Автоматизированное проектирование радиоэлектронной аппаратуры / Habr
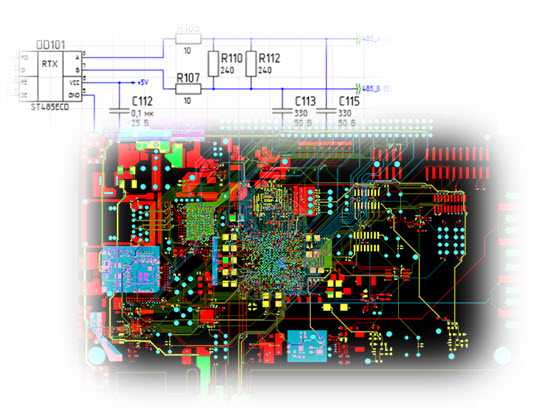
Целью публикации является ознакомление инженерно-технических работников с одним из бурно развивающихся направлений в современной индустрии информационных технологий.
Предисловие
Автоматизация проектной и расчетной деятельности в инженерной практике имеет длительную и достаточно насыщенную историю. Обращаясь к относительно недалекому прошлому достаточно вспомнить счеты, механические арифмометры и логарифмические линейки. Несколько позже в расчетную практику вошли электронные калькуляторы, которые и до настоящего времени имеют широкое применение. Все эти устройства нацелены на облегчение выполнения разнообразных расчетов, значительная доля которых приходится на проектную деятельность инженеров.
Существенным шагом в направлении автоматизации расчетной деятельности стало появление электронных вычислительных машин (ЭВМ), возможности которых позволили не только выполнять расчеты, но и управлять потоками необходимых вычислений и данных путем составления программ на специализированных языках программирования: Автокод (или Ассемблер), Алгол, Фортран и других. Программирование в корне изменило применимость наработанных в течение столетий математических методов алгебры, геометрии, численных методов, теории вероятностей, исследования операций, дискретной математики, линейного программирования и многих других. Повышение производительности ЭВМ (быстродействия и размеров оперативной памяти) с одновременным расширением спектра периферийных устройств: ввода-вывода текстовых и графических данных, накопителей для долговременного хранения информации, а также интенсивным развитием операционных систем, компиляторов языков программирования оказали существенное влияние на изменение роли ЭВМ в инженерной практике. Решение отдельных расчетных задач стало постепенно заменяться выполнением законченных этапов проектного цикла, что породило понятие системы автоматизированного проектирования в соответствии со следующим определением.
Система автоматизированного проектирования – автоматизированная система, реализующая информационную технологию выполнения функций проектирования, представляет собой организационно-техническую систему, предназначенную для автоматизации процесса проектирования, состоящую из персонала и комплекса технических, программных и других средств автоматизации его деятельности. Также для обозначения подобных систем широко используется аббревиатура
САПР.Основное назначение САПР заключается в повышении эффективности инженерной деятельности: сокращении трудоемкости и сроков проектирования, обеспечении высокого качества проектных решений и документации, минимизации натурного моделирования и испытаний опытных образцов, снижении затрат на подготовку производства.
В современной инженерной практике наибольшее распространение получили следующие виды САПР:
Содержание настоящей публикации ограничивается только вопросами, связанными с предметной областью САПР радиоэлектронной аппаратуры на печатных платах.
В 1948—1950 годах Уильям Шокли создал теорию p-n- перехода и плоскостного транзистора и первый такой транзистор был изготовлен 12 апреля 1950 года. В 1954 году Texas Instruments выпустила первый кремниевый транзистор. Планарный процесс на основе кремния стал основной технологией производства транзисторов и интегральных схем.
За сотрудничество в разработке первого в мире действующего транзистора в 1948 году Джон Бардин, Уильям Шокли и Уолтер Браттейн разделили Нобелевскую премию 1956 года. Становление и развитие технологии промышленного производства полупроводниковых приборов определило долгосрочную и стабильную тенденцию роста степени интеграции электронных компонентов, переход на полупроводниковую элементную базу существенно расширил области применения электронных устройств при драматическом увеличении их степени интеграции и, как следствие, функциональной сложности.

Расширению спектра применимости электронных устройств также содействовал и прогресс в технологии производства печатных плат, которые обладают высокими показателями надежности электрических соединений и механической прочностью, что является первоочередным требованием к мобильным и стационарным электронным изделиям. «Днем рождения» печатных плат считается 1902 год, когда изобретатель, немецкий инженер Альберт Паркер Хансен подал заявку в патентное ведомство родной страны.
Печатная плата Хансена представляла собой штамповку или вырезание изображения на бронзовой (или медной) фольге. Получившийся проводящий слой наклеивался на диэлектрик – бумагу, пропитанную парафином. Уже тогда заботясь о большей плотности размещения проводников, Хансен наклеивал фольгу с двух сторон, создавая двустороннюю печатную плату. Изобретатель также использовал идущие насквозь печатной платы соединительные отверстия. В работах Хансена есть описания создания проводников при помощи гальваники или проводящих чернил, представляющих собой измельченный в порошок металл в смеси с клеящим носителем.
Печатная плата (printed circuit board, PCB) — пластина из диэлектрика, на поверхности или в объёме которой сформированы электропроводящие цепи электронной схемы. Печатная плата предназначена для электрического и механического соединения различных электронных компонентов. Электронные компоненты на печатной плате соединяются своими выводами с элементами проводящего рисунка обычно пайкой.
Эти тенденции в развитии схемотехники и конструирования РЭА потребовали кардинальных изменений в подходах к организации процессов создания электронных изделий высокой функциональной и конструкторской сложности, что стимулировало появление промышленных систем автоматизированного проектирования радиоэлектронной аппаратуры.
На первых этапах становления САПР РЭА основными заказчиками стали предприятия — создатели сложных вычислительных комплексов, генеральные конструкторы которых стали организовывать специализированные подразделения САПР в структуре своих конструкторских бюро.
Создание САПР РЭА требовало привлечения эффективных математических методов и алгоритмов решения ключевых задач структурного и параметрического синтеза проектируемых устройств. К разработке соответствующего математического аппарата привлекались научные сотрудники ведущих ВУЗов: МГУ, ЛГУ, МФТИ, МИФИ, МЭИ, МВТУ, МИРЭА, МАИ, ЛЭТИ и многих других, а также политехнических институтов городов: Каунас, Киев, Львов, Минск. В целях интеграции ресурсов и координации деятельности по разработке САПР РЭА в Министерстве Радиопромышленности СССР выполнялись отраслевые программы РАПИРА и ПРАМ, нацеленные на создание информационно-совместимых пакетов программ автоматизированного проектирования.
Значительный вклад в теорию и практику САПР РЭА в частности внесли следующие ученые:
Абрайтис Людвикас Блажевич
Базилевич Роман Петрович
Вермишев Юрий Христофорович
Зайцева Жанна Николаевна
Маркаров Юрий Карпович
Матюхин Николай Яковлевич
Норенков Игорь Петрович
Петренко Анатолий Иванович
Рябов Геннадий Георгиевич
Рябов Леонид Павлович
Селютин Виктор Абрамович
Тетельбаум Александр Яковлевич
Широ Геннадий Эдуардович
Штейн Марк Елиозарович
и многие другие.
Структура и основные этапы проектирования РЭА
Современная электронная аппаратура реализуется на уровнях конструкторской иерархии, показанной на рисунке ниже. Для всех уровней иерархии используются соответствующие средства автоматизированного проектирования такие как САПР БИС/СБИС, печатных плат, блоков и шкафов.
Далее ограничимся вопросами автоматизированного проектирования типовых элементов замены (Уровень I). Полный цикл проектирования электронных устройств уровня I включает следующие основные этапы:
- Разработка схемы электрической принципиальной (Э3) электронного устройства.
- Цифроаналоговое моделирование схемы устройства.
- Размещение (расстановка) электронных компонентов и внешних соединительных разъемов на печатной плате. Оптимизация плана размещения компонентов с целью минимизации длин предполагаемых электрических соединений, обеспечения равномерного теплового рассеивания, создания приемлемой электромагнитной среды для передачи сигналов без искажений.
- Прокладка (трассировка) электрических соединений между эквипотенциальными выводами размещенных компонентов в соответствии с заданными правилами проектирования, регламентирующими ширину соединений, минимально допустимые зазоры с другими элементами печатного монтажа, обеспечения требований быстродействия и помехозащищенности.
- Контроль соответствия структуры печатного монтажа исходной электрической схеме и технологическим ограничениям производства.
- Выпуск конструкторской и производственной документации.
- Контроль целостности проектных данных, отслеживание внесенных изменений, обмен проектной информацией с другими автоматизированными системами.
Разработка схемы электрической принципиальной (Э3)
Схема электрическая — графическое изображение, используемое для передачи с помощью условных графических и буквенно-цифровых обозначений структуры электронного устройства. Включает условные графические обозначения (УГО) электронных компонентов и связей между их выводами.
Принципиальная схема может быть представлена на одном и более чертежных листов, при этом схема не регламентирует взаимное (физическое) расположения электронных компонентов. Всем компонентам на схеме и соединениям присваиваются уникальные идентификаторы (номер компонента по схеме, имя цепи и пр.). Для повышения читабельности схемы используются компактные графические объекты – шины и соединители.
