так хочется свой новый станок плазменной резки, а средств не хватает.
Помимо известных профильных заводов есть предприятия, которые занимаются производством станков плазменной резки, закупая лишь профильные детали и узлы, а все остальное изготавливают самостоятельно. В качестве примера мы расскажем, как делают станки плазменной резки с ЧПУ инженеры в производственном цеху.
Составляющие станка плазменной резки своими руками:
- Стол 1270х2540 мм;
- Ременная передача;
- Шаговые детали;
- Линейные направляющие HIWIN;
- Система, управляющая высотой факела THC;
- Блок управления;
- Стойка-терминал, в котором находится блок управления ЧПУ, стоит отдельно.
Характеристики станка:
- Скорость перемещения по столу 15 м/мин;
- Точность установки позиции плазмотрона 0,125 мм;
- Если использовать аппарат Powermax 65, то скорость реза будет 40 м/мин для 6 мм заготовки или 5 м/мин для заготовки толщиной 19 мм.
На подобный станок плазменной резки металла цена будет около 13000 у.е., не включая источник плазмы, который придется приобрести отдельно – 900 у.е.
Для изготовления такого станка комплектующие заказываются отдельно, а затем все собирается самостоятельно по такой схеме:
- Готовится основание для сварки стола, оно должно быть строго горизонтальным, это очень важно, лучше проверить уровнем.
- Сваривается рама станка в виде стола. Можно использовать трубы квадратного сечения. Вертикальные «ноги» необходимо усилить укосинами.
- Рама покрывается грунтовкой и краской, чтобы защитить от коррозии.
- Изготавливаются опоры для станка. Материал опор – дюраль, болты 14 мм, гайки лучше приварить к болтам.
- Сваривается водяной стол.
- Устанавливаются крепления для реек и ставятся рейки. Для реек используется металл в виде полосы 40 мм.
- Устанавливаются линейные направляющие.
- Корпус стола зашивается листовым железом и окрашивается.
- Устанавливается портал на направляющие.
- На портал устанавливается двигатель и концевые индуктивные датчики.
- Устанавливаются рельсовые направляющие, зубчастая рейка и двигатель оси Y.
- Устанавливаются направляющие и двигатель на оси Z.
- Устанавливается датчик поверхности металла.
- Устанавливается кран для слива воды из стола, ограничители для портала, чтобы не съехал со стола.
- Устанавливаются кабель-каналы Y,Z и X.
- Все провода прячутся в гофру.
- Устанавливается механизированная горелка.
- Далее изготавливается терминал с ЧПУ. Сначала сваривается корпус.
- В корпус терминала с ЧПУ устанавливается монитор, клавиатура, модуль ТНС и кнопки к нему.
Все, станок плазменной резки с ЧПУ готов.
Несмотря на то, что плазморез имеет достаточно простое устройство, все же не стоит браться за его изготовление без серьезных познаний в сварочном деле и большого опыта. Новичку проще заплатить за готовое изделие. А вот инженеры, желающие воплотить свои знания и умения в домашних условиях, что называется «на коленке», могут попробовать создать плазморез своими руками от начала и до конца.
принцип работы и особенности технологии, устройство ручного резака
На чтение 13 мин Просмотров 12.4к. Опубликовано Обновлено
Плазменная резка – новая великолепная технология, позволяющая разрезать металлы солидной толщины и любой природы, даже самой капризной. В качестве режущего предмета выступает не нож, а плотная струя плазмы, которая позволяет формировать идеально точный рисунок реза в единицу заданного времени.
Этот способ работы с содержит множество достоинств, которые мы разберем ниже. А сейчас начнем с физики – нужно разобраться с сутью процесса.
Физика плазмы
Технология плазменной резки металла отдает главную женскую роль нашей любимой электрической дуге. Он формируется между электродом и соплом. Иногда вместо электрода выступает металл, который нужно разрезать. Разберемся, что такое плазменная резка.
Начало процесса – включение источника электрического питания и подача тока высокой частоты в . Источник питания включается автоматически после нажатия тумблера розжига в аппарате.
Сначала формируется так называемая промежуточная дуга – она имеет временный характер и соединяет электрод с наконечником сопла резака. Нагревается эта дежурная дуга до уровня температуры около 8000°С.
Это важный момент общего процесса плазменной резки – нужно помнить, что настоящая дуга между электродом и металлом образуется не сразу, а через ее промежуточный вариант.
Следующий этап процесса – поступление воздуха из компрессора, который обычно прилагается к аппарату резки металла. Компрессор подает воздух в сжатом виде. Этот воздух поступает в камеру плазмотрона, в котором находится и уже раскалена временная электрическая дуга.
Дуга нагревает сжатый воздух, объем которого при нагреве увеличивается во много раз. Дополнительно к нагреву и увеличению объема воздух начинает ионизироваться и трансформироваться в настоящий проводник электрического тока. Он превращается в ту самую плазму
Малый диаметр сопла дает возможность разгонять поток этой раскаленной плазмы до огромных скоростей, с которыми струя вылетает из аппарата. Скорость потока может достигать трех метров в секунду.
Схема работы плазменной резки.Температура воздуха – запредельная, вплоть до 30 000°С. При этих условиях электрическая проводимость воздуха – плазмы практически равна проводимости разрезаемого металла.
Настоящая конечная дуга появляется мгновенно, как только поток плазмы достигает и касается поверхности металла. Временная дуга, в свою очередь, автоматически выключается. Металл начинает плавится точно в месте среза.
Жидкие металлические капли сразу же сдуваются струей сжатого воздуха. Это и есть принцип плазменной резки. Как видите, все просто, логично и понятно.
Классификация видов плазменной резки
Виды плазменной резки будут зависеть от среды, в которой проводятся работы по металлу:
Простой
Главное отличие способа – ограниченность электрической дуги. Для резки используется электрический ток и воздух. Иногда вместо воздуха применяются газ в виде азота. Если металлически лист тонкий – всего несколько миллиметров, процесс можно сравнить с лазерным разрезанием.
При этом способе толщина металлов не должна превышать 10-ти мм. Способ отлично работает для низколегированных сплавов стали и других мягких металлов. Режущим элементом выступает кислород, из которого формируется сжатая струя, превращающаяся в итоге в плазму.
В разрезах получаются очень ровные кромки, не требующие дальнейшей доработки.
С применением защитного газа
При этом способе вместо воздуха используются защитные газы, которые превращаются в плазменный поток после преобразования в плазмотроне. Качество срезов в данном случае значительно повышается благодаря отличной защите процесса от воздействия окружающей среды.
Газ для плазменной резки не представляет из себя ничего необычного: это может быть водород или аргон – «газовая классика».
С водой вместо воздуха
Отличны способ со многими преимуществами, одно из которых – отсутствие необходимости в дорогостоящей и громоздкой системе охлаждения.
Существуют и другие критерии классификации плазменной резки. К примеру, виды резки бывают разделительными и поверхностными. Первый из них используется чаще.
Еще один параметр – способ резки. Один вид – резка дугой, в котором разрезаемый металл выступает в качестве элемента электрической цепи. Другой вид – резка струей, когда электрическая дуга соединяет электроды, а не металлическую заготовку.
Плазменные резаки представлены на рынке в самых разнообразных вариантах, так что их можно классифицировать по маркам, производителям и многим другим техническим и торговым параметрам.
Есть, например, ручная плазменная резка – самый демократичный способ и по цене, и по простоте исполнения. Есть машинные автоматические технологии, устройства для которых намного дороже и сложнее.
Преимущества резки плазмой
Принцип работы плазменной резки.Самой близкой технологией является лазерная резка металлов, поэтому логично будет перечислить преимущества в сравнении с «соседкой»:
- Плазменной резке по плечу металлы любой природы, в том числе цветные, тугоплавкие и другие, сложные для обработки.
- Скорость процесса значительно выше, чем резка газовым резаком.
- Одна из значительных особенностей – возможность производить резы любой формы, включающие и геометрические узоры, и фигурную резку самой высокой сложности. Иными словами, резка с помощью плазмы – это реализация самых смелых творческих идей по металлу и другим трудно поддающимся материалам.
- нипочем любая толщина металла: скорость и качество никоим образом не теряются.
- Этому способу поддаются не только металлы, но и другие материалы: он вполне универсальный.
- Резка плазмой и быстрее, и эффективнее по качеству кромки, чем любые другие механические способы резки.
- В данном методе возможна работа не только перпендикулярно к поверхности металла, но под углом, что помогает освоить широкие листы металла.
- С экологической точки зрения это вполне благополучный вид работы с металлом с минимальным выбросом вредных веществ или загрязнений в воздух.
- Отличная экономия времени из-за отсутствия необходимости предварительно нагревать металл.
- Поскольку в методе не используются взрывоопасные газовые баллоны, он значительно безопаснее, чем другие способы.
Недостатки плазморезки
Ни один способ обработки металлов не обходится без недостатков, и плазменная резка здесь не исключение.
Недостатки плазменной резки следующие:
- Дороговизна всего модельного ряда аппаратов для плазменной резки, включая даже самые простые ручные варианты.
- Пределы толщины металла для резки плазмой: предельная толщина всего 100 миллиметров.
- Это шумный способ работы, потому что сжатый воздух или газ подаются с огромной скоростью.
- Оборудование непростое, дорогое и требующее грамотного и постоянного технического обслуживания.
Советы и нюансы
Еще одной отличительной положительно характеристикой метода является то, что во время процесса происходит нагрев лишь небольшого локального участка. Да и остывает этот участок намного быстрее, чем при лазерной или механической резке.
Охлаждение необходимо только для двух составных элементов – катода и сопла, как самых нагруженных. Это без проблем производится с помощью рабочей жидкости.
Плазменная дуга и струя. начинает работать стабильно в результате рабочего соотношения катода и сопла с паром из сжатого раскаленного воздуха. На катоде локализуется отрицательный заряд, на наконечнике сопла – соответственно положительный. В результате этого образуется промежуточная дуга.Лишняя влага впитывается специальным материалом, который находится в резервуаре камеры плазмотрона.
Правила безопасности при данном методе имеют строжайший характер, потому что все аппараты плазменной резки могут быть очень травматичными для мастера. Особенно это касается моделей с ручным управлением.
Все будет в порядке, если вы будете соблюдать рекомендации по защитной амуниции мастера: щиток, затемнённые очки, защитные ботинки и т.д. В этом случае вы сможете уберечься от главных факторов риска данного метода – капель расплавленного металла, высокого напряжения и раскаленного воздуха.
Еще один совет по безопасности – ни в коем случае не стучать резаком по металлу для удаления металлических брызг, как это делают некоторые мастера. Вы рискуете повредить аппарат, но главное – поймать кусочки расплавленного металла, например, лицом или другой незащищенной частью тела. Лучше поберечь себя.
Экономия расходных материалов занимает не последнее место в эффективной резке. Для этого зажигаем электрическую дугу не слишком часто, а точно и в срок, чтобы не обрывать ее без надобности.
Экономия ресурсов также распространяется на силу и мощность тока. Если рассчитать его правильно, вы получите не только экономию, но и отличный срез без заусениц, окалины и деформации металла.
Для этого следует работать по следующей схеме: сначала подать ток высокой мощности, сделать пару – тройку разрезов с его помощью. Если сила и мощность тока великоваты, на металле сразу же будет образовываться окалина из-за значительного перегрева.
После осмотра срезов будет ясно, оставить ток на этом уровне или изменить его. Иными словами, работаем экспериментально – малыми пробами.
Как работать плазморезкой?
Электрическая схема плазменного генератора.Резка металлов с помощью плазменного потока – слишком серьезное дело, чтобы заниматься им без предварительного изучения и тщательной подготовки. Это поможет вам сделать резку эффективнее со всех точек зрения, и, что весьма немаловажно, минимизировать риски, связанные с производственными опасностями.
Прежде всего нужно знать принцип работы плазменной резки – видеть картинку физических явлений целиком.
Плазменную горелку следует держать очень близко к поверхности и краю металла, в отличие от лазерной резки. Когда тумблер с «пуском» включится, первой загорится временная электрическая дуга, и только затем – настоящая, которая будет главным режущим элементом. с режущей дугой нужно вести по материалу ровно и медленно.
Скорость резки следует строго контролировать. Это можно делать, наблюдая за искрами с обратной стороны листа разрезаемого металла. Если этих искр нет, то это значит, что разрезка металла произошла неполная.
Такое может произойти по нескольким причинам: из-за слишком большой скорости ведения горелки или прохождения аппарата, либо слишком недостаточной мощности подаваемого тока, либо несоблюдения прямого угла в 90° между горелкой и поверхностью металла.
Дело в том, что полная проплавка металла происходит лишь при наклоне плазморезки к поверхности металла под прямым углом и ни градусом больше или меньше.
После завершения работы резак нужно наклонить. Воздух будет выходить и после выключения аппарата – непродолжительное время.
Перед работой невредно изучить схему вашего аппарата: именно в ней можно прочитать самую достоверную информацию по допускаемой толщине металла, который можно прорезать или сделать в нем отверстие. Устройство плазменного резака может различаться, все зависит от функций его назначения.
Выбор аппарата для плазменной резки
Покупка любого технического оборудования – дело, для которого не нужно жалеть времени и усилий: слишком высок риск неудачного решения и потери денег. А деньги здесь немалые, вы не найдете плазменного резака дешевле 500 USD в принципе.
Сначала разбираемся с параметрами и техническими характеристиками прибора.
