Сборка и герметизация микросхем и полупроводниковых приборов
Сборка и герметизация микросхем и полупроводниковых приборов включает в себя 3 основные операции: присоединение кристалла к основанию корпуса, присоединение выводов и защиту кристалла от воздействия внешней среды. От качества сборочных операций зависят стабильность электрических параметров и надёжность конечного изделия. кроме того, выбор метода сборки влияет на суммарную стоимость продукта.
Присоединение кристалла к основанию корпуса
Основными требованиями при присоединении полупроводинкового кристалла к основанию корпуса являются высокая надёжность соединения, механическая прочность и в ряде случаев высокий уровень передачи тепла от кристалла к подложке. Операцию присоединения проводят с помощью пайки или приклеивания.
Клеи для монтажа кристаллов могут быть условно разделены на 2 категории: электропроводящие и диэлектрические. Клеи состоят из связующего вещества клеи и наполнителя. Для обеспечения электро- и теплопроводности в состав клея как правило вводят серебро в виде порошка или хлопьев. Для создания теплопроводящих диэлектрических клеев в качестве наполнителя используют стеклянные или керамические порошки.
Пайка осуществляется с помощью проводящих стеклянных или металлических припоев.
Стеклянные припои – это материалы, состоящие из оксидов металлов. Они обладают хорошей адгезией к широкому спектру керамики, оксидов, полупроводниковых материалов, металлов и характеризуются высокой коррозионной стойкостью.
Пайка металлическими припоями осуществляется с помощью навесок или прокладок припоя заданной формы и размеров (преформ), помещаемых между кристаллом и подложкой. В массовом производстве применяется специализированная паяльная паста для монтажа кристаллов.
Присоединение выводов
Процесс присоединения выводов кристалла к основанию корпуса осуществляется с помощью проволоки, ленты или жёстких выводов в виде шариков или балок.
Проволочный монтаж осуществляется термокомпресионной, электроконтактной или ультразвуковой сваркой с помощью золотой, алюминиевой или медной проволоки/лент.
Беспроволочный монтаж осуществляется в технологии «перевёрнутого кристалла» (Flip-Chip). Жёсткие контакты в виде балок или шариков припоя формируются на кристалле в процессе создания металлизации.
Перед нанесением припоя поверхность кристалла пассивируется. После литографии и травления, контактные площадки кристалла дополнительно металлизируются. Эта операция проводится для создания барьерного слоя, предотвращения окисления и для улучшения смачиваемости и адгезии. После этого формируются выводы.
Балки или шарики припоя формируются методами электролитического или вакуумного напыления, заполнения готовыми микросферами или методом трафаретной печати. Кристалл со сформированными выводами переворачивается и монтируется на подложку.
Защита кристалла от воздействия внешней среды
Характеристики полупроводникового прибора в сильной степени определяются состоянием его поверхности. Внешняя среда оказывает существенное влияние на качество поверхности и, соответственно, на стабильность параметров прибора. данное воздействие изменяется в процессе эксплуатации, поэтому очень важно защитить поверхность прибора для увеличения его надёжности и срока службы.
Защита полупроводникового кристалла от воздействия внешней среды осуществляется на заключительном этапе сборки микросхем и полупроводниковых приборов.
Герметизация может быть осуществлена помощью корпуса или в бескорпусном исполнении.
Корпусная герметизация осуществляется путём присоединения крышки корпуса к его основанию с помощью пайки или сварки. Металлические, метало-стеклянные и керамические корпуса обеспечивают вакуум-плотную герметизацию.
Крышка в зависимости от типа корпуса может быть припаяна с использованием стеклянных припоев, металлических припоев или приклеена с помощью клея. Каждый из этих материалов обладает своими преимуществами и выбирается в зависимости от решаемых задач
Для бескорпусной защиты полупроводниковых кристаллов от внешних воздействий используют пластмассы и специальные заливочные компаунды, которые могут быть мягкими или твёрдыми после полимеризации, в зависимости от задач и применяемых материалов.
Современная промышленность предлагает два варианта заливки кристаллов жидкими компаундами:
- Заливка компаундом средней вязкости (glob-top, Blob-top)
- Создание рамки из высоковязкого компаунда и заливка кристалла компаундом низкой вязкости (Dam-and-Fill).
Основное преимущество жидких компаундов перед другими способами герметизации кристалла заключается в гибкости системы дозирования, которая позволяет использовать одни и те же материалы и оборудование для различных типов и размеров кристаллов.
Практические рекомендации
Выбор клея для монтажа кристаллов
Полимерные клеи различают по типу связующего вещества и по типу материала наполнителя.
Связующий материал
Органические полимеры, используемые в качестве адгезива, могут быть разделены на две основные категории: реактопласты и термопласты. Все они являются органическими материалами, но
существенно отличаются по химическим и физическим свойствам.
В реактопластах при нагреве полимерные цепи необратимо сшиваются в жёсткую трёхмерную сетчатую структуру. Возникающие при этом связи позволяют получать высокую адгезионную способность материала, но при этом ремонтопригодность ограничена.
В термопластичных полимерах не происходит отверждения. Они сохраняют способность к размягчению и расплавлению при нагреве, создавая прочные эластичные связи. Это свойство позволяет использовать термопласты в задачах, где требуется ремонтопригодность. Адгезионная способность термопластичных пластмасс ниже, чем у реактопластов, но в большинстве случаев вполне достаточна.
Третий тип связующего вещества – смесь термопластов и реактопластов, объединяющая в себе
преимущества двух типов материалов. Их полимерная композиция представляет собой взаимопроникающую сеть термопластичных и реактопластичных структур, что позволяет использовать их для создания высокопрочных ремонтопригодных соединений при относительно низких температурах (150
оС – 200оС).Каждая система имеет свои достоинства и недостатки. Одним из ограничений в использовании термопластичных паст является медленное удаление растворителя в процессе оплавления. Раньше для соединения компонентов с использованием термопластичных материалов требовалось провести процесс нанесения пасты (соблюдая плоскостность), сушки для удаления растворителя и только затем установки кристалла на подложку. Такой процесс исключал образование пустот в клеящем материале, но увеличивал стоимость и затруднял использование данной технологии в массовом производстве.
Современные термопластичные пасты обладают способностью очень быстрого испарения растворителя. Это свойство позволяет наносить их методом дозирования, используя стандартное оборудование, и устанавливать кристалл на ещё не высушенную пасту. Далее следует этап быстрого низкотемпературного нагрева, во время которого растворитель удаляется, и после оплавления создаются адгезионные связи.
Долгое время имелись сложности с созданием высоко теплопроводящих клеев на основе термопластов и реактопластов. Данные полимеры не позволяли увеличивать содержание теплопроводящего наполнителя в пасте, поскольку для хорошей адгезии требовался высокий уровень связующего вещества (60-75%). Для сравнения: в неорганических материалах доля связующего вещества могла быть уменьшена до 15-20%. Современные полимерные клеи (Diemat DM4130, DM4030, DM6030) лишены этого недостатка, и содержание теплопроводящего наполнителя достигает 80-90%.
Наполнитель
Основную роль в создании тепло-, электропроводящего адгезива играют тип, форма, размер и количество наполнителя. В качестве наполнителя используется серебро (Ag) как химически стойкий материал с наиболее высоким коэффициентом теплопроводности. Современные пасты содержат в себе
серебро в виде порошка (микросферы) и хлопьев (чешуек). Точный состав, количество и размер частиц экспериментально подбираются каждым производителем и в сильной степени определяют теплопроводящие, электропроводящие и клеящие свойства материалов. В задачах, где требуется диэлектрик с теплопроводящими свойствами, в качестве наполнителя используется керамический порошок.
При выборе электропроводящего клея следует принимать во внимание следующие факторы:
- Тепло-, электропроводность используемого клея или припоя
- Допустимые технологические температуры монтажа
- Температуры последующих технологических операций
- Рабочие температуры микросхемы
- Наличие металлизации соединяемых поверхностей
- Механическая прочность соединения
- Автоматизация процесса монтажа
- Ремонтопригодность
- Стоимость операции монтажа
Кроме того, при выборе адгезива для монтажа следует обращать внимание на модуль упругости полимера, площадь и разность КТР соединяемых компонентов, а также толщину клеевого шва. Чем ниже модуль упругости (чем мягче материал), тем большие площади компонентов и большая разница КТР соединяемых компонентов и более тонкий клеевой шов допустимы. Высокое значение модуля упругости вносит ограничение в минимальную толщину клеевого шва и размеры соединяемых компонентов из-за возможности возникновения больших термомеханических напряжений.
