особенности, принцип работы, преимущества и недостатки
Плазменную резку очень часто используют в таких отраслях промышленности, как судостроение, машиностроение, а также при изготовлении металлоконструкций, коммунальной сфере и т. п. Кроме этого, плазморез довольно часто используется в частной мастерской. С его помощью быстро и качественно разрезают любой материал, проводящий ток, и некоторые нетокопроводящие материалы – дерево, камень и пластик.Технология плазменной резки позволяет разрезать листовой металл и трубы, выполнять фигурный рез или изготавливать детали. Работа осуществляется при помощи высокотемпературной плазменной дуги. Чтобы ее создать, потребуется только источник тока, воздух и резак. Чтобы работа выполнялась довольно легко, а рез получался ровным и красивым, следует выяснить, как осуществляется принцип работы плазменной резки.
Как устроен плазморез
Этот аппарат состоит из следующих элементов:- источник питания;
- воздушный компрессор;
- плазменный резак или плазмотрон;
- кабель-шланговый пакет.
Источник питания для аппарата плазменной резки осуществляет подачу на плазмотрон определенной силы тока. Представляет собой инвертор или трансформатор.
Инверторы довольно легкие, в плане энергопотребления экономные, по цене недорогие, однако, способны разрезать заготовки небольшой толщины. Из-за этого их применяют только в частных мастерских и на маленьких производствах. У инверторных плазморезов КПД на 30% больше, чем у трансформаторных и у них лучше горит дуга. Часто используют их для работ в труднодоступных местах.
Трансформаторы гораздо увесистее, тратят много энергии, но при этом имеют меньшую чувствительность к перепадам напряжения, и с их помощью разрезают заготовки большой толщины.
Плазменный резак считается главным элементом плазмореза. Его основными элементами являются:
- сопло;
- охладитель/изолятор;
- канал, необходимый для подачи сжатого воздуха;
- электрод.
Компрессор требуется для подачи воздуха. Принцип работы плазменной резки предусматривает применение защитных и плазмообразующих газов. Для аппаратов, которые рассчитаны на силу тока до 200 А, применяется только сжатый воздух как для охлаждения, так и для создания плазмы. Они способны разрезать заготовки толщиной в 50 мм.
Кабель-шланговый пакет используется для соединения компрессора, источника питания и плазмотрона. По электрическому кабелю от инвертора или трансформатора начинает поступать ток для возбуждения электрической дуги, а по шлангу осуществляется подача сжатого воздуха, который требуется для возникновения внутри плазмотрона плазмы.
Принцип работы
При нажатии на кнопку розжига начинается подача тока высокой частоты от источника питания (инвертора или трансформатора). В результате этого внутри плазмотрона образуется дежурная электрическая дуга, температура которой достигает 8 тыс. градусов. Столб этой дуги начинает заполнять весь канал.После того как возникла дежурная дуга, в камеру начинает поступать сжатый воздух. Вырываясь из патрубка, он проходит через электрическую дугу, нагревается, при этом увеличиваясь в объеме в 50 или 100 раз. Кроме того, воздух начинает ионизироваться и перестает быть диэлектриком, приобретая свойства проводить ток.
Сопло плазмотрона, суженное книзу, обжимает воздух, создавая из него поток, которое начинает вырываться оттуда со скоростью 2 – 3 м/с. В этом момент температура воздуха часто достигает 30 тыс. градусов. Именно такой раскаленный ионизированный воздух и является плазмой.
В то время, когда плазма начинает вырываться из сопла, происходит ее соприкосновение с поверхностью обрабатываемого металла, дежурная дуга в этот момент гаснет, а зажигается режущая. Она начинает разогревать заготовку в месте реза. Металл в результате этого плавится и появляется рез. На поверхности разрезаемого металла образуются небольшие частички расплавленного металла, сдуваемые с нее потоком воздуха. Таким образом осуществляется работа плазмотрона.
Преимущества плазменной резки
Работы по резке металла часто осуществляются на стройплощадке, в мастерской или цеху. Можно использовать для этого автоген, но не всех это устраивает. Если объем работ, связанный с резкой металла, слишком большой, а требования, предъявляемые к качеству реза, очень высоки, то следует подумать о том, чтобы использовать плазменный резак, имеющим следующие достоинства:
- Если мощность подобрана правильно, то аппарат плазменной резки позволяет в 10 раз повысить производительность. Такой параметр позволяет плазморезу уступить только промышленной лазерной установке, однако, он значительно выигрывает в себестоимости. Целесообразно с экономической точки зрения применять пламенную резку для металла, имеющего толщину до 50 – 60 мм.
- Универсальность. С помощью плазменной резки обрабатываются чугун, медь, сталь, алюминий и прочий металл. Необходимо просто выбрать оптимальную мощность и выставить конкретное давление воздуха.
- Высокое качество реза. Аппараты плазменной резки способны обеспечить минимальную ширину реза и кромки без перекаливания, наплывов и грата практически без дополнительной обработки. Кроме того, достаточно важен такой момент, что зона нагрева материала в несколько раз меньше, чем при использовании автогена. А так как термическое воздействие минимально на участке реза, то и деформация от этого вырезанных деталей будет незначительной, даже если они имеют небольшую толщину.
- Не происходит существенного загрязнения окружающей среды. С экономической точки зрения, если имеются большие объемы работ, то плазменная резка гораздо выгоднее кислородной или механической. Во всех остальных случаях учитывают не материалы, а трудоемкость использования.
Недостатки плазменной резки
Недостатки в работе плазменной резки тоже имеются. Первый из них – максимально допустимая толщина реза довольно небольшая, и у самых мощных агрегатов она редко бывает больше 80 – 100 мм.
Кроме того, рабочее оборудование довольно сложное, что делает совершенно невозможным использование двух резаков одновременно, которые подключаются к одному аппарату.
Заключение
Принцип работы плазменной резки довольно прост. Кроме того, аппарат, который используется для этого, имеет большое количество преимуществ, в несколько раз превосходящие имеющиеся недостатки. Если его правильно эксплуатировать, то можно существенно сэкономить время и получить качественный результат.
Оцените статью: Поделитесь с друзьями!Принцип работы плазменной резки — Плазменная резка
Плазменную резку очень часто используют в таких отраслях промышленности, как судостроение, машиностроение, а также при изготовлении металлоконструкций, коммунальной сфере и т. п. Кроме этого, плазморез довольно часто используется в частной мастерской. С его помощью быстро и качественно разрезают любой материал, проводящий ток, и некоторые нетокопроводящие материалы – дерево, камень и пластик.
Как устроен плазморез
Этот аппарат состоит из следующих элементов:
- источник питания;
- воздушный компрессор;
- плазменный резак или плазмотрон;
- кабель-шланговый пакет.
Источник питания для аппарата плазменной резки осуществляет подачу на плазмотрон определенной силы тока. Представляет собой инвертор или трансформатор.
Инверторы довольно легкие, в плане энергопотребления экономные, по цене недорогие, однако, способны разрезать заготовки небольшой толщины.
Трансформаторы гораздо увесистее, тратят много энергии, но при этом имеют меньшую чувствительность к перепадам напряжения, и с их помощью разрезают заготовки большой толщины.
Плазменный резак считается главным элементом плазмореза. Его основными элементами являются:
Принцип работы
При нажатии на кнопку розжига начинается подача тока высокой частоты от источника питания (инвертора или трансформатора). В результате этого внутри плазмотрона образуется дежурная электрическая дуга, температура которой достигает 8 тыс. градусов. Столб этой дуги начинает заполнять весь канал.
После того как возникла дежурная дуга, в камеру начинает поступать сжатый воздух. Вырываясь из патрубка, он
проходит через электрическую дугу. нагревается, при этом увеличиваясь в объеме в 50 или 100 раз. Кроме того, воздух начинает ионизироваться и перестает быть диэлектриком, приобретая свойства проводить ток.Сопло плазмотрона, суженное книзу, обжимает воздух, создавая из него поток, которое начинает вырываться оттуда со скоростью 2 – 3 м/с. В этом момент температура воздуха часто достигает 30 тыс. градусов. Именно такой раскаленный ионизированный воздух и является плазмой.
В то время, когда плазма начинает вырываться из сопла, происходит ее соприкосновение с поверхностью обрабатываемого металла, дежурная дуга в этот момент гаснет, а зажигается режущая. Она начинает разогревать заготовку в месте реза. Металл в результате этого плавится и появляется рез. На поверхности разрезаемого металла образуются небольшие частички расплавленного металла, сдуваемые с нее потоком воздуха. Таким образом осуществляется работа плазмотрона.
Преимущества плазменной резки
Работы по резке металла часто осуществляются на стройплощадке, в мастерской или цеху. Можно использовать для этого автоген, но не всех это устраивает. Если объем работ, связанный с резкой металла, слишком большой, а требования, предъявляемые к качеству реза, очень высоки, то следует подумать о том, чтобы использовать плазменный резак, имеющим следующие достоинства:
- Если мощность подобрана правильно. то аппарат плазменной резки позволяет в 10 раз повысить производительность. Такой параметр позволяет плазморезу уступить только промышленной лазерной установке, однако, он значительно выигрывает в себестоимости. Целесообразно с экономической точки зрения применять пламенную резку для металла, имеющего толщину до 50 – 60 мм.
- Универсальность. С помощью плазменной резки обрабатываются чугун, медь, сталь, алюминий и прочий металл. Необходимо просто выбрать оптимальную мощность и выставить конкретное давление воздуха.
- Высокое качество реза. Аппараты плазменной резки способны обеспечить минимальную ширину реза и кромки без перекаливания, наплывов и грата практически без дополнительной обработки. Кроме того, достаточно важен такой момент, что зона нагрева материала в несколько раз меньше, чем при использовании автогена. А так как термическое воздействие минимально на участке реза, то и деформация от этого вырезанных деталей будет незначительной, даже если они имеют небольшую толщину.
- Не происходит существенного загрязнения окружающей среды. С экономической точки зрения, если имеются большие объемы работ, то плазменная резка гораздо выгоднее кислородной или механической. Во всех остальных случаях учитывают не материалы, а трудоемкость использования.
Недостатки плазменной резки
Недостатки в работе плазменной резки тоже имеются. Первый из них – максимально допустимая толщина реза довольно небольшая, и у самых мощных агрегатов она редко бывает больше 80 – 100 мм.
Следующий недостаток – достаточно жесткие требования, предъявляемые к отклонению от перпендикулярности реза. Угол отклонения не должен быть больше 10 – 50 градусов и зависит это от толщины детали. Если случается выход за эти пределы, то возникает довольно существенное расширение реза, что в результате влечет за собой быстрый износ расходных материалов.
Кроме того, рабочее оборудование довольно сложное, что делает совершенно невозможным использование двух резаков одновременно, которые подключаются к одному аппарату.
Заключение
Принцип работы плазменной резки довольно прост. Кроме того, аппарат, который используется для этого, имеет большое количество преимуществ, в несколько раз превосходящие имеющиеся недостатки. Если его правильно эксплуатировать, то можно существенно сэкономить время и получить качественный результат.
плазморез какой выбрать
плазма резак
аппарат ручной плазменной резки ручной
станок плазменной резки с чпу цена
аппарат для плазменной резки металла
Принцип плазменной резки. Работа на плазменной резке.
2.1 Нечто большее, чем просто одно из состояний вещества?
Как правильно понимать источники плазменной резки? Плазма представляет собой нагретый до высокой температуры газ, обладающий электропроводимостью, который состоит из положительно и отрицательно заряженных частиц, а также возбужденных и нейтральных атомов и молекул. Между процессами диссоциации, ионизации и рекомбинации, присущими плазменному состоянию, устанавливается динамический баланс. В результате плазма электрически нейтральна. В физике плазму часто называют четвёртым состоянием вещества. В природе плазменное состояние вещества, обусловленное высокими температурами, имеет место внутри солнца и других звёзд. Молния также является примером перехода вещества в плазменное состояние, происходящий под действием сил электрического поля большой величины.
Рисунок 1: Плазма — четвертое состояние вещества |
Для того чтобы создать плазму для технических потребностей, газ либо сильно разогревается с помощью источника тепла, либо подвергается действию сильного электрического поля, так чтобы перевести его в ионизированное состояние.
2.2 Принцип плазменной резки
Плазменная резка – это процесс термической резки, при котором плазменная дуга обжимается, проходя через сопло. Дуга прямого действия, которая возникает, когда электрический ток протекает от неплавящегося электрода (катода) на изделие (анод), используется для резки материалов, обладающих электрической проводимостью. Эта форма плазменной резки является наиболее часто используемой. В случае дуги косвенного действия, она создаётся между электродом и соплом. Даже если используется режущий газ, в состав которого входит кислород, тепловой эффект плазменной дуги преобладает. Таким образом, данный метод не рассматривается как процесс кислородной резки, а скорее как резка путём плавки.
Плазменные газы в дуге частично подвергаются диссоциации и ионизации, что делает их электропроводящими. Благодаря высокой плотности энергии и температуре плазма расширяется и движется по направлению к изделию со скоростью, которая в три раза превышает скорость звука.
Благодаря рекомбинации атомов и молекул на поверхности изделия потреблённая энергия сразу же высвобождается и усиливает тепловой эффект воздействия плазменной дуги на изделие. В плазменной дуге температура доходит до 30 000 К. В сочетании с высокой кинетической энергией плазменного газа такая температура обеспечивает чрезвычайно высокую скорость резки всех материалов, обладающих электрической проводимостью, которая зависит от толщины материала.