Разработка электрических схем выполняется с использованием предварительно подготовленных и аттестованных на соответствие требованиям ГОСТ библиотек условных графических обозначений электронных компонентов.
Логическое моделирование цифровых устройств
Логическое моделирование – один из распространенных способов проверки поведенческих и функциональных свойств проектируемых цифровых устройств и нацелено на сокращение затрат, связанных с созданием и испытаниями опытных образцов. Структура цифрового устройства для моделирования описывается на одном из распространенных языков описания электронной аппаратуры – VHDL и (или) Verilog, а значения сигналов в соединениях и динамика их изменений во времени отображаются в виде графических временных диаграмм.
Современные программные средства поддерживают режимы логического моделирования асинхронных и синхронных цифровых устройств в многозначном алфавите возможных значений сигналов. Допускается моделирование и анализ совместной работы аппаратной части цифрового устройства и программного обеспечения (прошивки) в составе этого устройства, что обеспечивает целостность и полноту результатов моделирования.
Моделирование аналоговых устройств

В настоящее время широко распространены следующие виды моделирования аналоговых устройств:
- Анализ схемы по постоянному и переменному току
- Анализ переходных процессов и передаточной функции
- Анализ шумов и устойчивости
- Температурный анализ при изменении рабочей температуры
- Параметрический анализ при изменении параметров моделей электронных компонентов (транзисторы, диоды, конденсаторы, резисторы, функциональные источники и др.)
Размещение электронных компонентов
Размещение (расстановка) электронных компонентов и соединительных разъемов на печатной плате является комплексной задачей, при решении которой требуется достижение компромиссов по следующим основным критериям:
- Расстановка компонентов с соблюдением установленных правил на минимально допустимые расстояния между их корпусами и выводами.
- Минимизация суммарной длины планируемых к реализации соединений с учетом требований по быстродействию и помехозащищенности (дифференциальные пары, функционально связанные группы, цепи синхронизации).
- Обеспечение равномерного распределения плотности соединений на печатной плате.
- Учет теплового рассеивания и электромагнитного излучения электронных компонентов.
Для оценки качества размещения электронных компонентов на печатной плате используются в частности оценки, связанные с анализом плотности распределения требуемых соединений или модель “силовых векторов”, указывающих для каждого компонента направление к его наилучшему посадочному месту на плате.
Трассировка электрических соединений
Трассировка соединений является ключевым этапом конструкторского проектирования радиоэлектронной аппаратуры, решает задачу прокладки соединений на слоях печатной платы между эквипотенциальными выводами компонентов с учётом заданных правил и ограничений, основными среди которых являются ограничения на ширину проводников и минимально допустимые зазоры между элементами печатного монтажа. Показателями эффективности применяемых методов трассировки являются полнота реализации электрической схемы, минимальная суммарная длина построенных соединений, количество использованных слоев и межслойных переходов.
В настоящее время на практике достаточно широко применяются следующие три способа (режима) трассировки печатного монтажа:
- Ручная трассировка выполняется конструктором путем нанесения рисунка проводников на чертёж платы.
- Автоматическая трассировка реализуется специализированными программами, осуществляющими послойную разводку проводников. Полученные результаты доступны конструкторам для последующей ручной корректировки и доработок.
- Интерактивная трассировка является комбинацией ручного и автоматического режимов трассировки. В этом случае конструктор задает условия для трассировки всех или части требуемых соединений, а программные средства осуществляют операции трассировки в заданных условиях.
Принимая во внимание факт, что результаты автоматической трассировки являются весьма критичными при автоматизированном проектировании ниже приводятся описания (в достаточно общей форме) распространенных алгоритмов решения этой задачи.
Волновой алгоритм автоматической трассировки
Впервые описание волнового алгоритма трассировки соединений на печатных платах было опубликовано в начале 60-х годов (Lee, C.Y., «An Algorithm for Path Connections and Its Applications», IRE Transactions on Electronic Computers, vol. EC-10, number 2, pp. 364—365, 1961). Простота этого алгоритма явилась стимулом для реализации множества соответствующих программных средств.
На каждой итерации алгоритм выполняет поиск и формирование соединения заданной ширины между двумя заданными точками на плоскости с учетом существующих препятствий. Для выполнения этих функций используется так называемое дискретное рабочее поле (ДРП) – двумерная числовая матрица, ячейки которой отображают соответствующие участки печатной платы с размерами равными ширине проводника, увеличенной на величину допустимого зазора. Это гарантирует, что два проводника, размещенные в соседних ячейках будут всегда иметь требуемый зазор между их краями. Ячейки ДРП, запрещенные для прокладки соединений, помечаются специальными метками.

Поиск соединения выполняется последовательным назначением числовых меток 1-2-3… соседним (не запрещенным для прокладки соединения) ячейкам ДРП, начиная с одной из соединяемых (“И”) и до встречи второй (“П”). В том случае, когда вторая соединяемая ячейка достигнута, от нее начинается формирование найденного соединения на основе последовательного выбора пар соседних ячеек в кодовой последовательности …3-2-1-3-2-1…
Построенное соединение отображается на ДРП новым множеством запрещенных для прокладки соединений ячеек и затем описанная процедура повторяется для последующей пары точек и т.д.
Методы геометрической трассировки
Методы геометрической (shape-based) трассировки составляют следующее за волновым поколение алгоритмов трассировки печатных плат и больших интегральных схем.
Эти методы оперируют геометрическими моделями объектов печатного монтажа (контактов, проводников и т.п.), осуществляя поиск и прокладку соединений в существующем лабиринте свободных ресурсов.
Алгоритмы этого класса решают задачу прокладки каждого соединения также в два этапа: поиск возможного соединения и его прокладка.
Поиск соединения выполняется последовательным распространением прямоугольных проб (“И” – исходная проба) по непрерывным участкам доступных трассировочных ресурсов — до встречи геометрического объекта “П” (или исчерпания всех ресурсов). Каждая сформированная проба является источником для формирования трех порожденных проб по ее ребрам (eN).
Найденный путь определяется как последовательность пар порождающих и порожденных проб
(П e18 e16 e14 e12 e10 e8 e2И)
Методы топологической трассировки
Методы топологической трассировки оперируют с топологической моделью трассировочных ресурсов, сформированной в результате применения операций триангуляции (или подобных на основе выпуклых многоугольных геометрических фигур) к множеству характерных точек элементов печатного монтажа: контактов, проводников, зон запретов на трассировку, контура платы и т.п.
Поиск соединения выполняется последовательным анализом смежных треугольников топологической модели, начиная с тех, одной из вершин у которых является “И” и завершая первым встреченным треугольником, у которого одна из вершин есть “П”.
Найденный путь определяется последовательностью ребер смежных треугольников, расположенных между начальной и конечной вершинами:
(П e12 e11 e10 e9 e8 e7 e6 e5 e4 e3 e2 e1И).
Представленные описания алгоритмов трассировки носят упрощенный характер и выполнены применительно лишь к простейшим однослойным структурам. На практике программные реализации этих алгоритмов обеспечивают возможности трассировки многослойных печатных плат с использованием межслойных металлизированных переходов, соблюдением широкого спектра ограничений на ширину проводников и минимально – допустимые зазоры между всеми элементами печатного монтажа.
Широкое применение электронных устройств в приборостроении, компьютерной индустрии, аэрокосмической отрасли, бытовой технике предъявляет все более жесткие требования к качеству и электрофизическим свойствам печатного монтажа, формируемого в процессе трассировки соединений на плате.
На сегодняшний день все более критичными становятся следующие дополнительные требования к методам трассировки:
- Реализация высокой плотности соединений.
- Обеспечение высокого быстродействия и синхронизации при передаче сигналов.
- Гарантии помехозащищенности сигналов в соединениях.
Документация на проекты электронных устройств
Завершающим этапом проектирования электронных устройств является выпуск проектной документации, включающий конструкторскую документацию и данные для изготовления печатных плат.
Конструкторская документация (КД) — графические и текстовые документы, которые, определяют состав и устройство изделия, содержат необходимые данные для его изготовления, контроля, эксплуатации. Включают спецификацию, электрическую схему, сборочный чертеж платы, перечень элементов, ведомость покупных изделий, технические условия, программу и методику испытаний и другие в соответствии с требованиями ГОСТ.

Данные на изготовление печатных плат формируются программным способом и содержат информацию, необходимую для изготовления фотошаблонов и сверления.
Форматы представления этих данных унифицированы (Gerber, ODB++) и являются стандартами de facto при передаче результатов изготовителю.

Сквозной цикл автоматизированного проектирования РЭА
С позиций пользователей (то есть разработчиков электронной аппаратуры) САПР РЭА являются программным продуктом, потребительские свойства которого оцениваются по следующим основным критериям:
- Поддержка сквозного цикла проектирования РЭА средствами автоматизации.
- Функциональные возможности отдельных подсистем (моделирования, трассировки соединений и др.).
- Открытость системы для ее интеграции с другими средствами автоматизации в той же или смежных предметных областях.
- Качественная и детальная пользовательская документация.
- Техническая поддержка пользователей со стороны компаний — разработчиков программного продукта.