Принимая решение о применении полимерных клеев, необходимо учитывать некоторые технологические особенности этих материалов и соединяемых компонентов, а именно:
- длина кристалла (или компонента) определяет величину нагрузки на клеевой шов после охлаждения системы. Во время пайки кристалл и подложка расширяются в соответствии со своими КТР. Для кристаллов большого размера необходимо использовать мягкие (с низким модулем упругости) адгезивы или согласованные по КТР материалы кристалла/подложки. Если различие КТР слишком велико для данного размера кристалла, соединение может быть нарушено что приведет к отслаиванию кристалла от подложки. Для каждого типа пасты производитель, как правило, даёт рекомендации по максимальным размерам кристалла для определённых значений разницы КТР кристалла/подложки;
- ширина кристалла (или соединяемых компонентов) определяет расстояние, которое проходит растворитель, содержащийся в адгезиве, до того как покинет клеевой шов. Поэтому размер кристалла должен учитываться и для правильного удаления растворителя;
- металлизация кристалла и подложки (или соединяемых компонентов) не обязательна. Обычно полимерные клеи имеют хорошую адгезию ко многим неметаллизированым поверхностям. Поверхности должны быть очищены от органических загрязнений;
- толщина клеевого шва. Для всех адгезива, содержащих тепло- , электропроводящий наполнитель, существует ограничение по минимальной толщине клеевого шва dx (см. рисунок). Слишком тонкий шов не будет иметь достаточно связующего вещества, чтобы покрыть весь наполнитель и сформировать связи с соединяемыми поверхностями. Кроме того, для материалов с высоким модулем упругости толщина шва может ограничиваться различными КТР для соединяемых материалов. Обычно для клеев с низким модулем упругости рекомендуемая минимальная толщина шва составляет 20-50 мкм, для клеев с высоким модулем упругости 50-100 мкм;
- время жизни адгезива до установки компонента. После нанесения адгезива растворитель из пасты начинает постепенно испаряться. Если клей высыхает, то не происходит смачивания и приклеивания соединяемых материалов. Для компонентов малого размера, где отношение площади поверхности к объёму нанесённого клея велико, растворитель испаряется быстро, и время после нанесения до установки компонента необходимо минимизировать. Как правило, время жизни до установки компонента для различных клеев варьируется от десятков минут до нескольких часов;
- время жизни до термического отверждения клея отсчитывается от момента установки компонента до помещения всей системы в печь. При длительной задержке может происходить расслоение и растекание клея, что негативным образом сказывается на адгезии и теплопроводности материала. Чем меньше размер компонента и количество нанесённого клея, тем быстрее он может высохнуть. Время жизни до термического отверждения клея может варьироваться от десятков минут до нескольких часов.
Выбор проволоки, лент
Надёжность проволочного/ленточного соединения в сильной степени зависит от правильного выбора проволоки/ленты. Основными факторами определяющими условия применения того или иного типа проволоки являются:
Тип корпуса. В герметичных корпусах используется только алюминиевая или медная проволока, поскольку золото и алюминий образуют хрупкие интерметаллические соединения при высоких температурах герметизации. Однако для негерметичных корпусов используется только золотая проволока/ лента, поскольку данный тип корпуса не обеспечивает полную изоляцию от влаги, что приводит к коррозии алюминиевой и медной проволоки.
Размеры проволоки/лент (диаметр, ширина, толщина) более тонкие проводники требуются для схем с малыми контактными площадками. С другой стороны, чем выше ток, протекающий через соединение, тем большее сечение проводников необходимо обеспечить
Прочность на разрыв. Проволока/ленты подвергаются внешнему механическому воздействию в течение последующих этапов и в процессе эксплуатации, поэтому, чем выше прочность на разрыв, тем лучше.
Относительное удлинение. Важная характеристика при выборе проволоки. Слишком высокие значения относительного удлинения усложняют контроль формирования петли при создании проволочного соединения.
Выбор метода защиты кристалла
Герметизация микросхем может быть осуществлена помощью корпуса или в бескорпусном исполнении.
При выборе технологии и материалов, которые будут использоваться на этапе герметизации, следует принимать во внимание следующие факторы:
- Необходимый уровень герметичности корпуса
- Допустимые технологические температуры герметизации
- Рабочие температуры микросхемы
- Наличие металлизации соединяемых поверхностей
- Возможность использования флюса и специальной атмосферы монтажа
- Автоматизация процесса герметизации
- Стоимость операции герметизации
ostec-materials.ru
Делаем микросхемы дома — шаги 0 и 1 / Habr
В этой статье я расскажу о начале своей работы над совершенно безбашенной задачей: конечная цель в том, чтобы получить рабочую микросхему по «толстым» нормам (5-10µm) дома. Это не первое апреля и я не сумасшедший, это просто моё хобби.Возникла эта идея не сейчас и неспроста. С детства я хотел быть газосварщиком, и… делать микросхемы. И если по первому пункту мне достаточно быстро удалось сделать дома сварочный аппарат (бутан-водород/кислород), то с микросхемами все никак не складывалось. Долгое время все мысли останавливались на том, что я не знал где можно взять собственно полупроводники необходимой чистоты (и мысли останавливались на ковырянии мощных транзисторов), пока на форуме не подсказали что в принципе, можно и купить пластины. Затем я даже наткнулся на человека, который 20 лет работал над похожей задачей, и в итоге сдался. Пожалуй, тут можно было опустить руки и перестать тратить время на глупые мечты. Но, однажды я увидел ролик чудовищно гениальной женщины – Jeri Ellsworth – она смогла сделать отдельные полевые транзисторы на основе заводских пластин – и тогда я решил, что настало время поплотнее заняться этой проблемой.
В этой статьях я расскажу о своём текущем прогрессе, но не ждите быстрого продолжения – весь процесс может легко занять пару лет.
Шаг 0:
Были скуплены все книги по теме из местных Интернет-магазинов (как раз на 1 полку), повыкачаны из торрентов все доступные сборники оцифрованных книг. Теоретической информации там конечно много, но с практической стороны – многое покрыто мраком. Даже старые техпроцессы в деталях не описаны нигде, и потому придется много пробовать. Также перерыл интернет в поисках местных поставщиков всех потенциально необходимых материалов (собственно кремний, фоторезисты, химия, газы). Пока найти не удалось местную компанию которая может изготавливать асферическую оптику из оптического/кварцевого стекла – но это в ближайший год не станет препятствием.
Шаг 1: Кремний

Далее – куча разбитых пластин для тренировки. Потренировался раскалывать пластину на кусочки (оказалось, что они все с ориентацией кристаллической решетки 111 – раскалываются треугольниками, а не квадратами). Т.к они еще не отполированы – я попробовал и отполировать – провал полный: паста гои кремний не берет, нужна алмазная паста. Если со временем получится полировать, можно будет пробовать делать солнечные батареи (а из монокристаллического кремния они получаются довольно эффективные).
И наконец – кусочки монокристаллического кремния. Те что толстые слева – погрязнее (но достаточно чистые для микросхем), 2 тоненьких справа – сверхчистые, намного выше требований чистоты кремния для обычных микросхем. Само собой, разрезать их дома не выйдет (если конечно не завалялась алмазная дисковая пила) – только разбить. Нужны для того чтобы пробовать осаждать пленки аморфного кремния химическим (PE CVD Sih5) или физическим (испарение в вакууме) путем.
Какие дальше стоят задачи
- В первую очередь – строительство печи на 1200 градусов для маленького образца. Промышленные печи под такую температуру в квартире не поставить, и стоят огого. Потому буду пробовать нагревать образец галогеновыми лампами с рефлекторами.
- Переезд в отдельную квартиру: меня сразу выгонят увидев бородатого мужика в противогазе и резиновых перчатках с кучей подозрительных баночек.
- Далее – необходимая химия и фоторезисты – и можно пробовать делать 1 транзистор по процессу Jeri.
Что я ищу и пока не нахожу
В первую очередь – это информация. Хотелось бы иметь контакты людей, которые работают на производстве – ведь я соберу все грабли, которые технологи собирали последние 50 лет Затем – информация о техпроцессах и главное – библиотеки под толстые техпроцессы – пока мне их не удалось достать, а из отдельных транзисторов особо не по-проектируешь. Ну и наконец, хочу найти разработчика ASIC, который показал бы мне основные шаги разработки (кое-что я думаю что знаю, но много пробелов и я могу ошибаться сильно). По всем этим вопросам приглашаю на форум по этому проекту (English only).
Комментарии / мнения — в студию.
habr.com
Сборка полупроводниковых приборов и интегральных микросхем
Министерство образования Российской Федерации

Кафедра: «Электронное машиностроение».
Сборка полупроводниковых приборов и интегральных микросхем
Выполнил: ст-т гр. ЭПУ – 32
Козачук Виталий Михайлович
Проверил: доцент
Шумарин Виктор Пракофьевич
Саратов 2000 г.
Особенности процесса сборки
Сборка полупроводниковых приборов и интегральных микросхем является наиболее трудоемким и ответственным технологическим этапом в общем цикле их изготовления. От качества сборочных операций в сильной степени зависят стабильность электрических параметров и надежность готовых изделий.
Этап сборки начинается после завершения групповой обработки полупроводниковых пластин по планарной технологии и разделения их на отдельные элементы (кристаллы). Эти кристаллы, могут иметь простейшую (диодную или транзисторную) структуру или включать в себя сложную интегральную микросхему (с большим количеством активных и пассивных элементов) и поступать на сборку дискретных, гибридных или монолитных композиций.
Трудность процесса сборки заключается в том, что каждый класс дискретных приборов и ИМС имеет свои конструктивные особенности, которые требуют вполне определенных сборочных операций и режимов их проведения.