Для начала процесса резки в первую очередь зажигается пилотная дуга между соплом и электродом путём подачи высокого напряжения. Эта низкоэнергетическая пилотная дуга подготавливает пространство между плазменным резаком и изделием, вызывая частичную ионизацию. Когда пилотная дуга контактирует с изделием (резка с лёта), благодаря автоматическому увеличению мощности зажигается основная плазменная дуга.
Рисунок 2: Принцип плазменной резки с помощью дуги прямого действия |
Металлический материал плавится и частично испаряется благодаря тепловой энергии дуги и плазменного газа. Расплавленный металл выдувается из реза под действием кинетической энергии плазменного газа. В отличие от кислородной резки, при которой около 70% тепловой энергии вырабатывается благодаря сгоранию железа, в процессе плазменной резки энергия, требующаяся, для того чтобы расплавить материал в резе создаётся только под действием электричества.
Выбор используемого плазменного газа зависит от того, какой материал требуется разрезать. Например, одноатомный газ аргон и/или двухатомные газы, такие как водород, азот, кислород и смеси этих газов, а также очищенный воздух, используются в качестве плазменного газа и режущего газа.
Резаки могут иметь как водяное, так и газовое охлаждение. В зависимости от того, где используются процессы плазменной резки, различают процессы, выполняемые над водой и на ней, а также такие, которые производятся под поверхностью воды.
2.3 Оборудование для плазменной резки
2.3.1 Источник питания для плазменной резки
Источник питания для плазменной резки подаёт рабочее напряжение и ток резки для основной и вспомогательной дуги. Напряжение источника питания для плазменной резки без нагрузки находится в диапазоне между 240 и 400 В. В состав источника питания входит система зажигания пилотной дуги (вспомогательной плазменной дуги), назначение которой состоит в возбуждении основной плазменной дуги. Для того чтобы это выполнить сначала зажигают плазменную дугу косвенного действия, используя импульсы высокого напряжения. Назначение данной дуги состоит в ионизации пространства между соплом и изделием, что позволяет возбудить основную плазменную дугу.
Рисунок 3: Пример установки для плазменной резки |
Источники питания для плазменной резки либо имеют круто падающую кривую вольтамперной характеристики (рис. 6), либо постоянную токовую характеристику (рис. 7), в связи с чем при удлинении дуги мощность резки изменяется незначительно или остаётся неизменной.
Рис.6: Источник питания для плазменной резки с крутоубывающей (крутопадающей характеристикой) кривой напряжения и тока | Рис.7: Источник питания для плазменной резки с постояноой токовой характеристикой (вертикальнок падение) |
2.3.2 Электрод и сопло плазменного резака
Повышение эффективности плазменной резки в большой степени зависит от конструкции плазменного резака. Чем плотнее плазменная дуга обжимается, тем выше скорость резки и качество кромки реза.
Важнейшими деталями плазменного резака являются плазменное сопло и электрод. Как плазменное сопло, так и электрод являются быстроизнашивающимися деталями. Неправильный подбор, либо неверное использование сопла или электрода могут значительно сократить срок их службы и повредить резак.
Срок службы электрода в значительной степени определяется силой тока резки, количеством зажиганий, а также типом используемого плазменного газа. Кроме того, управление газом и мощностью вначале и в конце резки, а также рассеяние тепла от электрода также играет ключевую роль. Обычно используются электроды стержневой формы из вольфрама, а также имеющие форму пальца из циркония или гафния, которые можно сделать заострёнными или плоскими. Ввиду того, что они подвержены эрозии, электроды из вольфрама могут применяться только с инертными плазменными газами и их смесями, а также с газами с низкой реакционной способностью и восстановительными плазменными газами. При использовании чистого кислорода, либо плазменных газов, в состав которых входит кислород, электроды будут служить значительно дольше, если они будут изготовлены из циркония или гафния. Эти материалы естественным образом формируют защитный слой, плавящийся при более высокой температуре (табл. 1), и, к тому же, они заключены в основную оболочку, обладающую очень большой теплопроводностью, которая интенсивно охлаждается. Если в плазменной резке используется кислород, увеличения срока службы электрода можно добиться, подавая два газа: процесс зажигания проводится с использованием газа с низкой окислительной способностью, а сам процесс резки с использованием кислорода.
Ключевые факторы, влияющие на срок службы сопла:
- диаметр на выходе сопла
- масса и теплопроводность материала сопла
- выход (произведение силы тока резания на напряжение резания)
- время действия плазменной дуги
- количество зажиганий
- последовательность прожигания отверстий
- и интенсивность охлаждения.
Водяное охлаждение является более интенсивным. Воздушное охлаждение требует большего количества газа.
Таблица 1: Типовые величины для расходных деталей, применяемых с плазменными резаками
Материал | Усл. | Температура | Используемый | Теплопроводность |
Вольфрам | W | ≈ 3400 | Ar | ≈ 174 |
Оксид вольфрама | WO3 | ≈ 1473 | Ar/H2 | |
Цирконий | Zr | ≈ 1852 | O2 | ≈ 22 |
Оксид циркония | ZrO2 | ≈ 2700 | Воздух | ≈ 2,5 |
Нитрид циркония | ZrN | ≈ 2982 | ||
Гафний | Hf | ≈ 2227 | ||
Оксид гафния | HfO2 | 1700 | O2 | |
Нитрид гафния | HfN | 3305 | Воздух | ≈ 29 |
Медь | Cu | 1083 | ||
Оксид меди | Cu2O | 1235 | Все | ≈ 400 |
Серебро | Ag | 961 | Все | ≈ 429 |
(Источник: информационный листок DVS 2107)
2.
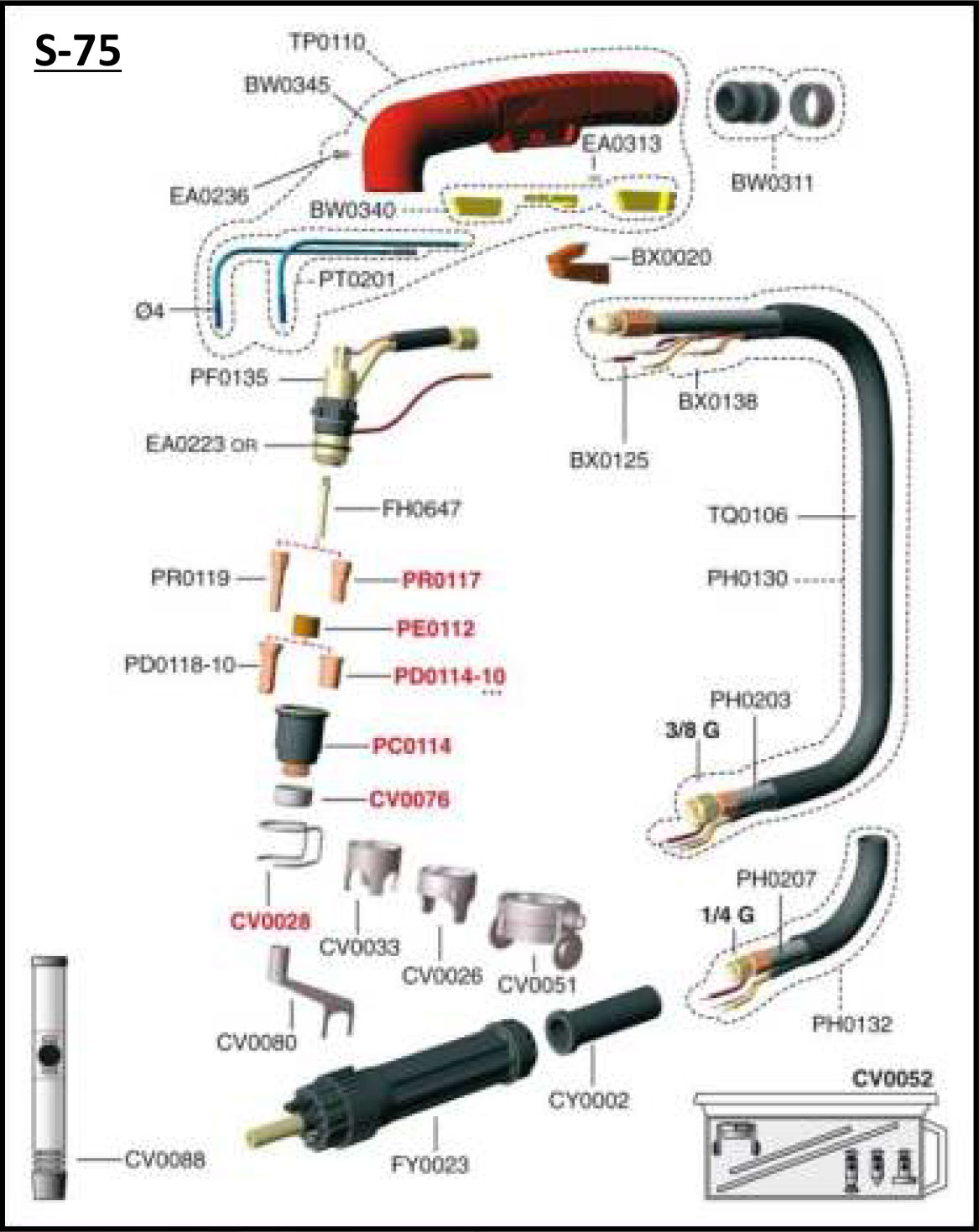
При плазменной резке с помощью плазменной дуги прямого действия разрезаемый материал должен обладать электрической проводимостью, так как изделие является частью электрической цепи. Заземление подсоединённого изделия должно проектироваться таким образом, чтобы обеспечивалось непрерывное прохождение тока.
2.3.4 Подаваемый газ
Системы плазменной резки работают с инертными, восстановительными газами или с газами с низкой реакционной способностью, а также с химически активными газами и их смесями. Подробное описание систем подачи газа и информация по выбору газов, а также рекомендации по качеству применяемого газа приведены в главе 4.
2.3.5 Системы циркуляции охладителя
Поскольку плазменная резка сопряжена с большими тепловыми нагрузками, необходимо эффективное охлаждение. Различают интегрированные и внешние контуры циркуляции водяного охлаждения и газового охлаждения. Резаки, работающие с током около 100 ампер и более, обычно охлаждаются водой.
2.3.6 Система воспроизведения
Требования, относящиеся к точности воспроизведения, а также эксплуатационные характеристики систем воспроизведения устанавливаются стандартом ISO 8206.
2.3.7 Стол для резки и система вытяжки
Столы для плазменной резки служат стабильной основой для расположения металлического листа, который требуется разрезать. Размеры стола зависят от размера, толщины и массы листа металла. Выделения, которые сопровождают процесс резки можно значительно уменьшить, используя плазменный резак в сочетании с вытяжной системой для удаления дыма и пыли, либо с водяным бассейном.
Плазменный резак по металлу: устройство, схема, видео
Плазменный резак — один из элементов станка для плазменной резки металла. Основное его предназначение заключается в образовании плазмы. Также известен под названиями «плазматрон» или «горелка».
Какими же особенностями обладает это устройство, какая схема используется для подключения, а главное, что важно учитывать при покупке и дальнейшем использовании изделия?
Из чего состоит
Плазмотрон состоит из нескольких основных элементов:
- Дуговая камера — пространство, в котором и образуется плазма.
- Сопло — превращающее плазменный поток в дугу нужной толщины.
- Электродержатель.
- Системы газо и водоснабжения.
- Изолятор.
Нередко подобное устройство дополнено специальным узлом завихрения, что позволяет стабилизировать дугу.
Как работает
Принцип работы оборудования достаточного прост. После нажатия кнопки, воздух проходит по определенным каналам, попадает в поток, который закручен по спирали, и под большим давлением выходит из сопла, обеспечивая дугу для идеального раскроя материалов.
Изначально возникает разряд между 2 элементами: электродом и соплом — это происходит за счет образования электрического потенциала. В результате зажигается дежурная дуга, которая необходима для возникновения рабочей. За счет вихревого потока электрическая дуга не касается стенок сопла, что позволяет стабилизировать её.
Тематическое видео: рекомендуем к просмотру.
Виды резаков и особенности выбора
Существует широкий выбор схем и вариантов плазменных резаков, благодаря чему не составит труда подобрать оборудование, которое в полной мере соответствует будущей сфере его использования.
Основные виды:
- для газов, которые содержат кислород;
- для окислительных сред;
- для инертных и восстановительных.
Помимо этого существуют вариации устройства с газожидкостной, водяной и магнитной стабилизацией дуги, но последние два варианта не получили широкого распространения и гораздо менее востребованы, чем иные виды плазматрона.
Стоит учитывать, что плазморез может быть выполнен как на основе инвертора, так и трансформатора.
Второй вариант актуальнее в том случае, если необходимо провести раскрой материалов повышенной толщины. Оборудование же, выполненное из инверторной сварки, отличается экономичностью и простотой использования, что обусловило его широкое распространение.
В зависимости от сферы использования можно выделить еще 2 вида резаков:
- промышленные;
- бытовые.
Они отличаются по мощности и функциональности. Соответственно в домашних условиях будет достаточно ручного аппарата, в то время как для обеспечения максимальной производительности труда, приобретается промышленный вариант.
Прямое и косвенное воздействие
Важно учитывать, что плазменный резак прямого воздействия применяется для работы с различными вариантами металлов, а также сплавами — материалами, которые проводят электроток. Соответственно, в этом случае раскраиваемый лист выступает в качестве одного из элементов цепи.