В этом ряду требований первостепенным, как правило, является требование возможности построения сквозного цикла проектирования – от выдачи технического задания на проект и до получения конструкторской документации и данных для изготовления изделия.

Содержание сквозного цикла определяется набором проектных этапов, последовательно выполняемых на основе единой информационной модели проекта.
Такой подход обеспечивает совместимость проектных данных и возможности итеративного проектирования изделия, то есть возобновления проектных работ с начального или одного из промежуточных этапов при изменениях проектных спецификаций.
Примером САПР РЭА отечественной разработки, обеспечивающей автоматизацию основных этапов проектирования электронных устройств, является программный продукт Delta Design компании ЭРЕМЕКС:
Во многих случаях компании – разработчики электронной аппаратуры организуют сквозные циклы проектирования на основе интеграции информационно – совместимых САПР РЭА от разных производителей, современный рынок которых достаточно разнообразен.
Завершая рассмотрение вопросов, связанных с автоматизацией проектирования электронной аппаратуры, необходимо отметить, что эта сфера деятельности в настоящее время продолжает достаточно интенсивно развиваться. В ближайшей перспективе следует ожидать появления новых методов и подходов к решению задач автоматизированного проектирования.
habr.com
Автоматизация проектирования электроники — Википедия
Материал из Википедии — свободной энциклопедии
Автоматизация проектирования электронных устройств (англ. Electronic Design Automation, EDA) — комплекс программных средств для облегчения разработки электронных устройств, создания микросхем и печатных плат.
Комплекс позволяет создать принципиальную электрическую схему проектируемого устройства с помощью графического интерфейса, создавать и модифицировать базу радиоэлектронных компонентов, проверять целостность сигналов на ней. Современные программные пакеты позволяют выполнить автоматическую расстановку элементов, и автоматически развести дорожки на чертеже многослойной печатной платы, соединяя тем самым выводы радиоэлектронных компонентов в соответствии с принципиальной схемой. Введённая схема непосредственно или через промежуточный файл связей («netlist») может быть преобразована в заготовку проектируемой печатной платы, с различной степенью автоматизации.
Системы автоматизации проектирования электроники могут иметь возможность моделирования разрабатываемого устройства и исследования его работы до того, как оно будет воплощено в аппаратуру.
Некоторые симуляторы[1]:
- SPICE — симулятор электронных схем общего назначения с открытым исходным кодом.
- PSpice — программа симуляции аналоговой и цифровой логики, описанной на языке SPICE.
- Logisim — для цифровых схем.
- LTSpice
- Ngspice — симулятор электронных схем общего назначения с открытым исходным кодом, обеспечивающий моделирование в режиме смешанных сигналов и на смешанном уровне.
- Micro-Cap — SPICE-подобная программа для аналогового и цифрового моделирования цепей с интегрированным визуальным редактором.
- TkGate — программа для редактирования (графического и с использованием Verilog) и моделирования цифровых схем.
- QUCS
Программное обеспечение проектирования[править | править код]
Список примеров в этом разделе не основывается на авторитетных источниках, посвящённых непосредственно предмету статьи или её раздела.Добавьте ссылки на источники, предметом рассмотрения которых является тема настоящей статьи (или раздела) в целом, а не отдельные элементы списка. В противном случае раздел может быть удалён. |
- ↑ Susmita Bandyopadhyay, Ranjan Bhattacharya. Discrete and Continuous Simulation: Theory and Practice. — CRC Press, 2014. — P. 228. — 375 p. — ISBN 978-1-4665-9639-9.
- Birnbaum, M. Essential Electronic Design Automation (EDA). — Prentice Hall PTR/Pearson Education, 2003. — 234 p. — ISBN 9780131828292.
- Wang, L.T. and Chang, Y.W. and Cheng, K.T. Electronic Design Automation: Synthesis, Verification, and Test. — Elsevier Science, 2009. — 972 p. — ISBN 9780080922003.
- Louis Scheffer, Luciano Lavagno, Grant Martin. EDA for IC System Design, Verification, and Testing. — CRC Press, 2006. — 544 с. — ISBN 0849379237.
ru.wikipedia.org
Основы электробезопасности при проектировании электронных устройств / Habr
Привет, Хабр!После волны, поднятой моим предыдущим постом, довольно заметное число людей спрашивали меня (в фейсбуке, в личке и т.п.), на что, собственно, обращать внимание, чтобы вместо умной розетки на ардуино не получить очередной тазик-эвтаназик.

Тема это большая и сложная, но я постараюсь выделить основные моменты — не в последнюю очередь на основании ошибок, которые я видел во всевозможных реальных устройствах и проектах, в том числе публиковавшихся на Хабре. Я не буду долго и нудно перечислять ГОСТы, но перечислю совсем базовые вещи, которые необходимо понимать и соблюдать, чтобы не убить хотя бы себя (если вы планируете не убивать также и окружающих, то после завершения этой статьи не поленитесь пролистать и релевантные ГОСТы).
Итак, вы собрались делать устройство, которое как минимум одним своим концом включается в розетку.
Определите степень потенциальной опасности
Не все устройства одинаково опасны — более того, устройства с одним и тем назначением могут быть более или менее опасны в зависимости от модели их использования. К факторам, определяющим опасность, могут относиться:
- Лёгкость контакта человека с токопроводящими частями — например, возможен ли этот контакт в бытовых условиях или для его достижения надо предпринимать специальные действия (например, влезть в электрощиток)
- Квалификация людей, для которых устройство предназначено — это могут быть дети, взрослые непрофессионалы или взрослые професионалы. Понимания опасности поражения током можно ожидать только от последних, от вторых — максимум отсутствия целенаправленных действий по поломке устройства.
- Наличие постоянного электрического контакта с телом человека или возможность появления такого контакта, от которого человек не сможет избавиться — к первому относятся, например, все медицинские приборы с нательными электродами, ко второму — например, установки в сильно ограниченном пространстве, в котором человек, случайно схватившийся за электрод под напряжением, не сможет самостоятельно освободиться.
- Наличие вблизи других заземлённых устройств или, наоборот, устройств под напряжением — скажем, у электрощитка заземлён корпус, так что, держась одной рукой за его дверцу, а другой случайно взявшись за провод под напряжением, отправиться к праотцам особенно легко. С другой стороны, непрофессионалы не должны вообще лазить внутрь щитка, а остальных заземление его корпуса защищает от появления на нём опасного напряжения, например, при обрыве внутри щитка фазного провода и случайном касании этим проводом корпуса щитка изнутри.
- Факторы, значительно снижающие напряжение пробоя — в первую очередь это высокая влажность, особенно с конденсацией, во вторую — пониженное давление воздуха (для устройств, которые применяются на высотах более 2000-3000 м, начинают быстро расти требования к величинам защитных воздушных зазоров между токопроводящими частями).
Обратите внимание, что в совершенно обычных бытовых условиях можно получить комбинацию сразу нескольких факторов — например, известные случаи убийства людей заряжающимися смартфонами в ванной. Во-первых, очень высокая влажность с конденсацией — попадая внутрь зарядного устройства, влажный воздух сильно снижает электрическую прочность изоляции между первичными и вторичными цепями, в результате чего пробой 230 В на USB-разъём зарядки становится более чем вероятным (а в китайских поделиях так и вовсе практически гарантированным). Во-вторых, металлические ванны и трубы водоснабжения должны быть заземлены, чтобы гарантировать отсутствие на них — и особенно между ними — опасных для жизни потенциалов. В-третьих, человек, сидящий в ванне, имеет не просто очень хороший электрический контакт с ней, а контакт, от которого он ещё и не может быстро избавиться.
Вычтем любое из этих обстоятельств — и процесс зарядки любимого айфона становится снова вполне безопасным.
В целом, если ваше устройство относится хотя бы по каким-то признакам к зоне риска — лучше всего его не делать, ибо понимание, как правильно сделать устройство для таких условий, достаточно нетривиально и требует соответствующего опыта.
Что и от чего мы изолируем?
Этот вопрос кажется тривиальным, но большинство поделок заваливаются именно на нём.
Тривиальный ответ: мы изолируем цепи которых может коснуться пользователь (т.н. вторичные цепи), от цепей, которые включены в розетку (т.н. первичные цепи).
Чуть менее тривиален ответ на вопрос, от какого напряжения мы изолируемся. С одной стороны, в розетке у нас 230 В среднеквадратичного напряжения, итого 324 В амплитудного — ну, допустим, даже если в результате того же отгорания нуля мы получим 380 В среднеквадратичного, это будет «всего лишь» 536 В амплитудного.
Тем не менее, сделать изоляцию, выдерживающую 600-800 В, совершенно недостаточно.
Проблема заключается в том, что в сети редко, но метко могут случаться всплески существенно большей величины — более того, они могут быть синфазными (например, при близком ударе молнии), т.е. наведёнными одновременно в нулевом и фазном проводах. В этом случае напряжение «в розетке» существенно не изменится относительно нормальных 230 В, а вот напряжение между розеткой и какой-либо другой «землей» может кратковременно превысить эти 230 В в разы.
На кратковременность такого импульса полагаться не стоит — если он пробьёт изоляцию вашего устройства, по пути пробоя может потечь ток и при более низком напряжении. Варианты тут от просто физического разрушения изоляции до зажигания разряда — как в люминисцентной лампе, в которой тлеющий разряд запускается 800-вольтовым импульсом со стартёра, а дальше горит уже от обычных 230 В переменного тока неограниченное время.