Выбор нужно делать только под свои планы и нужды. Задача – найти не самый лучший резак, а самый подходящий для вас по принципу «здесь и сейчас».
Две большие группы плазморезов – это инверторные и трансформаторные. Названия говорят сами за себя.
Открытая и закрытая плазменная струя.Если вам нужен компактный для работы с металлами небольшой толщины, вы можете остановить свой выбор на резаке инверторного типа. Они забирают немного энергии, легкие и с небольшими габаритами.
Вместе с тем работают они с перерывами и легко выходят из строя при перепадах сетевого напряжения. Цена на такие приборы вполне умеренная, из всех плазморезов это самые недорогие.
Другое дело – трансформаторные резаки. Здесь и с габаритами, и с весом «все в порядке»: серьезные аппараты по всем параметрам.
Энергии потребляют много, зато работать они могут практически без перерыва в течение целого дня. И толщина металла может быть побольше, чем при резке инверторной моделью. Стоимость таких устройств высокая – от 3000 до 20000 USD.
Выбор плазменного резака по мощности
Рассуждения начинаем со свойств и технических характеристик деталей, которые вы планируете обрабатывать и резать. Именно это этого рассчитывается мощность режущего прибора, потому что в нем будут различаться и сопло по своему диаметру, и тип используемого газа.
Применение плазменной резки – область чрезвычайно широкая, поэтому говорить нужно только о ваших конкретных нуждах.
К примеру, если толщина металлических заготовок около 30-ти мм, вам будет вполне достаточно резака с мощностью 90А. Он легко справится с вашим материалом.
А вот если ваш металл потолще, ищите подходящую модель в диапазоне мощности от 90 до 170А.
Выбор резака по времени и скорости разрезания материала
Скорость плазменной резки металла измеряют в сантиметрах за одну минуту. Эта скорость у разных аппаратов тоже разная и зависит от их общей мощности и природы разрезаемого металла.
Например, при всех прочих равных медленнее всего режется сталь, чуть быстрее – медь и ее сплавы. И еще быстрее – алюминий со своими алюминиевыми сплавами.
Устройство плазменного резака.Если для вас важна скорость, не забывайте о таком показателе, как длительность работы без перегрева, то есть без перерыва. Если в технической спецификации к аппарату написано, что длительность работы 70%, это означает, что после семи минут резки аппарат должен быть выключенным в течение трех минут, чтобы остыть.
Среди трансформаторных резаков встречаются чемпионы с продолжительностью работы в 100%. Иными словами, они могут работать целый день без отключения. Стоят они, конечно, немало. Но если у вас впереди длинные разрезы, думайте о покупке «чемпионских» трансформаторных плазменных резаков.
Пара слов о горелке
Снова оцениваем природу металла или другого материала, который планируем разрезать. От этого будет зависеть мощность горелка плазмореза. Она должна быть достаточной для качественного реза.
При расчетах нужно учитывать факт, что вы можете встретиться со сложными условиями работы, которая, как назло, должны быть произведена в самые короткие сроки, то есть резка должна носить выраженных интенсивный характер.
Во многих источниках рекомендуется выбирать сопло из меди: оно прочное и отлично охлаждается воздухом, намного быстрее, чем сопла из других металлов.
Рукоятку горелку не упускаем из зоны внимания, это важная часть для комфортной, а значит качественной работы. На рукоятке можно зафиксировать дополнительные элементы, которые помогут держать сопло на одинаковом расстоянии от поверхности металла. Данный совет распространяется только на ручные модели аппаратов.
Если вы собираетесь резать , выбирайте модель с горелкой, которая предназначена для поступления воздуха.
Если же ваши планы связаны с массивными толстыми заготовками, покупайте резак с горелкой для приема защитного газа – азота, например.
особенности, принцип работы, преимущества и недостатки
Плазменную резку очень часто используют в таких отраслях промышленности, как судостроение, машиностроение, а также при изготовлении металлоконструкций, коммунальной сфере и т. п. Кроме этого, плазморез довольно часто используется в частной мастерской. С его помощью быстро и качественно разрезают любой материал, проводящий ток, и некоторые нетокопроводящие материалы – дерево, камень и пластик.Технология плазменной резки позволяет разрезать листовой металл и трубы, выполнять фигурный рез или изготавливать детали. Работа осуществляется при помощи высокотемпературной плазменной дуги. Чтобы ее создать, потребуется только источник тока, воздух и резак. Чтобы работа выполнялась довольно легко, а рез получался ровным и красивым, следует выяснить, как осуществляется принцип работы плазменной резки.
Как устроен плазморез
Этот аппарат состоит из следующих элементов:- источник питания;
- воздушный компрессор;
- плазменный резак или плазмотрон;
- кабель-шланговый пакет.
Источник питания для аппарата плазменной резки осуществляет подачу на плазмотрон определенной силы тока. Представляет собой инвертор или трансформатор.
Инверторы довольно легкие, в плане энергопотребления экономные, по цене недорогие, однако, способны разрезать заготовки небольшой толщины. Из-за этого их применяют только в частных мастерских и на маленьких производствах. У инверторных плазморезов КПД на 30% больше, чем у трансформаторных и у них лучше горит дуга. Часто используют их для работ в труднодоступных местах.
Трансформаторы гораздо увесистее, тратят много энергии, но при этом имеют меньшую чувствительность к перепадам напряжения, и с их помощью разрезают заготовки большой толщины.
Плазменный резак считается главным элементом плазмореза. Его основными элементами являются:
- сопло;
- охладитель/изолятор;
- канал, необходимый для подачи сжатого воздуха;
- электрод.
Компрессор требуется для подачи воздуха. Принцип работы плазменной резки предусматривает применение защитных и плазмообразующих газов. Для аппаратов, которые рассчитаны на силу тока до 200 А, применяется только сжатый воздух как для охлаждения, так и для создания плазмы. Они способны разрезать заготовки толщиной в 50 мм.
Кабель-шланговый пакет используется для соединения компрессора, источника питания и плазмотрона. По электрическому кабелю от инвертора или трансформатора начинает поступать ток для возбуждения электрической дуги, а по шлангу осуществляется подача сжатого воздуха, который требуется для возникновения внутри плазмотрона плазмы.
Принцип работы
При нажатии на кнопку розжига начинается подача тока высокой частоты от источника питания (инвертора или трансформатора). В результате этого внутри плазмотрона образуется дежурная электрическая дуга, температура которой достигает 8 тыс. градусов. Столб этой дуги начинает заполнять весь канал.После того как возникла дежурная дуга, в камеру начинает поступать сжатый воздух. Вырываясь из патрубка, он проходит через электрическую дугу, нагревается, при этом увеличиваясь в объеме в 50 или 100 раз. Кроме того, воздух начинает ионизироваться и перестает быть диэлектриком, приобретая свойства проводить ток.
Сопло плазмотрона, суженное книзу, обжимает воздух, создавая из него поток, которое начинает вырываться оттуда со скоростью 2 – 3 м/с. В этом момент температура воздуха часто достигает 30 тыс. градусов. Именно такой раскаленный ионизированный воздух и является плазмой.
В то время, когда плазма начинает вырываться из сопла, происходит ее соприкосновение с поверхностью обрабатываемого металла, дежурная дуга в этот момент гаснет, а зажигается режущая. Она начинает разогревать заготовку в месте реза. Металл в результате этого плавится и появляется рез. На поверхности разрезаемого металла образуются небольшие частички расплавленного металла, сдуваемые с нее потоком воздуха. Таким образом осуществляется работа плазмотрона.
Преимущества плазменной резки
Работы по резке металла часто осуществляются на стройплощадке, в мастерской или цеху. Можно использовать для этого автоген, но не всех это устраивает. Если объем работ, связанный с резкой металла, слишком большой, а требования, предъявляемые к качеству реза, очень высоки, то следует подумать о том, чтобы использовать плазменный резак, имеющим следующие достоинства:
- Если мощность подобрана правильно, то аппарат плазменной резки позволяет в 10 раз повысить производительность. Такой параметр позволяет плазморезу уступить только промышленной лазерной установке, однако, он значительно выигрывает в себестоимости. Целесообразно с экономической точки зрения применять пламенную резку для металла, имеющего толщину до 50 – 60 мм.
- Универсальность. С помощью плазменной резки обрабатываются чугун, медь, сталь, алюминий и прочий металл. Необходимо просто выбрать оптимальную мощность и выставить конкретное давление воздуха.
- Высокое качество реза. Аппараты плазменной резки способны обеспечить минимальную ширину реза и кромки без перекаливания, наплывов и грата практически без дополнительной обработки. Кроме того, достаточно важен такой момент, что зона нагрева материала в несколько раз меньше, чем при использовании автогена. А так как термическое воздействие минимально на участке реза, то и деформация от этого вырезанных деталей будет незначительной, даже если они имеют небольшую толщину.
- Не происходит существенного загрязнения окружающей среды. С экономической точки зрения, если имеются большие объемы работ, то плазменная резка гораздо выгоднее кислородной или механической. Во всех остальных случаях учитывают не материалы, а трудоемкость использования.
Недостатки плазменной резки
Недостатки в работе плазменной резки тоже имеются. Первый из них – максимально допустимая толщина реза довольно небольшая, и у самых мощных агрегатов она редко бывает больше 80 – 100 мм.
Следующий недостаток – достаточно жесткие требования, предъявляемые к отклонению от перпендикулярности реза. Угол отклонения не должен быть больше 10 – 50 градусов и зависит это от толщины детали. Если случается выход за эти пределы, то возникает довольно существенное расширение реза, что в результате влечет за собой быстрый износ расходных материалов.Кроме того, рабочее оборудование довольно сложное, что делает совершенно невозможным использование двух резаков одновременно, которые подключаются к одному аппарату.
Заключение
Принцип работы плазменной резки довольно прост. Кроме того, аппарат, который используется для этого, имеет большое количество преимуществ, в несколько раз превосходящие имеющиеся недостатки. Если его правильно эксплуатировать, то можно существенно сэкономить время и получить качественный результат.
Оцените статью: Поделитесь с друзьями!Преимущества и недостатки плазменной резки
Преимущества и недостатки плазменной резки по сравнению с другими методами резки металлов?
Резка металлов – проблема, с которой приходится сталкиваться и в цеху, и на стройплощадке, и в мастерской. Простые решения вроде автогена устроят многих, но не всех. Если объем работ по резке металла большой, а требования к качеству реза высоки, то стоит подумать об использовании аппарата плазменной резки (плазмореза).
Первые установки и аппараты плазменной резки появились более полувека назад, но широкому кругу мастеров они стали доступны только в последние два десятилетия.
ПРЕИМУЩЕСТВА:
Какие преимущества в работе дает аппарат или станок плазменной резки металла в работе?
1. При правильном подборе мощности он позволит в 4-10 раз (по сравнению кислородной горелкой) повысить производительность. По этому параметру плазморез уступит лишь промышленной лазерной установке, зато намного выиграет в себестоимости. Экономически целесообразно использовать плазменную резку на толщинах металла до 50-60мм. Кислородная же резка более предпочтительна при раскрое стальных листов толщиной свыше 50 мм.
2. УНИВЕРСАЛЬНОСТЬ. Плазменная резка позволяет обрабатывать и сталь, и чугун, и алюминий, и медь, и титан, и любой другой металл, причем работы выполняются с использованием одного и того же оборудования: достаточно выбрать оптимальный режим по мощности и выставить необходимое давление воздуха. Важно отметить и то, что качество подготовки поверхности материала особого значения не имеет: ржавчина, краска или грязь помехой не станут.
3. ТОЧНОСТЬ и ВЫСОКОЕ КАЧЕСТВО РЕЗА. Современные плазморезы обеспечивают минимальную ширину реза и “чистые” без наплывов, перекаливания и грата кромки, почти не требующие дополнительной обработки. Немаловажно и то, что зона нагрева обрабатываемого материала намного меньше, чем при использовании автогена, а поскольку термическое воздействие на участке реза минимально, то и тепловые деформации вырезанных деталей незначительны, даже если они небольшой толщины.
4. БЕЗОПАСНОСТЬ, обусловленная отсутствием взрывоопасных газовых баллонов.
5. НИЗКИЙ уровень загрязнения окружающей среды. Касательно экономической стороны вопроса, то совершенно очевидно, что при больших объемах работ плазменная резка выгоднее той же кислородной или, например, механической. В остальных же случаях нужно учитывать не материалы, а трудоемкость использования. Например, сделать фигурный рез в толстом листе недолго и автогеном, но может потребоваться продолжительная шлифовка краев.
НЕДОСТАТКИ:
Ну а теперь поговорим о недостатках. Первый из них – относительно скромная максимально допустимая толщина реза, которая даже у мощных аппаратов редко превышает 80-100 мм. В случае же с кислородной резкой максимально допустимая толщина реза для стали и чугуна может достигать 500 мм.
Следующий недостаток метода – довольно жесткие требования к отклонению от перпендикулярности реза. В зависимости от толщины детали угол отклонения не должен превышать 10-50°. При выходе за эти пределы наблюдается значительное расширение реза и, как одно из следствий, быстрый износ расходных материалов.
Наконец, сложность рабочего оборудования делает практически невозможным одновременное использование двух резаков, подключенных к одному аппарату, что с успехом применяется при резке штучным электродом.