Процесс сборки включает в себя три основные технологические операции: присоединение кристалла к основанию корпуса; присоединение токоведущих выводов к активным и пассивным элементам полупроводникового кристалла к внутренним элементам корпуса; герметизация кристалла от внешней среды.
Присоединение кристалла к основанию корпуса
Присоединение кристалла полупроводникового прибора или ИМС к основанию корпуса проводят с помощью процессов пайки, приплавления с использованием эвтектических сплавов и приклеивания.
Основным требованием к операции присоединения кристалла является создание соединения кристалл основание корпуса, обладающего высокой механической прочностью, хорошей электро и теплопроводностью.
Пайка процесс соединения двух различных деталей без их расплавления с помощью третьего компонента, называемого припоем. Особенностью процесса пайки является то, что припой при образовании паяного соединения находится в жидком состоянии, а соединяемые детали в твердом.
Сущность процесса пайки состоит в следующем. Если между соединяемыми деталями поместить прокладки из припоя и всю композицию нагреть до температуры плавления припоя, то будут иметь место следующие три физических процесса. Сначала расплавленный припой смачивает поверхности соединяемых деталей. Далее в смоченных местах происходят процессы межатомного взаимодействия между припоем и каждым из двух смоченных им материалов. При смачивании возможны два процесса: взаимное растворение смоченного материала и припоя или их взаимная диффузия. После охлаждения нагретой композиции припой переходит в твердое состояние. При этом образуется прочное паяное соединение между исходными материалами и припоем.
Процесс пайки хорошо изучен, он прост и не требует сложного и дорогостоящего оборудования. При серийном выпуске изделий электронной техники припайка полупроводниковых кристаллов к основаниям корпусов производится в конвейерных печах, обладающих высокой производительностью. Пайка проводится в восстановительной (водород) или нейтральной (азот, аргон) среде. В печи загружают многоместные кассеты, в которые предварительно помещают основания корпусов, навески припоя и полупроводниковые кристаллы. При движении конвейерной ленты кассета с соединяемыми деталями последовательно проходит зоны нагрева, постоянной температуры, охлаждения. Скорость движения кассеты и температурный режим задают и регулируют в соответствии с технологическими и конструктивными особенностями конкретного типа полупроводникового прибора или ИМС.
Наряду с конвейерными печами для припайки полупроводникового кристалла к основанию корпуса используют установки, которые имеют одну индивидуальную нагреваемую позицию, на которую устанавливают только одну деталь корпуса (ножку) и один полупроводниковый кристалл. При работе на такой установке оператор с помощью манипулятора устанавливает кристалл на основание корпуса и производит кратковременный нагрев соединяемого узла. В зону нагрева подается инертный газ. Этот способ соединения деталей дает хорошие результаты при условии предварительного облуживания соединяемых поверхностей кристалла и основания корпуса.
Процесс присоединения кристалла пайкой подразделяют на низкотемпературный (до 400°С) и высокотемпературный (выше 400°С). В качестве низкотемпературных припоев используют сплавы на основе свинца и олова с добавками (до 2%) сурьмы или висмута. Добавка сурьмы или висмута в оловянно-свинцовый припой позволяет избежать появления «оловянной чумы» в готовых приборах и ИМС при их эксплуатации и длительном хранении. Высокотемпературные припои изготовляют на основе серебра (ПСр-45, ПСр-72 и др.).
На технологический процесс пайки и качество полученного паяного соединения деталей сильное влияние оказывают чистота соединяемых металлических поверхностей и применяемого припоя, состав атмосферы рабочего процесса и наличие флюсов.
Наиболее широкое применение процесс пайки находит при сборке дискретных полупроводниковых приборов (диодов, транзисторов, тиристоров и Др.). Это объясняется тем, что процесс пайки дает возможность получить хороший электрический и тепловой контакт между кристаллом полупроводника и кристаллодержателем корпуса, причем площадь контактного соединения может быть достаточно большой (для приборов большой мощности).
Особое место процесс пайки занимает при закреплении полупроводникового кристалла большой площади на основании корпуса из меди. В этом случае для снижения термомеханических напряжений, возникающих за счет разницы в температурных коэффициентах расширения полупроводниковых материалов и меди, широко используют молибденовые и молибденовольфрамовые термокомпенсаторы, имеющие площадь, равную площади полупроводникового кристалла, а ТКl—близкий к ТКl полупроводника. Такая сложная многоступенчатая композиция с двумя прослойками из припоя с успехом используется при сборке полупроводниковых приборов средней и большой мощностей.
Дальнейшее развитие процесс пайки получил при сборке интегральных микросхем по технологии «перевернутого кристалла». Эта технология предусматривает предварительное создание на планарной стороне кристалла с ИМС «шариковых выводов» или «контактных выступов», которые представляют собой бугорки из меди, покрытые припоем или оловом. Такой кристалл располагают на поверхности подложки или на основании корпуса так, чтобы бугорки соприкасались с ней в определенных участках. Таким образом, кристалл переворачивается и его планарная сторона посредством бугорков контактирует с поверхностью основания корпуса.
При кратковременном нагреве такой композиции происходит прочное соединение контактных выступов полупроводникового кристалла с основанием корпуса. Следует отметить, что те участки поверхности корпуса, с которыми соприкасаются «выступы», предварительно тоже облуживаются. Поэтому в момент нагрева происходит соединение припоя основания корпуса с припоем контактных выступов.
На рис. 1, а показан вариант присоединения кристалла ИМС, имеющего медные облуженные контактные выступы, к подложке. Такая конструкция выводов не боится растекания припоя по подложке. Наличие высокого грибообразного выступа обеспечивает необходимый зазор между полупроводниковым кристаллом и подложкой при расплавлении припоя. Это позволяет проводить присоединение кристалла к подложке с высокой степенью точности.
На рис. 1, в показан вариант сборки кристаллов, имеющих мягкие столбиковые выводы из припоя на основе оловосвинец.
П

рисоединение такого кристалла к основанию корпуса проводят обычным нагревом без дополнительного давления на кристалл. Припой контактных выступов при нагревании и расплавлении не растекается по поверхности облуженных участков основания корпуса за счет сил поверхностного натяжения. Это, кроме того, обеспечивает определенный зазор между кристаллом и подложкой.
Рассмотренный метод присоединения кристаллов ИМС к основанию корпуса или к какой-либо плате позволяет в значительной степени механизировать и автоматизировать технологический процесс сборки.
Приплавление с использованием эвтектических сплавов. Этот способ присоединения полупроводниковых кристаллов к основанию корпуса основан на образовании расплавленной зоны, в которой происходит растворение поверхностного слоя полупроводникового материала и слоя металла основания корпуса.
В промышленности широкое применение получили два эвтектических сплава: золотокремний (температура плавления 370°С) я золотогерманий (температура плавления 356°С). Процесс эвтектического присоединения кристалла к основанию корпуса имеет две разновидности. Первый вид основан на использовании прокладки из эвтектического сплава, которая располагается между соединяемыми элементами: кристаллом и корпусом. В этом виде соединения поверхность основания корпуса должна иметь золотое покрытие в виде тонкой пленки, а поверхность полупроводникового кристалла может не иметь золотого покрытия (для кремния и германия) или быть покрытой тонким слоем золота (в случае присоединения других полупроводниковых материалов). При нагреве такой композиции до температуры плавления эвтектического сплава между соединяемыми элементами (кристаллоснование корпуса) образуется жидкая зона. В этой жидкой зоне происходит с одной стороны растворение слоя полупроводникового материала кристалла (или слоя золота, нанесенного на поверхность кристалла).
После охлаждения всей системы (основание корпуса эвтектический расплавполупроводниковый кристалл) происходит затвердевание жидкой зоны эвтектического сплава, а на границе полупроводникэвтектический сплав образуется твердый раствор. В результате этого процесса создается механически прочное соединение полупроводникового материала с основанием корпуса.
Второй вид эвтектического присоединения кристалла к основанию корпуса обычно реализуется для кристаллов из кремния или германия. В отличие от первого вида для присоединения кристалла не используется прокладка из эвтектического сплава. В этом случае жидкая зона эвтектического расплава образуется в результате нагрева композиции позолоченное основание корпусакристалл кремния (или германия). Рассмотрим подробнее этот процесс. Если на поверхность основания корпуса, имеющего тонкий слой золотого покрытия, поместить кристалл кремния, не имеющий золотого покрытия, и всю систему нагреть до температуры на 4050°С выше температуры эвтектики золотокремний, то между соединяемыми элементами образуется жидкая фаза эвтектического состава. Так как процесс сплавления слоя золота с кремнием является неравновесным, то количество кремния и золота, растворившихся в жидкой зоне, будет определяться толщиной золотого покрытия, температурой и временем проведения процесса сплавления. При достаточно больших выдержках и постоянной температуре процесс сплавления золота с кремнием приближается к равновесному и характеризуется постоянным объемом жидкой фазы золото-кремний. Наличие большого количества жидкой фазы может привести к вытеканию ее из-под кристалла кремния к его периферии. При затвердевании вытекшая эвтектика приводит к образованию достаточно больших механических напряжений и раковин в структуре кристалла кремния, которые резко снижают прочность сплавной структуры и ухудшают ее электрофизические параметры.