По этой причине изоляцию между первичными и вторичными цепями бытовых устройств рассчитывают на напряжение 2,5 кВ.
Лирическое отступление: очень подробно про это можно почитать, например, в ГОСТ IEC 60950-1-2014 или ГОСТ IEC 60065-2013, на которые ссылается основополагающий документ — Технический регламент Таможенного союза (ТР ТС) 004/2011 «О безопасности низковольтного оборудования». В частности, оба документа указывают для сетей электропитания с действующим напряжением до 300 В возможное напряжение переходных процессов до 2500 В. По аналогичным документам живёт, в принципе, весь мир — под названиями ГОСТ, IEC или UL 60950.
Табличка из IEC 60950. В общем случае при расчётах, касающихся безопасности пользователя, стандарт рекомендует относить все питающие сети к категории II.
Важный момент: наличие изоляции не означает, что между первичной и вторичной цепями устройства не может протекать ток. В некоторых случаях избежать такого тока невозможно или неразумно — например, в импульсных источниках питания для снижения помех между первичкой и вторичкой стоит конденсатор небольшой ёмкости. В таком случае устройство должно быть спроектировано так, чтобы ток утечки между первичкой и вторичкой ни при каких обстоятельствах не превышал безопасный предел (3,5 мА для бытового стационарного оборудования, 0,25-0,75 мА для носимого оборудования; для медицинского оборудования свои нормы, они жёстче в 10-100 раз в зависимости от типа оборудования, тут можно посмотреть презентацию про различия в требованиях).
Итак, наши минимальные требования — изоляция прочностью 2,5 кВ между первичными и вторичными цепями с током утечки при нормальных условиях не более 3,5 мА.
Как мы это изолируем?
- Все компоненты, соединяющие первичные и вторичные цепи, должны быть рассчитаны на напряжение изоляции не менее 2,5 кВ. В импульсном источнике питания это, как правило, трансформатор, оптрон обратной связи и помехоподавляющий конденсатор.
- Никаких прямых соединений первичных и вторичных цепей быть не должно.
- Помехоподавляющие конденсаторы, соединяющие первичную и вторичную цепи, должны быть официально сертифицированы по классу не ниже Y2 (safety rated Y2 capacitors) — такие и только такие конденсаторы можно применять в цепях, где выход конденсатора из строя несёт опасность. Конденсаторы класса Y2 маркируются в действующем напряжении сети переменного тока, на которое они рассчитаны («250VAC»), при этом для них гарантируется устойчивость к одиночным импульсам напряжением до 5 кВ. Никакие другие конденсаторы, включая маркированные на 3 кВ и выше, но не имеющие класса безопасности, в подобных цепях использоваться не должны. Типовой пример — конденсаторы Murata серии DE2. Для reinforced insulation (см. ниже) должны применяться конденсаторы класса Y1, например, Murata DE1.
- При проектировании печатной платы зазоры между проводниками, деталями и корпусом устройства должны быть рассчитаны на пробивное напряжение не ниже 2,5 кВ.
С проектированием печатных плат начинается, разумеется, самое интересное. Дело в том, что «рассчитаны на напряжение не ниже» — это такая фраза ни о чём; в реальных условиях эксплуатации могут играть роль разные факторы, такие как длительность воздействия напряжения, состояние поверхности платы, влажность воздуха, наличие или отсутствие конденсации влаги… Чтобы с ними разобраться, в IEC 60950 введены различные способы классификации этих факторов, а прочность изоляции указывается не в вольтах, а в миллиметрах минимально необходимого зазора — с учётом вероятности пробоя данного зазора и последствий, к которым оно приведёт. В результате защита от одних и тех же 2,5 кВ случайного броска в питающей сети категории II будет выглядеть совершенно по-разному в зависимости от того, может отказ этой защиты вас убить или нет.
Во-первых, IEC 60950 вводит четыре класса изоляции в зависимости от её назначения и, соответственно, требуемой надёжности (точнее, вероятности отказа помножить на последствия этого отказа):
- Functional — необходимая для функционирования самого устройства, но не обеспечивающая защиты пользователя.
- Basic — обеспечивающая начальный уровень защиты пользователя, но недостаточно надёжная, чтобы обойтись без второго защитного барьера.
- Supplementary — второй защитный барьер. Имеет такую же прочность, как и Basic.
- Reinforced — изоляция повышенной прочности, которую можно применять без второго защитного барьера. Имеет вдвое большую прочность, чем Basic.
Далее про различные варианты реализации изоляции написано достаточно много (МЭКовские стандарты платные, но мы же понимаем, что в яндексе найдётся всё?), остановимся на требованиях к печатным платам в бытовых устройствах.
Для оценки диэлектрических способностей различных материалов IEC 60950 делит их на группы по параметру CTI (Comparative Tracking Index) — чем выше CTI, тем лучше изолирующие свойства материала:
- Группа IIIb — 100 < CTI < 175
- Группа IIIa — 175 < CTI < 400
- Группа II — 400 < CTI < 600
- Группа I — CTI > 600
Обычный стеклотекстолит FR4 имеет CTI = 175, то есть, относится к группе III, к границам между подгруппами IIIa и IIIb.
Кроме того, диэлектрические свойства материала, разряд в котором может произойти по его поверхности (случай печатной платы), зависят от уровня загрязнения этой поверхности, поэтому IEC 60950 вводит несколько обобщённых классов загрязнения (в стандарте более формализованные определения, ниже я привязываю их к условиям эксплуатации):
- Уровень I — загрязнения, не ухудшающие электрическую прочность изоляции. Относится только к оборудованию в чистых комнатах или в герметичных корпусах, не допускающих попадание внутрь даже бытовых загрязнителей.
- Уровень 2 — офисная или бытовая обстановка, возможные загрязнители обычно не проводят ток, но в единичных случаях при конденсации влаги могут стать проводящими.
- Уровень 3 — промышленная обстановка, агрохозяйства, особеннно неотапливаемые помещения. Загрязнители могут проводить ток, как в случае образования конденсата, так и без него.
- Уровень 4 — использование без защиты от внешней среды, регулярное воздействие воды или снега.
Отмечу, что нужный уровень защиты может быть реализован использованием адекватных внешних корпусов — например, устройство с уровнем 2 может эсплуатироваться на улице при использовании герметичного корпуса.
Наконец, в IEC 60950 используются два способа измерения расстояния, образующего изолирующий промежуток — clearance и creepage.
- Clearance — кратчайшее расстояние между проводниками.
- Creepage — расстояние между проводниками по поверхности печатной платы.
Для нашего случая для номинального напряжение в розетке 230 В ± 10 % необходимо ориентироваться на требования к изоляции в сетях до 300 В среднеквадратичного напряжения, до 420 В амплитудного и до 2500 В выброса при переходных процессах.
В зависимости от типа изоляции (функциональную не рассматриваем, т.к. говорим о безопасности пользователя) минимально необходимая дистанция по печатной плате составит:
- Basic: 3,0 мм, если у устройства есть дополнительная изоляция
- Reinforced: 6,0 мм, если у устройства нет дополнительной изоляции
Однако, если мы вернёмся к упомянутому выше Y-конденсатору, то без труда заметим, что максимальное расстояние между его ножками по даташиту — 7,5 мм.
Как нетрудно заметить, с учётом контактных площадок нам будет проблематично получить расстояние между проводниками 6,0 мм, если мы не начнём ножки растаскивать вручную.
К счастью, есть простой выход — как видно по картинке выше, creepage можно увеличить, сделав в текстолите вырез. Воздух имеет более высокую электрическую прочность, чем FR4 — для него пробивное напряжение приближается к 3 кВ/мм, а в целях обеспечения безопасности обычно принимается равным 1-1,5 кВ/мм. IEC 60950 требует для воздушного зазора для цепей до 300 В ширины 2,0 мм для базовой изоляции и 4,0 мм для усиленной (в случае, если производство имеет соответсвующую требованиям стандарта программу контроля качества, ширина может быть уменьшена до 1,5 мм и 3,0 мм, но сейчас это не наш случай).
То есть, мы можем обеспечить нужную изоляцию с помощью 4 мм воздуха или 6 мм печатной платы.
В силу сложности вопроса, стандарт не рассматривает комбинацию из воздуха и печатной платы, однако на практике именно такая комбинация в большинстве случаев и применяется — в плате между первичными и вторичными цепями делается вырез:
В данном случае, сделав вырез шириной 2 мм и длиной чуть больше ширины земляных полей, мы получили минимальный creepage равным 6,48 мм, что удовлетворяет требованию к reinforced insulation, а поперёк выреза, если считать «в лоб» — 3,7 мм текстолита и 2,0 мм воздуха, каждое из значений соответствует требованию одного слоя basic insulation, так что в сумме их также можно считать достаточными.
Вот с этим уже можно жить.
Отмечу, что правильное проектирование платы не освобождает от проблем с расположением компонентов: между любыми токопроводящими частями первички и вторички должны быть минимум те же 2 мм воздуха, а в случае незаземлённого корпуса между ним и первичкой для reinforced insulation стандарт требует 10 мм воздуха.