Если же говорить об изделиях, которые не способны проводить ток, то в данном случае более актуален будет резак косвенного воздействия.
Его конструкция несколько отличается, так как дуга образуется внутри сопла, а обработка проводится за счет струи, которая вырывается из отверстия под большим давлением. Такая схема не часто применяется только в том случае, если требуется проведение работ с неметаллическими изделиями.
Преимущества использования устройства
Плазменно-воздушная резка получила широкое распространение в различных сферах. Она активно применяется и в машиностроении, и на промышленных предприятиях, а также в любых других областях деятельности. Это позволяет значительно повысить производительность труда, а также создавать полностью идентичные элементы.
Что же касается преимуществ именно в пользу использования плазматрона, то стоит выделить следующие особенности:
- Простота использования и эффективность обработки.
- Гладкий срез, который не нуждается в шлифовке и механической зачистке.
- Минимальная область нагрева — идеально точный раскрой, а также отсутствие деформации материала.
- Надежная работа — устройство рассчитано на продолжительный период активной эксплуатации.
А чтобы работа была комфортной и удобной, важно правильно подобрать ручной резак — все зависит от того, в каких условиях и с какими материалами предстоит работать.
Какие параметры стоит учитывать
Выбирая плазморез, необходимо детально изучить особенности и технические характеристики изделия. В зависимости от этого будет зависеть срок работы устройства и его функциональность. При сравнении плазменных резаков, стоит определить, для работы с какими материалами они предназначены.
Предпочтительнее выбрать универсальный вариант, особенно если он предназначен для частого использования. Его стоимость выше, но при этом это выгоднее, покупки нескольких отдельных изделий.
Если же важно добиться идеального качества раскроя, а также безупречного разреза, который не нуждается в зачистках, то стоит определить функции изделия, подбирая его в соответствии с обрабатываемыми материалами. Эта информация указывается в технической документации, либо же пометка может быть выполнена на самом аппарате.
Самостоятельное изготовление ручного оборудования
Можно и вовсе собрать необходимое оборудование из инверторной сварки своими силами. Это достаточно простая задача, с которой легко справиться, приобретя необходимые элементы и используя для их соединения подходящую схему.
При выборе электродов стоит отдать предпочтение гафнию, так как это самый безопасный материала. Качество раскроя зависит и от диаметра, а также длины сопла. Выбор параметров зависит от особенностей изделия — для ручного аппарата оптимальны будут показатели 3 и 7 см соответственно.
При этом важно учитывать, что чем длиннее сопло — тем удобнее с ним работать, но срок его службы в этом случае сокращается. Поэтому столь необходимо придерживаться оптимального баланса. Для работы оборудования потребуется и компрессор. Если речь идет о ручной модели, то в случае используется сжатый воздух. Промышленная аппаратура функционирует на основе различных газов и их смесей (водород, кислород, азот, гелий).
Компрессор необходим для подачи сжатого воздуха — он подключается при помощи специального шланга.
А чтобы соединить все элементы схемы, необходимо использовать кабель-шланговый пакет. Соответственно, создавая плазмотрон из инверторной сварки или же трансформатора, необходимо соединить этот источник с электродом.
Как обеспечить безопасность при работе?
Завершив создание плазмотрона, необходимо провести тщательную проверку. Необходимо еще раз свериться со схемой, убедившись в том, что оборудование исправно. Если рабочая дуга не зажигается или же гаснет спустя непродолжительное время работы, то вероятно аппарат неисправен.
При правильном использовании устройства оно полностью безопасно и может применяться даже в домашних условиях — в быту, особенно в сельскохозяйственной сфере, подобные приборы весьма актуальны. Поэтому очень важно соблюдать аккуратность, а также следовать требованиям безопасности. И в результате получится качественный срез, металл не оплавится, а край не будет деформирован или покрыт окалиной.
Заключение
Ручной плазматрон — удобное в работе изделие, которое отличается практичность и эффективностью обработки. Благодаря его применению удается добиться безукоризненного результата, работая с различными типами материалов, как металлами, проводящими ток, так и с другими типами изделий.
Преимущества и недостатки плазменной резки
Преимущества и недостатки плазменной резки по сравнению с другими методами резки металлов?
Резка металлов – проблема, с которой приходится сталкиваться и в цеху, и на стройплощадке, и в мастерской. Простые решения вроде автогена устроят многих, но не всех. Если объем работ по резке металла большой, а требования к качеству реза высоки, то стоит подумать об использовании аппарата плазменной резки (плазмореза).
Первые установки и аппараты плазменной резки появились более полувека назад, но широкому кругу мастеров они стали доступны только в последние два десятилетия.
ПРЕИМУЩЕСТВА:
Какие преимущества в работе дает аппарат или станок плазменной резки металла в работе?
1. При правильном подборе мощности он позволит в 4-10 раз (по сравнению кислородной горелкой) повысить производительность. По этому параметру плазморез уступит лишь промышленной лазерной установке, зато намного выиграет в себестоимости. Экономически целесообразно использовать плазменную резку на толщинах металла до 50-60мм. Кислородная же резка более предпочтительна при раскрое стальных листов толщиной свыше 50 мм.
2. УНИВЕРСАЛЬНОСТЬ. Плазменная резка позволяет обрабатывать и сталь, и чугун, и алюминий, и медь, и титан, и любой другой металл, причем работы выполняются с использованием одного и того же оборудования: достаточно выбрать оптимальный режим по мощности и выставить необходимое давление воздуха. Важно отметить и то, что качество подготовки поверхности материала особого значения не имеет: ржавчина, краска или грязь помехой не станут.
3. ТОЧНОСТЬ и ВЫСОКОЕ КАЧЕСТВО РЕЗА. Современные плазморезы обеспечивают минимальную ширину реза и “чистые” без наплывов, перекаливания и грата кромки, почти не требующие дополнительной обработки. Немаловажно и то, что зона нагрева обрабатываемого материала намного меньше, чем при использовании автогена, а поскольку термическое воздействие на участке реза минимально, то и тепловые деформации вырезанных деталей незначительны, даже если они небольшой толщины.
4. БЕЗОПАСНОСТЬ, обусловленная отсутствием взрывоопасных газовых баллонов.
5. НИЗКИЙ уровень загрязнения окружающей среды. Касательно экономической стороны вопроса, то совершенно очевидно, что при больших объемах работ плазменная резка выгоднее той же кислородной или, например, механической. В остальных же случаях нужно учитывать не материалы, а трудоемкость использования. Например, сделать фигурный рез в толстом листе недолго и автогеном, но может потребоваться продолжительная шлифовка краев.
НЕДОСТАТКИ:
Ну а теперь поговорим о недостатках. Первый из них – относительно скромная максимально допустимая толщина реза, которая даже у мощных аппаратов редко превышает 80-100 мм. В случае же с кислородной резкой максимально допустимая толщина реза для стали и чугуна может достигать 500 мм.
Следующий недостаток метода – довольно жесткие требования к отклонению от перпендикулярности реза. В зависимости от толщины детали угол отклонения не должен превышать 10-50°. При выходе за эти пределы наблюдается значительное расширение реза и, как одно из следствий, быстрый износ расходных материалов.
Наконец, сложность рабочего оборудования делает практически невозможным одновременное использование двух резаков, подключенных к одному аппарату, что с успехом применяется при резке штучным электродом.
Процесс плазменной резки (принцип работы плазмореза)
Для начала определим, что же есть плазма. В данном случае это нагретый электрической дугой до высокой температуры (порядка 25000 °C) воздух в ионизированном состоянии. Последнее означает, что он утрачивает свойства диэлектрика и приобретает способность проводить электрический ток. В процессе резки плазменный поток становится проводником для тока, расплавляющего металл, и сам же его выдувает.
Для начала определим, что же есть плазма. В данном случае это нагретый электрической дугой до высокой температуры (порядка 25000 °C) воздух в ионизированном состоянии. Последнее означает, что он утрачивает свойства диэлектрика и приобретает способность проводить электрический ток. В процессе резки плазменный поток становится проводником для тока, расплавляющего металл, и сам же его выдувает.
Рабочий орган аппарата называется плазмотрон. Под этим словом подразумевается плазменный резак с кабель-шланговым пакетом, подключаемый к аппарату. Иногда плазмотроном ошибочно называют аппарат плазменной резки целиком. Разновидностей плазмотронов достаточно много. Но наиболее распространены и более всего пригодны для резки металлов плазмотроны постоянного тока прямой полярности. По виду дуги различают плазмотроны прямого и косвенного действия. В первом случае разрезаемое изделие включено в электрическую цепь, и дуговой разряд возникает между металлической деталью и электродом плазматрона. Именно такие плазмотроны применяются в устройствах, предназначенных для обработки металлов, включая и аппараты воздушно-плазменной резки. Плазматроны косвенного действия применяются, в основном, для обработки неэлектропроводных материалов (у них электрическая дуга возникает в самом резаке).
Сопло – важнейший элемент, определяющий возможности плазмотрона. При плазменной резке применяются сопла небольшого (до 3 мм) диаметра и большой (9-12 мм) длины. От размера диаметра сопла плазмотрона зависит количество воздуха, которое способен пропустить плазмотрон, этот параметр необходимо учитывать при подборе компрессора. Это также влияет на ширину реза и охлаждение плазмотрона. Что касается длины, то чем она больше, тем выше качество реза. Однако чрезмерное увеличение этого параметра ведет к снижению надежности работы и быстрому разрушению сопла. Считается, что длина канала должна быть больше диаметра в 1,5-1,8 раза.
Электродом (катодом) внутри плазматрона служит металлический стержень – другие конструкции в недорогих аппаратах не применяются. То же можно сказать и о материале: разновидностей изобилие, но массово используется лишь электрод из гафния.
Теперь пару слов о рабочих газах, используемых при плазменной резке. Их можно разделить на плазмообразующие и защитные (транспортирующие). Для резки в обычных плазменных системах бытового назначения (сила тока дуги – ниже 200 А, максимальная толщина реза – до 50 мм) сжатый воздух применяют и как плазмообразующий, и как защитный газ. При этом достигается удовлетворительное качество реза, хотя и наблюдается некоторое азотирование и окисление обрабатываемой поверхности. В более сложных системах применяются иные газовые смеси, содержащие кислород, азот, водород, гелий, аргон.
Выбор аппарата плазменной резки
Даже самые доступные аппараты плазменной резки сложны и довольно дороги в сравнении, например, со сварочными, поэтому к выбору недешевой техники нужно подходить осознанно. Прежде всего необходимо определиться, как обычно, с целями и задачами.
Первый параметр, без учета которого бесполезно учитывать остальные, – это максимально допустимая толщина реза. Данная величина обычно приводится для углеродистой стали, реже – для нержавеющей, еще реже – для алюминия и очень редко – для меди. Поскольку на максимально допустимую глубину реза сильно влияет теплопроводность материала, то для сплавов на основе меди этот показатель примерно на 30% ниже, чем для сплавов на основе железа. И если в технических характеристиках аппарата заявлена максимально допустимая толщина реза стали в 10 мм, это будет означать, что максимальная глубина реза медных сплавов составит 7 мм. Таким образом, вторым по важности показателем станет тип сплава, с которым предстоит работать.
Следующий фактор – планируемый режим эксплуатации плазмореза. Как и в случае со сварочными аппаратами, он определяется параметром “ПВ” (продолжительность включения), который определяет отношение времени работы аппарата ко времени, необходимому для его охлаждения. В некоторых промышленных аппаратах плазменной резки ПВ может приближаться к 100%, для ручной же резки металла вполне достаточно 40-50%.
На практике это выглядит следующим образом. Если ПВ плазмореза составляет 50%, то в течение часа эксплуатации он должен 30 минут работать и 30 минут остывать. При ручной резке приходится время от времени перемещаться или перемещать изделие и периодически выключать кнопку поджига на плазмотроне. Это время как раз и идет в зачет охлаждения, и поэтому работа кажется непрерывной. Такая формула дает сбой при работе с толстыми листами металла или при автоматической плазменной резке с ЧПУ, когда время реза может быть значительным. Дело в том, что параметр ПВ определяется для 10-минутного цикла, поэтому в начале смены, пока аппарат холодный, он будет отработать без перерыва и 15 минут даже при низком ПВ, а вот при цикличной работе может отключиться и после 5 минут непрерывной резки.
Когда ключевые параметры, определяющие принципиальную возможность использования аппарата, определены, следует уделить внимание такому аспекту, как удобство использования. Тут первостепенное значение приобретает мобильность, точнее, радиус действия, на который можно свободно удаляться от малоподвижного аппарата, “прикованного” к своему месту компрессором. Так, длина кабель-шлангового пакета плазмотрона может варьироваться до десятков метров. Кстати, важна не только длина: некоторые производители заявляют ее на уровне 30 м и более, но “забывают” сообщить о том, имеются ли евроразъемы на плазмотроне и источнике. Если таких разъемов нет, то укоротить или удлинить плазмотрон вряд ли получится, и всякий раз разматывать его для того, чтобы резать небольшие по размерам листы, будет утомительно. Главный же минус длинного плазматрона не в этом, а в том (и производители об этом, как правило, тоже умалчивают!), что при его длине свыше 20 метров наблюдается потеря мощности, причем довольно ощутимая. Поэтому разумнее всего выбирать плазмотрон небольшой (6-12 м) длины, оснащенный евроразъемом, чтобы при необходимости была возможность удлинить конструкцию, используя быстронаращиванмый удлинитель плазмотрона. Это будет, кстати, удобно и при работе на открытом воздухе в неблагоприятных условиях, когда выносить из помещения аппарат нежелательно. Однако, как уже отмечалось, использовать удлинитель нужно лишь в случае действительной необходимости.