При минимальных значениях времени и температуры сплавление золота с кремнием происходит не равномерно по всей площади соприкосновения кристалла с основанием корпуса, а лишь в ее отдельных точках.
В результате этого уменьшается прочность сплавного соединения, увеличиваются электрическое и тепловое сопротивления контакта и снижается надежность полученной арматуры.
Существенное влияние на процесс эвтектического сплавления оказывает состояние поверхностей исходных соединяемых элементов. Наличие загрязнений на этих поверхностях приводит к ухудшению смачивания контактирующих поверхностей жидкой фазой и неравномерному растворению.
Приклеиваниеэто процесс соединения элементов друг с другом, основанный на клея
mirznanii.com
быстрый старт с нуля / МАСТЕР КИТ corporate blog / Habr
Если вы помните мой предыдущий пост, там было высказано желание разобраться, что и как можно добавить к понравившейся мне модели, чтобы DIY forever. Большое спасибо пользователям UseTi, Phmphx, lomalkin и в особенности n4k4m1sh2, которые поделились интересными идеями на эту тему в комментариях. Понятно, что для поставленных целей нужны два навыка, один из которых — монтаж печатной платы. А значит сегодня мы будем паять, с нуля.С полки детского магазина был взят очередной набор, конкретно этот.
Итак, тестируем «Набор Юного электронщика». Получится ли с его помощью собрать рабочие конструкции с нуля не имея предварительных навыков, как это до того у нас получилось с механической моделью?
В наборе уже есть всё, чтобы быстро совершить сборку:
- паяльник, припой с каналом флюса (очень удобно!) и кусачки
- мультиметр
- две печатных платы с деталями
Т.е. есть что паять, чем паять и, что немаловажно — чем проверить компоненты и уже готовую схему.
Также, в набор входят две брошюры:
1. Методическое пособие, которое содержит общие сведения о приборах, деталях и процессе пайки.
2. Инструкция к сбору двух входящих в набор устройтсв и последующей настройки одного из них.
Брошюры хорошие, но, если вы помните, мне больше понравилась инструкция к роботу, где не было слов — только изображения + пошагово расписана сборка. В инструкции к этому набору пошаговой инструкции нет. В чем-то это и хорошо, потому что если ориентироваться на эти две брошюры, хочешь-не хочешь, придётся сначала всё прочитать и понять, и только затем действовать — то есть, они приучают мыслить системно. Но немного не хватает динамики, и, мне кажется, детям этого тоже может не хватать ещё больше, чем мне. Поэтому если будете собирать нечто подобное, надеюсь, этот пост сильно сэкономит вам время.
Дополнительные инструменты
Чего нет в наборе, но понадобится или может понадобится:
1. Пинцет. Мы взяли маникюрный.
2. Батарейка «Крона» на 9В
3. Крестообразная отвертка — в одной из схем есть клемма. Затянуть в ней провода получится часовой крестообразной отверткой.
4. Приспособление для пайки «третья рука» — вот уж без чего можно обойтись, хотя в инструкции и брошюре она постоянно упоминается. Конечно, с нею было бы удобнее, но если просто собрать все детали на плате, а затем её перевернуть, то обе входящих в набор платы будут относительно устойчивы и паять будет в принципе удобно и без дополнительных приспособлений.
5. Лупа
6. Оловоотсос
7. Очки и респиратор
8. Подставка для паяльника
9. Вентилятор\вытяжка
Из всего этого списка совсем туго придётся только без первых двух пунктов. Подставкой для паяльника у нас в этот раз стал робот из предыдущего поста. Остальное для монтажа двух маленьких плат было бы действительно лишним.
Зато нелишним будет напомнить, что при пайке выделяются пары олова, которые не слишком полезны для здоровья. Собственно пайка двух входящих в комплект схем заняла у меня не более 10 минут и мне не поплохело. Однако небольшой вентилятор, отгоняющий дым в сторону, или хотя бы открытое окно — это стандартная и очень хорошая практика. Кроме того, после пайки нужно вымыть руки. Глаза тоже нужно беречь — отлететь может откушенная кусачками ножка детали или в процессе пайки может отлететь капелька горячего олова (хотя у нас не отлетало). Поэтому надевайте защитные очки. Берегите себя!
Питание
Для начала, всё что нам понадобится — это докупленная отдельно батарейка «Крона». В наборе есть разъем под неё, который, по инструкции, надо впаять в первую схему. Мой совет: не делайте этого, оставьте её так и используйте в обеих схемах — и для тестирования первой, и для настройки второй.
Устройства, которые мы соберём, потребляют какое-то безумное количество мА\час.
Если речь идёт об электрической цепи, то наши ресурсы и то, как мы их быстро потратим, измеряются в А\ч (Ампер в час, mAh). Ёмкость типичной «Кроны» (по паспорту):
625 мА·ч ≈ 0,5 А·ч
Первое устройство, «Хамелеон», потребляет до 200 мА·ч. Поэтому нашей Кроны этой схеме хватит на:
625мАч/200мА = 3,125 часа.
а значит использовать её рекомендуется только для проверки работы схемы. Хорошим выходом будет аккумулятор на 12 вольт и ёмкостью не менее 0,5 А·ч.
мА·ч — это то, как быстро сядет батарейка! =)
Было бы круто иметь возможность припаять на платы один из таких разъёмов, и затем включить в него вот такой лабораторный блок питания. Но ни под один из доступных разъёмов на плате нет подходящих отверстий. Следовательно, подключить блок питания мы пока не можем.
Первый блин комом или сразу troubleshooting
Есть такой анекдот: купил человек самолёт и журнал с описанием «Как делать мёртвую петлю». Следуя инструкции, сел в самолёт, взлетел, начал делать мёртвую петлю — всё получается. Переворачивает страницу, а там: «… выход из мёртвой петли читайте в следующем номере».
Можно много говорить о культуре пайки и о том, что это целое искусство. Одно останется неизменным: если делаешь что-то в первый раз и по книжке, то сначала может не получится. Вот наша первая плата, набор «Хамелеон», вернее то, что из неё получилось. Какие ошибки были допущены?
1. Нарушена технология пайки, как результат — непропаянные контакты, которые лучше выпаять и впаять снова (не перепутав полярность!)
2. Нарушена технология работы: каждая деталь впаивалась по очереди. Ниже вы увидите, насколько выгоднее в этом плане послушать инструкцию и сначала собрать все детали, а потом закрепить их.
Результат: детали красиво стоят в кривь и в кось, а из трех цепочек диодов загорелась в итоге только одна.
Возможное решение: выпаять все детали и впаять заново.
Позитивный момент: можно найти всегда. В данном случае у нас нигде нет «паразитарных перемычек». Правда, удалять их достаточно просто в любом случае: просто провести жалом паяльника и разделить спаявшиеся вместе контакты.
Паять!
Итак, первая схема не получилась у нас из-за нарушения технологии пайки, поэтому сразу обговорим этот простой и на самом деле приятный момент.
В брошюре достаточно наглядно показано и рассказано, как паять, но, к сожалению, мне это не сильно помогло, т. к. там сказано «как надо», а хотелось бы понять саму технику.
Пожалуй, лучшая рекомендация, которую удалось найти, была в этом посте. Приведу её целиком:
Все дело в процессе. Делать надо так:
- Деталь вставляется в плату и должна быть закреплена (у вас не будет второй руки, чтобы держать).
- В одну руку берется паяльник, в другую — проволочка припоя (удобно, если он в специальном диспенсере, как на картинке).
- Припой на паяльник брать НЕ НАДО.
- Касаетесь кончиком паяльника места пайки и греете его. Обычно, это секунды 3-4. (на самом деле 1-2 с. — прим. А.Ч.)
- Затем, не убирая паяльника, второй рукой касаетесь кончиком проволочки припоя с флюсом места пайки. В реальности, в этом месте соприкасаются сразу все три части: элемент пайки и его отверстие на плате, паяльник и припой. Через секунду происходит «пшшшшш», кончик проволочки припоя плавится (и из него вытекает немного флюса) и необходимое его количество переходит на место пайки. После секунды можно убирать паяльник с припоем и подуть.
Дополнительно могу порекомендовать иллюстрированный комикс, переведённый хабрапользователем atarity.
Также, время от времени на жале паяльника образуется нагар и его нужно чистить. Для этого в индустрии используются специальные целлюлозные губки, обязательно смоченные водой. В нашем случае нагар можно снять просто стряхнув его механически — например, тупой стороной ножа.
Пошаговая инструкция
После того как первое устройство было нами несправедливо загублено, появилось понимание того, как выстроить процесс более эффективно. Надеюсь, эта пошаговая инструкция поможет вам так же быстро собрать свой собственный набор.
Итак, у нас есть горсть деталей и мы понятия не имеем что к чему. Берём симпатичный маникюрный пинцет (что было дома) и выбираем из этой груды все резисторы.
Вот так они выглядят. Если внимательно присмотреться, мы увидим что у нас 8 одинаковых, ещё 2 одинаковых и 1 «сам по себе». Присматриваться нужно к полосатой маркировке на корпусе. На плате место для резистора обозначается R (resistor). Первые 8 одинаковых становятся в ряд внизу, как это видно на плате, ещё 2 одинаковых слева вверху и один, который «сам по себе» — собственно, монтируется «сам по себе».