P.S. Справедливости ради, добавлю, что для reinforced insulation предназначены конденсаторы класса Y1, у которых обычно расстояние между ножками 10 мм. Впрочем, это не отменяет необходимости в прорезях в текстолите там, где не удаётся выдерживать зазор не менее 6 мм по разным причинам — из-за плотного монтажа, других компонентов с недостаточным зазором между выводами и т.п. Кроме того, даже если вы используете Y2-конденсаторы и гарантируете только базовую изоляцию, заложить все остальные компоненты, включая дизайн PCB, с запасом в вопросах безопасности лишним точно не будет.
Помимо этого, у прорезей в печатной плате есть ещё несколько положительных сторон — так, на их поверхности не скапливается грязь в силу отсутствия этой поверхности, да и с гигроскопичностью у них всё хорошо. Тем не менее, наличие прорезей само по себе ещё ничего не говорит о безопасности дизайна, равно как и их отсутствие — о его небезопасности.
Классические ошибки
Очевидная фатальная ошибка — это, само собой, полное игнорирование требований безопасности и выдерживание зазоров между первичными и вторичными цепями масштаба 0,5-1 мм, по принципу «при первом включении никого не убило — значит, всё в порядке». Вот, например, типичное любительское немецкое документальное кино, в котором выфрезерованы красивые прорези функциональной изоляции между проводниками сетевого питания, но при этом миллиметровый зазор между входом 230 В и землёй вторички, на которой сидит свободно доступный пользователю разъём USB — включать эту конструкцию в 230 В попросту опасно для жизни.
Помимо гарантированно фатальных, регулярно случаются ошибки потенциально фатальные.
Во-первых, неопытные разработчики интуитивно воспринимают как высокое напряжение между двумя проводами сети 230 В, но не между первичкой и вторичкой — и закладывают прорези именно между ними. Это бывает не лишено смысла, если дорожки сети идут на плате близко друг к другу, и это будет относиться к обеспечению функциональной изоляции, но не имеет прямого отношения к безопасности — в конце концов, в штатной схемотехнике между этими проводами у вас должен быть варистор на напряжение срабатывания порядка 430 В, так что сильно больше там не будет. Более того, если к вам прилетит высоковольтный синфазный импульс, то как раз между проводами сети ничего особенно интересного не случится.
А вот между первичкой и вторичкой — ещё как случится.
Во-вторых, прорезь в плате неопытными разработчиками воспринимается как то ли нечто декоративное, то ли как серебряная пуля и лекарство от всех болезней сразу. Например, тот самый Битроникс Лаб выложил картинки своей USB-развязки, которую они обещают бесплатно выдать всем покупателям опасного набора, и похвастался, что она сделана с запасом — на напряжение 5 кВ:
Для простоты расчётов я быстро набросаю её в DipTrace, благо наименования компонентов известны, а размеры щелей нетрудно вычислить из картинки — ширина 2 мм, длина не выходит за пределы ширины компонентов. Мы не знаем, как плата залита землёй, но будем предполагать, что полигоны не выходят за границы ножек компонентов.
Итого: ADuM4160 — clearance 5,4 мм по текстолиту + 2 мм воздуха, creepage 2,73*2 + 2 = 7,46 мм; AM2D — clearance 4,12 мм по текстолиту + 2 мм воздуха, creepage 6,75 мм. Значения приблизительные, так как форма площадок может отличаться, но ±0,1 мм нас тут явно не волнуют.
Нетрудно заметить, что реальные параметры лишь едва-едва превосходят требования IEC 60950 для сети 300 В с выбросами до 2500 В для случая reinforced insulation — а так как в случае Битроникс Лаб мы говорим по сути о медицинском оборудовании с прямым контактом с телом человека, крайне желательно проектировать его под максимально возможный уровень защиты.
Реальная гарантированная прочность изоляции всей конструкции будет не выше 3 кВ. Заявления о 5 кВ с этой платой неуместны ни под каким соусом — она не рассчитана на такой уровень защиты. В данном случае можно было, даже не увеличивая габариты печатной платы, придвинуть изолятор и DC/DC ближе друг к другу и сделать под ними единую прорезь, сверху и снизу выходящую за пределы корпусов компонентов хотя бы на миллиметр.
Замечу, что при высоких напряжениях — от 5 кВ и выше — начинает играть роль также форма проводников: напряжённость поля и, соответственно, вероятность пробоя выше на заострённых частях.
Как проверить имеющееся устройство?
Хотя лабораторные испытания по ГОСТовским методикам для большинства любителей неподъёмны, для маленьких компаний неприятны своей стоимостью и длительностью, в продаже есть приборы, которые позволяют грубо оценить безопасность устройств — это высоковольтные измерители сопротивления изоляции.
По сути, это гигаомметры (с верхним пределом 10-20 ГОм), при измерении подающие на щупы высокое напряжение — 1000 В для дешёвых моделей и 2500 В для тех, что подороже.
Если вы занимаетесь разработкой втыкаемых в розетку устройств или интересуетесь безопасностью китайских изделий — очень рекомендую приобрести, как минимум, что-нибудь вроде UT-502A (в Чип-и-дипе он тоже есть, но дорого).
Если ваше устройство выдержало 10 секунд под подаваемым им напряжением 2500 В — значит, всё не полностью безнадёжно. Такие испытания не является основанием считать устройство соответствующим стандартам — как нетрудно заметить, в общем случае даже слой функциональной изоляции уже обязан выдерживать подобные напряжения, хотя при этом вероятность его пробоя считается слишком высокой, чтобы использовать его для защиты пользователя.
Более показательным было бы тестирование оборудования импульсом с напряжением 5 кВ, но, увы, такие приборы стоят уже других денег.
С другой стороны, если даже на 2,5 кВ ваше устройство показало что-то, отличное от верхнего предела гигаомметра, вы теперь знаете, что с ним надо сделать.
habr.com
Siemens Digital Industries Software меняет подход к проектированию электрических систем
Совместная работа при проектировании электрических систем изделий.
Электрооборудование — основа современной продукции

Сегодня большинство изделий просто напичкано электроникой. Электронные системы воспринимают окружающую среду и управляют работой оборудования. Процессоры, печатные платы и встроенное программное обеспечение позволяют машинам интеллектуально реагировать на обстановку и воздействовать на нее при помощи двигателей и приводов. Электронные компоненты обеспечивают обмен данными с устройствами Интернета вещей (IoT). Кроме того, электроника интегрирована с электрооборудованием, ставшим своего рода «нервной системой» современных изделий.
Поэтому сегодня проектирование электрических систем — важнейший этап разработки продукции. При нехватке электрической мощности электроника начнет работать со сбоями, а при ее избытке — сгорит либо предохранитель, либо сами электронные компоненты. Слишком малая пропускная способность сети приводит к потере пакетов, что выводит из строя системы управления или не позволяет применять результаты аналитической обработки данных, поступающих с устройств Интернета вещей. Без надежных электрических систем современные изделия становятся просто неработоспособными.
Совместный и пошаговый процесс разработки

Проектирование электрических систем — очень трудоемкая задача. Причем решают ее не только инженеры-схемотехники. Большой вклад вносят и инженеры-механики. Они разрабатывают трассы прокладки проводки через механические узлы изделия, нередко объединяя провода в жгуты. Как правило, процесс идет следующим образом:
Проектирование электрической части: инженеры-схемотехники разрабатывают функциональный и логический проект электрической системы. Они выбирают типы электрических элементов и разъемов. Элементы соединяются проводниками. Затем выполняется контроль проектных решений, чтобы убедиться, что схема функционирует именно так, как задумывалось. На этом этапе получается полное описание электрической системы с указанием всех элементов, разъемов и соединяющих их проводников.
Трассировка электропроводки по механическим узлам: На основе проекта электросистемы инженеры-механики начинают прокладывать проводку по механическим узлам. При этом они следуют документации, подготовленной инженерами-схемотехниками. В ней указано, какие элементы соединяет каждый провод. Чтобы не создавать хаоса, инженер-механик объединяет провода в жгуты и находит оптимальные траектории их трассировки, обеспечивающие выполнение всех электрических соединений.
Итерационное проектирование и устранение возникающих проблем:
На трассировке жгутов проводки по механическим узлам изделия проектирование не завершается. Всегда возникают проблемы, требующие выявления и устранения. В частности, если провод оказывается слишком длинным, то происходит чрезмерное ослабление сигнала.
Если силовой кабель проложить рядом с кабелем управления, то возможно возникновение помех. Инженеры-схемотехники и инженеры-механики должны совместно и итерационно работать над выявлением и устранением проблем. На этом последнем этапе схемотехникам и механикам необходимо постоянно обмениваться информацией. Чтобы проверить качество прохождения сигналов, электрикам нужно знать исходные длины проводников и длины после внесения изменений. Механикам же нужно знать обо всех изменениях, вносимых электронщиками в проводку и разъемы. Поэтому важность обмена информацией и совместной работы трудно переоценить.
Трехминутная демонстрация создания, маршрутизации и упорядочения проводов, кабелей и жгутов в среде сборки Solid Edge:
Еще один момент — в ряде случаев инженерам-схемотехникам и механикам нужно решать проблемы совместными усилиями. Для этого нужно четко понимать взаимное расположение электрических элементов, проводки и механических узлов, что позволит успешно выявлять и устранять несоответствия.