Очень важный вопрос – проблема расходных материалов: электродов (катодов) и сопел. Важно, чтобы они были доступны и недороги. Как правило, износ этих деталей происходит или одновременно или с небольшим “разбросом” (один катод на два сопла). Одного сопла в среднем хватает на целую рабочую смену (при работе с деталями, толщиной до 10 мм).
Момент, не относящийся напрямую к плазматрону, но требующий обязательного учета, – это система подачи воздуха. Если отбросить самые маломощные модели, оборудованные встроенным компрессором и воспринимаемые многими профессионалами как малополезные игрушки, то следует помнить, что для работы плазматрону нужен мощный компрессор. И не он один: при достаточно большом расходе воздуха (100-250 л/мин при 0,4-0,6 МПа) жесткие требования предъявляются и к его качеству, а значит не обойтись без вспомогательных устройств – таких как влаго- и маслоотделители, фильтры. Поступать в аппарат воздух должен равномерно, без пульсаций, поскольку они серьезно влияют на стойкость сопел и электродов, на стабильность поджига дуги и, как следствие, на качество реза, а значит, нужен объемный ресивер.
ПРЕДЛОЖЕНИЕ ДЛЯ ЛЮБИТЕЛЯ
Среди современных устройств плазменной резки можно выделить отдельную и наиболее интересную для рядового потребителя категорию – переносные инверторные источники плазмы, применяемые при ручной резке. Их основные достоинства: низкое энергопотребление, компактность, небольшой вес, эргономичный дизайн. Недостатки: ограничение по максимальной мощности (не более 70 А), и, как следствие, по максимальной толщине реза (до 15-20 мм). Также придется мириться с невысокой продолжительностью включения и чувствительностью к перепадам напряжения. Оборудование, выходящие за рамки этого типа, как правило, рассчитано на промышленное применение.
Большинство аппаратов с плазмотронами воздушного охлаждения пригодны для резки металлических деталей толщиной до 50 мм. Для резки деталей толщиной свыше 50 мм или для увеличения производительности применяют более сложные и дорогие аппараты с плазмотронами водяного охлаждения
Максимальная глубина реза определяет толщину материала, которая может быть разрезана данным аппаратом в принципе. Скорость работы при этом в расчет не берется. Чтобы комфортно и быстро работать с деталями толщиной 3-4 мм, следует выбирать аппарат, максимально допустимая глубина реза которого – 8-10 мм.
Унифицированные разъемы для плазмотронов производятся в соответствии с европейскими стандартами и состоят из розеток (со стороны источника плазмы) и вилок (со стороны резака). Преимущество подобной системы заключается в возможности при необходимости удлинить или укоротить конструкцию без ощутимой потери мощности, прочности и электрического контакта.
Износ сопла заключается в нарушении его геометрической формы, что негативно влияет на качество реза. Износ же катода приводит к выработке стержня (допустимая глубина выработки – не более 1,5 мм), в результате чего может произойти пригорание катода к головке плазмотрона и его (плазмотрона) перегрев.
При минусовых температурах необходимо соблюдать определенные меры предосторожности. Поскольку в ресивере и шлангах образуется конденсат, который в случае замерзания может вывести из строя оборудование, то после окончания работ шланги обязательно продувают, а сам компрессор хранят в помещении с плюсовой температурой.
Принцип работы плазмореза, для чего он нужен и как работает – что такое воздушно-плазменная резка металла, ширина реза, скорость и устройство резака, область применения, основы на фото и видео, как выбрать аппарат
05ДекСодержание статьи
- Что это за метод
- Разновидности плазморезов
- Виды и принцип плазменных резаков
- Устройство плазменной резки
- Схема работы плазмореза
- Особенности технологии
- Виды и технологии плазменной резк
- Как выбрать плазменный резак
- Трансформаторные и инверторные аппараты
- Как работает аппарат водно-плазменной резки в отличие от воздушной
- Контактный и бесконтактный плазморез: для чего нужен и как он работает
- Параметры резака
- Оборудование своими руками
- Типы плазмотронов
- Как работает плазменная резка металла автомат
- Какие газы используются
- Преимущества и недостатки
- Возможности
В области металлообработки имеет весомое значение плазморез, о нем мы и расскажем: что это такое – воздушно плазменная резка металла, принцип работы, дополнительно покажем видео и фото.
Что это за метод
Его отличие в скорости разреза. Если классическое пламя, основанное на пропане и кислороде, с невысокой температурой горения. Указанный способ работает по принципу усиления электродуги под высоким давлением. В результате тепло не успевает распределиться по всей заготовке, а она – деформироваться.
Особенность – дуга плазмотрона является не только резаком. Она позволяет и производить сварочные работы, если будет использована присадочная проволока.
Разновидности плазморезов
Особенность разных типов – в способе розжига дуги и ее поддержания. В классическом варианте она образуется между соплом и деталью. Но если материал не имеет способности проводить ток, то ионизированная электродуга возникает между катодом и анодом и держится на постоянной основе. Отдельно стоят приспособления, использующие пар от жидкости (она находится в резервуаре), который усиливает давление и заменяет эффект ионизирующего вещества.
Виды и принцип плазменных резаков
В основном выбор зависит от сферы использования – какие металлы предстоит разрезать, ширина заготовок, требования к срезу, теплопроводность материала и прочие параметры. Разновидности:
- Инструменты, которые работают в среде инертных газов, – они являются восстановителями.
- Дополняются окислительными парами и насыщены кислородом.
- Технологии, работающие на основании смесей.
- Работа происходит в среде газожидкостных веществ.
- Водная или магнитная стабилизация – редко используется.
Из вышеперечисленных приборов самой распространенной основой являются инертные газы, например, аргон, водород, азот, гелий. В зависимости от толщины металла используют аппараты на инверторе или трансформаторе. Также они различаются по наличию контакта между резаком и заготовкой или по бесконтактному способу.
Исходя из мощности и предназначения, есть бытовые устройства и промышленные. Первые работают от стандартной сети с напряжением в 220 В, а вторые подключаются к 380 В.
Устройство плазменной резки
Уже в названии понятно, что главный элемент, оказывающий воздействие, – это плазма, которая состоит из ионизированного газа под давлением с высокой электропроводностью. Чем выше температура, тем сильнее проводимость, а значит, и скорость процедуры. Конструктивно прибор состоит из нескольких частей, как показано на схеме:
Источник электропитания
Энергию может подавать трансформатор или инвертор. Первый очень надежный, фактически нечувствительный к перепадам тока, а также может применяться по отношению к толстым металлическим брускам до 80 мм. К минусам можно отнести увеличенный вес и большую стоимость, не очень высокий КПД, поэтому прибор сложно назвать экономным. Обычно применяется на производстве при необходимости металлообработки крупных заготовок.
Инвертор имеет лишь один относительный минус – им нельзя резать материал более 40 мм в ширину. Зато есть масса плюсов:
- стабильное горение электродуги;
- высокая эффективность, на 30% больше экономии;
- легкость;
- компактность и мобильность.
Что такое плазменный резак или плазмотрон
Это основной узел, инструмент, с помощью которого через сопло подается плазма. От диаметра и длины отверстия зависит поток и, как результат, качество среза. Внутри находится электрод, он изготавливается из редких материалов с очень высокой прочностью и температурой плавления – бериллий, гафний или цирконий. Они при нагреве создают тугоплавкий оксид, который защищает целостность режущей кромки. Также есть охладитель с подачей воздуха и колпачок. Подробнее на схеме:
Компрессор
От этого элемента зависит то, как работает плазменный резак, – равномерно или с перебоями. В компрессионном устройстве содержится воздух, который подается в определенном объеме тангенциальной или вихревой струей. Если это не будет сделано, возможен нестабильный розжиг дуги, образование двух электродуг одновременно или полный выход плазмотрона из строя.
Схема работы плазмореза
Инженер нажимает на кнопку запуска, включается подача электричества, автоматически зажигается первая пробная дуга. Она еще не имеет достаточную температуру для соединения. Затем воздух начинает поступать на сопло через компрессор в сжатом виде, ионизироваться, становясь проводником электроэнергии, что в обычных условиях без ионной обработки противоестественно для кислорода.
Через узкое отверстие сопла начинает выходить поток плазмы. Нагрев газа увеличивается до 30 тысяч градусов, поэтому луч начинает проводить электричество также хорошо, как и металл. При соприкосновении дуги с заготовкой происходит разрез, который моментально обдувается для охлаждения.
Принцип работы плазмореза и скорость плазменной резки
Когда термообработанный кислород обогащается ионами и выходит через сопло, его ускорение достигает 2-3 тысяч метров в секунду. Этот параметр справедлив при условии узкого отверстия не более 3 мм. При такой быстроте передвижения веществ молекулы еще сильнее разогреваются. Такого жара хватает для плавки даже тугоплавких металлов. Чем меньше эта характеристика у материала, тем быстрее и с меньшими деформациями происходит процесс.
Особенности технологии
- Толщина заготовок – до 220 мм.
- Обрабатываются любые металлические вещества.
- Скорость первичного потока при начальной дуге обычно составляет 800 – 1500 м/с.
- Чем уже сопло, тем больше ускорение потока.
- Проплав очень точный, точечный.
- Область возле разреза остается фактически не нагретой.
Есть два подвида процедуры в зависимости от замыкания проводящего контура.
Как работает резка плазменной струей
Металл не является замыкающим элементом, он находится между двумя сторонами – анодом и катодом. Принцип используется в том случае, когда обрабатываются неметаллы и вещества с низкой электропроводностью, то есть диэлектрики. Плазма образуется между электродом и наконечником, а заготовка просто находится между двумя полюсами.
Плазменно-дуговая резка
Используется, когда нужно разрезать металлическую плашку, которая имеет высокую токопроводимость. Это позволяет разжигать электродугу между проводником и образцом для резки. При этом образуется струя. Плазмообразование происходит при содействии кислорода под высоким давлением и ионизирующего газа.
Обрабатываемая зона резги начинает плавиться и капли выдуваются вниз, образуя отверстие, ровный срез. Применяется постоянный ток прямой полярности.
Виды и технологии плазменной резки
Различают три технологических подхода в зависимости от среды, в которой проходит процедура:
- Воздух или азот в сочетании с электричеством. Самый простой аппарат.
- Два защитных газа, которые оберегают область воспламенения от воздействия окружающих веществ. Благодаря этому, появляется максимально чистая атмосфера – в этом пространстве будет очень ровный срез.
- С водой. Жидкость одновременно имеет две функции – защитную и охлаждающую. Применяется не со всеми металлами, так как некоторые из них вступают в химическую реакцию или быстрее после такой металлообработки окисляются.
Особенность всех трех типов в применении безопасных, пожаробезопасных материалов.
Как выбрать плазменный резак
Основное условие для выбора – назначение. При домашнем использовании удобнее инверторный источник питания. Также важен такой параметр, как сила тока – от нее зависит скорость работы. При выборе пользуйтесь таблицей:
Тип | Сила тока на 1 мм толщины |
Черный | 4 А |
Цветной | 6 А |
Отсюда следует, для распиловки двухмиллиметрового медного листа необходимо подать 12 ампер.
Трансформаторные и инверторные аппараты
При наличии трансформатора вы получите следующие характеристики:
- 100% продолжительность включения. То есть непрерывная работа без потребности делать перерывы.
- Высокое энергопотребление.
- Большая цена.
- Увеличенная ширина разрезаемых заготовок.
Они применяются на производствах. В быту используют инверторы. Они экономичны, имеют малые габариты и массу, поэтому могут иметь ручку для переноса.
Как работает аппарат водно-плазменной резки в отличие от воздушной
Устройство отличается тем, что среда, в которой образуется плазма, – это жидкость. Она является охладителем, а пар – плазмообразователем. Это выгодно, так как одна субстанция заменяет два газовых потока. К достоинствам можно отнести невысокую стоимость и компактность, но есть существенный недостаток – обрабатывать можно только тонкие листы, не более 80 мм. Конструкция значительно облегчается, так как не нужен компрессор или баллон для газа. А резервуар для пара нужен более компактный, ведь он имеет вязкую структуру.
Контактный и бесконтактный плазморез: для чего нужен и как он работает
Эти два способа точное повторение двух типов – с образованием струи (в обход заготовки, когда она имеет низкую электропроводность) и с наличием дуги между электроном и металлов, тогда столб образует контакт.
Параметры резака
Основное различие для мастера – ручной привод или машинный. Первый держит в руках оператор, а второй программируется в станке. Это сложные аппараты, которые в основном применяются при необходимости высокой точности. Ниже о них поговорим подробнее.
Оборудование своими руками
Намного безопаснее купить устройство, тем более что сейчас оно продается по доступной цене. Но умельцам предлагаем посмотреть видео по самостоятельному изготовлению:
Плазморезка ЧПУ: принцип работы в домашних условиях
Еще труднее изготовить аппарат с компьютерным управлением. Обработка происходит намного быстрее, качество детали выше. Мастер из этого ролика справился с самостоятельным изготовлением:
Типы плазмотронов
Различают инструмент по способу стабилизации дуги (подача стабилизатора, воздуха или воды):
- водяной;
- вихревой;
- двойной;
- аксиальный одинарный;
- магнитный.