На этом этапе, не упустите возможность поиграть с мультиметром. В брошюре подробно описано, как измерить сопротивление резистора.
Хорошая новость: у резисторов нет полярности. Это значит, что нам не важно, какой стороной мы их посадим на плату. Поэтому, долго не думая, придаём нужную форму контактам, сажаем всех на плату, отрезаем кусачками лишнее. Чтобы было удобно паять, мы положили плату на край небольшой картонной коробки, т. к. если её положить на стол, это не дало бы возможности припаять резисторы немного над платой, как это рекомендуется сделать.
Вот что у нас получится. Всё ещё далеко от идеала, но уже гораздо лучше по сравнению с первым набором! Продолжаем.
Теперь отберём все конденсаторы. На плате места для них обозначаются C (capacitor). Конденсаторы бывают полярные, а бывают неполярные. Это значит, что некоторые конденсаторы, если их посадить на плату «не той стороной» работать не будут и вся цепть работать не будет. Подсказка: желтые конденсаторы неполярны, поэтому просто сажаем их в гнёзда C3 и C4.
Цилиндрические конденсаторы полярны. Как определить полярность? Два способа:
1. До обрезки ножек та, что длиннее — это плюс. Достаточно совместить его с маркировкой «+» в посадочном гнезде конденсатора C1 или C2
2. Синяя полоса на конденсаторе — это «ключ». Она там, где минус. Достаточно разместить её с обратной стороны от маркировки «плюс».
Подсказка: если думать лень, просто посадите полярные конденсаторы как на изображении.
И диоды! Диоды все полярны. Способы определить полярность:
1. Более длинная ножка — плюс.
2. Фаска (скос) на боку основания самого диода. Не очеь удобно, т. к. у прозрачных диодов её не видно почти совсем. Все фаски диодов на данной плате должны оказаться с одной стороны — наружной.
3. Поставьте мультиметр в режим прозвона (значок «wi-fi», а на самом деле — звукового сигнала, на мультиметре), черным проводом (минус) коснитесь короткой ножки, красным (плюс) — длинной. В нашем случае диод загорится. Если поменять полярность — не загорится. Это происходит потому, что диод пропускает ток только в одном направлении.
Если перепутать полярность хотя бы у одного диода, то вся цепочка гореть не будет. Но! Нас эти три способа определения полярности диода не подвели. Последний способ можно ещё раз использовать после монтажа для прозвона цепи и чтобы убедиться, что полярность диодов не нарушена.
У нас осталась только ещё несколько деталей. По часовой стрелке на фото:
Кнопка. Не полярна. Просто поставить и надавить слегка — она закрепится на плате.
Микросхемы: у них есть «ключи» сверху на корпусе. У той, что длиннее, это выемка, которую надо совместить с обозначением на плате. В нашем случае выемка будет смотреть направо, в сторону резисторов. У микросхемы поменьше ключ в виде углубления в левом верхнем углу. Там он и должен оказаться на схеме. Также, эта выемка схематично обозначена на плате, тоже сверху.
Обратите внимание на старые добрые «ламповые» (в смысле — уютные) DIP-микросхемы. Сейчас кроме наборов для творчества их уже мало где встретишь, хотя паять их для меня лично — одно удовольствие, равно как и собирать шестереночные механизмы. В промышленности же на смену традиционным методам, которыми пользовались ещё наши родители и бабушки и дедушки тех, кому предназначается этот набор, пришёл поверхностный монтаж.
Микросхема стабилизатора напряжения. С ней всё просто, перепутать ничего не получится.
Клеммный разъем. Сюда мы будем подключать блок питания. Поэтому важно: у клеммного разъема отверстия под провод должны смотреть наружу платы, иначе их закроет собой близко стоящий конденсатор, и заклепить в клемме провода станет затруднительно (собственно, у нас так и вышло). В случае неправильного размещения клеммного разъема выпаять его без вакуумного оловоотсоса, скорее всего, не получится (у нас не получилось).
Готово! Нам удалось допустить всего одну существенную ошибку при сборке — это расположение клеммного разъема. Но на полярность это не влияет, скорее на удобство эксплуатации.
У нас получилось мини-проверяющее устройство, которое всегда покажет, сколько ещё батарейки осталось. Сейчас мы его настроим на проверку батарейки Крона, которая у нас уже есть и в которой заряд — 9В, пока она не села.
Помните, мы рекомендовали вам не впаивать провода с клеммами для батарейки в первую схему? Если впаяли — выпаяйте, сейчас они нам понадобятся.
Подключаем новую, ещё не севшую батарейку. Соблюдаем полярность (плюсовой разъем клеммы обозначен на плате). Загорелся первый красный светодиод. Схема работает!
Коротко разово нажимаем кнопку. Прибор измеряет напряжение в 9В и запоминает его. Если бы у нас была рядом севшая Крона, можно было бы проверить разность заряда.
Подсказка: быстро разрядить Крону можно при помощи первой схемы если вы её, конечно, правильно собрали. Как мы уже говорили, потребляет она до 200 мА, поэтому разрядит батарейку примерно за три часа.
Собственно, с теми же функциями измерения вольтажа справляется и входящий в набор мультиметр, но делает он это, конечно, не настолько эффектно. При наличии лабораторного блока питания, можно перепрограммировать наше устройство каждый раз под новый вольтаж. То же самое можно сделать, подключая разные батарейки и снова нажимая кнопку «запомнить».
В заключение хочется сказать спасибо тем, кто придумал и создал этот набор. Два дня назад у меня не было ни малейшего понятия о процессе монтажа печатных плат. Сейчас я отличаю резистор от транзистора и могу посадить их на плату, используя ключи, мультиметр и прочие подсказки. Кроме того, одно из устройств мне удалось сразу собрать и запустить в работу! Как всегда, это очень приятно: видеть и держать в руках то, что удалось собрать самостоятельно.
Благодаря этому двухдневному погружению в электронику, мне стало понятно, что ещё я хочу узнать:
1. Как прозванивать смонтированную печатную плату, чтобы найти, где дефект и устранить его, а не перепаивать всю плату целиком (у меня всё ещё есть надежда пересобрать первое устройство!).
2. Как рассчитать энергопотребление схемы и самостоятельно рассчитать, на сколько хватит того или иного заряда аккумулятора?
3. Три показателя, которое мы измерили в процессе сборки при помощи мультиметра — количество вольт в батарейке, сопротивление в омах резисторе, измерение силы тока в амперах. Как они взаимосвязаны и что я могу с этим делать?
4. Как прочитать принципиальную схему устройства и увидеть её на плате? Как совместить п. 3 и п. 4?
Поэтому хочу обратиться к тебе, Хабр. Поделись, пожалуйста, ссылками на статьи и книги по этой теме, которые тебе понравились, которые легко читать, и быстро можно понять.
А также, подскажи, пожалуйста, что бы ты сделал с питанием устройств, клеммами и разъёмами, потому что пока что у меня есть только вариант «два торчащих провода и батарейка Крона».
Надеюсь, этот обзор тоже поможет кому-то «въехать» в нужную тему быстрее и легче. Удачи вам!
habr.com
Сборка СВЧ микросхем
Сборка СВЧ микросхем включает в себя 3 основные операции: присоединение кристалла к основанию корпуса, присоединение выводов и защиту кристалла от воздействия внешней среды. От качества сборочных операций зависят стабильность электрических параметров и надёжность конечного изделия. кроме того, выбор метода сборки влияет на суммарную стоимость продукта.
Присоединение кристалла к основанию корпуса
Основными требованиями при присоединении СВЧ кристалла к основанию корпуса являются высокая надёжность соединения, механическая прочность и высокий уровень передачи тепла от кристалла к подложке. Операцию присоединения проводят с помощью пайки или приклеивания.
Присоединение выводов
Процесс присоединения выводов кристалла к основанию корпуса осуществляется с помощью проволоки, ленты или жёстких выводов в виде шариков или балок.
Проволочный монтаж осуществляется термокомпресионной, электроконтактной или ультразвуковой сваркой с помощью золотой, алюминиевой или медной проволоки/лент.
Защита кристалла от воздействия внешней среды
Характеристики полупроводникового прибора в сильной степени определяются состоянием его поверхности. Внешняя среда оказывает существенное влияние на качество поверхности и, соответственно, на стабильность параметров прибора. Данное воздействие изменяется в процессе эксплуатации, поэтому очень важно защитить поверхность прибора для увеличения его надёжности и срока службы.
Защита полупроводникового кристалла от воздействия внешней среды осуществляется на заключительном этапе сборки микросхем и полупроводниковых приборов.
Герметизация может быть осуществлена помощью корпуса или в бескорпусном исполнении.
Корпусная герметизация осуществляется путём присоединения крышки корпуса к его основанию с помощью пайки или сварки. Металлические, метало-стеклянные и керамические корпуса обеспечивают вакуум-плотную герметизацию.