Процесс плазменной резки (принцип работы плазмореза)
Для начала определим, что же есть плазма. В данном случае это нагретый электрической дугой до высокой температуры (порядка 25000 °C) воздух в ионизированном состоянии. Последнее означает, что он утрачивает свойства диэлектрика и приобретает способность проводить электрический ток. В процессе резки плазменный поток становится проводником для тока, расплавляющего металл, и сам же его выдувает.
Для начала определим, что же есть плазма. В данном случае это нагретый электрической дугой до высокой температуры (порядка 25000 °C) воздух в ионизированном состоянии. Последнее означает, что он утрачивает свойства диэлектрика и приобретает способность проводить электрический ток. В процессе резки плазменный поток становится проводником для тока, расплавляющего металл, и сам же его выдувает.
Рабочий орган аппарата называется плазмотрон. Под этим словом подразумевается плазменный резак с кабель-шланговым пакетом, подключаемый к аппарату. Иногда плазмотроном ошибочно называют аппарат плазменной резки целиком. Разновидностей плазмотронов достаточно много. Но наиболее распространены и более всего пригодны для резки металлов плазмотроны постоянного тока прямой полярности. По виду дуги различают плазмотроны прямого и косвенного действия. В первом случае разрезаемое изделие включено в электрическую цепь, и дуговой разряд возникает между металлической деталью и электродом плазматрона. Именно такие плазмотроны применяются в устройствах, предназначенных для обработки металлов, включая и аппараты воздушно-плазменной резки. Плазматроны косвенного действия применяются, в основном, для обработки неэлектропроводных материалов (у них электрическая дуга возникает в самом резаке).
Сопло – важнейший элемент, определяющий возможности плазмотрона. При плазменной резке применяются сопла небольшого (до 3 мм) диаметра и большой (9-12 мм) длины. От размера диаметра сопла плазмотрона зависит количество воздуха, которое способен пропустить плазмотрон, этот параметр необходимо учитывать при подборе компрессора. Это также влияет на ширину реза и охлаждение плазмотрона. Что касается длины, то чем она больше, тем выше качество реза. Однако чрезмерное увеличение этого параметра ведет к снижению надежности работы и быстрому разрушению сопла. Считается, что длина канала должна быть больше диаметра в 1,5-1,8 раза.
Электродом (катодом) внутри плазматрона служит металлический стержень – другие конструкции в недорогих аппаратах не применяются. То же можно сказать и о материале: разновидностей изобилие, но массово используется лишь электрод из гафния.
Теперь пару слов о рабочих газах, используемых при плазменной резке. Их можно разделить на плазмообразующие и защитные (транспортирующие). Для резки в обычных плазменных системах бытового назначения (сила тока дуги – ниже 200 А, максимальная толщина реза – до 50 мм) сжатый воздух применяют и как плазмообразующий, и как защитный газ. При этом достигается удовлетворительное качество реза, хотя и наблюдается некоторое азотирование и окисление обрабатываемой поверхности. В более сложных системах применяются иные газовые смеси, содержащие кислород, азот, водород, гелий, аргон.
Выбор аппарата плазменной резки
Даже самые доступные аппараты плазменной резки сложны и довольно дороги в сравнении, например, со сварочными, поэтому к выбору недешевой техники нужно подходить осознанно. Прежде всего необходимо определиться, как обычно, с целями и задачами.
Первый параметр, без учета которого бесполезно учитывать остальные, – это максимально допустимая толщина реза. Данная величина обычно приводится для углеродистой стали, реже – для нержавеющей, еще реже – для алюминия и очень редко – для меди. Поскольку на максимально допустимую глубину реза сильно влияет теплопроводность материала, то для сплавов на основе меди этот показатель примерно на 30% ниже, чем для сплавов на основе железа. И если в технических характеристиках аппарата заявлена максимально допустимая толщина реза стали в 10 мм, это будет означать, что максимальная глубина реза медных сплавов составит 7 мм. Таким образом, вторым по важности показателем станет тип сплава, с которым предстоит работать.
Следующий фактор – планируемый режим эксплуатации плазмореза. Как и в случае со сварочными аппаратами, он определяется параметром “ПВ” (продолжительность включения), который определяет отношение времени работы аппарата ко времени, необходимому для его охлаждения. В некоторых промышленных аппаратах плазменной резки ПВ может приближаться к 100%, для ручной же резки металла вполне достаточно 40-50%.
На практике это выглядит следующим образом. Если ПВ плазмореза составляет 50%, то в течение часа эксплуатации он должен 30 минут работать и 30 минут остывать. При ручной резке приходится время от времени перемещаться или перемещать изделие и периодически выключать кнопку поджига на плазмотроне. Это время как раз и идет в зачет охлаждения, и поэтому работа кажется непрерывной. Такая формула дает сбой при работе с толстыми листами металла или при автоматической плазменной резке с ЧПУ, когда время реза может быть значительным. Дело в том, что параметр ПВ определяется для 10-минутного цикла, поэтому в начале смены, пока аппарат холодный, он будет отработать без перерыва и 15 минут даже при низком ПВ, а вот при цикличной работе может отключиться и после 5 минут непрерывной резки.
Когда ключевые параметры, определяющие принципиальную возможность использования аппарата, определены, следует уделить внимание такому аспекту, как удобство использования. Тут первостепенное значение приобретает мобильность, точнее, радиус действия, на который можно свободно удаляться от малоподвижного аппарата, “прикованного” к своему месту компрессором. Так, длина кабель-шлангового пакета плазмотрона может варьироваться до десятков метров. Кстати, важна не только длина: некоторые производители заявляют ее на уровне 30 м и более, но “забывают” сообщить о том, имеются ли евроразъемы на плазмотроне и источнике. Если таких разъемов нет, то укоротить или удлинить плазмотрон вряд ли получится, и всякий раз разматывать его для того, чтобы резать небольшие по размерам листы, будет утомительно. Главный же минус длинного плазматрона не в этом, а в том (и производители об этом, как правило, тоже умалчивают!), что при его длине свыше 20 метров наблюдается потеря мощности, причем довольно ощутимая. Поэтому разумнее всего выбирать плазмотрон небольшой (6-12 м) длины, оснащенный евроразъемом, чтобы при необходимости была возможность удлинить конструкцию, используя быстронаращиванмый удлинитель плазмотрона. Это будет, кстати, удобно и при работе на открытом воздухе в неблагоприятных условиях, когда выносить из помещения аппарат нежелательно. Однако, как уже отмечалось, использовать удлинитель нужно лишь в случае действительной необходимости.
Очень важный вопрос – проблема расходных материалов: электродов (катодов) и сопел. Важно, чтобы они были доступны и недороги. Как правило, износ этих деталей происходит или одновременно или с небольшим “разбросом” (один катод на два сопла). Одного сопла в среднем хватает на целую рабочую смену (при работе с деталями, толщиной до 10 мм).
Момент, не относящийся напрямую к плазматрону, но требующий обязательного учета, – это система подачи воздуха. Если отбросить самые маломощные модели, оборудованные встроенным компрессором и воспринимаемые многими профессионалами как малополезные игрушки, то следует помнить, что для работы плазматрону нужен мощный компрессор. И не он один: при достаточно большом расходе воздуха (100-250 л/мин при 0,4-0,6 МПа) жесткие требования предъявляются и к его качеству, а значит не обойтись без вспомогательных устройств – таких как влаго- и маслоотделители, фильтры. Поступать в аппарат воздух должен равномерно, без пульсаций, поскольку они серьезно влияют на стойкость сопел и электродов, на стабильность поджига дуги и, как следствие, на качество реза, а значит, нужен объемный ресивер.
ПРЕДЛОЖЕНИЕ ДЛЯ ЛЮБИТЕЛЯ
Среди современных устройств плазменной резки можно выделить отдельную и наиболее интересную для рядового потребителя категорию – переносные инверторные источники плазмы, применяемые при ручной резке. Их основные достоинства: низкое энергопотребление, компактность, небольшой вес, эргономичный дизайн. Недостатки: ограничение по максимальной мощности (не более 70 А), и, как следствие, по максимальной толщине реза (до 15-20 мм). Также придется мириться с невысокой продолжительностью включения и чувствительностью к перепадам напряжения. Оборудование, выходящие за рамки этого типа, как правило, рассчитано на промышленное применение.
Большинство аппаратов с плазмотронами воздушного охлаждения пригодны для резки металлических деталей толщиной до 50 мм. Для резки деталей толщиной свыше 50 мм или для увеличения производительности применяют более сложные и дорогие аппараты с плазмотронами водяного охлаждения
Максимальная глубина реза определяет толщину материала, которая может быть разрезана данным аппаратом в принципе. Скорость работы при этом в расчет не берется. Чтобы комфортно и быстро работать с деталями толщиной 3-4 мм, следует выбирать аппарат, максимально допустимая глубина реза которого – 8-10 мм.
Унифицированные разъемы для плазмотронов производятся в соответствии с европейскими стандартами и состоят из розеток (со стороны источника плазмы) и вилок (со стороны резака). Преимущество подобной системы заключается в возможности при необходимости удлинить или укоротить конструкцию без ощутимой потери мощности, прочности и электрического контакта.
Износ сопла заключается в нарушении его геометрической формы, что негативно влияет на качество реза. Износ же катода приводит к выработке стержня (допустимая глубина выработки – не более 1,5 мм), в результате чего может произойти пригорание катода к головке плазмотрона и его (плазмотрона) перегрев.
При минусовых температурах необходимо соблюдать определенные меры предосторожности. Поскольку в ресивере и шлангах образуется конденсат, который в случае замерзания может вывести из строя оборудование, то после окончания работ шланги обязательно продувают, а сам компрессор хранят в помещении с плюсовой температурой.
Плазменный резак – что это такое, устройство, принцип работы, характеристики, что можно резать?
Резка металла на производстве и дома считается сложным процессом, для которого необходимы специальные инструменты и приспособления, одним из них является плазменный резак, который помогает быстро и безопасно выполнить раскрой металлических изделий любой сложности.
Что такое плазменный резак?
Не каждая кислородная горелка справляется с резкой любых типов металла. Некоторые виды стали, например, нержавейку, можно обработать при помощи плазменного резака, это устройство, которое использует возможности плазменно-дуговой резки. Идеальный ровный срез без зазубрин и «наплывов» возможно получить при использовании плазмореза. Благодаря универсальности и отличным характеристикам станки, работающие по принципу плазменной резки, могут легко справиться с самыми капризными материалами:
- листовым металлом;
- трубами разного диаметра;
- чугуном;
- сталью.
Устройство плазменного резака
Сложное электрическое устройство, которое способно создавать плазму, необходимую для резки металла – плазморез, состоит из определенных узлов. Некоторые модели оснащаются узлом завихрения, который сжимает газовую дугу для ее стабилизации. Основные составляющие аппарата для плазменной резки:
- система подачи газа и воды;
- дуговая камера;
- изолятор;
- сопло;
- электродержатель.
Принцип работы плазменного резака
Объяснить за счет чего в аппарате для резки металла образуется плазма, способная разрезать самый прочный металл, непросто. Чтобы понять, как работает плазморез, надо разобраться в его устройстве. При попадании электрического заряда в газ образуется плазма – ионизированный поток воздуха высокой температуры, доходящей до 20000-30000°С. Для охлаждения системы подается вода или специальный газ. После попадания вспомогательного разряда между соплом плазмореза и катодом возникает факел, который режет металл, разрушает твердые камни, наносит разнообразные покрытия.
Плазменный резак – характеристики
Главные технические характеристики устройств для резки металла необходимо знать, чтобы разбираться в видах моделей и понимать, чем они отличаются. Информация о параметрах аппаратов для плазменной резки должна содержать:
- Силу тока – основной показатель, влияющий на толщину металла, с которым может работать инструмент, и на скорость работы устройства. Рассчитать необходимую величину силы тока можно самостоятельно, если умножить толщину сплава в миллиметрах на 4, например, для плазменной резки листа металла толщиной 20 мм нужен резак мощностью 80 А.
- Продолжительность включения измеряется в %, для примера можно сказать, что работа плазменного резака с характеристиками ПВ 60% должна составлять 6 мин., а следующие 4 мин. агрегат должен отдыхать. Профессиональные модели плазморезов имеют ПВ от 80%, домашние недорогие устройства – около 50%.
- Тип питания агрегата бывает различным. В продаже имеются модели станков, которым требуется двух- или трехфазная сеть, 380 В требуется профессиональным трехфазным моделям. Обычные, работающие на параметрах домашних 220 В, приборы более удобны в использовании.
Что можно резать плазморезом?
В различных сферах производства специалисты по достоинству оценили характеристики ручного плазмореза, которым можно осуществлять разные работы: быстро и качественно раскроить большой объем металлических изделий, изготовить любые сложные геометрические формы с максимальным соответствием исходным чертежам. Современная и эффективная плазменная резка способна работать не только с металлами, но и с материалами, которые не проводят электрический ток:
- камнем;
- деревом;
- пластиком.
Плюсы и минусы плазмореза
Выбирая приспособление для эффективной работы с металлом, домашним мастерам предстоит сделать нелегкий выбор и решить, чему отдать предпочтение – плазменному резаку по металлу или обычной газовой горелке. Неоспоримые преимущества, которыми обладает плазменный резак, известны:
- высокая производительность и мощность;
- качественная обработка материала;
- универсальность;
- безопасность;
- экологичность.
Недостатком плазморезов считаются:
- высокая стоимость агрегата;
- ограничение толщины материала;
- невозможность работать двумя станками одновременно.