Как работает плазменная резка металла автомат
Отличие от описанного процесса только в наличии статического стола, динамического сопла, которое передвигается по полозьям и пульта управления. Особенность работы – программа действий задается дистанционно, оператор только включает станок и наблюдает за процедурой.
Какие газы используются
Применяют:
- сжатый воздух;
- кислород;
- азотно-кислородную смесь;
- азот;
- аргоно-водородную смесь.
Преимущества и недостатки
К плюсам можно отнести:
- высокую мощность и производительность;
- экономичность;
- качество и точность.
Минус – небольшая толщина среза, она сильно зависит от силы тока.
Возможности
Используется аппарат во множестве случаев, на предприятиях и в частных целях. Можно обработать как листы, так и трубы, любую конфигурацию металла. Работа происходит и с чистыми веществами, и со сплавами, даже с тугоплавкими. В статье мы рассказали про основы плазменной резки, область применения и максимальную ширину реза при использовании технологии.
Принципы работы и конструкция плазматрона в блоге
Плазмотрон – это устройство, которое подключается к источнику тока, и служит для образования потока плазмы, т.е. режущей плазменной дуги. Часто плазмотрон называют резаком – это стандартизированный термин. Плазменный резак – высокоточное устройство, поэтому для получения максимального качества кромки, резаки производятся на прецизионном оборудовании с очень жесткими допусками.Конструкция плазменного резакаДля защиты плазмотрона от брызг расплавленного металла и металлической пыли в процессе работы, на него надевают защитный экран, который необходимо время от времени снимать, очищать от загрязнений или вовсе менять. В резаках известных мировых производителей, как правило, реализована технология быстрого отключения, которая позволяет легко отсоединять резак для транспортировки или переключения с одного устройства на другое, если в этом возникнет необходимость. Охлаждение таких резаков производится при помощи окружающего воздуха и не требует выполнения специальных действий, регламентирующих порядок охлаждения.
Правила эксплуатации резаков
Особо следует остановиться на общих правилах эксплуатации резаков.
Следует регулярно проверять расходные детали резака на износ, желательно ежедневно. Износ расходных деталей приводит к изменениям качества резки, которое будет выражаться в изменениях характеристик угла скоса и ширины реза (и, как следствие, размер детали будет неверный) и образованием окалины. Обращайте внимание на износ эмиттера – центральной поверхности электрода. Замену электрода следует производить при глубине изъязвления от 1 мм. И помните, что сопло и электрод всегда следует менять в комплекте. В случае если одна деталь изнашивается раньше, чем вторая – необходимо проверить завихритель и/или защитный экран на предмет износа. Так же не рекомендуется наносить на уплотнительные кольца излишнее количество смазки.
Регулярно очищайте защитный экран от загрязнений, а перед началом работы всегда продувайте шланги подачи газа. Помните, что отказ от использования защитного экрана приводит к риску негативного влияния брызг расплавленного металла и металлической пыли на качество работы плазмотрона и даже к его поломке. Кроме очистки защитного экрана, время от времени стоит чистить и сам плазмотрон.
Резы должны начинаться и заканчиваться на разрезаемой заготовке. Если начало и конец резки выполняются за пределами поверхности листа, то срок службы расходных деталей резака значительно сокращается. При этом дуга отводится в сторону, вследствие чего повреждается сопло или защитный экран. Для достижения длительного срока службы расходных деталей резку следует начинать и заканчивать только на поверхности листа. Также рекомендуется программировать траекторию реза таким образом, чтобы дуга шла от одной вырезаемой детали к другой без остановки и зажигания дуги.
Во время резки резак не должен соприкасаться с разрезаемой заготовкой. Соприкосновение может привести к повреждению защитного экрана и сопла, и негативно повлиять на качество резки. Если данные простые правила не соблюдаются, то в результате Вы получаете резы низкого качества и существенное сокращение срока службы расходных деталей. В некоторых случаях резак может быть разрушен или поврежден.
Доступные сегодня на рынке самые технологичные резаки обеспечивают в разы более продолжительный срок службы расходных деталей по сравнению с теми, которые использовались несколько десятилетий назад. Но оператор, выполняющий резку и обслуживающий резак все равно должен следить за состоянием расходных деталей и за параметрами резки.
У производителей с мировым именем, таких как Hypertherm, в системах плазменной резки встроена функция определения окончания срока службы электрода. Данная функция позволяет предотвратить повреждение резака и заготовки, которое может возникнуть в результате автоматического прекращения подачи питания при износе электрода.
Стоит также обратить внимание на резаки DurаmaxTMHyamp, производства Hypertherm. Резаки данного производителя характеризуются высокой ударопрочностью и термостойкостью. К тому же за счет простоты конструкции, точности изготовления и высокого качества расходных деталей сокращается время на обслуживание, что в свою очередь повышает время бесперебойной работы. При резке с использованием электродов LongLife® от Hypertherm производится автоматическое повышение потока газа и протекание тока в начале резки и сокращение потока газа и протекания тока в конце, при этом эрозия эмиттера сводится к минимуму. Повышение срока службы комплектующих и резака в целом, в итоге приводит к сокращению затрат на производство вырезаемых деталей и заготовок.
Будьте бдительны и не подвергайте риску свое оборудование и здоровье своих работников.
О том как правильно выбрать источник питания для плазменной резки, можно прочитать в предыдущем материале в нашем блоге!Плазменно-дуговая резка – особенности процесса и оборудования
Процесс плазменной дуги всегда рассматривался как альтернатива кислородно-топливному процессу. В этой части серии описываются основы процесса с упором на рабочие характеристики и преимущества многих вариантов процесса.
Щелкните здесь, чтобы увидеть наши последние подкасты по технической инженерии на YouTube .Основы процессов
Процесс плазменной резки показан на Рис.1 . Основной принцип заключается в том, что дуга, возникающая между электродом и деталью, сужается с помощью медного сопла с мелким отверстием. Это увеличивает температуру и скорость плазмы, выходящей из сопла. Температура плазмы превышает 20 000 ° C, а скорость может приближаться к скорости звука. При использовании для резки поток плазменного газа увеличивается, так что глубоко проникающая плазменная струя прорезает материал, а расплавленный материал удаляется в вытекающей плазме.
Процесс отличается от кислородно-топливного процесса тем, что в плазменном процессе используется дуга для плавления металла, тогда как в кислородно-топливном процессе кислород окисляет металл, а тепло от экзотермической реакции плавит металл. Таким образом, в отличие от кислородно-топливного процесса, плазменный процесс может применяться для резки металлов, образующих тугоплавкие оксиды, таких как нержавеющая сталь, алюминий, чугун и сплавы цветных металлов.
Источник питания
Источник питания, необходимый для процесса плазменной дуги, должен иметь падающую характеристику и высокое напряжение.Хотя рабочее напряжение для поддержания плазмы обычно составляет от 50 до 60 В, напряжение холостого хода, необходимое для зажигания дуги, может достигать 400 В постоянного тока.При зажигании пилотная дуга образуется внутри корпуса горелки между электродом и соплом. Для резки дуга должна передаваться на заготовку в так называемом «переносном» режиме дуги. Электрод имеет отрицательную полярность, а деталь – положительную полярность, так что большая часть энергии дуги (примерно две трети) используется для резки.
Состав газа
В традиционной системе с вольфрамовым электродом плазма инертна и образуется с использованием аргона, аргона-H 2 или азота. Однако, как описано в Варианты процесса , можно использовать окисляющие газы, такие как воздух или кислород, но электрод должен быть медным с гафнием.Расход плазменного газа имеет решающее значение и должен быть установлен в соответствии с уровнем тока и диаметром отверстия сопла. Если поток газа слишком мал для текущего уровня или уровень тока слишком высок для диаметра отверстия сопла, дуга гаснет, образуя две последовательные дуги, электрод к соплу и сопло к заготовке.Эффект «двойной дуги» обычно катастрофичен при плавлении сопла.
Качество резки
Качество кромки плазменной резки такое же, как и при кислородно-топливной технологии. Однако, поскольку плазменная резка плавлением, характерной особенностью является более высокая степень плавления по направлению к верхней части металла, что приводит к скруглению верхней кромки, плохой прямоугольности кромки или скосу на кромке реза. Поскольку эти ограничения связаны со степенью сужения дуги, доступны несколько конструкций горелок для улучшения сужения дуги и обеспечения более равномерного нагрева в верхней и нижней части реза.Варианты процесса
Варианты процесса, Рис. 2a – 2e , в основном были разработаны для улучшения качества резки и стабильности дуги, уменьшения шума и дыма или увеличения скорости резки.
Двойной газ
Процесс работает в основном так же, как и в традиционной системе, но вокруг сопла установлен вторичный газовый экран, Рис. 2a . Благоприятные эффекты вторичного газа заключаются в увеличении сужения дуги и более эффективном «удалении» окалины.Плазмообразующий газ обычно представляет собой аргон, аргон-H 2 или азот, а вторичный газ выбирается в соответствии с разрезаемым металлом.
Сталь
воздух, кислород, азот
Нержавеющая сталь
азот, аргон-H 2 , CO 2
- Алюминий
аргон-H 2 , азот / CO 2
Преимущества по сравнению с обычной плазмой:
- Сниженный риск образования двойной дуги
- Более высокая скорость резания
- Уменьшение закругления верхней кромки
Впрыск воды
В качестве плазменного газа обычно используется азот.Вода впрыскивается в плазменную дугу радиально, Рис. 2b , чтобы вызвать большую степень сжатия. Температура также значительно повышается до 30 000 ° C.
Преимущества по сравнению с обычной плазмой:
- Улучшение качества и прямоугольности пропила
- Повышенная скорость резания
- Меньше риска образования двойной дуги
- Уменьшение эрозии сопла
Водяной кожух
Плазма может работать либо с водяным кожухом, Рис.2c , или даже с заготовкой, погруженной на 50-75 мм ниже поверхности воды. По сравнению с обычной плазмой вода действует как барьер, обеспечивая следующие преимущества:
Удаление дыма
- Снижение уровня шума
- Увеличение срока службы сопла
В типичном примере уровней шума при высоких уровнях тока 115 дБ для обычной плазмы водяной кожух был эффективным для снижения уровня шума до 96 дБ и резки под водой до 52–85 дБ.
Поскольку водяной кожух не увеличивает степень сжатия, прямоугольность режущей кромки и скорость резания заметно не улучшаются.
Воздушная плазма
Инертный или инертный плазмообразующий газ (аргон или азот) можно заменить воздухом, но для этого требуется специальный электрод из гафния или циркония, установленный в медном держателе, Рис. 2d . Воздух также может заменить воду для охлаждения горелки. Преимущество воздушно-плазменной горелки в том, что в ней вместо дорогих газов используется воздух.
Следует отметить, что, хотя электрод и сопло являются единственными расходными материалами, электроды с гафниевым наконечником могут быть дорогими по сравнению с вольфрамовыми электродами.
Плазма высокой толерантности
В попытке улучшить качество резки и конкурировать с превосходным качеством резки лазерных систем, доступны системы высокоточной плазменно-дуговой резки (HTPAC), которые работают с сильно сжатой плазмой. Фокусировка плазмы осуществляется за счет закручивания плазмы, генерируемой кислородом, когда она входит в отверстие для плазмы, и вторичный поток газа впрыскивается после плазменного сопла, Рис.2д . В некоторых системах дугу окружает отдельное магнитное поле. Это стабилизирует плазменную струю, поддерживая вращение, вызванное закрученным газом. Преимущества систем HTPAC:
- Качество резки находится между обычной плазменной резкой и лазерной резкой
- Ширина узкого пропила
- Меньше искажений за счет меньшей зоны термического влияния
HTPAC – это механизированная техника, требующая высокоточного высокоскоростного оборудования. Основные недостатки заключаются в том, что максимальная толщина ограничена примерно 6 мм, а скорость резки обычно ниже, чем при обычных плазменных процессах, и составляет примерно 60-80% от скорости лазерной резки.
Эта статья была подготовлена Биллом Лукасом в сотрудничестве с Дерриком Хилтоном, BOC
Плазменная резка – Функции, преимущества и недостатки
Режущие инструменты Плазменная резка – Функции, преимущества и недостатки
Редактор: Steffen Donath
Заготовки из электропроводящих материалов разрезаются с помощью ускоренной струи горячей плазмы. Это эффективный способ резки толстого листового металла.
Связанная компания
Hypertherm также разработала систему резки X-Definition, которая предлагается с системой XPR300. Этот процесс повышает качество и функциональность плазменной резки.(Источник: Hypertherm)
Создаете ли вы произведения искусства или производите готовые детали, плазменная резка предлагает неограниченные возможности для резки алюминия, нержавеющей стали и других материалов. Но что именно стоит за этой относительно новой технологией? Мы проясняем наиболее важные вопросы в нашем кратком обзоре с наиболее важными фактами о плазменных резаках и плазменной резке.
Как работает плазменная резка
Плазменная резка – это процесс, в котором электропроводящих материалов разрезаются посредством ускоренной струи горячей плазмы . Типичными материалами, которые можно разрезать с помощью плазменной горелки, являются сталь, нержавеющая сталь, алюминий, латунь, медь и другие проводящие металлы. Плазменная резка широко применяется в производстве, ремонте и реставрации автомобилей, промышленном строительстве, утилизации и утилизации . Благодаря высокой скорости и точности резки при невысокой стоимости, плазменная резка широко используется как в крупных промышленных приложениях с ЧПУ, так и в небольших хобби-компаниях, где материалы впоследствии используются для сварки.Плазменная резка – Проводящий газ с температурой до 30 000 ° C делает плазменную резку особенной.