Примитивные, разрозненные системы
С учетом растущего спроса на интеллектуальные, подключение к сети изделия и устройства Интернета вещей большинству компаний требуется простые и эффективные системы проектирования (лучше всего, если они уже имеются в организации). К ним относятся:
- универсальное приложение для разработки электросхем, в котором выполняется проектирование электрических систем;
- 2D-системы автоматизированного проектирования (CAD), применяемые для прокладки проводов и жгутов по механическим узлам изделия;
- электронные таблицы для подготовки спецификаций и проведения расчетов;
Чисто технически этого набора инструментов достаточно для проектирования электрических систем. Однако главные недостатки скрываются в способах взаимодействия инженеров-механиков и электриков, что создает риски для всего процесса разработки изделия; - Отсутствие автоматизации: эти три приложения никак не интегрированы между собой, что не позволяет автоматизировать процессы передачи информации с этапа проектирования электрооборудования на этап трассировки электропроводки по механическим узлам. Инженерам-механикам приходится вручную разбираться с документацией на электрическую систему, чтобы выяснить, где и какие провода требуются проложить;
- Отсутствие ассоциативности при итерационном процессе проектирования: Как уже отмечалось выше, разработка электрических систем является информационным процессом. Перечисленные инструменты никак не связаны между собой. Любые вносимые изменения приходится вручную оценивать и обсуждать с коллегами. Это не только тратит драгоценное время, но и приводит к появлению ошибок из-за человеческого фактора;
- Отсутствие интерактивности: Разрозненные инструменты не позволяют найти один и тот же провод и на электрической схеме, и на чертеже механического узла. Приложения не связаны между собой. В них отсутствует интеллектуальное представление элементов электрооборудования и проводки. Из-за этого инженеры тратят массу времени на выявление проблем, и возникает опасность внесения ошибок.
Указанные недостатки не просто создают неудобства в работе. Они способны привести к гораздо большим проблемам. Невозможность быстрого устранение несоответствий приводит к срыву сроков проектирования. Отсутствие средств поддержки совместной работы инженеров обесценивает их усилия. Высока вероятность того, что конструкторская ошибка перейдет на следующие этапы, что вызовет полную дезорганизацию всего процесса разработки.
Модули Solid Edge Wiring и Harness Design
К счастью, появились новые инструменты проектирования, устраняющие подобные риски. Чтобы соответствовать рыночному спросу и поддерживать высокий уровень качества, нужно найти оптимальный способ интеграции механических и электрических проектных решений. Модули Solid Edge для проектирования электрических систем отличаются удобством в работе, широкой функциональностью и высокой эффективностью, что по достоинству оценят заказчики.
Solid Edge: пакет доступных и удобных инструментов, решающих все задачи разработки изделий. Применительно к проектированию электромеханических систем Solid Edge выполняет 3D моделирование механических узлов, по которым прокладываются жгуты и провода.
Модули Solid Edge Wiring и Harness Design предназначены для разработки электросхем и совместной работы с инженерами-механиками над оптимизацией общей конструкции изделия. Модули поддерживают единство данных на всех этапах — от построения электросхем до конструирования жгутов проводки. В результате принять неверное проектное решение становится просто невозможным.
Модуль Solid Edge Electrical Routing: специализированная среда для эффективного проектирования проводки, трассировки проводов и объединения их в жгуты и кабели при работе со сборками в Solid Edge.
Все модули не только обладают широкой функциональностью, но и полностью интегрированы между собой, что дает целый ряд существенных преимуществ.
Автоматизированная передача информации: благодаря тесной интеграции информация по электрическим системам комплексно передается на этап разработки механических узлов. Инженеры механики получают четкий перечень проводов, которые следует проложить.
Все вносимые изменения двунаправленно передаются между электрической и механической частями проекта. В результате процесс проектирования автоматизируется, а производительность резко повышается.
Интеллектуальная ассоциативность проектной документации: при добавлении элементов в один документ они соответствующим образом добавляются и другие документы. Например, если проставить новый элемент на электросхеме, то он появится в 3D-сборке соответствующего механического узла, а также в конструкторской спецификации, а изменение цвета провода на 3D-сборке механического узла отображается на электросхеме и в спецификации. Иными словами, одно изменение распространяется на все документы. В результате устраняется человеческий фактор и минимизируется вероятность внесения ошибок.
Интерактивное выделение объектов: Рассматриваемые модули в реальном времени подключаются к модулю Solid Edge Electrical Routing. Это делает возможным совместную работу, когда выбор элемента в одном приложении приводит к его выделению в другом. Например, когда инженер-электрик выбирает провод на электросхеме, то этот же провод подсвечивается на 3D-модели механического узла. И наоборот: при выделении провода 3D-модели механического узла этот же провод подсвечивается на электросхеме. Такая функция облегчает обсуждение при выявлении и устранении междисциплинарных несоответствий.
Модули образуют интегрированное решение, повышающее производительность труда и инженеров-электриков, и инженеров-механиков. Специалисты совместно находят проблемы в электрических системах и исправляют их. В результате проекты выполняются вовремя и в рамках бюджета.
Чад Джексон (Chad Jackson), главный аналитик компании Lifecycle Insights:
«Одна из самых больших трудностей при разработке интеллектуальных и подключенных к сетям изделий — решение проблем интеграции электронных, электрических и механических систем. Удобная двунаправленная передача информации между инженерами-электриками и разработчиками механической части позволяет им работать только с актуальными версиями проекта, устраняет проблемы связанные с возрастающей сложностью проекта, а также упрощает совместную работу в случае выявления проблем. Применение модулей Solid Edge Wiring и Harness Design, тесно интегрированных с традиционной средой машиностроительного проектирования Solid Edge— шаг в правильном направлении».
Специальная цена на Solid Edge Electrical Design
Нанософт объявляет специальные цены на ПО для разработки электрической части проекта:
до 20 декабря действует скидка 40% на комплект Solid Edge Electrical Design+Solid Edge, а для пользователей Solid Edge — скидка 40% на Solid Edge Electrical Design.
habr.com
Разработка устройств, разработка электроники на заказ
Разработка электроники, приборов и устройств на заказ
Разработка электронных устройств, это направление науки и технологии, которое переживает сейчас «второе рождение» в связи с бурным прогрессом в элементной базе электроники и развитием инструментальных средств для отладки и проектирования.
То, что было научной фантастикой 8-10 лет назад, сейчас – уже реальность. Заинтересованы в разработке своих электронных устройств в первую очередь стартапы и изобретатели, у которых есть замечательные идеи, и которым хочется поскорее получить готовый прототип. Также в числе наших заказчиков – научные организации, которым необходимо получить электронный прибор для научных исследований, весьма часто которому нет аналогов, ввиду новизны объекта исследований. Также весьма востребована такая услуга у компаний, которые не могут найти готовое электронное устройство с нужным функционалом, но при этом заказчик видит для себя заманчивую нишу в бизнесе. Пока Ваши конкуренты ждут срока поставки 8-10 недель, заказанного товара из КНР, Вы уже получаете прибыль и захватываете рынок. Разработка электроники – это Ваш шанс явить идеи и изобретения миру!
Разработка устройства – этап проектирования архитектуры
Одним из ключевых этапов профессиональной разработки электронного устройства – это этап проектирования архитектуры будущего творения. Происходит тщательный опрос Заказчика, составляется детальное техническое задание, скрупулёзно анализируются технические условия и требования функционала, в ряде случаев предлагается более удачное с нашей точки зрения решение. После этого формируется функциональная схема устройства, происходит согласование с заказчиком и после этого начинается реализация функционала на основе моделей, например, очень хорошо себя зарекомендовали программные CAD/CAE решения от National Instruments. После моделирования выбирается то или иное техническое решение, формируются логические интерфейсы электронного устройства, определяются ресурсы электрического питания, обозначаются крупные функциональные узлы устройства. Уже на этом этапе определяются ключевые особенности будущего устройства, формулируется (пусть даже эскизно) логика взаимодействия отдельных блоков, формируются модели взаимодействия с конечным потребителем устройства. Анализируется техническое задание заказчика на предмет противоречий с последующем уточнением тех. задания.
Разработка электроники устройства – этап подбора элементной базы
После этапа создания архитектуры электронного прибора мы осуществляем процедуру более глубокой и тщательной детализации проекта, на основе функциональной схемы устройства осуществляется подбор уже непосредственно электронных компонентов. Если в устройстве будет использоваться микроконтроллер, то определяется какой это будет контроллер, с какой архитектурой и разрядностью. Определяется какая будет обвязка и силовые электронные компоненты, стоящие в устройстве. Учитываются также моменты, связанные с взаимодействием с периферией проектируемого электронного прибора. Тщательно анализируем в том числе и вопросы связанные с доступностью того или иного электронного компонента, применяемого в данной разработке. Формируем анализ энергопотребления, исходя из которого можно будет планировать, какой например аккумулятор будет использоваться в случае батарейного питания. Также дополнительно прорабатывается механический конструктив, например при использовании разъемов, устройств индикации, дисплеев, органов управления электронным прибором.