Виды плазменных резаков
Огромный ассортимент моделей резаков представлен в профессиональных магазинах электротоваров. Отличаются ручные плазменные резаки друг от друга многими параметрами. Какой тип агрегата выбрать – переносной или стационарный, программируемый или ручной – зависит от конкретных потребностей владельца. Разделяются плазменные резаки на следующие виды:
- по типу энергопотребления – на трансформаторные и инверторные модели;
- по виду контакта – на бесконтактные и контактные;
- по типу работы – на ручные и с ЧПУ.
Газ для плазмореза
Плазмообразующие газы – отдельный ряд среди химических элементов. В аппарате плазменной резки металла применяются различные газы и их смеси, от которых зависит качество работы. Физические свойства газов – атомная масса, теплопроводность, химическая активность влияют на показатели работы плазморезов. Смешивание газов – процесс непростой, и зависит от толщины металла, типа стали и других параметров. Хорошо зарекомендовали себя в работе смеси аргона и азота с водородом. Смесь азота и кислорода применяется для многих видов металла и считается самым экономичным вариантом.
Как выбрать плазменный резак?
Оптимизация рабочего процесса на производстве и дома – важное условие качественного результата. Выбирать машину для плазменной резки следует обдуманно. Чтобы не ошибиться с покупкой, специалисты рекомендуют ответить на несколько вопросов.
- С каким металлом предстоит работать? Для медных, латунных, алюминиевых, сплавов идеально подойдет плазморез с мощностью 6 А. Для работы с черными металлами и нержавейкой хватит мощности 4А.
- В каких условиях будет работать устройство? Для продолжительной работы лучше выбирать резаки с внешней компрессорной подачей воздуха. Для небольших мастерских подойдет плазморез с внутренним компрессором.
- Как часто планируется менять расходные материалы? Следует учитывать, что электроды и сопло – детали, которые нуждаются в периодической замене, и частота их изнашивания зависит от длительности и мощности работы резака. Выбирая плазморез необходимо убедиться, что расходные материалы имеются в магазине в наличии или под заказ.
Рейтинг плазменных резаков
Простота использования, компактность, универсальность – основные параметры, за которые профессионалы любят работать с плазменными резаками. ТОП-3 лучших моделей выглядит следующим образом.
- Переносной плазменный резак «Ресанта» инверторного типа работает быстро, точно и качественно. Сила тока регулируется плавно, существует система автоподжига дуги. Работает устройство от сети 220 В, необходим источник сжатого воздуха. Удобная ручка позволяет легко переносить плазморез, вентиляционные отверстия в корпусе помогают системе не перегреться, понятные индикаторы делают управление легким.
- «Сварог CUT 100» – плазменный резак последнего поколения, который хорошо зарекомендовал себя на рынке. Способность разрезать металл толщиной до 35-ти мм, защита от перегрева, безопасность сделали данную модель востребованной среди покупателей. Сжатый воздух и трехфазная сеть 380 В необходимы для работы устройства. Недостатком называют высокую стоимость аппарата.
- «Aurora Pro airforce 100» – агрегат необходимый там, где осуществляется плазменная обработка материалов. Мобильность, высокое качество работы, встроенные транзисторы улучшенного качества, многоступенчатая защита – бесспорные плюсы устройства.
Как пользоваться плазморезом?
Плазменная резка – процесс несложный. Соблюдение простых правил необходимо для получения качественного результата. Во время работы плазморезом следует соблюдать пошаговую инструкцию:
- Перед началом работы необходимо защитить себя, надев специальную одежду и очки. Помещение должно быть оснащено вытяжкой, на лицо можно надеть маску.
- Чтобы избежать травм, до работы следует проверить все электрические шнуры на отсутствие повреждений, убедиться в соответствии тока с необходимыми параметрами резака.
- Плазморез нужно подключить к сети и источнику сжатого воздуха.
- Заготовка должна быть очищена от грязи, краски и других покрытий.
- В зависимости от толщины материала подобрать оптимальную силу тока и скорость резания.
- Резак продуть газом, через 30-40 сек. выполнить розжиг пилотной, а после нее – рабочей дуги.
- Держа сопло под углом 90° к заготовке, аккуратно провести по намеченной траектории.
- Работать необходимо, соблюдая режим ПВ – продолжительности включения.
- После работы отключить аппарат в обратной последовательности.
Плазменный резак своими руками
Если денег на качественный станок для резки металла нет, можно сделать плазморез своими руками, имея несколько необходимых составляющих, самый главный – это источник питания, обладающий необходимыми характеристиками. Для этих целей отлично подходит сварочный инверторный аппарат. Компрессор средней мощности для подачи воздуха стоит купить в магазине. Другие важные составляющие плазменного резака можно изготовить из подручных материалов:
- Для горелки нужна ручка от мощного паяльника. Через отверстие в середине будет подводиться сжатый воздух и ток.
- Кнопку пуска лучше сделать крупной.
- Электроды из гафния и набор сопл следует купить в магазине.
- Сборка плазмотрона проста: за ручкой размещается металлическая трубка, внутри нее – катод, покрытый изоляцией, следом на резьбе располагается сопло.
- К самодельному плазмотрону подключается компрессор и источник питания.
- Работать с самодельным устройством следует аккуратно, соблюдая технику безопасности и не допуская перегревания.
Принцип действия плазменного резака – «Nord West Tool»
Плазменным резаком называется компонент аппарата плазменной резки, непосредственно направляющий плазму в зону резания. Конкретное исполнение резака зависит от типа оборудования. Так, в ручных аппаратах это устройство представляет собой аналог сварочного пистолета, удобного для удержания в руке. А вот резак стационарного аппарата выполнен по-другому. Это миниатюрный моноблок, который перемещается по направляющим в соответствии с командами координатного устройства.
В любом случае, независимо от варианта исполнения конструкция плазменного резака включает функциональные элементы, в число которых входят следующие:
- корпус;
- плазмотрон;
- сопло;
- электроды.
Каждый плазменный резак оснащается присоединительной арматурой для подвода электрического кабеля и шланга системы подачи газа.
Функционирование плазменного резака
При подаче электропитания к плазморезу в плазмотроне зажигается электрическая дуга. До тех пор, пока она не инициирует розжиг плазмы, этот электродуговой разряд называется дежурным. После того, как при соприкосновении резака с разрезаемым металлом дежурная дуга устанавливается и становится рабочей, в зону резания подаётся газ, являющийся «сырьём» для получения плазмы. Это может быть как обычный воздух, так и различные смеси, например, комбинация аргона с азотом.
Под действием дуги происходит ионизация газа, и он превращается в высокотемпературную плазму. На этом этапе мощность электросиловой дуги достигает максимума, и плазма в течение нескольких секунд разогревается до 30 тысяч градусов. Это обеспечивает расчётные параметры плазмореза и даёт возможность разрезать металл любой толщины – в интервале размеров, указанных в паспорте оборудования.
Плазма фокусируется в узкий пучок, проходя сквозь небольшое отверстие в форсунке, которая иначе именуется соплом. Хотя эта деталь изготавливается из тугоплавкого материала, но всё равно изнашивается, поэтому является расходным элементом, нуждающимся в периодической замене.
Перемещение и охлаждение
В аппаратах ручной резки резак удерживается рукой человека, выполняющего данную работу. Он ведёт устройство вдоль намеченной линии и, таким образом, режет заготовку по заданной траектории. В стационарных плазморезах функцию перемещения резака над разрезаемым металлом исполняет координатный привод, который передвигает режущее приспособление по специальным направляющим. Использование приводного механизма позволяет автоматизировать стационарные плазморезы с тем, чтобы резак перемещался по заранее заложенной программе.
Важной для работы плазменного резака системой является охлаждение. Его наличие продлевает срок службы форсунок и обеспечивает безопасность процесса резания. В настоящее время наиболее часто используемыми системами охлаждения являются следующие.
- Воздушная.
- Водяная.
- Смешанная.
В первых системах в качестве охладителя используется сжатый воздух, подаваемый под большим давлением к соплу. Водяное охлаждение считается более эффективным, но слишком громоздким. В связи с этим вода в качестве охладителя используется нечасто и, в основном, только в очень мощных стационарных аппаратах. Смешанная система охлаждения предусматривает одновременное использование воздуха и воды. Этот принцип постепенно устаревает и применяется всё реже.
В заключение отметим, что резак оснащается универсальной присоединительной арматурой, чем обеспечивается взаимозаменяемость устройств. Благодаря этому вы сможете легко заменять изношенное или отказавшее устройство новым без ущерба для общей функциональности режущего оборудования.
Плазменно-дуговая резка – особенности процесса и оборудования
Процесс плазменной дуги всегда рассматривался как альтернатива кислородно-топливному процессу. В этой части серии описываются основы процесса с упором на рабочие характеристики и преимущества многих вариантов процесса.
Нажмите здесь, чтобы увидеть наши последние подкасты по технической инженерии на YouTube .Основы процессов
Процесс плазменной резки показан на Рис.1 . Основной принцип заключается в том, что дуга, возникающая между электродом и деталью, сужается с помощью медного сопла с мелким отверстием. Это увеличивает температуру и скорость плазмы, выходящей из сопла. Температура плазмы превышает 20 000 ° C, а скорость может приближаться к скорости звука. При использовании для резки поток плазменного газа увеличивается, так что глубоко проникающая плазменная струя прорезает материал, а расплавленный материал удаляется в вытекающей плазме.
Процесс отличается от кислородно-топливного процесса тем, что в плазменном процессе используется дуга для плавления металла, тогда как в кислородно-топливном процессе кислород окисляет металл, а тепло от экзотермической реакции плавит металл. Таким образом, в отличие от кислородно-топливного процесса, плазменный процесс может применяться для резки металлов, образующих тугоплавкие оксиды, таких как нержавеющая сталь, алюминий, чугун и сплавы цветных металлов.
Источник питания
Источник питания, необходимый для процесса плазменной дуги, должен иметь падающую характеристику и высокое напряжение.Хотя рабочее напряжение для поддержания плазмы обычно составляет от 50 до 60 В, напряжение холостого хода, необходимое для зажигания дуги, может достигать 400 В постоянного тока.При зажигании пилотная дуга образуется внутри корпуса горелки между электродом и соплом. Для резки дуга должна передаваться на заготовку в так называемом «переносном» режиме дуги. Электрод имеет отрицательную полярность, а деталь – положительную полярность, так что большая часть энергии дуги (примерно две трети) используется для резки.
Состав газа
В традиционной системе с вольфрамовым электродом плазма инертна и образуется с использованием аргона, аргона-H 2 или азота. Однако, как описано в Варианты процесса , можно использовать окисляющие газы, такие как воздух или кислород, но электрод должен быть медным с гафнием.Расход плазменного газа имеет решающее значение и должен быть установлен в соответствии с уровнем тока и диаметром отверстия сопла. Если поток газа слишком мал для текущего уровня или уровень тока слишком высок для диаметра отверстия сопла, дуга гаснет, образуя две последовательные дуги, электрод к соплу и сопло к заготовке.Эффект «двойной дуги» обычно катастрофичен при плавлении сопла.
Качество резки
Качество кромки плазменной резки такое же, как и при кислородно-топливной технологии. Однако, поскольку плазменная резка плавлением, характерной особенностью является более высокая степень плавления по направлению к верхней части металла, что приводит к скруглению верхней кромки, плохой прямоугольности кромки или скосу кромки реза. Поскольку эти ограничения связаны со степенью сужения дуги, доступны несколько конструкций горелок для улучшения сужения дуги и обеспечения более равномерного нагрева в верхней и нижней части реза.Варианты процесса
Варианты процесса, Рис. 2a – 2e , в основном были разработаны для улучшения качества резки и стабильности дуги, уменьшения шума и дыма или увеличения скорости резки.
Двойной газ
Процесс работает в основном так же, как и в традиционной системе, но вокруг сопла установлен вторичный газовый экран, Рис. 2a . Благоприятные эффекты вторичного газа заключаются в увеличении сужения дуги и более эффективном «удалении» окалины.Плазмообразующий газ обычно представляет собой аргон, аргон-H 2 или азот, а вторичный газ выбирается в соответствии с разрезаемым металлом.
Сталь
воздух, кислород, азот
Нержавеющая сталь
азот, аргон-H 2 , CO 2
- Алюминий
аргон-H 2 , азот / CO 2
Преимущества по сравнению с обычной плазмой:
- Сниженный риск образования двойной дуги
- Более высокая скорость резания
- Уменьшение закругления верхней кромки
Впрыск воды
В качестве плазменного газа обычно используется азот.Вода впрыскивается в плазменную дугу радиально, Рис. 2b , чтобы вызвать большую степень сжатия. Температура также значительно повышается до 30 000 ° C.
Преимущества по сравнению с обычной плазмой:
- Улучшение качества и прямоугольности пропила
- Повышенная скорость резания
- Меньше риска возникновения двойной дуги
- Уменьшение эрозии сопла
Водяной кожух
Плазма может работать либо с водяным кожухом, Рис.2c , или даже с заготовкой, погруженной на 50-75 мм ниже поверхности воды. По сравнению с обычной плазмой вода действует как барьер, обеспечивая следующие преимущества:
Удаление дыма
- Снижение уровня шума
- Увеличение срока службы сопла
В типичном примере уровней шума при высоких уровнях тока 115 дБ для обычной плазмы водяной кожух эффективно снизил уровень шума до примерно 96 дБ и резку под водой до 52–85 дБ.
Поскольку водяной кожух не увеличивает степень сжатия, прямоугольность режущей кромки и скорость резания заметно не улучшаются.