Крышка в зависимости от типа корпуса может быть припаяна с использованием стеклянных припоев, металлических припоев или приклеена с помощью клея. Каждый из этих материалов обладает своими преимуществами и выбирается в зависимости от решаемых задач
Для бескорпусной защиты полупроводниковых кристаллов от внешних воздействий используют пластмассы и специальные заливочные компаунды, которые могут быть мягкими или твёрдыми после полимеризации, в зависимости от задач и применяемых материалов.
Современная промышленность предлагает два варианта заливки кристаллов жидкими компаундами:
- Заливка компаундом средней вязкости (glob-top, Blob-top)
- Создание рамки из высоковязкого компаунда и заливка кристалла компаундом низкой вязкости (Dam-and-Fill).
Основное преимущество жидких компаундов перед другими способами герметизации кристалла заключается в гибкости системы дозирования, которая позволяет использовать одни и те же материалы и оборудование для различных типов и размеров кристаллов.
Компания Diemat специализируется на разработке и изготовлении инновационных адгезивных и герметизирующих материалов, предназначенных для корпусирования электронных изделий. Эта технологически ориентированная компания выводит на рынок только патентоспособную продукцию. Специалисты компании Diemat разработали широкий спектр уникальных продуктов, не имеющих аналогов на рынке.
Компания Diemat производит уникальные по своим свойствам полимерные клеи и стеклянные припои для монтажа кристаллов и герметизации микросхем.
Компания Namics занимается разработкой и производством полимерных материалов для микроэлектронной промышленности. Постоянные глубокие исследования в области полимерных материалов помогают компании создавать новые продукты, занимая тем самым лидирующие позиции в современном мире производства полупроводников
Dow Corning® мировой лидер в области производства кремний-органических материалов для изделий электроники. Силиконовые материалы Dow Corning® отличаются высокими теплопроводящими, электроизоляционными свойствами и эксплуатационными характеристиками.
Корпорация Indium – это инновационный путь развития с 1934 года. Фундаментом технологического лидерства являются серьезные научные исследования при разработке технологических материалов и ориентация на высокотехнологичные и эффективные решения. Корпорация Indium специализируется на разработке передовых решений для производства электроники на основе металлов и их сплавов.
Компания SPM завоевала мировое признание как производитель высококачественной проволоки для микросварки с высокими допусками на основные характеристики. Вся проволока изготавливается методом вакуумной вытяжки из базовых металлов с высокой степенью очистки. SPM имеет многолетнюю репутацию поставщика монтажной проволоки по спецификациям заказчиков, использующих современное оборудование для микросварки.
Компания Ferro получила широкую известность среди разработчиков и производителей СВЧ электроники благодаря высоким техническим характеристикам, надёжности и качеству производимых материаолов для LTCC технологии. Низкотемпературная совместно обжигаемая керамика Ferro более 20 лет присутствует на рынке СВЧ электроники. Активно применяется ведущими производителями для создания радаров, антенн, фильтров, спутников и телекоммуникационных изделий. Постоянные глубокие исследования в области материалов для электроники позволяют компании Ferro занимать лидирующие позиции на рынке.
ostec-materials.ru
Лаба1.Часть3: сборка простых электронных схем на основе микросхем малой степени интеграции: 1i7 — LiveJournal
ЖЖ не проглотил вторую часть поста целиком тоже, поэтому разбиваю еще на две части. Здесь Часть 3 – Сама первая лабораторная работа, подбор реквизита для практических упражнений, введение в весь курс и в первую лабораторную работу.Итак, первое лабораторное занятие – “Сборка простых электронных схем на основе микросхем малой степени интеграции” – несколько практических упражнений для знакомства с основами цифровой логики:
– знакомство с макетными платами и базовыми элементами схемотехники (светодиоды, диоды, конденсаторы и т.п),
– базовые операции булевой алгебры в физическом исполнении,
– логические элементы (гейты),
– динамика в виде простого таймера,
– элементарные устройства вывода (диодный дисплей)
триггеры (флип-флопы) из первого знакомства выпали и оставлены для лучших времен.
Входные предположения об объектах обучения:
– имеют смутные воспоминания об основах электродинамики из курса школьной программы (напряжение плюс-минус, течет ток, можно добавлять сопротивление)
– имеют хорошее представление как минимум об основах дискретной математики (булева алгебра) и программирования (процедурное мышление), чтобы после прохождения ознакомительных упражнений иметь возможность интуитивно ощутить, что из представленных простых физических элементов логики можно строить большие дискретные системы любой степени сложности, в которых будут реализованы уже сложные абстрактные идеи, которые можно сформулировать на языке логики.
Собственно лабораторная работа
1. Главные детали — макетная плата, диоды и светодиоды
Макетная плата (breadboard) позволяет создавать электронные цепи любой конфигурации без применения паяльника – просто втыкая ножки элементов схемы в отверстия платы. Это возможно благодаря тому, каким образом эти дырочки соединены внутри под пластмассой проводниками. По краям проходят горизонтальные полосы с плюсом и минусом по всей длине платы – если воткнуть провод от батарейки (например плюс) в одну из дырок в любом месте, плюс будет подан по всей длине этой полосы и от него можно будет “питаться”, воткнув провод в любую другую дырку этой же горизонтальной полосы.
Основа платы – последовательность вертикальных (если смотреть на фото ниже) полосок-проводников по пять дырок над каждой. Если воткнуть два провода в две дырки над одной и той же вертикальной полосой, они будут соединены в цепь (тоже самое, что скрутить их ножки напрямую). Две соседние полоски никак не соединены, поэтому втыкая одни концы элементов в одни вертикальные полоски, а другие концы тех же элементов втыкать в другие, можно выстраивать последовательные цепи любой конфигурации. После этого с горизонтальной полосы с плюсом на одну из вертикальных полос через проводок подается плюс, а с горизонтальный полосы с минусом в другую часть цепи через другой проводок подается минус, и вся схема начинает работать.
Если сейчас не очень понятно, все прояснится после первого эксперимента со светодиодом.
За направление тока на схемах принято брать направление от плюса (+) к минусу (-).
Замечание: не путать “конвенционное” направление тока (от плюса к минусу) с направлением физического потока электронов, которые бегут от минуса к плюсу – т.е. в противоположном направлении – в некоторой литературе (в том числе в книге tron.ix на одной из первых картинок – отсюда и замечание) – используется направление потока электронов, в другой – “конвенционное” направление тока – это связано с традициями и некоторыми другими нюансами – электрические схемы удобнее читать, используя “конвенционное” направление плюс->минус, поэтому будем использовать везде именно его.
Диод – это проводник, который пропускает ток только в одном направлении – от плюса (+) к минусу (-), а от минуса (-) к плюсу (+) не пропускает. На схемах диод обозначается стрелочкой, упирающейся в вертикальную черту, стрелка указывает разрешенное диодом направление тока. Ножка диода, которую в режиме пропускания тока нужно подключать к плюсу называется анод, которую к минусу – катод.
Светодиод – тот же самый диод, только в режиме пропускания тока (когда на анод подается плюс, а на катод – минус) он светит лампочкой, а в режиме непропускания не светит. На схеме светодио обозначается также, как обычный диод, только стрелочка обведена в кружочек. Анод светодиода – длинная ножка (на нее подаем плюс), катод – короткая (ее обычно подключаем к минусу). На всех схемах в лабе – на фото и видео – длинная ножка находится слева, а короткая – справа.
2. Определение булевых значений TRUE/FALSE на выбранном участке цепи — светодиод в качестве индикатора текущего значения
Булевы переменные определяются уровнем напряжения на участке цепи, с которого снимаем значение. За TRUE=1=HIGH принимаем значение плюс (+) (“напряжение HIGH”), за FALSE=0=LOW принимаем минус (-) или землю (“напряжение LOW”).
Для того, чтобы воочию проверить текущее булево значение на выбранном участке, можно использовать светодиод – подключить к точке снятия значения анод (длинная ножка), катод (короткая ножка) при этом подключить к минусу. Если в точку подключения анода подан плюс (+), т.е. снимаемое значение должно быть TRUE, ток потечет от анода к катоду через светодиод и его лампочка загорится. Если в точке подключения анода будет минус или земля, ток не потечет, лампочка не загорится – снятое значение – FALSE.
Замечание: светодиод не рекомендуется подключать напрямую к батарейке без промежуточного сопротивления или если подключенное сопротивление слишком мало, т.к. иначе он сможет перегореть из-за слишком сильного тока, на который он не рассчитан (какое-то время он будет светиться, но при этом сильно нагреется и в конечном итоге перегорит). С сопротивление 500Ом (которое быше было выбрано в качестве “послабее”) светодиоду ничего не грозит.