Разработка электроники – этап разработки схемотехники
Когда более основательно оформилась элементная база, идет следующий этап – разработка схемотехники самого электронного устройства, на данном уровне уже максимально происходит процесс отладки процессов в электронной схеме, осуществляется то непосредственное «священнодействие», после которого говорят – устройство ожило!
Здесь уже мы имеем симпатичную принципиальную схему электронного устройства, со всеми подключенными элементами и работающей логикой электронной схемы, которую можно показать заказчику. Уже на отладочной плате мигают светодиоды, уже отправляются и получаются сигналы на портах, уже устройство реагирует на органы управления. И тернистый путь процесса, который мы называем “разработка электроники” движется в правильном направлении и приносит свои плоды.
Разработка печатной платы устройства и трассировка
В том случае если принимается решение о запуске прототипа устройства в серийное производство, то одним из важных этапов является разработка чертежа дорожек печатной платы, трассировка их с учетом особенностей схемотехники электронного прибора и подготовка его к серийному производству. При разработке печатной платы обязательно учитываются различные особенности конструкции, например если в схеме есть силовые цепи, то естественно для нормальной работы прибора мы рассчитываем ширину дорожек на плате, если в устройствах есть высокочастотные цепи, то правильным образом делается экранировка и учитывается влияние соседних цепей на работу схемы прибора. При разводке сигнальных цепей компоновке дорожек уделяем самое пристальное внимание. Важное внимание уделяем компоновке электронных компонентов на плате с точки зрения механической прочности и размещения в корпусе. Применяем широкий спектр специализированных программных инструментов для разработки печатных плат, но чаще отдаём предпочтение таким инструментам как Altium Designer. В число операций по подготовке входит формирование gerber файлов для сверлильного станка с ЧПУ, оформление полного комплекта технической документации для организации серийного производства электронного устройства на заводе.
Сборка и макетирование прототипа электронного прибора
После макетирования устройства и отладки схемотехники, мы собираем готовый прототип электронного прибора для демонстрации в аккуратном корпусе, оснащенном всеми интерфейсными разъёмами, органами управления и индикации. Осуществляем монтаж электронных компонентов на платы устройства, производим пайку шлейфов и жгутов, изготовляем дополнительную отладочную оснастку, после чего организуем тестирование разработанного прототипа , в том числе и тепловое тестирование. Можем подобрать уже готовый корпус электронного прибора или спроектировать новый. Уже на данном этапе делаем первичную эргономическую проработку и рациональным образом организуем взаимодействие между прибором и органами управления и индикации, при этом придерживаемся принципов лаконичности и непротиворечивости элементов интерфейса. Если планируется демонстрация прототипа нашего устройства на выставке или ином важном мероприятии, то по согласованию с заказчиком мы заказываем полиграфию для визуального «фронтенда» разработки. Например это могут быть самоклеющиеся наклейки для органов управления или шилды на корпус разработанного устройства.
Разработка прошивки и прикладного ПО для нового устройства
Также в том, случае если проект разработанного устройства содержит в себе микроконтроллер, SoC или иной «высокотехнологичный» электронный узел, потребуется также разработка микропрограммного обеспечения, или как чаще говорят на сленге «прошивки» обеспечивающей широкие возможности для раскрытия потенциала применяемой элементной базы. Работаем с широким спектром программных и аппаратных средств. Но чаще при разработке устройств отдаем хорошо зарекомендовавшим себя решениям от Texas Instruments и STM.
Также для сложных проектов можем предложить написание прикладного ПО для распространенных программных платформ, будь то десктопные приложения, так и веб-приложения работающие на платформе Apache и им подобных. В том числе можем разработать и симпатичный веб-интерфейс для взаимодействия с электронным прибором.
Разработка и сопровождение сложных комплексных проектов
Помимо «пайки транзисторов» мы можем также предложить нашим заказчикам услуги системной интеграции, которые порой весьма тесно переплетаются в том числе и с разработкой электронных устройств. В число этих услуг входят, интеграция сервисов, внедрение промышленной автоматизации на оборудовании сторонних производителей, интеграция SCADA систем. Возможен и экономически оправдан редизайн уже имеющихся электронных приборов на более современной элементной базе либо модернизация таковых.
Также в спектр задач входит сборка и техническое сопровождение серверного и специализированного оборудования, организация каналов связи между различными подразделениями компаний. Осуществляем инженерный аудит уже имеющейся инженерной инфраструктуры, находим слабые места и предлагаем при необходимости варианты для лучшей реализации задач. Ведь технологии не стоят на месте, и нам всегда есть что предложить нашим заказчикам.
Наши услуги по разработке электроники:
- разработка принципиально новых электронных устройств
- редизайн электроники на самой современной элементной базе
- разработка электроники с использованием последних достижений схемотехники
- разработка систем управления для промышленных применений
- проектирование нетиповых кастомных решений
- контрактная разработка на заказ
- изготовление рабочих прототипов приборов
- разработка приборов на заказ
- изобретение и разработка электронных приборов
- осуществление R&D задач
fantasylab.ru
Как создать новый продукт для рынка электроники. Часть 1 / Promwad corporate blog / Habr

Статьи о разработке продуктов в сфере электроники — это большая редкость на Хабре. Я говорю не о любительских проектах или прототипах, а об успешных коммерческих устройствах для массового рынка.
Ведь презентации новых гаджетов Apple, Samsung и других брендов — это только видимая часть айсберга, под которой скрывается человеко-десятилетия труда людей самых разных специализаций: инженеры, программисты, дизайнеры, логисты, руководители различных уровней, продавцы и так далее. Пока ты не погружаешься в эту внутреннюю кухню, может показаться, что процесс довольно простой и понятный: была бы идея, хорошая команда и достаточное финансирование. Однако не все так просто.
Хочу поделиться своим опытом и видением, которое было сформировано за время моего трудового пути от инженера до руководителя, в компаниях как продуктовых, так и сервисных.
Многие читатели Хабра знакомы с внутренней кухней разработки ПО, а ведь железо — это совсем другая история. Готовы? Тогда поехали.
Для начала расскажу, как идет процесс разработки электроники, и сравню его с разработкой ПО. Упрощенно этапы создания нового устройства выглядят так:
Фаза №1. Анализ
У всех эта фаза проходит и называется по-разному: «Расчеты», «Проектирование», «Сбор требований». Одни компании сразу же стартуют с тех. задания, написанного инженером «в теме», другие уделяют чертовски много времени планированию и проработке. Почему же это может быть важно? Причины просты:
- Планирование бюджета. Как правило, процесс разработки продукта довольно длинный и будет неприятно, если после 8—9 месяцев инвестирования у вас внезапно закончатся деньги. Матерые компании и продакт-менеджеры имеют собственные технологии планирования для новых продуктов, которые банки даже принимают в качестве гарантий по кредитам.
- Оптимизация себестоимости. Если вы производите 50 тыс. устройств в год, будет полезно экономить каждый доллар в себестоимости устройства.
- Управление. В разработку любого продукта, даже довольно простого, завязаны тысячи людей (прямо или косвенно: поставщики компонентов, инженеры, маркетологи, рабочие завода-изготовителя и т.д.). Задачи нужно будет делегировать правильным специалистам в правильное время.
- Цена ошибки, она очень высока, и чем раньше мы ее выявляем, тем лучше.
Главная задача фазы анализа — определить четкую концепцию продукта, над которым предстоит работа на последующих этапах, и синхронизировать ее с остальными участниками по мере необходимости. Следует учитывать вопросы конечных клиентов, себестоимость, требования производственных площадок, планы проекта, контрактные обязательства, бюджеты, финансирование, исполнителей, разрешающие и сертифицирующие документы, выбор материалов и компонентов.
Если говорить о планировании нового продукта, то это своего рода искусство, которым занимаются продакт-менеджеры. (Я хочу посвятить отдельный пост продакт-менеджменту в электронике).
Финальный этап фазы анализа — подготовка технического задания, в нем мы определяем функциональные и нефункциональные требования к продукту, прорабатываем технический дизайн и создаем скетчи устройства:
Пример: эскизы новых электронных устройств, созданные командой промдизайнеров компании Promwad
В электронике мы всегда говорим об ограниченности ресурса. Разработчики ПО вне темы embedded уже давно забыли про дефицит, например, оперативной памяти. А тем временем подобные ограничения делают работу инженера крайне увлекательной. Для инженеров-электронщиков технические параметры устройства — это рамки творчества.
Я уже говорил про цену ошибки, внесение изменений в электронике — это долго и дорого. Для ПО можно выпустить обновления, а что можно выпустить для реального предмета? Только другой реальный предмет, в котором недостатки устранены.
Некоторые продукты в сфере электроники «не взлетали» именно по причине нерабочего софта.
Даже самое тщательное планирование не защитит от ошибок на 100%. Вы наверняка читали подобные заголовки новостей:
- Apple отзывает iPod nano: в плеерах найден дефект аккумулятора
- Nokia отзывает 14 миллионов потенциально бракованных зарядных устройств
- Intel отзывает партию чипсетов для процессоров из-за обнаруженного дефекта
- Garmin отзывает более миллиона GPS-навигаторов из-за перегрева аккумуляторов
- Lenovo отзывает свои компьютеры из-за риска внезапного возгорания
Итак, что мы получаем в итоге фазы проектирования? Набор документации, контрактных обязательств и команду, которая понимает продукт и заряжена на успех.