Воздушная плазма
Инертный или инертный плазмообразующий газ (аргон или азот) можно заменить воздухом, но для этого требуется специальный электрод из гафния или циркония, установленный в медном держателе, Рис. 2d . Воздух также может заменить воду для охлаждения горелки. Преимущество воздушной плазменной горелки в том, что в ней вместо дорогих газов используется воздух.
Следует отметить, что, хотя электрод и сопло являются единственными расходными материалами, электроды с гафниевым наконечником могут быть дорогими по сравнению с вольфрамовыми электродами.
Плазма высокой толерантности
В попытке улучшить качество резки и конкурировать с превосходным качеством резки лазерных систем, доступны системы высокотолерантной плазменно-дуговой резки (HTPAC), которые работают с сильно сжатой плазмой. Фокусировка плазмы осуществляется за счет закручивания генерируемой кислородом плазмы, когда она входит в отверстие для плазмы, и вторичный поток газа впрыскивается после плазменного сопла, Рис.2д . В некоторых системах дугу окружает отдельное магнитное поле. Это стабилизирует плазменную струю, поддерживая вращение, вызванное закрученным газом. Преимущества систем HTPAC:
- Качество резки находится между обычной плазменной резкой и лазерной резкой
- Ширина узкого пропила
- Меньше искажений за счет меньшей зоны термического влияния
HTPAC – это механизированная техника, требующая высокоточного высокоскоростного оборудования. Основные недостатки заключаются в том, что максимальная толщина ограничена примерно 6 мм, а скорость резки обычно ниже, чем при обычных плазменных процессах, и составляет примерно 60-80% от скорости лазерной резки.
Эта статья была подготовлена Биллом Лукасом в сотрудничестве с Дерриком Хилтоном, BOC
2021 Лучшие станки плазменной резки с ЧПУ | Доступные плазменные столы с ЧПУ на продажу
Вы с нетерпением ждете планов DIY плазменной резки или придумываете идею купить доступный комплект плазменных столов с ЧПУ для изготовления металла с размерами плазменных столов 4×4, 4×8, 5×10, 6×12 в США, Великобритании, ОАЭ, Канаде, Австралии, Россия, Южная Африка, Китай, Индия или другие страны Азии, Европы, Северной Америки, Южной Америки, Африки и Океании? Ознакомьтесь с руководством по покупке лучших станков плазменной резки с ЧПУ 2021 года для производителей металла, слесарей, станков с ЧПУ, операторов и новичков, мы предложим вам самые дешевые станки плазменной резки с ЧПУ 2021 года с индивидуальными услугами плазменной резки, чтобы они соответствовали вашим планам, проектам и проектам стола плазменной резки с ЧПУ. идеи.
Что такое плазменный резак?
Плазменный резак – это новый тип станка для термической резки металла, в котором в качестве источника тепла используется рабочий газ и плазменная дуга с высокой скоростью и высокой температурой для локального расплавления металла и выдува расплавленного металла с высокой скоростью. скорость воздушного потока при одновременном образовании узких швов плазменной резки. Этот резак используется для резки различных металлов, таких как углеродистая сталь, нержавеющая сталь, медь, алюминий, чугун и др. Он не только имеет узкие режущие швы, высокую скорость резки, небольшую зону термического влияния, плоский разрез, низкую деформацию заготовки, простоту в эксплуатации, но также имеет значительные преимущества и эффект экономии энергии.Он применяется во всех видах оборудования, производстве металлических конструкций, услугах по ремонту и установке, изготовлении листового металла, сверлении отверстий, рытье и ремонте, снятии фаски и других проектах и планах резки металла.
Что такое плазменный резак с ЧПУ?
Станок плазменной резки с ЧПУ – это тип станка для резки металла с числовым программным управлением и контроллером ЧПУ, который использует плазменный резак для резки различных металлов на различные профили и формы, включая низкоуглеродистую сталь, нержавеющую сталь, углеродистую сталь, оцинкованную сталь, горячекатаную сталь, холоднокатаную сталь. прокат стальной, чугун, латунь, медь, сплав, алюминий, бронза, титан.Комплект плазменной резки с ЧПУ состоит из рамы станка, контроллера плазменного станка с ЧПУ, источника питания плазмы, плазменной горелки, плазменного стола с лезвиями или зубьями, привода, двигателя, системы плазменной резки с ЧПУ, инструментов для портовых грузовых перевозок (портовый грузовой генератор, детали портового грузового воздушного компрессора – насос и двигатель), программное обеспечение плазменной резки с ЧПУ, направляющая, шарико-винтовая передача, дополнительные детали и расходные материалы. Плазменный резак с ЧПУ также известен как плазменный резак с ЧПУ, плазменный стол с ЧПУ, станок для плазменной резки с ЧПУ, стол для плазменной резки с ЧПУ, газорезательный станок с ЧПУ, газокислородный газовый станок с ЧПУ, плазменный плазменный станок с ЧПУ, станок кислородно-топливной резки с ЧПУ, Станок плазменной и газокислородной резки с ЧПУ.
Что такое плазменный стол с ЧПУ?
Плазменный стол с ЧПУ – это тип плазменного станка с ЧПУ с настраиваемой столешницей сварочного рабочего стола, который можно хорошо адаптировать для резки металлических проектов различных размеров. По обеим сторонам рамы рабочего стола имеются направляющие, а монтажное сиденье для резки соединено с возможностью скольжения с двумя направляющими над рамой рабочего стола. Режущее установочное гнездо соединено с режущими элементами с возможностью скольжения. Рама рабочего стола включает раковину и множественную опорную стойку, обе стороны раковины жестко снабжены фланцами, на фланцах установлена прижимная конструкция.Прижимная конструкция включает прижимную пластину, расположенную над опорной стойкой, и прижимной узел, соединенный с положением фланца. Прижимной узел включает вращающийся винтовой стержень, соединенный с фланцем, и компрессионное кольцо, соединенное с резьбой со стержнем винта, винтовой стержень проходит через прижимную пластину, и прижимная пластина расположена под компрессионным кольцом на винтовой штанге. На раме стола верстака установлен прижимной механизм. После того, как пластина помещена на раму рабочего стола, прижимное кольцо вращается, чтобы прижимная пластина сжимала пластину на раме рабочего стола, что может сплющивать пластину с плохой плоскостностью и тенденцией к перекатыванию, что экономит трудозатраты на изготовление листового металла резка удобнее и безопаснее.
Как работает плазменный резак с ЧПУ?
Плазменная резка – это метод обработки, при котором используется тепло высокотемпературной плазменной дуги для плавления металлической заготовки и удаления расплавленного металла за счет высокоскоростного импульса плазмы для создания щели. Плазменные резаки генерируют электрическую дугу, используя кислород, азот или сжатый воздух. Это превращает газ в плазму, а также быстро пробивает металл, чтобы разрезать его с помощью широкополосного доступа. Газорезательная горелка работает, добавляя в пламя струю кислорода, которая окисляет металл и превращает его в шлак.Плазменный резак движется по траектории инструмента, управляемой компьютером. Термин «ЧПУ» означает «компьютерное числовое управление», что означает, что компьютер используется для управления G-кодом, поддерживаемым движением, в программе. По сравнению с ручными станками плазменной резки, станки плазменной резки с ЧПУ обеспечивают автоматическую обработку с высокой эффективностью, высокой скоростью и качеством.
Для чего используется плазменный резак с ЧПУ?
Какие материалы может резать плазменный резак? Плазменные резаки с ЧПУ используются для резки листового металла, квадратных и круглых металлических труб, в том числе чугуна, холоднокатаной стали, горячекатаной стали, нержавеющей стали, оцинкованной стали, углеродистой стали, меди, латуни, сплавов, бронзы, алюминия, титана.Машины для плазменной резки широко используются в отраслях станкостроения, нефтехимического оборудования, легкой промышленности, сосудов высокого давления, судостроения, горнодобывающего оборудования, электроэнергетики, строительства мостов, авиакосмической промышленности, стальных конструкций и т. Д. Могут применяться плазменные резаки. любителям, домашний магазин, домашний бизнес, небольшой магазин, малый бизнес, школьное образование, промышленное производство.
Сколько типов плазменных резаков?
К наиболее распространенным типам устройств плазменной резки относятся ручные устройства плазменной резки (переносные устройства плазменной резки) и устройства плазменной резки с ЧПУ (любительские станки с ЧПУ и промышленные станки с ЧПУ).Наиболее распространенные источники питания плазменной резки включают установку плазменной резки Huayuan и установку плазменной резки Hypertherm.
По типам внешнего вида, плазменные резаки с ЧПУ можно разделить на настольные плазменные с ЧПУ, портальные плазменные с ЧПУ, портативные плазменные станки с ЧПУ.
По способам работы его можно разделить на сухую плазму, полусухую плазму и подводную плазму.
По качеству резки его можно разделить на обычную плазму, тонкую плазму, лазерную плазму и так далее.
Сколько типов плазменных столов с ЧПУ?
Наиболее распространенные типы комплектов плазменных столов с ЧПУ включают плазменные столы 4×4, плазменные столы 4×8, плазменные столы 5×10 и плазменные столы 6×12 в футах, некоторые пользователи могут называть комплекты столов для плазменной резки с ЧПУ как типы 48 x 48 дюймов, 48 дюймов Типы x 96 дюймов, типы 60 x 120 дюймов в дюймах, некоторые пользователи могут называть наборы таблиц как 1212 типов, 1325 типов, 1530 типов, 2040 типов в миллиметрах (мм).
Каковы преимущества плазменной резки?
Плазменная резка – это эффективный метод резки листового металла и металлических труб, благодаря которому он нашел широкое применение во многих отраслях промышленности. Вы можете воспользоваться 10 лучшими преимуществами: быстрая резка, простота использования, низкая стоимость, безопасность в использовании, многозадачность, расширенная универсальность, широкий диапазон материалов и толщин, устранение деформации листа, повышение скорости внутренней прошивки и уменьшение окалины.
По сравнению с традиционным полуавтоматическим и ручным методом резки, автоматический металлорежущий станок с ЧПУ значительно повысил эффективность и качество.Система резки металла с ЧПУ – это машина для плазменной, газовой, водоструйной и лазерной резки с экспоненциальным управлением. Он выполняет автоматическую постоянную высококачественную резку с высокой загрузкой и эффективностью в соответствии с программным обеспечением для раскроя с ЧПУ.
В промышленном производстве термическая резка металла обычно включает газовую резку, плазменную резку и лазерную резку. По сравнению с газовой резкой плазменная резка имеет более широкий диапазон резки и более высокую эффективность. Технология тонкой плазменной резки близка к качеству лазерной резки по качеству обрабатываемой поверхности материала, но стоимость намного ниже, чем у лазерной резки.Он показал большие преимущества в экономии материалов и повышении производительности труда. Это способствовало развитию технологии плазменной резки от ручного или полуавтоматического до числового программного управления и стало одним из основных направлений развития технологии резки с числовым программным управлением.
1. Он может резать более толстые металлы, такие как нержавеющая сталь, алюминий и его сплавы, медь и ее сплавы, чугун и другие металлические материалы. Вы также можете использовать пистолет для плазменной резки без переноса для резки непроводящих неметаллических материалов и изоляционных материалов с толщиной резки более 150 мм.
2. Высокая скорость резки и высокая эффективность производства, особенно при резке тонких металлов с высокой мощностью, эффективность производства повышается более значительно.
3. Качество резки высокое, прорезь гладкая и плоская, разрез узкий, а зона термического влияния и деформация меньше, чем при других методах резки.
4. Низкая стоимость из-за высокой скорости, использование дешевого газа, такого как азот, требует меньше сырья и труда, чем другие методы для резки того же материала.
Сколько стоит плазменный резак с ЧПУ?
В соответствии с различными требованиями и конфигурациями для источника питания плазмы, плазменной горелки, системы управления плазменным ЧПУ, стола для плазменной резки с зубьями или лезвиями, инструментов для портовых грузовых перевозок (портовый грузовой генератор, детали воздушного компрессора портовых грузовых перевозок – насос и двигатель), двигателя, водителя Программное обеспечение для плазменной резки с ЧПУ, система плазменной резки с ЧПУ, рама станка, направляющая, шариковая винтовая пара, дополнительные детали и расходные материалы, устройства плазменной резки с ЧПУ имеют доступный прайс-лист от 4280 долларов США.00–18 000 долларов США в рамках вашего бюджета. Если вы хотите купить дешевые плазменные столы с ЧПУ за границей, стоимость доставки, налогов и таможенного оформления должна быть включена в окончательную цену.