Основной процесс при плазменной резке и сварке заключается в создании электрического канала перегретого, электрически ионизированного газа – то есть плазмы – от самого плазменного резака через обрабатываемую заготовку, таким образом формируя готовую схему обратно в плазму. резак через клемму заземления . Это достигается с помощью сжатого газа (кислород, воздух, инертный газ и другие, в зависимости от разрезаемого материала), который на высокой скорости вдувается в заготовку через сфокусированное сопло.Внутри газа дуга образуется между электродом около газового сопла и самой заготовкой . Эта электрическая дуга ионизирует часть газа и создает токопроводящий плазменный канал. Когда ток от резака плазменного резака проходит через эту плазму, он выделяет тепла, достаточного для того, чтобы расплавить заготовку . В то же время большая часть высокоскоростной плазмы и сжатого газа сдувает горячий расплавленный металл, разделяя заготовку.
Плазменная резка – эффективный способ резки тонких и толстых материалов. Ручные резаки обычно могут резать стальной лист толщиной до 38 мм , более мощные резаки с компьютерным управлением могут резать до стальной лист толщиной до 150 мм . Поскольку плазменные резаки производят очень горячий и очень локализованный «конус» для резки, они очень полезны для резки и сварки листов изогнутой или угловой формы.
Преимущества и недостатки плазменной резки
Преимущества:
- работа одной или нескольких горелок в зависимости от серии
- резка всех электропроводящих материалов
- резка высоколегированной стали и алюминиевых материалов средней и большой толщины
- отличная производительность на малых и средних толщина низкоуглеродистой стали
- резка высокопрочной конструкционной стали с меньшим тепловложением
- высокие скорости резания (до 10 раз выше, чем у кислородного топлива)
- любая обработка высококачественных заготовок на средние и толстые листовой металл
- плазменная резка гарантирует автоматизацию
- плазменная резка под водой позволяет очень низкое тепловое воздействие и низкий уровень шума на рабочем месте
Недостатки:
- ограничение использования до 160 мм (180 мм) для сухой резки и 120 мм для подводной резки
- 9 0086 относительно высокое энергопотребление
- лазеры предлагают еще более высокое качество резки
- дороже, чем системы кислородно-ацетиленовой резки
- возможно развитие шума при сухой резке
Применение плазменной резки
Ручные плазменные резаки обычно используются мастерскими для обработки тонкого металла, заводского обслуживания, сельскохозяйственного обслуживания, ремонтных центров сварки, сервисных центров по металлу (лом, сварка и демонтаж), строительных работ (например,грамм. здания и мосты), торговое судостроение, производство прицепов, ремонт автомобилей и произведений искусства (изготовление и сварка).
Резка мягкой стали с Flash 101.
(Источник: Kjellberg)
Механизированные плазменные резаки обычно намного больше, чем ручные плазменные резаки, и используются вместе со столами для резки. Механизированные плазменные резаки могут быть интегрированы в систему вырубки, лазерной или роботизированной резки.Размер механизированного плазменного резака зависит от используемого стола и портала. Этими системами нелегко маневрировать, поэтому перед установкой следует рассмотреть все их компоненты вместе с компоновкой системы.
Между тем производители также предлагают комбинированные устройства, подходящие как для плазменной резки, так и для сварки. В промышленном секторе существует практическое правило: чем сложнее требования к плазменной резке, тем выше затраты.
Когда были разработаны первые плазменные резаки?
Плазменная резка возникла из плазменной сварки 1960-х годов и превратилась в очень продуктивный процесс резки листового металла и листов в 1980-х годах .По сравнению с традиционной резкой «металл против металла» при плазменной резке не образуется металлическая стружка, а обеспечивается точная резка. Первые устройства плазменной резки были большими, медленными и дорогими. Поэтому они в основном использовались для повторения схем раскроя в режиме массового производства. Как и в случае с другими станками, технология CNC (Computer Numerical Control) использовалась в плазменной резке с конца 1980-х по 1990-е годы . Благодаря технологии ЧПУ, плазменные резаки получили большую гибкость при резке различных форм на основе серии различных инструкций, запрограммированных в числовом управлении станка .Однако станки плазменной резки с ЧПУ обычно ограничивались вырезанием шаблонов и деталей из плоских стальных листов только с двумя осями движения.
За последние десять лет производители различных устройств плазменной резки разработали полностью новых моделей с меньшим соплом и более тонкой плазменной дугой . Это обеспечивает лазерную точность на кромках плазменной резки. Некоторые производители комбинируют точный ЧПУ с этими горелками для производства деталей, требующих незначительной доработки или не требующей никакой доработки , что упрощает другие процессы, такие как сварка.
Что такое термическое разделение?
Термин «термическое разделение» используется как общий термин для процессов, в которых материалы разрезаются или формируются под действием тепла с или без резания потока кислорода таким образом, что при дальнейшей обработке не требуется переделка. Тремя доминирующими процессами являются Газокислородная, плазменная и лазерная резка .
Плазменная горелка со скосом.
(Источник: Lind)
Кислородная резка
Когда углеводороды окисляются, они выделяют тепло.Как и в случае с другими процессами сжигания, газокислородная резка не требует дорогостоящего оборудования, источник энергии легко транспортировать, и для большинства процессов не требуется ни электричества, ни охлаждающей воды. Обычно достаточно горелки и баллона с топливным газом. Газокислородная резка является преобладающим процессом резки тяжелой, нелегированной и низколегированной стали , а также используется для подготовки материала к последующей сварке . После того, как собственное пламя довело материал до температуры воспламенения, включается струя кислорода, которая вызывает горение материала.Как быстро достигается температура возгорания, зависит от топливного газа. Скорость правильной резки зависит от чистоты кислорода и скорости струи газообразного кислорода. Кислород высокой чистоты, оптимизированная конструкция сопла и правильный топливный газ гарантируют высокую производительность и минимизируют общие производственные затраты.
Плазменная резка
Плазменная резка была разработана в 1950-х годах для резки металлов, которые нельзя обжигать (например, нержавеющих сталей, алюминия и меди). При плазменной резке газ в сопле ионизируется и фокусируется благодаря специальной конструкции сопла.Только с помощью этого потока горячей плазмы можно резать такие материалы, как пластмассы (без перенесенной дуги). В случае металлических материалов плазменная резка также зажигает дугу между электродом и заготовкой для увеличения передачи энергии. Очень узкое отверстие сопла фокусирует дугу и плазменный ток. Дополнительную перевязку разрядного тракта можно обеспечить вторичным газом (защитным газом). Выбор правильной комбинации плазма / защитный газ может значительно снизить общие производственные затраты.
Лазерная резка
Система Autorex от Esab – первый шаг к автоматизации плазменной резки. Его можно легко интегрировать в существующие производственные линии.
(Источник: Esab Cutting Systems)
Лазерная резка – это новейшая технология термической резки, которая была разработана после плазменной резки. Лазерный луч генерируется в резонаторной полости системы лазерной резки . Хотя расход газа в резонаторе невелик, его чистота и правильный состав имеют решающее значение.Специальные газы для резонатора защищают устройства от цилиндра в полость резонатора и оптимизируют производительность резки. Для резки и сварки лазерный луч направляется от резонатора к режущей головке через систему пути луча . Убедитесь, что в системе нет растворителей, частиц и паров. Особенно для высокопроизводительных систем (> 4 кВт) рекомендуется азот из жидкого источника. При лазерной резке кислород или азот могут использоваться в качестве режущего газа. Кислород используется для нелегированной и низколегированной стали , хотя процесс аналогичен газокислородной резке.Здесь также важную роль играет чистота кислорода. Азот используется для нержавеющей стали, алюминия и никелевых сплавов для достижения чистой кромки и сохранения критических свойств основного материала.
Впрыск воды для плазменной резки и сварки
Вода используется в качестве охлаждающей жидкости во многих промышленных процессах, вызывающих высокие температуры процесса. То же самое и с впрыском воды при плазменной резке. Вода впрыскивается через инжектор в плазменную дугу аппарата плазменной резки.Плазменная дуга обычно возникает, когда в качестве плазменного газа используется азот, как в случае с большинством аппаратов плазменной резки. Как только вода впрыскивается в плазменную дугу , это приводит к высокому сужению . В этом особом процессе температура значительно повышается до 30 000 ° C и выше . Если сравнить упомянутые выше преимущества процесса с традиционной плазмой, можно увидеть, что качество резки и прямоугольность реза значительно улучшаются , и материалы идеально подготовлены для сварки.Помимо улучшения качества резки при плазменной резке, можно также наблюдать увеличение скорости резки , снижение риска двойной кривизны и уменьшение эрозии сопла .
Плазменная резка с усиленным эффектом сужения
Вихревой газ часто используется в индустрии плазменной резки для достижения лучшего удержания плазменного столба и более стабильной дуги перегиба. По мере увеличения количества вихрей входящего газа центробежная сила перемещает точку максимального давления к краю камеры повышенного давления, а точку минимального давления намного ближе к оси.Разница между максимальным и минимальным давлением увеличивается с увеличением количества завихрений. Большой перепад давления в радиальном направлении сужает дугу и приводит к высокой плотности тока и омному нагреву вблизи оси.
Это приводит к гораздо более высокой температуре возле катода . Следует отметить, что закручивающий газ ускоряет эрозию катода по двум причинам: Повышение давления в камере и изменение структуры потока около катода .Также следует учитывать, что газ с большим числом завихрений увеличивает составляющую скорости закрутки в точке резания в соответствии с сохранением углового момента. Предполагается, что это вызывает разные углы у левой и правой кромок пропила.
А теперь ваша очередь!
Оставьте отзыв об этой статье. Какие вопросы остаются открытыми, какие аспекты вас интересуют? Ваши комментарии помогут нам стать лучше!
(ID: 45939723)
Как выбрать ручной плазменный резак и использовать его [Руководство]
Преимущества плазменной резки
Часто бывает достаточно одного разреза.Производители, подрядчики, обслуживающий персонал, художники и мастера, которые испытывают на себе преимущества ручного станка для плазменной резки, редко хотят возвращаться к кислородно-ацетиленовой резке или механическим процессам резки, таким как пилы, отрезные круги, ножницы и ножницы.
Плазменная резка может повысить производительность и снизить стоимость резки. Преимущества плазменной резки:
- Более быстрая резка
- Цикл предварительного нагрева не требуется
- Режет любой металл, проводящий электричество (в отличие от газокислородного топлива, который не режет нержавеющую сталь или алюминий).
- Предлагает мобильность на рабочих местах
- Минимизирует зону термического влияния и обеспечивает резку с небольшим пропилом (шириной пропила). Плазменные аппараты
- также могут выполнять строжку, протыкание, фаску, вырезание отверстий и обводку форм.
Фактический процесс эксплуатации ручного аппарата воздушно-плазменной резки относительно прост. Фактически, самое сложное – это выбрать машину, которая лучше всего подходит для вашего применения, и правильные аксессуары, прежде чем зажечь дугу.
Что такое плазменная резка?
Плазма выглядит и ведет себя как высокотемпературный газ, но с одним важным отличием: она проводит электричество и режет любой электропроводящий металл.
Плазменная дуга возникает в результате электрического нагрева газа, обычно воздуха, до очень высокой температуры. Это ионизирует его атомы и позволяет им проводить электричество. В плазменной дуговой горелке используется вихревое кольцо, которое раскручивает газ вокруг электрода. Газ нагревается в камере между электродом и наконечником горелки, ионизируя газ и создавая плазму. Это приводит к значительному расширению плазменного газа в объеме и давлении. Небольшое узкое отверстие наконечника резака сжимает плазму и ускоряет ее по направлению к заготовке на высоких скоростях (20 000 футов в секунду) и температурах (до 30 000 градусов по Фаренгейту).
Плазменная струя высокой интенсивности плавит очень ограниченную область. Сила струи (или дуги) проталкивает заготовку и удаляет расплавленный металл. Эта дуга легко прорезает металлы с плохой теплопроводностью (нержавеющая сталь) или отличной проводимостью (алюминий).
По сравнению с плазменной резкой пламя, создаваемое газокислородной горелкой, недостаточно концентрируется и плохо режет нержавеющую сталь и алюминий. Плазменная резка считается стандартным процессом для этих металлов.
Выбор плазменного резака
При покупке аппарата плазменной резки следует учитывать несколько факторов.
Толщина материала
Толщина металла, который вы будете резать регулярно, и максимальная толщина металла важны при выборе правильного плазменного резака. Как и источник сварочного тока, мощность плазменного резака и допустимое напряжение определяют его размер. Плазменный процесс требует относительно высокого напряжения и низкого уровня силы тока, в отличие от сварки.Многие ошибочно судят о плазменной машине исключительно по силе тока. Хотя это важный показатель, помните, что общая выходная мощность (в ваттах) равна силе тока, умноженной на напряжение. Выполните математические вычисления, чтобы получить более точное сравнение продуктов. Производительность плазменной машины определенного размера сильно различается в зависимости от производителя.
Скорость резания
Зная скорость резания для толщины разрезаемого металла, можно рассчитать производительность, обычно в частях в час.Это помогает гарантировать, что режущая часть операции не станет узким местом. Многие производители предоставляют таблицы скорости резания, которые позволяют сравнивать характеристики скорости резания.