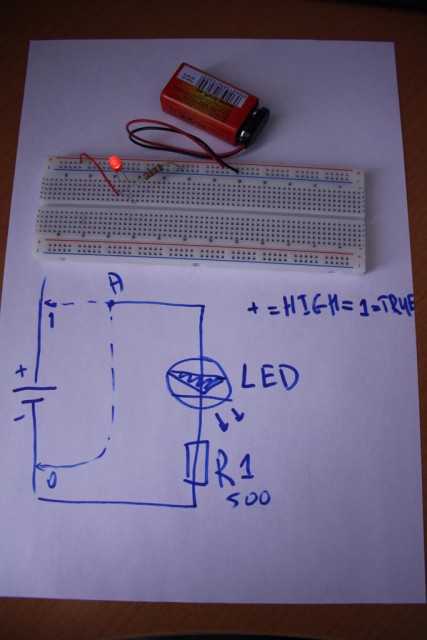
Вход A подключен к плюсу (+) – считаем, что в этой точке цепи значение 1=TRUE=HIGH – лампочка светодиода горит

Вход A подключен к минусу (-) – считаем, что в этой точке цепи значение 0=FALSE=LOW – лампочка светодиода не горит
Задание в аудитории: нарисовать на доске схему подключения светодиода и попросить группу реализовать ее на макетных платах. В этот момент сразу вскрывается нюанс, специфический для работы в аудитории. В книге tron.ix для каждого упражнении есть две картинки – одна показывает логическую схему подключения, на второй нарисована макетная плата с дырочками и все нужные элементики так, чтобы было видно, какие ножки куда втыкаются и т.п. Сидя дома с книгой проще смотреть на вторую картинку и просто повторять рисунок из книги на живой макетной плате. В аудитории с большим количеством человек этот фокус никак не прокатывает – внятное фотореалистичное изображение макетной платы со всеми дырочками и со всеми элементами, натыкаными в кучку, на доске маркером нарисовать довольно сложно, поэтому проще нарисовать принципиальную схему, а студенты уже сами вникают, как составить ее физическое воплощение на макетной плате. Первое задание с простым светодиодом и сопротивлением заняло около 10ти минут, т.к. это было первое знакомство с устройством макетной платы (схему соединений дырочек внутри платы во время первого задания кстати с доски можно не стирать) и повторная встреча с основами электродинамики после долго расставания – кое-кто например сначала решил засунуть ножки светодиода прямо в дырки полос для электропитания (причем обе в плюс), но после некоторых разъяснений и уточнений все в тему вникли и на следующих заданиях процесс конвертации логической схемы в физическую цепь шел уже значительно веселее.
3. Таблица истинности и оператор OR
Как было показано в предыдущем упражнении, в качестве переменных, которые могут принимать булевы значения TRUE/FALSE, мы можем брать определенные участки цепи – т.к. в разных условиях напряжение на одном и том же участке может быть как HIGH (+), так и LOW (-) – отсюда и термин “переменная” – возможностью присвоения значения.
При этом если мы встроим между двумя участками цепи некоторое комбинацию из электрических элементов (типа диодов, сопротивлений и т.п), эта промежуточная комбинация (или схема) может влиять на то, какое значение будет снято на втром (выходном участке) цепи в зависимости от текущего значения на 1м (входном) участке цепи. Т.е. эта промежуточная схема по сути преобразовывает одно или несколько значений на входящих участках цепи в новое значение на исходящем участке цепи по определенному правилу. Т.к. значения на всех участках (входящих и исходящих) могут принимать значение TRUE/FALSE, т.е. они являются булевыми переменными, мы можем принять промежуточную схему-преобразователь за обычный булев оператор (а именно за его физическую реализацию).
В дискретной математике любой оператор задается своей таблицей истинности, в которой перечислены все возможные комбинации значений переменных-параметров (для двух входных переменных: 11, 10, 01, 00) и указано значение резульатата действия оператора для каждой из комбинаций (для двух входных переменных это будет 4 значения единиц и нулей).
Как было указано в начале – предполагается, что аудитория должна быть знакома как минимум с основыми понятиями дискретной математики, к которым относятся в том числе таблицы истинности – в аудитории это предположение подтвердилось – долго объяснять, что из себя представляет таблица истинности, не пришлось – все и так уже были в курсе.
В качестве первого примера рассмотрим физическую реализацию элементарного булева оператора OR. Его принципиальная схема выглядит следующим образом:
Как выглядит его таблица истинности можно узнать, найдя определение этого оператора в учебнике по дискретной математике или собрав приведенную схему на макетной плате – для задания значений входным переменным-параметрам A и B можно втыкать соответствующие провода A и B в отсеки (+) (TRUE=1) или (-) (FALSE=0), при этом результат действия оператора на участке цепи Q будет видно по текущему состоянию красного светодиода (горит – оператор вернул Q=TRUE=1, не горит – Q=FALSE=0). Мы воспользуемся конечно вторым вариантом.

A=1 B=1 Q=1
A=1 B=0 Q=1
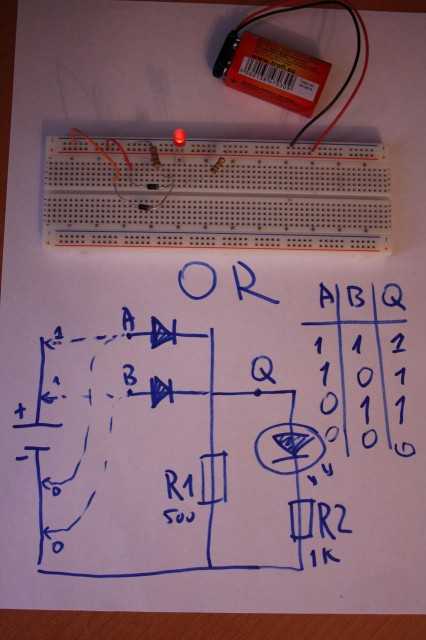
A=0 B=1 Q=1

A=0 B=0 Q=0
Замечание: почему так происходит физически в данном случае понять довольно просто – при подключении анода любого из входных диодов к плюсу (A=1 или B=1) цепь замыкается и на точку Q (к которой в том числе подключен анод светодиода) подается ненулевое напряжение – лампочка горит – Q=HIGH=TRUE. Если ни один из анодов A и B не подключен к плюсу (+) (т.е. A=0=FALSE и B=0=FALSE), напряжению в цепи взяться вообще неоткуда, т.к. участок с плюсом полностью изолирован – поэтому лампочка гореть не может и Q=LOW=FALSE. Но заострять внимание здесь и на следующих схемах на этом механизме во время занятия в аудитории думаю не обязательно, т.к. мозг студентов в этот момент занят впитыванием и усвоением информации о том, что привычные им из дискретной математики и программирования булевы операторы могут вести себя также, как и живые лампочки на схеме, которую они только что собрали из нескольких проводов, т.е. давать одни и те же таблицы истинности. Поэтому важнее сакнцентировать внимание именно на наблюдении принципиальной возможности существования точки перехода “физика в лице электродинамики” -> “абстракции дискретной математики”. Дополнительное погружение в электродинамику может повредить этому процессу или в конечном итоге просто не будет воспринятно так, как нужно – объяснение деталей механизма этого процесса можно оставить на самостоятельную работу, на отдельное занятие напотом или иметь ввиду на случай дополнительных вопросов из аудитории (если вдруг кто-то все-таки усвоит новую информацию достаточно быстро и захочет дополнительных объяснений).
4. Оператор AND
Почти ничего нового по сравнию с предыдущим упражнением – просто строим оператор AND по схеме.

A=1 B=1 Q=1

A=1 B=0 Q=0
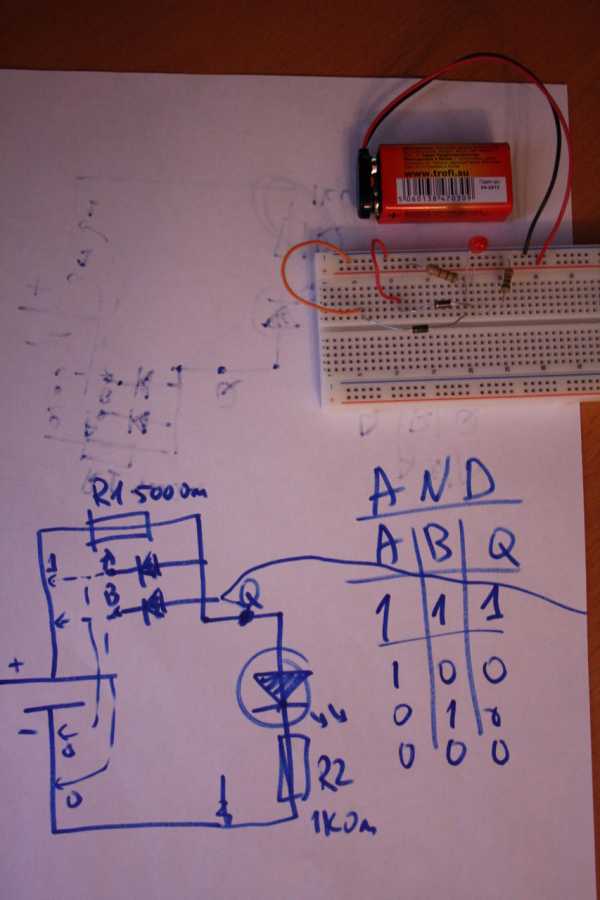
A=0 B=1 Q=0

A=0 B=0 Q=0
Замечание: по физике процесса – если замыкаем один из катодов (A или B) на минус (-), ток потечет напрямую от плюса к минусу по участку сети через соответствующий диод, а на участок сети Q (при такой конфигурации он оказывается подключенным параллельно диоду) силы тока просто “не хватит”, чтобы зажечь лампочку (т.е. присвоить Q=TRUE), т.к. при параллельном подключении участков цепи ток распределяется обратнопропорционально значению внутренних сопротивлений этих участков (например если подключить один из диодов через индивидуально сопротивление, то фокус работать не будет – ток потечет по обоим каналам).