Руководство по ценообразованию
, G230Модель | Минимальная цена | Максимальная цена | Средняя цена | |
STP1212 | $ 4280,00 | 3 $ $ $00 | $ 6,560.00 | $ 5,680.00 |
STP1325R | $ 6,060.00 | $ 12,060.00 | $ 8,020.00 | |
STP1530 | $ 4,880.00 | $ 7,180.00 | $ 6,080.00 | |
STP1530R | $ 6,080.00 | $ 18,000.00 | $ 9,150.00 | |
STP3000-G | $ 6 800,00 | $ 15,600,00 | $ 10,180,00 |
Технические характеристики
, ST20218Марка | STYLECNC | STYLECNC | STYLECNC | |
Размеры стола | 4’x4 ‘, 4’x8’, 5’x10 ‘, 6’x12’ | |||
Плазменный контроллер ЧПУ | Starfire, FireControl, контроллер ЧПУ Mach4 | |||
Программное обеспечение Plasma CAM | FastCAM, SheetCAM, программное обеспечение Autodesk Fusion 360 Plasma CAM | |||
Режимы резки | Плазменная резка | Газовая резка | |||
Блок питания | Huayuan | Hypertherm | |||
Скорость резания | 0-10000 мм / мин | |||
Диапазон цен | 4280 долл. США.00 – 18000,00 долл. США |
Источник питания плазменной резки и толщина резки
Китайский источник питания Huayuan | 63A | 0–8 мм |
100A | 0–15 мм 9022 9022 9022 20 мм | |
200A | 0-30 мм | |
США Источник питания Hypertherm | 65A | 0-12 мм |
85A | 0-16 мм | |
2105A | 130A | 0-20 мм |
200A | 0-30 мм |
Как использовать плазменный резак с ЧПУ или стол для плазменной резки с ЧПУ?
1.Ручная бесконтактная резка.
а. Прикоснитесь роликом горелки к заготовке и отрегулируйте расстояние между соплом и плоскостью заготовки до 3-5 мм. (Когда машина выполняет резку, переключатель «Выбор толщины резки» находится в верхнем положении).
г. Включите резак, чтобы зажечь плазменную дугу. После прорезания заготовки двигайтесь в направлении резания с равной скоростью. Скорость резания основана на предпосылке прорезания. Слишком медленный разрез повлияет на качество разреза и даже сломает дугу.
г. После резки выключите выключатель резака, и плазменная дуга погаснет. В это время сжатый воздух распыляется с задержкой для охлаждения резака. Через несколько секунд выброс автоматически прекращается. Снимите резак, чтобы завершить весь процесс резки.
2. Ручная контактная резка.
а. Переключатель «Выбор толщины резки» находится на низком уровне и используется при резке более тонких листовых металлов на одной машине.
г.Поместите сопло резака в начальную точку разрезаемой заготовки, включите выключатель резака, зажгите плазменную дугу, прорежьте заготовку и затем равномерно перемещайте по направлению резки.
г. После резки откройте и замкните выключатель резака. В это время сжатый воздух все еще распыляется. Через несколько секунд распыление автоматически прекратится. Снимите резак, чтобы завершить весь процесс резки.
3. Автоматическая резка.
а.Автоматическая резка в основном подходит для резки толстых заготовок. Выберите положение переключателя «Выбор толщины реза».
г. После снятия ролика резака резак и полуавтоматический станок надежно соединяются, и насадка входит в комплект принадлежностей.
г. Подключите питание полуавтоматического плазменного резака и установите радиусный стержень или направляющую в соответствии с формой проекта (если вам нужно вырезать дугу или окружность, потребуется радиусный стержень).
г. Если штекер выключателя горелки выключен, замените штекер дистанционного выключателя (подготовленный в принадлежностях).
эл. Отрегулируйте подходящую скорость ходьбы в соответствии с толщиной заготовки. И установите переключатели «вверх» и «вниз» на полуавтоматическом резаке в направлении резания.
ф. Отрегулируйте расстояние между соплом и заготовкой на 3-8 мм и отрегулируйте центральное положение сопла относительно начальной полосы прорези заготовки.
г. Включите переключатель дистанционного управления.После резки заготовки включите выключатель питания полуавтомата для резки. На начальном этапе резки всегда обращайте внимание на разрезанный шов и выбирайте подходящую скорость резки. И обратите внимание, нормально ли работают две машины в любое время.
ч. После резки выключите переключатель дистанционного управления и выключатель питания полуавтоматической машины плазменной резки. На этом весь процесс резки завершен.
4.Круг ручной резки.
В зависимости от материала и толщины заготовки выберите метод одиночной или параллельной резки и выберите соответствующий метод резки. Затяните поперечину в произвольном приспособлении к отверстию для винта на держателе резака. На требуемый радиус и затяните, затем отрегулируйте расстояние от наконечника до сопла горелки в соответствии с длиной радиуса заготовки (необходимо учитывать ширину прорези). После регулировки затяните центральные крепежные винты, чтобы предотвратить ослабление, и ослабьте клетку, чтобы затянуть винты с накатанной головкой.На этом этапе можно вырезать заготовку.
Какое напряжение у плазменного резака?
Когда станок плазменной резки с ЧПУ завершает весь набор работ по резке, система плазменной резки с ЧПУ завершает контроль механической точности, и в то же время завершает контроль качества резки и пропила с помощью источника питания плазменной резки. Можно сказать, что хороший источник питания для плазменной резки обеспечивает высочайшее качество резки, а точность резки чрезвычайно важна. При фактическом использовании и эксплуатации станка плазменной резки с ЧПУ, из-за марки выбранного источника питания плазменной машины, мощности источника питания плазмы, режущего пистолета источника питания плазмы, электрода режущего сопла и других расходных материалов, толщина металлического листа и т. д.он также включает в себя различные параметры процесса плазменной резки, которые напрямую влияют на стабильность, качество резки и эффект процесса резки.
Источник питания ручного плазменного резака должен иметь достаточно высокое напряжение холостого хода, чтобы легко зажигать дугу и обеспечивать стабильное горение плазменной дуги. Напряжение холостого хода обычно составляет 120-600 В, а напряжение столба дуги обычно составляет половину напряжения холостого хода. Увеличение напряжения столба дуги может значительно увеличить мощность плазменной дуги, тем самым увеличивая скорость резки и сокращая листовые металлы большей толщины.Напряжение столба дуги обычно не может быть достигнуто путем увеличения внутреннего сжатия электрода и регулирования расхода газа, но напряжение столба дуги должно быть менее 65% напряжения холостого хода, в противном случае это приведет к нестабильность плазменной дуги.
Насколько толстым может резать плазма?
Станок для плазменной резки с ЧПУ: в зависимости от размера сконфигурированного источника питания для плазменной резки толщина резки обычно находится в пределах 0,5-100 мм, а источник питания для плазменной резки высокой мощности может резать до более 100 мм; Газорезательная машина с ЧПУ: Обычный резак 6-180 мм (максимум 250 мм), специальный резак обычно не превышает 300 мм, конечно, его также можно настроить, чтобы увеличить.
Как выбрать пылеуловитель для плазменного стола с ЧПУ?
Устройство для приема материала и удаления пыли для станка плазменной резки с ЧПУ включает в себя рабочий стол, состоящий из кронштейна и решетчатой рабочей поверхности, закрепленной на верхней части кронштейна. Кронштейн снабжен пластиной для приема материала, которая может перемещаться горизонтально относительно рабочего стола и расположена в решетке. Нижняя часть рабочей поверхности в форме решетки параллельна рабочей поверхности в форме решетки, а пластина для приема материала выполнена из стали. пластина из проволочной сетки, нижняя часть рабочего стола непосредственно под приемной пластиной для материала снабжена резервуаром для воды для удаления пыли, а нижняя часть резервуара для воды для удаления пыли снабжена колесами.Устройство приема материала и удаления пыли позволяет легко извлекать заготовки и отходы, вырезанные машиной для плазменной резки и упавшие под рабочий стол, и в то же время оно может значительно снизить загрязнение металлической пылью, образующейся при резке заготовки.
Поиск и устранение неисправностей
1. Слишком низкое рабочее давление воздуха.
Когда работает плазменный резак с ЧПУ, если рабочее давление намного ниже, чем давление, требуемое инструкциями, это означает, что скорость выброса плазменной дуги ослаблена, а входящий воздушный поток меньше требуемого значения.В это время не может образоваться высокоэнергетическая высокоскоростная дуга. В результате разрез некачественный, непроницаемый и нарост. Причины недостаточного давления воздуха: недостаточная подача воздуха от воздушного компрессора. Регулировка давления клапана регулирования воздуха на станке плазменной резки с ЧПУ слишком низкая, в соленоидном клапане есть масло, а воздушный тракт неровный. Поэтому необходимо проверять эти аспекты один за другим, вовремя находить проблемы и исправлять их.
2. Слишком высокое рабочее давление воздуха.
Если давление воздуха на входе слишком высокое, после образования дуги избыточный поток воздуха сдувает концентрированный столб дуги, рассеивает энергию столба дуги и снижает режущую способность дуги. Основные причины: неправильная регулировка входящего воздуха, чрезмерная регулировка редукционного клапана давления воздушного фильтра или отказ редукционного клапана давления воздушного фильтра.
3. Неправильная установка изнашиваемых деталей, например, сопел электродов.
Сопло электрода имеет резьбу, и его необходимо затянуть на месте. Из-за неправильной установки сопла, например, из-за того, что резьба не затягивается или вихревое кольцо установлено неправильно, резка будет нестабильной, а уязвимые части будут повреждены слишком быстро.
4. Входное напряжение переменного тока слишком низкое.
Перед вводом в эксплуатацию проверьте, имеет ли электрическая сеть, подключенная к станку плазменной резки с ЧПУ, достаточную пропускную способность и соответствуют ли спецификации кабеля питания требованиям.Место установки плазменного резака с ЧПУ должно находиться вдали от крупногабаритного электрооборудования и мест с частыми электрическими помехами.
5. Провод заземления плохо контактирует с заготовкой.
Заземление – это важная подготовка перед резкой. Если специальный заземляющий инструмент не используется, изоляция на поверхности заготовки и длительное использование заземляющего провода с серьезным старением и т. Д. Вызовут плохой контакт между заземляющим проводом и заготовкой.
6. Скорость резки и вертикальность зажима режущего пистолета.
Скорость резания должна быть быстрой или медленной в зависимости от материала и толщины реза, а также текущего размера. Слишком высокая или слишком медленная скорость приведет к неровной поверхности среза и появлению окалины на верхнем и нижнем краях. Кроме того, резак не удерживается вертикально, а распыляемая дуга также распыляется под углом, что также приводит к наклону режущей поверхности.
Контроллер плазменного ЧПУ и программное обеспечение
Наиболее распространенной комбинацией контроллера и программного обеспечения является система управления ЧПУ Starfire и программное обеспечение для раскроя FastCAM.Конечно, вы можете выбрать контроллер ЧПУ Mach4 и контроллер ЧПУ FireControl, программное обеспечение CAM для плазменной резки Sheetcam и программное обеспечение CAM для плазменной резки Autodesk Fusion 360.
Плазменный контроллер ЧПУ Starfire
Контроллер ЧПУ Starfire разработан с учетом плазменных помех, молниезащиты, высокой надежности и импульсной способности. Он имеет функции автоматической памяти точек останова. Подходит для всех типов машин плазменной и газовой резки. Дополнительный беспроводной пульт дистанционного управления можно использовать для работы на больших расстояниях.
Программное обеспечение FastCAM Plasma CAM
FastCAM – это полностью автоматическое программное обеспечение для непрерывного раскроя кромок. Программное обеспечение в основном предназначено для станков с ЧПУ, в том числе для плазменных, плазменных, лазерных и гидроабразивных станков с ЧПУ, используемых для рисования, программирования, раскроя, проверки и резки с ЧПУ деталей произвольной формы. Использование FastCAM может увеличить скорость раскроя стали и эффективно сэкономить сталь; повысить эффективность программирования, раскроя и раскроя, а также повысить эффективность раскроя продукции.Функция автоматического совмещения ребер предназначена для реализации прямоугольных и непрямоугольных деталей в процессе автоматического раскроя, то есть автоматического совмещения кромок любой детали с разной длиной стороны без ручного редактирования, а также автоматической обработки стыковых кромок. и непрерывная резка различных деталей, чтобы предотвратить и избежать термической деформации резания, автоматически обрабатывать направление резания и положение точки перфорации и использовать режущую кромку для непосредственного предварительного нагрева резания, чтобы избежать перфорации.
Устройство плазменной резки VS Устройство для плазменной сварки
Устройство плазменной резки поставляется с устройством плазменной сварки, которое представляет собой уникальный тип системы плазменной сварки. Он использует плазму для сплавления двух металлов вместе. За счет увеличения плазменного дугового разряда установка для плазменной сварки может быть преобразована в установку для плазменной резки.
На данном этапе большая часть предприятий по термической резке и сварке связана с плазменной резкой. Среди них машина для плазменной резки разработала портативную, консольную, портальную, настольную, труборезную машину и другие виды оборудования для резки, в то время как плазменная сварка делится на ручную сварочную машину и роботизированную сварочную машину.
В аппарате плазменной резки используется плазменная дуга для создания высокой температуры для плавления разрезаемого материала. В то же время он использует сжатый газ, чтобы сдувать материал, который нужно разрезать на прорези, чтобы завершить окончательные проекты резки. Он обладает такими преимуществами, как хорошее качество реза, малая ширина реза, высокая точность, быстрая резка, безопасность и чистота. Это современный резак по металлу.
Плазменный сварочный аппарат – это сварочный аппарат, в котором в качестве источника тепла используется плазменная дуга, а в качестве присадочного металла – сплав определенного состава (металлическая проволока, порошок сплава).Плазменно-дуговая сварка – это качественный метод сварки. Отношение глубины / ширины сварного шва велико, зона термического влияния узкая, деформация заготовки мала, и существует много типов свариваемых материалов, особенно развитие плазменной сварки импульсным током и плазменно-дуговой сварки расплавленным электродом. Расширяется область применения плазменно-дуговой сварки, она имеет преимущества высокой эффективности конструкции и низкой стоимости.