Чтобы определить максимальную номинальную толщину резки низкоуглеродистой стали, следуйте линии от точки 15 дюймов в минуту (дюймов в минуту) на карте резки. Точка, в которой эта линия пересекает кривую резки, определяет максимальную рекомендуемую производственную толщину резки устройства.Примечание: рейтинг основан на 15 IPM, потому что это минимальная скорость, на которой оператор достигает плавного, устойчивого резания при использовании ручного резака. |
Хотя универсального стандарта не существует, Миллер упрощает сравнение, определяя производительность с помощью двух стандартов: номинальной резки и резки.
- Номинальная резка – это толщина металла, при которой оператор может вручную резать низкоуглеродистую сталь со скоростью 15 дюймов в минуту.Это считается минимальной скоростью, при которой оператор обеспечивает плавный, устойчивый рез и наилучшее возможное качество резки.
Расчетная резка |
- A sever cut Рейтинг означает, что оператор доводит машину до максимально возможной толщины (1-1 / 4 дюйма для блока на 55 ампер). Скорость резки будет очень низкой, и резка потребует значительной очистки.К счастью, скорость резки увеличивается по мере того, как материал становится тоньше.
Отрезанный отруб |
Как и скорость резания, толщина реза сильно различается в зависимости от модели.
Первичная мощность
Для плазменной резки требуются два основных элемента – воздух и электричество, поэтому следующий вопрос, который следует задать, – какой тип входной мощности доступен. Некоторые 30-амперные плазменные резаки, такие как Spectrum® 375 X-TREME ™, работают с напряжением 120 или 240 вольт.Если ваша входная цепь имеет 30-амперный прерыватель, вы даже получаете равную режущую способность при обоих напряжениях (с 20-амперным прерывателем режущая способность снижается на 20 процентов). Miller предлагает основное решение для управления питанием, называемое технологией Auto-Line ™, которая позволяет машине принимать входное напряжение от 190 до 630 вольт, одно- или трехфазное, 50 или 60 герц. И даже если основная мощность резко падает и падает, но остается в диапазоне от 190 до 630 вольт, устройства с технологией Auto-Line обеспечивают стабильную, стабильную дугу и полную мощность резки.Если вы работаете в поле и планируете использовать вспомогательную мощность привода двигателя, настоятельно рекомендуем плазменный резак с технологией Auto-Line. В аналогичных устройствах без Auto-Line возникают неустойчивые дуги резания, частые срабатывания выключателя, перегоревшие платы и предрасположенность к преждевременному выходу из строя трансформатора. Эти проблемы обычно возникают из-за того, что после срабатывания плазменного резака возникает такая нагрузка на линию, что уровни напряжения падают ниже рабочего диапазона плазменного резака.
Окружающая среда и подача воздуха
В условиях сильной запыленности и металлической стружки (например, от шлифовки) машины Miller® с технологией Wind Tunnel Technology ™ и Fan-On-Demand ™ обеспечивают лучшую надежность.Благодаря технологии аэродинамической трубы охлаждающий воздух проходит через машину, не обдувая электронные компоненты, поэтому шлифовальная пыль не может оседать на критически важных компонентах. Fan-On-Demand означает, что охлаждающий вентилятор работает только при необходимости, уменьшая количество мусора, попадающего в устройство. Что касается подачи воздуха, большинство производителей ручных плазменных резаков рекомендуют использовать обычный воздух в качестве режущего газа. В мобильных приложениях подрядчики часто выбирают азот в баллонах, потому что он стоит дешевле, чем воздух в баллонах.Некоторые люди считают, что при резке нержавеющей стали азот вызывает немного меньшее окисление, так как он суше, чем сжатый воздух.
Высокочастотные пуски или пуски контактов
Плазменные резакииспользуют либо высокочастотный (ВЧ) пуск, либо технологию контактного пуска для зажигания вспомогательной дуги. Если вы планируете использовать плазменный резак рядом с телефонами, компьютерами, станками с ЧПУ или другим электронным оборудованием, имейте в виду, что HF часто мешает электронному управлению. Чтобы избежать потенциальных проблем с ВЧ, все аппараты плазменной резки Miller имеют конструкцию с контактным пуском, которая не создает помех.Контактный метод запуска также создает видимую вспомогательную дугу, которая помогает лучше расположить резак.
Как работает плазменная резка и что такое плазменная резка
Вы ошеломлены, пытаясь понять, что такое плазменная резка? Мы знаем, что это может показаться действительно сложной областью работы, когда вы впервые на нее смотрите. Даже терминология может показаться странной, например, что такое «вихревое кольцо», когда оно дома?
К счастью, если немного углубиться, все не так сложно, как кажется на первый взгляд.Несмотря на то, что используемая технология очень впечатляющая, а выходные температуры невероятны, практическое применение плазменной резки довольно просто.
Итак, мы составили для вас супер-руководство, в котором есть все, что вам нужно знать о плазменной резке. Он знакомит вас с основами из раздела «Что такое плазма?» а затем проведет вас через все гайки и болты того, как работает плазменная резка, прежде чем завершить некоторые из вопросов, которые часто возникают у людей об этой работе.
Мы обещаем, что к концу все станет ясно, и вы сможете объяснить плазменную резку, как старый человек.
Прежде чем мы сможем поговорить о том, как работает плазменная резка, нам сначала нужно ответить на вопрос: «Что такое плазменная резка?»
Возможно, вы слышали в школе о трех состояниях материи: твердое, жидкое и газообразное. Ну, их больше трех, и плазма – это четвертое состояние материи.
Материя переходит из одного состояния в другое, когда вы добавляете энергию молекулам или атомам материала.Так, если, например, нагреть лед, он тает и превращается в воду.
Тогда, если вы нагреете его еще немного, он станет газом или паром, как мы обычно называем водяной пар. Наконец, если вы нагреете его еще больше, газ разделится на ионы, и в этот момент он будет проводить электричество и считается плазмой.
Проще говоря, плазменные резаки проталкивают электрическую пилотную дугу через узкое отверстие, заполненное газом. Плазменный газ может быть любым кислородом, аргоном, производственным воздухом, азотом и т. Д.
Этот процесс нагревает газ до температуры, достаточной для перехода в плазму, четвертое состояние вещества.
В качестве электрического проводника плазма может затем образовывать цепь с металлом (или другим материалом), который разрезается, и это приводит к тому, что плазменная дуга может прорезать материал.
Ограниченное отверстие называется соплом. Это узкое отверстие проталкивает газ с очень высокой скоростью, а очень высокотемпературный газ, проходящий через сопло на металл, позволяет ему прорезать металл почти так же, как нож проходит через масло.
Пилотная дуга, которая возникает в большинстве высококачественных плазменных резаков, действует между электродом и соплом для ионизации газа до начала переноса дуги.
В меньших моделях плазменного резака вы можете обнаружить, что создание плазмы начинается, когда наконечник резака используется для создания искры путем прикосновения к металлической поверхности, или может использоваться пусковая цепь (высокочастотная конструкция, которая является очень похоже на свечу зажигания в автомобильном двигателе). Стоит отметить, что для работы станков с ЧПУ можно использовать только плазменный резак, использующий пилотную дугу.
Подпишитесь: получите БЕСПЛАТНО 30-страничную таблицу символов сварки в формате PDF с примерами для каждого символа!
Ручной режим
На изображении показан рабочий, режущий металл плазменным резаком. Автор изображения – Jbolles на Flicker.Если вы хотите использовать ручную плазменную систему (машины для плазменной резки 110/220 В), неплохо знать, что, когда система находится в выключенном состоянии, сопло и электрод будут соприкасаться внутри резака.
Как только вы нажимаете на спусковой крючок, вы генерируете постоянный ток от источника питания, который затем проходит через соединение, и в то же время начинает течь плазменный газ.
Затем плазменный газ создает давление внутри сопла до тех пор, пока оно не станет достаточным, чтобы отодвинуть сопло от электрода. Это создает вспомогательную дугу, которая позволяет газу превращаться в плазменную струю.
Как только это происходит, постоянный ток переключается с электрода на сопло и образует путь между электродом и обрабатываемой деталью. Он будет оставаться на месте до тех пор, пока триггер не будет отпущен, после чего он вернется в состояние ВЫКЛ.
Работа с прецизионной плазмой
Видео выше демонстрирует одну из систем прецизионной плазменной резки на примере ESAB.
В прецизионном плазменном резаке дело обстоит иначе. Электрод и сопло отделены друг от друга за счет вихревого кольца. Это кольцо с крошечными вентиляционными отверстиями, которые выталкивают предварительный поток плазменного газа в вихрь.
При включении источника питания он создает до 400 В постоянного тока напряжения холостого хода. Затем в горелку поступает плазменный газ. В этот момент сопло временно подключается к положительному потенциалу источника питания и образует цепь вспомогательной дуги.Электрод, конечно, в этой точке находится под отрицательным потенциалом. Затем консоль дугового запуска создает искру высокой частоты (опять же, как в свече зажигания).
Эта искра позволяет плазменному газу ионизироваться, и он приобретает способность проводить электричество, образуя полную вспомогательную дугу. Как только эта дуга соприкасается с заготовкой, ток смещается, чтобы соединить электрод с разрезаемым металлом. Заготовка всегда лежит на полностью заземленном столе для резки, чтобы во время работы ток не протекал в другом месте.
Это изменяет постоянный ток для получения правильной силы тока, выбранной пользователем плазменного резака, и переключает предварительную подачу газа на оптимальную смесь газа для материала, который вы режете. Затем через сопло подается вторичный газ, защитный газ, чтобы дополнительно сфокусировать плазменную дугу – это обеспечивает сверхчистый рез, который сохраняет углы скоса как можно меньшими и уменьшает пропил.
Компоненты плазменной системы
Система плазменной резки состоит из 5 основных компонентов:
Блок питания
Источник питания – преобразует одно- или трехфазное сетевое напряжение в полезное постоянное напряжение до 400 В постоянного тока.Это гарантирует, что плазменная дуга остается стабильной на протяжении всего процесса дуговой резки.
Консоль зажигания дуги
Консоль зажигания дуги – это простая схема, которая предназначена для подачи переменного напряжения около 5000 В переменного тока с частотой 2 МГц (что является очень высокой частотой) для создания искры, запускающей плазменную дугу.
Газ
Газы – необходим поток газа, и плазменные системы могут использовать практически любой газ, но обычно азот, производственный воздух, кислород, аргон и т. Д. Они могут служить двум целям: 1.для формирования основы плазменной дуги или 2. для экранирования плазмы для улучшения качества резки
Охлаждение
Система охлаждения – плазменные резаки нагреваются настолько, что, если бы в них не было системы охлаждения, сопло или электрод могли загореться, поэтому для постоянного контроля температуры используется система жидкостного охлаждения.
Факел
Плазменный резак – плазменный резак предназначен для правильного выравнивания плазменной дуги и обеспечения эффективной работы системы охлаждения.Расходные материалы для плазменного резака включают сопла, электрод и вихревые кольца.
Материальные аспекты
Плазменным резаком можно резать только электропроводящие предметы. Это связано с тем, что материал является частью цепи плазменной дуги. Если он не электропроводен – цепи и резки нет.
Это означает, что он подходит для большинства металлов, включая:
- Конструкционная сталь, нержавеющая сталь, нелегированная, высоколегированная и низколегированная сталь
- Металлические плакированные пластины
- Алюминий
Вы также можете использовать плазменную резку латуни, чугуна, меди и титана, но температура плавления этих материалов может помешать получению качественной режущей кромки.
Вы можете использовать плазменную резку для резки материала толщиной от 0,5 мм до 180 мм, хотя это зависит от машины плазменной резки и материала.
Процесс плазменно-дуговой резки
Существует множество вариантов процесса плазменной резки, но основные принципы этого процесса остаются неизменными при резке нержавеющей стали, конструкционной стали, легированной стали, меди или любого другого материала или листового металла.
Этот процесс состоит из пяти отдельных этапов:
Intitiation
Запуск вспомогательной дуги – это момент, когда подается команда пуска и в который генерируется начальная дуга, чтобы вызвать приток газа к электроду и вытеснить его через газовое сопло.
Генерация основной дуги
Генерация основной дуги – следующим шагом является зажигание дуги и обеспечение образования электрической дуги между электродом в машине для плазменной резки и самой заготовкой, и в этот момент начинается резка, и в то же время, если два плазменных газа При необходимости защитный газ начнет поступать для оттачивания режущего пламени.
Местное отопление
Локальный нагрев и плавление – затем, когда плазма начинает работать, температура повышается, что вызывает локальный нагрев и плавление заготовки, но это также может вызвать проблемы внутри сопла, и, следовательно, на этом этапе требуется система охлаждения.
Выброс материала
Выброс материала – ослабленный материал из заготовки затем выталкивается из пропила с использованием кинетической энергии, которая передается потоком газа плазменной струи.
Механизм
Движение дуги – затем после выброса материала плазменная дуга перемещается по поверхности материала до завершения процесса резки.
Варианты процесса плазменной резки
Как правило, процесс плазменной резки одинаков во всех вариантах.Тем не менее, каждый вариант резки дает определенное преимущество в зависимости от области применения, в которой он используется для
.Под вариациями понимаются различные способы использования плазмы для резки в зависимости от системы охлаждения, конструкции электродов в плазменной горелке, используемого плазменного газа или последнего типа применяемой плазмы для резки.
Некоторые из доступных опций:
Стандартный
Стандартная / обычная плазменно-дуговая резка – отверстие сопла – единственное, что используется для ограничения плазменной дуги, и вторичная среда не используется (охлаждающая жидкость обычно представляет собой воду или воздух).