Фаза №2. Разработка
Как правило, электронное изделие состоит из следующих компонентов, которыми занимается инженерный отдел:
- Железо
- Корпус
- Софт
- Технологии производства
А вот эти компоненты остаются за границами инженерного отдела (мы к ним вернемся позже):
|
|
Железо. Благодаря современным САПРам разработка аппаратного обеспечения — это достаточно стандартизованный процесс, который при хорошо сформированных вводных не длится долго (от 2 недель до пары месяцев максимум). Самая сложная штука — это конструкция. Дело в том, что физическое расположение одних элементов относительно других играет большую роль и оказывает непосредственное влияние на работоспособность современного устройства.
Промышленный дизайн. Внешниий вид корпуса плотно привязан к технологии производства. Технология — это материалы, а значит — стоимость. Дизайнер может нарисовать абсолютно волшебную штуку, но для ее воплощения в жизнь понадобится труд конструктора и технолога. Технологические лидеры ставят уникальный дизайн во главу угла, и потому непрерывно создают новые технологии производства.
Программное обеспечение в электронике работает в условиях ограниченных ресурсов. Подход к его разработке кардинально отличается от подходов, принятых в индустрии разработки ПО для веба, десктопов и т.п. Используются другие инструменты и другая среда разработки: версии ОС для встраиваемых систем Windows CE, Linux Embedded и т.п.
Программисты-электронщики сильно завязаны на железе. Если разработчик десктопных приложений не задумывается о корректности работы своей аппаратной платформы, то инженер-программист сталкивается с этим постоянно, особенно при работе с новыми компонентами. У меня были проекты, в которых баги в программе возникали из-за ошибок в работе процессора либо от плохого монтажа. К слову последнее — это действительно серьезная проблема для дизайн-центров.
Еще пример: программист и дизайнер могут создать интерфейс пользователя, который будет отлично работать на тестовой платформе, но вызовет перегрузку оперативной памяти на реальном устройстве. Причем такие ошибки не всегда можно заметить сразу. Сутки устройство работает корректно, а потом перезагружается.
Все эти особенности существенно усложняют жизнь программистов, которые работают со встраиваемым ПО, хотя многие специалисты выбирают электронику как раз ради таких увлекательных задач.
Как правило, промежуточным результатом фазы разработки являются опытные образцы устройства. Процесс их сборки — это вообще отдельная история. Со всего мира в одну точку на карте съезжается сотня компонентов, каждый упакован в отдельную посылку. На специализированном предприятии по специальным технологиям делаются рабочие образцы, они могут выглядеть так:
Пример: образец бортового автомобильного самописца, разработанного в компании Promwad. Корпус выращен в 3D-принтере по технологии лазерной стереолитографии. За счет шлифовки и покраски внешний вид устройства был максимально приближен к заводской версии.
Ваше положение на карте мира практически не имеет значения при разработке софта. А вот при разработке железа сроки производства образца могут различаться в десятки раз в зависимости от положения разработчика и изготовителя. Компании в Китае собирают образец за 2 недели, в России этот срок может доходить до пары месяцев.
После сборки образцы уходят на тестирование. По его результатам мы можем повторить весь процесс с самого начала, чтобы исправить найденные косяки либо понять, что в таком исполнении продукт никому не нужен. Такой вот суровый scrum c циклом в год.
Конечно, мы рассчитываем на удачное завершение тестирования, т.к. хотим перейти к самой увлекательной части проекта — постановке электроники на массовое производство…
UP. Продолжение статьи читайте тут: часть 2.
habr.com
как разработать корпус устройства / Promwad corporate blog / Habr

Разработка корпуса — один из основных этапов создания продукта для рынка электроники. В руках промышленных дизайнеров сосредоточена большая власть и ответственность: именно они определяют внешний вид устройства, стремятся сделать его привлекательным, стильным и удобным.
Каждый день мы пользуемся результатами работы промдизайнеров: смартфонами, ноутбуками, ТВ-приставками, клавиатурами, мышками и другими устройствами. Посмотрим на процесс создания всех этих вещей изнутри и ответим на три самых распространенных вопроса, которые возникают в процессе реализации проектов по разработке корпуса для электроники:
- Промдизайн: что вообще скрывается под этим словом?
- Разработка дизайна и конструкции корпуса: из чего состоит проект?
- Работа с промдизайнерами: как организовать сотрудничество и оценить результаты?
1. Промдизайнеры и графические дизайнеры. Отличия
Важно понимать существенную разницу в работе графического и промышленного дизайнеров: первый — творит, предлагает смелые идеи и работает в двухмерном пространстве, второй — анализирует характеристики устройства, требования заказчика и воплощает их в реальном устройстве, создавая свои работы в трехмерном пространстве.
Промдизайнер обладает знаниями о технологиях, материалах, конструкции, эргономике, поэтому он рисует не просто красивую картинку, а воплощает свои идеи с учетом всех дополнительных требований. Ведь без учета технологий производства и параметров себестоимости даже самый лучший эскиз корпуса так и останется на бумаге.
2. Дизайн и конструкция корпуса: этапы разработки
Разработка корпуса для электронного устройства — это не только дизайн (эскизы, 3D-модели), но также разработка конструкции и документации для серийного производства.
Как правило, проект по разработке дизайна включает следующие этапы:
- Генерация идей и концептуальная проработка
- Разработка оригинального дизайна и конструкции
- Выбор материалов для корпуса
- Создание прототипов и опытных образцов корпуса
- Постановка на производство
Начиная с эскизов и предпроектных исследований важно учитывать технологические и ценовые особенности будущего устройства, поэтому дизайнеры должны работать вместе с технологами и конструкторами, которые реализуют требования производства и оценивают себестоимость.
Самая сложная и длительная часть работы — это предварительный анализ и разработка эскизного предложения (концепции). На этих этапах команда разработчиков решает следующие задачи:
- Исследование. Промдизайнер собирает информацию и погружается в тему: анализирует лучший опыт отечественных и зарубежных компаний, которые проектировали аналогичные изделия; изучает конструкционные и отделочные материалы, оценивает рациональность их применения; определяет требования к будущему изделию (эргономические, функциональные, экономические).
- Техническое задание. Далее по результатам исследований можно готовить ТЗ, в котором будут указаны эксплуатационные, технические и эстетические требования к изделию. Для создания конкурентоспособного продукта они должны быть на уровне или выше рыночных аналогов. Как правило, ТЗ составляется совместно с заказчиком, с учетом его пожеланий.
- Генерация идеи. На этом этапе дизайнер ведет эскизный поиск: делает зарисовки на бумаге или графическом планшете. Источником его вдохновения является не только материал исследований и ТЗ, но также архитектура, графика, произведения искусства, природный мир. Какой-то элемент из этого списка может стать отправной точкой для последующего формообразования. В результате заказчик получает несколько концепций будущего дизайна.
- Трехмерное моделирование и визуализация. Лучшие эскизные предложения промдизайнер создает в виде трехмерной модели будущего объекта, включая визуализацию и наложение текстур. Он также готовит итоговые файлы для согласования проекта с заказчиком: 3D-модели и фотореалистичные 2D-изображения.
- Разработка конструкции. На основе выбранного дизайна создается конструкция корпуса. Она учитывает возможностей производства, сборки и характеристики материалов. Этот этап выполняется в современных системах автоматизации проектных работ (САПР), таких как CREO (Pro/Engineer).
3. Работа с промдизайнерами: ведение и сдача/приемка проекта
Дизайн-проектирование может начаться с разных этапов. В некоторых проектах заказчик знает только о технической начинке будущего устройства, тогда дизайн корпуса создается с нуля. Бывает, что заказчик предлагает дизайнерам готовую концепцию, которую нужно проанализировать и доработать.
В процессе работы с промдизайнерами полезно придерживаться следующих правил:
- Делим проект на четкие этапы, с конкретными целями и задачами. Последовательно обсуждаем все предварительные результаты.
- Договариваемся о личных встречах или видеоконференциях, общение только через электронную почту или скайп менее продуктивно.
- Ставим цели: у всех участников проекта должно быть четкое понимание будущего устройства (целевая аудитория, функциональность, ценовая категория, себестоимость). Без этого дизайн разработать невозможно.
- Выбор дизайна лучше доверить мнению нескольких компетентных специалистов, для более объективной оценки. Мнение одного человека не всегда объективно.
При оценке результатов работы дизайнера стоит обратить внимание на следующие характеристики:
- Внешний вид корпуса. Формы, пропорции линий, цветовое решение — всё это должно соответствовать запросам потребителей.
- Фирменный стиль. Дизайн должен соответствовать общей философии и политике компании.
- Материалы и технологии производства. Выбранные материалы корпуса должны соответствовать требованиям к устройству, учитывать заданную себестоимость и возможности производства.
- Практичность. Использование продукта должно быть безопасным, простым и интуитивно понятным.
- Удобство сборки и обслуживания. Собираемость изделия должна быть проверена на прототипах, важно оценить возможности ремонта и технического обслуживания устройства.
Мы надеемся, что эти советы помогут вам запустить свой проект и получить ожидаемый результат. Более подробно эта тема раскрыта на нашем сайте: разработка промдизайна в Promwad.
habr.com