Демонстрационное видео– Руководство пользователя
Как использовать плазменный резак
Начало работы с плазменным резаком может быть сложной задачей.Необходимо учитывать не только технические аспекты использования машины, но и меры предосторожности.
Наше пошаговое руководство по плазменной резке поможет вам повысить эффективность, продлить срок службы оборудования и улучшить качество резки.
Плазменные резаки просты в использовании и очень удобны. Использование устройства плазменной резки может повысить производительность и снизить затраты на резку. Некоторые из преимуществ использования плазменного резака заключаются в том, что инструмент не требует какого-либо цикла предварительного нагрева, режет любой электропроводящий металл, переносится на рабочих площадках, уменьшает зону термического влияния и производит рез с небольшим пропилом.
Пошаговое использование процедуры плазменной резкиШаг 1. Убедитесь, что рабочая зона чистая
Перед настройкой плазменного резака для начала резки убедитесь, что рабочая среда чистая насколько возможно. Если вокруг устройства есть пыль или мусор от шлифовки, охлаждающий вентилятор может всосать эти частицы, что может вызвать серьезное повреждение устройства.
Убедитесь, что вы носите соответствующее защитное снаряжение для плазменной резки.
Шаг 2 – Установите стабильную рабочую поверхностьРуководство по плазменной резке Джея Лено
Рабочая поверхность должна быть безопасной. Работа с плазменным резаком может быть рискованной, если вы размещаете и работаете на нестабильной поверхности. Если вы кладете металл на поверхность, которая работает как стол, убедитесь, что он достаточно прочен, чтобы по нему можно было резать. Использование металлического зажима для фиксации детали делает процесс резки безопасным.
Шаг 3. Подключите плазменный резак
Убедитесь, что устройство выключено, и подключите его.
Шаг 4 – Подключение воздушного компрессора
Если плазменный резак не имеет встроенного воздушного компрессора, подключите внешний воздушный компрессор к устройству. Для работы плазменного резака необходим газ, например сжатый воздух.
Шаг 5 – Включите воздушный компрессор
На этом шаге включите воздушный компрессор.
Шаг 6 – Прикрепите зажим заземления
Зажим заземления является частью устройства плазменной резки и также необходим для защиты устройства плазменной резки и пользователя.Плазменная резка включает в себя электрический заряд, плавящий металл. Таким образом, установка заземляющего зажима также является проблемой безопасности. Прикрепите зажим близко к тому месту, где вам нужно разрезать.
Шаг 7 – Включите машину
Обычно вы найдете выключатель за устройством. Включите плазменный резак, переместив этот переключатель в положение ON.
Шаг 8 – Установите силу тока
Установите контроль силы тока. Вы можете попробовать разные усилители в зависимости от толщины металла, который вы режете.
Шаг 9 – Обрежьте металл
Держите конец сопла на краю основного металла. Нажмите на курок, чтобы зажечь дугу. Медленно проведите горелкой по металлу. Если у вас есть плазменные шаблоны, используйте направляющую вокруг сопла.
Шаг 10 – Выключите машину
Когда вы закончите, выключите устройство.
Шаг 11 – Отсоедините зажим заземления
Не забудьте отсоединить зажим от металла.
Шаг 12 – Выключите подачу воздуха
На этом этапе, повернув рычаг на 90 градусов, выключите подачу воздуха.
Шаг 13 – Дайте резаку остыть и намотайте все шланги
Вы только что закончили резку, дайте резаку остыть. После отпускания спускового крючка продувка длится 20-30 секунд. Намотайте все шланги и оберните резак, авиалинию и линию заземления.
Заключение
Это очень простое руководство, которое даст вам указание на то, на что следует обратить внимание, начиная с использования плазменного резака. В Интернете также есть много других руководств и справочников.
Ссылки:
https://www.millerwelds.com/resources/article-library/tech-tips-for-better-plasma-cutting
Cool Tools: Plasma Cutting Machine
Независимо от задачи инструменты необходимы нашей работе в Architect of the Capitol (AOC), и этот последний пример «крутого инструмента» AOC входит в число самых популярных и быстрых инструментов, которые мы используем.
Он генерирует температуру 35 000 градусов по Фаренгейту или выше и разгоняется почти до скорости звука. Эти экстремальные, но строго контролируемые условия позволяют инструменту прорезать металл, как горячий нож через масло.
И делайте это с точностью.
Самый крутой инструмент – это станок плазменной резки с числовым программным управлением (ЧПУ). Этот инструмент, расположенный в цехе листового металла при офисном здании, был приобретен около трех лет назад и позволяет цеху резать металлические детали, компоненты и вывески, чего раньше он никогда не мог делать эффективно, если вообще не мог.
Джордж Кэллоуэй из AOC работает на установке плазменной резки, для работы с которой требуется только один человек.
Инструмент стоит на столе размером 4 на 4 фута, наполненном водой, который помогает поглощать тепло и искры, генерируемые плазменным резаком.Режущий материал кладется на стол на решетку, приподнятую над уровнем воды; над ним вырисовывается контроллер – штанга, которая охватывает стол и удерживает и направляет плазменный резак в любом направлении.
Плазменный резак проталкивает сжатый воздух через сопло резака, нагнетая воздух до тех пор, пока он не превратится в перегретую высокоскоростную плазменную струю, рассекающую расплавленный металл. Он режет в соответствии с тем, какой дизайн был создан с помощью программного обеспечения автоматизированного проектирования (САПР), которое отправляется с ноутбука на контроллер.Плазменный резак используется для обработки токопроводящих металлов, включая сталь, алюминий и латунь, размером до 4 на 4 фута и толщиной от 1/8 дюйма до дюйма или более.
Начальник цеха листового металлаДжордж Кэллоуэй продемонстрировал, как работает плазменный резак, создав звездообразный вырез диаметром примерно 6 дюймов из листа алюминиевого лома толщиной 1/8 дюйма. Сначала Кэллоуэй прикрепил к столу алюминиевый прямоугольник размером 1 на 2 фута. Затем, используя программное обеспечение САПР на ноутбуке, он быстро сконструировал звезду, которую нужно вырезать.
Перед включением плазменного резака всех наблюдателей, не одетых в защитные очки с оттенком 3, необходимые для рабочих, которые работают на станке, просили стоять за пластиковым занавесом желтого или зеленого оттенка, чтобы защитить глаза от мощного ультрафиолета (УФ-излучения). ) свет, излучаемый плазмой. Ультрафиолетовый свет опасен для незащищенных глаз и сродни взгляду на солнце.
Это потому, что Солнце также состоит из плазмы, чрезвычайно горячего, ионизированного (заряженного) газа, который составляет четвертое состояние материи – после твердого тела, жидкости и газа.Около 99 процентов всего вещества во Вселенной – это плазма, включая звезды, поэтому вполне уместно, что символ звезды был вырезан в качестве примера того, на что способен плазменный резак. Из-за очень высоких температур плазмы это реже встречается на Земле, но в природе встречаются такие примеры, как молнии и полярные сияния (северное и южное сияние).
Искры летят, когда плазменный резак вырезает звезды из алюминиевого листа за секунды.
Когда плазменный резак начал вырезать звезду, яркие вспышки искр и света прожигали алюминий, когда резак следовал точным линиям и углам, определенным программным обеспечением.Это закончилось за секунды. Несколько мгновений спустя Кэллоуэй показал результат – влажную, но отчетливую пятиконечную звезду, требующую минимальной отделки.
Универсальность раскройного станка позволяет цеху листового металла создавать детали, начиная от основных компонентов и заканчивая сложными вывесками: стальные пластины толщиной 1/4 дюйма, используемые для крепления замков для складских помещений; Алюминиевые лицевые панели толщиной 1/8 дюйма для установки телевизионных мониторов на станциях досмотра входных дверей полиции Капитолия США; вывеска офисного здания O’Neill House; и замысловатые вывески из латуни.
«Мы недавно вырезали крышки слива для Rayburn, 7-дюймовые круглые круги с 20 полудюймовыми кругами внутри каждого, – сказал Кэллоуэй. «Мы сделали 30 таких за три часа. Если бы нам пришлось делать это вручную, на завершение всего магазина, вероятно, потребовалось бы три месяца».
Напротив, для управления машиной требуется только один человек. «Установка плазменной резки сэкономила нам значительные ресурсы, – сказал помощник суперинтенданта административного здания Райан Коломбо.
«Это« крутой инструмент », потому что он экономит много времени и делает то, что мы не могли делать раньше», – сказал Кэллоуэй.«Он каждый раз образует идеальный круг и идеальный квадрат. Вы не можете сделать это вручную. Так что это довольно круто».
Установка для плазменной резки без высокочастотной резки CUT-65DS | Станок для дуговой резки без сенсорного управления
Установка плазменной резки YesWelder CUT-65DS – это установка для резки с невысокой частотой. Он использует запуск с обратным выбросом воздуха, который включает в себя движение электрода в головке горелки назад под действием давления воздуха. Отличный выбор для домашних работ и небольших бизнес-проектов, а также для профессионалов, легкий и портативный: Размер: 16 дюймов (L) x 6.3 дюйма (Ш) x 11 дюймов (В). Вес:
17,2 фунтаСтарт без ВЧ
Пуск с обратным выбросом воздуха происходит без помех, он безопасен и идеально подходит для общего использования, безопасен для окружающей электрической машины и здоровья человека
Non-touch Pilot ARC
Горелка с пилотной дугой эффективно прорезает грубые, окрашенные и ржавые поверхности с минимальным образованием шлака. Технология Pilot arc позволяет резать, не касаясь кончика металла. Лучшее качество резки и более длительный срок службы расходных деталей.
Цифровое управление
- Машина для плазменной резки CUT-65DS использует ведущую международную технологию интеллектуального цифрового управления MCU, и все ее основные части выполняются с помощью программного обеспечения.
- Может регулировать время вспомогательной дуги, ток вспомогательной дуги, ток резки и время замедления поста.
- Не чувствителен к изменению параметров; на производительность отрезного станка не повлияет изменение параметров некоторых деталей.
Мощная резка :
- Входной ток (автоматический выключатель): 63A
- Требования к воздушному компрессору:
- Максимальный вход 33 А при 220 В, максимальный вход 35 А при 110 В
- 10-43A Выход постоянного тока, 0.3-0,4 МПа, идеальная чистая пропила 5/8 дюйма и максимальная обрезка 63/64 дюйма,
- Выход постоянного тока 10-25 А, 0,4-0,5 МПа, 5/16 дюйма, идеальный разрез и 5/8 дюйма максимальный разрез
Наш компактный плазменный резак имеет ручку для переноски и использует безопасный сжатый воздух для резки нержавеющей стали, легированной стали, мягкой стали, меди, алюминия и других цветных металлических материалов.
Двойное напряжение
Возможность двойного напряжения позволяет машине работать напрямую от сети 110 В 50/60 Гц или от 220 В 50/60 Гц с использованием адаптера питания.
Технология инвертора IGBT
- В аппарате используется инверторная технология IGBT, что значительно снижает объем и вес плазменного резака и, очевидно, повышает эффективность преобразования.
- Подходит для переключения Частота за пределами звукового диапазона, что практически исключает шумовое загрязнение.
Что внутри?
- Нет Touch Pilot Arc Cutter
- Резак 13 ’S45
- Адаптер питания 110 В-> 220 В
- Зажим заземления 10 ‘и кабель
- Газовый шланг
- Фильтр воздушного компрессора
- Датчик расхода воздуха
- Ключ установочный электрод
- Руководство пользователя
Портативный станок для плазменной резки с высоким качеством
Описание товара
Описание продукта:
DW1530 Портативный станок для газовой / плазменной резки с ЧПУ имеет небольшие размеры, основное оборудование изготовлено из твердого алюминиевого сплава с хорошим балансом, легким весом, небольшой рабочей инерцией и приятным внешним видом.Он работает как полуавтоматический станок для резки «маленький спортивный автомобиль» и может резать прямо на необработанном стальном листе. Тем не менее, ручная резальная машина может вырезать различные странные формы, выходящие за рамки полуавтоматической резки с точки зрения функциональности и эффективности. Это очень удобно и гибко, занимает меньше места и не требует больших затрат. Плазменная резка также позволяет точно резать цветные металлы.
Характеристики:
1. Используя структуру питьевой машины, можно легко перемещать и использовать небольшое пространство. Лучший выбор для небольшой фабрики.
2. Режущая головка с управлением High Touch, так что головка может подниматься и опускаться в зависимости от формы материала.
3.Этот аппарат без источника плазмы покупатель может купить Hypertherm (торговая марка США). Это поможет сэкономить деньги.
4. Обработанные материалы малого и аккуратного пропила без вторичной обработки.
5. Усовершенствованная цифровая система управления, функция хранения большой емкости, удобство чтения и обработки.
6. Совместимое ПО: Ucancam, Type 3, Artcum и др.
7. USB-порт для загрузки программы.
Установка DW1530:
Если вы собираетесь использовать DW1530 для резки металлической пластины, выполните следующие действия:
a. Закрепите гусеницу болтами рядом с металлической пластиной, которую нужно разрезать.
г. Соберите приводной блок с ЧПУ на направляющей, а затем установите поперечную балку на приводном блоке с ЧПУ. (Способ установки можно увидеть на видео)
c. Соберите THC (регулятор высоты резака). (Способ установки можно увидеть на видео)
d. Соберите резак (газовый резак или плазменный резак) на THC.