Со вторичной средой
Плазменно-дуговая резка с использованием вторичной среды – это когда вторичная среда (то есть другая среда) втягивается в плазменный резак для дальнейшего сжатия плазменной дуги и обеспечения определенных характеристик, которые зависят от области применения, для которой плазменная струя использовал.
С впрыском воды
Плазменно-дуговая резка с впрыском воды – в этой форме плазменной резки вода нагнетается в плазменную дугу, что приводит к значительному повышению температуры через газовое сопло примерно до 30 000 градусов по Цельсию, что может улучшить качество получаемой резки.
Преимущества и недостатки плазменной резки
На изображении показан ручной плазменный резак. Изображение Тима Дриваса в Википедии.К преимуществам плазменной резки можно отнести:
- Это зависит от серии станка для плазменной резки, но часто можно использовать одну или несколько горелок одновременно.
- Вы можете разрезать любой материал, проводящий электричество
- Вы можете легко найти высоколегированную сталь, алюминий и аналогичные материалы средней или большой толщины.
- Вы получаете превосходные характеристики при работе с мелкоуглеродистой и средней сталью любой толщины.
- Вы можете вспахивать высокопрочную конструкционную сталь без нагрева, как при других методах резки.
- Скорость плазменной резки примерно в 10 раз выше, чем газокислородной
- Позволяет эффективно обрабатывать высококачественную заготовку для листового металла большой и средней толщины.
- Плазменная резка идеально подходит для автоматизации процесса резки
- При плазменной резке под водой – очень низкий уровень шума и очень низкое тепловое воздействие
К недостаткам плазменной резки можно отнести:
- Максимальный размер резки по-прежнему ограничен 180 мм при сухой плазменной резке и только 120 мм при работе под водой
- Вы все равно получаете несколько более широкий пропил, чем идеальный
- Потребляемая мощность при плазменной резке высока
- Он не обеспечивает такого же качества резки, как лазерная резка.
- Это намного дороже в эксплуатации, чем кислородно-ацетиленовая система.
- Вы можете обнаружить, что сухая резка шумнее, чем вы предпочитали
Часто задаваемые вопросы (FAQ)
Опасны ли газы плазменной резки?
Хотя технически дым от плазменной резки не опасен – пары от разрезаемого металла опасны.Большинство металлов при сжигании на воздухе образует токсичные отложения, которые нельзя вдыхать, даже оксид железа (ржавчина) при вдыхании может накапливаться в легких и со временем нанести реальный вред вашему здоровью.
Нужна сварочная маска для плазменной резки?
Официально? Нет. При плазменной резке можно просто надеть защитные очки, но мы рекомендуем, чтобы при плазменной резке обязательно надевать как защитные очки, так и сварочную маску. Это дает вашим глазам максимальную защиту независимо от метода резки, с которым вы работаете.
Может ли плазменный резак резать дерево?
Что такое плазменная резка? Это использование плазменной резки для резки материалов, и для того, чтобы это происходило эффективно, необходимо, чтобы разрезаемый материал был электропроводным. Если она не является электропроводной, дуга пропадет – древесина не электропроводна, и плазменный резак не может резать древесину.
Будет ли плазменный резак резать ржавый металл?
Да, потому что ржавчина проводит электричество так же хорошо, как и любой другой металл, поэтому ржавчина совсем не препятствует процессу плазменной резки.Он прорежет грязную, ржавую и даже окрашенную сталь такого же качества, как и нержавеющую сталь.
Опасны ли плазменные резаки?
Да. Тепло, выделяемое при плазменной резке, невероятно интенсивно. Есть риски для ваших глаз (вы всегда должны носить очки с боковым щитком и сварочным шлемом), вашей одежды (вам нужно использовать огнестойкие костюмы) и даже ног и рук (требуются специальные перчатки и обувь).
Даже при всем этом существует риск искр или расплавленного металла, которые могут стать причиной пожара на рабочем месте или на столе для резки.
Насколько толстым может резать плазменный резак?
Это в некоторой степени зависит от машины и материала. Тем не менее, ваш средний ручной плазменный резак с радостью произведет плазменную резку толщиной до 38 мм стали или листа нержавеющей стали.
Однако, если вы используете плазменный резак с компьютерным управлением, он может выполнять плазменную резку толщиной до 180 мм.
Что ждет плазменную резку в будущем?
В настоящее время вы можете использовать высококлассные плазменные резаки, чтобы прокладывать себе путь через невероятные 200 дюймов металлической пластины за одну минуту. При этом они производят 40 000 градусов тепла.
Ничего подобного. Ученые доказали, что вы можете производить плазменную резку с температурой до 10 триллионов градусов. Конечно, маловероятно, что такой режущий плазменный инструмент когда-либо понадобится для резки металла, но он показывает, что в будущем у этой технологии есть огромный потенциал.
Текущая проблема с плазменным резаком – это мусор, который он оставляет после себя, а именно окалина. Это своего рода осадок, который образуется расплавленным металлом, который прилипает к углам металла и существенно ухудшает качество резки.
Качество резки оборудования для лазерной или водной резки, напротив, намного выше, чем при плазменной резке. Это означает, что после завершения резки не требуется никаких отделочных работ.
Если бы вы спросили на некоторых семинарах, «что такое плазменная резка?» они ответят, что это генератор отделочных работ.Они предпочли бы использовать в своей работе оборудование для лазерной резки или оборудование для гидрорезки, но эти станки дороги, обычно недоступны в портативных моделях, и они выполняют работу в 100 раз дольше, чем плазменные резаки.
Итак, долгожданное будущее плазменной резки – это более чистая отделка получаемой резки. Если они смогут справиться с этим, сохранив при этом скорость плазменной резки, как сейчас, они будут непревзойденной силой в мире резки.
Принцип работы станка плазменной резки pdf .
Принцип плазменной резки означает сосредоточить много. Это система резки, использующая тепло, выделяемое дуговым разрядом между материалом режущего объекта и электродом внутри резака. Для резки заготовок ss304 использовался аппарат плазменной резки с автоматическим перемещением горелки. Процесс плазменной резки показан на рис.И материал режущего объекта плавится, чтобы разрезать. Для загрузки металлической пластины желательно больше места, особенно при погрузке вилочным погрузчиком. Эта высокотемпературная плазменная струя плавит материал заготовки. Обычный стол со сборным ящиком или водяным столиком. Так называемая длительность включения составляет 100. Раздел 2 Введение в плазменную резку Основные сведения о плазменной резке.Описать процесс плазменной резки и его применение в торговле трубопроводной арматурой. Определить различные компоненты оборудования для плазменной резки, а также оборудование, необходимое для его использования. Перечислить характеристики и опасности, связанные с плазменной резкой. . Из сопла выдувается плазменная струя высокой температуры и высокой скорости. Тепло дугового разряда превращает рабочий газ в высокотемпературное плазменное состояние.В процессе плазменно-дуговой обработки материал удаляется путем направления высокоскоростной струи ионизированного газа с высокой температурой от 11000 до 28000 ° C на заготовку. Принцип работы плазменной обработки, принципиальная схема, детали процесса pam. Это увеличивает температуру и скорость плазмы, выходящей из сопла. Хотя для КПК это может быть 40, что означает следующее. Температура плазмы превышает 20 000 с и скорость.Основной принцип заключается в том, что дуга, возникающая между электродом и деталью, сужается с помощью медного сопла с мелким отверстием. Плазменная резка – это процесс, при котором разрезают электропроводящие материалы с помощью ускоренной струи горячей плазмы. Типичные материалы, разрезаемые плазменным резаком, включают сталь, нержавеющую сталь, алюминий, латунь и медь, хотя можно разрезать и другие проводящие металлы, а также плазменная резка часто используется в мастерские по ремонту и реставрации автомобилей, промышленное строительство и др.Принцип работы пам. Когда твердое тело нагревается, молекулы начинают более энергично колебаться. Атмосферные условия из рабочей зоны и т. Д. Принцип работы плазменной обработки Принцип плазменной обработки показан на рисунке. В плазменной горелке, известной как пушка или плазмотрон, объем газа, такой как h3 n2 02 и т. Д. Плазма – это состояние вещества, подобное твердой жидкости или газу.Работает 4 минуты плазменной резки и 6 минут нужно, чтобы она остыла. Добавление тепла к материалу заставляет молекулы в нем вибрировать или двигаться быстрее.Разница между принципом работы плазменной резки и плазменной резки с ЧПУ
Газорезку еще называют кислородной резкой, через высокотемпературное пламя локализованное нагревание поверхности железного листа к точка воспламенения (1000 градусов Цельсия), а затем выпустить кислород под высоким давлением при розжиге лист железа сгорания образует надрез.
Плазменный резак с ЧПУ , также известный как электрический резка, через мощность плазмы для преобразования обычного промышленного электричества в высокоэнергетическую плазменную дугу. Энергия плазменной дуги используется для сжигания стали. пластину, в то время как сжатый газ используется для сдува остатков, чтобы сформировать разрез.
Принцип работы системы управления раскройного станка с ЧПУ:
Управление продольным ходом дальнего света системы ЧПУ для газорезательного оборудования с ЧПУ, управление автомобилем с бокового движение резака, сочетание горизонтального и вертикального движения траектории превращаются в горелку, а заготовка вырезается по форме.В то же время ПЛК в системе управления реализует действие и временное управление газом. регулирующий клапан тракта режущего газа. При фактическом использовании числовых управлять газорезательной машиной, чтобы сохранить высоту режущей головки и константа стального листа, он также должен быть оснащен автоматическим устройство регулировки высоты конденсатора.
Программное и аппаратное обеспечение системы управления компоненты: поскольку газорезательная машина с ЧПУ имеет высокую точность управления и требования к скорости резания, шаговый двигатель может использоваться для движения без обратной связи контроль.Функция управления системой управления координируется промышленным машина управления и карта управления движением. Мотор-драйвер управления Система может реализовать привод разделения волны и постоянного тока, улучшить точность движения двигателя и решить проблему нагрева при движении большой крутящий момент ну.
Принцип работы плазменного станка с ЧПУ резак: мощность дуги высокоионизированных газов передается на заготовку, высокая температура плавления и обдува заготовки, образование плазменной дуги раскройные работы.
Сжатый воздух в камеру после Факел разделен на две части, а именно на формирование плазменного газа и вспомогательный газ. Газоплазменная дуговая плавка металла и сопутствующие компоненты Вспомогательное газовое охлаждение и резак выдувал расплавленный металл.
В состав режущей способности входят два части: главная цепь и цепь управления. Электрический принцип включает в себя основные цепь, контактор, трехфазный силовой трансформатор с высоким реактивным сопротивлением утечки, трехфазный мостовой выпрямитель, высокочастотная катушка зажигания дуги и защитный элемент.Высокое реактивное сопротивление утечки приводит к внешним характеристикам блок питания.
В этом разница между пламегасителем и принцип работы плазменной резки с ЧПУ.
Define Plasma – ознакомьтесь с программным обеспечением для плазменной резки и плазменной резки
Компоненты плазменной системы
Базовая система плазменной резки включает следующие компоненты:
- Источник питания – Источник постоянного тока постоянного тока.Напряжение холостого хода обычно находится в диапазоне от 240 до 400 В постоянного тока. Выходной ток (сила тока) и общая мощность источника питания в киловаттах определяют скорость и толщину резки системы. Основная функция источника питания – обеспечение необходимой энергии для поддержания плазменной дуги после ионизации.
- Схема зажигания дуги – В большинстве горелок с жидкостным охлаждением на 130 ампер и выше это схема высокочастотного генератора, которая вырабатывает переменное напряжение от 5000 до 10000 вольт на частоте примерно 2 МГц.Это напряжение создает внутри горелки дугу высокой интенсивности для ионизации газа и образования плазмы. Вместо схемы пуска с высокой частотой, описанной выше, в воздушно-плазменных горелках обычно используется движущийся электрод или технология «обратного пуска» для ионизации газа.
- Горелка – служит держателем расходуемого сопла и электрода и обеспечивает охлаждение (газ или вода) этих деталей. Сопло и электрод сжимают и удерживают плазменную струю.
Программное обеспечение для плазменной резки
Для механизированной резки используется программное обеспечение плазменной резки для программирования станка.В некоторых случаях программное обеспечение ЧПУ можно использовать для программирования отдельных деталей или небольших серий, но большинство производителей и производителей полагаются на программное обеспечение, обычно называемое программным обеспечением для раскроя CAD / CAM, которое предлагает гораздо более широкие функции и возможности.
Некоторые типы программного обеспечения CAD / CAM для раскроя для плазменной резки могут контролировать и автоматически настраивать практически все аспекты операции плазменной резки. Например, Hypertherm ProNest ® поддерживает такие параметры, как ток дуги, напряжение, предварительный поток газа, настройки потока резки, скорости резки, высоты резки, типы прожига, высоты прожига и т. Д.Все это предназначено для упрощения работы оператора станка и повышения производительности.
Другие функции, обычно встречающиеся в программном обеспечении плазменной резки:
- Предотвращение столкновений
- Цепная резка
- Мостовая резка
- Резка общей линии
- Многоголовочная резка
- Разрез скелета
И в некоторых случаях программное обеспечение может помочь в достижении оптимальных результатов, например:
- Повышенное качество отверстий
- Более простая установка фаски
- Более короткое время цикла
Типовые области применения и отрасли
Плазмаиспользуется как в ручных, так и в механизированных системах для резки широкого спектра проводящих материалов, включая низкоуглеродистую сталь, углеродистую сталь, нержавеющую сталь, алюминий, медь, латунь и другие металлы.