Замечание: в аудитории – при построении цепи желательно уместить ее в левой пловине макетной платы, т.к. дальше мы будем использовать ее же для составного оператора NAND.
(помарки: “катод” подписан неправильно, диоды A и B нарисованы как светодиоды)
5. Оператор NOT и транзистор
Аналогично строим цепь для
1i7.livejournal.com
Делаем микросхемы дома — часть 3 / Habr
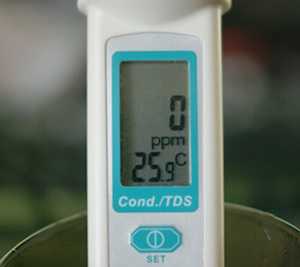
Напомню цель проекта: научиться изготавливать несложные кремниевые цифровые микросхемы в «домашних» условиях. Это никоим образом не позволит конкурировать с серийным производством — помимо того, что оно на порядки более совершенное (~22нм против ~20мкм, каждый транзистор в миллион раз меньше по площади), так еще и чудовищно дешевое (этот пункт не сразу стал очевиден). Тем не менее, даже простейшие работающие микросхемы, изготовленные в домашних условиях будут иметь как минимум образовательную и конечно декоративную ценность.
Как я уже упоминал в комментариях к другому топику, попытка выйти с этим проектом на kickstarter провалилась — проект не прошел модерацию из-за отсутствия прототипа. Это заставило в очередной раз переосмыслить пути коммерциализации этой упрощенной технологии. Возможность релиза технологии домашних микросхем в виде RepRap-подобного opensource-кита покрыта туманом: очень уж много опасной, дорогой и нестойкой химии — так просто рассылать по почте не выйдет. Также по видимому отсутствует возможность делать мелкие партии микросхем дешевле серийных заводов: сейчас минимальные тестовые партии микросхем можно изготавливать примерно по 30-50$ штука (в партии ~25 штук), и существенно дешевле 30$ за микросхему сделать это на самодельной упрощенной установке не получится. Кроме того, не смотря на низкую цену на обычных заводах — любительские микросхемы практически никто не делает, задач где они имели бы преимущества перед FPGA/CPLD/микроконтроллерами практически нет, а стоимость и сложность разработки — остается очень высокой.Но как я уже упоминал выше — даже с этими недостатками проект остается для меня интересным.
Из того, что уже упоминалось в моих других статьях в последние месяцы — куплен кислородный концентратор, позволяет получить ~95% кислород без головной боли. Из вредных примесей — похоже только углекислый газ (35ppm), будем надеяться, этого будет достаточно. Также едет из Китая генератор озона (ему на входе нужен кислород) — есть результаты исследований, показывающих что им удобно растить тонкие подзатворные диэлектрики и использовать как один из этапов для очистки пластин.
Уже достаточно давно куплен металлографический микроскоп, и исследованы кучи существующих микросхем. В целом, стало намного понятнее с чем придется иметь дело. И наконец, поскольку микроскоп — симметричный прибор, его можно использовать для проекции уменьшенного изображения при фотолитографии. Совмещение изображения — визуальное и ручное. Источник освещения для проецирования — даже не обязательно УФ диодом делать, белый свет также вполне подойдет — качество изображения позволяет (хотя мощные 405нм диоды у меня тоже есть). Достижимые таким образом нормы фотолитографии — микронные (если сильно постараться — то до ~350нм), но смысла сильно уменьшать транзисторы нет — т.к. пропорционально уменьшается и «размер кадра», контакты к которым придется приваривать выводы станут слишком мелкими. Так что придется первоначально ограничиться нормами 10-20мкм, как и планировалось.
Микроскоп несколько поколебал веру как в отечественных производителей, так и в китайских. Оказалось, некоторые «отечественные» микроскопы — перемаркированные китайцы за 200-300% цены. С другой стороны — один из объективов похоже немного кривоват и предметный столик имел небольшой дефект литья — пришлось дорабатывать напильником (в прямом смысле этого слова).
Один из важных химических элементов для производства микросхем — вода. Опять-же в Китае куплен кондуктометр — измеритель электропроводности воды. По электропроводности можно оценить количество растворенных солей (+-50%, если не известно что именно растворено). В воде обычно растворены соли калия, натрия, кальция и марганца — и все они очень опасны для микросхем (особенно натрий и калий), т.к. их ионы могут быстро двигаться в кремнии и оксиде кремния при обычных температурах и изменять электрические параметры транзисторов (для полевых транзисторов — пороговое напряжение, утечку).
Измерил имеющиеся образцы воды, и получил следующее:
Концентрация примесей | |
Водопроводная вода | 219ppm |
«Новый» бытовой фильтр | 118ppm |
«Старый» бытовой фильтр | 210ppm |
Кипяченая вода из нового фильтра | 140ppm (!!! 2 раза перепроверял) |
Бидистиллированная вода из Русхима (Не похоже на бидистиллированную) |
10ppm |
Деионизировнаная вода из института микробиологии | 0ppm |
Деионизированная после 6 часов на воздухе (Из-за растворения углекислого газа из воздуха) |
8ppm |

Также удалось купить и TMAH (тетраметиламмония гидроксид) — используется как проявитель для фоторезиста, не содержащий ионов щелочных металлов (которые как мы знаем — зло).
Для вакуумной системы — вместо покупки вакуумной резины (несколько раз пытался — но так и не осилил), нашелся в Китае вот такой вот gasket maker — паста, которую можно выдавить в нужную форму, она затвердевает — и становится резиновой.
По печке: для теплоизоляции — куплено вот такое базальтовое полотно, используется для теплоизоляции ядерных реакторов. Выдерживает 1000-1200 градусов.
Под микроскопом — видно отдельные нити расплавленного базальта, из которых сплетено полотно. Вот это настоящие нанотехнологии!!! В голове по началу не укладывается: как из камня можно сделать тончайшие нити, и соткать гибкий материал? (масштаб: 1 пиксель ~ 3 микрометра):
Найдены и порезаны кварцевые трубки для печки разного диаметра. Первый уровень теплоизоляции — воздушный зазор межу вставленными друг в друга трубками.
Изначально я думал питать печку прямо от 220 вольт — но все-же благоразумно решил перейти на питание постоянным напряжением 48 Вольт — это позволит как точнее регулировать и контролировать мощность, так и сделает конструкцию безопаснее. Куплены 2 блока питания на 400Вт. Как китайцы такой блок производят и доставляют за 19$ — загадка:
Для контроля температуры — изначально были куплены высокотемпературные термопары, рассчитанные на 1200 градусов (про них писал в прошлой серии — но фотографии не было). Размер конечно конский. Вероятно будет проще следить за уровнем инфракрасного излучения на длине волны 1мкм — кварц для него прозрачен.
И наконец — инертная среда для печки. В моем случае это Аргон. Из-за особенностей разделения газов — аргон получается чище, чем азот, хоть и несколько дороже. Я купил маленький 10л баллон, и регулятор. Регулятор внезапно не подошел — резьба не совпадает, нужно или переходник искать, или другой регулятор покупать.
Оказалось, сжатые газы продают рядом с домом (жизнь в промышленной зоне Москвы имеет свои преимущества) — и я приехал за ним с тележкой. Рабочий не оценил мой порыв — и настоятельно рекомендовал завернуть баллон в картон, чтобы прохожие не переживали. За 15 минут мы справились с камуфляжем. В общем, встреча с реальным миром вечно дарит сюрпризы 🙂
Генератор азота — это конечно удобно, работать с пластинами в инертной атмосфере и не возиться с баллонами, но также не критично.
Единственное, что серьёзно могло бы облегчить работу — это образцы spin-on dopants и spin-on glass. В России по различным причинам их не используют и не производят, за рубежем — производителей мало, продается большими партиями и стоит дорого (тысячи $). Компания Emulsitone, у которой покупала образцы Jeri Ellsworth когда делала свои транзисторы — похоже загнулась, с ними связаться так и не удалось. Но это также не обязательный пункт — работать можно и без них (с фосфорной и борной кислотами, POCl3 и BBr3), хоть и намного сложнее / несколько опаснее.
И наконец — конечно не хватает спонсора для моих проектов, иногда между дополнительными затратами времени и дополнительными затратами денег приходится выбирать первое. Если кто-то из компаний или частных лиц имеет желание спонсировать мои проекты (условия обсуждаемы) — вы знаете, где меня найти :-).
Update: Ориентировочная смета есть, высылаю по запросу — т.е. представление на что именно нужны деньги — есть.
Затем нужно думать, как в домашних условиях сделать ультразвуковую или термокомпрессионную сварку проволоки с кремниевой пластиной — это нужно для подключения выводов.
Надеюсь, в обозримом будущем домашние микросхемы мы все-же увидим 🙂
habr.com