Применяемые материалы и отрасли:
Могут обрабатываться все виды металлических материалов, таких как сталь, медь, алюминий и нержавеющая сталь. Железная пластина, алюминиевая пластина, оцинкованный лист, стальная пластина белого цвета, титановые пластины, и так далее, как листовой металл.
Судостроение, строительное оборудование, транспортное оборудование, аэрокосмическая промышленность, строительство мостов, военная промышленность, ветроэнергетика, конструкционная сталь, котельные контейнеры, сельскохозяйственная техника, электрические шкафы шасси, производители лифтов, текстильное оборудование, оборудование для защиты окружающей среды и т. Д.
Наш завод:
Dwin в основном производит станки плазменной резки, лазерные гравировальные станки, станки лазерной резки, станки для лазерной маркировки, рекламные фрезерные станки с ЧПУ, фрезерные станки с ЧПУ по мрамору и деревообрабатывающие станки с ЧПУ. И мы получили сертификаты CE, FDA и SGS.
FAQ:
Q: Как насчет режущего эффекта машины?
A: В режиме газовой резки можно резать металлический лист толщиной более 20 мм; в режиме плазменной резки можно разрезать металлический лист толщиной 20 мм.
Q: Как насчет послепродажного обслуживания?
A: 1. Один год гарантии качества, машина с основными частями (за исключением расходных материалов) должна быть заменена бесплатно, если в течение гарантийного периода возникнут какие-либо проблемы.
2. Пожизненное обслуживание бесплатно.
3. Мы предоставим расходные материалы по агентской цене, когда вам потребуется их замена.
4,24 часа онлайн-обслуживания каждый день, бесплатная техническая поддержка.
5. Машина была отрегулирована перед поставкой.
6. Наши сотрудники могут быть отправлены в вашу компанию для установки или настройки при необходимости.
6 лучших бюджетных плазменных резаков до 500 долларов в 2021 году
Для изготовителя металла нет ничего важнее сварки, чем резка.
И ничто не делает резку металла проще, чем плазменный резак.
Но найти дешевый плазменный резак, который справился бы со своей работой, не так-то просто.
Ознакомьтесь с этой подборкой бюджетных аппаратов плазменной резки, которые мы собрали для вас.
Быстрое сравнение
Продукт | |||
---|---|---|---|
Изображение | Продукт | Подробности | |
Да Сварочный аппарат CUT-55DS | Мощный и доступный Гарантия 1 год Пилот без касания arca | ||
Лотос LTP5000D | Регулятор в комплекте Улучшенное охлаждение Дуга начинается без касания | ||
Иствуд Versa Cut 20 | Простота использования Экстра чистые срезы Расходные материалы обычные | ||
Форни Easy Weld 20 P | Высокое качество Готовность к генератору Сделано в США | ||
Primeweld CUT50D | 120 или 240 вход Отличное обслуживание клиентов Широкий рабочий диапазон | ||
Super Deal CUT50 | Яркий дисплей Легкий Регулируемый постпоток |
Плазменные резаки до 500 долларов с отзывами
Это лучшие бюджетные плазменные резаки, которые можно найти менее чем за 500 долларов
1.Машина плазменной резки Welder CUT-55DS
- Двойной вход 120/240 В
- Режет пластину до 1/2 дюйма
- Головка горелки AG60
- Бесконтактный запуск дуги
- Блокировка спускового крючка 2T / 4T
Плюсы
- 13-футовый разъем резака
- Поставляется с воздушным фильтром
- 20-секундная продувка воздуха
- Алюминиевая ручка, не пластиковая
- Включает запасные расходные материалы
Минусы
- Дешевый качественный воздушный шланг
- Инструкция плохо написана
Обзор
Имея выходную мощность 55 А, недорогой плазменный резак YesWelder CUT-55DS подходит для множества имеющихся на рынке устройств плазменной резки на 50 и 60 А.Эта машина может разрезать стальную пластину толщиной 1/2 дюйма. Высокочастотная вспомогательная дуга без касания означает более длительный срок службы расходных материалов, но также означает, что вы не можете использовать этот резак со столом с ЧПУ, потому что высокочастотные резаки мешают работе цифровой электроники.
Плазменный резак YesWelder CUT-55DS оснащен резаком Longevity AG60, и он достаточно хорошо справляется со своей работой. Одной из приятных особенностей этой конструкции является откидной экран, закрывающий панель управления. Некоторые пользователи сообщают о проблемах с воздушным потоком, возможно, из-за дешевого воздушного шланга.Даже на такой недорогой машине, как эта, вам нужны соответствующий воздушный поток и давление, чтобы резак продолжал работать и обеспечивать приемлемую производительность.
Одна вещь, которая немного странная в плазменном резаке YesWelder CUT-55DS, – это решение использовать основное соединение на 120 вольт с адаптером на 240 вольт, в то время как большинство машин с двумя напряжениями используют 240 основных источников питания с адаптером на 120 вольт. YesWelder предоставляет этот доступный плазменный резак годовой гарантией и 30-дневной гарантией возврата денег.
2. Плазменный резак Lotos LTP5000D
- Двойная входная мощность 120/240 В
- Гарантия 1 год
- Немецкое охлаждение PAPST
- Может резать сталь 3/8 дюйма
- Мощность резки 50 ампер
Плюсы
- Высокочастотная дуга зажигается
- Вес 26 фунтов
- 13-футовое соединение резака
- Поставляется с регулятором
- Рабочий цикл составляет 60 процентов
Минусы
- Короткий, 6-футовый зажим заземления
- Нет разъема на 120 В
Обзор
Этот аппарат плазменной резки отличается высокочастотным бесконтактным запуском вспомогательной дуги.Lotos LTP5000D выдает 50 ампер, этого достаточно, чтобы резать 5/8-дюймовую сталь. Он также рассчитан на работу от 120 или 240 вольт и весит всего 26 фунтов. Эта машина включает в себя влагоотделитель, регулятор давления и воздушный фильтр с плазменным резаком.
На Lotos LTP5000D предоставляется 1-летняя гарантия, и пользователям нравится его производительность при резке тяжелой стали. В нем используется немецкая технология охлаждения PAPST, что в значительной степени является причиной того, что он может обеспечить 60-процентную нагрузку на свои 50 ампер при работе от 240 вольт.
13-футовое соединение резака является плюсом, но пользователи жалуются на короткое 6-футовое заземление, отсутствие адаптера на 120 вольт, и многие считают, что зажим заземления имеет дешевое качество. LTP5000D поставляется со встроенным быстроразъемным соединением для воздушной линии. Есть несколько сообщений о нестабильном качестве, например, о том, что иногда провода не подключены, но Lotos действительно получает хорошие отзывы о своем обслуживании клиентов, и Lotos LTP5000D действительно предлагает большую ценность для этого ценового диапазона.
3.Плазменный резак Eastwood Versa Cut 20
- Входная мощность 110 вольт
- Горелка типа Трафимет S25K
- Выход 15 ампер
- Режет пластину до 1/8 дюйма
- Зажим заземления 10 футов
Плюсы
- Низкое давление воздуха
- 0.Наконечник 65 мм для чистых резов
- 20-футовый разъем резака
- Предназначен для листового металла
- Выполняет прецизионные пропилы
Минусы
- Не настоящий фонарь Trafimet
- Не работает со столом с ЧПУ
Обзор
Плазменный резак Eastwood Versa Cut 20 прост в использовании, он работает строго в 15 ампер с единственной регулировкой – давлением воздуха.Этот недорогой станок с острием диаметром 0,65 мм позволяет выполнять точные пропилы. Этот очень тонкий поток резки и низкое давление воздуха 30 фунтов на квадратный дюйм идеально подходят для обработки листового металла кузова автомобиля. Иствуд наиболее известен как дом по ремонту автомобилей. Прецизионный наконечник позволяет выполнять гораздо более узкие разрезы, чем большинство плазменных резаков, что означает меньше усилий по подготовке панелей к сварке.
.
Поскольку плазменный резак Eastwood Versa Cut 20 использует высокочастотную дугу, он не работает со столом с ЧПУ. Еще одна незначительная проблема заключается в том, что фонарик, указанный как фонарик типа «Трафимет», на самом деле не является подлинным Trafimet S 25.Настоящий плазменный резак Trafimet почти вдвое дороже этого доступного по цене аппарата. С другой стороны, он использует общедоступные расходные материалы и детали Trafimet.
Плазменный резак Eastwood Versa Cut 20 с 20-футовым соединением резака, возможностью выполнять точную резку методом волочения на поверхности и источником питания 120 В является выгодной сделкой с местом, где вы режете менее 1/8 -дюймовая пластина.
4.Станок для плазменной резки Forney Easy Weld 20 P
- Вход 120 вольт – подключите где угодно
- 35-процентный рабочий цикл
- Гарантия 1 год
- Выходная мощность 20 А
- Весит всего 21 фунт
Плюсы
- Промышленное строительство
- Режет сталь 1/4 дюйма
- Совместимость с генератором
- 13-футовое соединение резака
- Резак газовый
Минусы
- только 120 вольт
- Дорогой для своего уровня мощности
Обзор
Плазменный резак Forney Easy Weld 20P легкий и мощный для машины на 120 вольт.Обладая выходной мощностью 20 А, он способен резать сталь толщиной до 1/4 дюйма. При весе 21 фунт он очень портативный и довольно практичный для использования по дому, в мастерской и в качестве рабочего инструмента для профессионалов, которым необходимо работать дома у клиентов.
Модель Forney Easy Weld 20P в промышленном исполнении, 13-футовом соединении резака и зажигании дуги лобовой резки обеспечивает надежные и профессиональные функции, которые трудно найти в этом ценовом диапазоне. Форни занимается производством сварочных аппаратов уже 90 лет и знает, что нужно для того, чтобы плазменный резак продолжал работать в современных промышленных условиях.
Конечно, нет ничего идеального, и в этом случае вам может понадобиться что-то более мощное, чем эта машина, если вы занимаетесь каким-либо объемным производством. 1/4 дюйма – это предел, если вы делаете такие вещи, как изготовление зацепов, изменение рам или настройку деталей подвески. У Forney хорошее обслуживание клиентов и гарантия на этот высококачественный плазменный резак сроком на 1 год.
5.Плазменный резак Primeweld CUT50D
- Двойное входное напряжение 120/240
- Перетаскивание дуги горелки
- Режет сталь 1/2 дюйма
- 10-футовое заземление
- 12.5-футовый резак AG60
Плюсы
- Превосходное обслуживание клиентов
- Манометр находится спереди
- Воздушный фильтр в комплекте
- Стандартные расходные материалы AG60
- Гарантия 3 года
Минусы
- Не может использоваться для ЧПУ
- Не запуск без касания
Обзор
Плазменный резак PrimeWeld Cut50D имеет мощность резки 50 ампер и позволяет легко обрабатывать сталь толщиной до 1/2 дюйма.Широкий диапазон значений силы тока позволяет снизить ток до 15 А, что достаточно для резки листового металла кузова автомобиля, если вы будете осторожны. Primeweld дает на этот недорогой аппарат трехлетнюю гарантию.
Он имеет двойное входное напряжение 120/240 В и включает адаптер для подключения бытовых вилок на 120 В. Primeweld Cut50D использует зажигание дуги с торможением. Просто коснитесь поверхности, подождите секунду и перетащите, чтобы разрезать. Основным недостатком перетаскивания является то, что расходные материалы расходуются быстрее, но это дешевый элемент обслуживания, а дополнительные расходы минимальны.
Primeweld Cut50D Соединение резака имеет большую длину 12,5 футов с защитным покрытием, предотвращающим искровое повреждение, а для резака AG60 легко найти детали, что значительно упрощает поддержание надлежащих характеристик резки. Поскольку в этом станке используется высокочастотная технология, он не может работать на станке плазменной резки с ЧПУ из-за цифрового шума. Доступная по цене машина, которая сочетает в себе эти функции, такую мощность и непревзойденное обслуживание клиентов, – замечательная сделка.
6.Super Deal DC Inverter (CUT 50) Плазменный резак
- Входная мощность 120 или 240 вольт
- Гарантия 1 год
- Может резать сталь 1/2 дюйма
- 11-футовый шланг горелки
- Выход 50 А
Плюсы
- Регулировка охлаждения после потока
- Включает регулятор воздуха
- Супер яркий дисплей управления
- 60-процентный рабочий цикл
- Манометр на передней панели
Минусы
- Плохо написанная документация
- Плохое обслуживание клиентов
Обзор
Платформа Zeny Cut50 используется несколькими производителями недорогих плазменных резаков.Такая стандартизация допускает низкие диапазоны цен на этот тип оборудования, при этом каждый производитель указывает определенные дополнительные функции и оборудование, которые определяют конечный уровень цен на отдельные машины.
Этот аппарат для плазменной резки от Super Deal представляет собой продуманное сочетание функций платформы Cut50, включая зажигание дуги подъемного типа, бесшумный вентилятор и яркие светодиодные цифровые контрольные датчики. Владельцы часто отмечают высокое качество сборки. Инвертор постоянного тока Super Deal (Cut 50) оснащен двойным входным напряжением 120/240 В.
Этот аппарат оснащен регулятором подачи воздуха и имеет 11-футовый разъем для подключения резака. Он может легко резать сталь толщиной 1/2 дюйма, и пользователи часто хвалят качество резки и простоту использования. Инвертор постоянного тока Super Deal (Cut 50) имеет легкий вес 24 фунта и включает в себя воздушный регулятор.
Резак представляет собой стандартный P-31, в котором используются легко обнаруживаемые расходные детали.